随着煤制油技术的不断发展,对煤油泵等主要组件的要求越来越高.磨损是影响煤油泵工作稳定性和使用寿命的主要因素.硬质陶瓷相WC以其耐磨性高,热膨胀系数小,相对延展性好等特点被广泛应用于制备颗粒增强复合材料.已有研究表明,Ni基WC复合涂层能够有效提高试样表面硬度,增强表面耐磨性[1-5].但目前多采用机械外加WC颗粒与金属基自熔性合金粉末混合的方式制备颗粒增强复合涂层,制备过程中WC增强相容易发生烧毁、分解和失效等问题[6-7],从而影响硬质颗粒在涂层中的增强作用.
设计意图:教师借助立体模型和模式图进行新知识的教学后,利用抽象性更强的平面简图进行变式评价和总结。类比生活常识,利用启发式讲授,理清细胞核—遗传信息—生命活动的联系,分析核质之间的逻辑关系,落实重要概念:控制遗传代谢,再升华到结构功能观,使学生螺旋式掌握概念,实现发展核心素养的目标。
采用原位自生增强颗粒方法可以有效解决外加增强颗粒烧毁、分解及失效等问题,避免了外加颗粒造成的污染以及增强颗粒与基体界面发生化学反应的问题.此外,通过原位自生反应获得的增强颗粒与基体的相容性较好,能够与基体良好结合,而且增强颗粒与基体之间具有良好的热力学稳定性[8].因此,原位自生颗粒增强金属基复合材料受到广泛关注.张春华等[9]采用类激光熔覆技术在316不锈钢表面制备了Stellite合金沉积层,结果表明,合金涂层显著提高了基体的硬度和耐磨性.孙海勤等[10]利用激光熔覆技术在45#钢表面原位生成了VC颗粒增强Ni基复合涂层,结果表明,由于原位自生VC颗粒的生成及其均匀分布,复合涂层的平均硬度高达1 300 HV,且其耐磨性约为纯Ni60熔覆层的两倍.张艳梅等[11]通过在Ni基合金粉末中复合添加WO3、Al和石墨的方式,在激光熔覆过程中利用上述粉末之间的放热反应原位合成WxC颗粒增强Ni基复合材料涂层,对涂层的微观组织和相组成进行了分析,并对WxC陶瓷相的形成机理进行了探讨.孙国进等[12]利用熔铸技术原位合成了TiCP/Fe复合材料,并对其组织结构和力学性能进行了研究,通过正交试验法得出Ti、C和Si的最佳质量分数分别为6%、2.3%和1%.目前的研究均是采用激光熔覆和熔铸技术制备原位自生颗粒增强金属基复合涂层,但这两种方法存在设备昂贵和涂层易产生缩孔等不足.真空熔覆技术的真空环境可以避免有害气体的侵入,使得微观缺陷和开裂敏感性减小,制备的涂层可以提高零件的耐磨性、耐蚀性及耐热疲劳等性能[13].
本文采用真空熔覆技术并以含有W、C元素的Colmonoy88合金粉末为原料,在316L奥氏体不锈钢表面原位生成WxC颗粒增强Ni基复合涂层,并且对其组织形貌、硬度和摩擦磨损性能进行了系统研究.
1 材料及方法
试验材料为Colmonoy88自熔性粉末,平均晶粒度为50 μm,粉末成分为w(C)≤0.6%,w(Cr)≤15%,w(B)≤3%,w(Si)≤4%,w(Fe)≤3.5%,w(W)≤15.5%,余量为Ni.基体材料为316L奥氏体不锈钢圆盘,直径为55 mm,厚度分别为16、10和4 mm.利用真空熔覆工艺制备WxC颗粒增强Ni基复合涂层.利用60#、100#、240#、320#、400#和600#SiC金相砂纸打磨基体材料,随后利用超声波丙酮进行为时15 min的清洗,之后在基体表面进行喷砂处理,然后再次利用超声波丙酮进行清洗.
将合金粉末放入小型试罐中,以5∶1的质量比加入自制粘结剂并均匀搅拌.为了去除粉末膏剂中残留的空气与水分,对混合粉末膏剂进行抽真空处理.然后将处理后的粉末膏剂涂在经过喷砂处理后的基体表面,预制涂层厚度约为2 mm.将涂好膏剂的试样放入烘箱中烘干,烘干温度为80 ℃,烘干时间约为3 h.将烘干后的试样放到真空炉中进行真空熔覆处理,得到的加热温度曲线如图1所示.在具体试验过程中,0~1 h内升温到270 ℃,1~3 h内以90 ℃/h的升温速度加热至450 ℃并保温0.5 h,之后再以200 ℃/h的升温速度继续升温.这种升温方式可以保证预制涂层中的水分可以完全去除[14].当温度达到1 180 ℃后保温20 min,使得涂层内外温度均匀,涂层与基体内元素得到充分扩散.保温后随炉自然降温,当温度低于400 ℃时,关闭真空阀,当温度低于100 ℃时,从炉中取出试样并进行空冷.
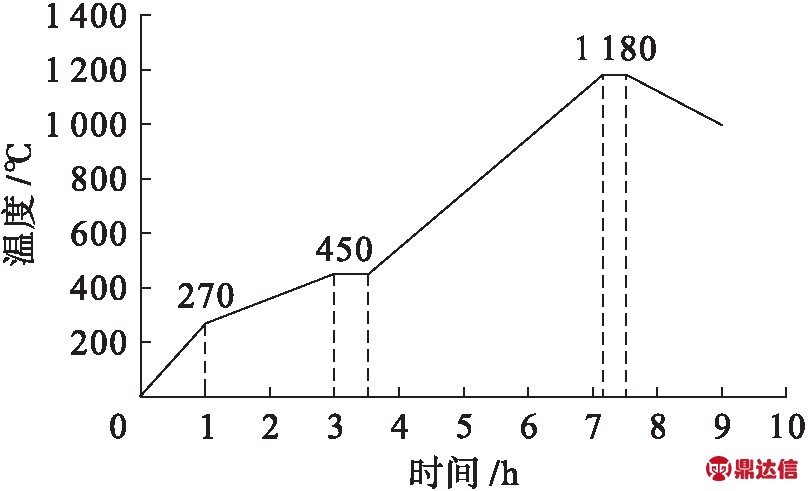
图1 真空熔覆加热温度曲线
Fig.1 Heating temperature curve in vacuum cladding
经过真空熔覆后的试样经线切割、镶嵌、打磨和抛光之后,利用金相显微镜及日立S-3400N型扫描电子显微镜(SEM)观察样品截面的组织形貌,并利用SEM自带的能谱分析仪(EDS)分析样品的微观结构和化学成分.采用XRD7000型X射线衍射仪对复合涂层进行相结构分析,具体试验中选用Cu靶,电压为40 kV,电流为30 mA,扫描速度为4°/min,扫描区间为20°~100°.采用HVS-1000型数显显微硬度计测量复合涂层的显微硬度,施加载荷为200 g,加载时间为10 s.采用MMU-5G型材料端面高温摩擦磨损试验机对复合涂层的摩擦磨损性能进行测试,试验形式为销盘磨损.下摩擦副选用Colmonoy88合金粉末等离子堆焊层圆盘,尺寸为φ 43 mm×3 mm.上摩擦副分别为Colmonoy88合金粉末真空熔覆层试样和316L不锈钢销棒,尺寸为φ 4 mm×15 mm.法向载荷为150 N,磨盘转速为150 r/min,磨损时间为20 min,磨痕直径为21 mm,磨损行程为200 m.利用扫描电子显微镜分析磨损后试样的磨痕形貌和磨损机制.
在互联网的大背景下,电子商务的发展除了依靠人才以及政府政策支持外,还需要有完善的配套设施,尤其需要有完善的物流体系。当前宿迁市政府为了促进电子商务的发展,在相关配套设施方面已经不断加大投入力度,但在物流体系层面还存在以下几个问题:
2 结果与分析
2.1 复合涂层组织形貌
图2为真空熔覆原位自生WxC增强Ni基复合涂层的组织形貌.由图2a可见,真空熔覆原位自生WxC增强Ni基复合涂层分为明显的三个区域:涂层(区域Ⅰ)、扩散区(区域Ⅱ)和基体(区域Ⅲ).复合涂层组织均匀致密,且无裂纹和气孔等缺陷,复合涂层厚度约为660 μm,基体熔深为300 μm,熔覆层稀释率为31.34%.在熔覆过程中Ni基合金颗粒之间的连接界面率先熔化,在Ni基颗粒之间形成烧结颈,随着温度的增加与保温处理的进行,烧结颈不断生长,逐渐将预制涂层中的原子间隙填充,孔隙率随着烧结颈的生长而降低.与此同时,材料中的合金元素在熔融状态下的涂层材料中充分扩散,在浓度梯度和重力作用下,涂层与基体材料之间发生了元素相互扩散,使得熔融状态下Ni基合金涂层与基材相互稀释、渗透,因此,在涂层与基材之间形成了明显的扩散层,扩散层组织细密,与涂层的接合处无缺陷,表明涂层与基材结合良好,有利于对基材表面性能进行改善.由图2b可见,深灰色基体上弥散分布着白色块状颗粒(区域A),基体与块状颗粒之间存在明显的灰色相(区域B).对不同颜色区域分别进行EDS检测,其EDS扫描结果如表1所示.由表1可见,区域A主要元素成分为W与Cr元素;区域B主要元素成分与区域A大致相同,但其W含量较区域A有所降低,而Cr、Fe、Ni三种元素含量则比区域A高.区域C主要元素为Cr元素,推测该处为Cr的碳化物.由图2c可见,复合涂层近界面处含有大量鱼骨状组织(区域D),经EDS分析可知,其主要元素成分为W.在真空熔覆过程中W与C原子结合生成WC晶核并开始长大,周围熔液依靠先形核的WC晶核与温度梯度作用以依附方式长大成为块状组织,随着周围熔液中W和C原子的减少,后形核的WC晶核只能依靠温度梯度与成分分布情况形成方向各异的鱼骨状组织.
降雨和径流可以在裸露的分散性土边坡引起严重侵蚀。侵蚀在边坡上导致严重的斜向滑移和冲沟,进而造成堤防内部缺陷[18]。主要破坏型式如图1所示。
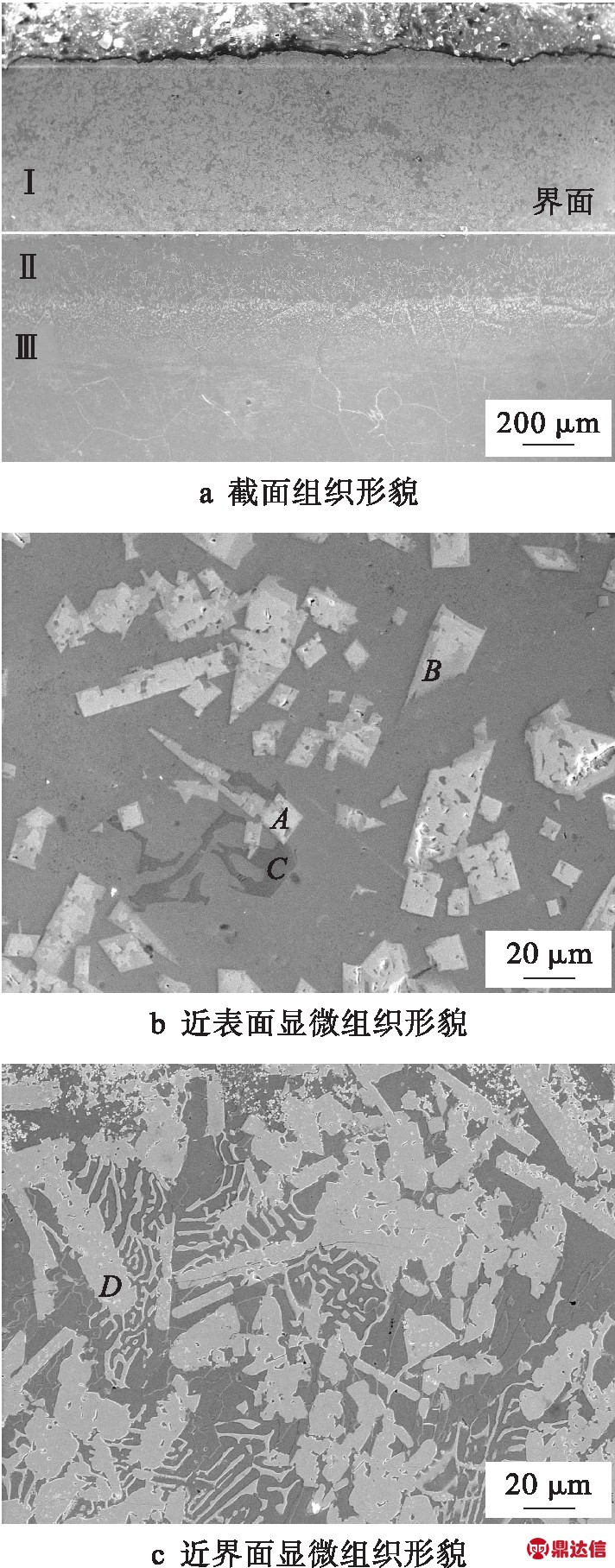
图2 复合涂层的组织形貌
Fig.2 Microstructural morphologies of composite coating
表1 不同区域EDS测定结果(w)
Tab.1 Test results of EDS in different areas (w) %
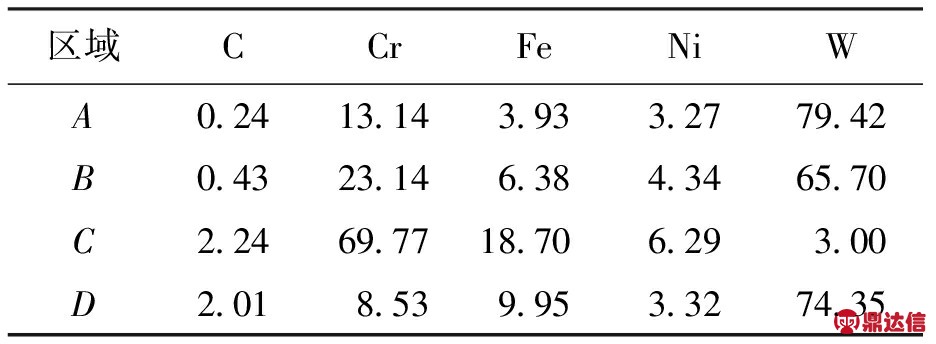
区域CCrFeNiWA0.2413.143.933.2779.42B0.4323.146.384.3465.70C2.2469.7718.706.293.00D2.018.539.953.3274.35
图3为真空熔覆原位自生WxC增强Ni基复合涂层的XRD图谱.由图3可知,复合涂层主要由γ-Ni、Cr7C3、(Cr,Fe)7C3、W2C、WC和Fe3W3C组成.结合图2和EDS扫描结果可知,白色块状组织为WxC相,且该相周围的灰色组织为(Cr,Fe)7C3和WxC共存的多相组织.
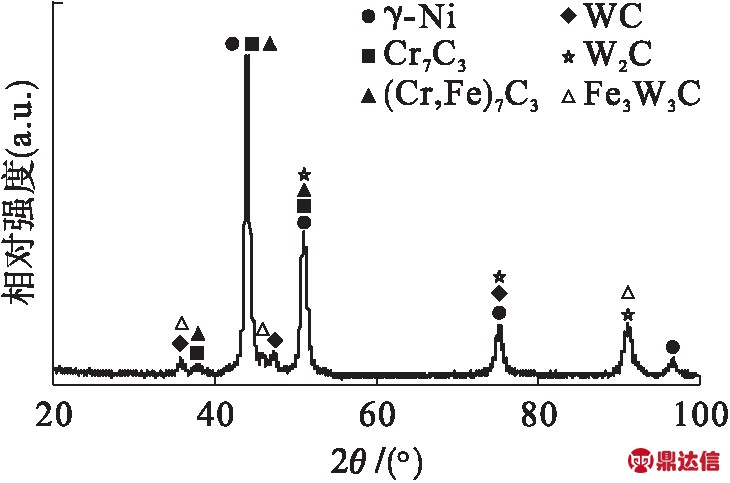
图3 复合涂层的XRD图谱
Fig.3 XRD spectra of composite coating
在真空熔覆过程中W原子可能会与C原子发生如下反应:
W+C=WC
2W+C=W2C
W2C+C=2WC
根据热力学原理,某反应物和产物的摩尔吉布斯自由能[15]计算表达式为
Gi,T=Hi,T-TSi,T
(1)
式中:Hi,T为摩尔焓;Si,T为摩尔熵;T为温度.摩尔焓、摩尔熵和摩尔定压热容可以分别表示为
Hi,T=Hi,298+Cpi,TdT
(2)
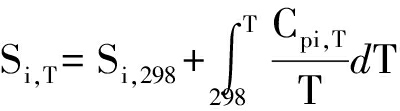
(3)
Cpi,T= ai+bi×10-3T+ci×105T-2+
di×10-6T 2
(4)
式中,ai、bi、ci、di均为相应常数.
吉布斯自由能变化量表达式为
ΔG=G生成物-G反应物
(5)
上述W与C原子发生反应的吉布斯自由能分别为-39.48、-58.12和-20.82 kJ/mol,因而在熔覆过程中三个反应都可能发生,并生成WC和W2C.Cr元素为强碳化物形成元素,在真空熔覆过程中游离的C与Cr原子结合,形成了稳定性较高的碳化物Cr7C3.因为Fe与Cr的原子半径和晶格常数相近,Cr7C3中的部分Cr原子很容易被Fe原子取代,从而形成复合碳化物(Cr,Fe)7C3[16].率先原位自生形成的硬质相可为后形成的硬质相晶核提供形核核心,促进其他硬质相的生成,并形成了(Cr,Fe)7C3和WxC共存的多相组织.
2.2 复合涂层硬度
图4为真空熔覆原位自生WxC增强Ni基复合涂层的显微硬度分布曲线.复合涂层平均硬度(1 086 HV)约为基体硬度的4倍.Cr在涂层中的均匀分布使其碳化物Cr7C3在复合涂层中亦呈均匀分布,且与涂层中的WC与W2C一起对Ni基合金涂层产生弥散强化作用.同时大量的WxC与Cr7C3等硬质相的存在,使得结晶过程中发生了优先依附于硬质相表面的异质形核,增加了涂层中的晶核数目,减少了晶核生长所需的溶质含量,抑制了晶核的生长,从而促使晶粒细化,并对复合涂层产生了晶界强化作用.由图4可见,硬度曲线中距涂层表面0.1~0.2 mm处出现了小段硬度上升趋势,随后硬度又缓慢下降,这是因为当熔融状态下的合金粉末内部元素发生扩散时,Cr、Ni、W、Si和Fe等具有较大原子半径的大密度原子在重力作用下向下扩散,但因为其扩散能力较弱,在涂层完全凝固之前只能进行短距离扩散,从而聚集在涂层中部,因此,涂层表面附近WC等硬质相含量较低.熔覆过程中元素的烧损和挥发导致表面硬质相含量进一步减少,随着距表面距离的增加,涂层中硬质相的含量增加,涂层硬度随之增大.基体中的Fe元素及复合涂层中的合金元素的相互扩散使得复合涂层中Cr、Ni、W等元素的相对含量降低,导致这些元素对复合涂层的固溶强化作用减弱,硬度降低,且越靠近基体涂层受Fe元素稀释影响越大,因此,复合涂层硬度呈先增大再减小的趋势.基体材料受元素扩散的影响,其靠近界面处的扩散层显微硬度会有所提高,且其硬度随与界面距离的增大而减小,这种硬度逐渐降低的扩散层可以在复合涂层与基体之间产生过渡作用,从而对复合涂层受到的冲击产生缓冲效果.
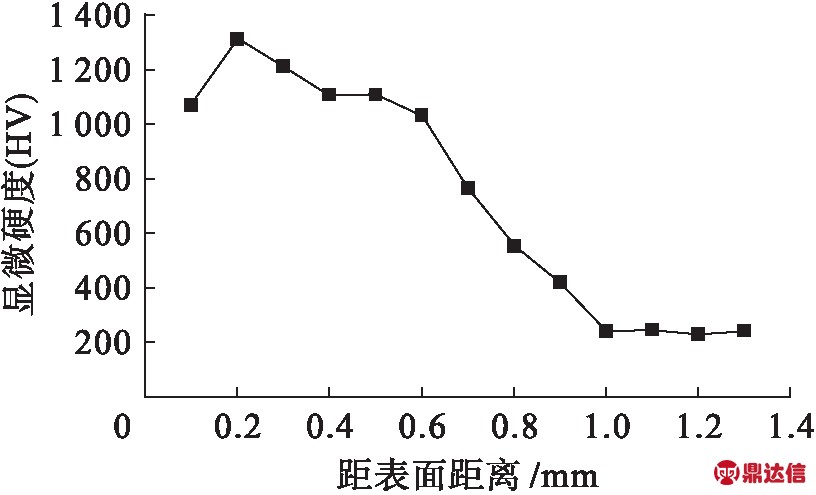
图4 复合涂层的显微硬度曲线
Fig.4 Microhardness curve of composite coating
2.3 复合涂层摩擦磨损性能
图5、6分别为316L不锈钢基材与真空熔覆原位自生WxC增强Ni基复合涂层的摩擦系数曲线和失重量.由图5可见,基材与复合涂层的起始摩擦系数大致相同,随后基材摩擦系数逐渐增大,且呈不规则波动,复合涂层的摩擦系数则在初始阶段的波动之后开始呈周期性波动,表明此时的磨损过程已经进入稳定阶段.经测量计算可知,316L不锈钢基材的质量损失为58.4 mg,平均摩擦系数为0.470 8.复合涂层的质量损失为1.596 mg,平均摩擦系数为0.374.
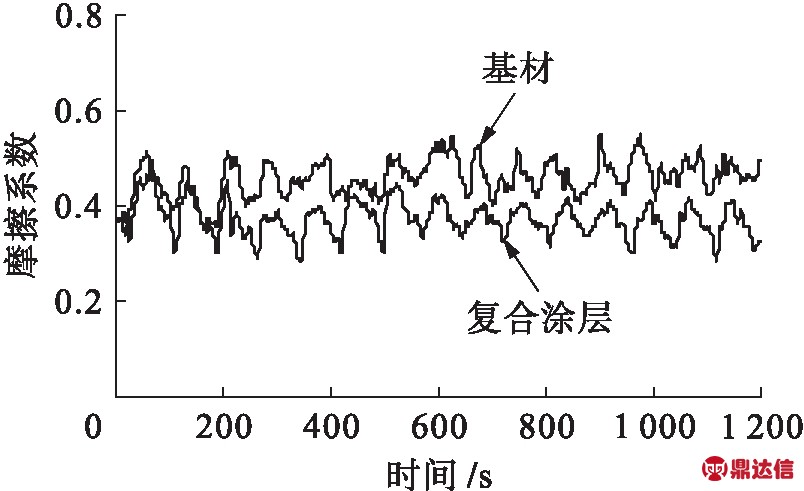
图5 基材与复合涂层的摩擦系数曲线
Fig.5 Friction coefficient curves of substrate and composite coating
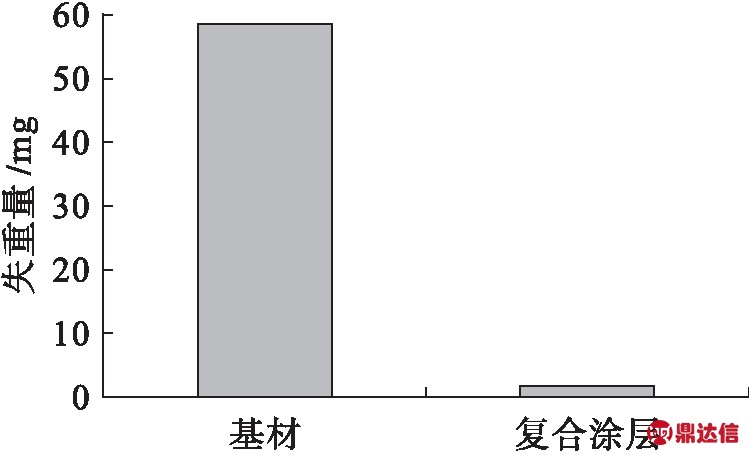
图6 基材与复合涂层的失重量
Fig.6 Mass loss of substrate and composite coating
真空熔覆复合涂层的相对耐磨性[17]计算公式为
只要愿意成长,班主任登上“巨人之肩”的途径有很多,但最便捷的方法是专业阅读。阅读不受时空的限制,在短时间内就可以获得系统的知识,将“巨人”的经验据为己有。所以,与其每天为班级突发事件疲于奔命,不如留一点时间进行专业阅读,站上“巨人之肩”,多一点预见,多一些方法,让管理更有成效。
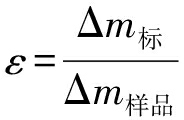
(6)
式中,Δm标和Δm样品分别为标准样品(基材)和试验样品的磨损失重量.相关计算结果表明,复合涂层相对耐磨性约为基材的37倍.
但是,以“酉鸡”与“卯兔”来解释日中的“金鸡”与月中的“玉兔”,却与人们在现实生活中的观察不符。因为鸡所属的“酉”时是傍晚的五时至七时,并无太阳,反而是月亮初升的时刻;而兔所属的“卯”时,则为早晨的五时至七时,也没有月亮,反而是太阳初升之时,明显与“日中有金鸡,乃酉之属;月中有玉兔,乃卯之属”的说法矛盾。于是,便又有试图以“镜像”的观念来解释东方的兔在西边的月中、而西方的鸡在东边的日中的现象者,如北宋人陆佃在其《埤雅》中说:
图7为316L不锈钢基材与真空熔覆原位自生WxC增强Ni基复合涂层的磨痕形貌.摩擦磨损过程中材料的损耗主要有微观切削、塑性变形和硬质相颗粒剥落三种形式,其中硬质相颗粒剥落被普遍认为是材料损耗的主要因素[18].由图7a可见,基材表面具有明显的塑性变形,主要磨损机制为磨粒磨损和氧化磨损.在压应力和切应力共同作用下,316L不锈钢基材易发生塑性变形,且随着摩擦磨损时间的增加而愈发严重,导致涂层部分表面脱落成为磨粒,并对摩擦表面进行切削,从而形成犁沟槽.复合涂层的Ni基合金基体主要起支撑和粘结硬质相的作用,Ni基合金基体在摩擦磨损过程中被逐渐损耗,导致WxC、Cr7C3等硬质相裸露在基体表面(见图7b),从而产生抗磨作用.复合涂层的主要磨损机制为磨粒磨损.(Cr,Fe)7C3具有较高的硬度(1 300~1 600 HV)和强韧性,因此,原位自生形成的(Cr,Fe)7C3界面相可以对WxC起到比基体更好的固定效果.原位自生硬质相与Ni基合金基体之间发生了元素扩散,两者相互润湿,可以有效提高界面相(Cr,Fe)7C3与基体的结合力,使得硬质相颗粒在磨损过程中不易剥落,从而有利于减小复合涂层的磨损率.裸露在涂层表面的硬质相在摩擦磨损过程中可以抵御外来的坚硬磨料嵌入基体,并与磨粒相互碰撞挤压,使得磨粒的尖锐角被磨平甚至使其破碎,从而导致磨粒切削能力降低,进而提高复合涂层的耐磨性.WxC、Cr7C3和(Cr,Fe)7C3等硬质相在涂层内的弥散分布增大了复合涂层的硬度,可以减少磨损过程中Ni基体的损耗,有利于防止硬质相颗粒发生剥落.
“4G全网建设技术”大赛的比赛内容更新及时,引领教学内容的及时更新,例如:2015年比的是4G全网的组建、网络规划、设备配置、数据配置、业务调试及故障排除等。2016年有理论考试、4G网络配置与优化、4G网络故障排除3部分。其中,4G网络配置与优化部分考核了无线接入网、核心网及承载网等知识点,要求参赛学生基于要求对网络数据进行容量计算、设备部署、数据配置完善及网络性能优化,最终实现4G业务的开通[2]。职业技能大赛赛项大规模纳入通信行业最新技术,导致职业院校通信专业必须对教学内容不断调整,以紧跟通信技术的发展步伐。
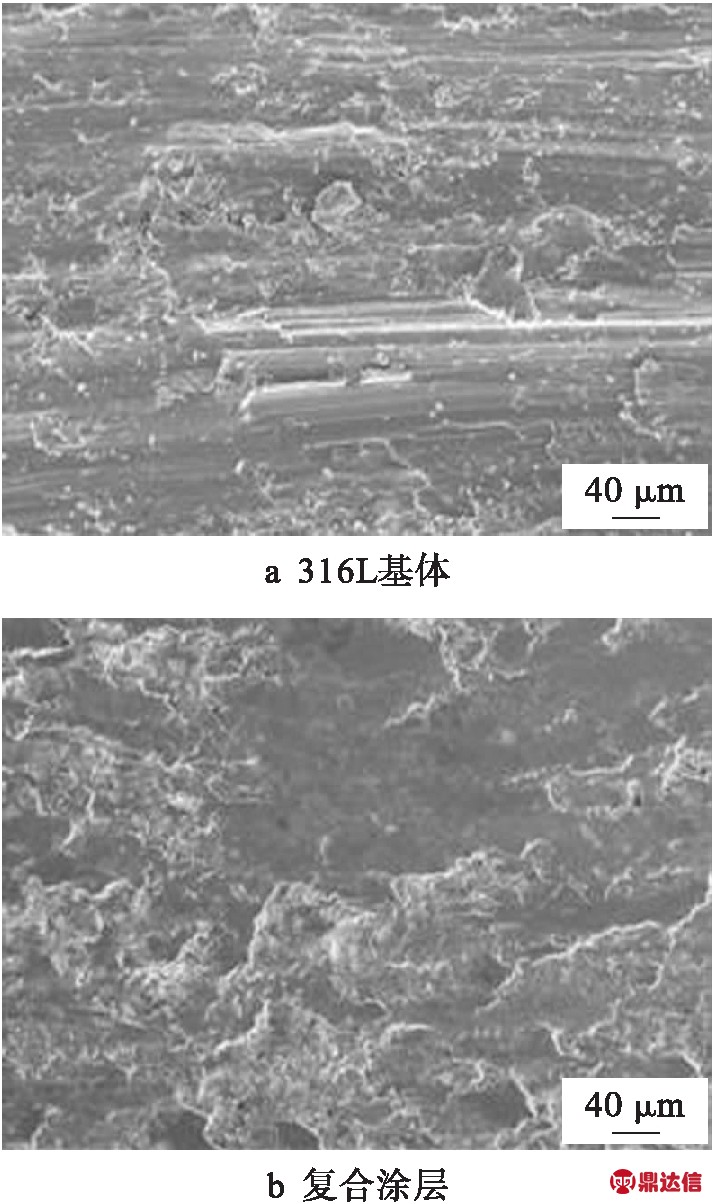
图7 基材与复合涂层的磨痕形貌
Fig.7 Morphologies of abrasion traces of substrate and composite coating
3 结 论
通过以上试验分析可以得到如下结论:
1) 利用真空熔覆工艺可在316L不锈钢表面制备原位自生WxC增强Ni基合金复合涂层.复合涂层组织均匀致密,且无气孔等缺陷.
2) 真空熔覆原位自生WxC增强Ni基复合涂层主要相结构包括γ-Ni、Cr7C3、(Cr,Fe)7C3、W2C和WC.W2C和WC相以块状形貌弥散分布在基体上,(Cr,Fe)7C3相主要以界面相存在于涂层中.
3) 真空熔覆原位自生WxC增强Ni基复合涂层的平均硬度为1 086 HV,且约为基材硬度的4倍.与基体材料相比,复合涂层的相对耐磨性约为基体材料的37倍,可见,在316L不锈钢表面真空熔覆Ni基涂层后可显著改善其耐磨性.
帕利塔纳的许多居民不希望任何形式的杀戮发生在这个圣地。2014年,200位耆那教僧人以绝食表达全面素食的信念,直至8月10日,他们完成了这个心愿。
4) 真空熔覆原位自生WxC增强Ni基涂层的磨损机制主要为磨粒磨损,316L不锈钢的主要磨损机制为磨粒磨损与氧化磨损.