摘 要:材料表面的散射特性和表面粗糙度对产品的性能有十分重要的影响,基于激光散射原理设计了用于检测表面粗糙度和表面散射特性的多波长光纤传感器。光纤传感器的探头采用特殊的几何设计,用650 nm、1 310 nm和1 550 nm激光作为光源,选择2 mm的工作距离作为最佳测量距离,对不同表面粗糙度的样品进行了测试和分析。实验结果表明:同一波长下,随着表面粗糙度的增大,以外磨样品为反射面测得的反射强度减小;同一粗糙度下,入射波长越长,反射强度越大。多波长光纤传感器可以精确地测量表面粗糙度,并能有效地减小系统误差。系统误差分析得到传感器的相对误差范围大约为3.56%~7.43%。
关键词:表面粗糙度;多波长光纤传感器;激光散射;在线测量
导师简介:张骏(1965-),男,教授,硕士生导师,博士,主要从事光电信息获取与处理方面的研究。Email:jzhang@ytu.edu.cn
0 引 言
在大型光学工程和激光应用中,材料的表面散射特性和表面粗糙度对于研究光学系统和加工产品的性能具有十分重要的意义。国内外许多学者也已在这方面做了大量的研究[1-9],从早期的定性测量发展到了如今的定量测量,从原先的接触式测量法到现在的非接触式测量法[7-8],分析了多种材料表面的散射特性。对于表面粗糙度的测量,接触式测量法会损伤材料表面的质量和性能,导致测量不准确;而非接触式测量法避免了材料表面的损伤,减少了误差。
随着激光技术的发展,非接触式测量法得到了越来越广泛的发展,其中非接触式的光学测量方法倍受关注,例如基于激光散射原理的光纤传感器[1-6],散射法[8-10],平均散射强度(mean scattered intensity,MSI)分析法[11],散斑分析法[12-15]等。由于在大型光学工程中对光学元件表面粗糙度测量精度的要求高[16],采用接触式测量法会对待测样品产生严重的误差,测量不准确;文中采用了非接触式的光学测量法来检测材料表面的散射特性以及测量表面粗糙度值。当光源照射到材料表面时,光的散射特性可以通过镜向反射强度和散射强度来描述[17-18]。在实验系统中采集不同粗糙度表面的散射强度值,利用测量原理中粗糙表面的光散射强度和粗糙度的关系可以预测粗糙表面的粗糙度值。在复杂环境中,空气中的悬浮颗粒[19]将沉积在材料表面污染材料,并增加材料表面的散射,利用这种非接触式的光学测量法可以有效地检测颗粒污染表面的散射特性。
利用光纤传感技术,文中设计了基于激光散射[20-21]的测量表面散射特性和表面粗糙度的光纤测量仪,称为多波长光纤传感器(multi-wavelength fiber sensor,MWFS),利用从两个不同波长下测得的粗糙表面的光散射强度比值可以获得表面粗糙度值。实验装置由激光器、耦合装置、传感器、探测器、数据采集系统五部分组成。通过这个装置可以有效地测量粗糙表面的散射特性和表面粗糙度值。光纤传感器具有测量装置简单、数据处理方便、非接触在线测量的优点。由于这些优点,该方法也适于分析污染颗粒对材料表面的散射特性。
1 表面粗糙度的测量原理
假设粗糙表面微观不平度的随机分布符合高斯分布,忽略表面的吸收,通过测量粗糙表面的反射强度可以得到表面散射特性和表面粗糙度。在研究中,采用光纤传感技术研究表面粗糙度和粗糙表面的主要特性。如图1所示设计的光纤束端面结构,其由中间的发送光纤(小芯径的单模光纤)和围绕它的的按照等角度间隔分布的紧密排列的六根接收光纤(多模的大芯径特殊光纤)组成,且不管发送光纤还是接收光纤都选择工作在1 550 nm波长的石英光纤。光纤束的强度调制函数可以认为是六个单光纤对的强度调制函数之和。
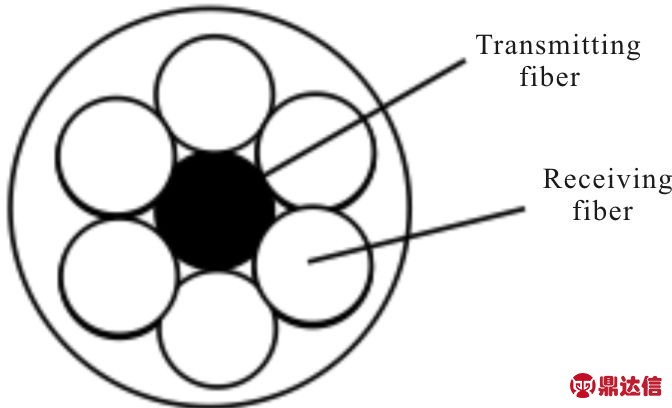
图1 光纤束端面结构示意图
Fig.1 Schematic diagram of fiber bundle end face
单光纤对的有效受光面积[4]为:
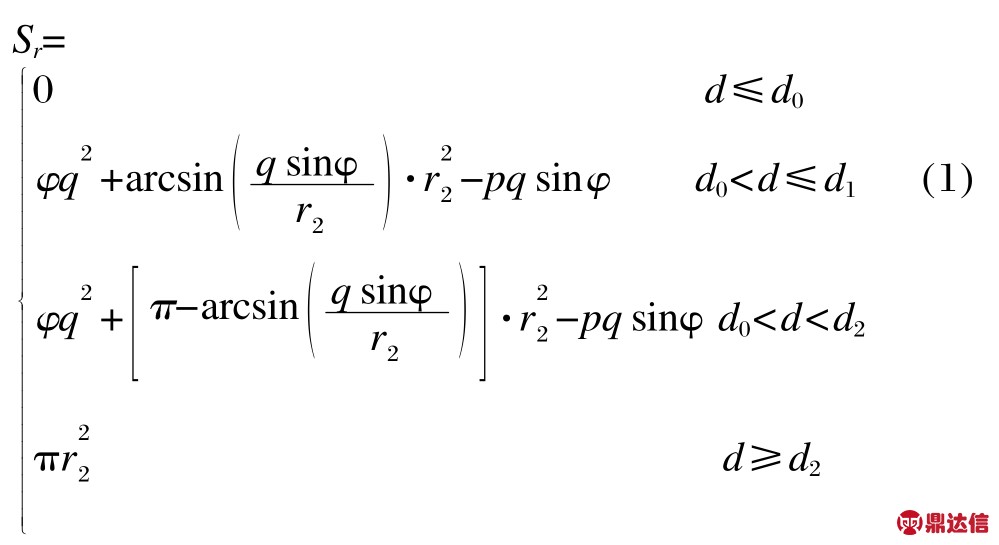
记
式中:r1、r2分别为发送光纤、接收光纤的纤芯半径;a为两光纤间距;d为光纤探头与被测样件表面之间的距离;p为发送光纤和接收光纤的轴间距,p=r1+ a+r2;q为反射光在光纤端面处的光斑半径q=r1+2d tanN1,
N1=arcsinNA1,NA1为发送光纤的数值孔径。
传感器的发送光纤是单模光纤,在单模光纤中光的分布为高斯分布,故认为其出射光强的分布也符合高斯分布,如图2所示,则出射光场点(,z)处的光强为:

式中:Pt为发送光纤发出的光功率;q(z)为出射光束在距离z处的光斑直径;为观察点与光斑中心的距离。
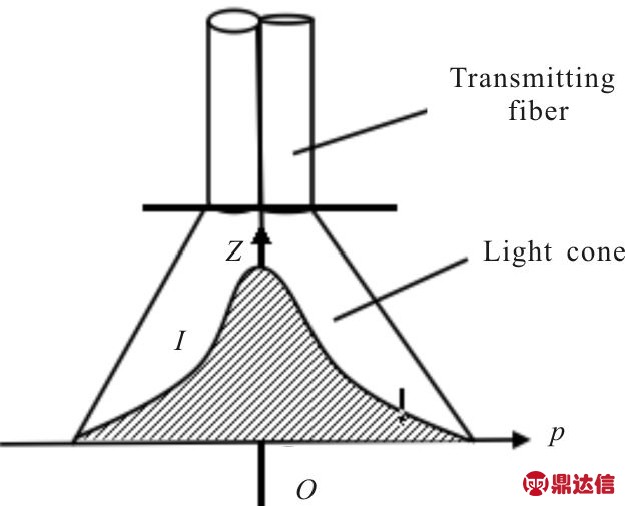
图2 发送光纤出射光强高斯分布示意图
Fig.2 Gaussian distribution of intensity of transmitting fiber
假设反射面为理想镜面,在距离反射面d处接收光纤端面的反射光强度可看作距离2d处的发送光纤发出的光强度,即

则接收光纤所能接收的光功率为:

假设接收光纤中心处的光强为光纤端面处的平均光强,则

由公式(1)、(5)可推导出单光纤对的光强调制函数为:
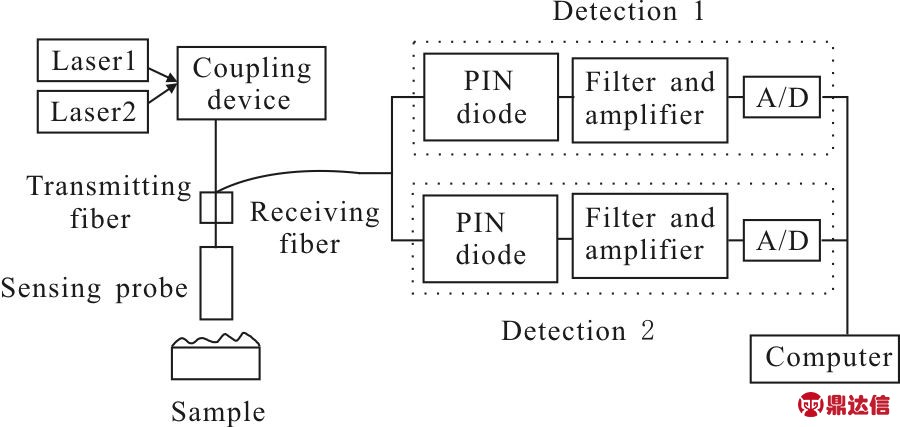
式中:b=p-r2,c=r1+2d tan(N1)。
由公式(6)可以看出,光强调制函数M与光纤对的结构参数、光纤性能参数以及距离d有关,当光纤对的光纤轴间距及光纤选定后,M主要取决于距离d。在NA2≥NA1(NA2为接收光纤的数值孔径)的条件下,将公式(6)简记为:

则光纤束的光强调制函数的表达式为:

根据Beckmann散射模型,粗糙表面的平均散射光功率[4]可表示为:

式中:s为散射系数,|
s|≤1;D为漫散射引起的不相干分量;g(
i,
s)因子[8]为控制镜向分量的相对大小,表达式为:

散射系数[8]为:

式中:0为光滑表面的散射系数;
i和
s分别为入射角和散射角;
为轮廓均方根偏差;
为入射光的波长。
当i=
s时,镜向散射系数和镜向散射平均功率分别为:
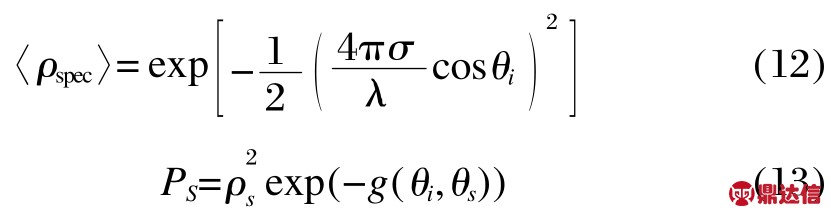
当一定波长的光垂直入射到粗糙表面时,i=
s=0,根据公式(10)、(12)及(13),可得镜向散射平均功率的表达式为:

光纤表面粗糙度传感器的光强输出为:

由公式(6)、(15)可以得到反射光强和表面粗糙度以及工作距离之间的关系。由于非系统误差(记为(
))严重影响了光纤传感系统的精密测量,采用多波长可以有效地减小非系统误差。设双波长分别为
1和
2,上述干扰因素对于双光源的影响结果分别记为
(
1)和
(
2),则方程(15)可以改为:
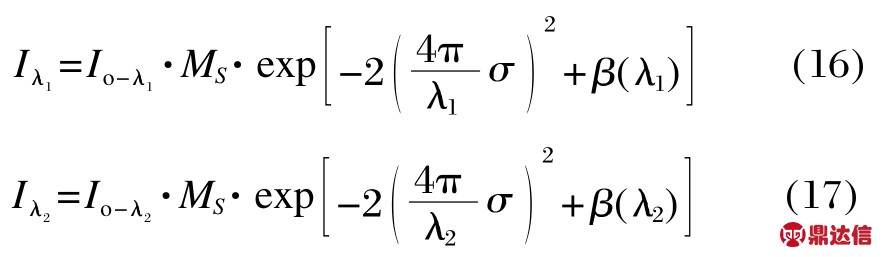
由于使用相同的光纤路径,可以认为(
)对双波长的影响相等,即
(
1)
(
2)。双波长的反射光强比值为:
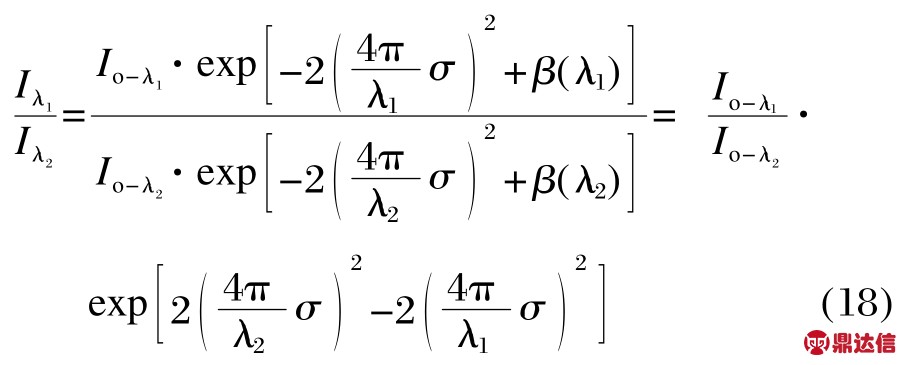
式中:1和
2为测量中的工作波长。从方程(18)中得到表面轮廓均方根偏差
的表达式为:

式中:I1和I
2分别是两波长下的反射强度,Io-
1和Io-
2分别是两波长下的入射强度。表面轮廓算术平均偏差Ra和表面轮廓均方根偏差
的关系为:
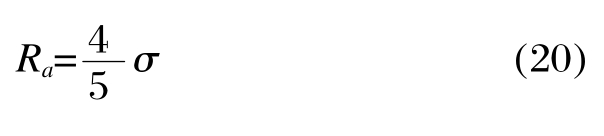
2 实验装置
表面粗糙度的测量系统如图3所示,系统由激光器、耦合装置、传感器、探测器、数据采集系统五部分组成。实验中采用三种不同波长的激光器作为入射光源,其中波长650 nm和1 310 nm作为一组光源,波长650 nm和1 550 nm作为另一组光源。
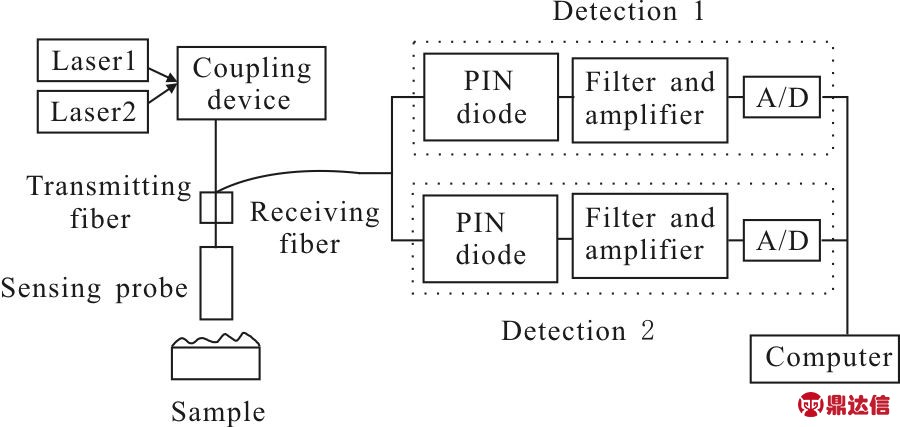
图3 改进的表面粗糙度检测光纤传感器的结构模型
Fig.3 Structure model of improved fiber optic sensor for measuring surface roughness
两种不同波长的激光器(1,2)发射出光,经光纤耦合器进入发送光纤,该光纤出射的光垂直入射到被测样品的表面,光线经被测表面相互作用之后,返回的反射光携带有被测表面的轮廓信息被接收光纤接收,接收光纤中的光信号再分成两个支路分别进入探测器一(光纤耦合硅探测器,型号:DET02AFC,波长范围为400~1 100 nm)与探测器二(光纤耦合InGaAs探测器,型号:DET01CFC,波长范围为800~1 700 nm)中,由于探测器只允许规定波长范围内的光线通过,所以利用两个探测器可以将两个不同波长的光源分开;然后经探测器将光信号转换为电压信号,再对电信号进行滤波放大预处理,经A/D转换后进入计算机,以电压信号来显示被测样品表面的散射光强。
3 表面粗糙度的理论模拟与实验
为了研究表面粗糙度对光散射特性的影响,选用哈尔滨市精密样板工具厂生产的外磨标准金属样品(符合GB6060.2-85标准,不同表面粗糙度Ra为0.10 μm,0.20 μm,0.40 μm,0.80 μm)作为测试样本进行检测,并与相关参数下理论模拟的计算结果进行比对分析。
3.1 粗糙表面的特征提取
当两组入射光源的波长为650 nm和1 310 nm,650 nm和1 550 nm时,三种不同波长下不同粗糙度样品的反射强度随着工作距离变化的模拟和实验结果如图4和图5所示。从两个图中可以看出理论曲线与实验曲线的趋势基本一致,图4中不同波长下不同粗糙度的模拟曲线比图5中的实验曲线平滑,且各曲线之间没有交叉点。从图中还可以看出:同一波长下,随着表面粗糙度的增大,以外磨样品为反射面测得的反射强度减小;同一波长、粗糙度下,随着工作距离的增加,反射强度先增大后减小,且在某一距离处反射强度有最大值;同一粗糙度下,入射波长越长,反射强度越大;多波长下测得的反射强度的变化比单波长下测得的反射强度的变化更明显;不同入射波长(650nm、1310nm、1 550 nm)下,不同粗糙度强度曲线的衰减率分别约为0.905%、12.1%、36.5%。所有曲线的趋势基本上相同,且特性曲线的前坡线性范围较小,但灵敏度较高。光反射强度在峰值区对表面粗糙度的变化最敏感,所以利用峰值区的反射强度可以计算表面粗糙度。实验中选择2 mm的工作距离作为最佳测量距离,在这个距离处测得的反射强度可以计算得到表面粗糙度值。
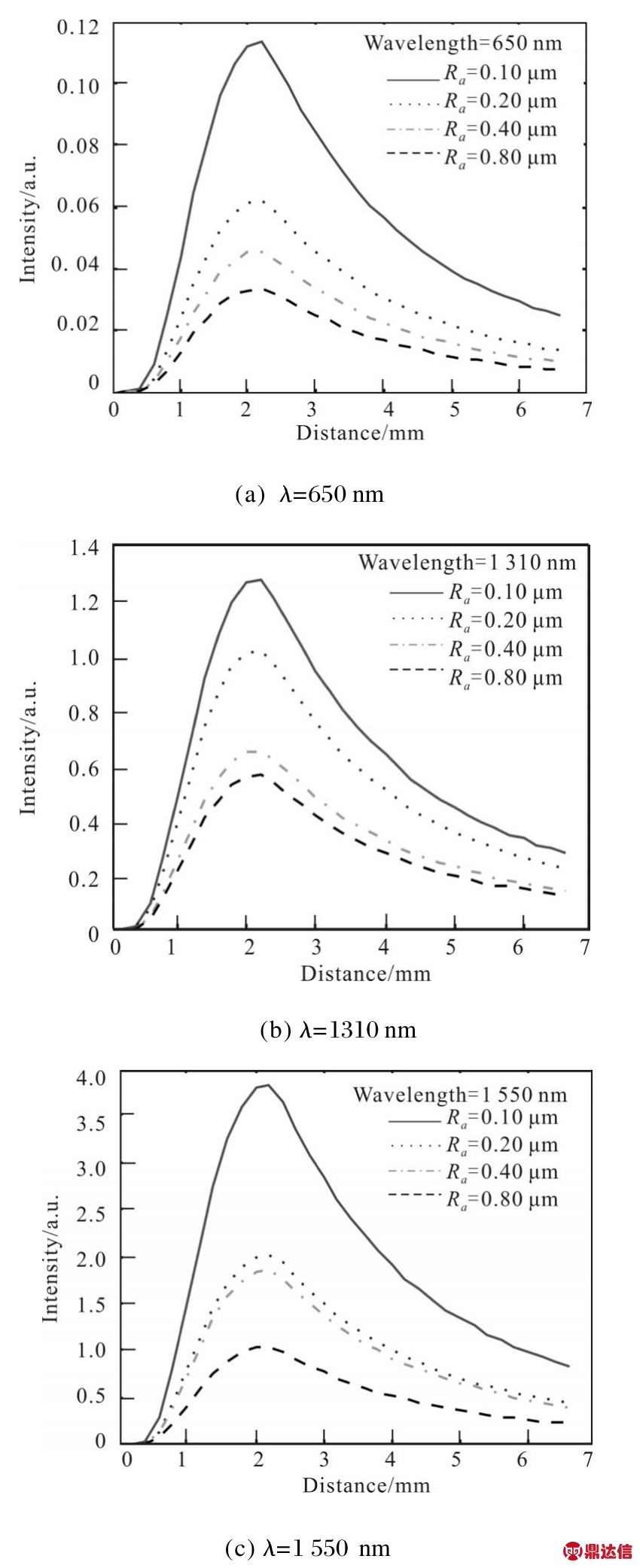
图4 不同波长下不同粗糙度(Ra=0.10 μm,0.20 μm,0.40 μm,0.80 μm)样品的反射强度随着工作距离变化的模拟结果
Fig.4 Simulated results on reflected intensity of grinding specimens (R
a=0.10 μm,0.20 μm,0.40 μm,0.80 μm)varying as working distance under the different wavelengths
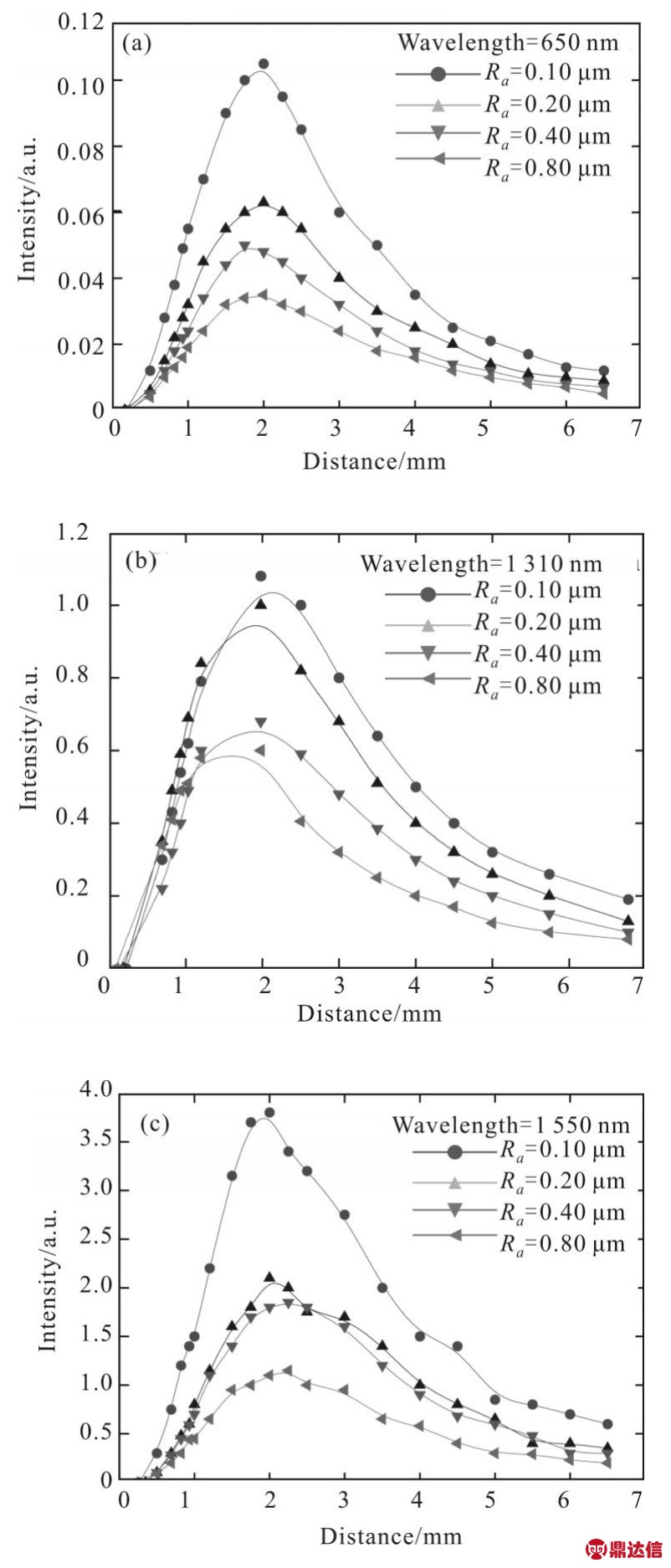
图5 不同波长下不同粗糙度(Ra=0.10 μm,0.20 μm,0.40 μm,0.80 μm)样品的反射强度随着工作距离变化的实验结果
Fig.5 Experimental results on reflected intensity of grinding specimens(Ra=0.10 μm,0.20 μm,0.40 μm,0.80 μm)varying as the working distance under the different wavelengths
3.2 表面粗糙度的测量及误差分析
三种不同波长下不同粗糙度样品的理论数据与实验数据的差值如图6所示,从图中可以得到各个波长下所得到的实验数据与理论结果之间的误差,从而可以得到2 mm工作距离处反射强度的相对误差,进而可以计算得到双波长下测量表面粗糙度的相对误差。当入射波长为650 nm时,测量不同粗糙度样品(Ra=0.10 μm,0.20 μm,0.40 μm,0.80 μm)传感器的相对误差分别为4.98%、4.30%、7.87%、6.38%;而入射波长为1310nm时,传感器的相对误差分别为12.44%、1.31%、7.51%、8.46%;入射波长为1550 nm时,传感器的相对误差分别为0.804%、5.12%、1.70%、6.63%;从上述分析中可以计算得到多波长光纤传感器测量表面粗糙度的相对误差范围大约为3.56% ~7.43%,进一步可以得到传感器的平均相对误差为5.625%。
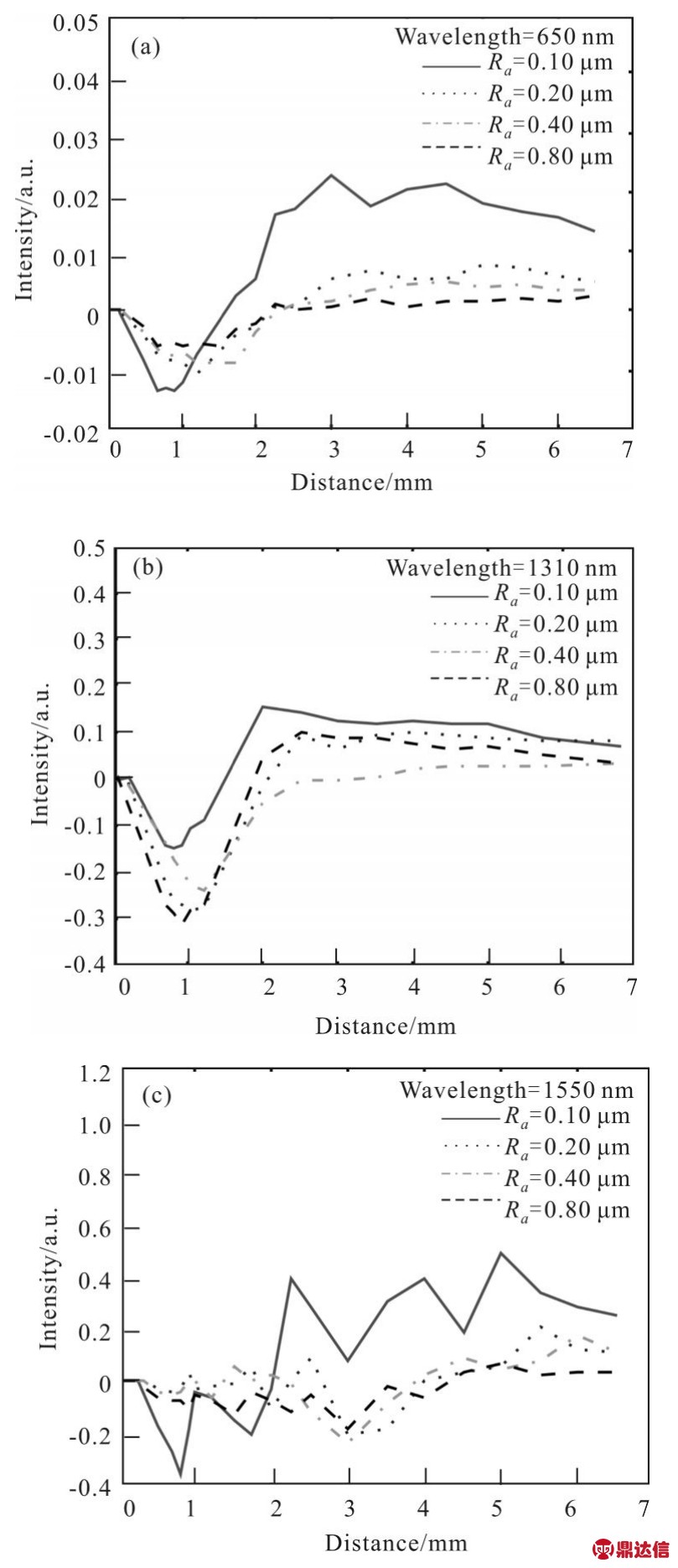
图6 不同波长下不同粗糙度样品的误差曲线
Fig.6 Error curves of grinding specimens with different roughness under different wavelengths
4 结 论
非接触式的光学测量法对于测量粗糙表面的散射特性和表面粗糙度具有十分重要的研究意义。文中基于激光散射原理提出了一种在线测量表面粗糙度的方法,通过测量表面反射强度的比值可以得到表面粗糙度值。利用已知粗糙度的样品作为测试样本,研究粗糙表面的散射特性以及系统的测量误差。
结果表明同一波长下,随着表面粗糙度的增大,以外磨样品为反射面测得的反射强度减小;同一粗糙度下,入射波长越长,反射强度越大;多波长下测得的反射强度的变化比单波长下测得的反射强度的变化更明显,这里选取峰值区的强度值来计算表面粗糙度值。该系统在测量中不仅可以消除非系统误差,还能减小系统误差,提高了测量的准确率。计算得到系统的相对误差范围大约为3.56%~7.43%。