摘 要:分析了吸污车真空泵由于旋片顶部圆弧设计尺寸过小存在的旋片磨损问题。经过对旋片不同顶部圆弧设计半径的真空泵进行测试,结果表明:旋片顶部圆弧半径小的真空泵其驱动功率大,建议加大旋片圆弧半径尺寸,以接近理论计算值为佳。
关键词:真空泵;旋片;顶部圆弧;磨损
吸污车是抽排城市粪便、污泥等污物的专用车辆。它是由汽车底盘、真空系统组成。真空系统主要包括真空泵、油气分离器、水气分离器、四通阀、罐体等。其工作原理是真空泵抽吸罐内空气,使罐内形成负压,在大气压力的作用下,粪便或污泥被吸入罐内。真空泵是形成负压、抽吸污物的主要部件。
1 真空泵结构与工作原理
真空泵主要由泵体、转子、旋片、铜套、前后端盖等组成,见图1。
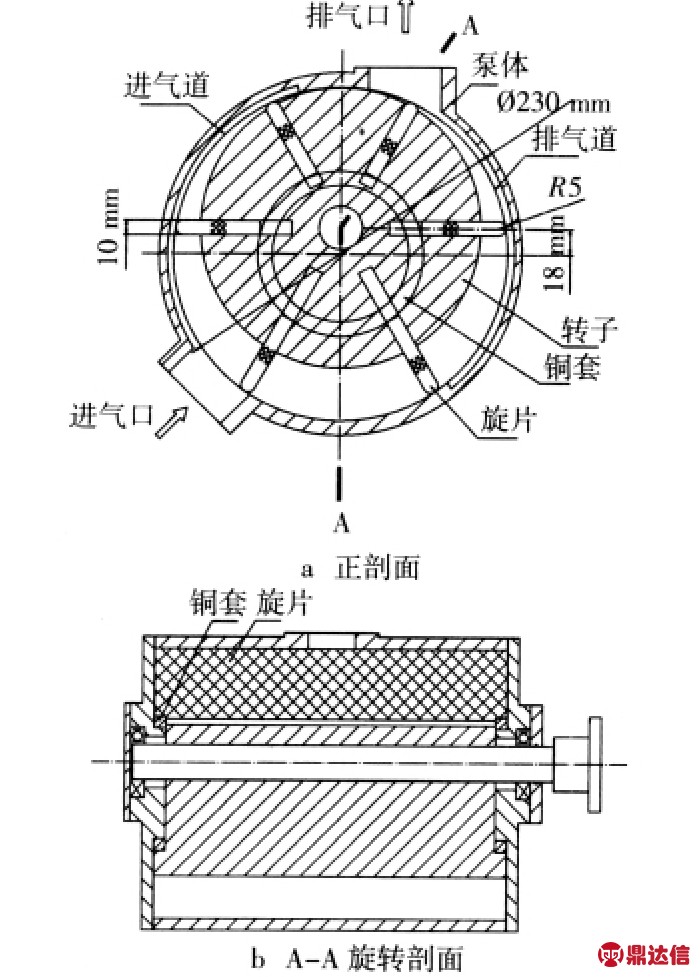
图1 真空泵结构剖面示意
转子上加工有6道槽,槽内安装旋片,转子与泵体的轴线有一个偏心距离,转子旋转时,旋片在铜套挤推和离心力的作用下,其顶部与泵体内腔始终保持接触,旋片将泵体和转子之间分成6个空间,由于存在偏心距离,使每个空间的容积不同,容积由小变大为吸气过程,由大到小为排气过程,吸气口与罐体相通,通过真空泵的连续运转,不断抽吸罐内空气,以此使罐内形成负压,在外界大气压的作用下,污物通过吸污管抽进罐内。
为减少真空泵运动部件的磨损,润滑系统为所有运动部件提供润滑。旋片连续旋转其顶部与泵体内腔形成油膜,使旋片与泵体内腔得到无接触润滑。为减少旋片的磨损,旋片的顶部加工成圆弧型,以减少运动阻力,且不发生跳动现象。
2 真空泵旋片磨损问题
目前所使用的真空泵为单级旋片泵,在使用过程中存在泵片磨损快、功率消耗大、润滑油升温快、工作噪声大、性能不稳定的问题。根据旋片磨损情况分析发现,磨损部位在旋片顶部圆弧顶点附近,占圆弧长度很小部分,说明主要是旋片顶部圆弧半径尺寸设计存在问题。旋片的顶部加工成圆弧型,减少了旋片旋转过程中的运动阻力。圆弧半径尺寸大小不同,使旋片顶部与泵体间形成油楔不同,油楔高度大,润滑油在此空间给转动旋片的反作用力大,增加了旋片的运动阻力,形成泵片磨损快、功率消耗大等问题。图2为旋片顶部圆弧半径分别为5、15 mm,其油楔最大高度分别为5、0.86 mm,油楔油压作用面积前者是后者的1.6倍。
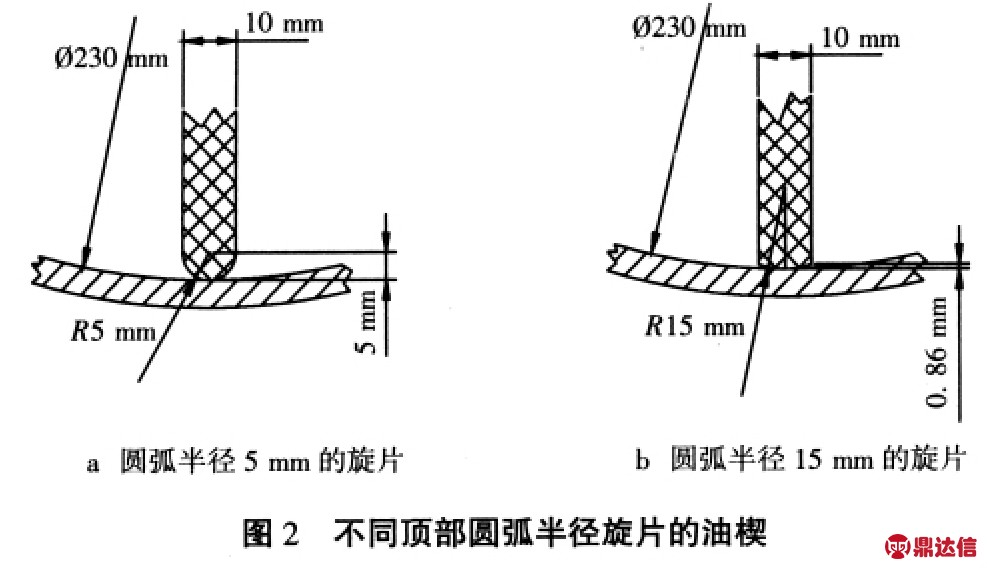
3 旋片顶部圆弧结构尺寸计算
3.1 旋片顶部圆弧半径公式推导和计算
其中β为旋片与泵体接触点A处公法线与旋片中心线的夹角,ε为旋片中心线与转子、泵体内腔中心连线的夹角,e为泵体中心与转子中心的偏心距,O为转子中心,O1为泵体中心,R为泵体内腔半径,B为旋片厚度,r为旋片顶部圆弧半径,见图3。
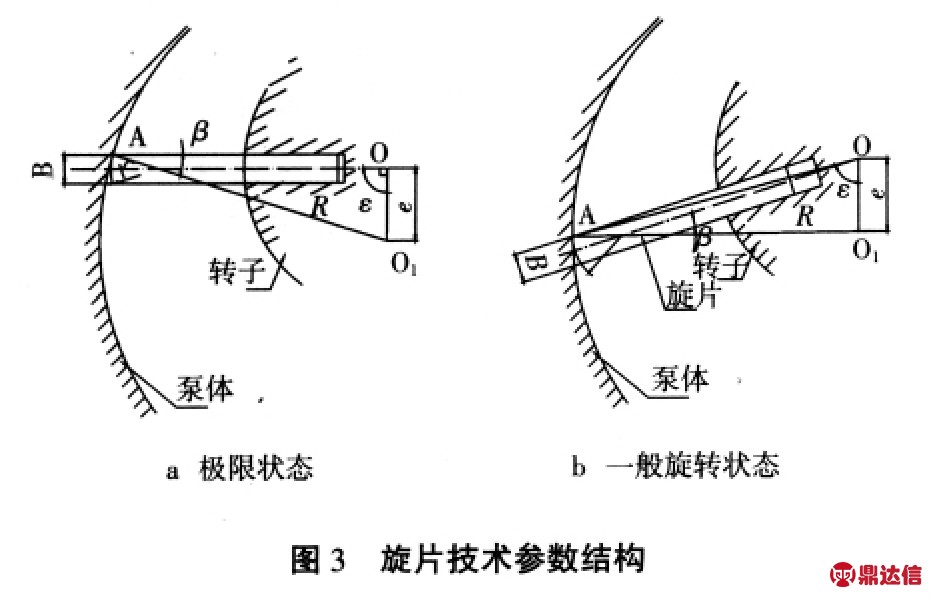

当β为最大值时,接触点A移到旋片顶端圆弧边缘点;
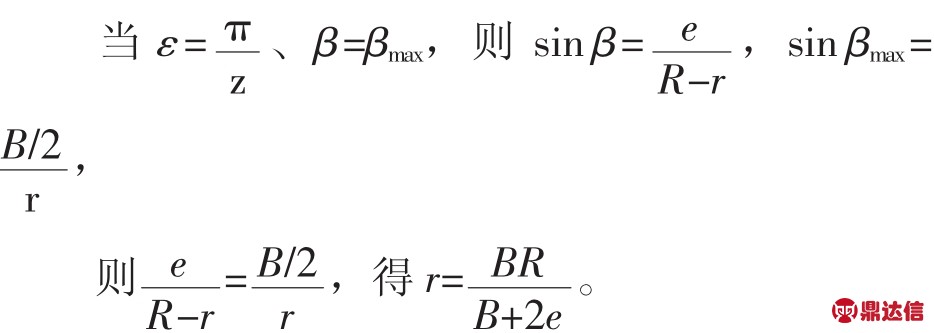
3.2 计算分析
抽气速率5 m3/min真空泵的技术参数为:偏心距e=18 mm,泵体内腔半径R=115 mm,旋片厚度B=10 mm,旋片顶部圆弧半径r=5 mm,在e、R、B不变的情况下,计算理论值。
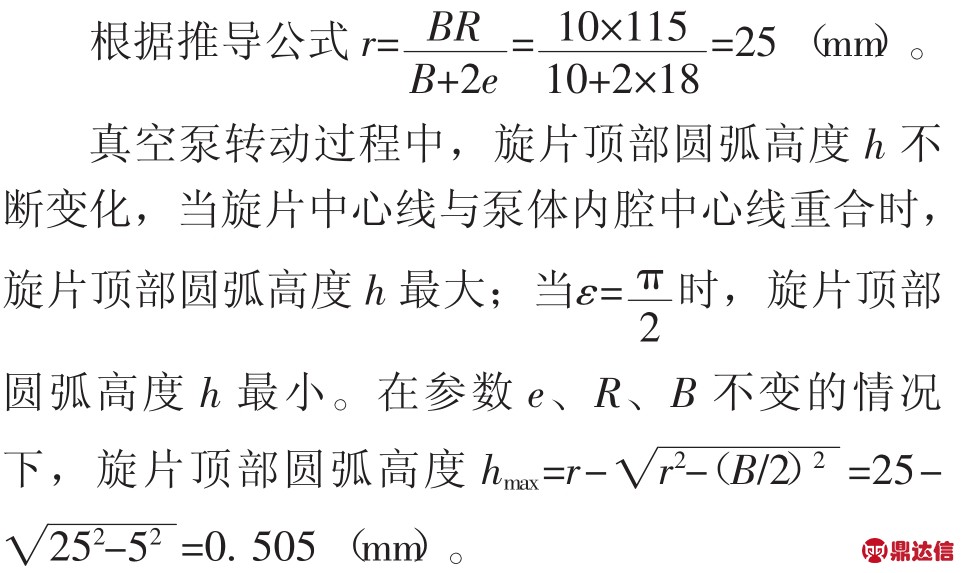
真空泵工作时,旋片顶部圆弧与泵体内腔形成收敛型油楔,油楔高度随旋片顶部圆弧减小而增大,油楔高度增大,使旋片承受反向圆周力,径向力增大,使旋片磨损快,润滑油温升高、噪声大(旋片撞击泵体),造成真空泵功率增大。
4 试验测试
根据上述情况分析及计算,对不同顶部圆弧半径的旋片进行试验测试,测试其参数变化情况。
在真空泵内分别安装顶部圆弧5和15 mm的旋片进行试验测试,在真空泵转速为300和600 r/min工况下,将真空泵压力调整到0.090 MPa和0.094 MPa得出4组试验数据,见表1。
表1 不同真空压力下的4组试验数据
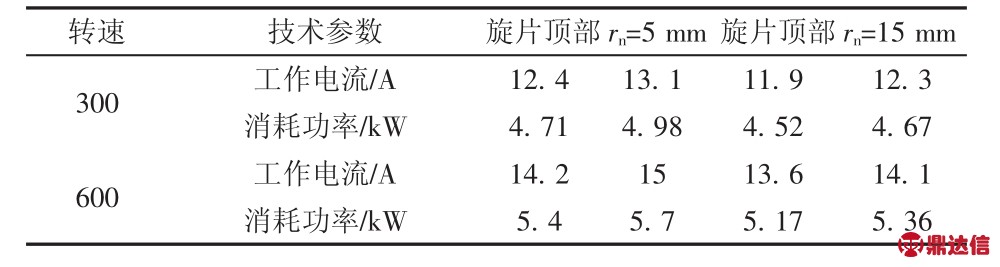
注:消耗功率为工作电流乘以电压。
试验数据显示,旋片顶部圆弧大的真空泵在相同真空度工况下,功率消耗比旋片顶部圆弧小的真空泵功率消耗小,说明其工作阻力小,噪声和磨损相应减少,能延长真空泵的使用寿命。
5 结论
经过计算可知,吸污车真空泵存在的旋片磨损问题是由旋片顶部圆弧设计尺寸过小造成的。对2种不同顶部圆弧半径旋片的真空泵测试结果表明,旋片顶部圆弧小的真空泵其驱动功率大,建议加大旋片圆弧尺寸,接近理论计算值为佳。