摘要:超薄显示技术已成为市场的一种主流趋势。本文利用刻蚀后清洗的间歇式工艺研究了显示屏半成品的化学减薄。在光刻胶和边框胶保护下,调整氢氟酸浓度,加入一定量的硝酸、浓硫酸和盐酸,并添加超声辅助条件,刻蚀速率明显提高。通过交替的清洗工艺有效地降低了表面粗糙度,并减少了表面白色附着物的沉淀。显示屏厚度从0.8 mm减薄到0.3 mm,基板表面粗糙度为11.32 nm,厚度均匀性为4.76 %。设计的间歇式减薄工艺可以应用到现有的显示屏生产工艺中,为制作超薄液晶显示屏和超薄有机发光显示屏提供了一条可行的方案。
关 键 词:显示屏;化学减薄;间歇式工艺;刻蚀
1 引 言
随着科技的发展,显示行业的竞争愈来愈激烈。竞争的焦点集中在:(1)高分辨率;(2)超薄及高亮度设计;(3)低功耗。超薄显示技术是市场的一种主流趋势[1]。消费者一直希望电视能像画一样挂在墙上,但受材料变形、热处理问题、量产稳定性问题的限制,显示器模组的厚度很难做到像纸一样薄。当前超薄显示器模组技术主要包括有源矩阵阵列的设计[2]、显示器结构的设计[3]、背光源部件的设计[4-5]、以及对平板玻璃原料的减薄[6-7]。
本文在显示屏制作工艺中增加减薄工艺。通过物理和化学方法使显示器厚度达到轻薄化的目的。目前国内外玻璃化学腐蚀工艺主要使用氢氟酸混合物[8],但腐蚀时间长、表面粗糙度大。超声扰动有利于提高腐蚀速率,增加腐蚀的光滑性[9]。预处理液有利于填充玻璃表面的微小裂纹,可以有效防止氢氟酸腐蚀中玻璃基板上裂纹的放大,提高显示屏的良品率[10]。本文以氢氟酸为主要溶液,调节超声强度,化学刻蚀条件,增加间歇式工艺,解决表面粗糙及表面白色附着物沉淀的问题,显示屏厚度从0.8 mm减到0.3 mm,均匀性好,良品率提高。设计一条产业化生产的减薄工艺流程,只需增加间歇式减薄设备,工艺简单,成本低,能满足超薄显示屏制作生产的目的。对未来的超薄液晶显示器和超薄有机发光显示器非常实用。
2 实 验
2.1 实验材料和仪器
本文采用的显示屏是从上海天马显示器有限公司购买的,显示屏厚度0.800 mm,如图1。实验所用的化学药品均是从北京盛维特科技有限公司购买的,主要有氢氟酸(HF)溶液(40%)、浓硝酸(HNO3)溶液(68%)、盐酸(HCl)溶液(34%)、浓硫酸(98%),丙酮,乙醇。去离子水是实验室自制的。光刻胶和边框胶是从长春市芳冠电子科技有限公司获得的。
显示屏厚度和刻蚀速率均采用螺旋测微器测量的,从日本三丰Mitutoyo购买的,型号为0-25 mm 103-107 0.01 mm。表面粗糙度(RMS)采用日本精工株式会社的SPA300HV 原子力显微镜(AFM)(Seiko Instruments Inductry, Co.Ltd.Japan.),SPI3800 控制器,扫描方式为敲击模式(Tapping Mode)。
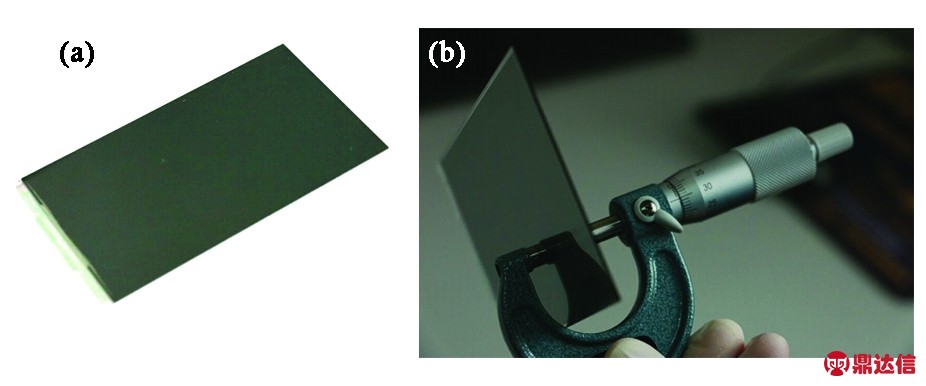
图1 待减薄的显示屏(a) 和厚度测试(b)照片
Fig.1 Photo of display panel to be slimmed (a) and thickness measurement (b)
2.2 实验方法
2.2.5 刻蚀速率
2.2.1 显示屏表面预处理
依次用丙酮、乙醇冲洗,最后用去离子水清洗擦净,除去玻璃表面灰尘、油脂。
2.2.2 显示屏必要部分保护
烘箱加热至180 ℃,显示屏侧面涂布边框胶,防止刻蚀液渗透进显示屏内部。放入烘箱,烘30 min,使边框胶固化。再把烘箱降温至70 ℃。在显示屏的电极端涂布光刻胶,防止刻蚀液腐蚀引线电极。涂抹后放入烘箱中,烘15 min。
2.2.3 测量玻璃初始厚度并配制溶液2.2.4 减薄后处理
刻蚀后,先用丙酮清洗,再用乙醇清洗,最后用去离子水清洗后吹干,对比刻蚀前后厚度变化,观察表面效果。
3.4 间歇操作条件的影响
研究不同温度、超声时间、不同刻蚀液配比下,显示屏的刻蚀速率。刻蚀速率为单位刻蚀时间内刻蚀显示屏的厚度,单位为 μm/min。
3 结果与讨论
3.1 氢氟酸对刻蚀速率的影响
在温度为60 ℃条件下,分别配置浓度为15%、20%、30%、40%的氢氟酸溶液500 mL,所指浓度为质量浓度g/mL,提供原溶液浓度为40%。放入聚乙烯材料器皿中,放入厚度为0.8 mm的显示屏。分别刻蚀5 min,取出后使用螺旋测微器测量厚度,得出刻蚀速率与氢氟酸浓度间的关系,如图2。实验发现随着氢氟酸浓度的提高,刻蚀速率提高,当氢氟酸浓度达到40%时,平均刻蚀速率为57 μm/min。但是刻蚀后的厚度均匀性变差,如图2,5点的均匀性为49.86%。表面变得粗糙20.66 nm,如图3,刻蚀性能变差。考虑要实际生产应用,浓度过高也会增加成本,因此在传统刻蚀液中添加其他组分。
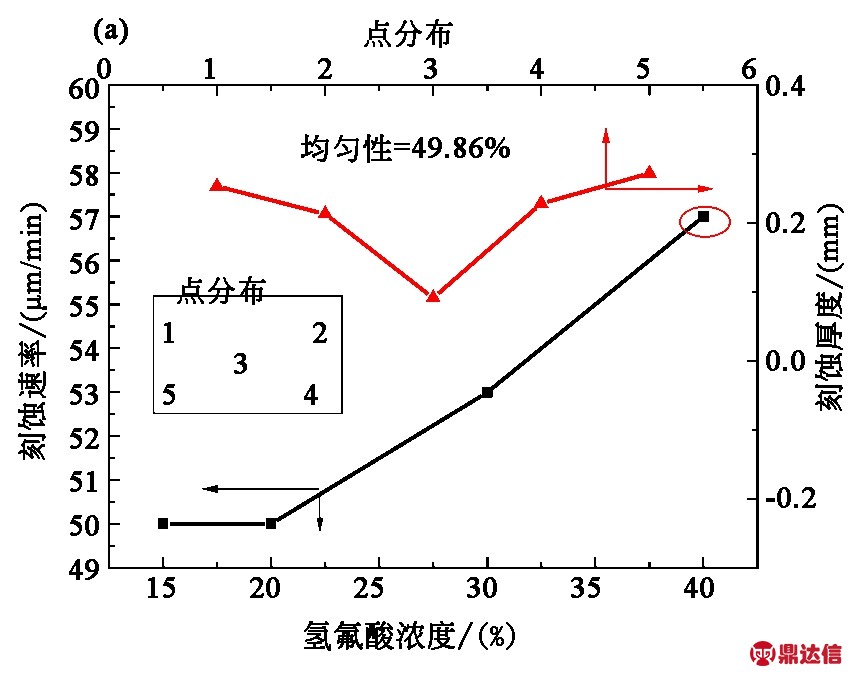
图2 氢氟酸浓度对刻蚀速率的影响及40% HF浓度下的刻蚀厚度均匀性图
Fig.2 Effect of HF concentration on etching rate and the etching thickness uniformity at 40% HF concentration
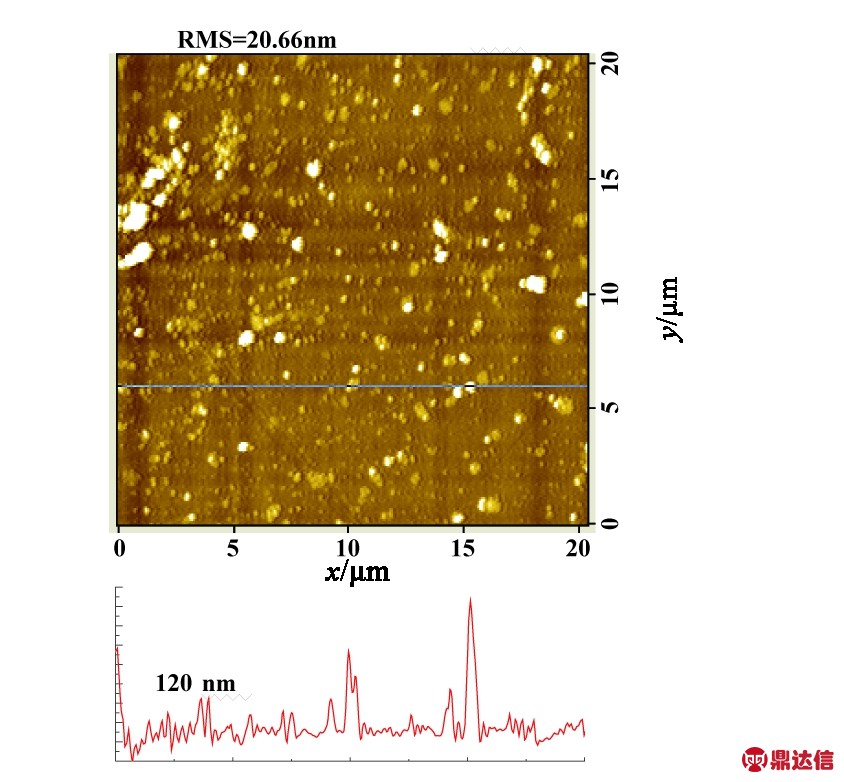
图3 40% HF浓度下原子力图
Fig.3 AFM image of RMF=20.66 nm at 40% HF concentration
3.2 超声强度对刻蚀速率的影响
超声的化学作用是能使玻璃的主要成分SiO2的Si-O键断裂,有利于HF酸对玻璃的腐蚀作用。为量化超声强度对刻蚀速率的影响,配置30%的氢氟酸溶液500 mL,温度60 ℃,分别在超声强度为0、20%、40%、60%、70%的情况下对厚度为0.8 mm的显示屏进行化学刻蚀。刻蚀速率与超声强度间的关系,如图4。可见当超声强度由无到40%的过程中刻蚀速率仅提高了21%,而当超声强度变为60%时,刻蚀速率提高到51 μm/min,超声效果明显。因为超声强度不够时,提供的化学力不足以打开Si-O键的作用力,故对刻蚀速率的提高不明显,当超声强度达到60%时,刻蚀速率提高最为明显,Si-O键被打开。而当超声强度提高到70%时,光刻胶会因为震动强度过大而脱落,对显示屏的金属腐蚀,光刻胶达不到保护作用。
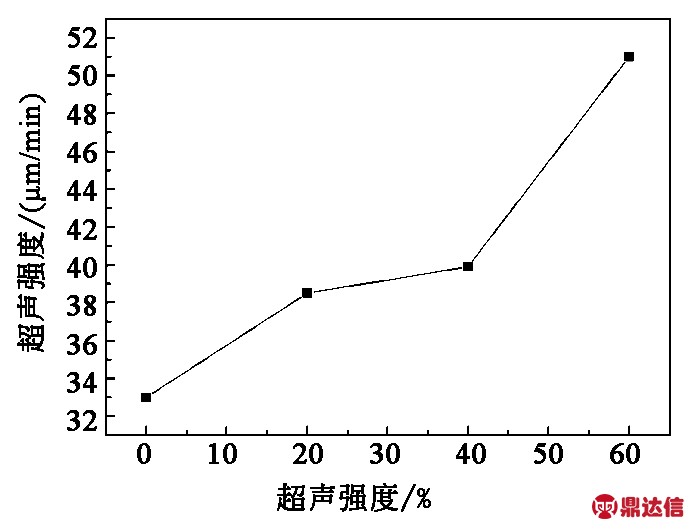
图4 超声强度对刻蚀速率的影响
Fig.4 Effect of ultrasonic intensity on etching rate
3.3 硝酸对刻蚀速率的影响
在对二氧化硅反应中,氢氟酸起到主要作用,而硝酸的加入会在酸性、氧化能力上对氢氟酸有着较好的提高。硝酸对刻蚀速率的影响,如图5。
在500 mL的30%的氢氟酸溶液中分别加入3%、5%、8%、10%浓度的硝酸(硝酸原溶液为68%)。实验时间5 min,温度60 ℃,刻蚀后用螺旋测微器测量分析。可见当硝酸浓度达到10%时,刻蚀速率能提高到原来的81%。实验发现,在有小量浓硫酸的作用辅助下,刻蚀速率也会有少量提高,但是不够明显,当添加盐酸后,由于盐酸的理化性质,溶液在刻蚀一次后,呈现棕黄色,在下一次的刻蚀中效果降低。但是由于玻璃与氢氟酸作用后生成的盐类的溶解度的不同,反应后白色结晶物附着在玻璃表面阻碍氢氟酸与玻璃的进一步反应。所以应从反应工艺上对此进行进一步的精进。
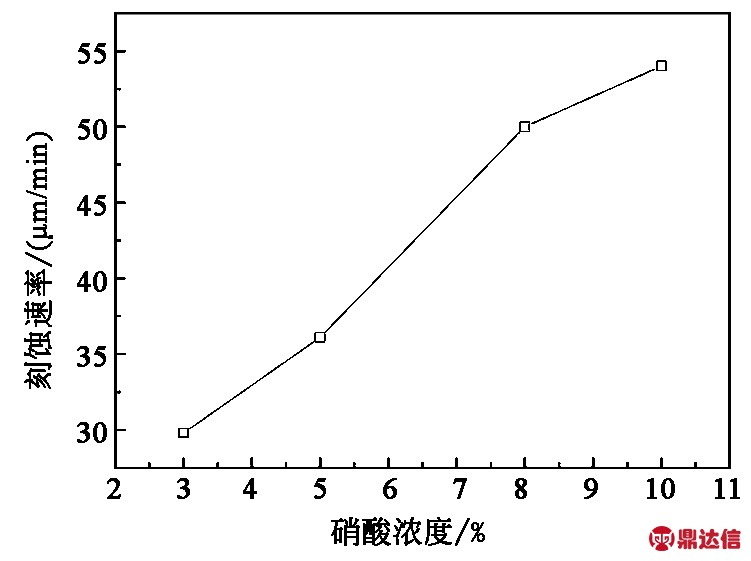
图5 硝酸浓度对刻蚀速率的影响
Fig.5 Effect of HNO3 concentration on etching rate
本文采用的具体实验流程如下:
由于玻璃与氢氟酸作用后生成的盐类的溶解度不同,反应后白色结晶物保留在玻璃表面阻碍氢氟酸与玻璃的进一步反应。本实验采用间歇式刻蚀工艺,就是刻蚀一定时间后,取出清洗,然后继续刻蚀,再清洗,反复几次的办法。为寻找玻璃表面沉淀物达到饱和的最佳时间,分别在刻蚀20 s后,30 s后,40 s后,45 s以及50 s后,取出清洗后,然后测量刻蚀厚度,如图6。当刻蚀40 s后,白色沉淀物覆盖在显示屏表面,最大程度阻止反应进一步进行。故在刻蚀40 s后取出显示屏清洗掉沉淀物,清洗时间大约10 s,再放入继续刻蚀,在6分钟后就能达到技术要求。粗糙度为11.32 nm,均匀性为4.76%。
3.5 工艺流程设计
本文研究中发现仅用氢氟酸刻蚀减薄显示屏,表面粗糙,刻蚀过程中表面白色物附着沉淀阻止反应有效进行。因此玻璃表面受到的刻蚀效果不均匀,导致表面粗糙。然而,增加间歇式工艺后,表面明显平滑,均匀性好。
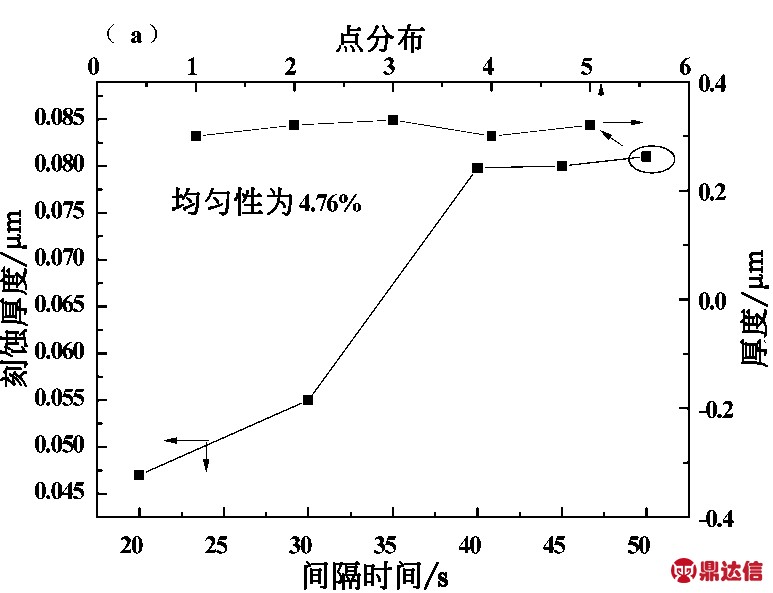
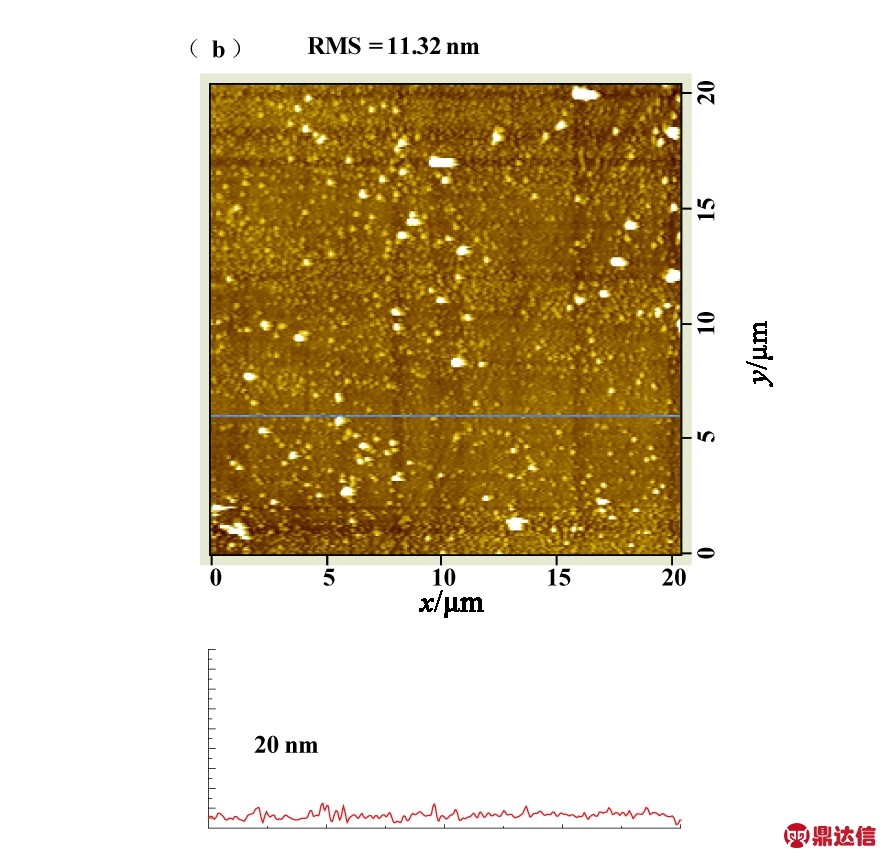
图6 (a)刻蚀厚度与间隔时间的关系及刻蚀均匀性图;(b)刻蚀后表面粗糙度图
Fig.6 (a) Relations between etching thickness and intermittent time, and etching uniformity; (b) Surface roughness of RMS=11.32 nm after etching
为此,设计了在显示屏制作工艺中,增加间歇式减薄工艺流程,如图7。在制屏工艺的对盒、划片工序后,贴偏振片工序前,增加间歇式减薄工艺。先在显示屏侧面涂布边框胶,防止药液渗入显示屏内。接着在显示屏的电极引线处涂布光刻胶防止刻蚀液腐蚀金属引线电极。然后进行刻蚀,清洗,反复刻蚀、清洗工艺,最后再去胶。涂胶、刻蚀、清洗可以在一台流水线设备内完成,通过刻蚀节拍和要求增设不同量的刻蚀槽、清洗槽,达到间歇式刻蚀的目的。
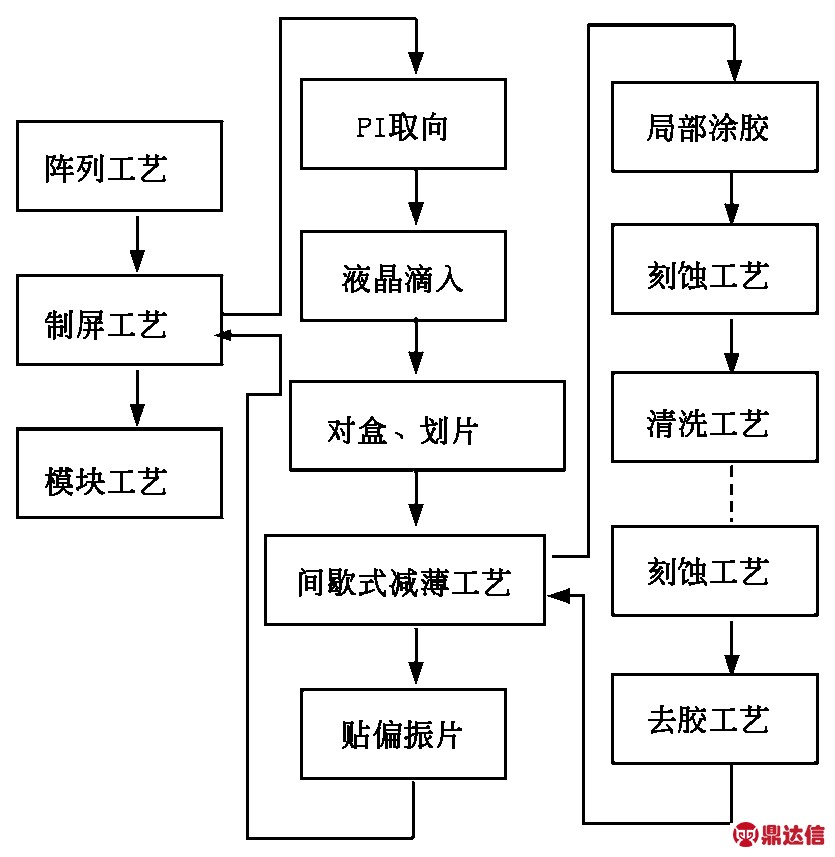
图7 显示屏减薄工艺流程设计
Fig.7 Design of slimming process for display panel
与先对玻璃减薄,后制屏的工艺相比,优点如下:
(1)工艺难度低。对盒和划片前的工序是针对大尺寸基板的传输和加工。在此工艺后增加减薄工艺,可以避免大尺寸超薄基板的传输、基板定位的问题,也不受PI涂布和摩擦等工艺对基板厚度的限制,可以最大限度的减薄。
(2)成品率高、量产稳定。对盒、划片工序后减薄,高温工序(如PI固化、边框胶固化等)作用的都是未减薄的显示屏,不存在高温导致超薄基板变形的问题,成品率高、量产稳定;
(3)超薄显示屏。对盒工艺后减薄,可以对显示屏的上下玻璃基板同时进行减薄,而且减薄后上下两块基板互相支撑,可以获得超薄显示屏;
(4)设备成本低。制屏前半程中,PI取向、液晶滴入、以及对盒和划片等设备都不需要改变,可
以使用现有的生产线,只需增加部分设备,设备成本低。
4 结 论
本文采用物理和化学的方法,对显示屏半成品进行化学减薄。研究发现显示屏减薄过程中氢氟酸的浓度至关重要,过高浓度会破坏边框胶,使药液渗入显示屏内部。通过增加硝酸、盐酸、硫酸提高刻蚀速率,降低刻蚀时间,增加超声强度提高刻蚀效果。超声强度为60%时,对刻蚀有较好的辅助作用。为降低表面粗糙度,解决刻蚀过程中白色附着物沉淀的问题,设计了间歇式减薄工艺。优化配比为氢氟酸(40%)∶硝酸(68%)∶硫酸(98%)∶水为600∶147∶10∶233,每刻蚀40 s取出冲洗一次10 s,共计6 min,减薄后显示屏厚度基本一致,0.30~0.33 mm。间歇操作的方法有效地减少了反应后结晶物在玻璃表面滞留,促进了氢氟酸与玻璃的进一步反应,刻蚀后的显示屏粗糙度和均匀性较好。可应用到超薄液晶显示屏和超薄有机发光显示器的生产中。