0 引言
随着市场对于物流自动化装备需求的不断增加,机器人在物流仓储行业得到越来越广泛的应用。智能仓储机器人在物流系统的应用,在提高作业效率、降低工作人员劳动强度、优化资源、降低成本等方面发挥了重要作用。用机器人取代人工、提高仓储自动化水平已是势在必然。另外,在“工业4.0”、“智能制造”等数字化制造的背景下,智能工厂是工业变更时代未来的发展方向。而智能物流是智能工厂的基础和保障,因此智能物流将迎来巨大发展契机,仓储环节的码垛机器人集成系统应用也随之大幅增长。
目前大部分物流仓储行业的机器人自动码垛系统实现方式有以下两种:1)机器人码垛线上的产品为同一品种批次,只需设置一次码垛信息,输送线控制系统便能实现自主码垛;2)机器人码垛线上有多品种多批次的产品,输送线控制系统通过识别产品外箱的条码(条码包含产品品种与批次信息)自主区分产品的品种与批次,实现自动分道码垛,从而实现相同品种批次的产品码放在同一托盘的功能。
在医药行业,同样要求同种产品不能混批码放,但产品箱粘贴的是药品电子监管码,此码是药品的唯一追溯码,输送线控制系统通过条码号不能解析出产品品种与批次信息,不能实现自主码垛,因此自动码垛环节需要在上位计算机的合理调度管理下进行。在本文中输送线控制系统扫描电子监管码后上传上位机系统,上位机系统获取此电子监管码绑定的产品与批次信息,实现从产品上线到产品码垛以及产品垛型的全面管理。本文以某医药物流仓储系统为例,详细介绍智能码垛系统的研究与应用。
1 医药物流码垛系统概述
该医药自动化物流仓储系统包括16条与车间生产线对接的自动化箱式输送线。生产线同时生产不同品种不同批次的产品并通过16条输送线输送至码垛系统。在16条输送线的上线口分别有条码阅读器,输送线控制系统扫描产品电子监管码,并将已读到电子监管码上传上位机系统,用于对上线产品进行记录跟踪,同时对盲码产品进行剔除。16条箱式输送线产品最终合流到一条主线上输送,G1设备读取电子监管码并上传至上位机,由上位机系统根据调度算法分流到三条码垛线。机器人抓取工位G2、G3、G4三段设备分别有条码阅读器,用于对产品电子监管码的再次校验与上位机系统分配码垛工位。码垛系统共3台真空吸盘式机器人,每次动作吸取一个产品箱,每一台机器人对应8个码垛工位,共24个码垛工位,可以同时完成24个品种批次的产品码垛,码垛完成的托盘经自动化输送线进入立体仓库。系统布局图如图1所示。
上位机系统实现了上线产品记录跟踪、产品智能分流管理、动态分配码垛工位管理与产品码垛垛型管理等功能。上位机系统对医药物流码垛系统的管理原则为:从上线口开始对产品进行实时跟踪,同品种的不同批次产品不能混批次码放,同品种同批次的产品只能占用一条码垛线,但同时可以占用多个码垛工位。
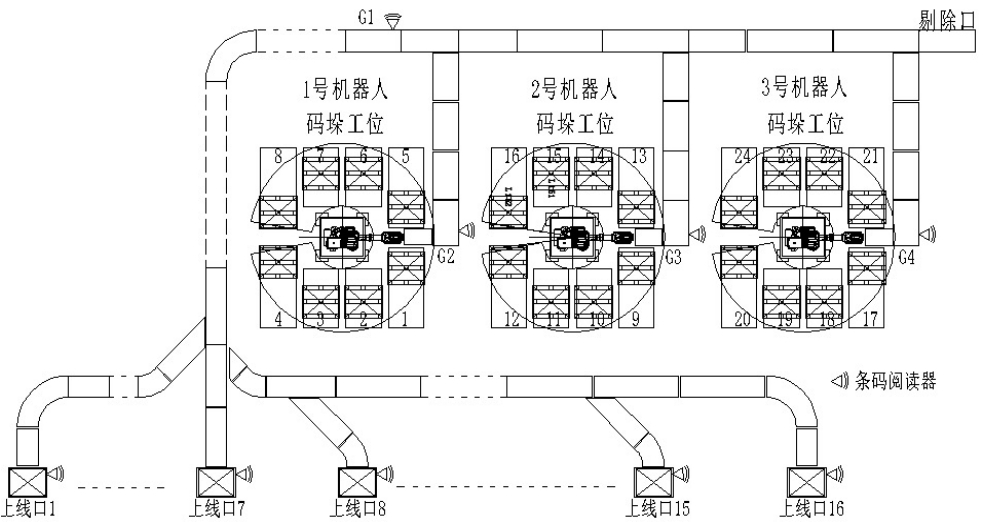
图1 系统布局图
2 上位机系统智能码垛管理
2.1 上线口产品管理
此码垛系统的16条箱式线与车间生产线实现无缝对接,包装完成的产品箱直接进入箱式输送线,省去了人工搬运产品环节,极大程度减少劳动力的使用,提高了生产效率与产品入库及时性。条码阅读器读取产品电子监管码,盲码产品进行剔除,上位机系统通过接口系统查询此电子监管码是否已绑定产品信息,无绑定信息自动剔除;并计算当前上线产品的品种批次数量,多于24种则进行剔除。
对于正常产品箱上位机系统记录每一个上线口的产品电子监管码、产品名称、批次、车间生产线编号与当前状态。产品进入上线口,当前状态为“上线输送”;当产品经过G1设备分流时,当前状态更新为“进入码垛线”,但当G1设备上产品盲码时,此产品被输送至剔除口,需要人工用手持终端设备扫描电子监管码对产品进行人工入库,产品当前状态更新为“人工扫描入库”;当产品在码垛工位托盘上时,当前状态更新为“在码垛工位”;当码垛托盘入库后,当前状态更新为“在库房内”,当产品出库后,当前状态更新为“已出库”。在上位机系统可以实时查询上线产品数量、每一个上线口的已上线产品数量,每一箱产品的当前位置,实现了产品从上线到出库的全程跟踪记录,保证了上线产品记录数据的完整性与准确性。
2.2 码垛前的产品箱分流算法
16条箱式输送线产品箱合流到一条主线输送,经过G1设备时进行分流到三条码垛线,产品箱分流算法描述如下:输送线控制系统扫描G1设备产品电子监管码向上位机系统要求分配码垛线。上位机系统按照每条码垛线的品种批次、数量等信息,并结合码垛工位信息,遵循三条码垛线码垛产品数量均衡、线体不拥堵、效率最高等原则,进行智能计算后,给输送线控制系统写入码垛线去向,输送产品箱至对应的码垛机器人站台。同时上位机系统生成码垛作业,码垛作业信息包括码垛线号、品种、批次等。当同品种同批次产品再次经过G1时,上位机系统即可在码垛作业中查询此产品的码垛作业信息下发指令。
在实际应用过程中,由于箱式线输送速度比较快或者产品箱在输送过程中位置调整变化,可能会造成G1设备的产品箱读码失败,产品箱之间距离间隔较短,当上位机系统与输送线控制系统通讯出现网络延时,出现后箱按照前箱的指令输送现象,造成产品箱进入错误的码垛线,此条码垛线无该产品的码垛作业,设备报警,直接影响了整条码垛线的作业效率。
为解决以上问题,在输送线控制系统扫描电子监管码要求分配码垛线去向时,优化上位机系统和输送线控制系统的通讯握手方式,在分流算法中加入校验算法,即把码垛线号与电子监管码同时写入输送线控制系统,输送线控制系统判断上位机写入的电子监管码与当前系统采集的电子监管码是否一致,不一致则继续向上位机系统上传电子监管码要求分配码垛线去向,一致则进行输送,通过此校验算法从根本上解决了产品箱分流出现的问题。
2.3 码垛工位动态分配算法
产品箱进入机器人抓取位G2、G3、G4时,输送线控制系统扫描电子监管码后上传上位机系统,上位机系统分配产品箱的码垛托盘工位与垛型号,机器人抓取产品进行作业。码垛作业流程图如图2所示。上位机系统智能分配工位算法描述如下:
1)此处同样应用了上节描述的电子监管码校验算法,杜绝了发生混品种、混批次码垛现象。
2)上位机系统与输送线控制系统进行产品箱码垛工位信息交互时,机器人抓取动作同时进行,提高了码垛效率。
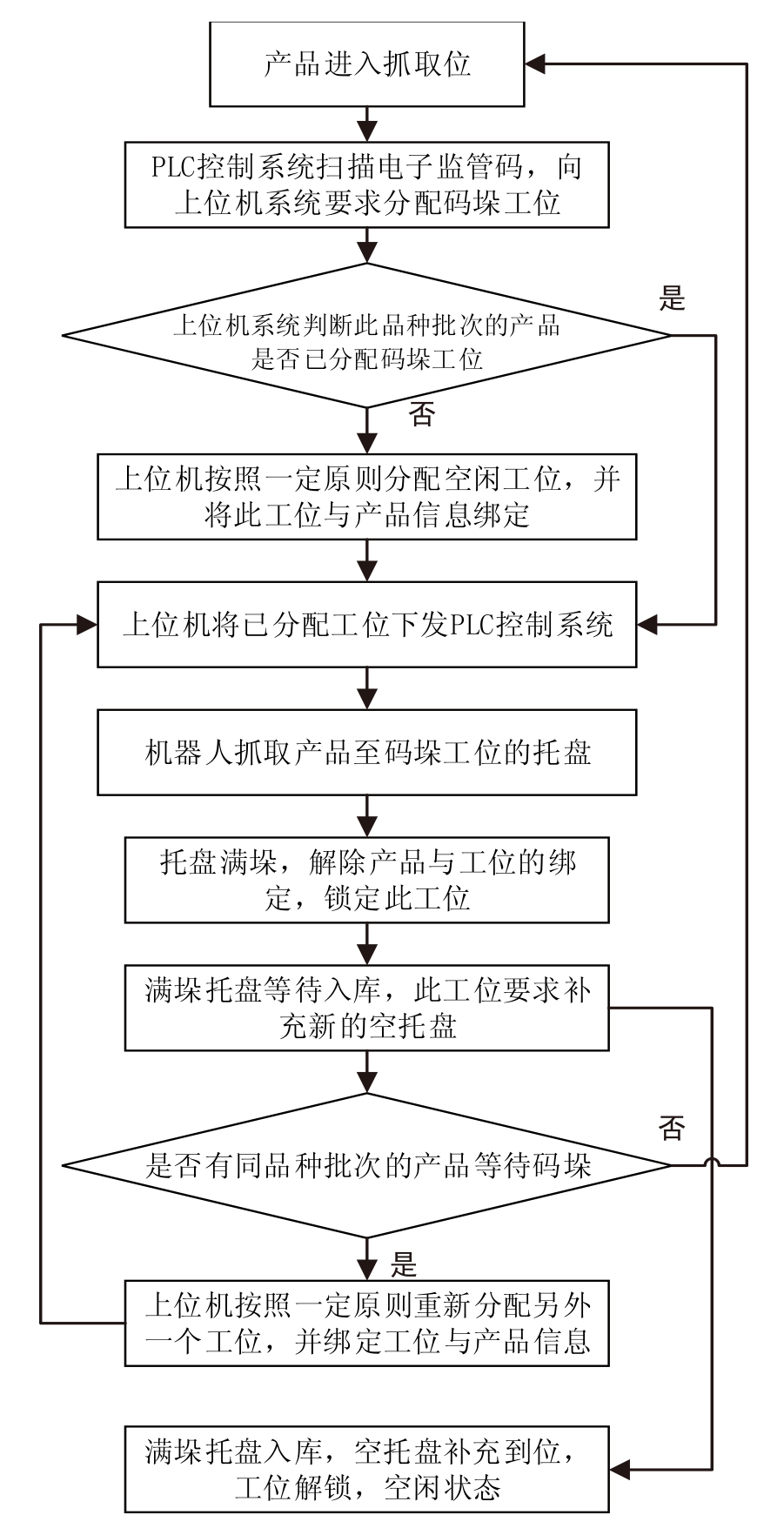
图2 产品码垛流程图
3)8个码垛托盘工位循环分配原则。
4)优先分配距离机器人近的4个工位,机器人行走距离短,码垛时间短、效率高。
5)在机器人码垛过程中,上位机系统将产品信息与码垛工位进行绑定,当输送线控制系统反馈托盘码垛完成信号后,上位机系统解除产品与此工位的绑定并锁定当前工位,满垛托盘等待入库并需要给此工位补充新的空托盘,当新空托盘补充到位后对此工位进行解锁,此工位处于空闲状态,可以进行码垛。如果此时仍有此种产品箱等待机器人抓取,而原来的码垛工位尚未解锁,上位机系统则重新分配另外一个空闲工位,而不是等待原来的工位,大大提高了码垛效率。
6)上位机系统与车间赋码系统对接,收到赋码系统的断批指令后,上位机系统自动计算已码垛产品数量,与车间生产数量对比,数量一致删除此产品的码垛作业,同时允许新品种上线。数量不一致说明仍有部分产品箱在箱式线输送,此时等待剩余产品箱码垛入库,这样提高了产品断批的及时性与码垛工位的利用率。
7)上位机系统可以设置每一个工位的使用状态,锁定或者打开。当工位处于空闲未使用状态时,可以进行锁定,锁定后的工位处于不可用状态。当系统出现某些异常情况时,可以对工位锁定,提高了工位利用的灵活性。
通过以上码垛工位动态分配算法,杜绝了混品种、混批次码垛现象的发生,缩短了机器人的行走距离,提高了码垛效率与工位利用的灵活性、利用率。
2.4 产品垛型管理
目前机器人码垛系统编程工作一般通过示教再现的方式实现,即现场调试人员手动移动机器人,将码垛过程中的产品抓取点、产品放置点以及运动轨迹中必要的过渡点对机器人进行示教,编写程序,反复测试机器人程序,并不断进行修改。这样机器人系统要记录大量的示教数据,示教的过程复杂,这不仅加重了现场操作人员的工作量,而且机器人的编程工作量也很大,十分不利于提高机器人的调试效率。在此医药物流码垛系统中,共有50多个品种的产品需要进入自动化码垛系统,即50多种箱型,每一种箱型的尺寸都不相同,而且在使用过程中,还会出现增加新品种新箱型的情况。如果按照目前的方法,每增加一种新的产品箱型,都需要对机器人重新做一次调试工作,而且用户很难独立完成,码垛系统可操作性、可维护性低。
在总结多个码垛项目的基础上,针对各种垛型图样的共性,设计了一种能够充分描述机器人码垛过程中所有工作参数的垛型数据结构及其相关的编程方法。在该垛型数据结构中,包含了机器人抓取和放置产品时的位置、垛型号、箱体尺寸和机器人搬运产品时所有的过渡点等信息。该码垛系统能够适应多种垛型的工艺要求,运行稳定可靠。所设计的垛型数据结构包含了机器人搬运过程中的全部信息,更改和修改垛型时,只需在线或者离线更新垛型数据结构即可。
当增加新的码垛品种时,用户只需要在上位机系统界面输入物料编码、箱体尺寸信息、箱体垛型、箱型号等信息,点击【添加】按钮,此产品的垛型信息会自动同步至机器人垛型数据中。当需要修改码垛产品垛型信息时,修改完毕点击【修改】按钮,垛型信息同样会同步更新到机器人垛型数据。用户操作简单方便,增加了码垛系统可维护性。上位机系统垛型管理界面如图3所示。
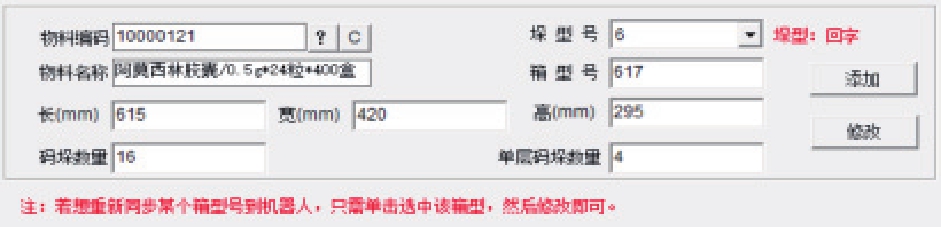
图3 上位机垛型管理示意图
3 结束语
此智能码垛系统已在某医药公司运行半年多,码垛产品累计计数30万多箱,账目准确,无丢箱、无产品箱进入错误的码垛线,无产品混品种混批次码放等现象发生,机器人无压箱、压垛现象发生,系统运行稳定可靠。
在互联网经济及产业互联网化的趋势下,仓储物流业正迎来空前的发展机遇和全新的模式变化。其中机器人技术的应用程度已经成为决定企业间相互竞争和未来发展的重要衡量因素。根据统计,如果应用仓储物流机器人,在保证同等储存能力的条件下,可至少节约70%以上的土地和80% 以上的劳动力。随着生产线的速度不断提高和现代物流意识的增强 , 许多医药企业已经采用自动码垛方式,智能仓储物流机器人将对医药物流运作模式和整个物流体系变革产生深远影响。
可以预见,智能机器人在物流行业的应用,未来几年将进入持续稳定发展的新时期。智能机器人的日益普及和高速发展,必将引爆一场仓储物流智能化的变革,甚至是整个物流行业、制造业、生产和生活方方面面的智能化大革命。
参考文献:
[1]吴勇.自动码垛与物流[J].现代制造,2003,(3):38-40.
[2]李红果,刘新乐,徐德众,周益林,朱佳琪.一种多垛型机器人码垛系统的设计[J].包装工程,2017,38(5):40-44.
[3]孙浩.码垛机器人的设计与研究[D].山东理工大学.2013.
[4]李晓刚,刘晋浩.码垛机器人的研究与应用现状、问题及对策[J].包装工程,2011,32(3):96-102.