摘要:为实现某企业阀门系统口径550mm电动闸阀结构轻质化要求,研究阀体内部流场分布状况,运用有限元法对阀体结构进行瞬态动力学分析与形状优化。建立闸阀参数化模型,采用有限元分析软件对优化前阀体强度进行数值模拟,并基于DOE对闸阀壁厚进行目标优化设计,对优化后的阀体进行流固耦合分析,得到阀体受到的最大等效应力为103MPa。结果表明,改进后的阀体强度能够满足实际工况要求,与原设计相比,产品重量减轻26%,轻量化效果显著。
关键词:电动闸阀;流固耦合;轻量化;结构强度
0 引言
电动闸阀在核电、冶金、石化、国防军工等工业领域有着广泛的应用,其需求量大,使用面广[1]。在动力作用下,通过阀杆运动带动阀瓣的往复来控制闸阀的启闭。其工况环境错综复杂,在高温、高压、强辐射下,阀体结构易出现冲蚀、变形、破损等问题,从而造成极大的安全隐患。我国阀门行业起步晚,发展相对落后,在闸阀设计技术创新、工艺优化、设备管理等方面同世界顶尖水平还有较大差距[2]。在传统的闸阀设计过程中,设计人员仅通过力学公式计算或仿制,估算阀体的受力情况,这种方法显然缺乏准确性与可靠性。近年来,随着有限元技术在工业工程领域的应用日益增加,关于闸阀结构分析优化方向的研究也在逐渐增多。李美求等[3]针对以往闸阀设计方法的缺点,提出其等效应力分类设计途径;Liu等[4]基于数值模拟分析闸阀内液流流动行为,提出闸阀流道优化方法;Luo等[5]利用Abaqus计算出阀体在高压载荷下的应力分布情况,并削减阀体壁厚,得到了满足强度要求的闸阀结构;尚玉来等[6]通过对加强筋位置的优化布局,有效地减少了阀体变形的问题。
现阶段,大多数电动闸阀结构轻量化都通过减小壁厚尺寸,施加阀体内腔压力来分析计算其等效应力。采用流固耦合与DOE(Design of Experiment)协同分析闸阀受力方面的研究还鲜有报道。本文基于流固耦合与DOE功能模块,对某企业电动闸阀进行结构优化与轻量化设计分析,揭示各设计参数同最大等效应力分布的规律。在保证强度要求的前提下,提高了电动闸阀设计水平,缩短制造周期,降低设计成本。
1 模型建立
1.1 三维模型建立
闸阀一般在全开或全闭状态使用,本文主要研究闸阀全开状态下阀体的强度问题。在满足数值计算精度要求的基础上,电动闸阀模型的建立应尽可能简便。故删去不必要的螺栓与倒角,使计算过程更加简便,有利于结果的分析。采用Solidworks建立闸阀阀体的实体模型,如图1所示。
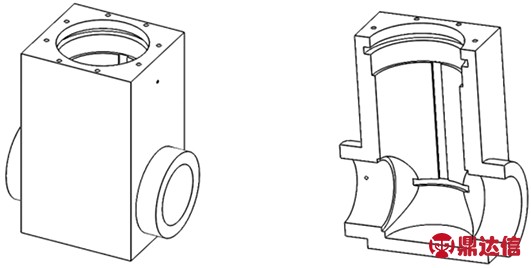
图1 阀体三维模型(左)及剖视图(右)
1.2 数学模型建立
(1)流场数值计算
闸阀内通入的介质为高温蒸汽,在流场中的运动过程遵循一般物理规律。其数值模拟由流体力学计算基本方程构成,即连续性方程、动量守恒方程和能量守恒方程。模拟计算通过数值替换三大方程中的未知数进行求解,进而得到电动闸阀离散后的速度与压力值[7]。假定流动没有热损失,不考虑壁面之间的能量交换。
1)连续性方程:

(1)
式中,ρ为流体密度;u、v、w分别为x、y、z方向上的速度分量。
2)动量(Navier-Stokes)方程:

(2)
式中,ui、uj为平均速度,下标代表不同的方向;ρij为应力;fi为i方向应力。
闸阀内部流道结构复杂,将流道高温蒸汽流动设为标准湍流(k-ε)模型,方程式为:
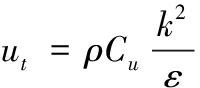
(3)
式中,ut为湍流粘性系数;Cu为经验常数,取0.09;k为湍动能;ε为湍动耗散率。
(2)流固耦合理论
实际工程领域一般由多个物理场构成,单一场基本不能存在。流固耦合分为单向耦合与双向耦合。单向耦合通常不考虑固体域对流体域的作用,而双向耦合则要求两种计算域同时存在。电动闸阀的轻量化着重于固体域的分析,因此选择单向流固耦合作为模拟方法[8]。由于电动闸阀内部流体与内腔之间的相互作用,流道与阀体内腔的各变量相等,具体可表示为如下参数方程:
n·τf=nτs
lf=ls
vf = vs
(4)
其中,τf、τs为流道与阀体的应力;lf、ls为流道与阀体的移动量;vf、vs为流道与阀体的速度。
根据理论式(1)~式(3)在Fluent fluid中对电动闸阀流道进行数值模拟,计算完成后将流道外壁面的压力场结果导入到阀体内耦合面,在Workbench中利用理论(4)进行耦合运算。
2 前处理设置
2.1 网格划分
将建立的三维模型导入到DM(Design Model)中,采用fill功能抽取闸阀内流道,区分开两种不同计算区域[9]。采用Ansys mesh自由网格划分方式,将跨度中心角设为细化(Fine),相关中心参数设为细化(Fine),滑移度设为高(High)。阀体模型划分单元总数为159947,流道模型划分单元总数为120150。网格划分模型如图2所示。
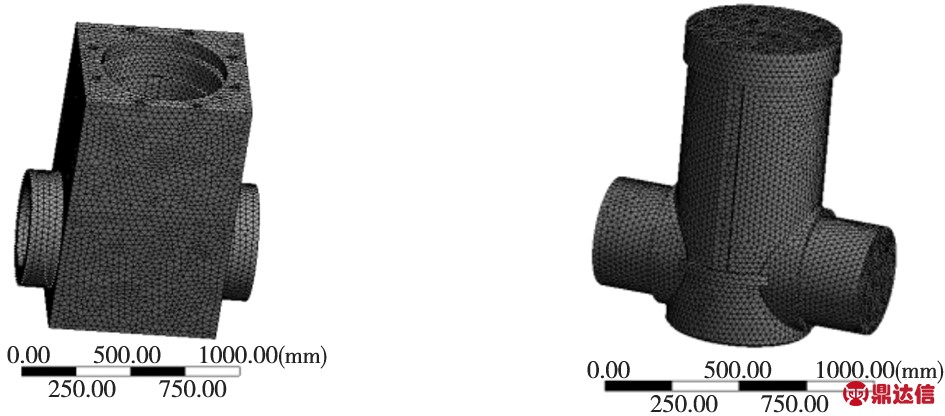
(a)阀体 (b)流道
图2 网格划分
2.2 数值模拟设置
(1)流场
电动闸阀内部流道液流介质为高温蒸汽,工况最大流速不超过50m/s,属于低速流动过程。由于低速蒸汽在流动过程中各项性能参数(如速度、压力、密度等)基本没有变化,可近似等于常数,故闸阀流道介质按不可压缩流体来进行模拟计算[10]。模型边界条件为:采用速度入口,大小为42m/s,温度为540℃;采用压力出口,大小为电动闸阀设计压力10.5MPa;流体域表面设为无滑移,即各方向速度分量为0。
(2)结构场
电动闸阀为特种装备,根据实际需求选用力学性能良好的合金锻造钢F91(10Cr9Mo1VNbN)作为电动闸阀材质。其质量特性包括:质量密度为7780kg/m3,弹性模量为212GPa,泊松比为0.29,设定流体域与固体域交接面为耦合面。
3 数值模拟结果及分析
3.1 数值模拟
在Fluent fluid中进行数值模拟,通过后处理得到流体域的速度矢量和耦合面压力分布情况,如图3所示。
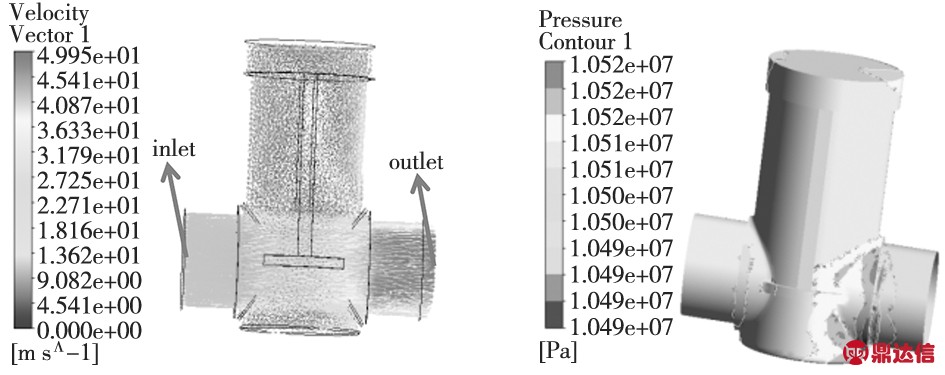
(a)速度矢量图 (b)耦合面压力云图
图3 流道数值模拟结果
由图3a可知,水平方向高温蒸汽流动较稳定,从入口到出口处速度变化范围很小,主流道流速基本维持在42m/s,最大流速为49.95m/s。而竖直方向流道速度较水平方向有一个较为明显的差值,这说明该阀门系统工作时,阀体竖直方向结构的优化对流道压力的损失影响不大,可以适当地减小其壁厚,从而达到轻量化的目标。由图3b可知,流固耦合面压力值基本维持在10.5MPa,流道各处压力稳定。气流在介质流道孔相贯处有较小的压力损失,基本可忽略。阀体弯道边沿处压力最大值为10.52MPa。
在Workbench中构建流体域与固体域的耦合分析,将流体域计算得到的压力输出为固体域的输入载荷,进而得出阀体应力值分布情况,其最大应力点在流道相贯的边沿处,大小为100.35MPa,如图4所示。
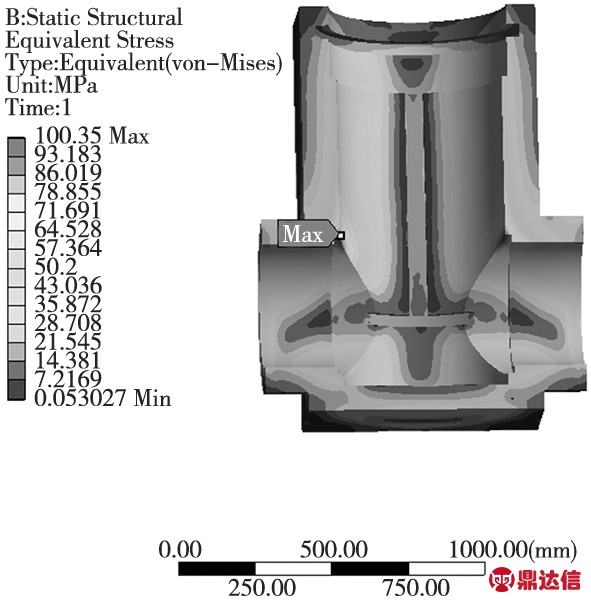
图4 优化前阀体应力分布云图
3.2 结构优化
(1)优化数学模型
从图4可知,除闸阀内腔交汇处等效应力值较大,阀体上部等效应力值较小,在材料许用应力范围之内。因此针对这部分进行降重优化,同时确定横向与纵向加强筋尺寸与分布,以满足闸阀阀体的强度要求。由于电动闸阀的设计要同时满足对安全和经济成本的要求,本文采用Workbench中Design of Exploration优化设计模块,通过设置初始值变化区间与目标函数定义,在取值区间内自动寻优,得到最优的一组解[11-12](即目标函数的临界极值)。选定阀体上部位壁厚h0、横向与纵向加强筋的宽度w1、w2和高度l1、l2为设计变量,σ小于[σ]为约束条件([σ]为许用应力值),阀体的总重量M(kg)为目标函数,建立如下轻量化设计数学模型(5):
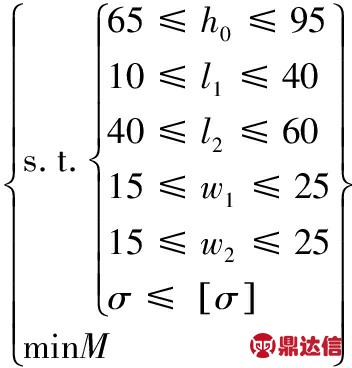
(5)
(2)DOE设计优化
在DOE界面设置好设计参数的上下边界,如表1所示,选择Screening Method算法自动寻优,总共100个样本点。
表1 电动闸阀阀体主要设计变量

更新设计点后,通过多次迭代得到闸阀各参数优化结果。图5为各设计变量对阀体总重量和最大等效应力的局部影响因子图,由图可知,阀体上部位壁厚h0对总重量影响最大;横向加强筋宽度l1和壁厚h0对阀体最大等效应力值的影响较大。
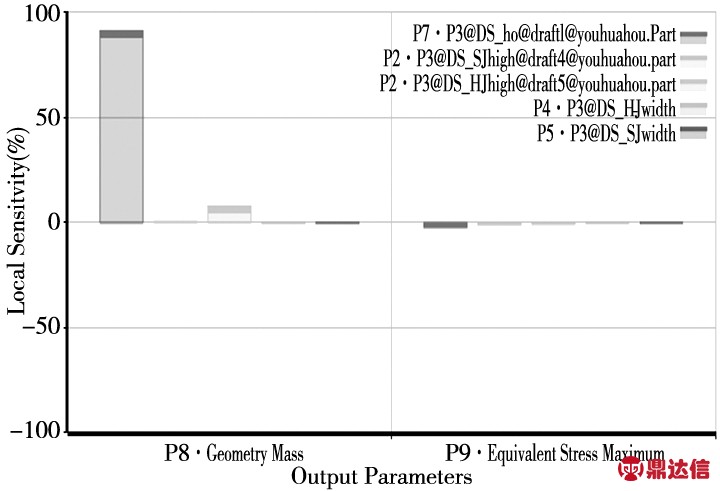
图5 设计变量对目标函数的影响因子图
图6为阀体上部位壁厚h0和横向加强筋宽度w1对总重量规律分布的响应图,由图可知,阀体壁厚h0减小,总重量M有很大的降低,但阀体的强度水平明显下降,安全性能无法得到保障。图7为设计变量h0和w1对最大等效应力规律分布的响应图,由图可知,壁厚h0和横向加强筋w1数值越大,最大等效应力σ越小。但是其数值降低到一定程度后,σ的变化不再明显。经过综合考虑,选用h0=66.792mm、l1=46.860mm、l2=31.579mm、w1=18.617mm、w2=15.629mm为最后尺寸。
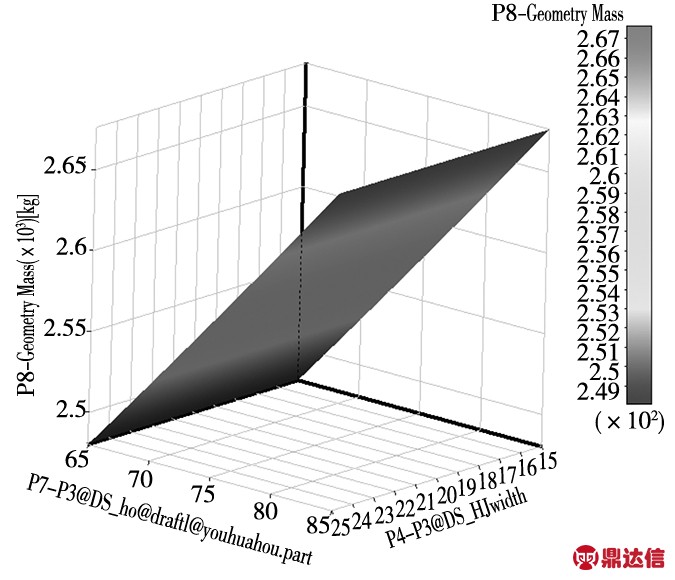
图6 h0、w1对阀体重量变化的3D响应图
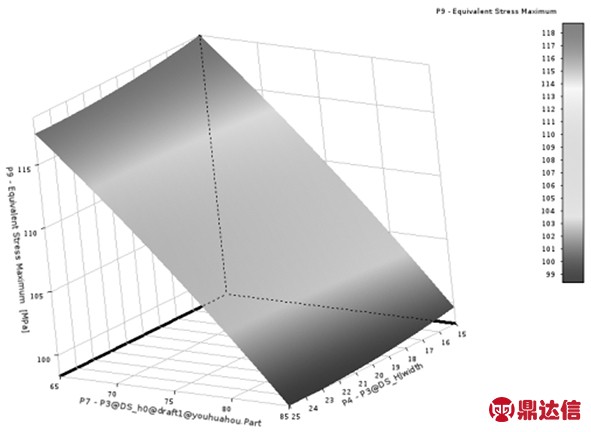
图7 h0、w1对阀体最大等效应力变化的3D响应图
(3)优化后结构分析
将DOE设计后的阀体最佳参数组合传递回Workbench集成分析模块,对阀体与流道进行分析。由于篇幅原因,详细过程不再赘述。其分析结果如图8所示。
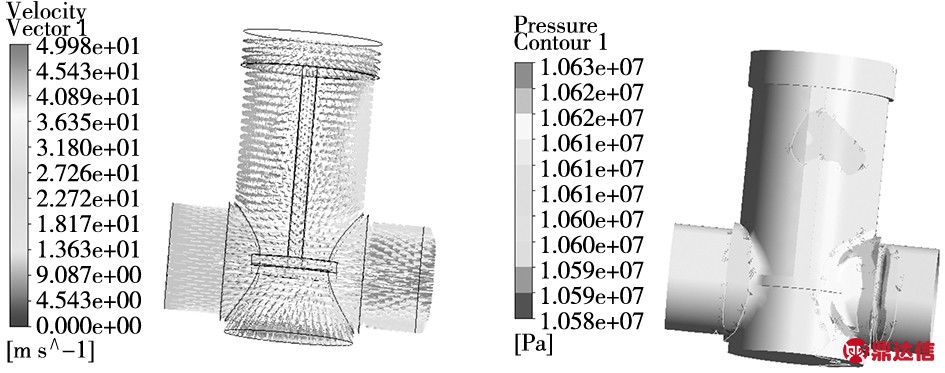
(a)速度矢量图 (b)耦合面压力云图
图8 优化后数值模拟图
由图8a可知,流体最大流速为49.98m/s,与优化前的最大流速差距较小,最大流速位置基本不变。由图8b可知,流固耦合面处的最大压力为10.63MPa,闸阀内流道流体流动特性基本不变。
将流固耦合结果导入到静力学分析模块,得到优化后阀体所受等效应力如图9所示。
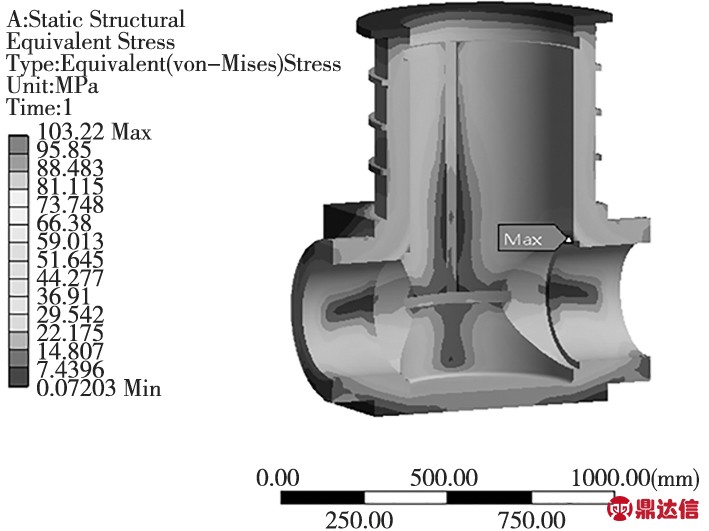
图9 优化后阀体等效应力分布图
由图9可知,结构优化后阀体受到的最大等效应力值为103.22MPa,小于材料的许用应力,结构强度满足要求。
表2为优化前与圆整优化后阀体各参数对比分析,阀体壁厚h0由80mm减小到68mm,壁厚降低16%。优化前后阀体所受最大等效应力差距较小,能满足强度要求。同时,电动闸阀的总重量由3488kg减小到2579kg,轻量化效果明显。
表2 优化前后阀体参数对比
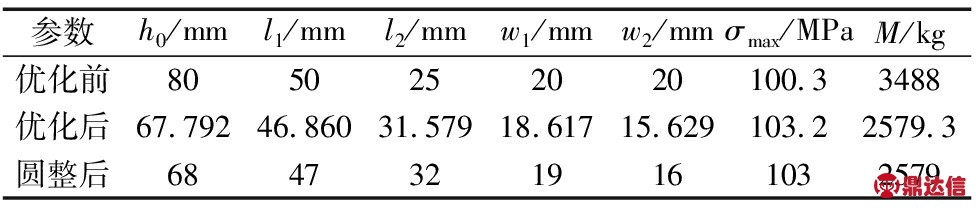
4 结论
本文以某企业DN550电动闸阀为例,以其阀体结构轻量化为目标,基于Ansys Workbench环境多功能模块结合的优化设计,得到以下结论:
(1)利用流固耦合方法可以更准确地模拟实际工况下阀体的受力状况。由阀体结构应力云图可知,阀体上部位整体受到的应力值较小,优化后阀体结构应力分布更加均匀。最大等效应力发生在阀体垂直与水平通道相贯处,造成阀体内部结构的疲劳损坏。
(2)采用Design of Exploration优化设计模块研究了电动闸阀阀体上部位壁厚、横向与纵向加强筋尺寸与最大等效应力之间的关系。在目标区间内,随着设计参数的增大,阀体所受最大等效应力值增大,达到临界值后最大等效应力趋于稳定。优化后阀体总重量降低26%,极大降低了材料成本。
(3)本文结合流固耦合技术与DOE设计对阀体进行仿真优化,减少了电动闸阀的设计周期和材料成本,为未来闸阀类产品设计开发提供了一种行之有效的研究方法。