摘要:目的针对以往载人航天应用系统中电子设备热设计的仿真分析方法不准确的问题,提出一种基于热平衡试验测量发热元器件温度数据验证热仿真分析结果的电子设备热设计方法。方法通过对应用系统电子设备在轨实际热工况条件的深入分析,结合电子设备的物理特性、电气特性及其技术特点,利用计算机应用技术和数字仿真技术建立电子设备热模型,并进行热仿真分析,再将仿真计算得到的发热元器件壳温与实际热平衡试验测量得到的元器件真实壳温比对,检验热仿真分析结果的准确性。结果某电子设备在真空度为1.0×10-4 Pa,温度为45 ℃条件下开展热平衡试验,实测得到的发热元器件温度值与热仿真分析温度值之差小于1 ℃。热平衡试验过程中,切换电子设备的不同工作模式时,通过器件的工作电流和电压计算出其热负荷指标与仿真得到的热耗值之差低于0.1 W。结论基于热平衡试验的发热元器件实测温度数据,验证了热仿真分析结果的电子设备热设计方法科学有效,有助于后续空间站应用系统电子设备热设计工作。
关键词:空间站应用系统;电子设备;热设计;仿真分析;热平衡试验
目前,我国已经进入空间站工程实施阶段。空间站将开展我国迄今为止最大规模的空间利用活动,涉及到领域广泛的空间科学、相关应用和技术领域,包括空间生命科学和生物技术、微重力流体物理与燃烧科学、空间材料科学、微重力基础物理、空间天文、空间物理与空间环境、空间地球科学及应用,以及航天医学、航天器和空间应用新技术试验等重要方向,在建成后的10年将持续开展多达数百项空间科学、应用和技术研究。为了完成学科领域广泛、技术要求复杂、实验变化多样的应用任务,应用系统规划了包括多功能主动光学设施在内的重大研究设施,采用实验柜形式的科学和技术实验平台,以及研制一批重要的独立实验载荷。分别安排在空间站的三个舱段,部分在密封舱内,部分在舱外真空环境下。为支持所有研究设施、科学与技术实验平台和独立载荷高效地完成各项实验任务,应用系统将研制在轨信息系统,联接所有实验设备,统一向实验设备提供管理控制、数据通讯、数据预处理、数据存储、数据传输等功能[1]。
应用系统在轨信息系统的硬件组成主要是电子设备,在空间站的各类应用载荷中,电子设备也占据了很大比重。电子设备已经是空间站应用系统得以运转的极其重要的硬件基础。为了改善空间站应用电子设备的性能,进一步提高其长寿命、高可靠要求,需要将热仿真技术应用于其热设计过程中。借助热仿真技术可以模拟空间站应用电子设备在特殊工作环境中的边界条件,缩短高性能、高可靠要求电子设备的研制周期,借助热仿真也可以降低其热设计和热试验的成本与风险[2]。
1 电子设备热技术状态
文中以在航天工程型号中搭载过且具有实际在轨飞行试验经历,将来需要安装在空间站实验舱内真空环境下工作的电子设备为研究对象。其由飞行器平台负责提供散热通道,产品内部的热控设计工作是为了确保箱体内部电子器件产热传递到箱体壁面,并通过平台提供的散热通道传递给飞行器平台系统。电子设备属于常加电载荷,入轨后即进入正常工作模式,其功耗最大为50 W,最小为40 W,平均45 W。该电子设备为箱体结构见图1,安装于实验舱后锥段铝蜂窝板上。机箱本体尺寸为400 mm×350 mm×300 mm,机箱面板厚度为6 mm,通过底面固定在飞行器实验舱后锥段内。
电子设备内部由6组PCB组件组成,各PCB设置有板框,板框通过锁紧机构与箱体前后侧板连接。
1.1 热源分布
统计需要散热的元器件的结壳热阻、数量、热功耗以及结温I级降额指标等基本情况,见表2。计算分析电子设备热流密度较大的电子元器件分布及其热耗值,如图2所示。
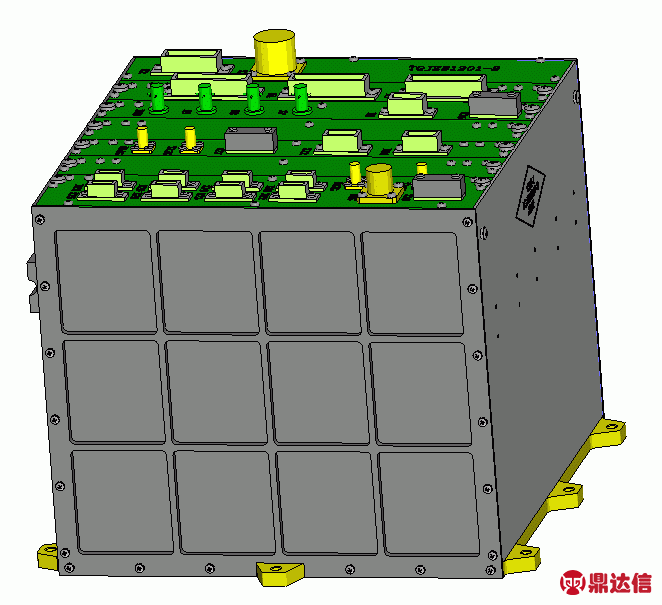
图1 电子设备外形
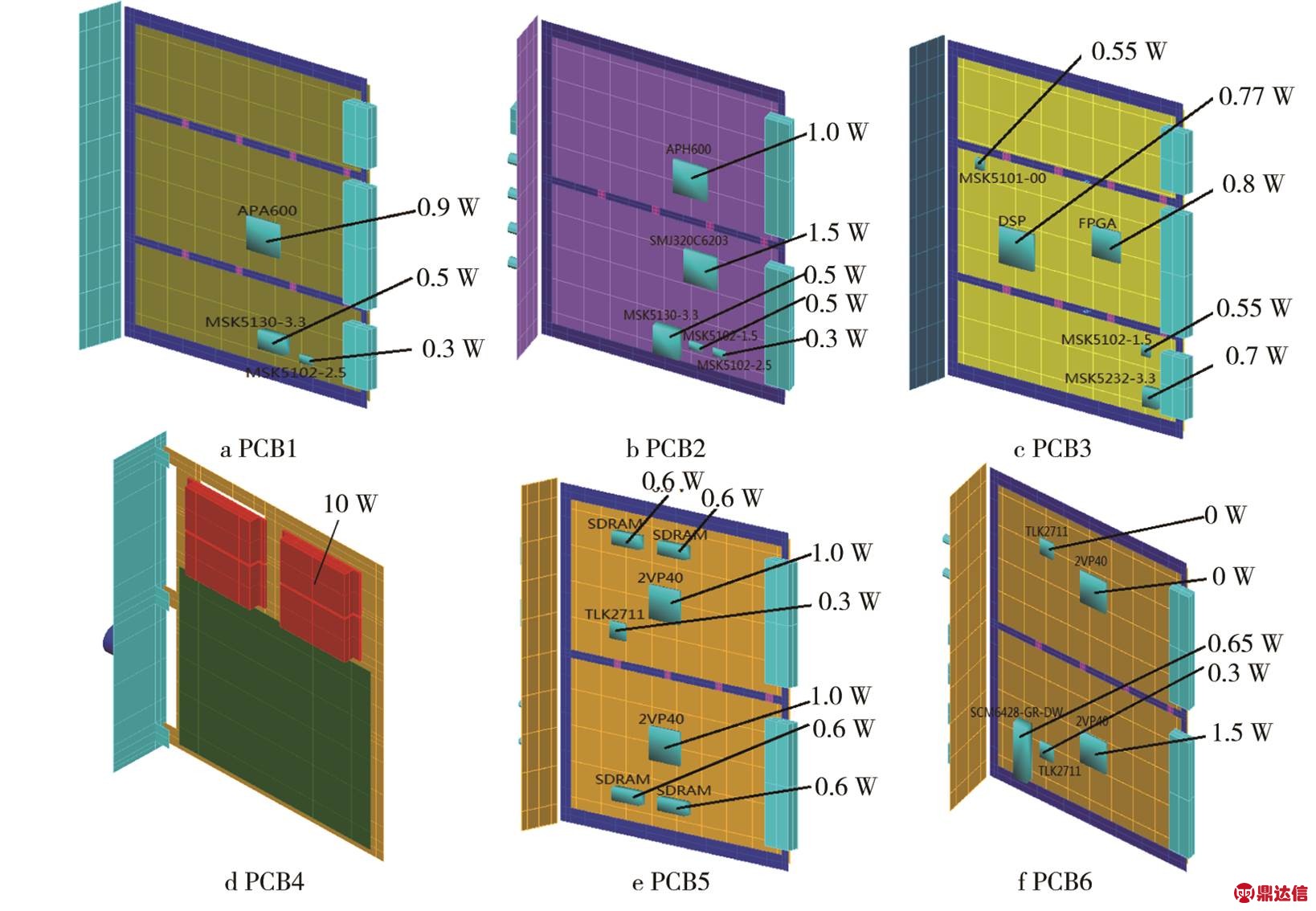
图2 各PCB组件的热耗分布
1.2 产品材料热属性
电子设备箱体材料为镁合金MB15。除安装接触面外,其他外表面喷涂发射率为0.85的ERB-2黑漆。
1.3 产品温控指标
电子设备的启动温度为-10~+45 ℃,最佳工作温度范围为+20~+30 ℃,工作温度范围为-10~+45 ℃,轨道存储温度范围为-20~+60 ℃。
2 热设计
2.1 大功率电子元器件
按照工程型号系统产品设计和建造规范要求,热耗大于0.3 W的元器件需进行专门热设计。大功率电源模块涂D-3导热脂固定在PCB支架上,PCB支撑框与左侧板间涂D-3导热脂固定。PCB上热流密度较大,且安装面积较大的元器件,采用1.0 mm T2铜导热片导出。铜导热片与电子元器件的对接面垫单面带胶,无胶面涂覆D-3导热脂,铜导热片与电路板框的对接面涂覆D-3导热脂。为保证力学性能可靠,电子元器件四周留有固定铜导热条的螺钉孔。对于安装面积较小且不宜用T2铜导热片的元器件,采用热良好、具有扩热效应的0.3 mm银导热片。
2.2 机箱热设计
电子设备箱体结构采用组合面板模式,各板间的接触充分利用板厚,且采取了止口搭接的形式,以增大接触面积,减小接触热阻。板框以锁紧方式固定在前后侧板上,锁紧方式为楔形机构。箱体非安装外表面喷涂ERB-2黑漆,以加强机箱辐射散热。鉴于电子设备安装板为铝蜂窝板,散热较差、机箱热功耗较大,且由于A 机和B机为冷备关系,故用两根热管将A 机和B机两个机箱连接起来,以增加散热面积和热容,再加一根热管将热量导到热容较大的冷板上。其中连接到冷板的热管安装在A机后侧板上。为减小接触热阻,热管安装面填充导热脂[3—4]。
3 热仿真分析
根据电子设备箱体与PCB的结构、材料、几何尺寸、安装组合方式、以及元器件安装布局方式,使用代表当今世界机械领域主流的新标准三维造型设计软件Pro/Engineer完成电子设备的器件、PCB组件以及机箱级产品的三维实体模型的建立工作。运用NASA等航天工程领域专用的热仿真分析软件Sinda/Fluint的ThermalDeskTop模块建立电子设备辐射热分析模型。为考核电子设备在实际应用的空间环境温度下,其内部电子元器件温度能否满足元器件结温I级降额指标要求,需要对其进行热仿真分析[5—7]。
3.1 建立热模型
运用Sinda/Fluint的ThermalDeskTop模块建成的电子设备热模型如图3所示。
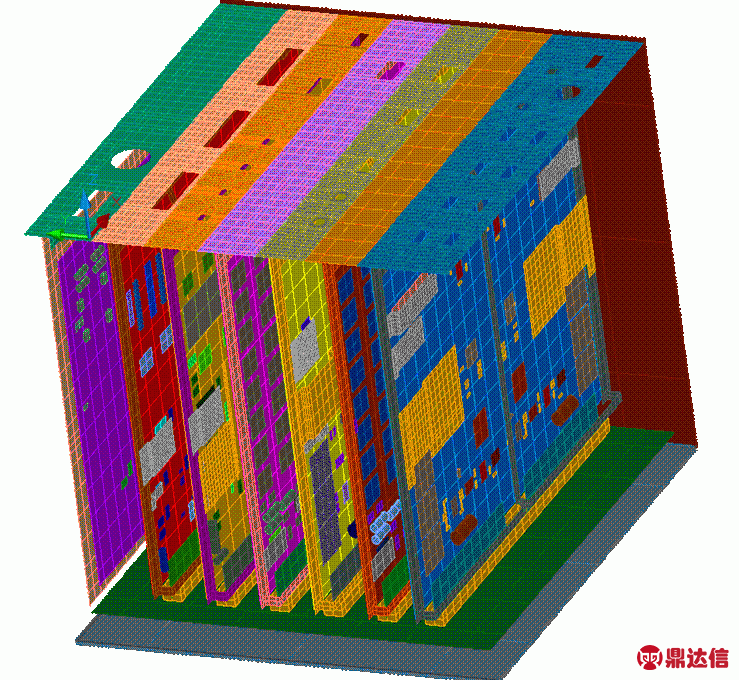
图3 电子设备整机热模型
电子设备热模型物性参数见表1。安装面温度作为热分析边界温度,箱体各面板安装接触换热系数按150 W/(m2·℃)计算,涂D-3导热脂界面的安装接触换热系数为1000 W/(m2·℃)。
表1 热模型物性参数
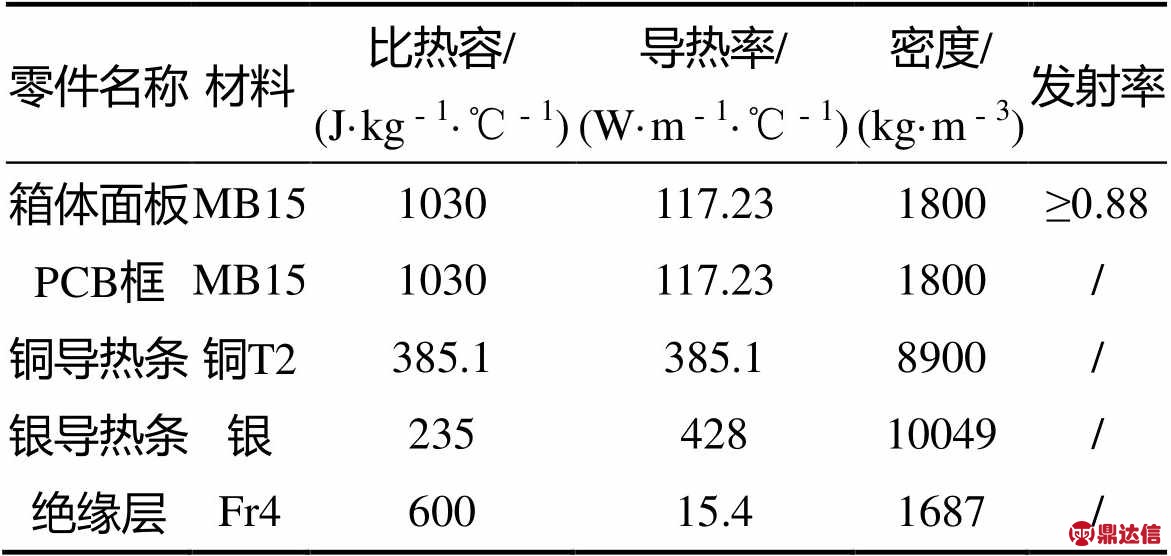
3.2 设置热边界条件及模拟热工况
由于电子设备所使用的元器件在温度较高的条件下其可靠性会降低,而低温条件下元器件是发热的,元器件温度不会太高,因此对其进行高温工况模拟并进行热分析。模拟电子设备热工况时设置的热边界条件:安装面边界温度设定在45 ℃;舱段热辐射背景边界温度设定在45 ℃;冷板温度为10 ℃。
3.3 热仿真分析及计算结果
热仿真分析得到电子设备各PCB温度分布结果如图4所示,各PCB上元器件的温度见表2。从表2中数据可以看出,在采取设置PCB框、铜/银导热条、涂覆D-3导热脂、箱体表面喷涂黑漆等措施后,所有元器件的工作温度均能够满足电子元器件I级降额设计指标的要求。其中元器件结温最高值为61.15 ℃,是位于PCB3上的MSK5101-00元器件,其余量为18.85 ℃。
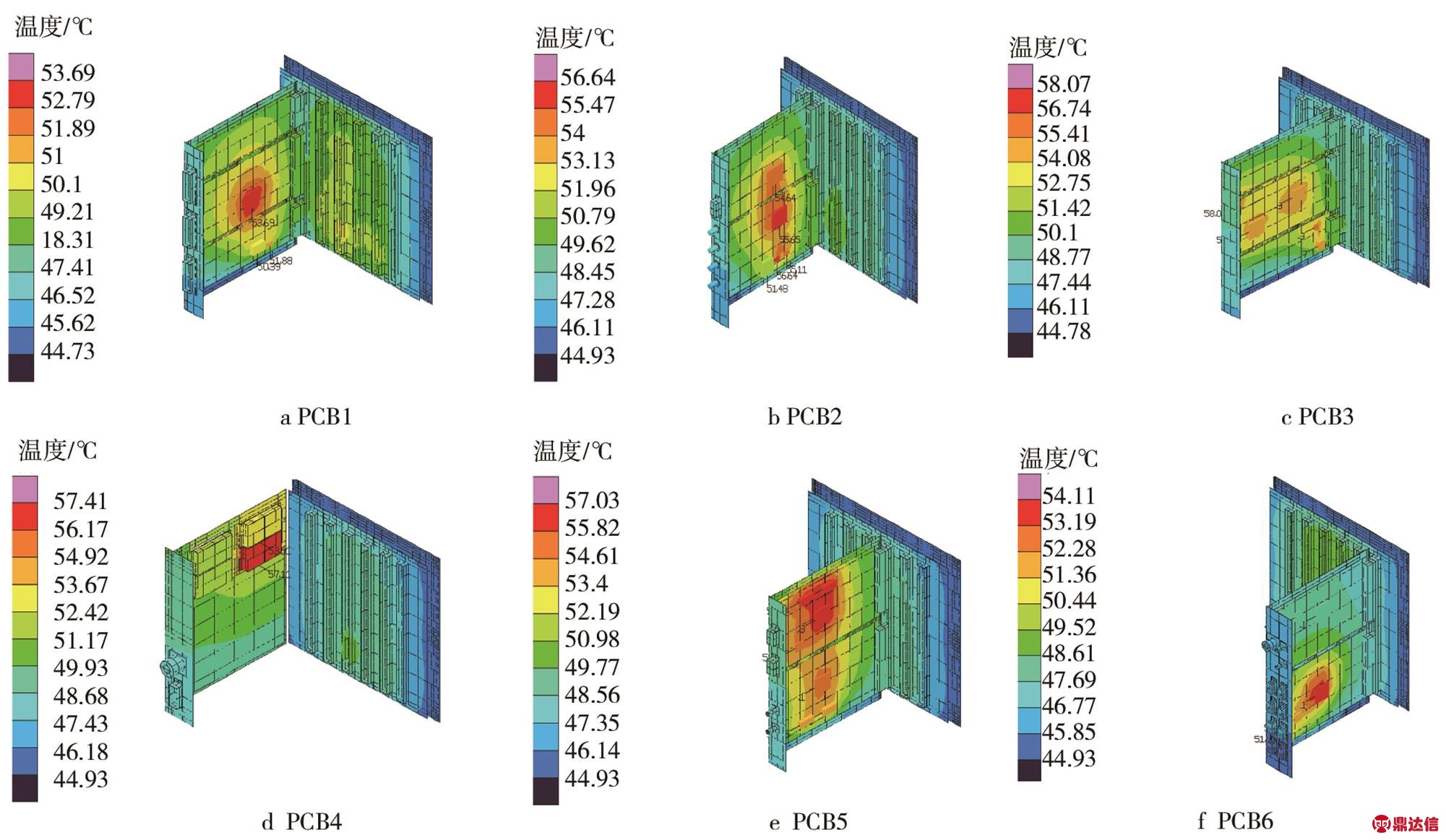
图4 各PCB组件的温度分布及主要器件温度值
表2 发热元器件温度与热耗数据
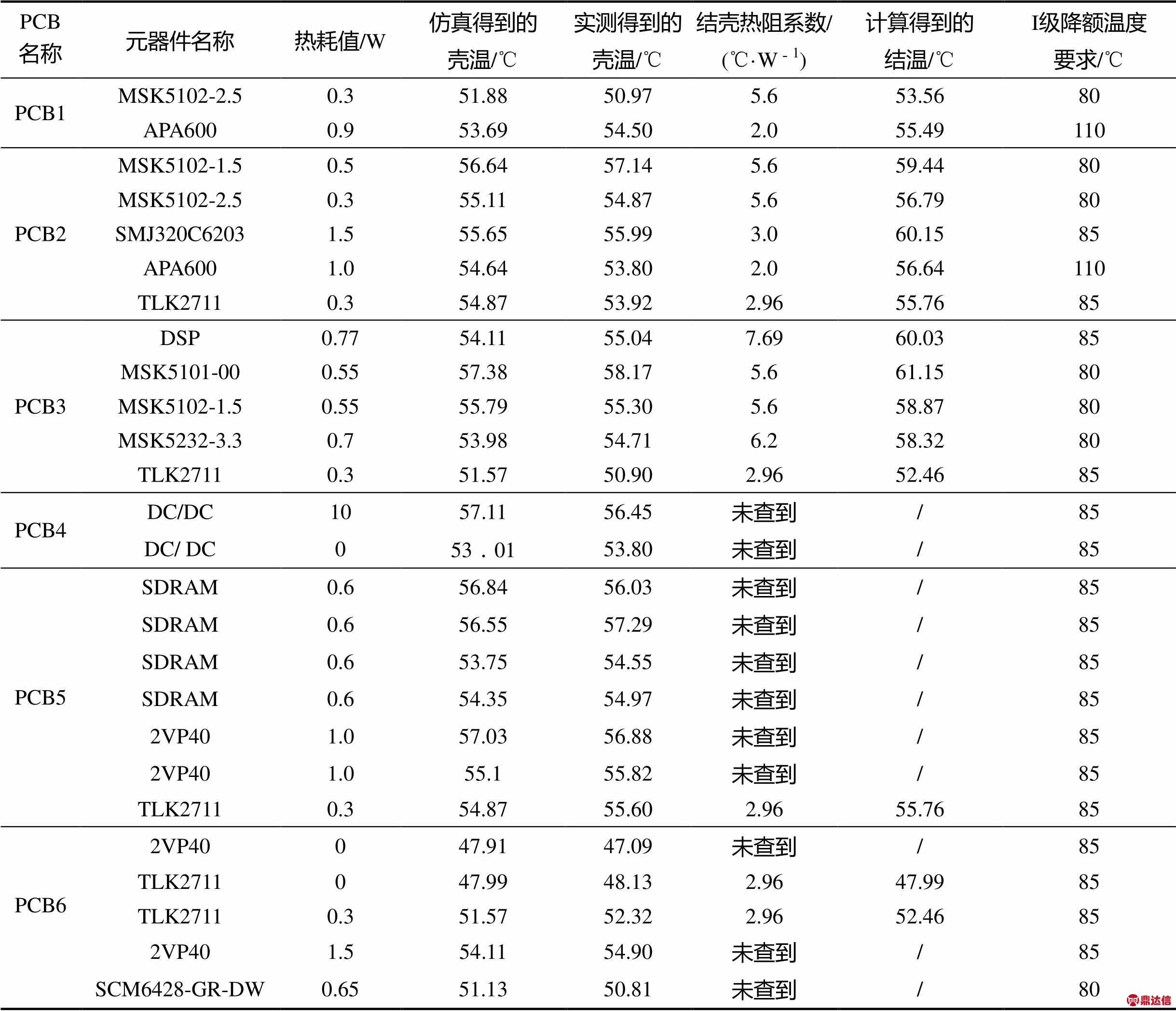
4 验证热仿真分析结果
为了验证上述热仿真分析及计算得到的电子设备发热元器件的温度是否真实反映了其空间热工况条件下的热特性,采用热真空环境模拟试验系统和由Pt100温度传感器构成的温度测量系统,完成了电子设备在真空度为1.0×10-4 Pa和温度为45 ℃条件下的热平衡试验测试工作。实测试验采集得到各PCB上发热元器件的壳体温度数据见表2。从表2可见,热平衡试验实测得到的发热元器件温度值与热仿真分析得到的发热元器件温度值之差都在1 ℃范围之内。热平衡试验过程中,切换电子设备的不同工作模式时,通过器件的工作电流和电压即功率来计算出其热负荷指标与表2中所列的仿真得到的热耗值之差不超过0.1 W[8—11]。
若真空热平衡试验实测得到的电子设备发热元器件温度数据结果同热仿真分析得到的温度数据结果比对后的差值超过1 ℃,或者热平衡试验过程中计算出其热负荷指标与仿真得到热耗值之差超过0.1 W,则需要通过实测得到的元器件温度和热耗数据结果对电子设备热模型进行修正、标定,以提高热模型的成熟度。
另外,该电子设备在以往航天工程某型号中搭载过并顺利完成了相关的飞行试验及留轨试验任务,发热元器件均安装了热敏电阻传感器用以监测其在空间真实应用热环境中的壳体温度。根据飞行试验温度数据统计,也验证了发热元器件结温是能满足元器件I级降额设计指标的要求。根据以往航天工程型号的飞行验证经验,对于未查到结壳热阻的元器件亦能满足元器件I级降额设计指标的要求。
5 结语
上述热仿真分析得到的电子设备发热元器件温度和热耗两项热技术指标均与真空热平衡试验实际测试得到的结果基本一致,完全符合该空间工程型号系统产品设计和建造规范的要求。因此,热仿真分析得到的元器件温度和热耗数据结果是比较准确的,从而也表明电子设备的元器件、电路板、机箱三级产品热设计合理,各元器件温度均满足I级降额设计要求,符合工程设计指标要求。
文中所运用的基于热平衡试验测量发热元器件温度数据验证热仿真分析结果的电子设备热设计方法是科学、有效的,有助于开展空间站应用系统电子设备热设计工作。可以提高长寿命、高可靠要求电子设备热设计的准确性,对推动未来我国空间站电子设备研制工作的顺利完成也具有一定的参考价值。