摘 要:薄壁件在多点柔性工装系统定位和支撑作用下,支撑单元布局对其加工变形的影响尤为明显。为此,结合有限元技术、正交实验理论和多元非线性回归的方法,提出以支撑单元的布局为设计参数,建立以薄壁件的最大变形和平均变形为指标的加工变形预测模型。为了简化计算,采用加权的方法将多目标预测模型转化为单目标预测模型,进一步以该单目标预测模型为目标函数,采用全局寻优能力较强的遗传算法进行优化计算,得到理论最优的装夹布局。实验结果表明:多点柔性工装系统的装夹布局与薄壁件的加工变形确实有非线性回归关系,且通过遗传算法得到的最优装夹布局,经过加工分析其最大变形量和平均变形量分别比均匀分布布局降低了53.0%和54.4%,比正交实验最低降低了19.0%和8.9%。
关键词:薄壁件;多点柔性工装;支撑单元布局优化;多元非线性回归;遗传算法
近年来,许多学者对大型薄壁件的加工变形控制问题进行了深入研究,随着自动化水平的不断提高,多点柔性工装系统成为研究的热点,它能够有效地解决大型薄壁件在铣削加工中的变形问题,但是传统的装夹方法一般采用均布分布和密集支撑的方法,浪费了大量的资源占用量和调配时间。因此,多点柔性工装系统的优化方法得到了关注,张晓峰、周凯等[1]通过有限元方法对薄壁件多点柔性加工变形进行分析,并总结相关变形规律;陆俊百、周凯等[2-4]提出了自适应优化的方法和遗传算法两种方法优化装夹布局,经过优化分析得到了最优布局,使资源得到最佳利用,且满足高速高精度加工需求。
在多点优化领域,多元非线性回归的方法得到了广泛的利用,赵茂俞、薛克梅等[5]通过多元非线性回归的方法建立拉伸筋截面凸筋圆角半径、拉伸筋的高度与最大等效应力、最大变薄率之间的数学模型,并优化出最优解;卢庆华、徐济进等[6]研究了焊接热输入、振动加速度对焊接最高温度的影响,并运用多元非线性回归的方法建立焊接最高温度的预测模型。
本文主要针对航空薄壁件,采用多点柔性工装系统对其铣削过程建立了有限元仿真模型。设计不同支撑单元装夹布局分布的正交实验,得到相关数据,运用多元非线性回归技术建立加工变形与装夹布局的预测模型,通过相关性检验和线性回归的显著性检验证明模型的可行性。把预测模型作为遗传算法优化的目标函数,为了简化计算,用加权的方法将多目标转化为单目标函数,借助遗传算法的全局寻优能力,对多点柔性工装系统支撑单元布局优化分析,得到理论最优支撑单元布局。该方法为多点柔性工装合理地选用支撑单元布局以控制薄壁件加工变形提供了有效途径。
1 多点柔性工装系统和有限元模型
1.1 多点柔性工装系统
多点柔性工装系统的结构图如图1所示。该系统主要由底座、动梁(X向导轨)、Y向导轨、Z向调整支柱、万向真空吸头和真空发生器等组成,该系统通过吸附装置对吸盘进行真空处理,使得吸盘的真空吸附力对薄壁件进行夹紧,吸盘内部安装支撑体,通过吸盘内部的支撑体对薄壁件进行定位,根据实际需要布置m×n方阵阵列的支撑单元单元,底座上有m个动梁沿底座上的导轨做X向移动,动梁上的n个支撑单元沿动梁做Y向移动,每个支撑单元可以沿Z向调整[7]。
在加工过程中柔性工装系统和薄壁件的受力示意图如图2所示。图中:G为工件重力,当在加工过程中为铣削力F和G;Fx为真空吸盘吸力,作用于整个吸盘范围内,单位面积上的吸力取决于真空度的大小;FN为支撑反力作用于接触点,沿接触面法线方向向外;δ为薄壁件加工时的最大变形;Δ为工件厚度;d为两个支撑单元间的距离。
1.2 有限元模型的建立
本文利用有限元分析软件ABAQUS对薄壁件和柔性夹具的装配模型简化并进行变形分析,建立多点实体支撑模型如图3所示,薄壁件选用7050-T7451铝合金,长×宽×厚=300 mm×150 mm×4 mm,弹性模量E=71.7 GPa,泊松比λ=0.3,密度ρ=2 820 kg/m3,吸盘直径为20 mm,在真空度为-0.7bar时脱离力Ft=16.3 N,内部支撑体选用φ=10 mm的中碳钢,弹性模量E=209 GPa,泊松比λ=0.3,密度ρ=7 800 kg/m3。
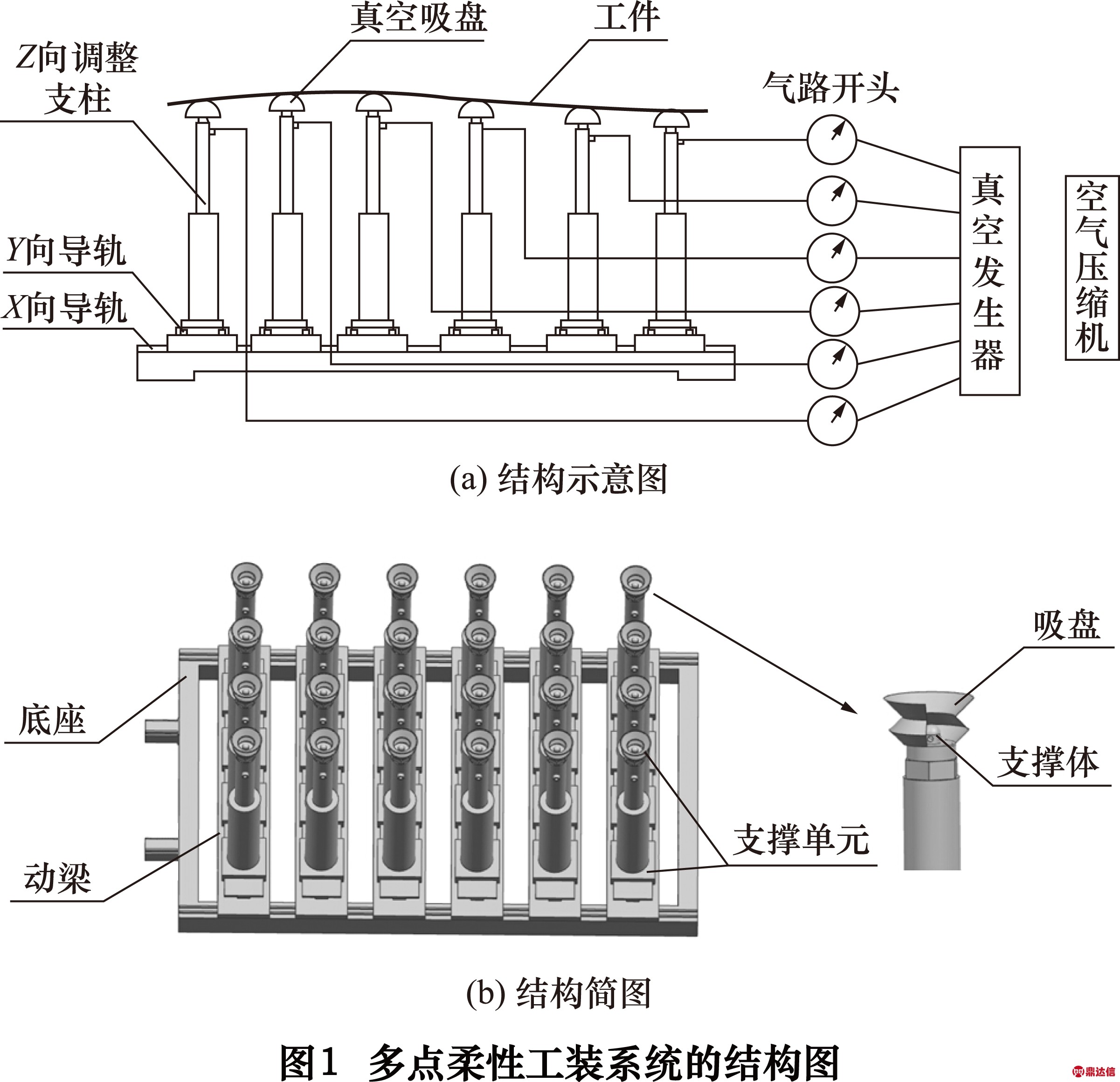
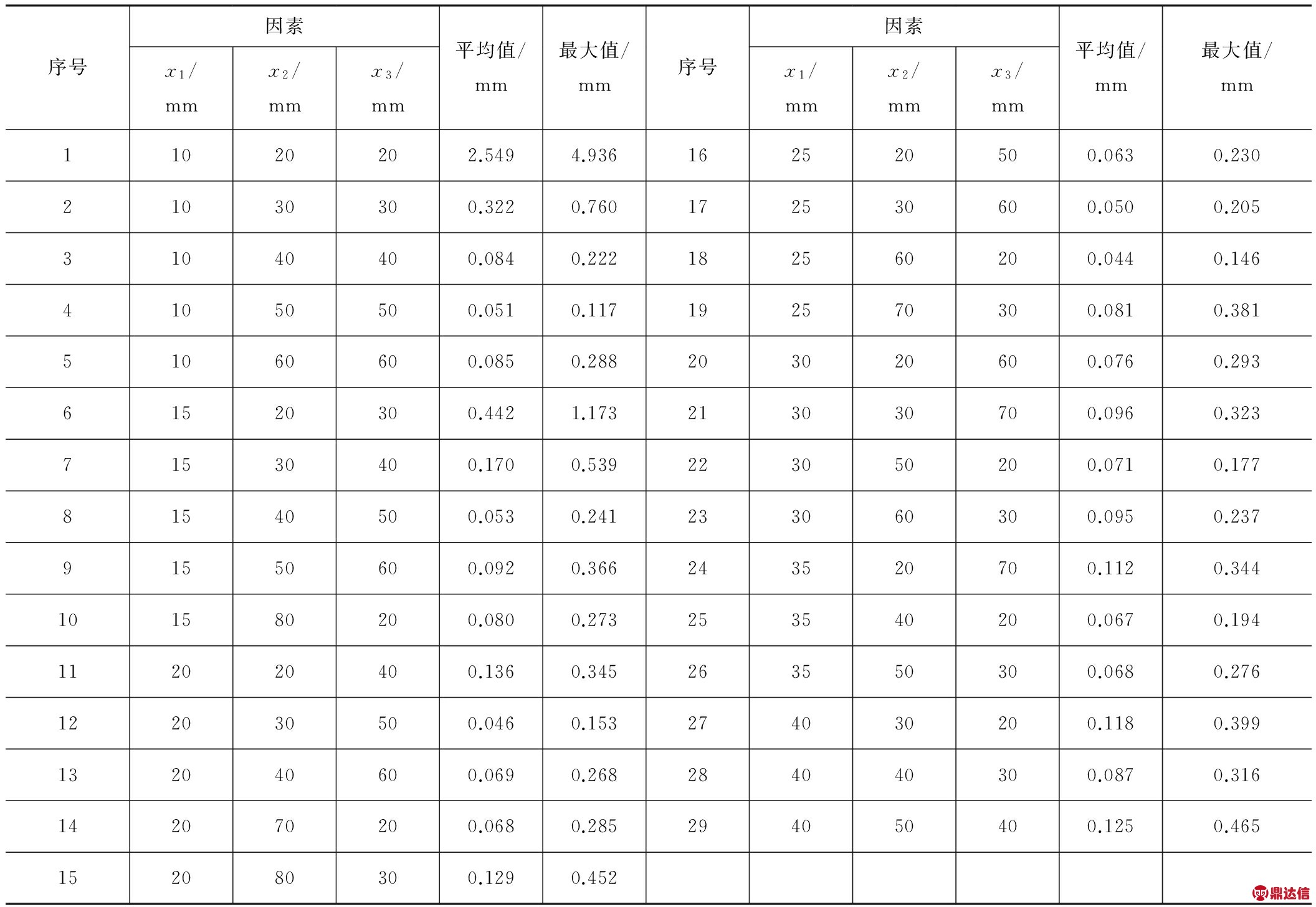
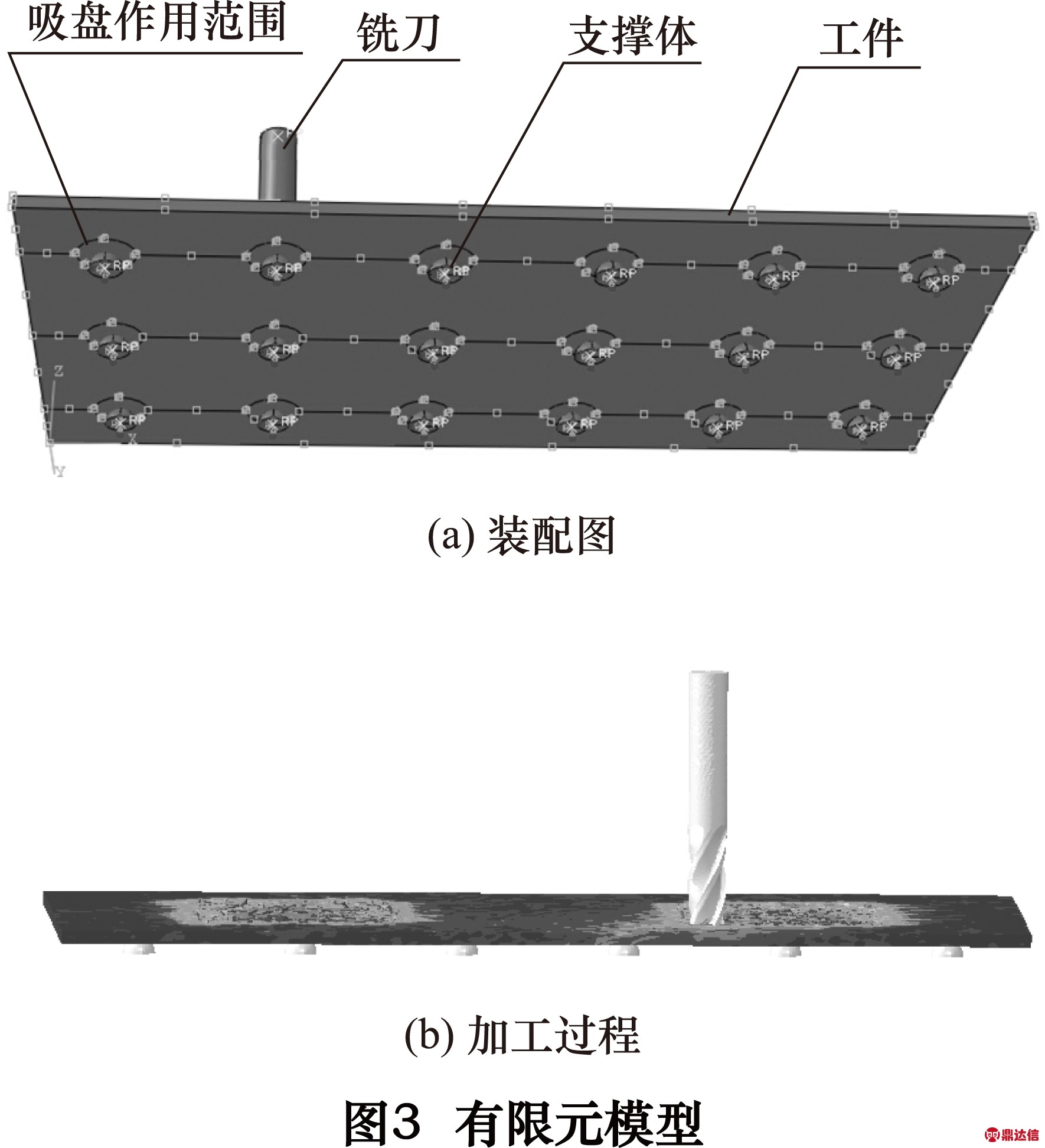
2 多元非线性回归模型的建立与验证
在多点柔性工装系统的装夹下,除了传统引起加工变形的原因(如装夹力、铣削力等),支撑单元的布局对其加工变形的控制尤为重要,以3×6布局为例,运用多元非线性回归的方法,总结其装夹布局和加工变形的预测模型,为以后的遗传算法优化做准备工作。
2.1 多元非线性回归模型
根据整个薄壁件的对称性,同时为了便于计算和减少计算量,建立两个预测模型,如图4所示,第一个预测模型以薄壁件的1/2为研究对象,以薄壁件的最大加工变形和平均加工变形为因变量,支撑单元的横向间距(即动梁间距x1、x2、x3)为自变量;第二个预测模型以薄壁件的1/4为研究对象,以薄壁件的最大加工变形和平均加工变形为因变量,支撑单元纵向边距(y1、y2、y3)为自变量。采用正交设计制定实验方案,对实验方案进行模拟数值计算,回归出不同支撑单元对加工变形影响的预测模型。
设计数值模拟方案,分别仿真模拟薄壁件的铣削加工过程,获得加工过程中最大变形和平均变形的结果,即多元非线性回归样本数据。第一个预测模型的多元非线性样本数据如表1所示,第二个预测模型的多元非线性样本数据如表2所示。
多元非线性回归处理多变量参数与目标函数之间的非线性拟合数学关系方程式为[8]:

(1)
式中:f(x)为因变量;β为待定多项式系数:m为设计变量数;xj、xi为自变量。
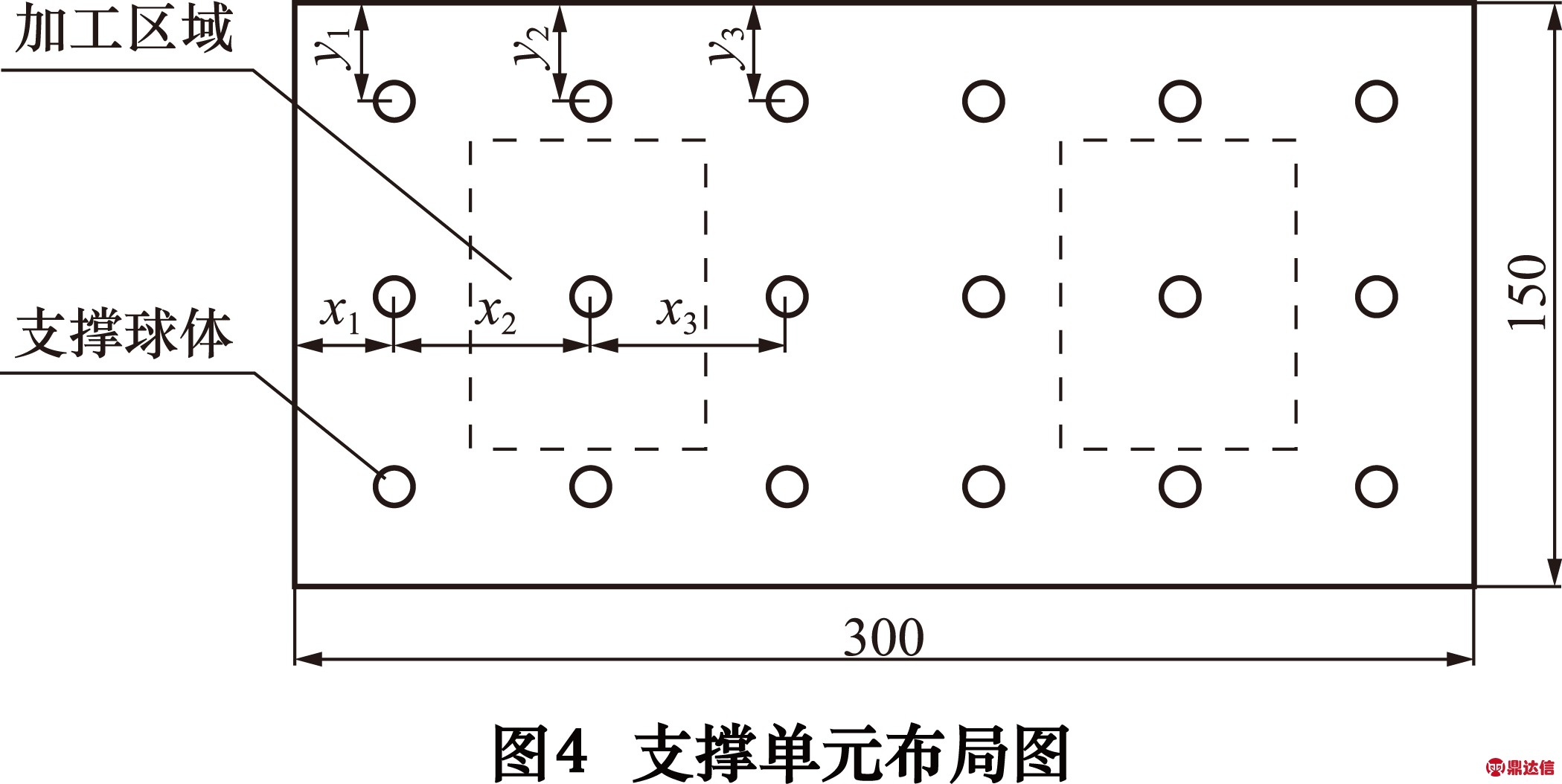
薄壁件铣削加工模拟实验数据回归分析的第一个预测模型自变量有动梁间距x1、x2、x3,因变量平均变形量fave(x)和最大变形量fmax(x),样本数据如表1所示;第二个预测模型自变量支撑单元边距y1、y2、y3,因变量平均变形量fave(y)和最大变形量fmax(y),样本数据如表2所示。运用Matlab软件数值计算,最后得到薄壁件变形量与支撑单元布局的多元非线性回归方程。
表1 第一个预测模型多元非线性样本数据
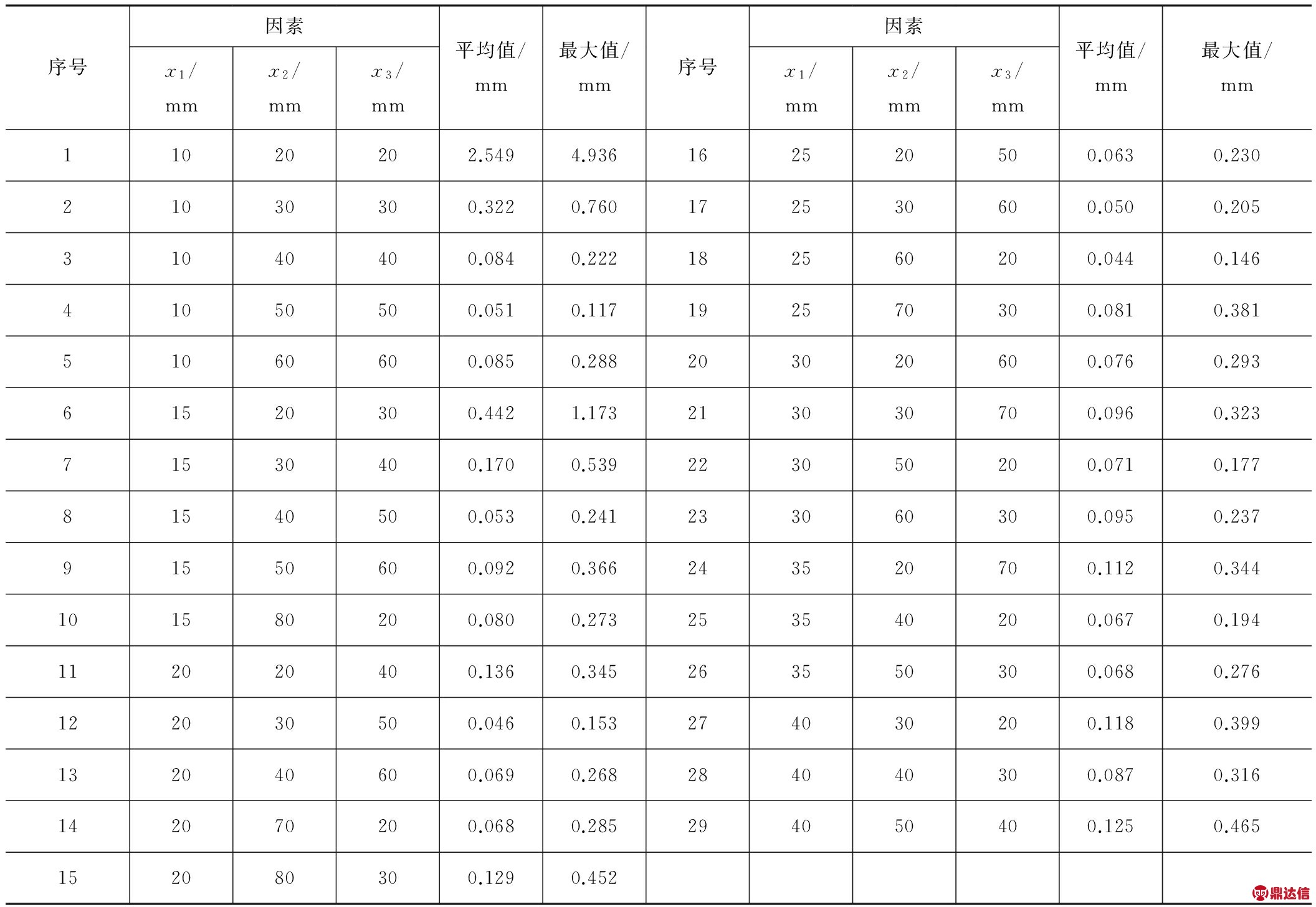
表2 第二个预测模型多元非线性样本数据

第一个预测模型:

(2)
第二个预测模型:

(3)
2.2 回归模型的检验
根据多元非线性回归的检验方法,对回归方程进行相关性检验和显著性检验[9-10]。相关性表示自变量与因变量的线性关系,可以用相关系数R来表示他们之间的密切程度。
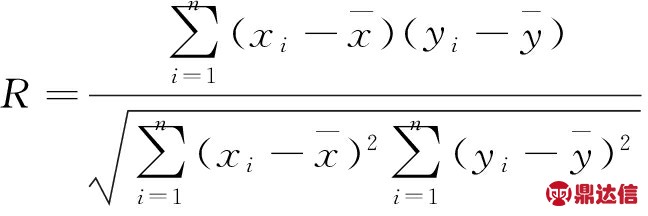
(4)
越接近1,表示自变量与因变量关系越密切,拟合效果越好。通过回归,得出第一个预测模型的两个方程的相关系数为别为0.988 3和0.965 4,第二个预测模型的两个方程的相关系数分别为0.990 1和0.985 0,结果都非常接近1。因此,可以确定该两种模型的拟合效果非常好。
对于线性回归的显著性检验,给定显著水平α

(5)
式中:P为概率;F为线性回归显著性检验方法;p为自由度;n为样本数。
回归计算得出F的数值,在给定的显著性水平下,若
F≥Fβ(p,n-p-1)
(6)
则认为线性回归显著,本模型经回归后,第一个预测模型的F值为188.6和160.1,第二个预测模型的F值为98.6和100.1,均远大于从文献[7]查表所得到的F值。因此,可以确定线性回归显著。可见,该数学模型能够精确地反应变形量与支撑单元布局之间的关系。
3 装夹布局优化
本章所建立的两个预测模型需要对其进行分别优化计算,但每个预测模型均有两个因变量平均变形量fave和最大变形量fmax,属于多目标优化,为了简化计算,选择将多目标转化为单目标优化的处理方法[11],在薄壁件的铣削加工过程,平均变形量反映的是整体的变形情况,而最大变形量是薄壁件的局部最大变形,两种变形结果都反映整薄壁件加工变形的重要信息,取其权重相等,即k1=k2,那么第一个预测模型的单目标函数变为
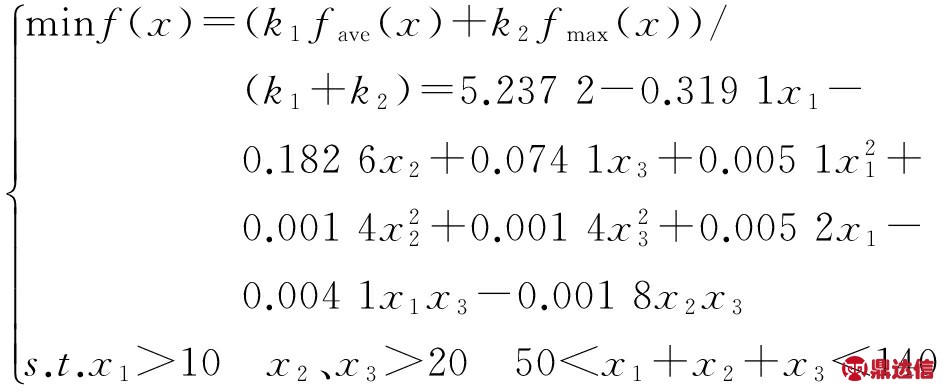
(7)
第二个预测模型的单目标函数变为
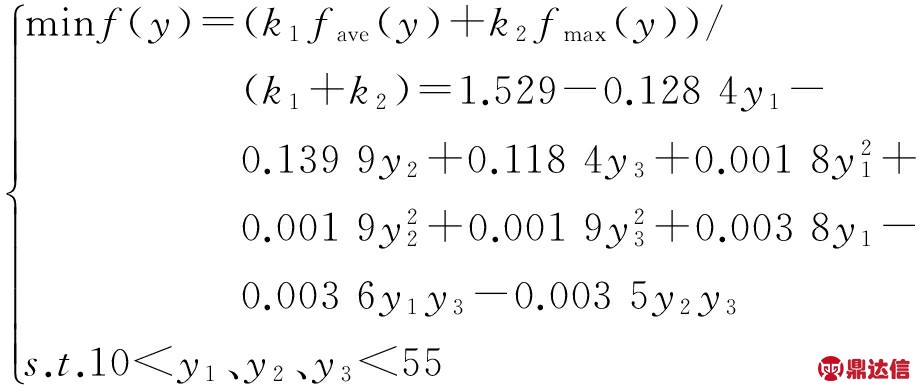
(8)
遗传算法对支撑单元布局优化流程图如图5所示。
运用MATLAB编程进行进行GA运算,以式(7)和(8)分别作为优化的目标函数,经过迭代最终获得各支撑单元布局优化过程的收敛情况如图6所示,其中横坐标是进化代数,纵坐标为目标函数值(适值),由图看出,随着遗传算法优化的不断进行,加工变形量不断降低。最终获得支撑单元布局的最优结果如表3所示。
如图7所示为均匀分布布局和最优布局的布局情况和变形情况的对比。
根据多点柔性夹具的运行原理,并通过有限元、多元非线性回归和遗传算法最终总结出使得薄壁件加工变形最小的布局方案,从变形云图中明显可以看出GA优化的最优方案明显优于传统加工过程中的均匀布局。通过表4我们可以清晰、直观比较出均匀布局,正交实验最优结果和GA最优结果中的最大变形和平均变形。GA最优布局平均变形量比均匀布局降低了54.4%,比正交实验最优结果降低了8.9%;最大变形量比均匀布局降低了53.0%,比正交实验最优结果降低了19.0%。
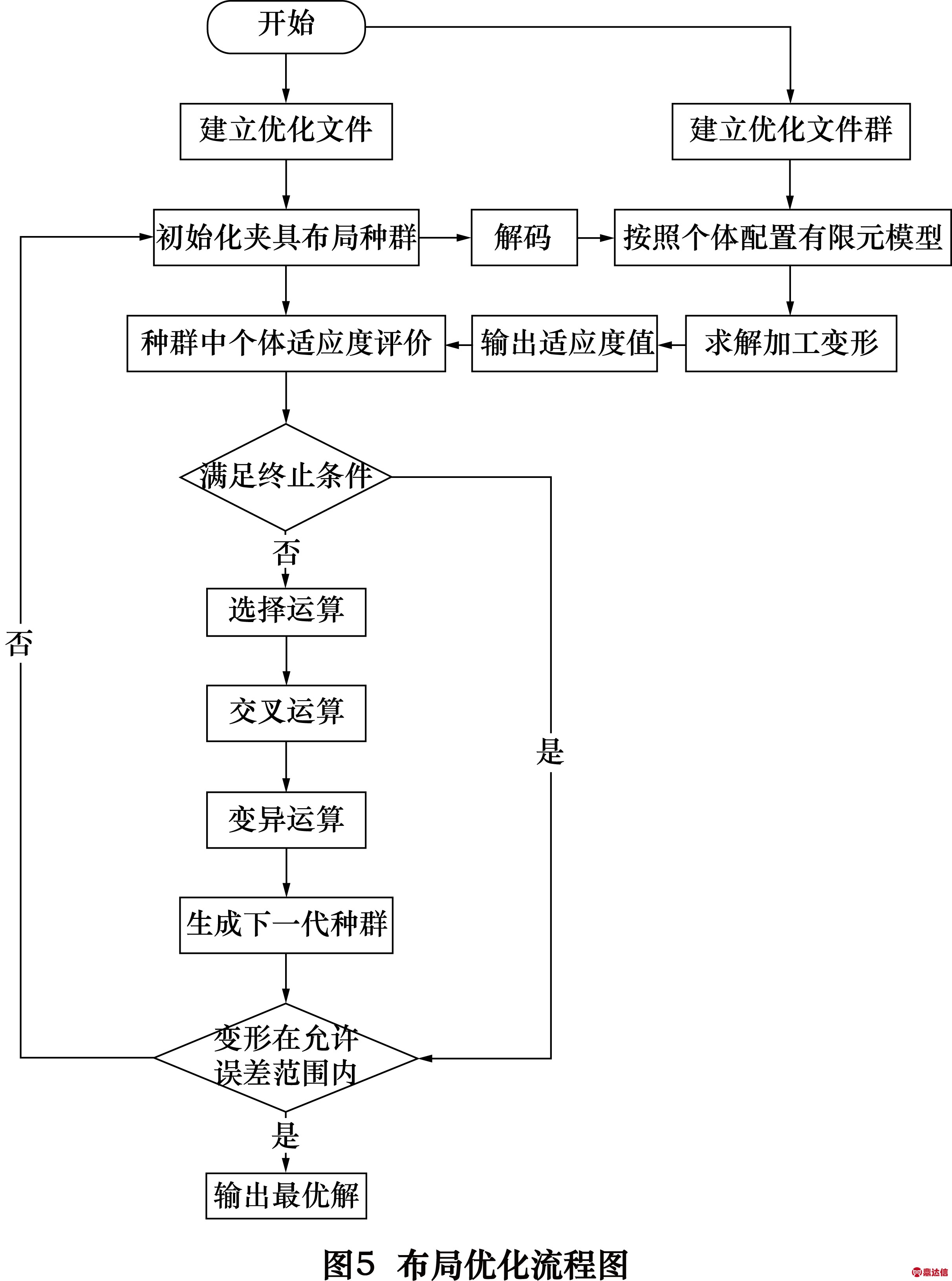
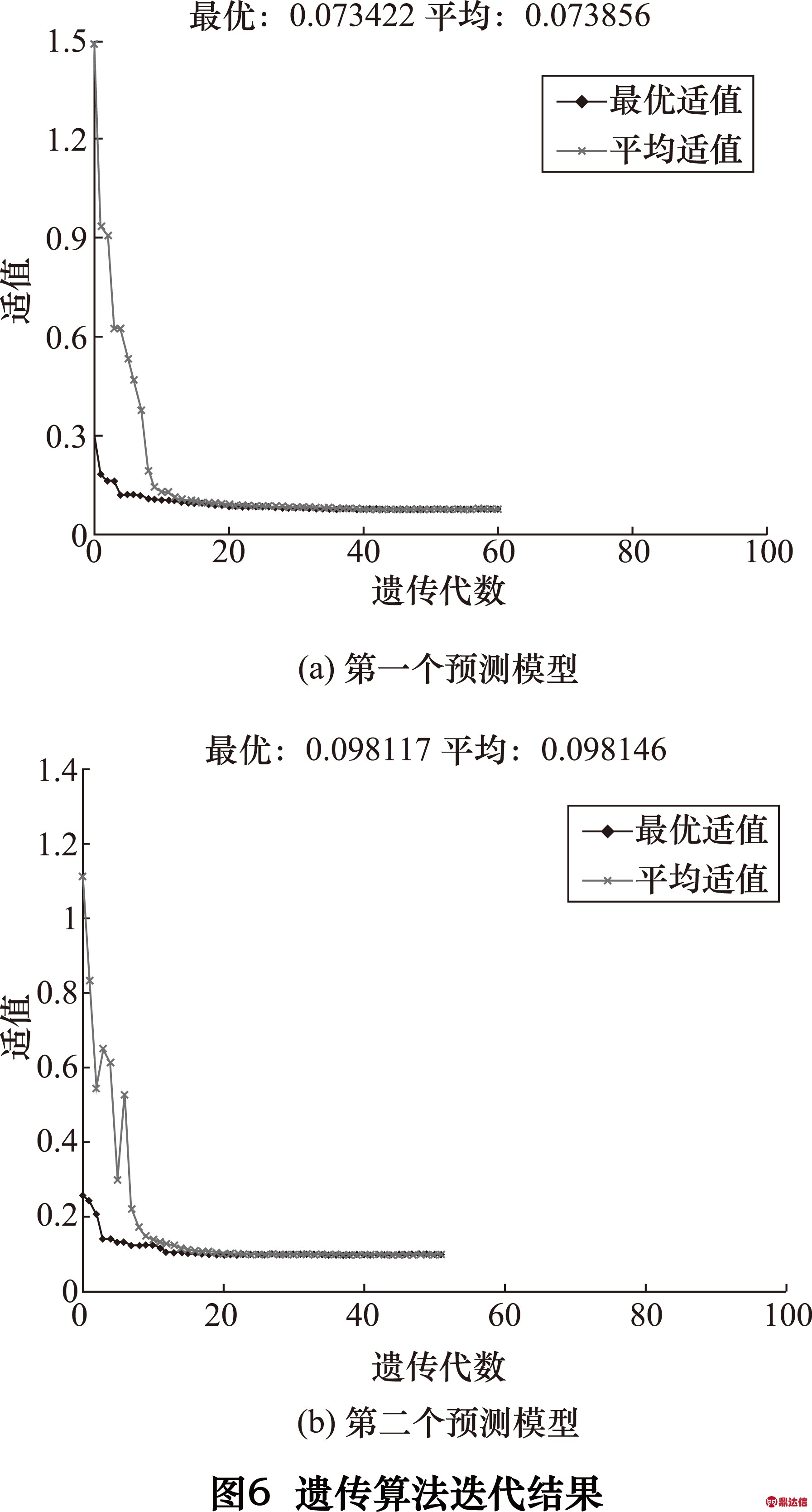
表3 支撑单元最优布局

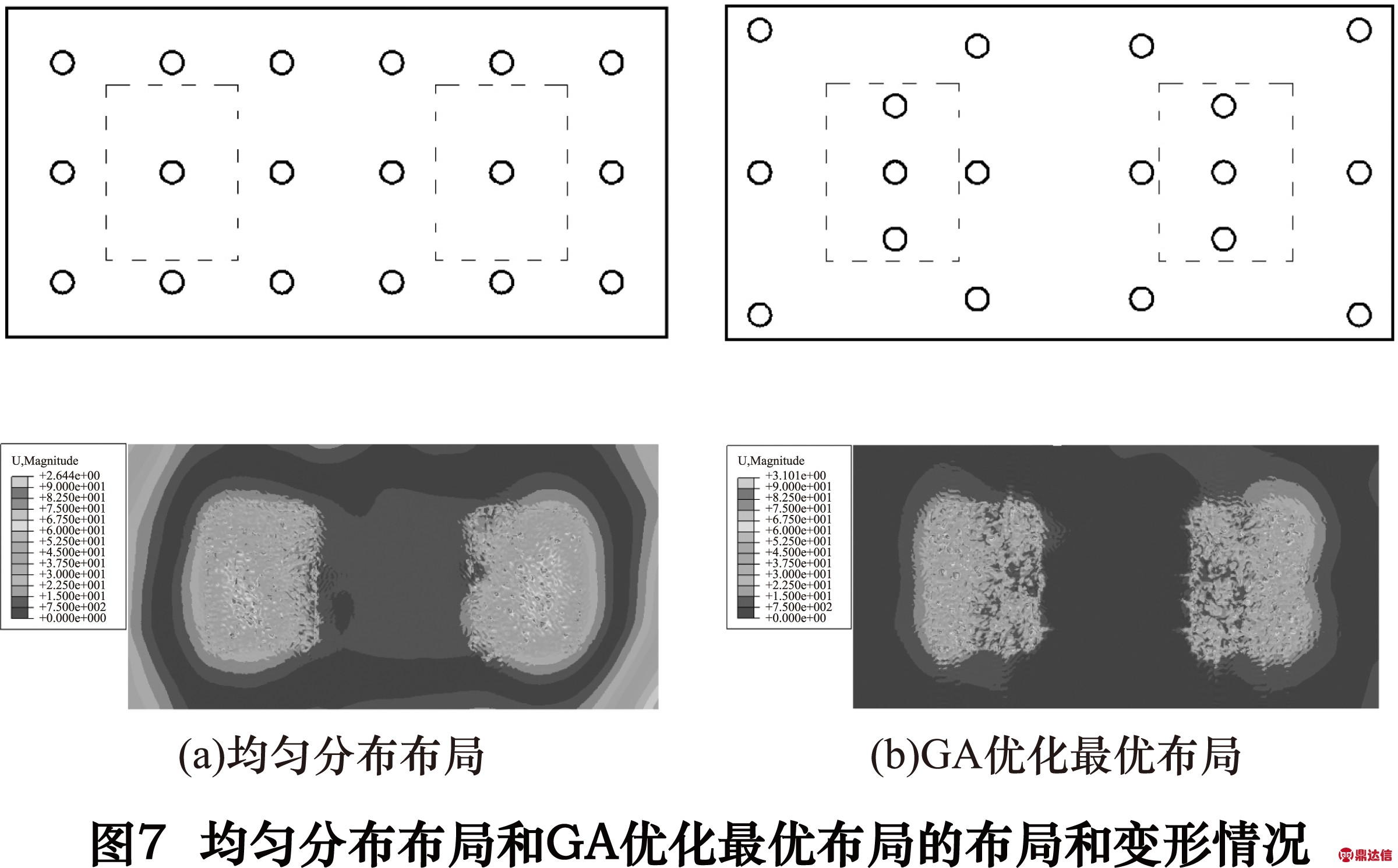
表4 变形结果对比
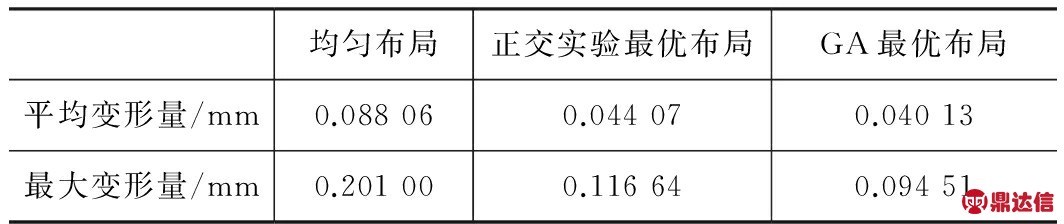
4 结语
(1)以横向动梁间距和纵向支撑单元间距为因素,建立两组正交实验,运用有限元的方法进行模拟加工,分别得到每组实验薄壁件的最大变形量和平均变形量。运用MATLAB软件,采用多元非线性回归的方法拟合出两组支撑单元布局和薄壁件加工变形(最大加工变形和平均加工变形)之间的回归方程。通过对两组回归方程的显著性和相关性检验,可知回归方程的有效性和准确性。
(2)通过加权处理,将两组多目标预测模型转化为单目标预测模型,运用MATLAB软件编程并进行GA运算,根据目标函数(加工变形预测模型)对个体适应度进行评价,依据优胜略汰的进化规则,以全局并行搜索方式来求得最优的支撑单元布局。通过对最优支撑单元布局的模拟加工得到GA最优布局平均变形量比均匀布局降低了54.4%,比正交实验最优结果降低了8.9%;最大变形量比均匀布局降低了53.0%,比正交实验最优结果降低了19.0%。