摘要:介绍了 API Spec 7标准、SY/T 5144标准、GB/T 22512.2标准中关于钻铤螺纹应力分散槽结构方面的发展历史。指出原有结构使公、母螺纹啮合的完整扣数目减少,降低其承载能力,并使弯曲强度比增加。提出了螺纹应力分散槽结构的改进方法,减少了应力集中,提高了钻铤螺纹的使用寿命。
关键词:钻铤;螺纹;应力分散槽;结构
钻铤在井眼中承受的载荷非常复杂,特别是钻铤接头,同时承受内压、外压、轴向载荷、弯曲载荷和转矩的作用,钻铤在钻进过程中还承受着动载的作用,在复杂载荷作用下,钻铤发生断裂失效的现象普遍存在[1]。通过大量的钻铤失效调查,发现其失效部位大部分集中在螺纹连接处。根据大港油田近30a钻铤螺纹失效统计,内螺纹断裂占34%,外螺纹断裂占66%;四川川东地区1996~1997年发生的303起钻具失效事故中,钻铤失效达137次,占45.2%,在失效类型中,连接螺纹失效达222次,占73.3%,其中发生在公扣处的失效达131次,占59.0%;大庆油田钻铤螺纹损坏占钻铤失效总数的88.4%,因此钻铤损坏基本上都发生在钻铤螺纹连接处[2]。研究表明,在钻铤的内、外螺纹消失处加工应力分散槽,减轻应力集中,是减少钻具失效的途径之一。虽然带应力分散槽的钻具在螺纹部位发生断裂事故有所减少,但仍然存在。塔里木油田CXL5井在钻井过程中,1个月内发生了5起钻具断裂事故造成了巨大经济损失[3]。某油田2002~2004年钻具失效统计结果:钻具失效次数最多的是钻铤,占钻具失效总数的63.1%;对油、气井2002~2004年不同类型钻铤失效次数统计结果:油、气井钻铤内螺纹接头断裂失效次数最多,占44.6%;其次为钻铤外螺纹断裂失效,占28.4%。为了解决钻铤断裂问题,该油田新购钻铤和修复钻铤全部要求加工应力分散槽。应力分散槽的结构形状有标准规定的结构形状,也有自己设计的应力减轻槽形状[4]。因此,采用何种结构的螺纹应力分散槽引起了人们的关注,进一步探讨钻铤螺纹应力分散槽的结构并对其进行改进,对减少钻具失效意义重大。
1 标准对钻铤螺纹应力分散槽的要求
API Spec7《旋转钻井设备规范》(1985年,第35版)较早地在标准中明确给出了螺纹应力分散槽。参考API Spec7,我国于1987年4月首次发布了行业标准SY5144—1986《钻铤》[5],其中关于螺纹应力分散槽的规定如图1~2所示。GB9253.1—1988《石油用螺纹和量规》中的应力分散槽等效采用了API Spec7第35版。
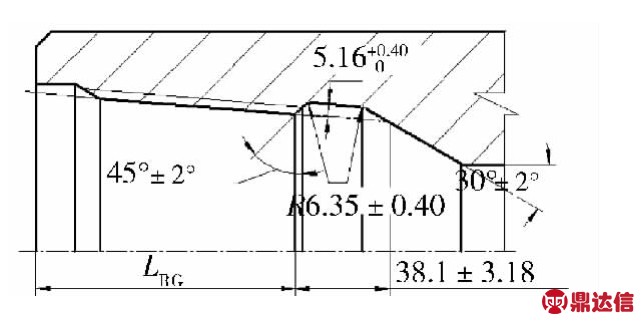
图1 内螺纹应力分散槽
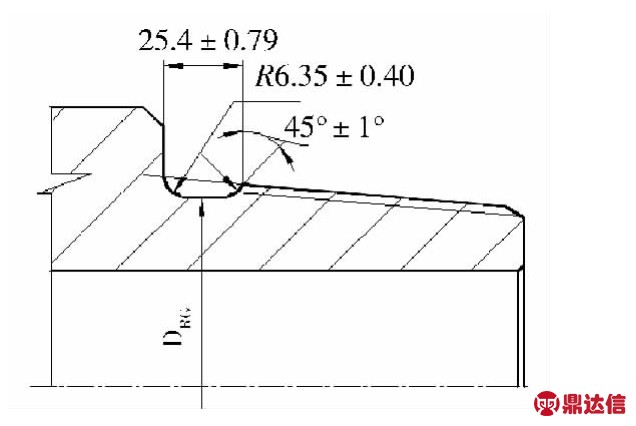
图2 外螺纹应力分散槽
SY/T5144—1997《钻铤》[6]是 SY5144—1986第1次修订版。该标准参考了API Spec7《旋转钻井钻柱构件规范》(1994年4月,第38版)的有关技术内容,本标准对内螺纹应力槽分散槽进行了结构改进,如图3所示,并将图1所示的内螺纹应力分散槽作为一种替代的内螺纹连接部位应力分散槽,外螺纹应力分散槽保持不变,如图2所示。
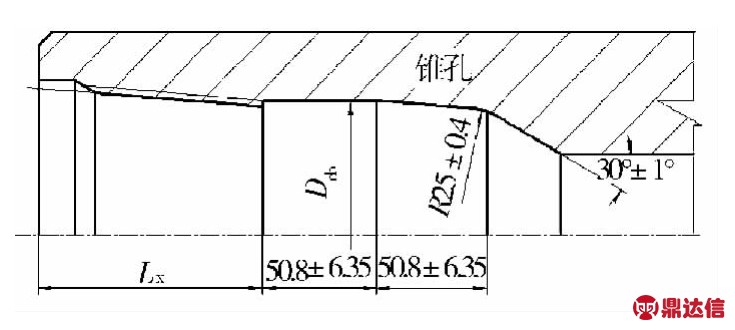
图3 内螺纹内孔应力分散槽
SY/T5144—2007《钻 铤》[7]是 SY/T5144—1997的升级版。该标准参考了API Spec7《旋转钻井钻柱构件规范》(2001年11月,第40版)的有关技术内容,保留了SY/T5144—1997中的应力分散槽,并完善了内螺纹应力分散槽的结构表达,如图4所示。避免了SY/T5144—1997中内螺纹应力槽结构的理解歧义。
GB/T22512.2—2008《石油天然气工业 旋转钻井设备 第2部分:旋转台肩式螺纹连接的加工与测量》[8]中关于应力分散槽的要求与SY/T5144—2007《钻铤》一致。
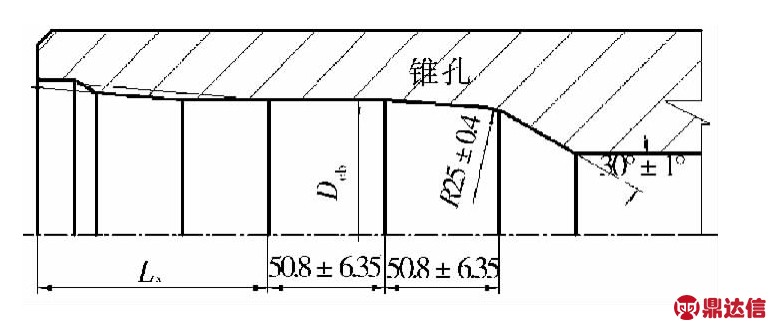
图4 内螺纹内孔应力分散槽
即将出版的SY/T5144—2013《钻铤》是SY/T5144—2007的最新升级版。保留了螺纹应力分散槽结构,并与GB/T22512.2—2008相统一。
2 原有结构存在的问题
主要讨论钻铤内螺纹应力分散槽的结构。内、外螺纹连接后如图5所示。
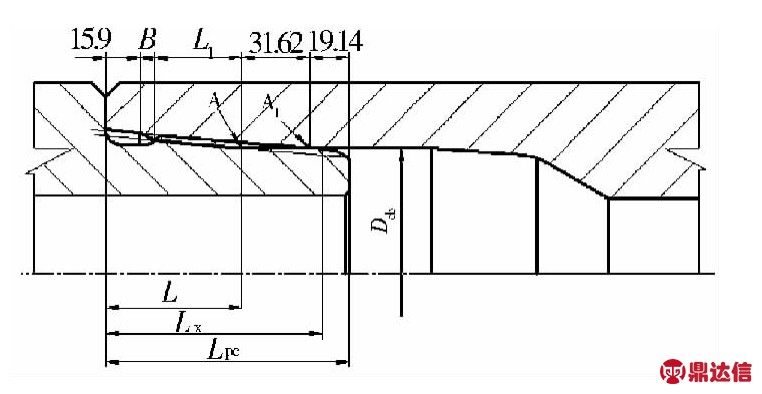
图5 NC50内、外螺纹连接结构
以177.8mm钻铤接头(内径71.4mm)螺纹NC50-70为例,分析内、外螺纹带应力分散槽时啮合的具体情况。NC50-70螺纹的尺寸如下:
内螺纹台肩面至最后一牙刻痕长度Lx=101.6 mm,内螺纹件圆柱段直径Dcb=117.48mm,内螺纹大端小径D2=128.07mm,大端扩孔长度为15.9 mm,螺距P=6.35mm。可计算出:内螺纹完整扣(内螺纹端面至完整扣处A点,内螺纹小径轮廓线与内螺纹件圆柱段直径Dcb的交点)长度L=63.54 mm,倒角宽度B=7mm,从而得出:实际完整扣长L1=L-15.9-B=40.64mm。螺距 P=6.35 mm,完整扣牙数6.4。对内螺纹而言,在长度Lx范围内只有6牙处于完全啮合状态,其余处于半啮合或非啮合状态,半啮合长度为31.62mm,而且啮合的牙型高度由完整牙高逐渐过渡为零。对外螺纹而言,外螺纹长度Lpc=114.3mm,在长度Lpc范围内,台肩面至内、外螺纹的啮合末点A1(外螺纹大径轮廓线与内螺纹件圆柱段直径Dcb的交点)长度95.16 mm,其余19.14mm处于自由悬臂状态。
通过以上分析,内、外螺纹带应力分散槽时,存在的主要问题是:啮合的完整扣长度缩短,部分处于半啮合状态,而且外螺纹有部分扣处于悬空自由状态。这样可引起钻铤螺纹在复杂载荷的作用下,容易在A1截面发生断裂失效,这与近几年来钻铤内螺纹在距其端面80~100mm处发生断裂的失效形式基本吻合。图6为带应力槽的203mm钻铤内螺纹断裂情况。
另外,带有应力分散槽的钻铤一旦螺纹损坏需要修复时,钻铤端部需切弃一定长度后才能重新加工螺纹,不同规格的钻铤要切弃的长度为70~100 mm,因而,钻铤材料浪费相当大,并且进一步缩短了钻铤的使用寿命。
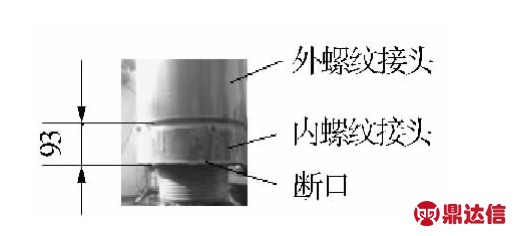
图6 钻铤内螺纹断裂实例
3 螺纹应力分散槽对弯曲强度比的影响
SY/T6288—2007《钻杆和钻铤选用作法》[9]中6.1.2.2规定,钻铤内、外螺纹接头的弯曲强度比按下式计算:
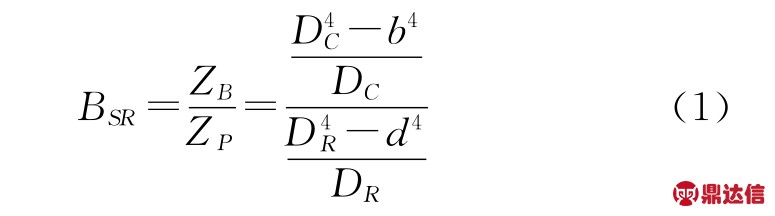
其中
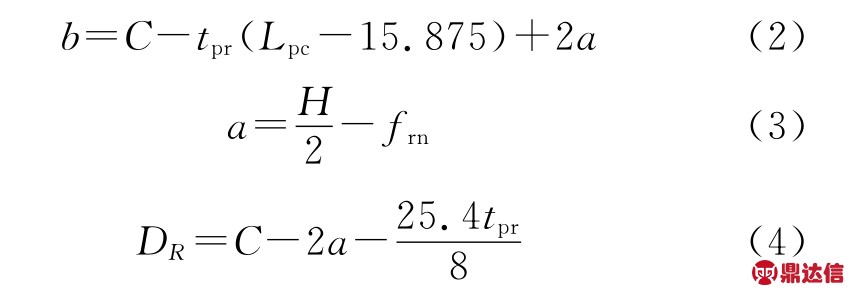
式中:BSR为钻铤弯曲强度比;ZB为内螺纹接头截面模数,mm3;ZP 为外螺纹接头截面模数,mm3;DC 为内、外螺纹接头外径,mm;b为外螺纹末端处的内螺纹牙根直径,mm;DR为距外螺纹接头台肩19.05 mm处外螺纹的牙根直径,mm;d为钻铤内径,mm;C为螺纹基面中径,mm;tpr为锥度,mm/mm;Lpc为外螺纹锥部长度,mm;a为齿高,mm;H 为原始三角形高度,mm;frn为牙底削平高度,mm。
查阅GB/T 22512.2—2008可得:C=128.059 mm;tpr=1∶6;H=5.487mm;frn=0.965mm。将以上数据分别代入式(2)~(4),可得:a=1.778 5 mm;b=115.212mm;DR=123.973mm。
由于内、外螺纹带有应力分散槽,需对b和DR做修正,外螺纹末端有19.14mm处于悬臂自由状态,可推出:b=C-tpr(Lpc-15.875-19.14)+2a=118.405mm。
外螺纹件的槽直径DRG=120.45mm,所以,修正后的DR=DRG=120.45mm。查阅SY/T 5144—2007可得:D=177.8mm;d=71.4mm。将Dc、d及修正后的b、DR 代入式(1)即可得BSR=2.95。
177.8mm 钻铤接头(内径71.4mm)螺纹NC50-70不带应力分散槽时,弯曲强度比BSR=2.73。
根据API RP7G推荐平衡连接(所谓平衡连接就是指内、外螺纹抗疲劳性能大致相当)时,BSR=2.5。通常可接受的BSR为1.9~3.2,根据实际情况而定。由以上计算看出,螺纹加工应力分散槽后,弯曲强度比略有提高,但在推荐范围内。
4 结构改进建议
针对内螺纹螺纹应力分散槽存在的问题,提出内螺纹应力分散槽的改进思路,①加长内螺纹完整扣长度,使之与外螺纹长度相同,以增加螺纹有效啮合牙数,相应地减小内螺纹件圆柱段直径Dcb,使之与内螺纹完整扣处(A′点)的小径相同。②内螺纹应力分散槽后孔圆柱段长度由原50.8mm增加到88.9mm。改进后的内螺纹内孔应力分散槽结构如图7所示。以NC50为例,完整扣长L=114.3 mm,Dcb=109mm。
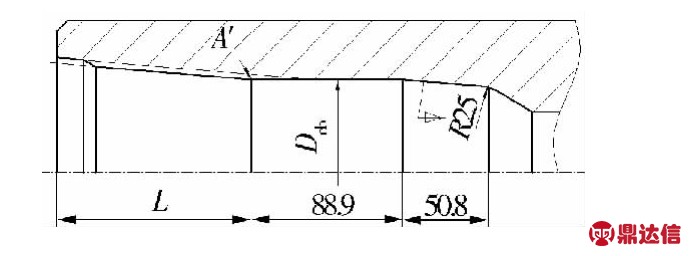
图7 改进后的内螺纹内孔应力分散槽结构
外螺纹应力分散槽保持不变。研究结果表明:带有应力减轻槽的外螺纹具有较小的应力集中,特别是API标准应力减轻槽的应力集中最小,因此抗疲劳性能最佳,建议外螺纹采用这种应力减轻槽结构[10]。
5 结语
改进后的内螺纹应力分散槽,保证了内、外螺纹啮合的完整性。改善了应力在轴向的分布状况,具有明显的应力减轻效果。当钻铤螺纹损坏需要修复时,切弃的端部长度缩短,可增加修复次数,延长钻铤的使用寿命。