薄壁平面件(径厚比大于50或壁厚小于等于2 mm),特别是精密物理实验超精密零件,具有刚度低、壁厚小(大于0.1 mm,小于2 mm)等特点。卡盘或卡爪等在装夹中存在限制,易产生严重的装夹变形,从而影响工件加工质量[1-3]。对于高压微喷、爆轰性能检测等精密物理实验所需超精密薄壁平面件,装夹变形引起的形位偏差将直接影响实验效果[4-5]。
为了克服薄壁类零部件装夹过程的难点,多数情况下,需根据零部件形貌尺寸并结合制造工艺路线,进行特定工装的开发,通用性较低[6-8]。其中,最常用的是采用数值仿真模拟薄壁类零部件的装夹状态并规划装夹工艺流程,然后根据仿真结果研发相应工装[9-11]。早期King等基于工装的刚体化,利用非线性技术优化工件装夹定位布局[12]。针对薄壁件加工的特定区域定位误差及变形,王少锋等提出了一种跟随加工区域布置定位点的定位新方法,为支承和定位点布局全局优化提供优化初值[13]。为避免传统机械工装在装夹时引入较大装夹变形,真空吸附技术已经在小型或规则形状薄壁零部件装夹中开始较大范围应用[14-16]。此外,刘春青等提出了一种确定薄壁件在多点柔性定位时参数选择和吸附压力的寻优算法,以实现最优选择[17]。
上述各方法基于弹性力学均提出了优化算法或模型,明确了局部以及特定设计变量。但是,对于超精密加工薄壁平面件真空吸附装夹过程,仍需进一步分析在任一瞬时切削力(在一个切削点处)作用下的变形,并将吸具研制、零件材料及切削力状态纳入整体考虑。本文结合材料力学与有限元法,建立真空平面多孔吸具的优化设计方法,才能更全面建立整个表面的变形加工误差控制模型。
1 薄壁平面件吸附装夹受力分析
1.1 平面件静止受力状态
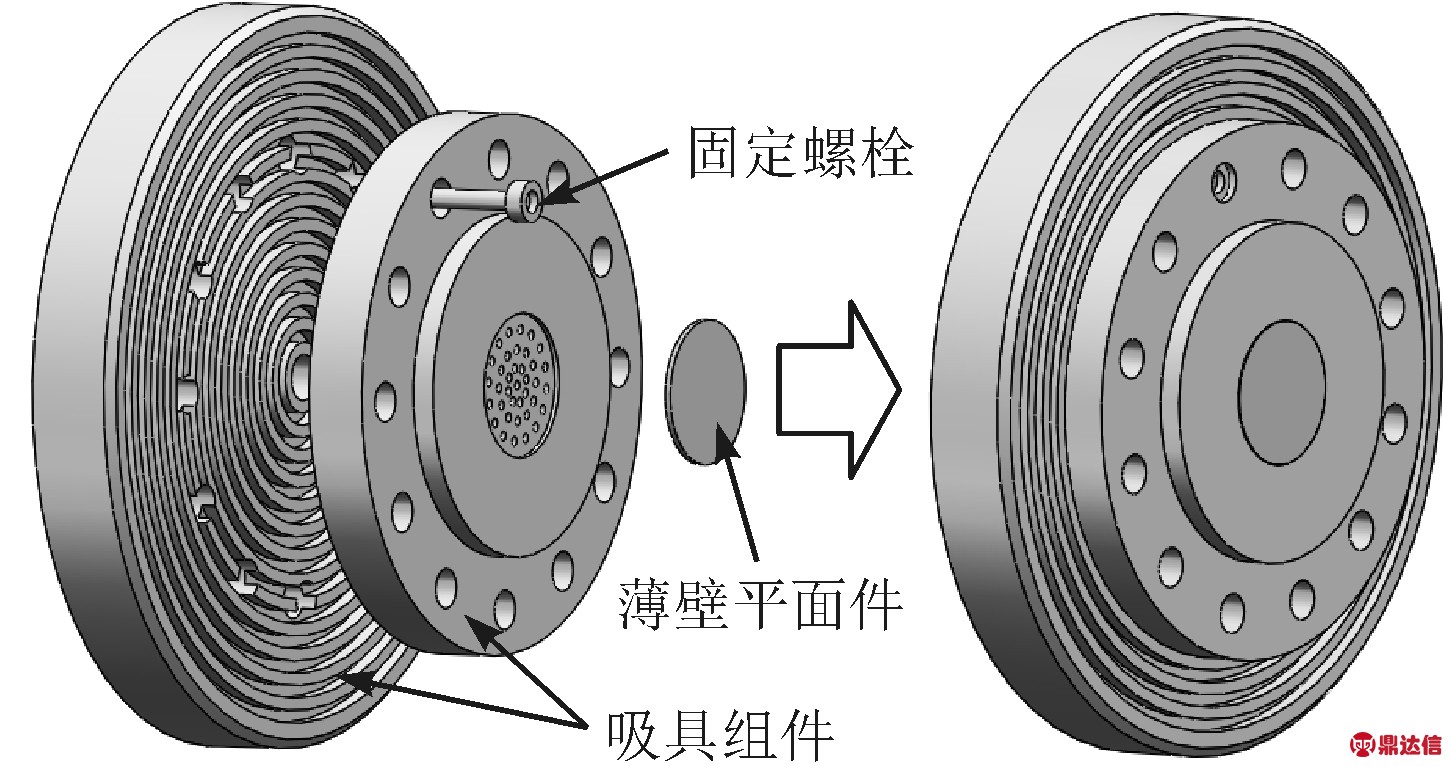
图1 多孔平面真空吸附装夹状态
加工前,将薄壁平面件采用真空多孔平面吸附方式装夹于吸盘,装配过程及装夹状态如图1所示。薄壁平面件吸附于吸盘平面后,在吸孔区域的受力状态如图2所示。

q为真空度,即大气压强P1和真空负压P2的差值,q=P1-P2;
δ为工件受压变形后的挠度;t为工件厚度;
r为真空吸孔半径;R为薄壁件半径
图2 平面件受力分布状态
由图2可知,平面件内接触面受到负压P2,待加工面受到空气压强P1。平面件可等效为圆周简支平面圆板模型。根据轴对称载荷圆周简支平板变形理论[18],可得出均布载荷作用下的平面件吸孔区域的静态变形挠度方程为
由此能看出,对于新生儿坏死性在小肠结肠炎者,使用腹部B超进行检查,能取得良好效果,其在检出门静脉积气以及肠壁积气的概率更高,因此值得进一步在临床中推广使用。

(1)
式中:rx为孔中心到计算点的径向距离;μ为材料泊松比;D′为平面件等效抗弯刚度,公式为
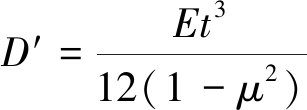
(2)
其中E为材料弹性模量。
All authors declared that there are no con flicts of interest.
而在氧化石墨烯样品的制备当中,则可以通过进行PH值的区分且使用超声分散法进行石墨烯样品的制备。以此为基础的氧化石墨烯湿敏原件制备的过程当中,需要选择氧化铝作为基片进行制备,在氧化铝基片两端进行温银浆的涂抹,将其置于150摄氏度的环境下进行干燥,在600摄氏度的环境下进行热处理,以此方式重复进行两次,最后将石墨烯分散液滴至去基片当中,滴至的过程中保证其电极接通,同样重复上述步骤五次,其得到的氧化石墨烯湿敏原件数量为五份[3]。
头盔结构部位如图1所示。帽体则采用了EPP是发泡聚丙烯的缩写(Expanded polypropylene),是一种新型泡沫塑料的简称。EPP以其独特而优越的性能成为目前增长最快的环保新型抗压缓冲隔热材料。响应“可持续性发展”的理念,由于EPS自身很好的抗老化,抗腐蚀的特性,几乎不会自然分解,由此造成了极大的环境污染,对我们生存的空间造成了巨大的挑战,因此放弃了传统的的EPS材料。而EPP材料对人体无毒且没有气味,可100%循环使用且性能几乎毫不降低,是实在的新型环保泡沫塑料。
如图2所示,薄壁平面件在吸孔处发生径向和轴向变形,并产生径向和轴向应力,分别为
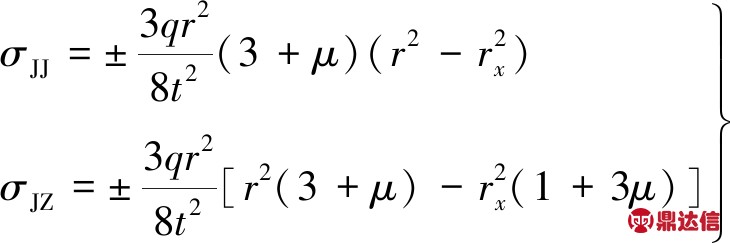
(3)
上述各式即可表征薄壁平面件加工前初始吸附固定后的静力学状态。
1.2 平面件切削受力状态
薄壁平面件采用单点金刚石超精密车床进行横车加工。在超精密切削条件下,进给量f远大于切削深度ap,因此可用典型单点金刚石切削模型来研究切削过程[19]。切削过程存在3个切削分力,即主切削力Fc、切深抗力Fp与进给力Ff,如图3所示。
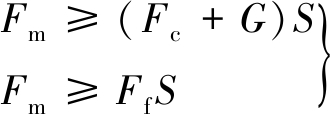
图3 横向车削及切削力状态
由于超精密加工时的切深抗力Fp在切削合力中占较大比例,因此切深抗力Fp对薄壁平面件的变形影响不可忽略[20]。根据经验公式,可得出单点金刚石恒线速车削6061铝合金的Fc、Ff与Fp的计算公式为[21-22]
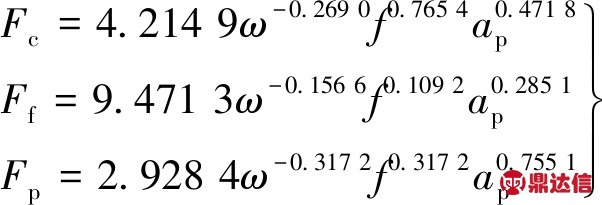
(4)
式中:ω为主轴转速,r/min;f为进给量,mm/s;ap为切削深度,μm;Fp取最大比率0.7进行验证计算。
刀尖产生的切深抗力Fp作为集中力引起的变形可采用直角三角形进行拟合,得出吸孔刀尖切削区域的动态变形挠度为[23]
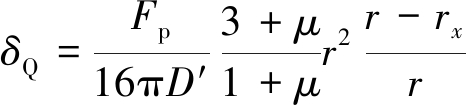
(5)
由此可知切削力最大处在平面件边缘位置。同理,切深抗力Fp作用于吸孔中心时,切削过程也产生径向应力σQJ和轴向应力σQZ,表达式分别为
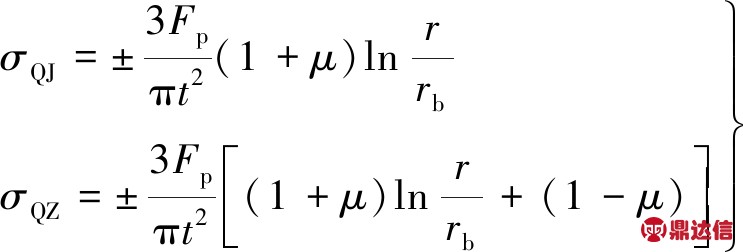
(6)
式中:rb为最大应力位置距真空吸孔边缘的距离,值为
rb=r-b
(7)
其中b为刀尖与工件接触半径,μm。根据超精密车削微观表面形成机理[24],刀尖与工件接触半径b的理论值为

(8)
式中:rD为刀尖圆弧半径,μm。
式(1)~式(8)即可表征薄壁平面件真空平面吸附装夹的切削及非切削时的受力变形状态。
2 吸附装夹与切削稳定性
对于半径为R的吸附平面,在表面加工半径为r的真空吸孔,令径向各孔圆心位置距离为s1,同一径向位置上相邻两孔的距离为s2,如图4所示。
总之,推进民生水利深入发展,重在深化认识,重在不断实践。应将民生理念贯穿于水利建设、管理、改革各个方面,体现在政策制定、工作部署、项目安排、业绩考核等各项工作中,把民生水利发展成效作为水利贯彻群众路线的重要标准,努力开创民生水利发展新局面。
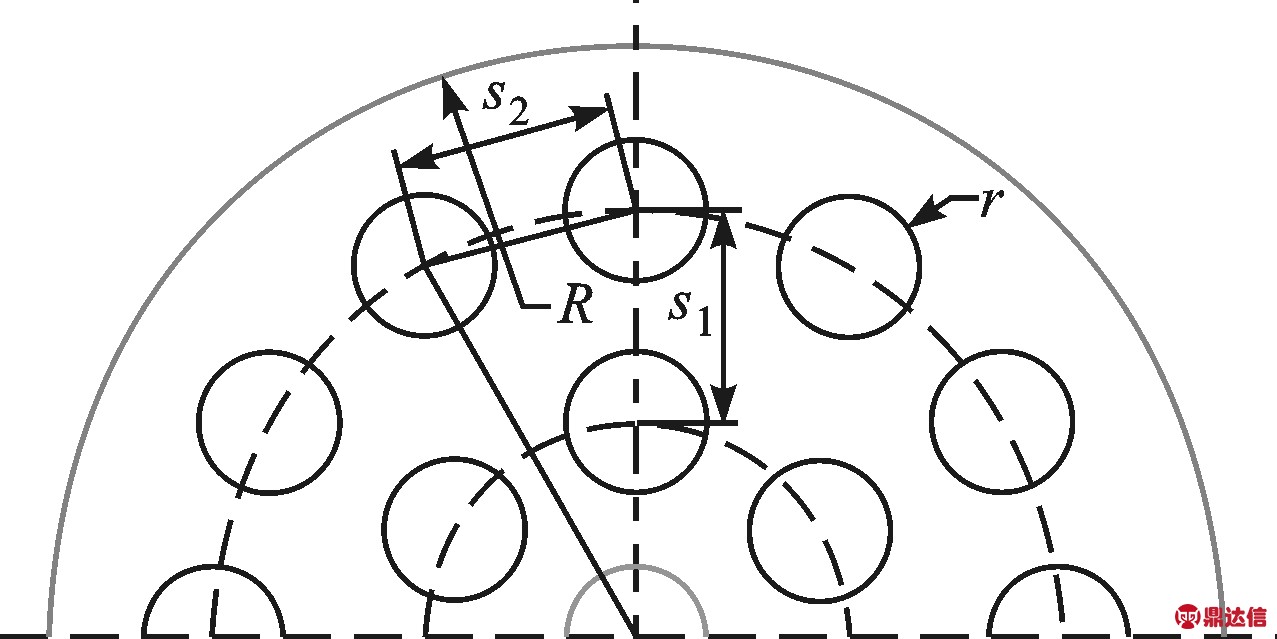
图4 圆平面吸孔位置布局
图4所示的尺寸与几何参数与圆平面内可加工的吸孔圈数n之间的关系为
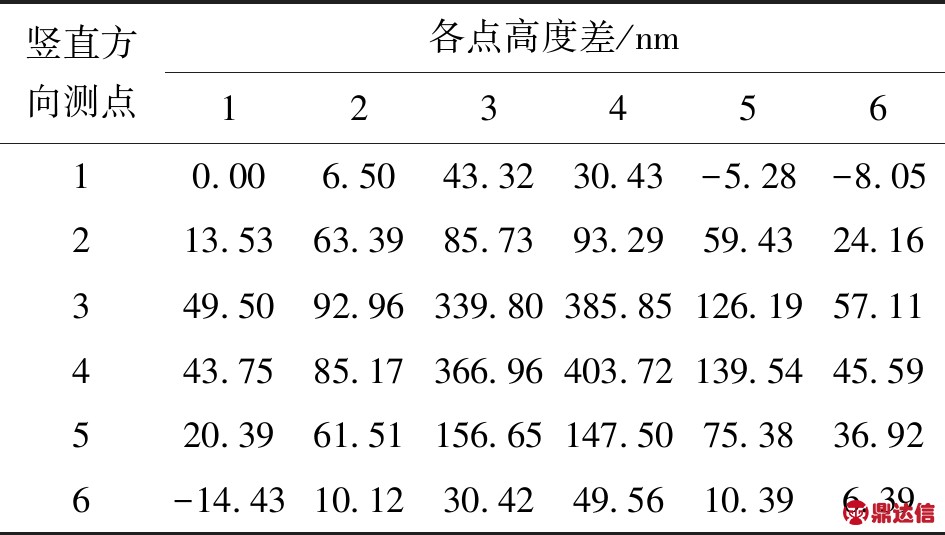
(9)
式中:n=1,2,3,…。当n=1时,仅存在一个中心吸孔;使式(9)成立的n的最大正整数即为圆平面可加工的最大吸孔圈数。
在360°圆周范围内,第i圈能够加工的均匀分布的最大吸孔数mimax,可根据圆心角弦长公式得出
如今的宜章茶叶生产基本实现了由传统的手工加工向机械加工的转变,茶叶产品品质和效益得到大幅提高。木森森茶业、标明合作社两家茶业龙头企业先后获得有机食品认证,并通过了QS认证;莽山仙峰有机茶业有限公司已获得绿色食品认证;宜章县莽山标明茶叶种植专业合作社的“宜章莽山茶”,入选了《2015年度全国名特产优新农产品目录》;瑶益春的“莽山绿茶”和木森森的“过山瑶绿茶”入选了《2017年度全国名特优新农产品目录》。

(10)
由式(9)(10),可得平面上可加工的吸孔总数为
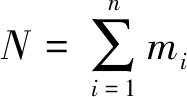
(11)
式中:mi是第i圈实际加工吸孔数。加工后的圆平面与工件表面接触时,实际接触总面积为
A=πR2-πr2N
(12)
接触区域受到的实际接触压强为
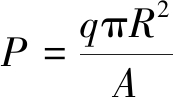
(13)
已知薄壁平面件保持平衡的充要条件是任意瞬时所受力及力矩均平衡,数学表达[25]为
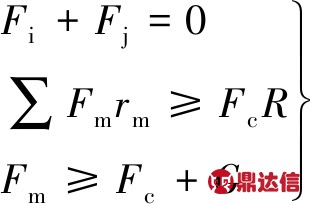
(14)
式中:Fi为支撑力;Fj为大气压力;Fm为径向静摩擦力;rm为任意点距工件中心轴距离。
2.1 切削状态装夹稳定性
(1)在明确切削周向稳定性条件之前,需要明确平面件周向所受力及力矩作用。吸孔区域微圆弧静摩擦力矩计算区域见图5。
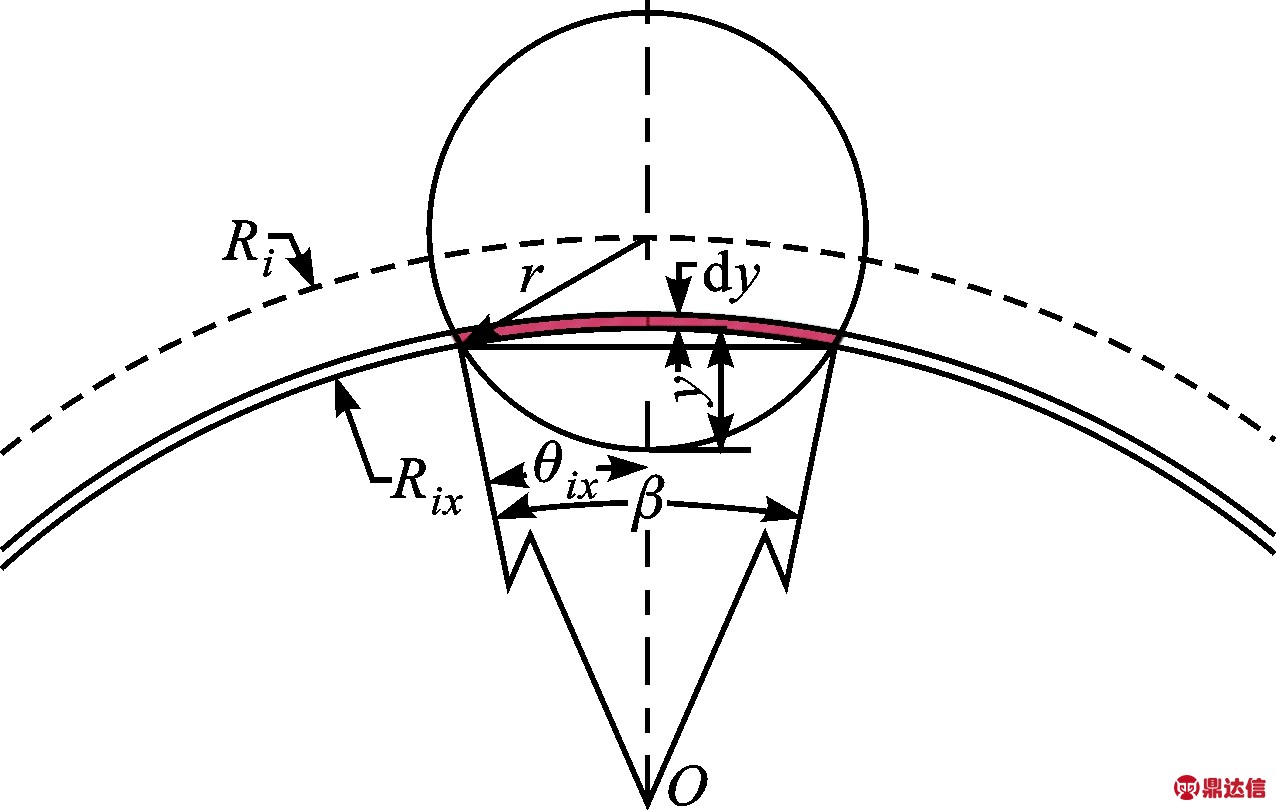
Ri为第i圈吸孔圆心所在虚拟圆半径;Rix为以圆平面圆心在径向
距离吸孔y处的虚拟圆半径;β为微圆弧段所对应的圆心角
图5 吸孔区域微圆弧静摩擦力矩计算区域
由图5可知,y方向dy所属微圆弧段部分的面积为
dA0=Rixβdy
(15)
该微圆弧一圈的实际接触面积为
dAi=2πRixdy-miRixβdy
(16)
在均布压强P,则任微圆实际接触面积dAi所产生的摩擦力矩为
dLifm=dAiPRixη
(17)
式中:η为铝合金之间摩擦系数。第i圈吸孔所在圆环区域产生的摩擦力矩为
Lifm=dAiPRixη
(18)
所有吸孔在区域产生的总摩擦力矩为
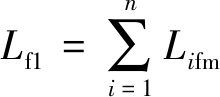
(19)
可得工件实际接触区域的总摩擦力矩为


(20)
相邻吸孔圈之间的区域如图6所示。该类区域需区分内圆环面与单一吸孔及最外圈吸孔的外围部分,即2≤i≤n-1与i=1或n两种情况。
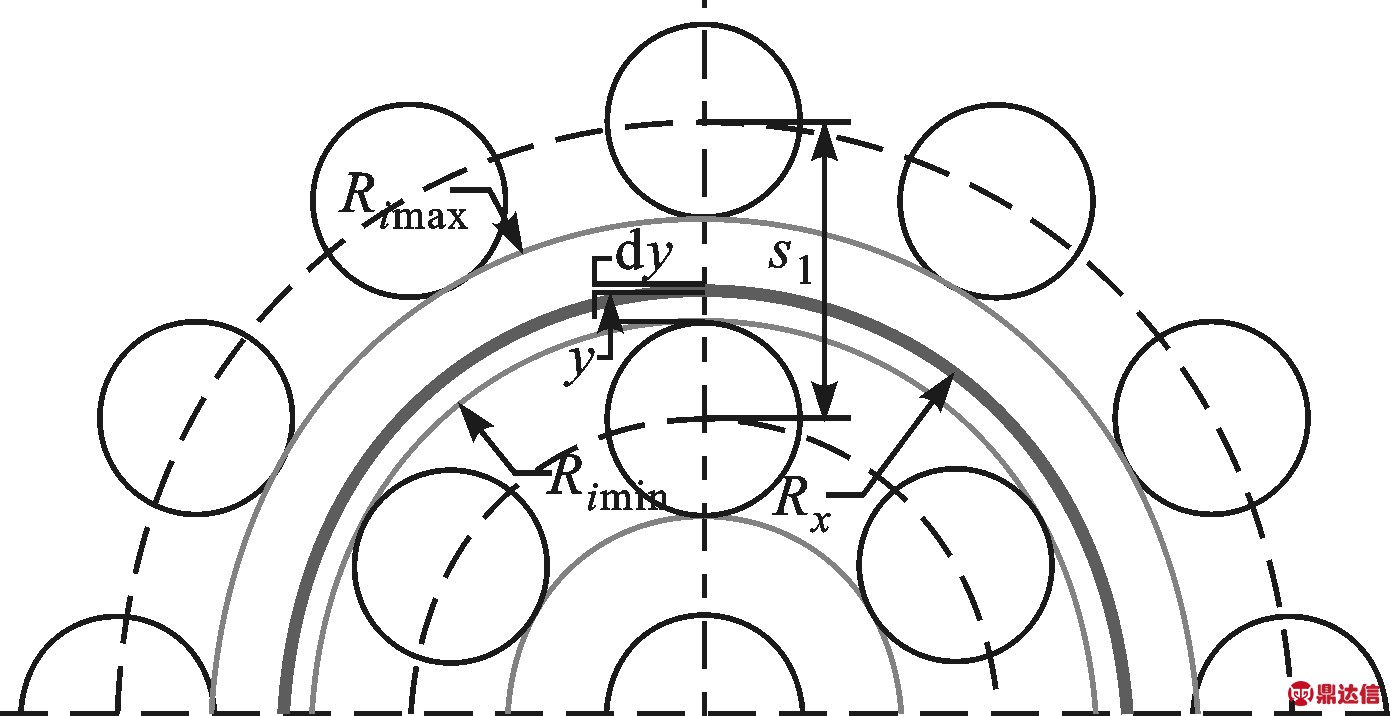
Rimin为第i圈的最小半径值;Rimax为第i圈的最大半径值;
Rx为环接触区域中y处的半径
图6 圆环接触静摩擦力矩计算区域
计算得到圆环接触面的总静摩擦力矩为
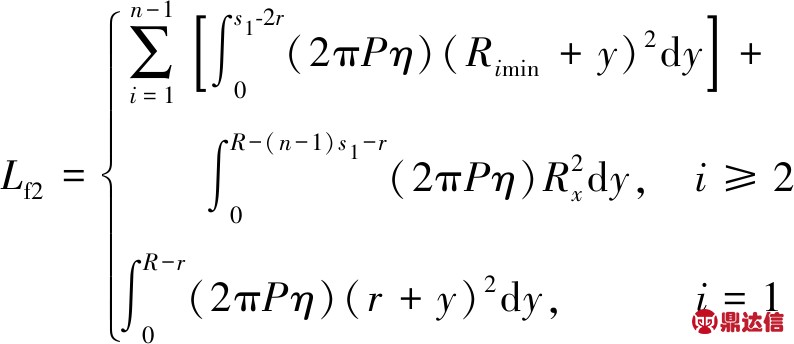
(21)
又知周向产生的总摩擦力矩Lf由吸孔所在圆环带的实际接触面积产生的总摩擦力矩Lf1与圆环接触面的总摩擦力矩Lf2之和组成,即
Lf=Lf1+Lf2
(22)
由图3及式(14)可知,工件保持周向稳定需要保证实际接触面产生的静摩擦力矩Lf与工件周向所受到的外作用力矩平衡,即需要满足条件为
Lf≥FcRS
(23)
式中:S为吸附稳定系数,取值为2。
(2)工件所受径向力有主切削力Fc、重力G、静摩擦力Fm以及进给力Ff。加工过程需要保持竖直径向与水平径向的力平衡,根据式(14),有
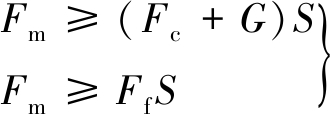
(24)
由式(24)便可判定薄壁平面件的径向稳定性。其中,静摩擦力Fm为
Fm=PAη
(25)
根据式(23)~式(25),获得使用真空度的验证条件为

(26)
式中:f-1(Lf)和f-1(Fm)分别为式(24)和式(25)中真空度q的反函数。
2.2 设计目标函数及其约束条件
薄壁件装夹状态与真空吸具的孔径r、真空度q二者有关。因此,以最小切削深度apmin等效为平面度要求δP、平面件厚度t为前置设计变量,真空度q为过程设计变量,设计过程如下。
由于磁盘和非易失存储器(Non-Volatile Memory,NVM)的存储介质不同,数据存储在不同介质上的性能差异较大,所以针对此问题我们设计了相应的数据部署方案。假设所有的数据原本均存储在磁盘中,设定初始数据块的标签表示Label=N,并且以读写、冷热和生存周期标签为迁移标准。
(1)由式(1),可得吸孔半径r设计目标函数为
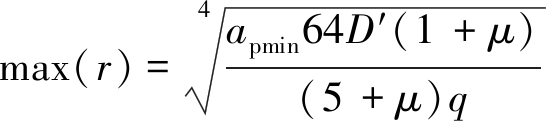
(27)
对于任意真空度q,r的设计约束条件为
r≤max(r)
(28)
(2)预设s1与s2确定平面吸孔数量。
(3)根据式(26)验证可使用真空度若不满足式(26),重新预设吸孔半径r。
(4)变形约束条件:超精密加工切削深度最小值apmin与加工后平面度限制δP比较,取二者最小值。因此,加工前静态吸附变形δJ限制条件为
δJmax≤min(apmin,δP)
(29)
(5)加工应力约束条件:在切深抗力Fp与均布载荷q的双重作用下,为了防止加工中轴向应力引起吸孔区域的轴向塑性变形,加工过程的动态应力最大值σmax的约束条件为
由于民办院校的办学性质,多数教师处于不坐班状态,教师在完成自己的本职教学工作后便会离校,回家备课、研究学术、做项目、写论文,只能通过书本知识和自身教学实践经验来提高自己的教学水平和学术水平。在这种情况下,即使教师付出再多的努力来提高自己,但效果还是不明显。对于青年教师来说,如果仅依靠个人的努力和传统的方法,即使工作热情高、时间充裕、积极性高、毕业学历高,也不能快速有效地提升教学能力和专业水平。
σmax=max(σJZ+σQZ)≤σe
(30)
其中6061铝合金在温度为240°时的弹性极限σe=240 MPa[26]。根据式(30)验证并限制其切削状态下的装夹与加工应力,以控制工件外形精度。
水行政管理亮点纷呈。政策法规建设取得重大突破。新修订的西藏自治区关于水法、水土保持法实施办法,首次明确水电站征收水资源费,涉水工程实行规划同意书制度,水土保持工作纳入政府目标考核体系。最严格水资源管理制度在雪域大地生根落户,地(市)用水总量红线已经划定正待审批。工业采矿、矿泉水生产、水电站等重点项目水资源论证形成常态化。水行政执法力度不断加大,违法开采地下水企业自备井依法封填,违法采砂活动及时得到整顿,依法办理取水许可的意识明显增强。
综上,式(27)~式(30)构成了真空多孔吸具吸孔孔径2r、真空度q的共同设计准则与验证方法。
为了验证本文方法的可行性,选取肤色,发色各异的人脸图像2000张,经过数据预处理后,放入到T-GAN模型中进行测试翻译。部分实验结果如图3所示,可以看出,本文算法在输入的各种肤色和发色手绘人脸图像上,根据人脸的特殊性,引入相应的文本描述,翻译结果能够达到一个较好的效果,接近真实图像,与文本描述内容也比较接近。
3 吸具优化设计
前置设计变量及工艺参数:薄壁平面件材料为6061铝合金,泊松比μ=0.33,弹性模量E=68 GPa,半径R=25 mm,坯件厚度t=2 mm;吸具材料为2A12铝合金;铝合金之间的摩擦系数η=0.22;切削深度ap=(1~10) μm;进给量f=(5~20) mm/min;恒线速走刀,主轴初始转速ω=5 000 r/min,最大转速15 000 r/min;加工后表面平面度δP≤1 μm。
优化设计步骤如下。
(1)根据实际操作规程,真空度q的实际可调范围是(0.001~0.1) MPa。由式(28),可得apmin条件下,当真空度分别为0.1 MPa和0.001 MPa时,吸孔最大可选半径rq0.1=7.984 mm和rq0.001=25.246 mm。根据式(28),可得吸孔半径优化设计范围,即
3.1.1 心理护理 临床中腹腔镜技术越来越成熟,可是仍然有不少患者对其不了解,容易有恐惧和焦虑的情绪。术前护理人员告知患者手术的特点和优点,让患者能够建立信心。
r≤min(rq0.1,rq0.001)
因此,可预设吸孔孔径r=1 mm。
(2)根据图6,初设s1=4 mm,s2=4 mm,可得平面内吸孔总圈数n=6,各圈分别可加工的最大吸孔数分别为1、6、12、18、25、31。数控编程优化后,各圈加工吸孔数mi=1,8,12,16,21,24。
(3)由式(4),可得各切削分力的理论最大值Fcmax=0.545 N,Ffmax=4.267 N,Fpmax=0.789 N。
(4)将上述理论值带入式(30)及式(28),验证动态应力最大值σmax的约束条件,可得
σmax=(0.32×10-6q+0.55)≪σe
由结果可知,切深抗力和均布载荷引起的轴向动态应力小于弹性极限,变形属于弹性应变。考虑真空度控制范围,可以认为上述判定合理。
式(13)中:T0y为沿箱梁高度方向分布的温度差,单位:℃;T0x为沿箱梁宽度方向分布的温度差,单位:℃;y,x为受热面和计算点之间的实际距离,单位:m;Cx、Cy均为指数系数,根据具体的结构类型与所在部位,结合计算时刻等因素选定。
(5)根据预设加工吸孔尺寸和吸孔数量以及式(23)(24)(26),分别验证周向及径向稳定性,可得真空度q的控制下限qmin=0.0198 MPa,由此可预设真空度q的控制值为q=0.03 MPa。
(6)通过有限元验证工件装夹变形。薄壁件与真空吸具均采用C3D10(六面体)三维应力实体单元,且吸具简化为刚体。负压均布载荷q作用下的状态以及真空吸附加载后的仿真变形效果分别如图7和图8所示。
20世纪80年代初,安吉县开展了落实山林承包责任制工作,至1985年全县80%以上集体竹林已联产承包到户,涉及6万余户农户,自此以家庭承包经营为主体的竹林经营模式在安吉确立。本世纪初,安吉第二、第三产业进入高速发展阶段,2004年全县一二三产占比分别为12.7∶52.8∶34.5,农村社会结构发生显著变化,传统家庭竹林经营体制开始松动,大户承包、委托代管、公司经营等新型竹林经营主体不断涌现。2004年,浙江省出台了《浙江省农民专业合作社条例》,在顺应时代和行政推动下,毛竹农民合作社在安吉应运而生、不断发展,截至2017年12月,安吉县登记核准毛竹合作社80家,其中股份制合作社21家。
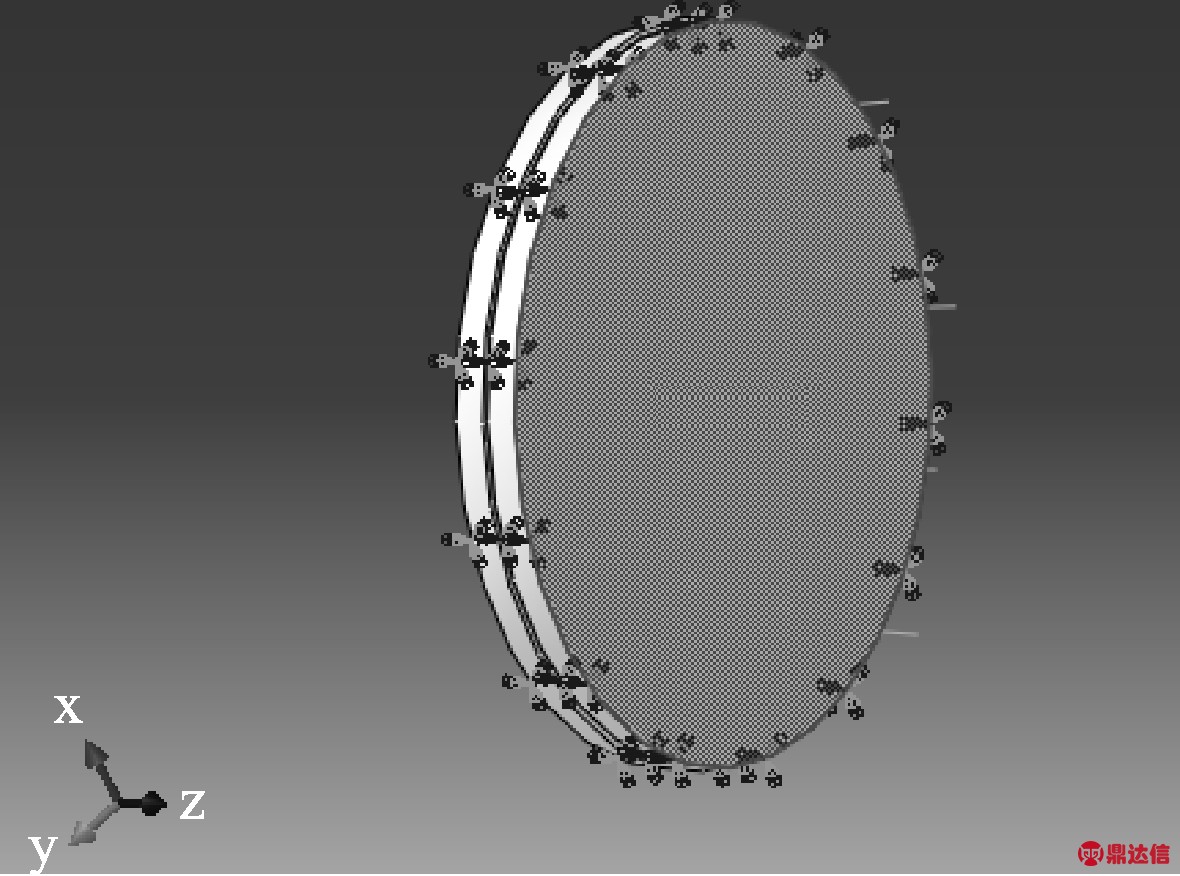
图7 吸附受力状态的有限元模型
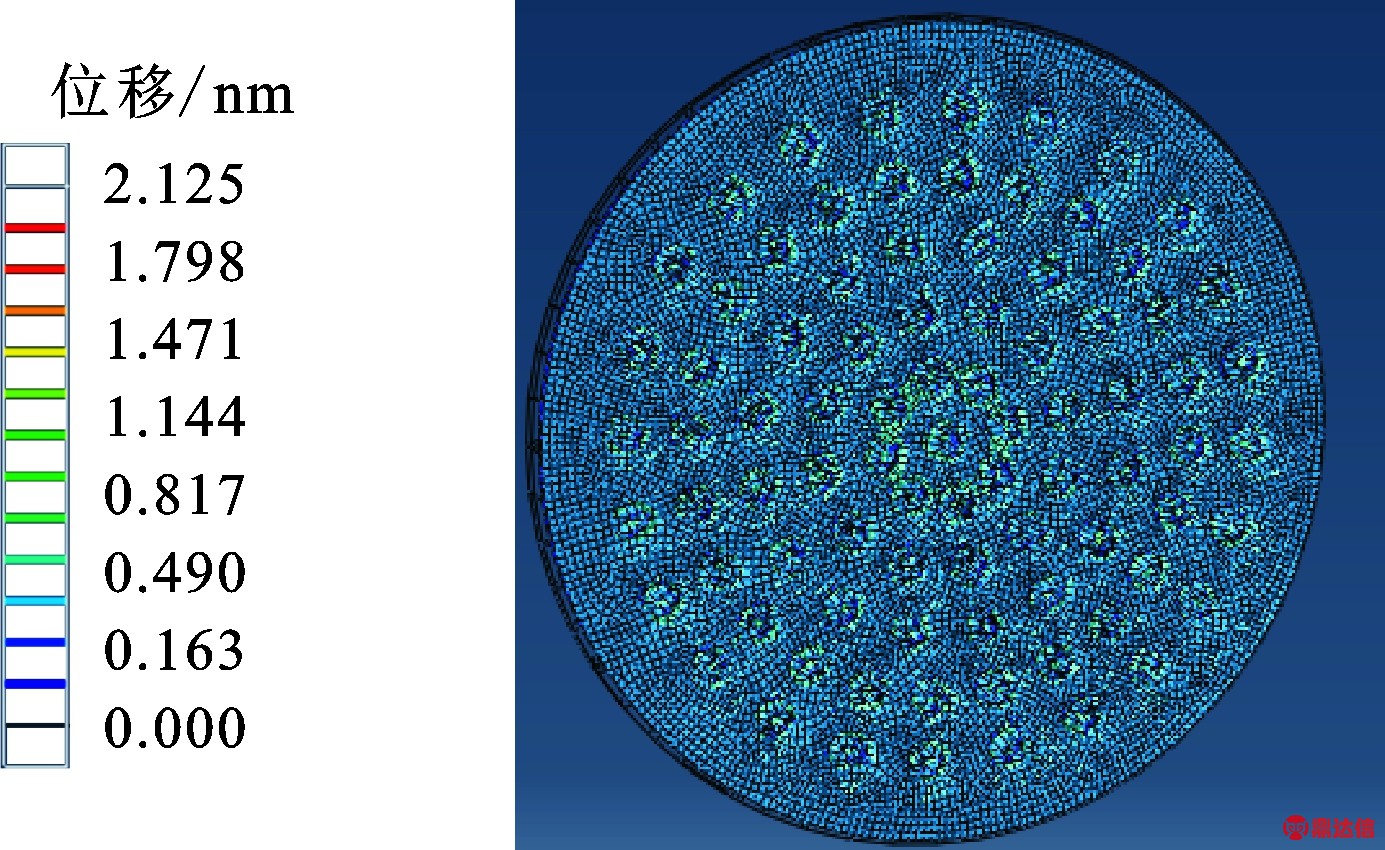
图8 吸附受力状态仿真结果
由图8可知,在真空度q=0.03 MPa时,吸孔区域的静态最大变形量δJmax≤2.125 nm,吸孔中心平均变形量为1.539 nm。
采用理论计算和仿真分别得到的变形量均在nm量级,基于激光传感器精度并结合理论与仿真误差以及材料接触等因素,可认为计算和仿真结果基本一致。由此基于该优化设计方案研制的吸具样件及吸附装夹效果如图9所示。
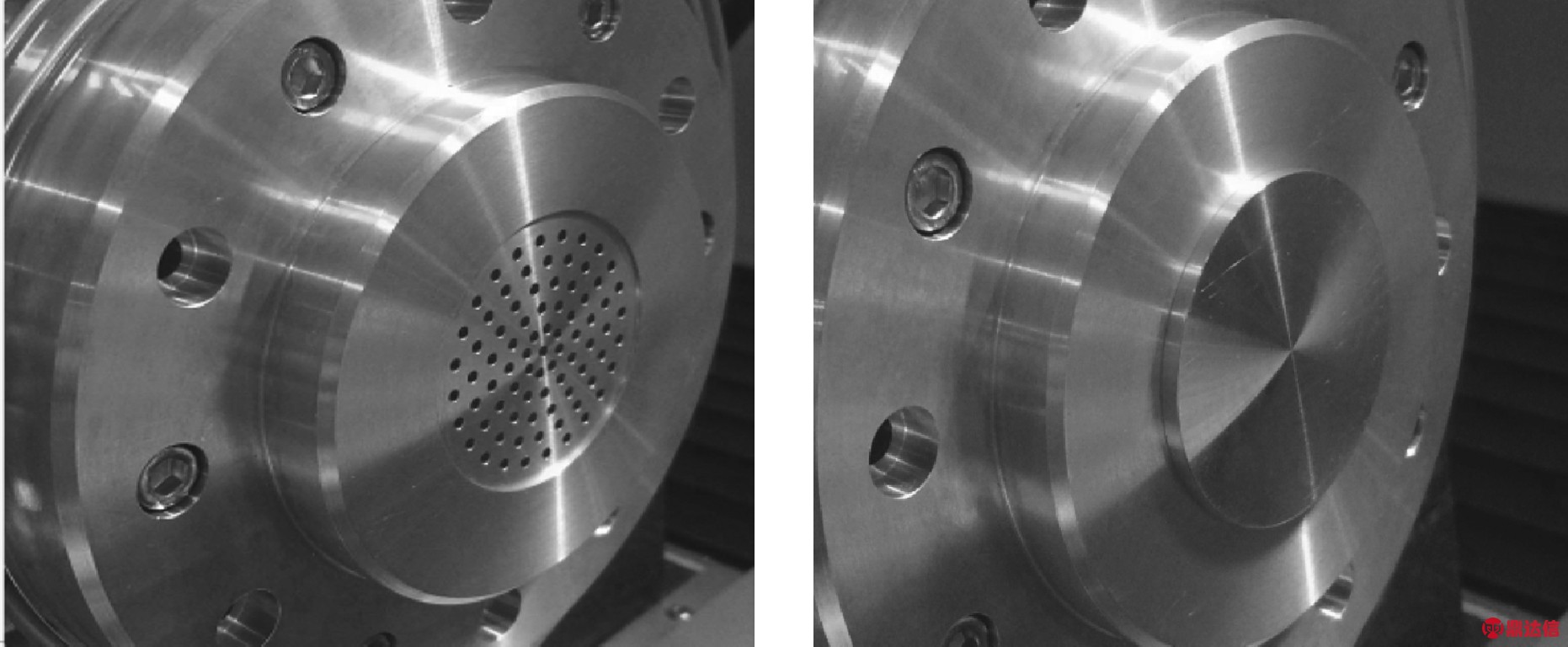
(a)装夹前吸具样件 (b)装夹后吸附状态
图9 吸具样件与吸附状态
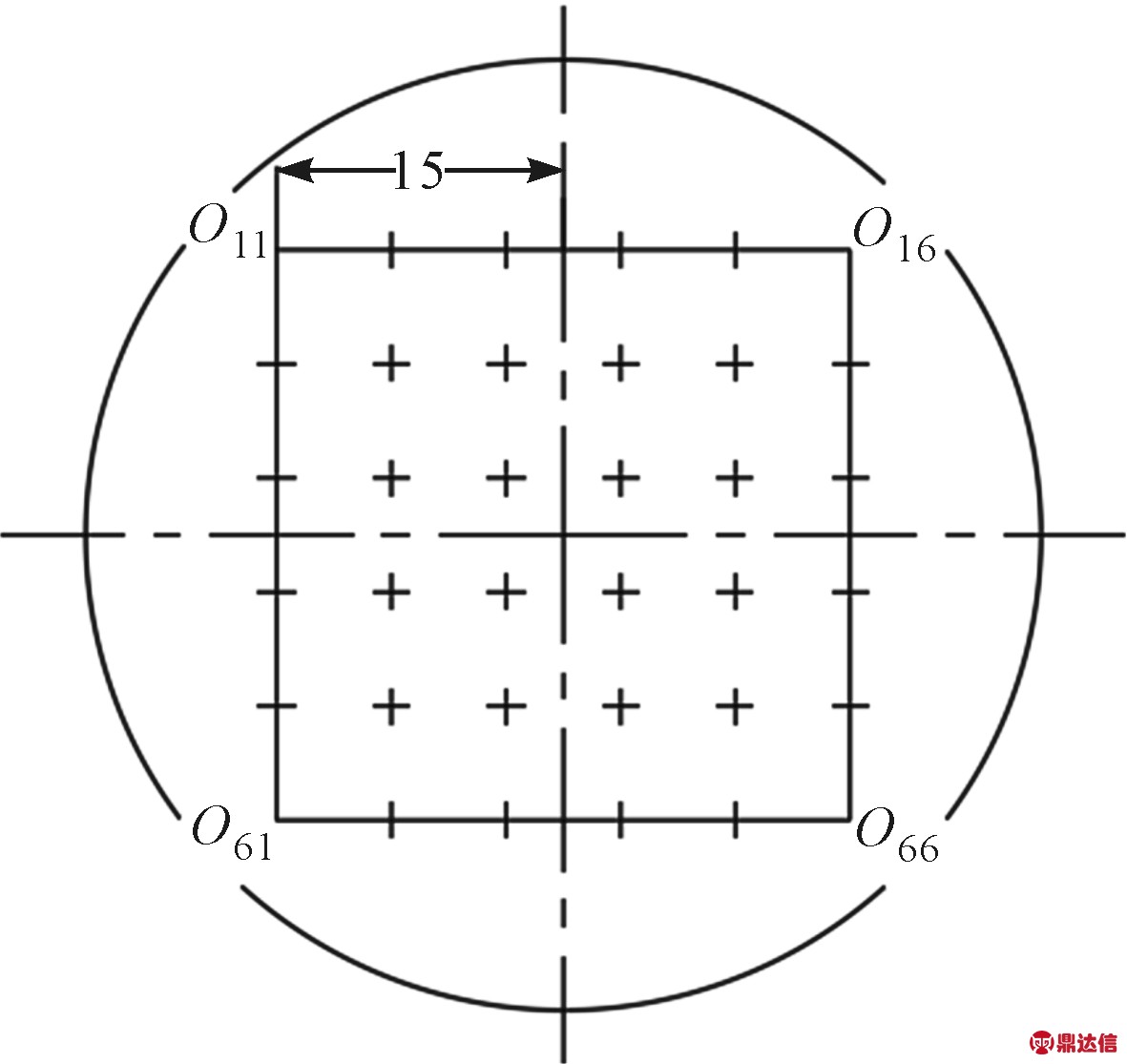
图10 平面件测量点分布位置
车削试验完成后采用Form Talysurf PGI1240(分辨率为0.8 nm)测量加工后厚度为1.8 mm的薄壁平面件,测量点分布位置如图10所示。
图10中,一共布点36个,测量时首先测量O11并以该值为基准0点,相对值为0,后续测量各点与O11取差值,获得的各点高度差数据如表1所示。
表1 平面件各测量点与O11测量数据差
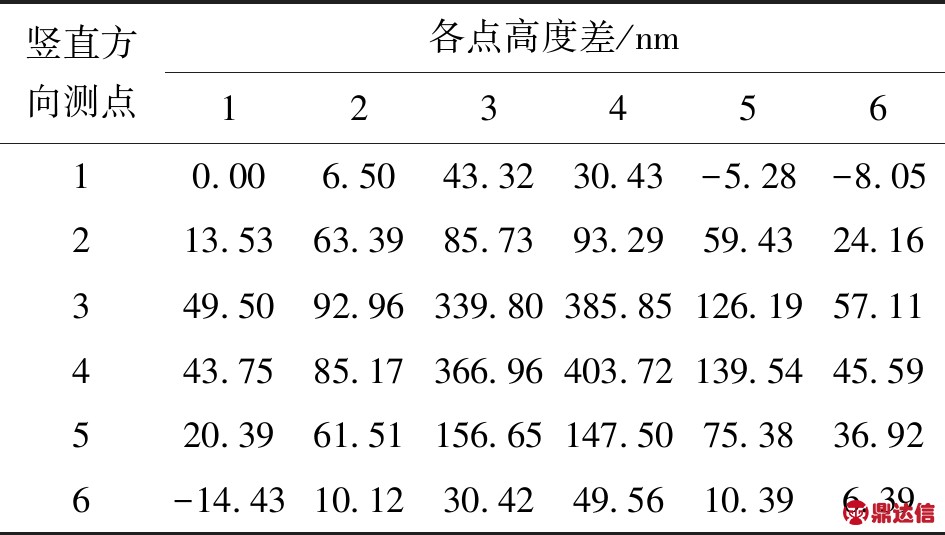
竖直方向测点各点高度差/nm12345610.006.5043.3230.43-5.28-8.05213.5363.3985.7393.2959.4324.16349.5092.96339.80385.85126.1957.11443.7585.17366.96403.72139.5445.59520.3961.51156.65147.5075.3836.926-14.4310.1230.4249.5610.396.39
经计算得出,平面度实际公差为418.15 nm。位于同一同心圆位置的测量点高度差小于30 nm,靠近中心位置,由于线速度减小,高度差出现增大。
根据图8和表1所示,考虑加工及测量误差,可以认为该真空吸具的结构优化设计是合理有效的,满足薄壁平面件超精密加工安装定位的变形控制与平面度需求,能够实现稳定吸附装夹。
4 结 论
(1)吸具吸孔设计布局与真空度影响薄壁平面件加工的静态力学变形。在工件尺寸确定的情况下,吸孔的数量越少,孔径越小,所需真空度越大;吸孔布局确定之后,真空度越大则薄壁平面件装夹及切削过程变形越大。
(2)在吸附装夹与切削过程中,工件变形主要产生在吸孔区域,越靠近吸孔中心,工件变形量越大,且吸孔中心位置的变形量最大。
(3)吸孔设计以及吸具的设计布局额外受到实际加工能力的制约。因此,在对吸具进行优化设计时,必须将吸孔实际加工能力纳入设计考量。