随着“中国制造2025”战略的发展,轮胎企业正开启新时代转型升级之路,智能制造在轮胎工业已取得重大进展[1~2]。自动化技术的应用是实现智能制造的必要条件[3~4]。但密炼生产工艺的自动化程度仍存在较大提升空间。轮胎企业中密炼车间天然胶和合成胶主要通过人工将胶块搬运至密炼机输送线上或搬运至碎胶机生产线,由于单块胶块重量达约50 kg,频繁搬运造成工人的劳动强度大,工作效率低,而且手工抓拿空间较小且需弯腰向下操作,危险性极大且存在搬运胶种误操作等相关问题。固体块状的橡胶原材料在常温下比常见的橡胶成品弹性、韧性都稍差,但仍属柔软易变形类固体物质,因此抓取难度较大。此外,由于胶块停放时间影响,胶块之间有时会存在粘连现象,如何通过一种自动化抓胶装置彻底替代人工成为难题。业内的一些轮胎企业外购真空吸盘吊、气动吸盘吊,但其存在可靠性差、维修成本高、自动化程度低等问题[5]。传统轮胎生产中的密炼环节中由于不同轮胎企业密炼车间生产工艺略有差异,部分轮胎企业工艺要求先将胶块放置烘胶房中烘胶,然后送至密炼车间的密炼机输送线旁边,由工人搬运至密炼机输送线上。这种工艺情况下胶块硬度较小,但当前很多企业工艺要求不对胶块进行烘胶而是直接搬运至密炼机输送线上,由于胶块硬度较大,特别是当气温进入冬季,环境温度较低,一些轮胎企业引进的钢针式抓胶搬运机器人无法有效的保证将胶块抓起。而采用真空吸盘形式进行抓胶,由于胶块表面平整度不均,外形尺寸存在一定差异,在实际应用过程中会出现中途脱落现象,可靠性差。此外,当前市场上的自动化抓胶装置对粘连胶块的有效抓取与分离处理都不能找到很好的解决方案。
1 设计目标
基于现有技术中存在的人工搬运劳动强度大以及现有搬胶技术自动化程度低、可靠性差的问题,新型机器人自动搬胶系统可有效替代人工,并能够自动区分胶种。而且抓胶过程不受企业生产工艺及环境温度影响,可靠程度高,可有效解决自动化搬胶过程中出现的胶块粘连问题。
2 装置设计
在轮胎企业密炼车间中,由人工叉车将天然胶块和合成胶块送至密炼机上料输送线旁边,部分企业自动化程度高,可由AGV送至碎胶机自动化生产线旁边。然后通过机器人自动搬胶装置将胶块抓取并放置到密炼机入料输送线上。机器人自动搬胶装置主要由机器人、抓具、安全防护系统、图像识别系统以及控制系统组成。如图1所示。整个电气控制系统充分考虑人机的交互功能。系统采用PLC控制方式,PLC的CPU作为整个控制系统的心脏并具有完善的安全连锁、保险及报警等功能。在生产线的操作侧设计有急停开关,此急停开关与密炼机的急停开关组成串联系统,当出现意外情况可及时停止炼胶设备及机器人的运行。
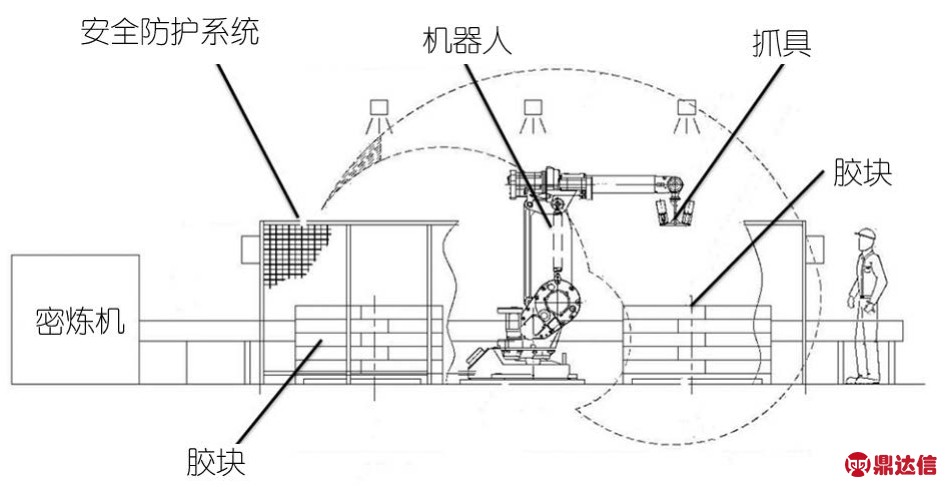
图1 密炼机生产线运行示意图
3 系统设备应用
3.1 系统工作原理
通过安装在机器人抓具上的照相测量装置(包括激光测距装置)确定待搬运胶块实际位置并将信息传给机器人系统,同时通过照相测量装置确认输送带上是否有空位,然后机器人借助抓具将胶块从托盘移至输送带空位上实现胶块的自动搬运。整个工作区域设置安全栏及安全光栅并通过系统控制实现安全防护。机器人自动搬胶流程如图2所示。
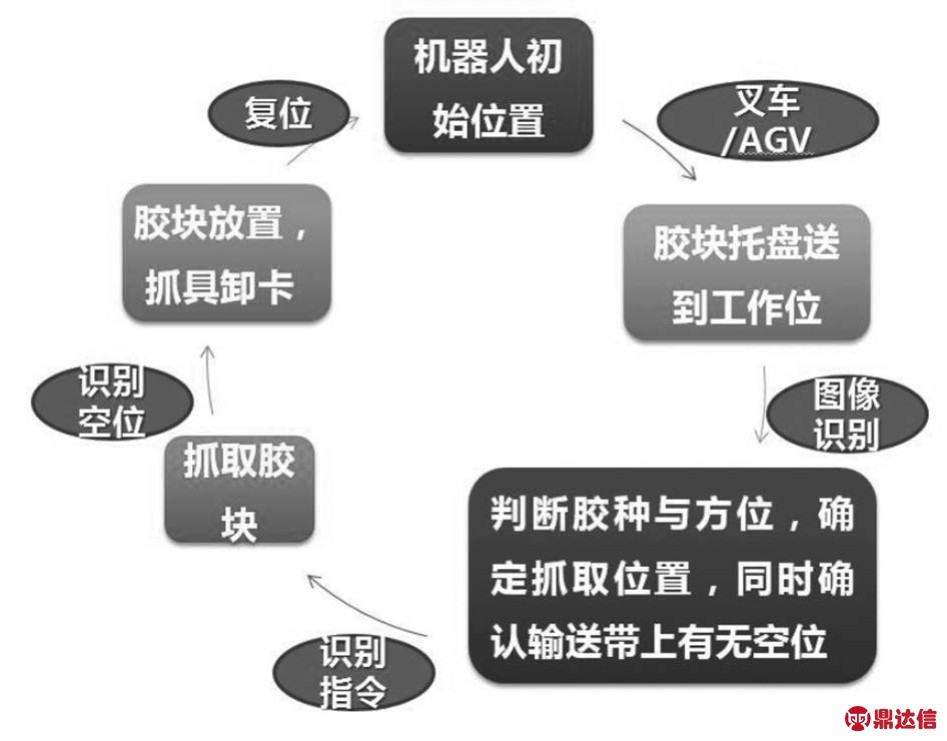
图2 机器人自动搬胶流程图
3.2 工作过程
机器人通过抓具上的激光测距装置和图像识别系统锁定所需搬运的胶块并通过钢针或螺杆实现对胶块的抓取与搬运。对于生产工艺要求胶块烘胶后进入密炼机的轮胎企业,胶块或胶块表面温度高于0℃时,抓具中电机连接螺杆在油缸作用下,沿着导轨滑块上移,直至两侧螺杆末端位置处在抓具靠近胶块表面且不触碰胶块的位置。当抓具靠近胶块时,连杆气缸带动钢针运动,将钢针插入胶块中,机器人带动抓具将胶块移至密炼机生产线,同时旋转抓具,保证胶块按照正确方向放置在密炼机上料输送带上方,然后连杆气缸带动钢针收缩,胶块脱落至密炼机上料输送带上。对于生产工艺要求胶块不经烘胶直接送入密炼机或碎胶机的轮胎企业,由于胶块硬度较大,抓具移至胶块上方,同时连杆气缸收缩,电机带动螺杆转动,当抓具移动至胶块表面时,电机在油缸驱动和导轨滑块作用下螺杆钻入胶块中,当螺杆钻入2/3胶块厚度时,油缸停止动作并锁定位置,夹具在机器人作用下提起并带动胶块送至密炼机上料输送线,电机反转同时在油缸驱动下,沿导轨滑块放置胶块于密炼机上料输送线上。
对于钢叉式模块工作的特殊情况,当连杆气缸插入胶块后,发现胶块粘连在一起时,螺杆在电机和油缸驱动下钻入胶块中,螺杆不断钻入,直至钻通胶块。在自身重力作用下,胶块与胶块之间将会出现间隙,如果胶块与胶块之间仍未分离,螺杆继续在电机和油缸、导轨滑块作用下钻入胶块中,然后螺杆通过电机反转,并由油缸驱动上移,直至两胶块分离,然后抓具在机器人作用下移送至密炼机上料输送线并按前序步骤放置胶块。
对于螺杆模块工作的特殊情况,当螺杆插入胶块1后,发现胶块粘连在一起时,其中电机继续在油缸驱动和导轨滑块作用下带动螺杆钻入胶块1,并开始接触下层胶块表面,在胶块自身重力作用下,两胶块间将会出现间隙,如果胶块仍未分离,螺杆继续在电机和油缸以及导轨滑块作用下钻入下层胶块,然后螺杆在电机驱动下反转,并由油缸驱动上移,粘连胶块分离,然后抓具在机器人作用下移送至密炼机上料输送线并按前序步骤放置胶块。
分离过程如图3所示。
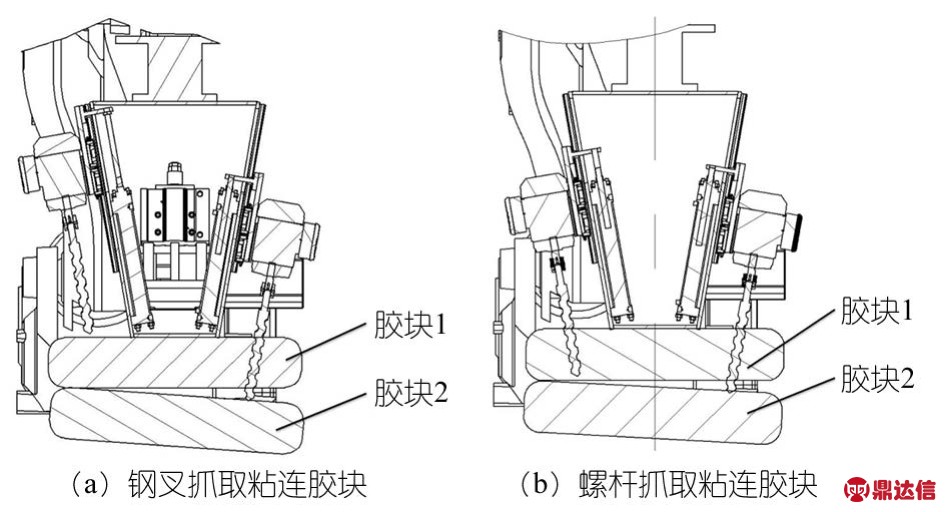
图3 黏连胶块分离过程结构图
4 关键部件结构设计
4.1 抓具工作原理
为可靠抓取胶块,抓具方案采以两组气缸为动力驱动的钢叉对称布局,同时另外两侧布置两组油缸动力驱动的电机螺杆,以适应天然胶和合成胶的抓取应对。两种不同结构模块根据生产工艺及环境温度导致的胶块硬度进行使用,钢叉式结构适应于室温下的合成胶和经烘胶后的胶块的抓取,电机驱动螺杆式模块适应于硬度较大的胶块搬运。抓具抓取胶块的卸载主要靠抓具上的支架挡板辅助。
4.2 结构特点
抓具主要由电机及螺杆、油缸、导轨滑块、气缸、钢针等组成。具体工作过程如图4所示。抓具包括支架,支架安装在机械臂上,支架底端设有挡板,该支架上设有推送元件,推送元件为推杆气缸结构。推送元件伸缩杆安装有钢针,推送元件伸缩杆带动钢针上下移动。支架还设有滑块上下滑动的滑台,滑台的滑块安装有电机,电机主轴连接有螺杆,螺杆底端朝下设置,滑台为液压油缸驱动滑台。钢针和螺杆底端向内倾斜设置。支架上还设有用于检测抓具和待搬运胶块距离的激光测距传感器以及用于对胶块图像监控的图像传感器。
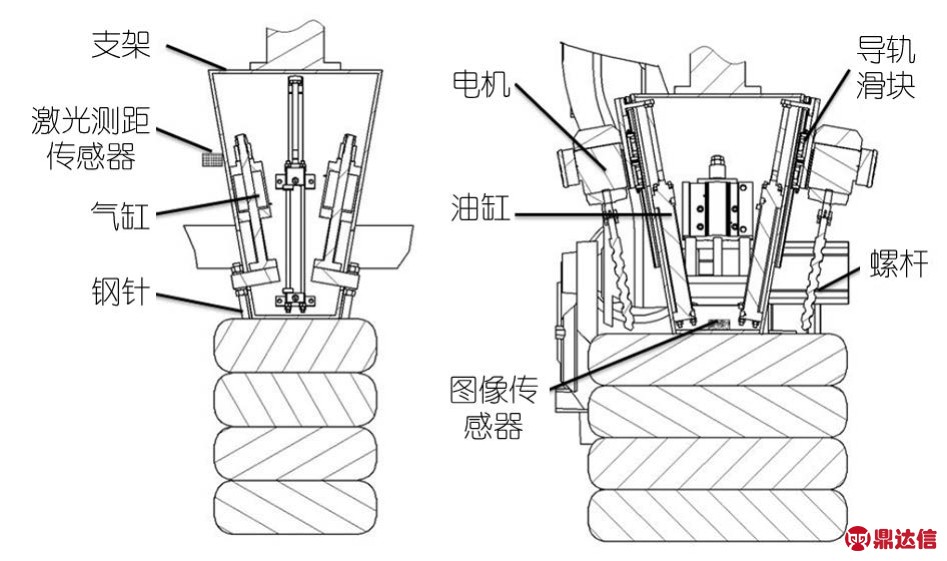
图4 机器人抓具结构图
4 技术优势
机器人自动搬胶装置,通过图像识别、激光测距装置确定胶块的种类与位置,由于自身的弹性变形使得胶块牢固挂装在钢针或螺杆上,然后通过机械臂自动搬运至输送带上,实现胶块自动搬运输送要求,且在胶块搬运过程中,胶块和钢针(螺或杆)连接稳定,可有效避免脱落,保证稳定搬运要求。通过抓具结构既可适应不同胶种的抓取,又可以处理抓取胶块过程中出现的胶块黏连问题。
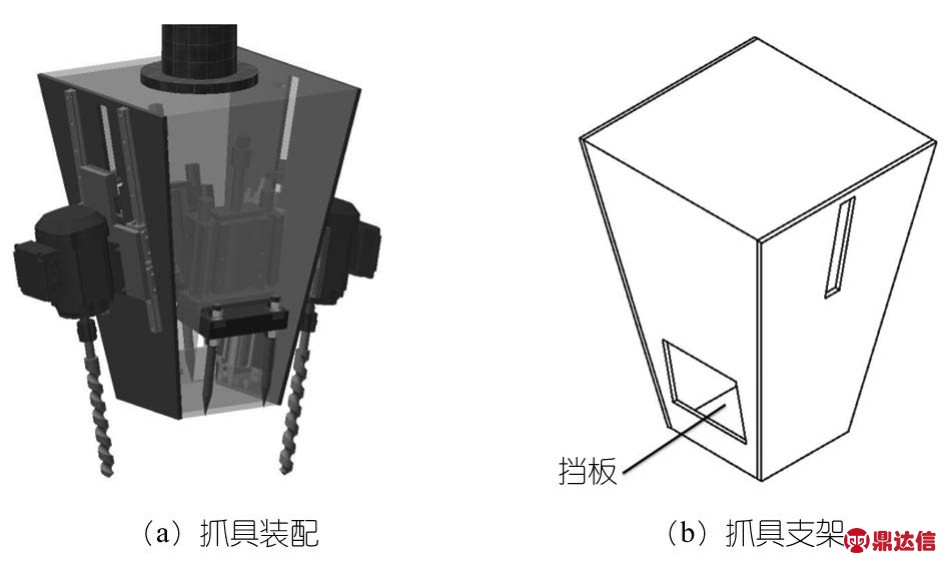
图5 机器人抓具支架结构图
5 小结
机器人自动搬胶系统采用复合式结构组合,主要由气缸带动钢叉和减速电机驱动螺杆对胶料进行抓取,能够快速辨识胶块种类与抓取位置,满足几何形状不规则等情况下的制品抓取搬运。机构结构简单,钢叉结构提升了对胶料的抓取效率;螺杆结构增大了其与胶料的摩擦系数,解决了硬质胶块抓取的难题。此搬胶系统可有效协助解决胶块粘连问题,使得抓取胶料时更加牢固、快捷方便,可有效降低劳动强度,提高工作效率。
参考文献:
[1]范仁德.中国橡胶工业2025的思考(下)[J].中国橡胶,2015,31(23):22~27.
[2]肖玥. 中国制造2025下我国轮胎制造业中小企业战略研究[D].北京外国语大学, 2017:1~5.
[3]杜品圣.德国智能工厂建设路径[J].中国工业评论, 2016(01):44~54.
[4]王化平,金丽,徐祖建,等. 一种取料、搬运、冲压、码垛一体化的机器人[P]. 湖北:CN108972591A, 2018-12-11.
[5]黎利华,陈超艳,钟亮.降低真空吸盘型机械手掉件故障策略探讨[J].物流技术, 2019,38(01):130~132+135.