摘要: 针对液压滑阀阀体沉割槽内液体流速不同会产生径向卡紧力的问题,利用CFD软件对某滑阀沉割槽处阀芯台肩所受径向压力分布进行研究,同时,根据滑阀内部流道的结构特点,结合理想流体伯努利方程,建立了沉割槽处阀芯台肩上压力分布的数学模型,并且通过实验验证了模型的准确性,分析了沉割槽尺寸及流量对阀芯径向压力分布的影响。研究表明:阀芯台肩上径向压力分布不均匀,且压力值随入口流量、沉割槽深度和宽度呈二次多项式函数关系上升;随压力点位置从远离出口位置至靠近出口呈平方关系下降;当阀口开度为0.5 mm、流量为40 L/min时阀芯台肩径向卡紧力为4.2 N,是流量为10 L/min情况下的16倍,且沉割槽深度减半后,卡紧力增至14.47 N。最后,提出了一种偏心沉割槽结构,仿真结果表明,入口流量大于40 L/min时,偏心沉割槽结构中径向压力分布的不均匀度比传统同心结构提高了64%以上,有效降低阀芯径向卡紧力。
关键词: 滑阀;沉割槽;径向卡紧力;偏心
阀芯作为液压滑阀的运动部件,其上所受的液动力、摩擦力等是制约滑阀特性的一个重要的因素,而其所受的径向不平衡力会产生阀芯卡紧,是影响运动特性关键因素之一。近10年来,Amirante[1]运用计算机仿真技术研究了开中心滑阀阀芯上液动力与开口的变化关系并进行了实验验证[2];设计了一种阀杆中部增加补偿轮廓的比例换向阀阀芯,能够平衡阀芯上液动力[3]并进行了实验验证[4]。王安麟等运用CFD技术研究了滑阀开启关闭过程中瞬态液动力的影响,并运用参数化建模优化阀芯中部补偿轮廓尺寸,为滑阀多学科结构优化奠定了基础[5];吴小峰等利用计算机流体动力学方法研究了液压换向阀轴向瞬态液动力的影响因素,同时提供了滑阀内部流道结构参数的优化设计方法[6],但文献[5-6]方法需要大量的试验数据,很难从理论上得到结构的最优设计。Lisowski等运用CFD和实验结合的方法,研究了在阀体上增加内流道的方式,可以在不改阀芯驱动力的情况下提高45%的额定流量[7]。Lisowski等通过设计合理的阀芯几何结构,运用液动力在比例换向阀中进行压力补偿[8-9],使得阀口射流角仅与阀芯位置相关,与压力无关,但并未明确油液流动形式、阀芯尺寸及其对阀性能参数的影响。Posa等运用边界层结合直接数字仿真技术分析了阀的开口量和阀口压差对流量系数和液动力的影响[10],然而此研究难以通过实验进行验证。Guo等研究了大流量阀芯上不平衡力产生滑阀的液动力和阀芯振动,并提出每对阀口结构相同且初始开口或者遮盖量相等的条件下,可以确保作用在各阀口上液动力平衡[11],但尚未进行实验验证。冀宏等研制了非全周开口滑阀压力分布及噪声测量实验装置[12],通过阀套平移和转动依次测量不同开度阀口下阀腔壁面压力分布,并为研究节流槽结构、压力分布和噪声间的关系提供实验平台,为解决阀口局部压力测量提供一种有效的方法。以上学者均针对滑阀阀芯运动所受液动力对阀芯轴向受力的影响因素及改进措施。针对径向卡紧力研究,Hong等设计了一种螺旋槽的滑阀阀芯台肩[13],用以改善润滑效果及压力分布。其他学者[14]也多关注于阀芯台肩形状、平衡槽的形状尺寸及偏心等方面的研究。为了进一步提高液压阀的功率重量比,减小阀芯运动所需的驱动力,除了上述学者研究方向外,陆倩倩等首次提出在液压滑阀内部沉割槽由伯努利效应引起的液压卡紧亦存在,并通过仿真进行系统分析[15],但尚无理论和实验支撑。因此,为降低传统滑阀和2D伺服阀[16-17]阀芯启动时需要克服的卡紧力,研究滑阀阀芯径向压力分布及卡紧力的影响因素非常重要。
本文首先通过可视化手段对某滑阀的出口处沉割槽内的流场进行建模和仿真分析,讨论沉割槽内流场作用在阀芯台肩上径向压力分布及其影响因素;然后,根据连续性原理和理想的伯努利方程建立了出口截面沉割槽处阀芯台肩上径向压力分布的理论公式,并通过实验对阀芯台肩上压力进行测量,验证了仿真和理论分析结果,其次,通过径向压力分布进行了径向卡紧力的计算,最后提出一种偏心形式的沉割槽结构并进行了数值仿真验证。
1 模型建立
1.1 仿真模型
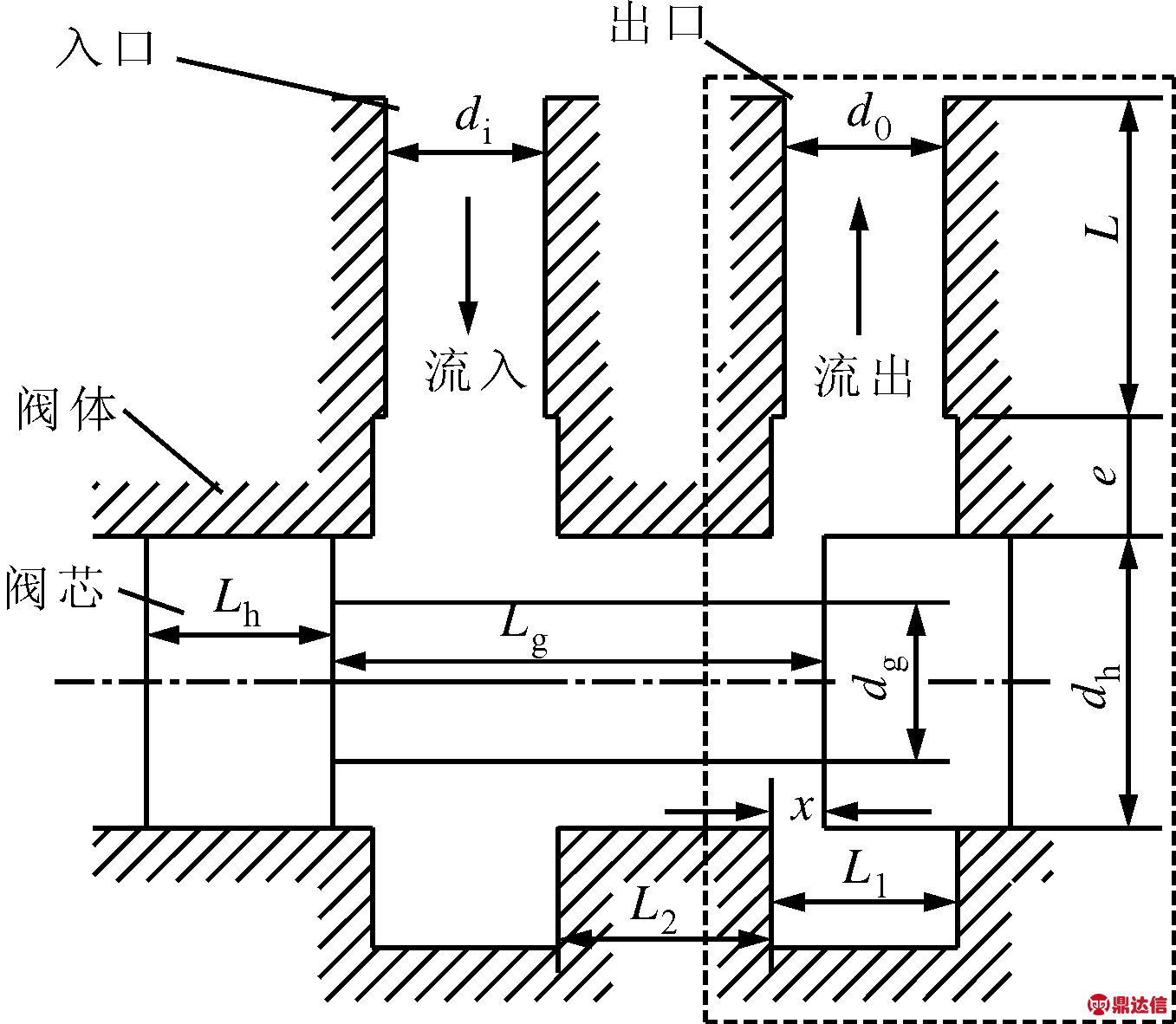
图1 两位两通滑阀结构示意图
本文以某六通径两位两通滑阀为研究对象,额定流量为60 L/min,结构如图1所示,其中沉割槽宽度L1为7 mm,槽深e为4 mm,活塞直径dh为11 mm,活塞环长度Lh为7 mm,活塞杆直径dg为6 mm,出、入口直径do、di均为6 mm,工作方式为出口节流。考虑阀腔内结构的对称性,建立图1虚线框内阀腔流体域的半剖模型。将三维模型进行四面体网格划分,同时定义进口、出口、对称面和壁面,如图2a所示。将网格导入到Fluent16.0中,定义流动介质为ISO VG 32液压油,密度为873 kg/m3,黏度为0.027 9 kg/(m·s),选用稳态模拟,及标准的k-ε模型,定义入口形式为流量入口,出口为压力出口,并且选用SIMPLE算法设置仿真补偿和时间。图2b为出口压力5 MPa,入口流量为40 L/min的压力云图。
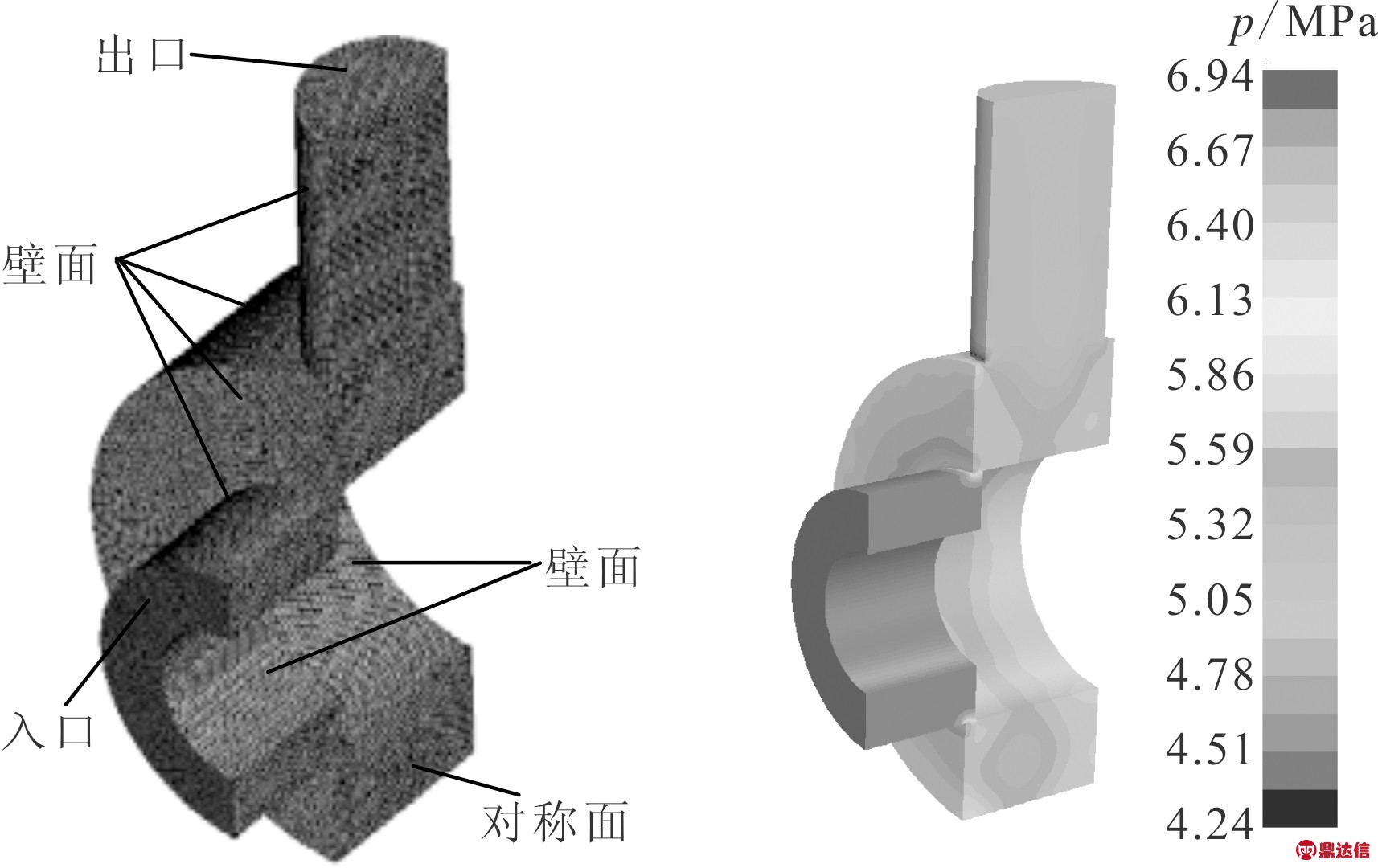
(a)模型网格 (b)压力云图
图2 仿真模型网格及压力云图
1.2 仿真条件及结果
仿真条件设置如下:入口流量Q分别为10 L/min、40 L/min;阀口开度x分别为0.5 mm、2 mm;沉割槽深径比e/dh分别为0.18和0.36。
在通过出口轴线与阀芯轴线相垂直的截面上,每隔π/6选取阀芯台肩表面上6个关键点,提取不同仿真条件下关键点的压力值,压力分布曲线如图3所示,其中右侧纵坐标适用于流量为10 L/min的情况。
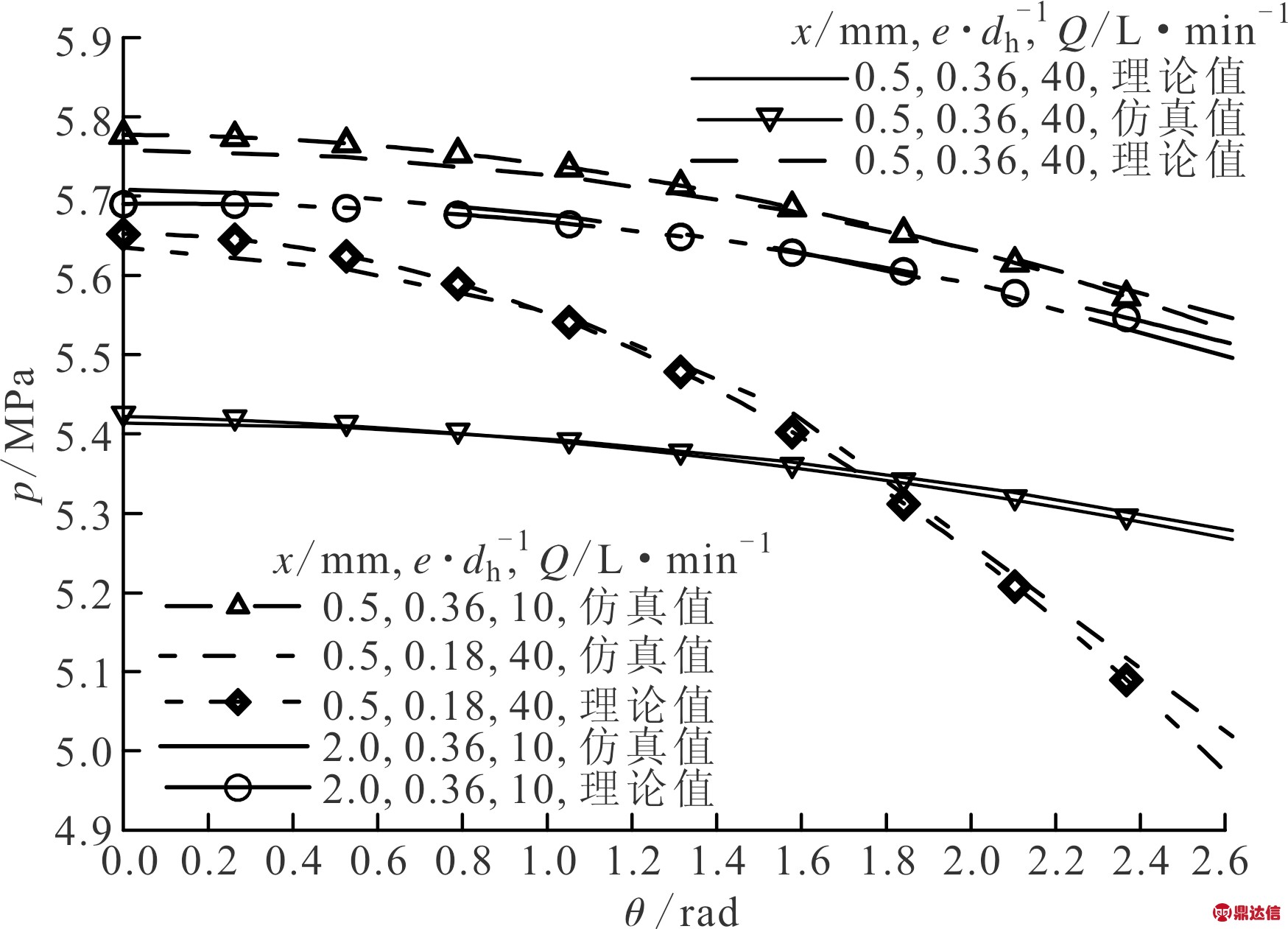
图3 理论和仿真结果曲线汇总
由图3中仿真曲线变化趋势知阀芯凸肩上关键点的压力值随流体流向出口的方向递减。流量越大,压力递减的幅度越大。出口压力为5 MPa,e/dh为0.36,当入口流量为10 L/min和40 L/min时,压力降低幅值分别为0.010 MPa和0.150 MPa;e/dh越大,压力递减幅度越小,入口流量为40 L/min,出口压力为5 MPa时,e/dh分别为0.18和0.36时,压力递减幅值为0.616 MPa和0.150 MPa;且根据文献[15]中研究可知,压力变化幅值与出口压力无关。
2 理论分析
2.1 理论推导
为研究出口节流环槽处阀芯台肩上压力分布情况,假设以下5种情况:
(1)忽略图1模型中入口油液流入滑阀阀杆与阀体区域的影响;
(2)静态仿真,无壁面滑移;
(3)油液不可压缩且特性稳定;
(4)忽略壁面上粗糙度及缝隙泄漏;
(5)忽略流动过程的粘性摩擦损失。
流体从滑阀阀杆与阀体构成的同心圆环流入,经节流阀口至沉割槽区域,再汇流至出口流出,如图4a中箭头方向所示。为得出沉割槽处阀芯凸肩上压力分布的理论表达式,选取夹角为dθ的微元为研究对象,如图4b所示,dθ微元中油液从区域①流入,经过阀口②,到达区域③。
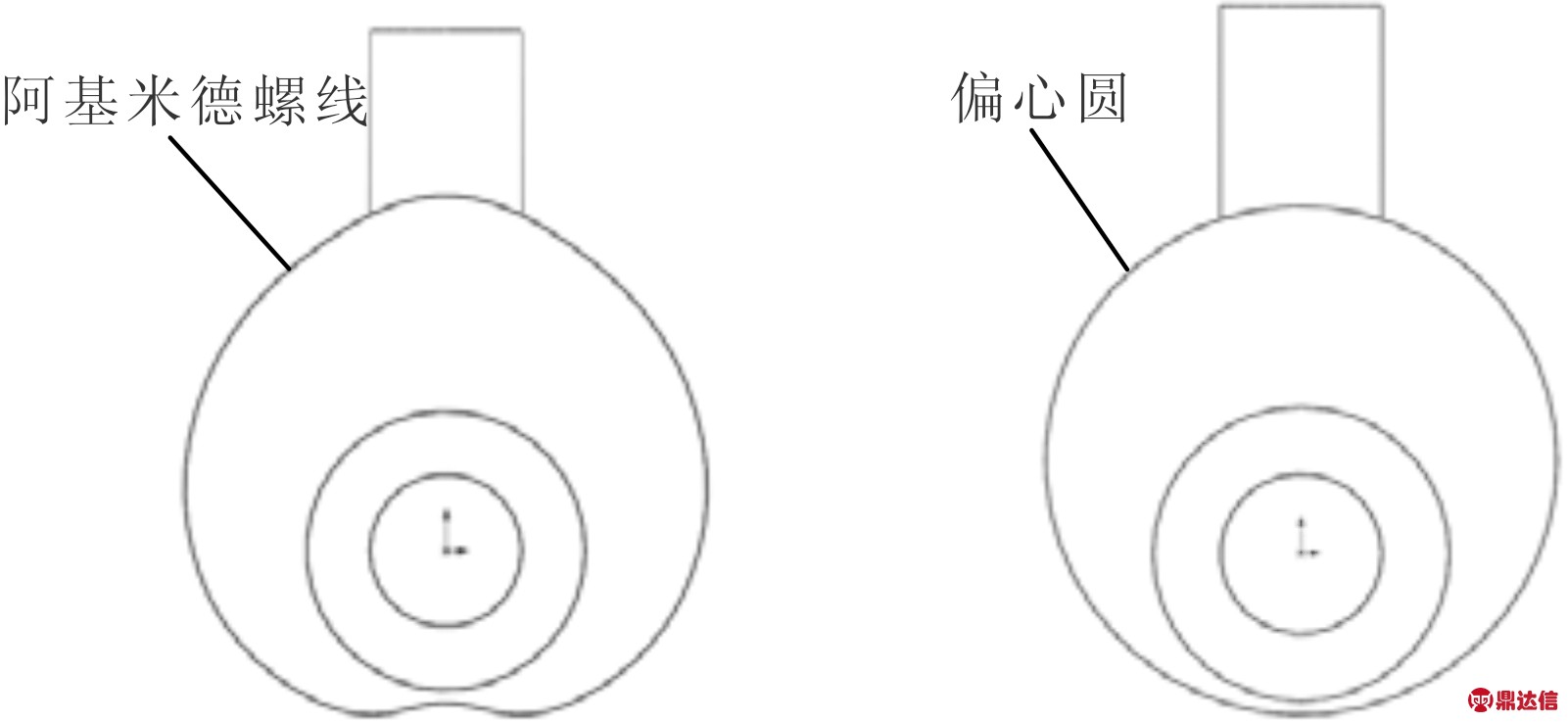
(a)液流方向 (b)微元
图4 模型中液流方向及微元
因滑阀阀口属于异型流道,其临界雷诺数为280[18],认为滑阀正常工作均属于紊流状态。根据薄壁小孔节流公式,微元中经区域①流经阀口②的流量表达式为
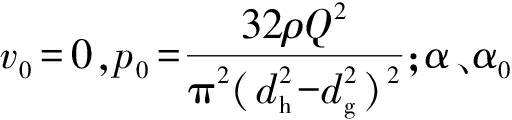
(1)
式中:Cd为流量系数;x为阀口开度,mm;δ为阀芯与阀体间隙,mm;ρ为流体密度,kg/m3。每个dθ对应的区域均有dQ流量流入沉割槽区域③。且在沉割槽壁面的限制下形成漩涡,如图5所示。根据假设,沉割槽处阀芯台肩上由漩涡产生的轴向速度相等且会产生能量耗散,当能量耗尽后,沉割槽区域内的油液沿着图5a中虚线箭头方向从0经π/2向π方向汇总至出口流出,因此沉割槽内任意θ位置对应的流量为
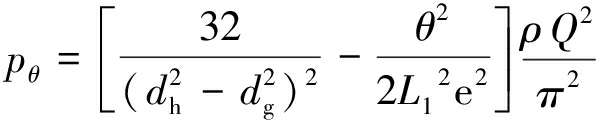
图5 沉割槽截面内的漩涡

(2)
理论上,当θ=0时,Q0=0。故沉割槽内任意θ位置的平均流速vθ等于Qθ与该位置沉割槽内通流截面面积Aθ的比值
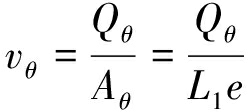
(3)
根据入口流量Q等于通过节流口的流量
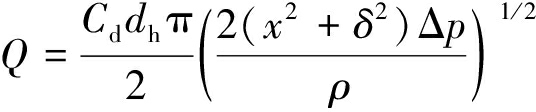
(4)
且理想伯努利方程为
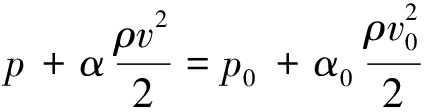
(5)
由式(2)~式(5)可得沉割槽内压力pθ分布
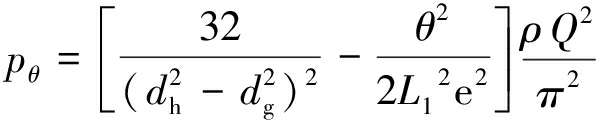
(6)
式中:p0、v0分别表示压力点在0驻点位置对应的压力和流速[18],且取为动能修正系数,取1。
由式(6)可以看出,沉割槽内压力分布与压力点位置θ、入口流量Q、沉割槽截面尺寸L1和e有密切关系。
2.2 理论解析和仿真对比
图3为阀口开度x分别在0.5 mm和2 mm、入口流量Q为10 L/min和40 L/min、沉割槽深径比e/dh等于0.18和0.36情况下关键点的压力分布理论和仿真曲线,曲线随压力点位置成抛物线下降的趋势,压力值也十分吻合。验证了式(6)的压力值随位置点关系是正确的。
图6表示出口压力为5 MPa、e/dh为0.36的情况下,压力点分别在π/6、π/2和5π/6位置的压力值随入口流量变化的仿真曲线。由图6可见,仿真曲线呈抛物线上升关系,与式(6)中压力分布随流量变化趋势一致。因式(6)中的中括号项在θ∈[0~5π/6]区间,恒大于0,故在理论上关键点压力值随流量增加呈抛物线上升,且压力幅值随着压力点位置靠近出口而逐渐减小。
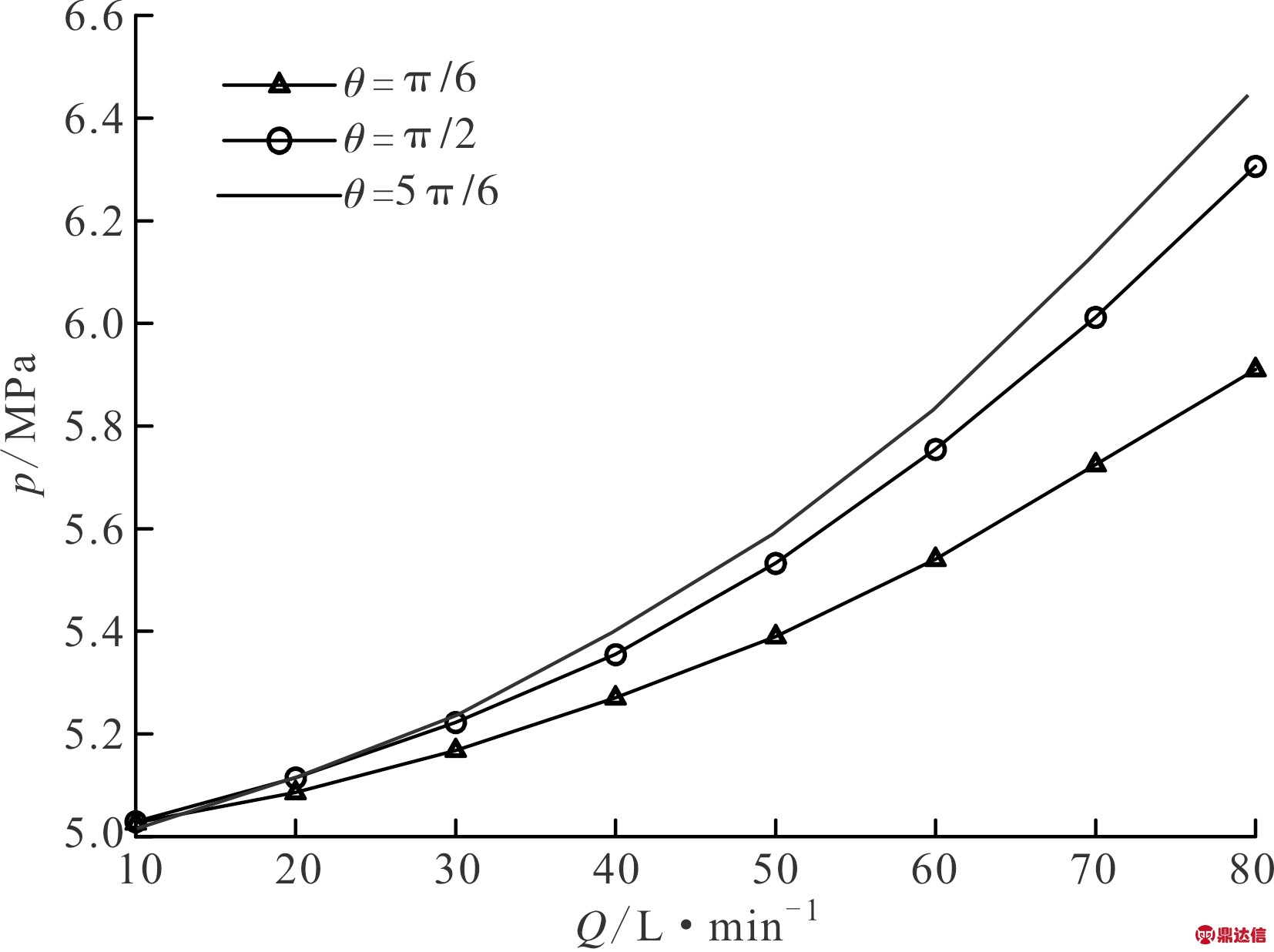
图6 不同流量下同一位置点的压力分布曲线
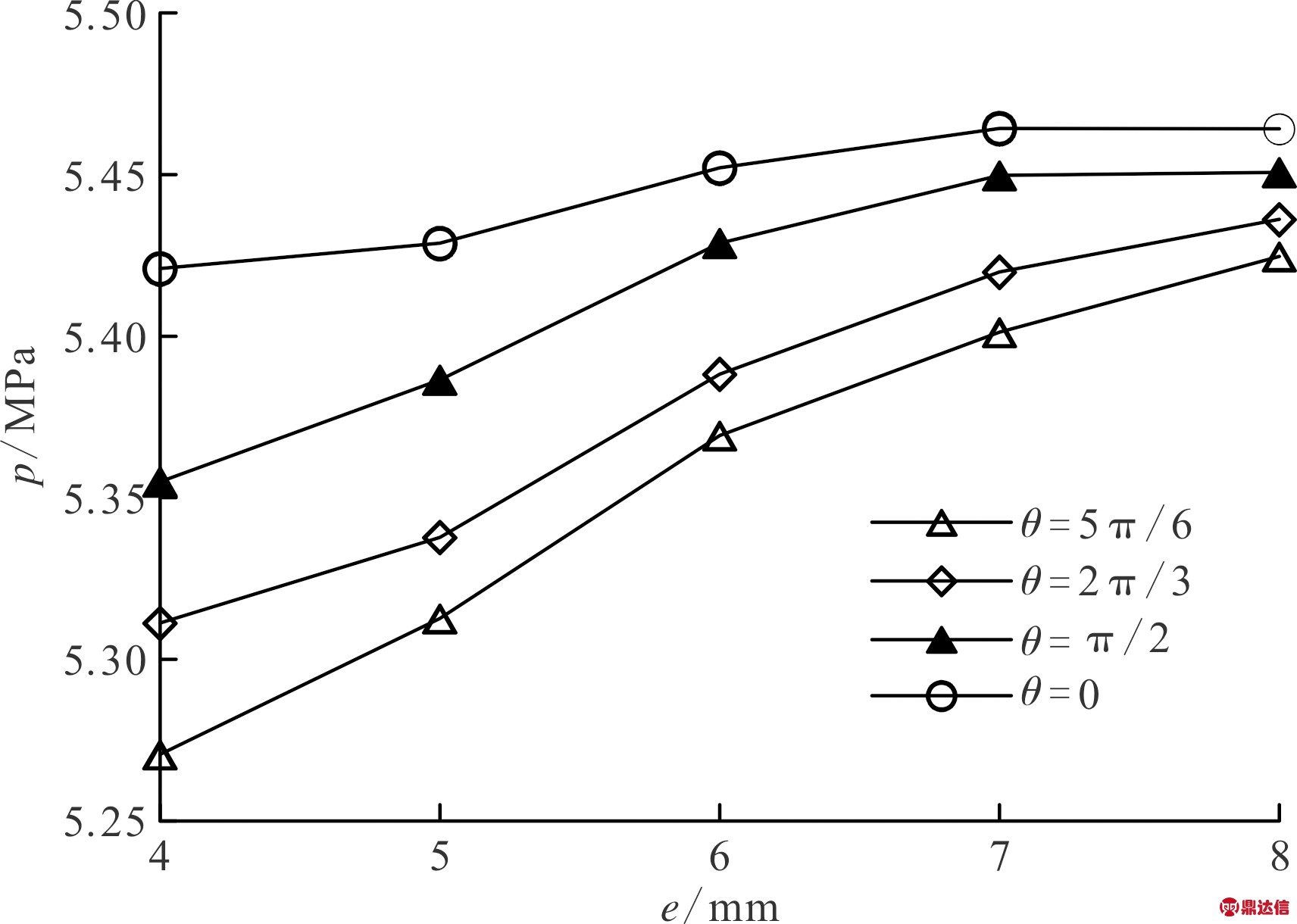
图7 40 L/min时沉割槽不同深度同一位置的压力分布曲线
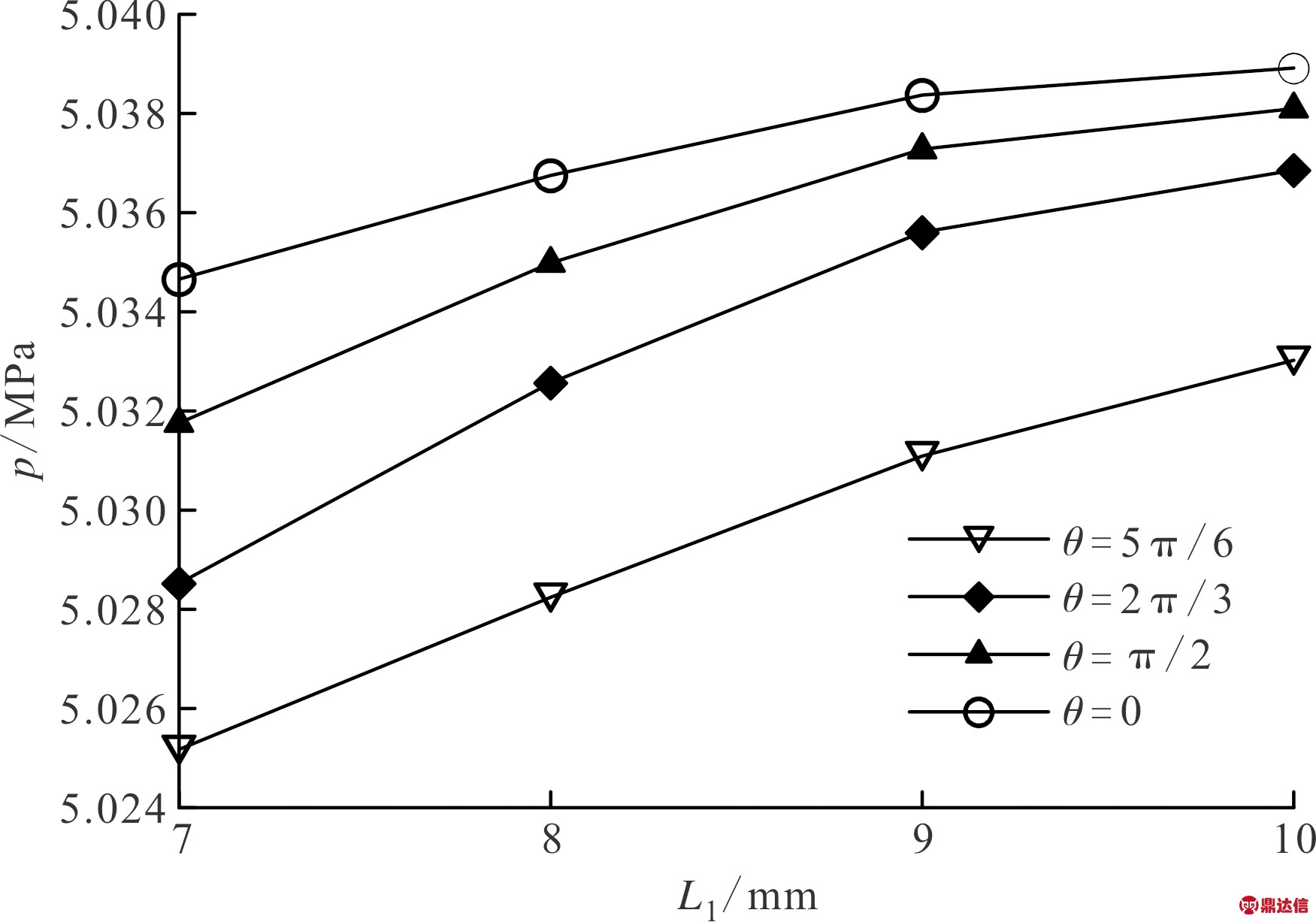
图8 10 L/min时沉割槽不同宽度同一位置的压力分布曲线
图7和图8为相同入口流量和阀口开度下,不同沉割槽尺寸的压力分布仿真曲线。图7是在入口流量为40 L/min,沉割槽宽度为7 mm的情况下,深度为4、5、6、7和8 mm这5种情况下,关键点位置在0、π/2、2π/3和5π/6下的压力分布仿真曲线;图8是入口流量为10 L/min,沉割槽深度为4 mm情况下,宽度为7、8、9和10 mm这4种情况下,阀芯台肩关键压力点位置在π/6、π/2、2π/3和5π/6时的压力分布仿真曲线。由图7、图8可见,压力分布随沉割槽深度和宽度近似成二次幂函数分布,与理论公式中的关系吻合。
综上,通过理论和仿真结果对比得出,关键点的压力值与压力点位置呈二次多项式函数下降关系,与入口流量、沉割槽宽度和深度均呈二次多项式函数上升。由图5~图8可以得出,入口流量、关键点位置及沉割槽尺寸对压力分布影响与式(6)中各参数之间影响关系在理想情况下非常吻合,故式(6)在理想情况下可作为计算沉割槽处阀芯台肩径向压力的参考公式。
3 实验验证
3.1 实验台架
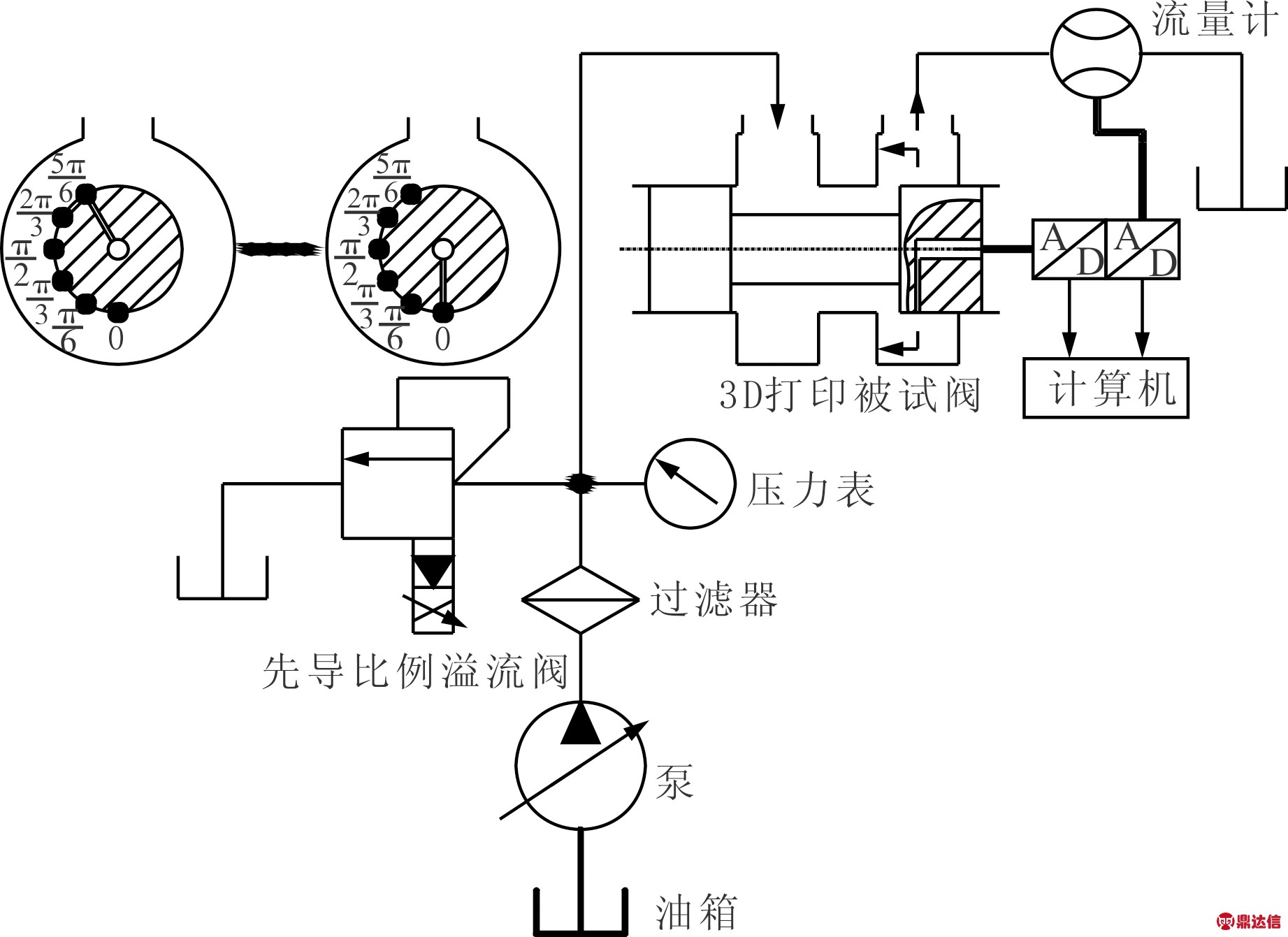
图9 实验台原理示意图

图10 实验测试现场图
为了验证沉割槽内关键点的压力分布,搭建原理如图9所示的实验系统。系统主要由液压泵站、传感器、采集卡和计算机等组成,测试现场如图10所示。被测试的对象使用3D成型技术制作出固定开口(x=0.5 mm)的6个被试阀,被试阀内部尺寸与仿真模型尺寸相同,每个被试阀引出一个位置的测压油道,即6个被测阀的测压油道分别对应θ=0、θ=π/6、θ=π/3、θ=π/2、θ=2π/3和θ=5π/6,且测压油道尺寸相同。图11是测压油道位置在θ=0位置时的剖分图。测压油道通过转接阀块引出测压口,连接压力传感器(Huba 511.940003142,0~6 MPa),如图10。通过NI 6361采集卡将压力信号传至计算机,上位机使用LabVIEW2014编写的通用采集程序,以单通道1 kHz的采样频率,并将各通道信号滤波、平均及量纲转换后作为被测点的压力值。
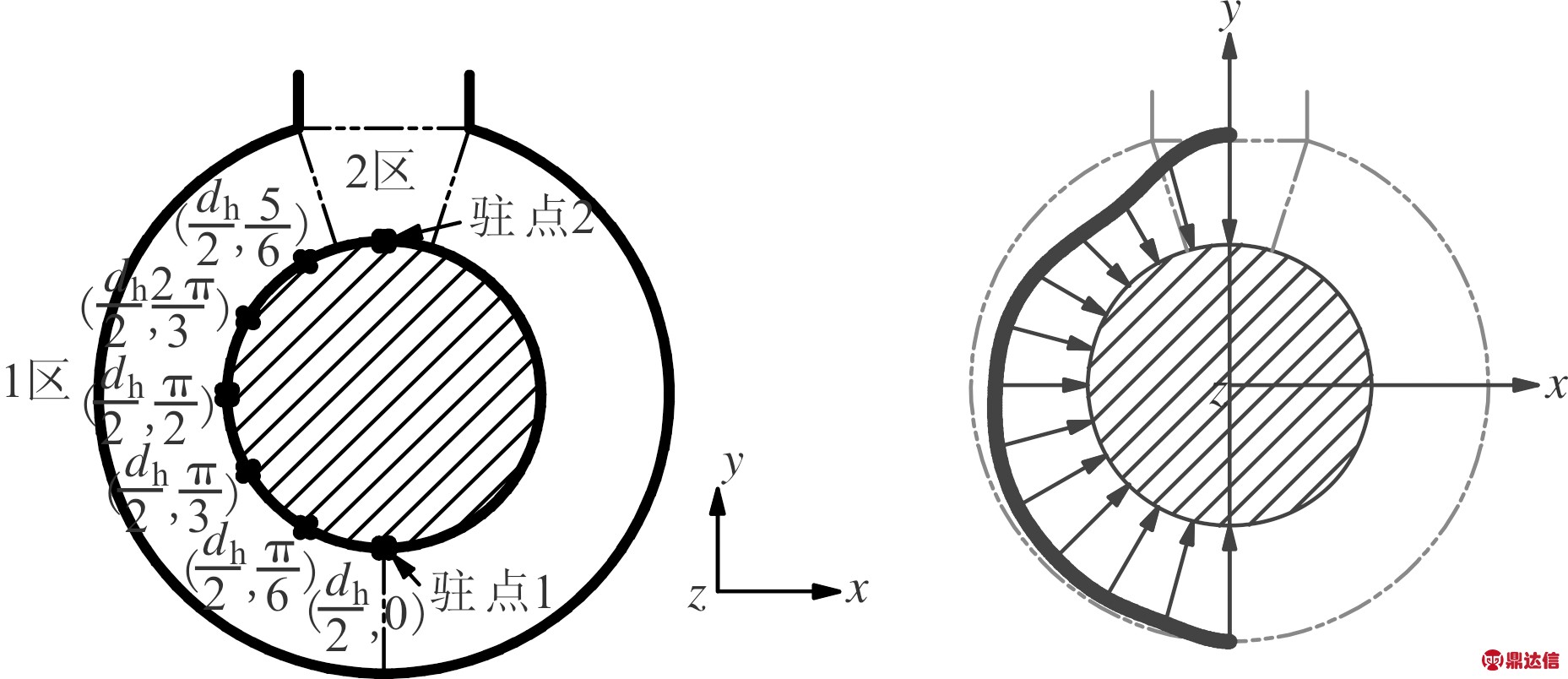
图11 3D成型阀剖面图
3.2 实验结果
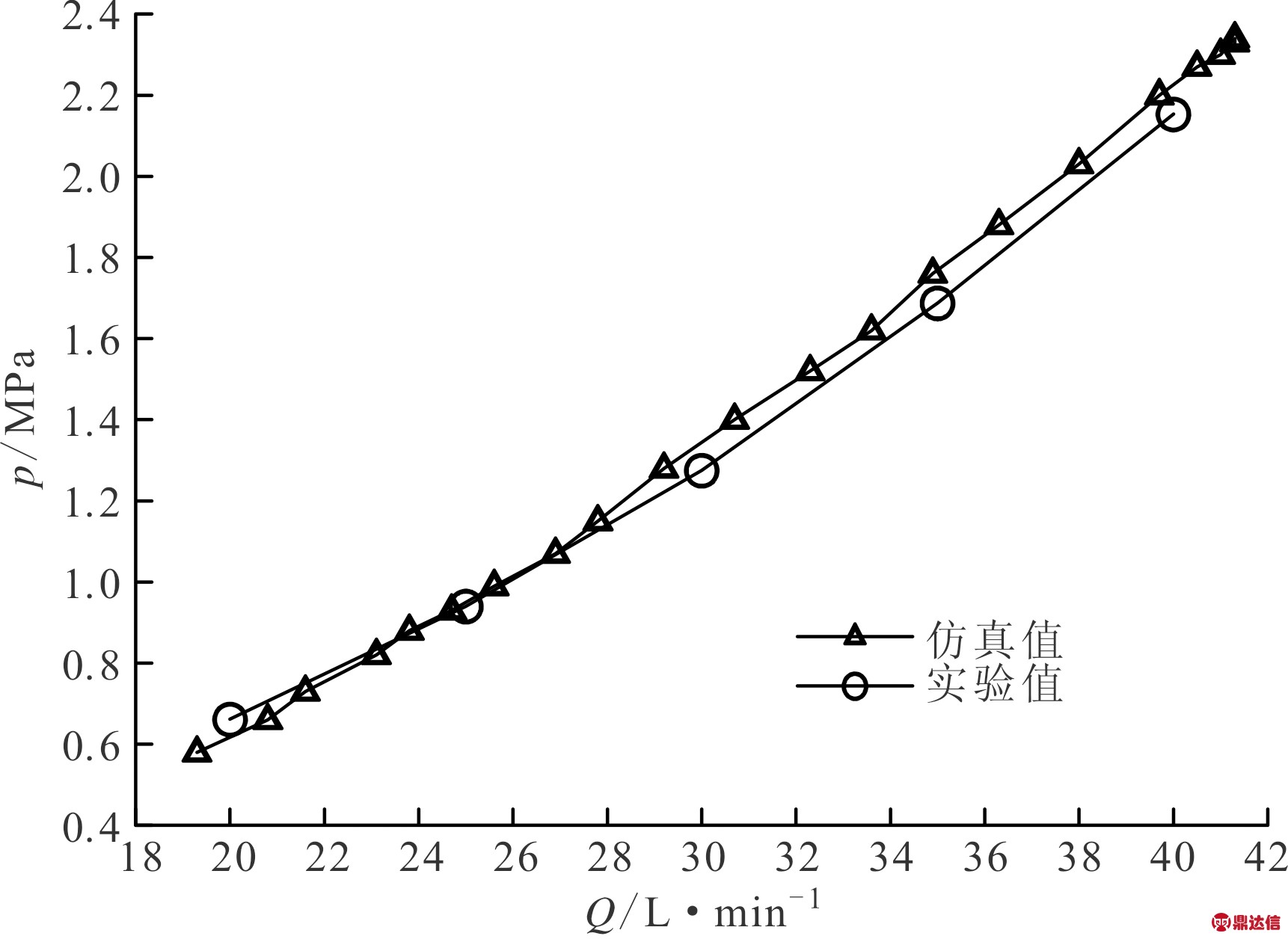
图12 0位置压力随流量变化的仿真和实验曲线
实验过程中,被试阀的入口流量从19 L/min逐渐增加至40 L/min,记录关键点随流量变化的压力值。图12为测压点在0位置时的压力分布与入口流量的关系,实验和仿真压力随流量变化趋势一致性很好。图13是入口流量在40 L/min下,关键点位置从0到5π/6变化时的压力分布实验和仿真结果,验证了压力值随测压点从远离出口到靠近出口附近逐渐下降。
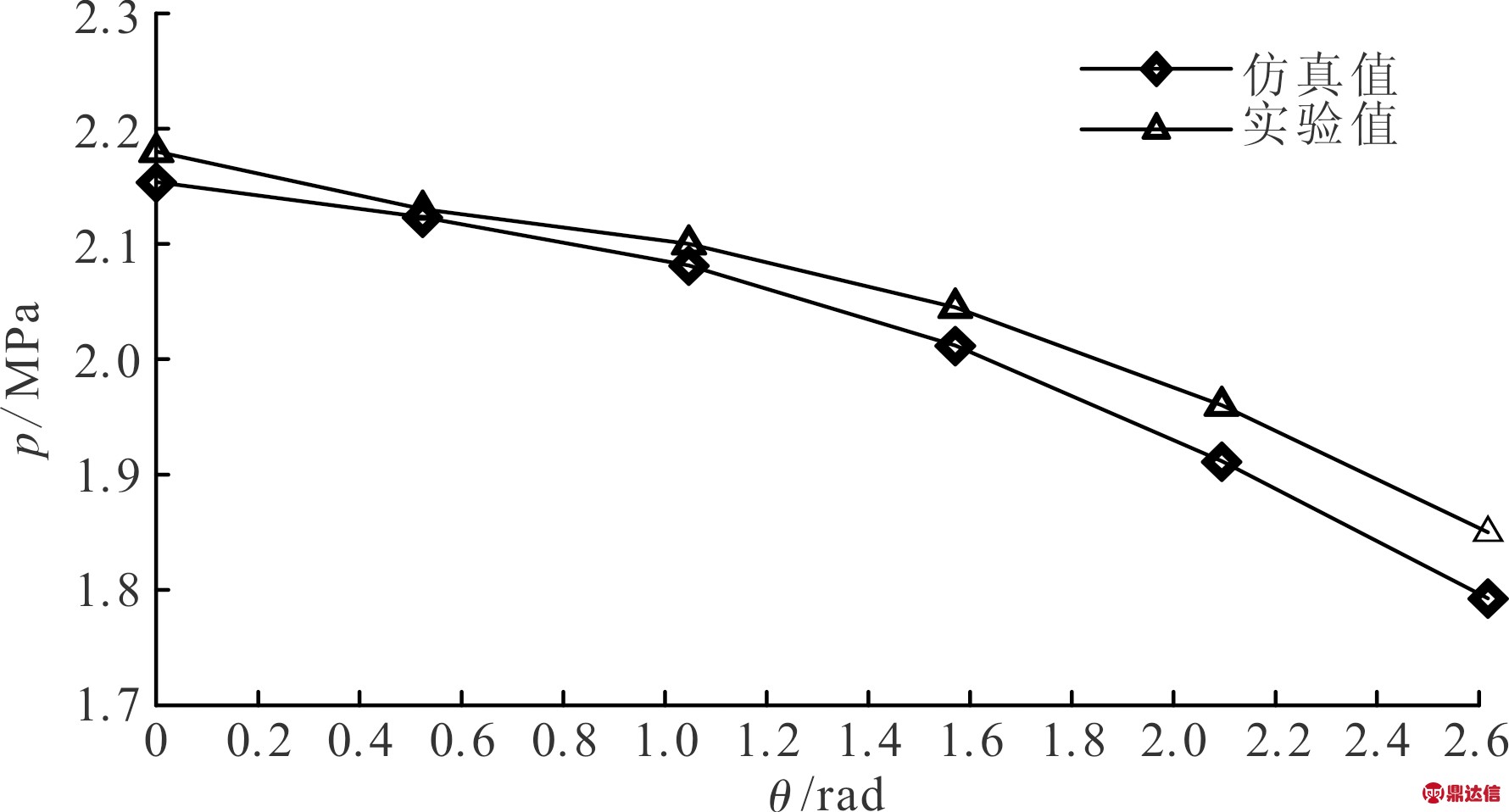
图13 40 L/min时阀芯台肩周向压力分布仿真和实验曲线
4 阀芯台肩径向卡紧力分析
忽略阀芯台肩上轴向压力分布不均,且模型关于对称面(X=0)对称,仅讨论Y方向径向力。根据式(5),将台肩径向压力与其所在微元弧面积相乘后沿Y轴方向进行投影,得到微元上阀芯台肩所受的径向力沿Y轴的分力为
dFy=0.5Pθ(L1-x)dhcosθdθ
(7)
将dFy在θ∈[0~5π/6]范围内进行积分,得Y轴方向上径向卡紧力
Fy=dFy=

(8)
由式(6)可得:当入口流量为10 L/min和40 L/min时,开口量为0.5 mm,L1=7 mm,e=4 mm的情况下Y方向的径向合力分别为0.26 N和4.2 N;当沉割槽深度e=2 mm时,入口流量为40 L/min时,Fy=14.47 N。由此可知,阀芯台肩上因伯努利效应产生的径向压力不均会产生径向卡紧力,且流量越大,径向卡紧力越大;沉割槽深度越浅,径向卡紧力急剧增加。
5 沉槽结构优化分析
5.1 驻点及台肩径向压力分布
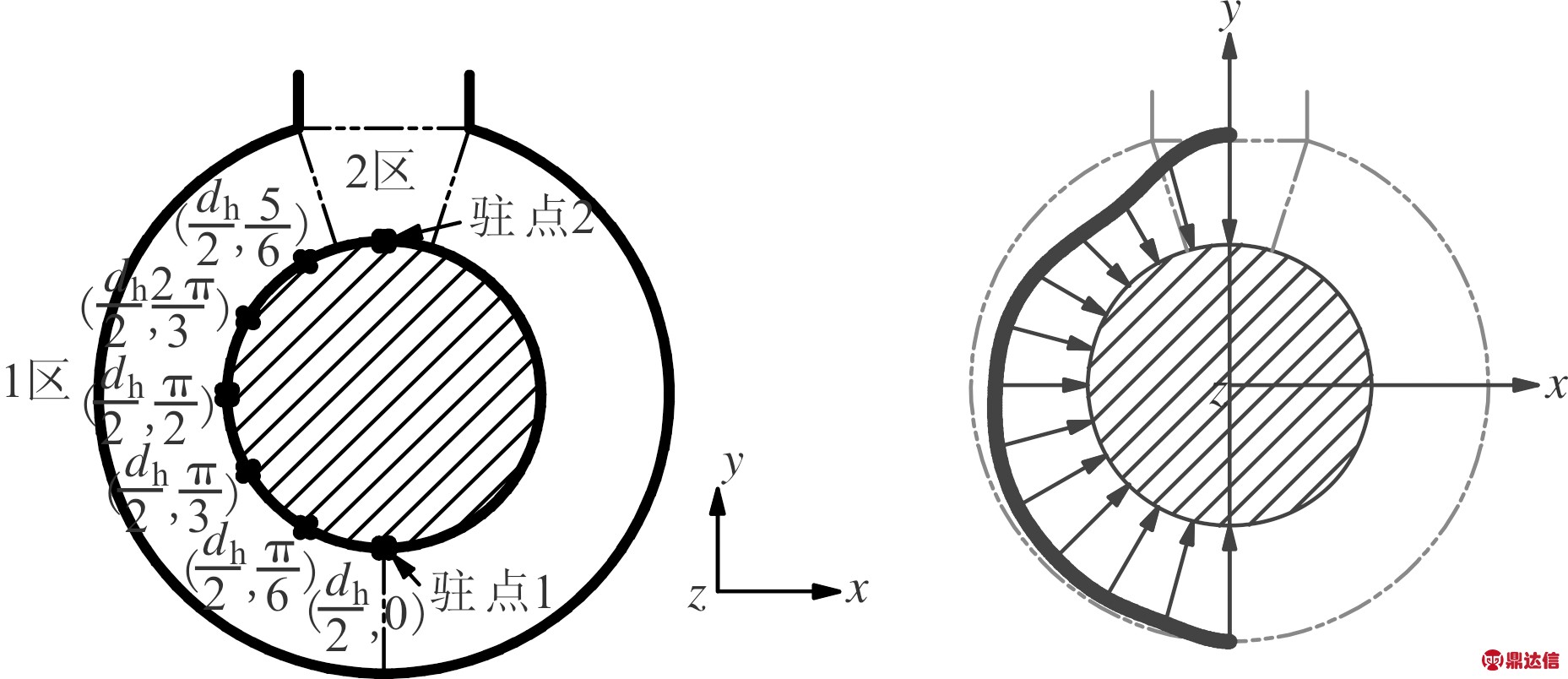
(a)测压点及驻点位置 (b)阀芯台肩径向压力分布
图14 阀芯台肩测压点驻点位置及径向压力分布
由上文知沉割槽处阀芯台肩在关键点上的压力从0到5π/6处逐渐下降,如图14a中的1区,且在0位置,因流速接近为零,故压力达到最大,为驻点。但是,阀芯台肩正对出口处的压力因对流和流速方向变化会产生驻点2,故此位置的压力也会急剧增加到最大值。图14b表示入口流量为40 L/min,出口压力为5 MPa,0.5 mm开口的仿真结果的压力分布趋势。因阀腔结构关于X=0对称,故X轴方向的压力对称分布,即径向压力不平衡主要分布在Y轴方向。
将各位置压力值沿Y轴方向投影的代数和Δpy与此情况下径向压力最大值pmax的比值作为衡量压力沿Y轴分布的不均匀度ε,计算公式如下

(9)
式中:ε=0,表示压力沿Y轴径向力平衡。在图14b的仿真条件下,根据式(7)计算可得ε=0.13,正值表示压力合成沿Y轴正方向。
5.2 沉割槽外壁轮廓优化及分析
由式(6)知,沉割槽处阀芯台肩上的压力分布与沉割槽截尺寸有关,当沉割槽宽度L1固定,假设关键点压力pθ相等,可反推出任意位置沉割槽深度eθ的变化方程。并得出无径向压力不均匀沉割槽壁面理论轮廓的极径r表达式

(10)
取原同心圆环与无径向压力不均匀的理论轮廓轨迹所对应的阀腔体积相等,且活塞直径相同,当入口流量为40 L/min时,根据下式确定0位置的最小深度e0

(11)
根据式(11)可得e0=2.89 mm。无径向压力不均理论轮廓如图15a所示,这种阿基米德螺线轮廓加工困难,故尝试采用偏心圆进行轮廓逼近,如图15b,沉割槽(偏心圆)内径19 mm,偏心3.5 mm。
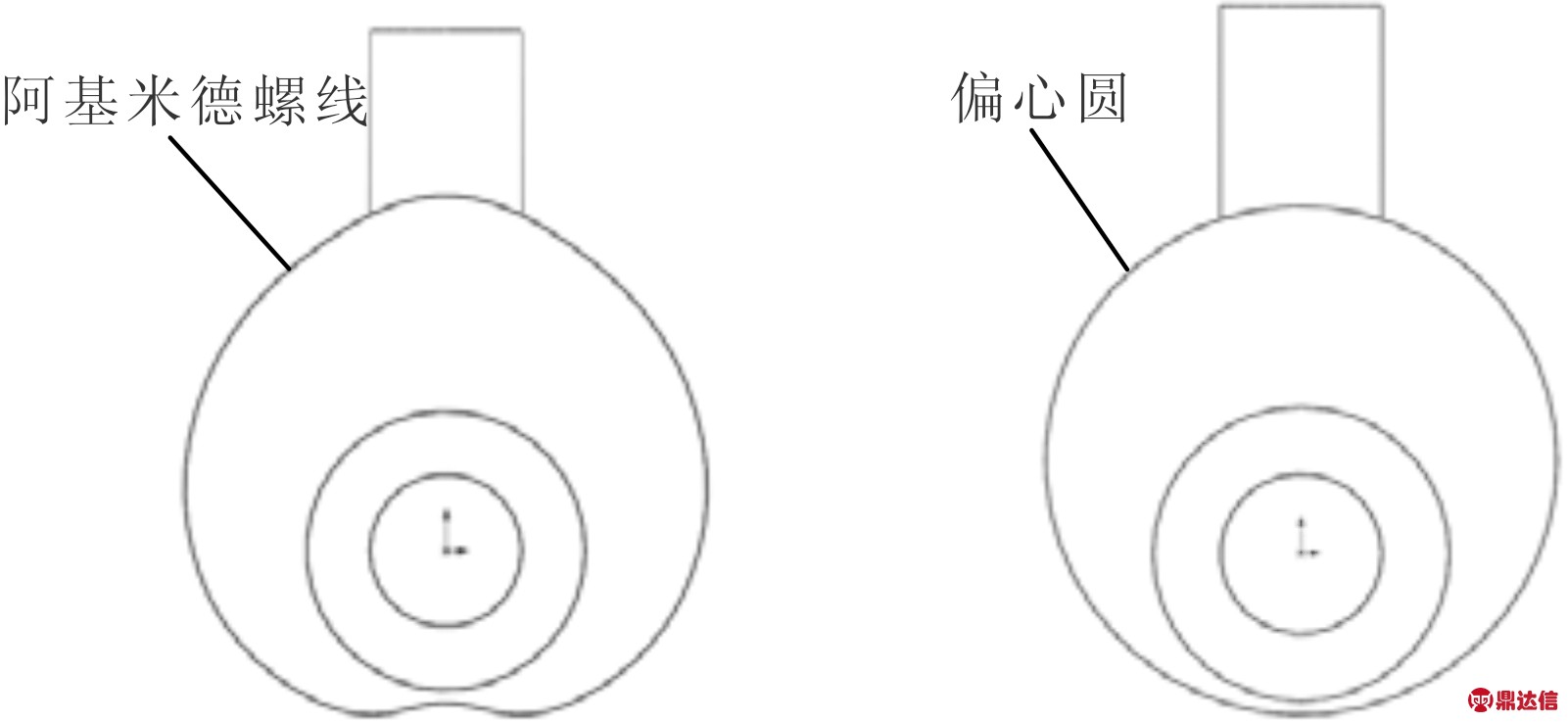
(a)A沉割槽 (b)B沉割槽
图15 两种沉割槽的轮廓
将偏心圆模型进行流体动力学仿真,在出口压力为5 MPa、入口流量分别为40 L/min和60 L/min、开口0.5 mm情况下得到压力分布曲线如图16所示。
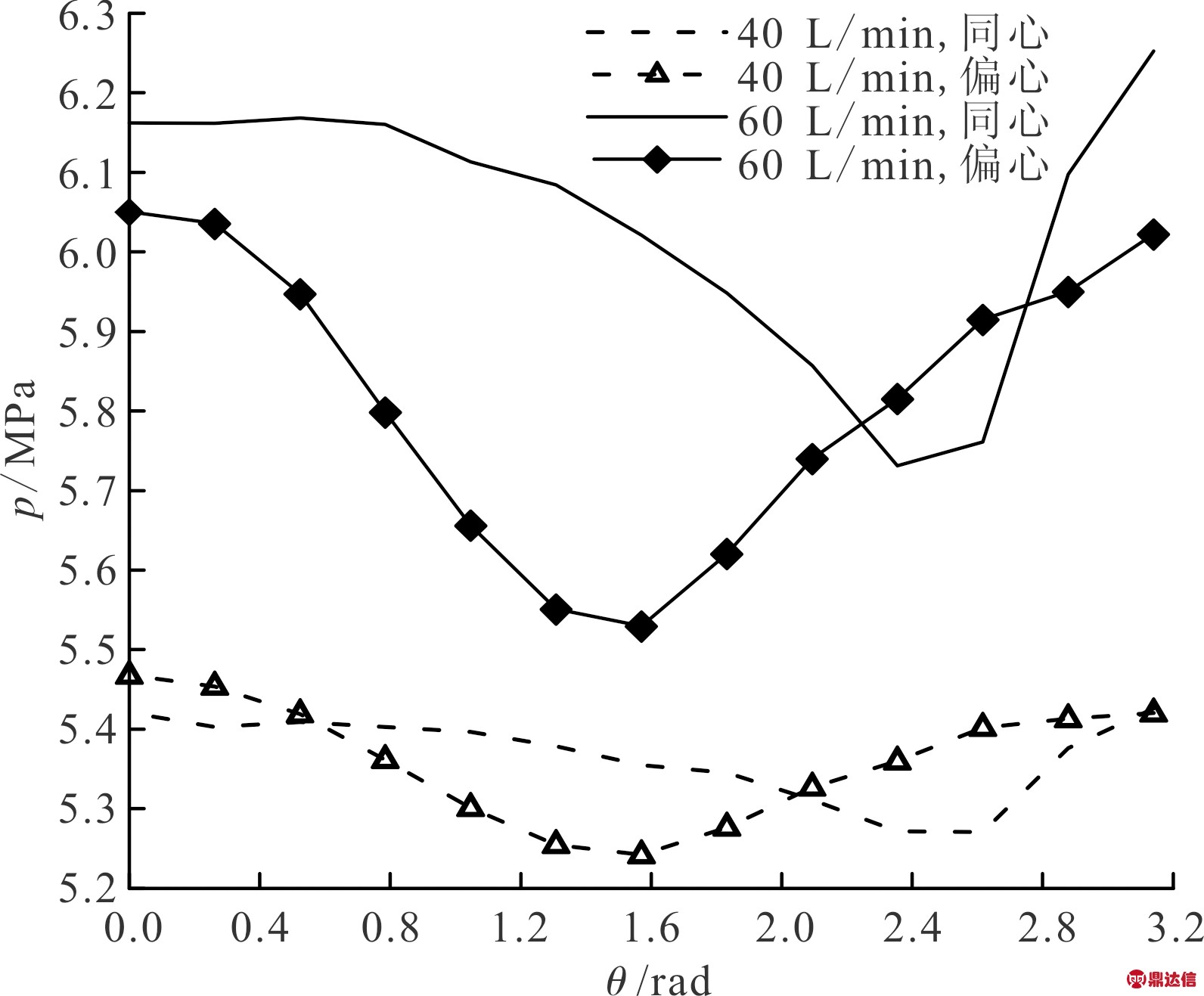
图16 同心和偏心沉割槽结构阀芯上压力分布曲线
图16中偏心形式沉割槽内的阀芯表面压力分布近似关于Y=0对称,将4组曲线对应的压力值代入式(7)中,得到不均匀度ε如表1所示。显然,偏心沉割槽内的阀芯台肩上压力不均匀度在40 L/min和60 L/min情况下,相对同心形式分别提高了64%和87%,故径向卡紧力亦相应减小。且偏心结构并未改变阀芯凸肩与阀体配合长度,故泄漏量不会因沉割槽结构变化增加;同时,阀芯凸肩尺寸未变,流经阀口产生的压力损失也不会改变。
表1 同心和偏心沉割槽处阀芯台肩的压力不均匀度
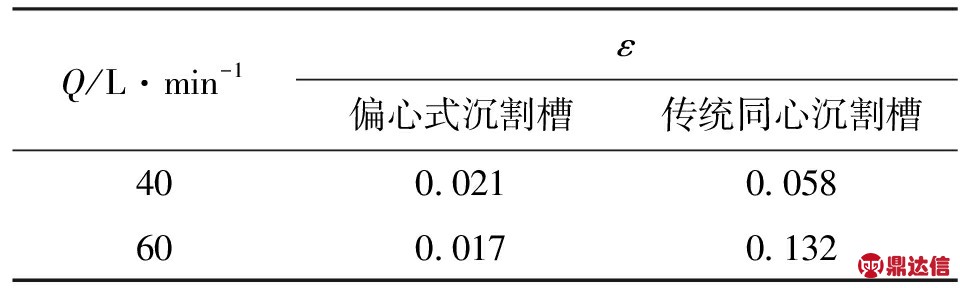
6 结 论
(1)运用流体仿真软件对出口处沉割槽内阀芯台肩上的压力分布进行分析,研究了径向压力分布不均匀程度的影响因素,并通过解析和实验的方法进行验证;
(2)出口沉割槽处阀芯台肩上的径向压力值随压力点位置靠近出口呈平方关系下降;且压力不均分布会产生径向卡紧力,卡紧力值与流量的平方呈正比;沉割槽深度越浅,卡紧力越大。
(3)理论和仿真分析结果表明,在沉割槽内外壁直径相同的情况下,采用偏心形式可以有效的降低沉割槽处阀芯台肩上的压力分布不均匀度,为减小阀芯卡紧力提供了新型阀腔结构的设计思路。