摘 要:双离合变速器(dual clutch transmission,DCT)具有换挡速度快、传动效率高和质量小等优点,搭载DCT的电动汽车的动力性与经济性可显著提高。在DCT中,电液控制系统总成的设计尤为关键。以纯电动汽车的两挡干式双离合变速器(简称为2DCT)为研究对象,对其电液控制系统总成进行设计。首先,基于2DCT中干式双离合器的结构和性能参数,对2DCT电液控制系统的关键元件进行选型和计算。然后,基于2DCT电液控制系统的原理,设计了一体式液压阀体,并通过静力学分析来验证其结构的稳定性。最后,对2DCT电液控制系统的一体式液压阀体的结构进行拓扑优化,以减小液压阀体的质量,从而实现轻量化。结果表明,所设计的电液控制系统总成的工作特性和结构强度均满足要求,可充分提高电动汽车的平顺性和响应速度。研究结果可为电动汽车变速器电液控制系统总成的开发提供理论依据。
关键词:电汽动车;双离合变速器;电液控制系统总成;结构优化
电动汽车具有效率高、噪声小和环境污染小等优点[1],是未来汽车发展的重要方向。目前,全球主流电动汽车均采用“驱动电机+单挡减速器”架构[2]。但是,在汽车起步加速与高速巡航工况下,驱动电机的效率降低[3],此时须通过增加减速器挡位来使车辆在高效区间内工作,以满足动力性与经济性要求。双离合变速器(dual clutch transmission,DCT)具有体积小、结构简单和成本低等优点,其可在短时间内无动力中断换挡,有效提高换挡的平顺性[4]。搭载DCT的电动汽车在起步时不需要离合器参与工作,且在行驶过程中换挡次数少及换挡摩擦热量较小。
汽车变速器电液控制系统总成包括电液控制系统与液压阀体两部分。电液控制系统总成作为变速器的重要组成部分,既要满足各工况下的换挡需求,又要满足强度和轻量化要求。近年来,国内外众多学者针对汽车变速器电液控制系统总成做了不少研究。例如:于会龙[5]对DCT液压系统的控制框图、换挡油缸和供油调压系统进行了介绍,并运用仿真软件对其进行建模分析;秦娜等[6]分析了DCT 液压系统的工作原理,并分析了脉冲周期、占空比等参数对该系统的影响;毕长飞[7]对自动变速器的液压系统进行了设计,通过理论计算得到了其液压控制单元和液压缸的结构尺寸,并通过对比分析确定了自动变速器仿真模型的正确性和可靠性;刘芳等[8]探讨了混合动力传动系统液压阀体结构的设计优化过程以及阀体的泄漏控制方法;Lei等[9]根据DCT的结构和换挡原理,对其液压系统进行了设计,并通过试验验证了其可行性;郑诗强等[10]针对三段式变速箱的换段液压系统,设计了集成式阀体,并通过静力学分析验证了阀体结构的可靠性;秦滔等[11]采用六面体单元对DCT 液压阀体模型进行网格划分,并通过静力学分析得到了液压阀体的应力分布和最大应力,以校核液压阀体的强度,并在此基础上对液压阀体进行轻量化设计。
然而,上述研究大多针对的是燃油汽车的DCT,对电动汽车DCT的研究仍有待深入。基于此,以自主设计的纯电动汽车的两挡干式双离合变速器(下文简称为2DCT)为研究对象,对其电液控制系统总成进行设计;同时,提出了一种一体式液压阀体结构优化方法,在保证阀体整体强度的前提下对其结构进行拓扑优化,以满足轻量化要求。
1 2DCT电液控制系统参数设计
1.1 2DCT机械系统的原理
基于某型纯电动汽车的2DCT,对其电液控制系统进行设计。该型电动汽车的性能参数如表1所示,其搭载的2DCT的机械系统原理如图1所示。
表1 某型电动汽车的性能参数
Table 1 Performance parameters of a certain type of electric vehicle
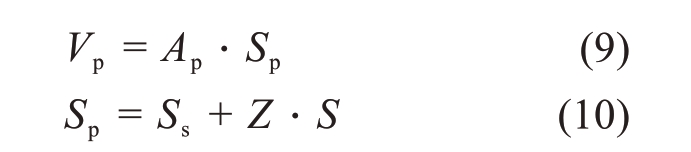
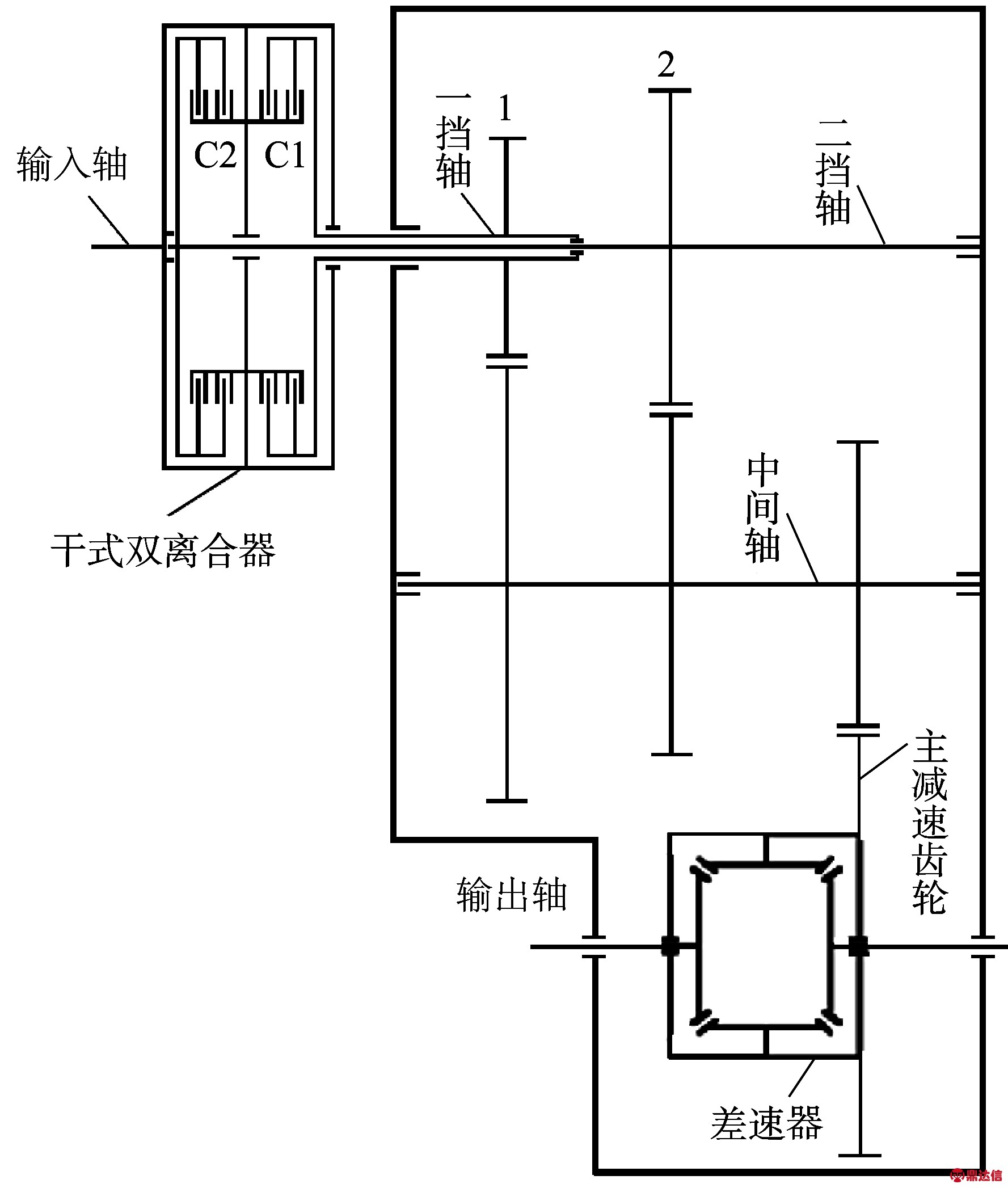
图1 2DCT机械系统的原理
Fig.1 Principle of 2DCT mechanical system
该型纯电动汽车的驱动电机为永磁同步电机,其与变速器由花键连接。在一、二挡离合器摩擦片(C1、C2)的压紧作用下,动力先从输入轴经干式双离合器及其固定齿轮传递至中间轴,再通过中间轴上固定齿轮的啮合作用传递至主减速齿轮,最后通过差速器传递至输出轴。因2DCT只有2个挡位,所以不需要同步器来进行换挡操作。
考虑到驱动电机的峰值转矩为250 N·m,为满足设计需求,设2DCT的最大扭矩为290 N·m;为满足电动汽车整车爬坡度和最高时速的要求,设2DCT的一挡传动比为11.71,二挡传动比为4.66。
1.2 干式双离合器设计
根据2DCT 的性能指标和驱动电机接口的边界条件,要求干式双离合器的最大传递扭矩为290 N·m,外径小于0.215 0 m。相较于传统的干式双离合器,所设计的干式双离合器尺寸较小,则其摩擦片的面积和摩擦系数应较大。所设计的干式双离合器的基本参数如表2所示,其三维模型和装配示意图分别如图2和图3所示。
表2 干式双离合器的基本参数
Table 2 Basic parameters of dry dual clutch

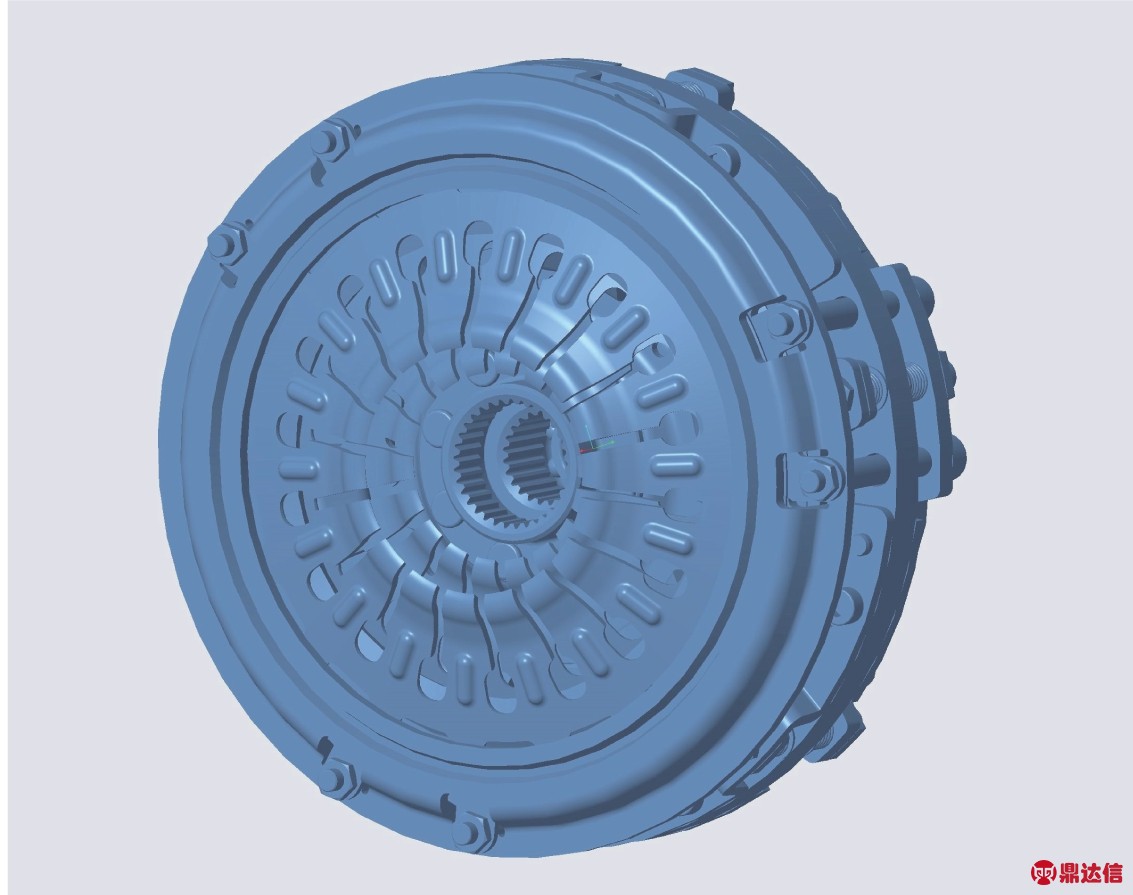
图2 干式双离合器三维模型
Fig.2 Three-dimensiomal model of dry dual clutch
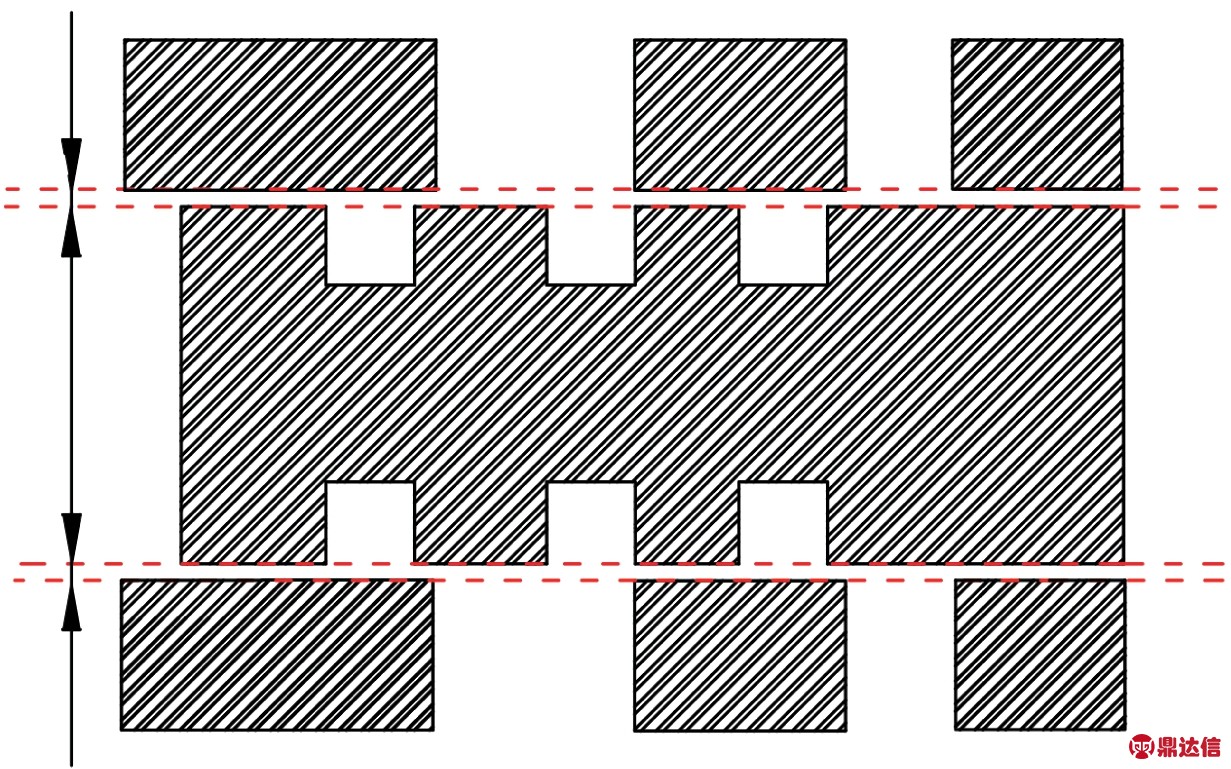
图3 干式双离合器装配示意
Fig.3 Schematic diagram of dry dual clutch assembly
1.3 电液控制系统工作压力计算
基于干式双离合器的基本参数,求解其工作时所需的压力。
干式双离合器的扭转传递方程为:

式中:T 为干式双离合器的摩擦转矩,N·m;μ 为干式双离合器摩擦片的摩擦系数;F为干式双离合器摩擦片表面的最大压紧力,N;Re为干式双离合器摩擦片的当量半径,m;Z 为摩擦片数量;β 为干式双离合器的储备系数,相较于传统燃油汽车,电动汽车在低速下的输出扭矩较大,β 可选择较小数值,本文取β=1.2;Tout为驱动电机的最大输出扭矩,N·m,本文取Tout=290 N·m。
干式双离合器摩擦片的当量半径Re为:
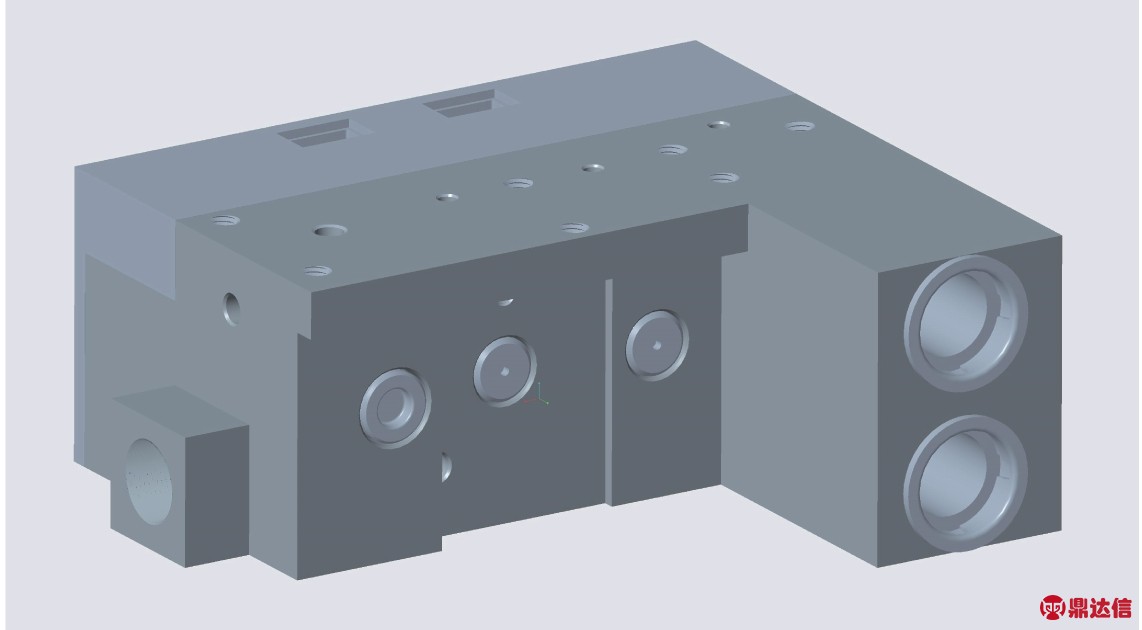
式中:D为摩擦片外径,m;d为摩擦片内径,m。
将表1 中的数值代入式(2),计算得到干式双离合器摩擦片的当量半径为0.146 0 m。
干式双离合器摩擦片表面的最大压紧力F为[12]:

将相关数值代入式(3),计算得到干式双离合器摩擦片表面的最大压紧力为2 443.5 N。
2DCT 电液控制系统中液压缸内活塞杆与干式双离合器通过分离杠杆连接,基于干式双离合器摩擦片的最大压紧力可计算电液控制系统的最大工作压力。液压缸内活塞杆的受力平衡方程为:

式中:Fp为活塞液压力,N;F1为活塞密封圈阻力,N,其数值较小,在计算中可被忽略;F2为干式双离合器膜片弹簧的最大弹力,N,本文取F2=1 100 N。
2DCT电液控制系统的最大工作压力Pp为:

式中:Ap为活塞面积,m2。
联立上述公式,计算得到2DCT电液控制系统的最大工作压力为3.1 MPa,即2DCT 中干式双离合器在传递最大扭矩时其油路的输出压力为3.1 MPa。
1.4 电液控制系统泄漏量计算
2DCT 电液控制系统泄漏包括油泵泄漏和机械阀泄漏。
1.4.1 油泵泄漏
油泵泄漏分为径向泄漏和端面泄漏。径向泄漏是指油泵内因齿轮啮合以及齿顶与泵体之间存在间隙而产生的泄漏,如图4所示。
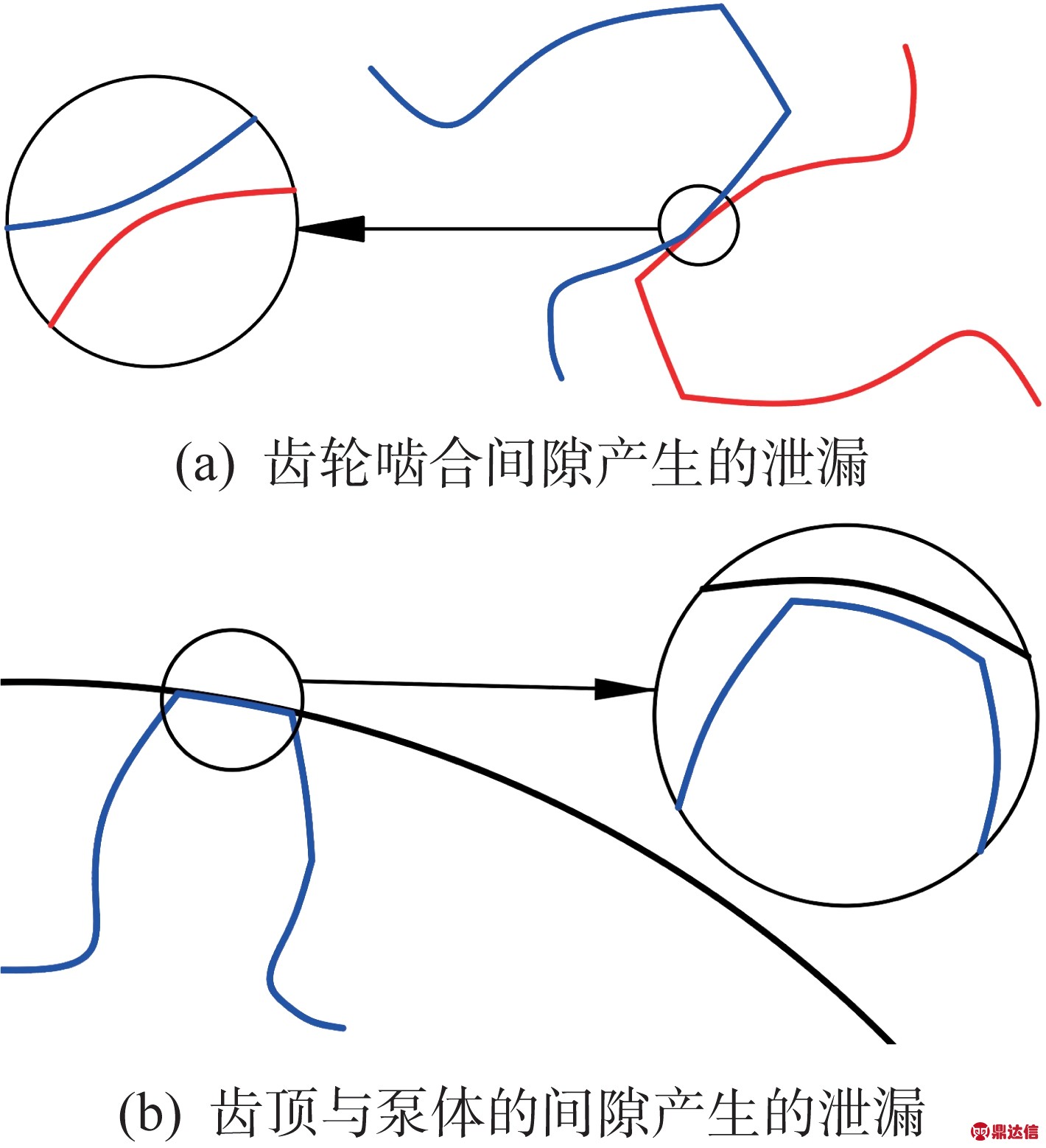
图4 油泵径向泄漏示意
Fig.4 Schematic diagram of radial leakage of oil pump
油泵径向泄漏量Qr可等效为[13]:

式中:B 为油泵齿轮宽度,m;n 为油泵电机转速,r/min;h 为径向间隙高度,m;μ 为液压油动力黏度,N·s/m2;ΔP为压力差,Pa;p为油泵齿轮的螺旋参数;s为油泵齿轮的齿顶总宽度,m。
端面泄漏是指油泵内因齿轮端面与两侧泵盖之间存在间隙而产生的泄漏,如图5所示。
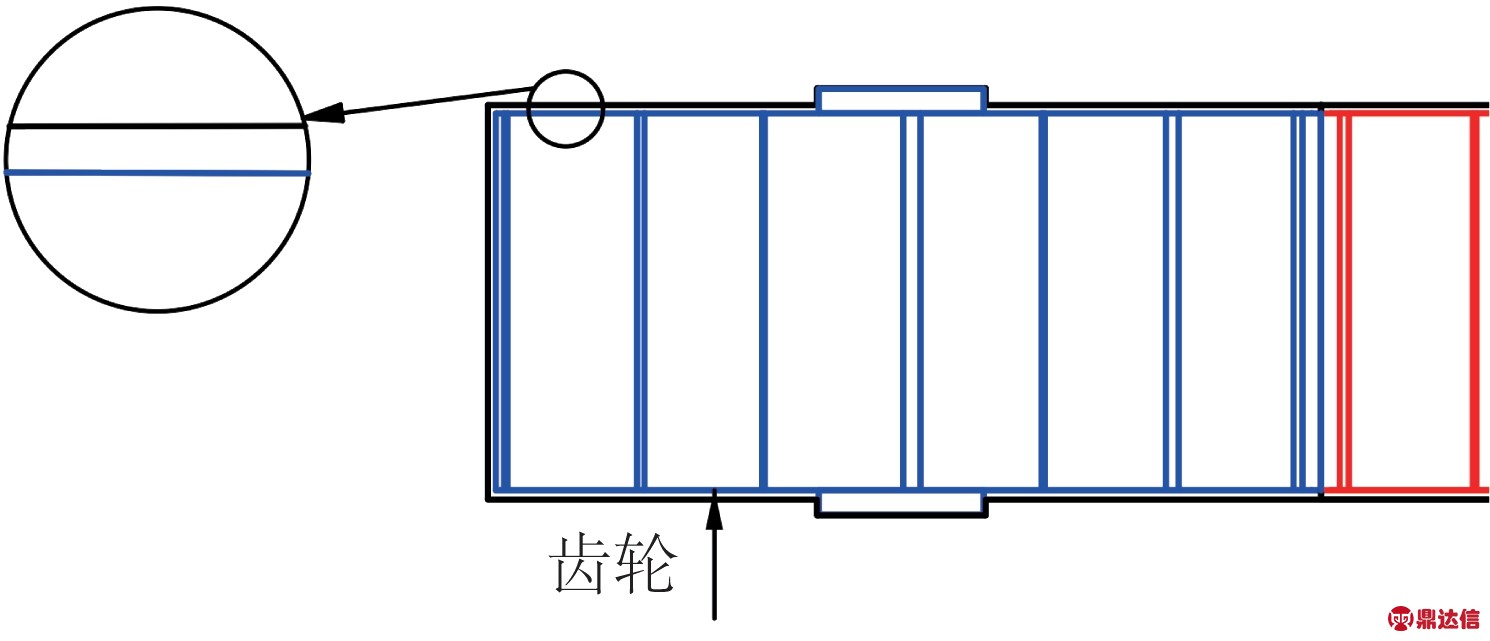
图5 油泵端面泄漏示意
Fig.5 Schematic diagram of end face leakage of oil pump
油泵端面泄漏量Qe可等效为[13]:

式中:ht为油泵端面间隙宽度,m;Rf为油泵齿轮齿根圆半径,m;Rj为油泵滑动轴承内圈半径,m;αH为油泵齿轮高压区包角,(°);αT为油泵齿轮过渡区包角,(°)。
联立式(6)和式(7)并代入相应数值,计算得到油泵的总泄漏量为2.3 L/min。
1.4.2 液压阀体阀芯泄漏
液压阀体阀芯泄漏一般发生在阀芯与阀座结合处,如图6所示。
根据现有的产品参数,计算得到液压阀体阀芯的总泄漏量为0.7 L/min。
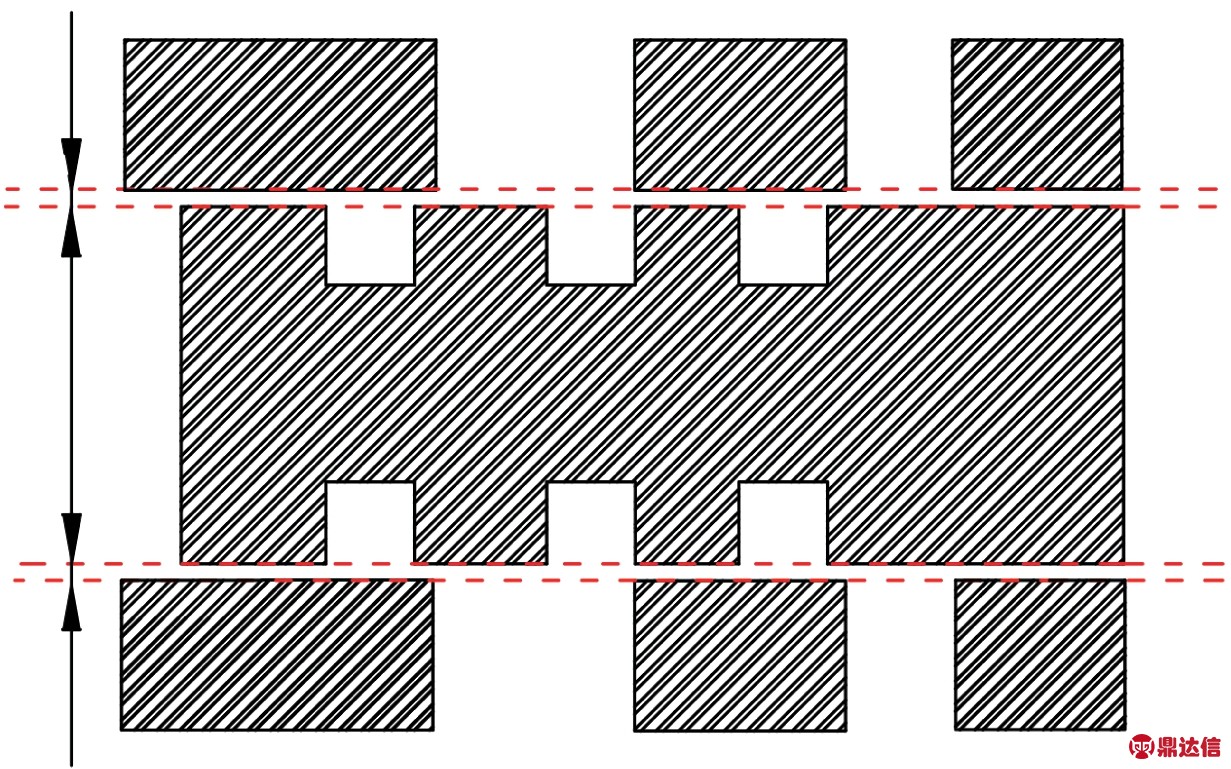
图6 液压阀体阀芯泄漏
Fig.6 Leakage of hydraulic valve core
1.5 电液控制系统充油流量计算
设2DCT的换挡时间为0.3 s,即在0.3 s内对液压缸完成充油并使活塞推动离合器结合以传递扭矩。2DCT电液控制系统的充油流量Qf为:
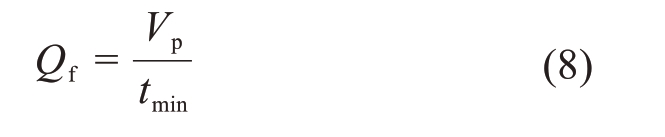
其中:
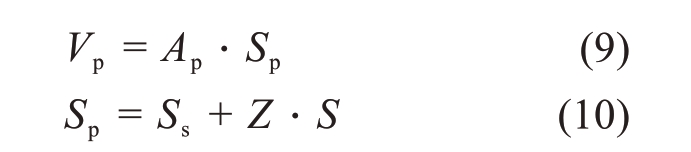
式中:Vp为液压缸的工作腔体积,m3;tmin为2DCT的换挡时间,s,tmin=0.3 s;Sp为活塞行程,m;Ss为膜片弹簧的行程,m;S为干式双离合器各摩擦片的行程,m。
联立式(8)至式(10),计算得到活塞的行程为0.015 0 m。代入已知参数,计算得到2DCT所需的最大充油流量为3.5 L/min。
通过计算,最终确定2DCT电液控制系统的峰值流量为2DCT的最大充油流量与油泵的最大泄漏量之和,为6.5 L/min。
2 2DCT电液控制系统传动设计
2DCT电液控制系统由动力源、执行器、控制阀、液压附件和工作介质组成。在2DCT电液控制系统中,油泵将机械能转换为压力能,使得液压油流经单向阀、压力调节阀等控制阀后到达执行机构——液压缸,然后液压缸中的活塞杆将压力能转换为机械能以驱动负载——干式双离合器。根据要求设计2DCT电液控制系统的传动方案,如图7所示。
在2DCT电液控制系统中,油泵在电机的驱动下从油底壳中抽出液压油,液压油经过滤器后进入主油路;在压力调节阀调节主油路压力后,液压油经直接换挡电磁阀进入高速开关阀,最终流入液压缸。其中,直接换挡电磁阀7为常低,直接换挡电磁阀8为常高。以二挡离合器为例:当离合器摩擦片结合时,直接换挡电磁阀7输出液压油,液压油经高速开关阀9后进入液压缸10,控制液压缸充油以使离合器摩擦片结合;当离合器摩擦片分离时,直接换挡电磁阀7的输出压力降低,单向阀5两端形成压力差并打开内部油口,液压油回流至直接换挡电磁阀7,最终流入油底壳,完成泄油。

图7 2DCT电液控制系统传动方案
Fig.7 Transmission scheme of 2DCT electro-hydraulic control system
高速开关阀位于干式双离合器和直接换挡电磁阀之间。在2DCT电液控制系统正常工作的情况下,高速开关阀处于右位,此时一、二档离合器的油路与直接换挡电磁阀的油路接通;在2DCT电液控制系统部分失效的情况下,高速开关阀的电磁铁工作,推动其阀芯向左移动以连通左位,2DCT电液控制系统进入安全模式,此时二挡离合器的油路被切断,仅连通一挡离合器油路,电动汽车在一挡状态下安全行驶。
3 2DCT电液控制系统液压阀体设计
3.1 液压阀体二维布局
根据2DCT电液控制系统各元件的参数,采用一体式液压阀体,其二维布局如图8所示。相比于传统的三段式阀体,一体式液压阀体的体积和泄漏量较小,加工难度较低,适用于结构相对简单的电液控制系统。
3.2 液压阀体三维布局
设2DCT 电液控制系统液压阀体主油路油管的内径为6 mm,分支油路油管的内径为4 mm,油管的最小壁厚为3 mm。在保证2DCT电液控制系统各元件不互相干涉的情况下,应尽量减小其液压阀体的体积,以保证液压阀体能够正常安装并与变速器壳体搭载。2DCT 电液控制系统液压阀体的三维布局及总装配图分别如图9和图10所示。

图8 2DCT电液控制系统液压阀体二维布局
Fig.8 Two-dimensional layout of hydraulic valve body of 2DCT electro-hydraulic control system
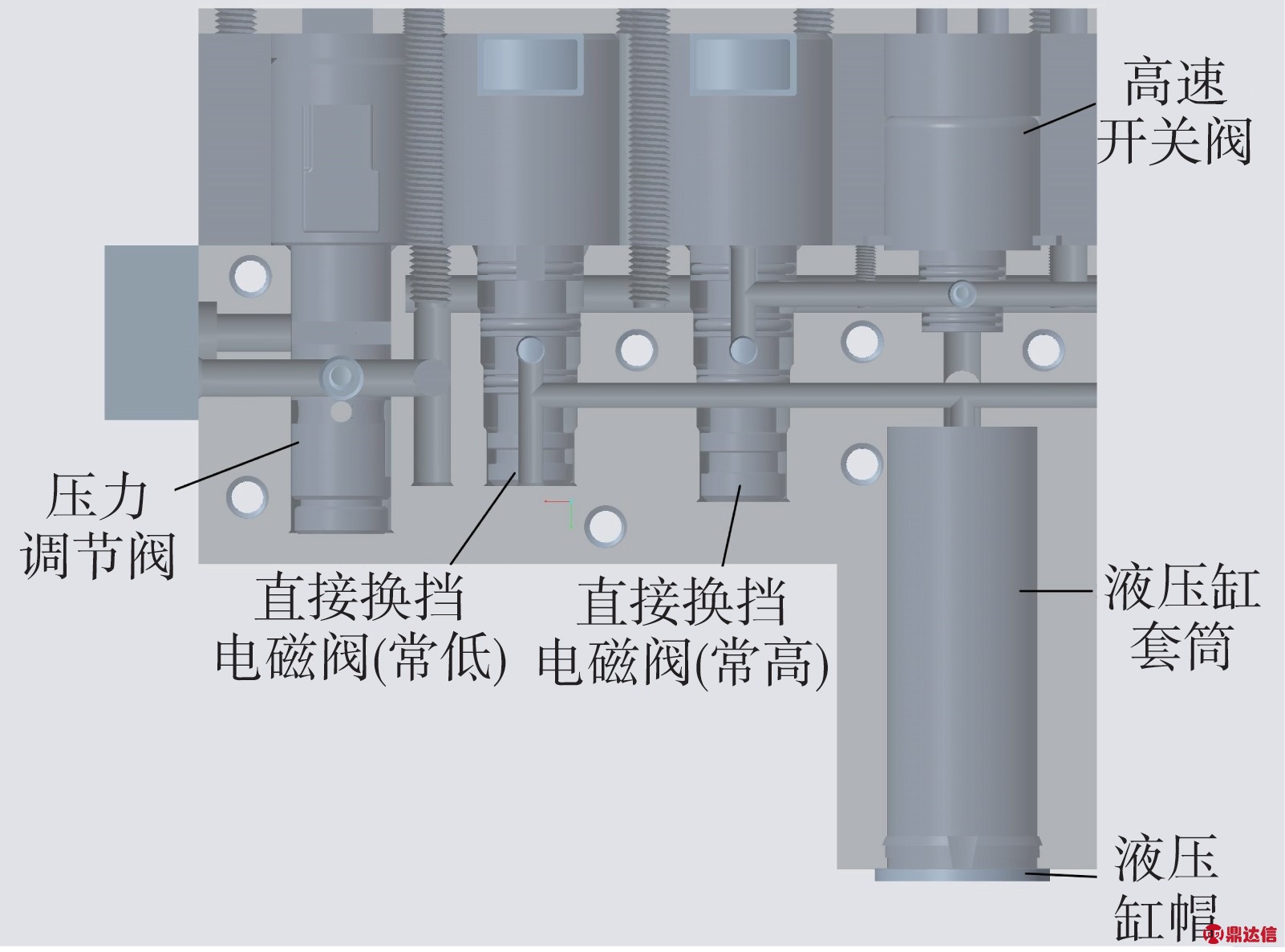
图9 2DCT电液控制系统液压阀体三维布局
Fig.9 Three-dimensional layout of hydraulic valve body of 2DCT electro-hydraulic control system
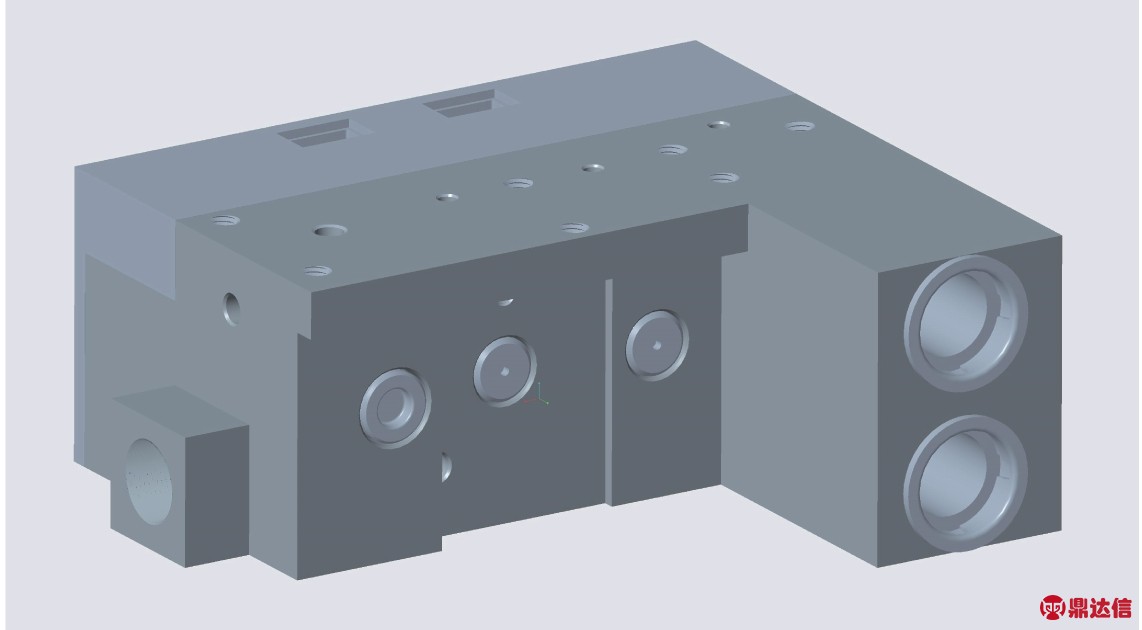
图10 2DCT电液控制系统液压阀体总装配示意
Fig.10 Total assembly diagram of hydraulic valve body of 2DCT electro-hydraulic control system
4 2DCT 电液控制系统液压阀体强度分析及结构优化
4.1 强度分析
2DCT 电液控制系统液压阀体试样的材料为6061铝合金,其属性参数如表3所示。
在进行静力学仿真分析前,先对2DCT电液控制系统液压阀体三维模型进行简化:去除倒角、圆角等不利于网格划分的部分。然后利用四面体单元对简化后的液压阀体三维模型进行网格划分。根据液压阀体的设计尺寸,设阀体表面的划分网格尺寸为2 mm,安装孔和螺栓孔等重要结构的划分网格尺寸为1 mm。2DCT电液控制系统液压阀体三维模型的网格划分情况如图11所示。
表3 6061铝合金材料的属性参数
Table 3 Attribute parameters of 6061 aluminum material
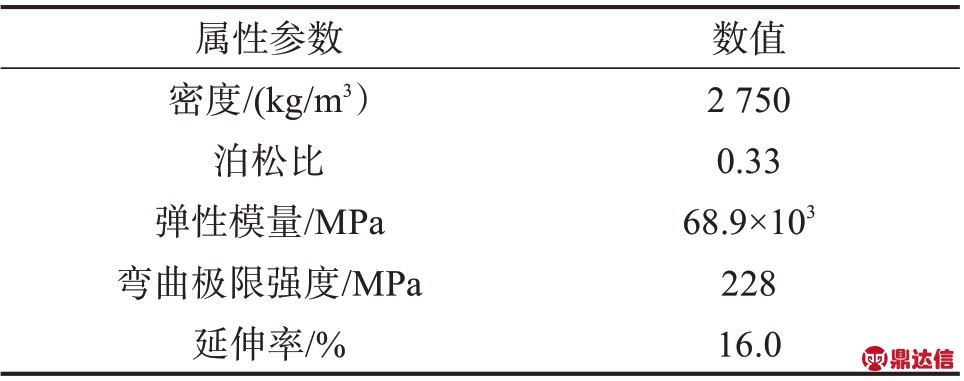
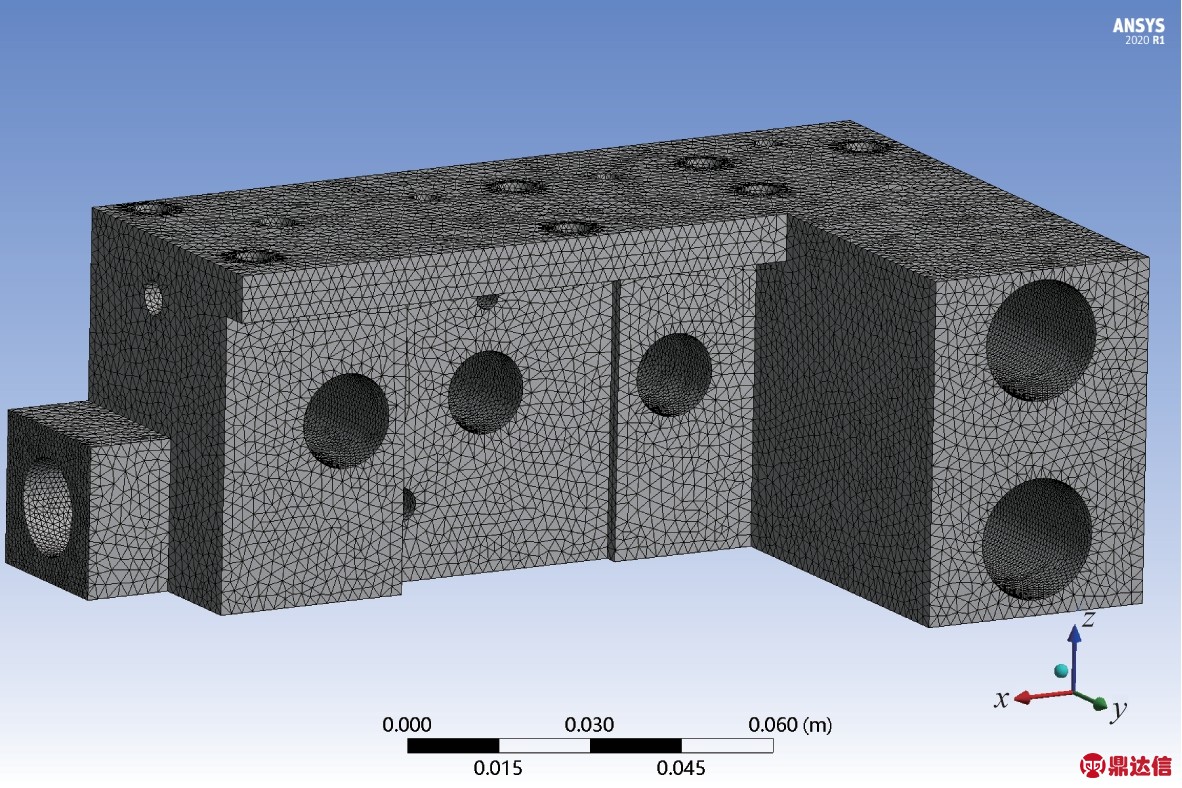
图11 2DCT电液控制系统液压阀体三维模型网格划分
Fig.11 Mesh division of three-dimensional model of hydraulic valve body of 2DCT electro-hydraulic control system
为分析2DCT电液控制系统液压阀体的强度,在其螺栓孔处加载9 200 N预紧力,并对阀体同时加载一、二挡离合器油路的最大油压(3.1 MPa)。通过静力学仿真分析,得到液压阀体的变形云图与应力云图,如图12所示。
由仿真结果可知,2DCT电液控制系统液压阀体的应力集中出现在螺栓孔预紧力加载处,最大应力为72.28 MPa,远小于材料的极限强度(310 MPa),说明所设计的液压阀体的强度符合要求。
4.2 液压阀体结构优化
鉴于所设计的2DCT 电液控制系统液压阀体的质量仍较大,在轻量化方面仍有较大的优化空间,可通过拓扑优化方法进行阀体轻量化设计。拓扑优化(topology optimization)是一种根据给定的负载情况、约束条件和性能指标,在给定区域内对结构材料分布进行优化的数学方法[14]。通过拓扑优化,可在材料均匀分布的空间中找到最佳的结构优化方案。
4.2.1 约束条件及加载
设2DCT 电液控制系统液压阀体螺栓孔的最小壁厚为3 mm,其余开孔由拉胀式堵头封堵,其约束条件如图13所示。
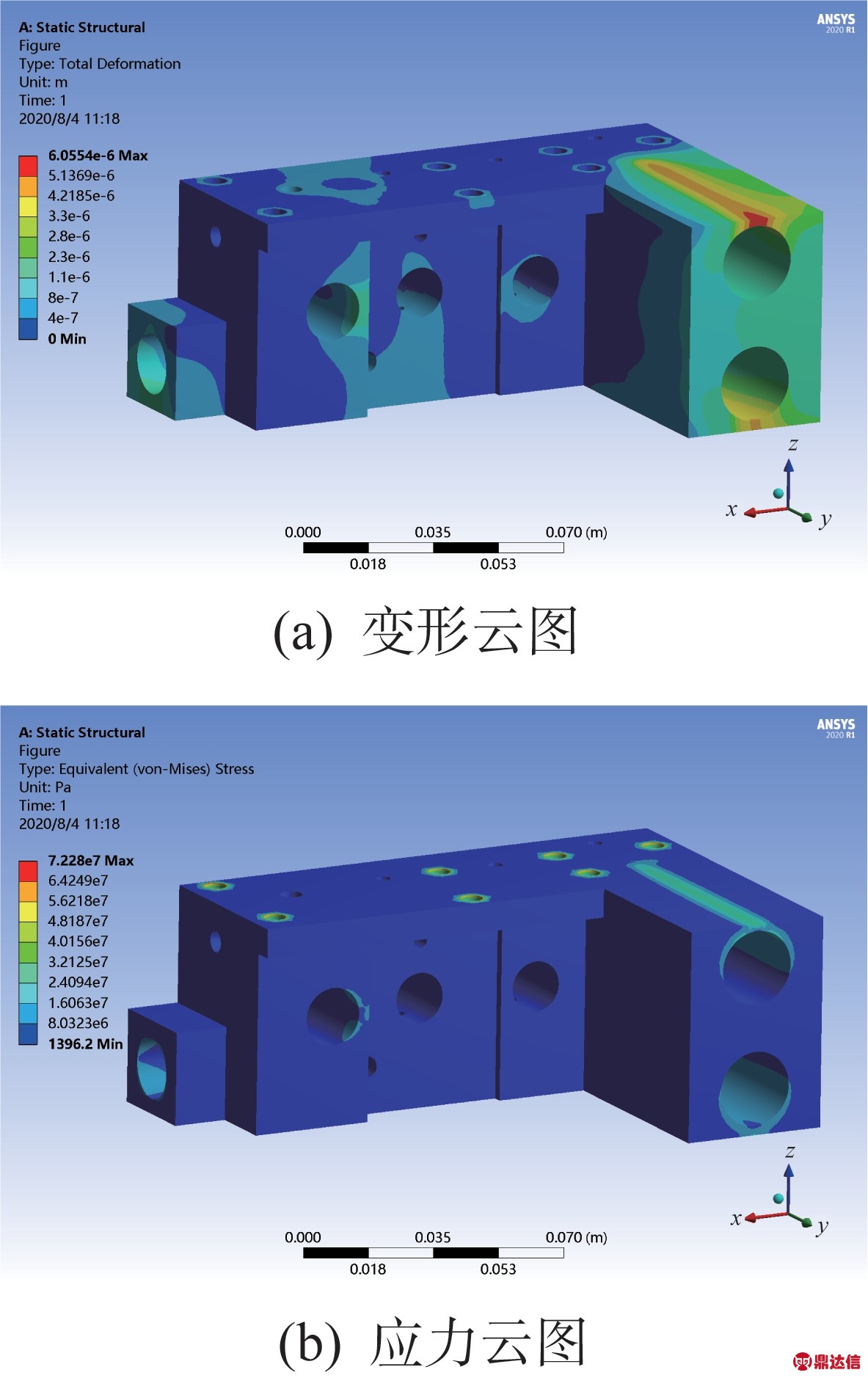
图12 2DCT 电液控制系统液压阀体的变形云图和应力云图
Fig.12 Deformation nephogram and stress nephogram of hydraulic valve body of 2DCT electro-hydraulic control system
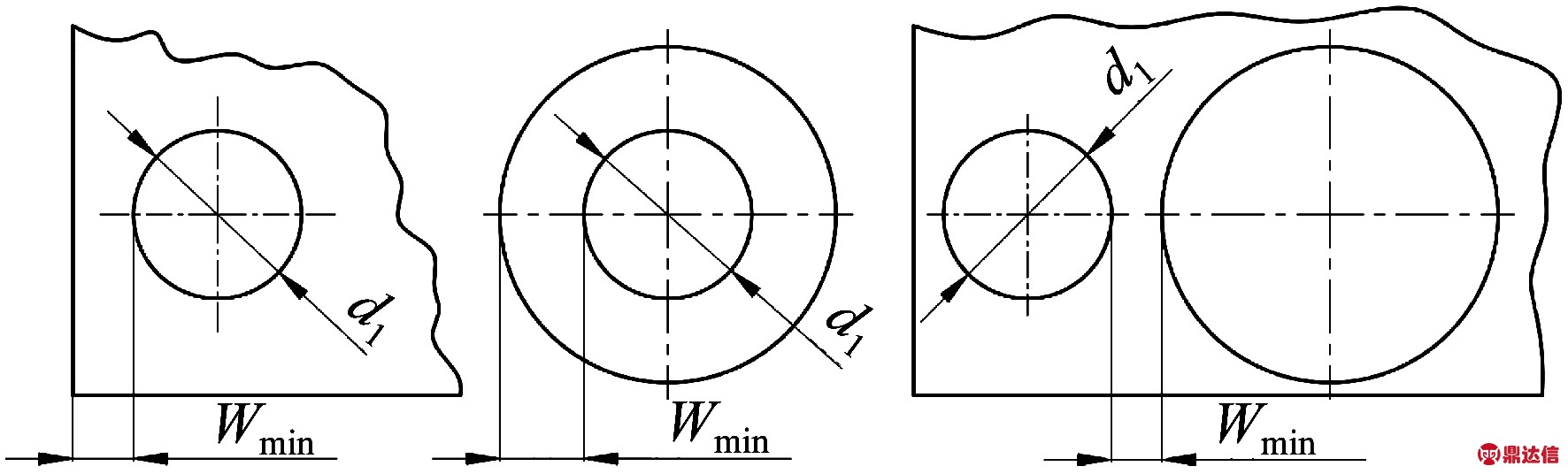
图13 2DCT 电液控制系统液压阀体开孔处壁厚的约束条件
Fig.13 Constraint conditions of opening wall thickness of hydraulic valve body of 2DCT electro-hydraulic control system
2DCT 电液控制系统液压阀体开孔处的最小壁厚与其外径的关系为:

式中:Wmin为开孔处的最小壁厚,mm;f为计算系数,与液压阀体的材料有关,本文取f=0.5;d1为开孔的外径,mm。
为保证液压阀体开孔处的结构强度,根据所选开孔堵头和主、分支油管内径的设计值(6和4 mm),确定对应的壁厚分别为3.0 和2.5 mm。为确保电磁阀阀芯部分位于液压阀体内部,电磁铁部分外置且被护板保护,确定电磁阀安装位置周围的最小壁厚为6 mm。
4.2.2 优化求解
设2DCT 电液控制系统液压阀体的体积分别减小15%,30%和40%,其拓扑优化结果如图14所示。
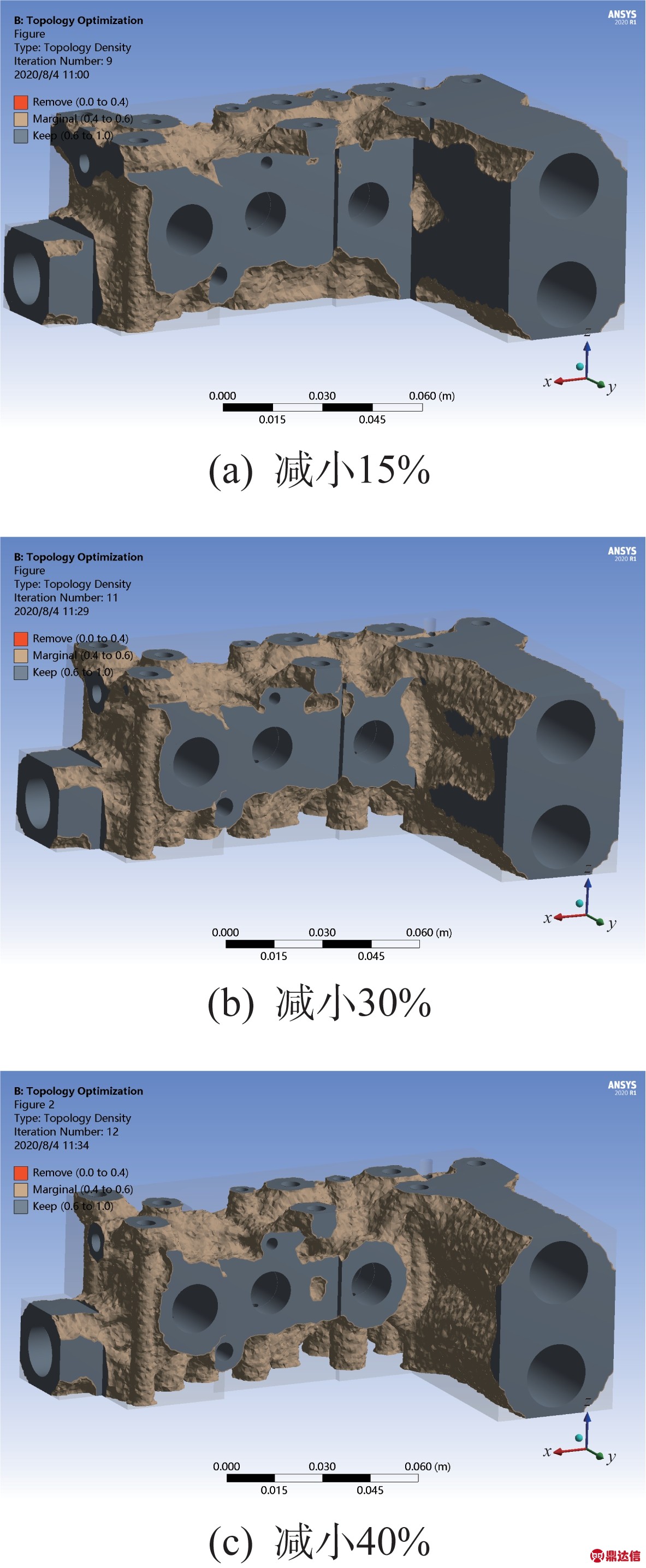
图14 2DCT电液控制系统液压阀体拓扑优化结果
Fig.14 Topology optimization results of hydraulic valve body of 2DCT electro-hydraulic control system
4.2.3 优化结果处理
选取保留60%体积的2DCT电液控制系统液压阀体进行处理。首先对其进行表面圆滑处理并实体化,导入三维建模软件后对不利于加工的结构(如图15所示)进行修正,修正原则如下:
1)减少液压阀体开孔数量,提高其整体强度;
2)删除或填补异形结构,降低液压阀体加工难度;
3)对不规则形状进行处理,提高液压阀体整体平整性。
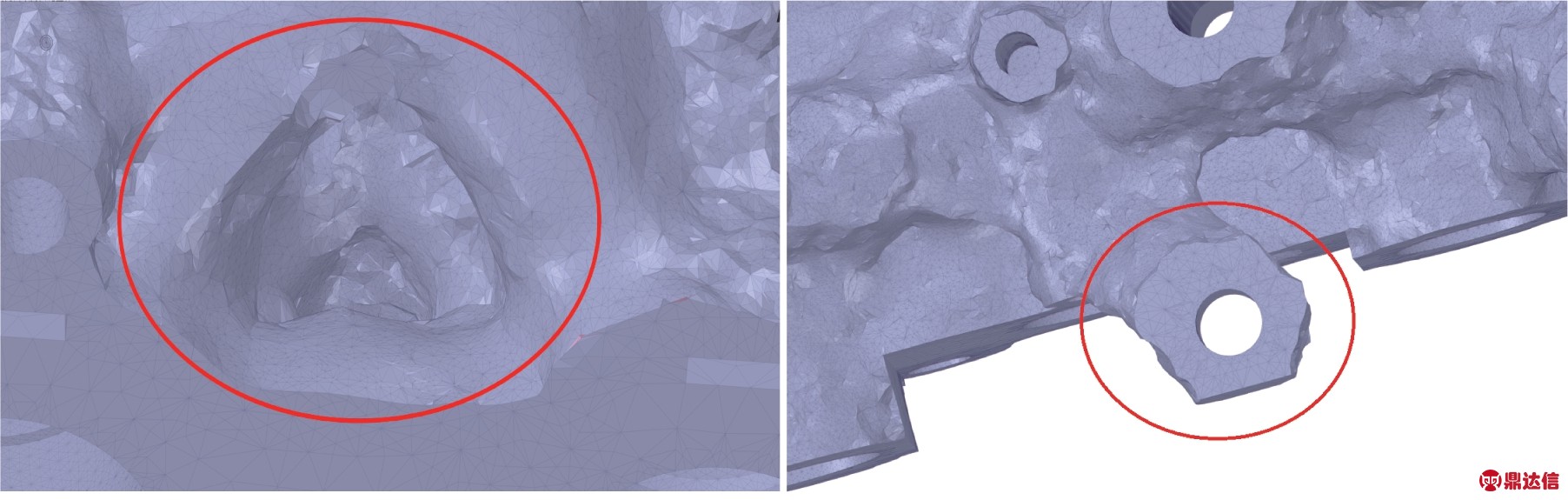
图15 2DCT电液控制系统液压阀体中不利于加工的结构
Fig.15 Structure not conducive to processing in hydraulic valve body of 2DCT electro-hydraulic control system
基于上述修正原则,得到图16 所示的2DCT 电液控制系统液压阀体三维模型。相比于优化前的模型,此模型在保证制造要求的前提下油路、油孔及安装孔等结构清晰,且轻量化程度大大提高。

图16 优化后的2DCT电液控制系统液压阀体三维模型
Fig.16 Three-dimensional model of hydraulic valve body of 2DCT electro-hydraulic control system after optimization
4.3 优化后液压阀体强度校核
对优化后的2DCT 电液控制系统液压阀体的强度进行校核,以验证优化后阀体结构的稳定性。通过静力学仿真分析,得到优化后液压阀体的变形云图和应力云图,如图17所示。

图17 优化后2DCT 电液控制系统液压阀体的变形云图和应力云图
Fig.17 Deformation nephogram and stress nephogram of hydraulic valve body of 2DCT electro-hydraulic control system after optimization
在2DCT 电液控制系统中一、二挡分离杠杆位置确定的情况下,液压缸的纵向高度可确定。由于液压阀体纵向高度受到限制,液压缸上、下壁面略薄。根据图17 结果可知,优化后2DCT 电液控制系统液压阀体的最大应力为95.25 MPa,远小于材料的屈服应力。考虑到液压缸内设有套筒来保证活塞工作时其内壁的粗糙度和强度,液压阀体优化结果符合要求。表4 为优化前后2DCT 电液控制系统液压阀体的体积、质量、包络尺寸、最大应力和最大变形量的对比。由表4 可知,优化后液压阀体的体积较优化前减小了24%;包络尺寸基本相同;最大应力和最大变形量虽增大,但仍在安全范围内。综上可知,2DCT 电液控制系统液压阀体的整体优化结果符合预期。
表4 优化前后2DCT电液控制系统液压阀体性能对比
Table 4 Comparison of hydraulic valve body performance of 2DCT electro-hydraulic control system before and after
optimization
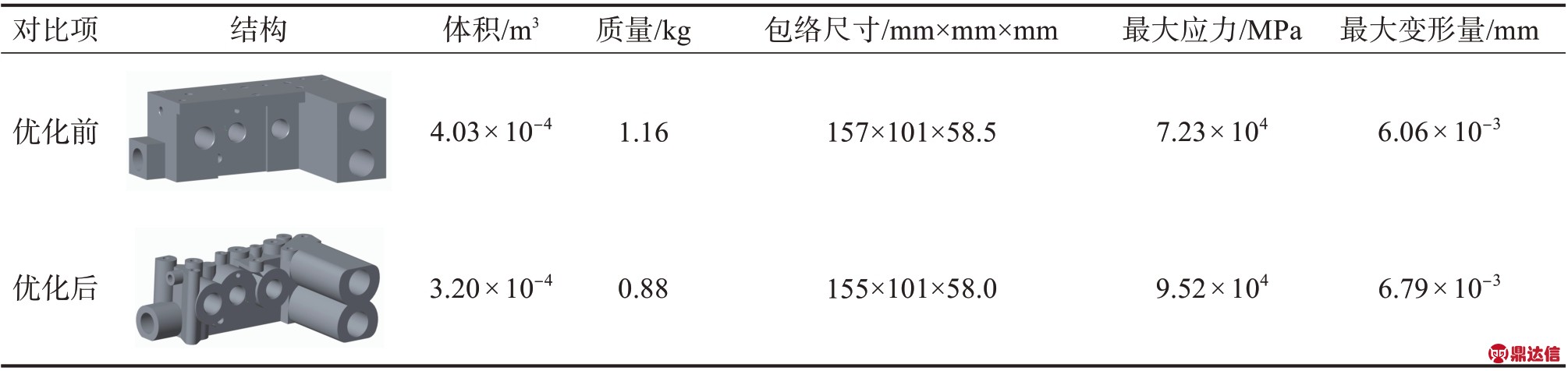
5 结 论
DCT 对于提高电动汽车动力性、舒适性和经济性具有重要意义。本文以某型电动汽车的2DCT为研究对象,对其电液控制系统总成进行设计,并对控制系统液压阀体的结构进行拓扑优化。
1)根据电动汽车和驱动电机的性能参数,确定了2DCT电液控制系统设计方案,并对与其连接的干式双离合器进行设计和装配。
2)对2DCT 电液控制系统进行元件选型和回路设计,通过计算得到了该系统所需的工作压力和充油流量,并设计了一体式液压阀体。
3)对2DCT 电液控制系统液压阀体进行强度分析,并通过拓扑优化对阀体结构进行轻量化设计,在保证结构强度的前提下减小阀体质量。
相比于传统的电液控制系统,本文设计的2DCT电液控制系统的控制效率和功能集成度较高。该电液控制系统采用一体式液压阀体,相比传统的三段式液压阀体,其体积和泄漏量较小,可满足车辆轻量化要求。