摘要:为了研究飞秒激光对不锈钢材料的加工工艺,采用基于飞秒激光材料烧蚀的微细加工方法,深入研究了飞秒激光高效高质量微细加工不锈钢材料的工艺条件与参量优化,并应用于微型不锈钢悬臂梁的制作。分析了激光能量密度、激光扫描速度、重复扫描次数对加工形貌和蚀除速率的影响,制作出了高质量的微米量级的不锈钢微型悬臂梁。结果表明,飞秒激光微细加工是一种极具前途与极具柔性的微机电系统器件加工手段。
关键词:激光技术;飞秒激光;微加工;微型悬臂梁;参量优化
引 言
微型悬臂梁以其结构相对简单、应用广泛与高性能的特点成为了一种典型的微型传感与激励器件,在微机电系统(micro-electro-mechanical systems,MEMS)和微传感系统中被广泛使用。在化学气体探测分析[1]、生化探测[2-4]以及其它一些精密分析测量领域[5]正受到越来越多的关注。更小尺寸的微悬臂梁在灵敏度方面显露出了一定的优势[6],因此,微加工手段与加工工艺对提高微悬臂梁的性能有重要意义。目前,制备微型悬臂梁大多以硅基材料或聚合物材料为主,而金属微型悬臂梁因其优良的导电性与机械、力学性能,在许多应用中会显示出更大的优越性[7-8]。加工金属微悬臂梁的常用方法有光刻法,湿法、干法蚀刻,LIGA法(一种基于X射线光刻的MEMS加工技术)[9]以及微金属注射成型法[7]。前3种方法一般只能进行2维加工,后两种方法虽然可以进行3维加工,但工艺相对较复杂并且柔性较差。
近几年,飞秒激光作为一种新的微加工手段越来越多地引起人们的关注。飞秒激光具有很高的峰值功率和功率密度,极短的作用时间及非线性吸收等优点。利用其与材料作用过程中的非线性吸收特性及空间高斯光束的的特点,可以使烧蚀作用区域极小,甚至达到超衍射加工效果。由于激光作用时间极短,甚至短于材料中电子-晶格弛豫的特征时间(几个皮秒),使因热传导作用影响的热效应牵涉的范围减小,材料熔化、液相流动以及材料再凝结等过程的影响被大大减小甚至可以忽略,使加工表面更为平整和光滑,提高了微加工过程的精确度和可控性。关于飞秒激光与金属材料相互作用的理论和实验研究已有研究者进行了大量的研究[10-15],并试图加工各种微型器件。作者将采用飞秒激光微加工方法在不锈钢薄片上直接制备微型悬臂梁结构,着重进行工艺条件与参量的优化。
1 实验材料与方法
实验中选取了两种尺寸的不锈钢试样:30μm厚的不锈钢薄片和2mm厚的不锈钢块状试样。采用2mm厚的块状试样进行飞秒激光烧蚀不锈钢材料的参量试验与优化,选用30μm厚的薄片试样进行微悬臂梁的制作。激光加工之前,对试样进行预磨、抛光和超声波清洗处理。
实验装置如图1所示,飞秒激光显微加工装置由飞秒激光系统、光学传输及控制系统与3维精密数控工作台3部分组成,实验在大气环境下中进行。飞秒激光器输出光束中心波长800nm,输出最大激光能量2mJ,脉冲宽度50fs,重复频率1kHz。激光束经过显微物镜聚焦垂直入射到加工试样上表面,实验选用的两种显微物镜L1,L2的放大倍数/数值孔径分别为10×/0.25和20×/0.5,聚焦光斑直径通过CCD测得分别为4μm和2μm。激光能量通过半波片与格兰棱镜的组合在0mJ~2mJ之间调节,激光进入显微镜前通过一个圆形光阑去除杂散光提高光束质量。试样固定在一个高精度的3维数控工作台上,定位精度为300nm,步长为30nm,该3维平台可准确地控制样品移动速度并且可以按照设定的图案和尺寸进行加工。
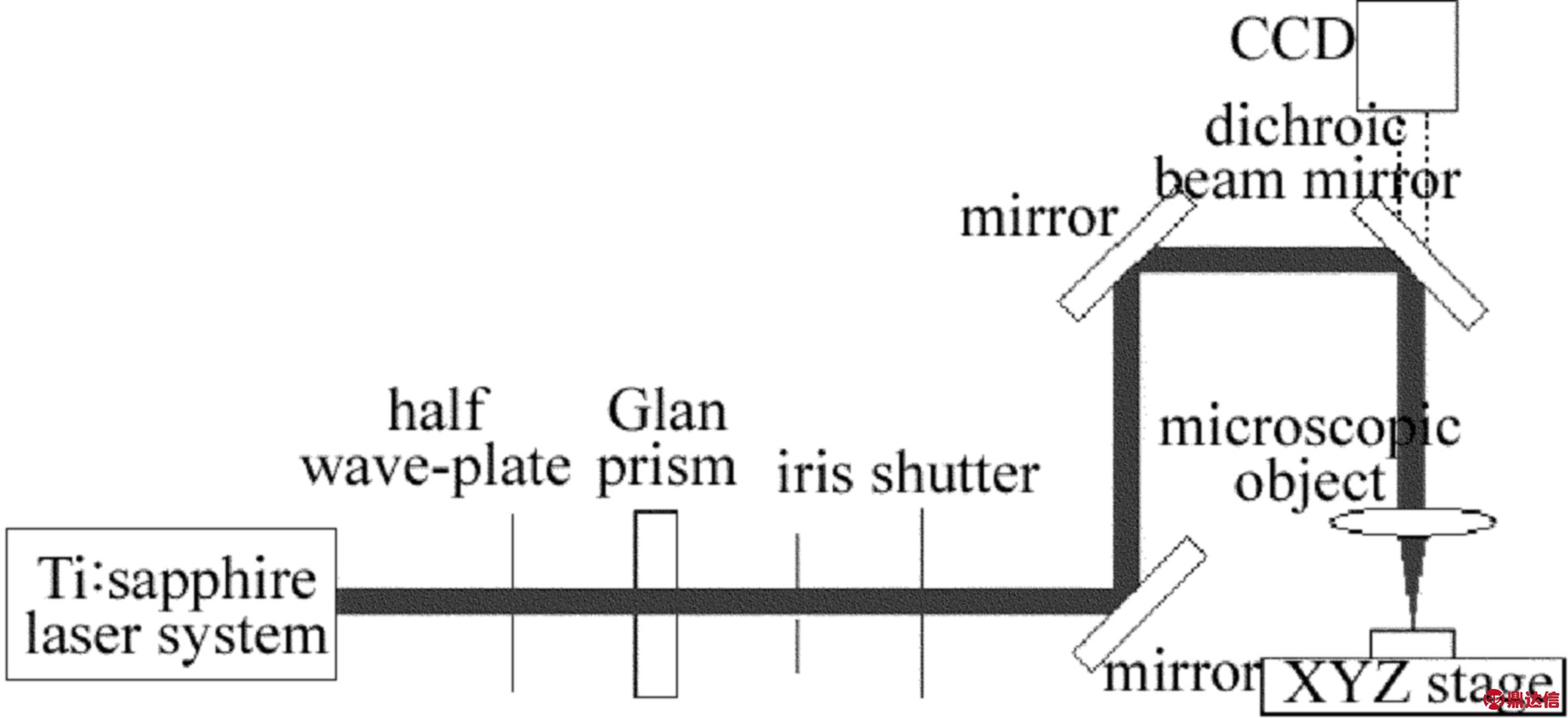
Fig.1 Schematic diagram of femtosecond laser micromachining
通过与显微目镜相连的CCD实时观测飞秒激光加工的过程,并拍照记录;通过带有刻度的金相显微镜测量缝宽和缝深;采用Sirion200型场发射扫描电镜对加工后的试样进行微观形貌分析。
2 实验结果与讨论
2.1 切割缝宽与加工参量的关系
飞秒激光材料加工中,材料的烧蚀阈值是一个很重要的参量。MANNION等人曾采用脉宽150fs、重频100Hz和中心波长725nm的飞秒激光对不锈钢材料进行了烧蚀实验,测得单脉冲烧蚀阈值Fth(1)≈(0.21±0.02)J/cm2,100个激光脉冲作用下的烧蚀阈值Fth(100)≈(0.13±0.01)J/cm2[10],实验中测得的阈值结果与其大致相符[15]。
参量优化实验中,实验过程与结果通过与光学显微镜相连的CCD拍照记录。兼顾加工效率与加工质量的前提下,选取激光能量密度从25J/cm2(100倍单脉冲烧蚀阈值)到400J/cm2(1700倍单脉冲烧蚀阈值);扫描速率从50μm/s到500μm/s;重复扫描次数1~4。
采用30μm厚的薄片试样进行切割实验的结果如图2a所示。每行的3条切缝对应的激光能量密度和扫描速度相同,重复扫描次数从左到右依次为1,2,4遍。光学照片清晰地反映出,随着激光能量密度和扫描速度的变化,割缝质量的变化。利用带有刻度的金相显微镜读取缝宽,得到缝宽与激光能量密度和扫描速度之间的变化关系,如图2b所示。5个能量密度下,缝宽都伴随扫描速度的提高而减小,但扫描速度对缝宽的影响不大,图中任一能量密度处,最高、最低扫描速度对应的缝宽差在3μm左右;在加工能量密度超过160J/cm2的情况下,当扫描速率减小到100μm/s时,缝宽接近一极限值,继续减小扫描速度,缝宽的变化不明显。
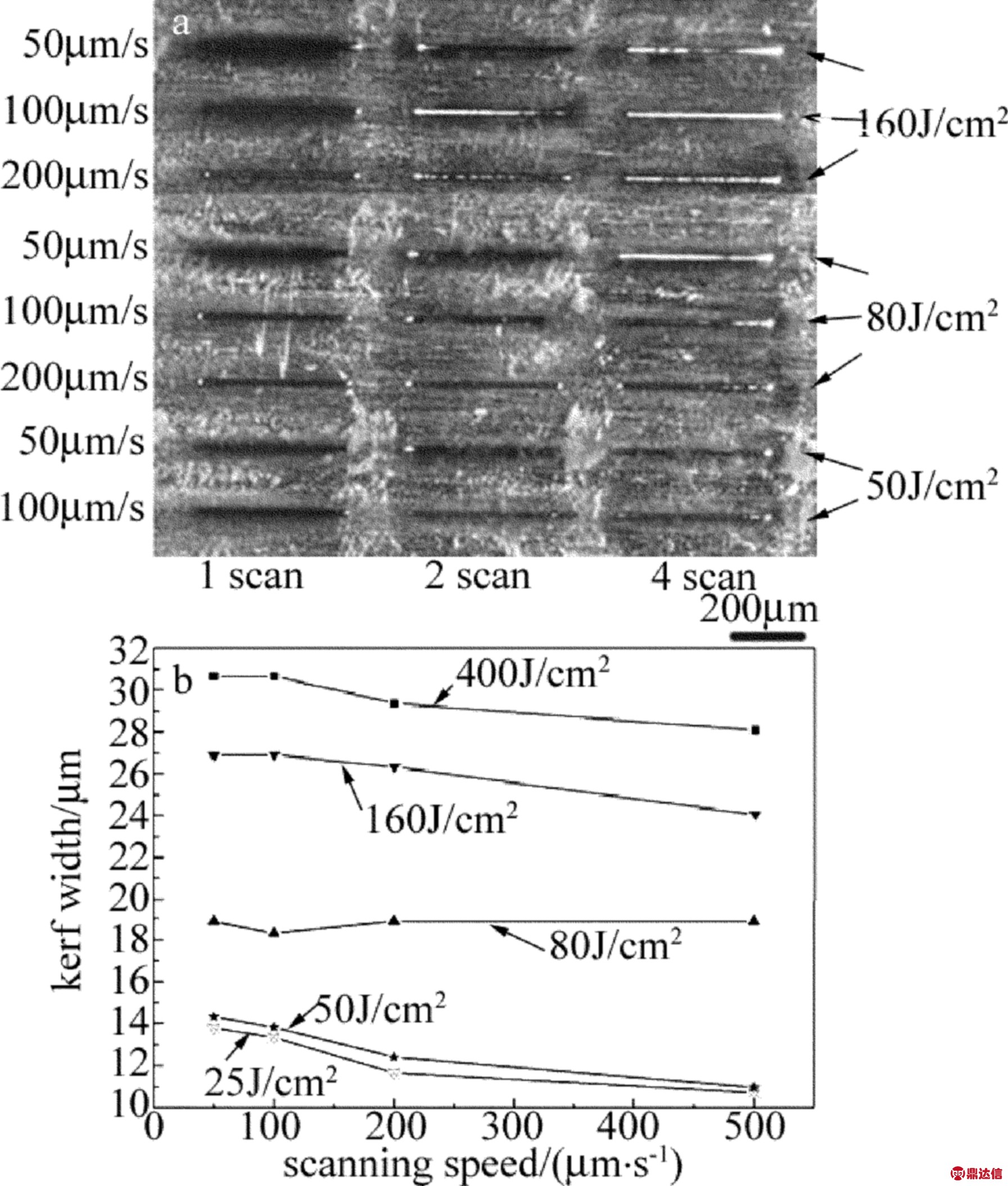
Fig.2 a—microscopic images of the femtosecond laser cutting b—relationship of cutting width and scanning speed
从图2b中还可以看出,在一定的扫描速度下,缝宽随激光能量密度的变化不是简单的线性关系。能量密度从50J/cm2增加到80J/cm2,缝宽变化在5μm左右;能量密度从80J/cm2增加到160J/cm2,缝宽变化在7μm左右;能量密度从160J/cm2增加到400J/cm2,缝宽变化在4μm左右。由此可知,缝宽与激光能量密度的关系不是线性的,而是随着激光能量密度的提高,缝宽增加的趋势越来越缓。根据以上实验分析:缝宽随扫描速度的提高而缓慢减小;随激光能量密度的提高而显著变大,上升的趋势随能量的提高而趋于平缓。由此可知,缝宽主要受限于激光能量密度。要得到尺寸更精细的悬臂梁结构,选取较小的激光能量密度是关键。
图3是相同能量密度(F=50J/cm2)在4种扫描速度条件下,重复扫描次数分别为1,2,4遍时对应的刻蚀形貌,实验材料为2mm厚的不锈钢块状试样。从图上可以看出,改变重复扫描次数对试样表面的刻蚀形貌改变不大,缝宽的变化不明显;随着扫描速度的提高,割缝的边缘愈加平滑,缝宽也逐渐变窄,激光刻蚀造成的污染也显著减少,但是激光刻蚀的深度也明显减小。考虑了加工参量对缝宽和加工形貌的影响后,不同加工参量对应的蚀除速率也是激光加工中需要研究的问题。
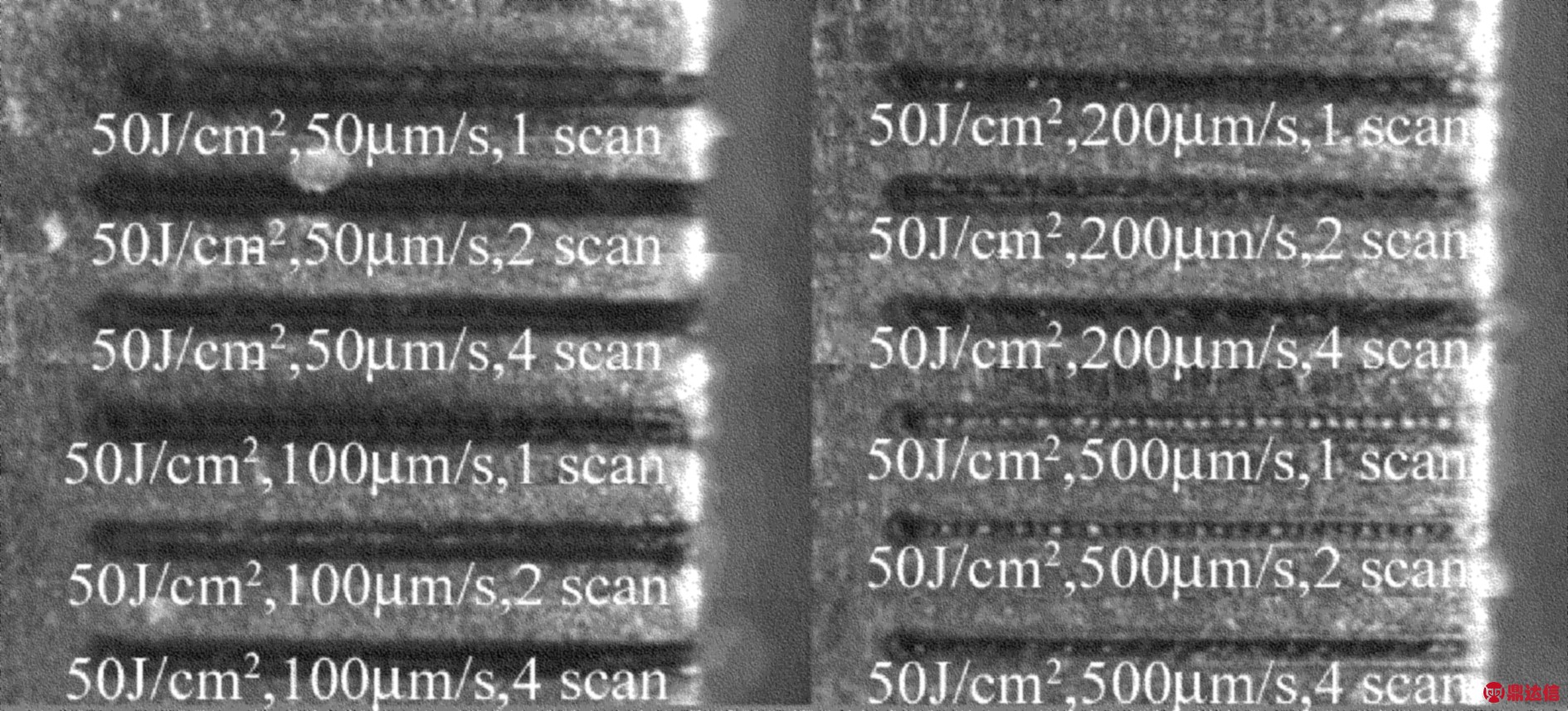
Fig.3 Cutting results with an energy fluent of 50J/cm2,scanning speed of 50μm/s~500μm/s and scanning repetition of 1~4
2.2 蚀除速率与加工参量的关系
实验中用激光一遍蚀除材料的深度来表示激光蚀除速率[16],以表征切割加工的速度。实验参量范围选取同于分析缝宽的实验。
蚀除速率与激光能量密度的关系如图4所示。在4种扫描速度下,蚀除速率都随激光能量密度的增大而提高,但蚀除速率的提高随能量密度的增大会出现饱和现象。扫描速率500μm/s条件下,激光能量密度由25J/cm2提高到160J/cm2,材料蚀除速率随之提升了7μm/scan;继续提高激光能量密度至400J/cm2,蚀除速率只提升了2μm/scan。扫描速率200μm/s和100μm/s条件下,蚀除速率也是在激光能量密度约150J/cm2时达到一个近饱和值。继续减小扫描速率至50μm/s时,蚀除速率在激光能量密度达到约75J/cm2后增加趋势减缓,逐渐进入饱和状态。由此可知,扫描速度越慢,蚀除速率可以在较低的能量密度条件下达到饱和状态。因此,激光加工中过分提高激光能量密度来提升蚀除速率是不可取的,过高的激光能量密度不仅会影响材料表面的加工形貌,降低加工的精度,而且对提高蚀除速率贡献不大。正确选择激光能量密度的原则应该是:入射激光能量密度值应该选择在蚀除速率进入饱和状态值附近。
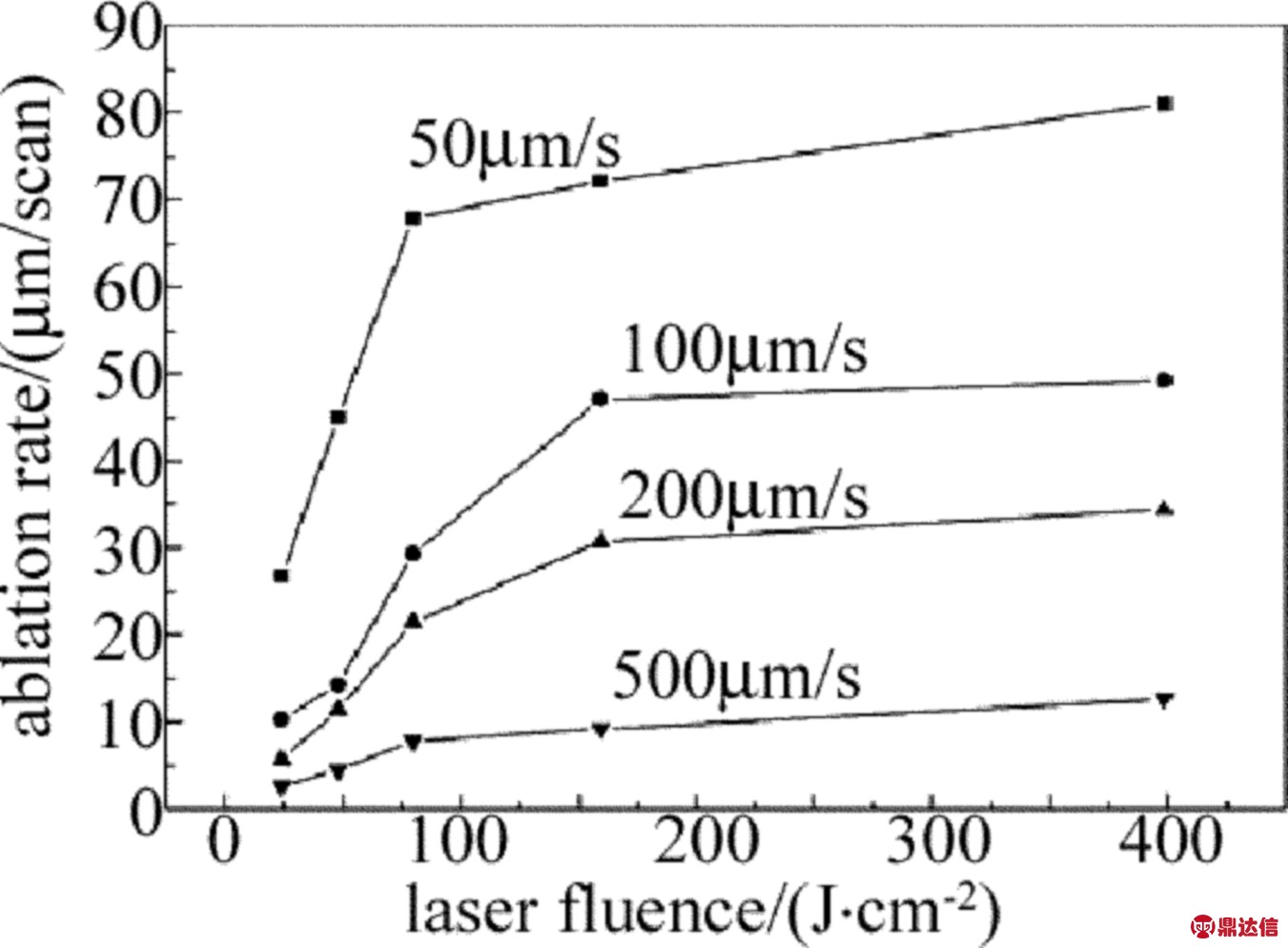
Fig.4 The relationship of laser fluence and ablation depth
2.3 工艺优化与微型悬臂梁制备
选择合适的加工参量组合是高质量微悬臂梁加工的关键:(1)高能量密度能带来高蚀除速率,但是会牺牲加工质量,例如:切割缝宽较大,加工区域污染较多;(2)高扫描速度能保证窄缝宽,但是会降低蚀除速率,并且当扫描速度过高时,加工平台步进电机加减速的影响会比较明显;(3)重复扫描次数是与其它加工参量相关的,在切穿加工试样后适当的增加若干遍激光扫描,通常对切割边缘的质量有提升作用。
实验加工的悬臂梁传感器设计为不锈钢材料微腐蚀疲劳测试的样品,其结构尺寸如图5所示,梁厚30μm、宽30μm、长50μm,距梁根部10μm处有3μm~5μm宽的应力槽。实验选用的不锈钢薄片的厚度为30μm,所以在厚度方向不需要加工。根据以上对加工参量的分析,实验中选取了两组典型的加工参量进行了实验,加工参量如表1所示。采用10×/0.25的聚焦物镜以满足聚焦焦深的需要,和2mm的较小光阑孔径来消除杂散光的影响。
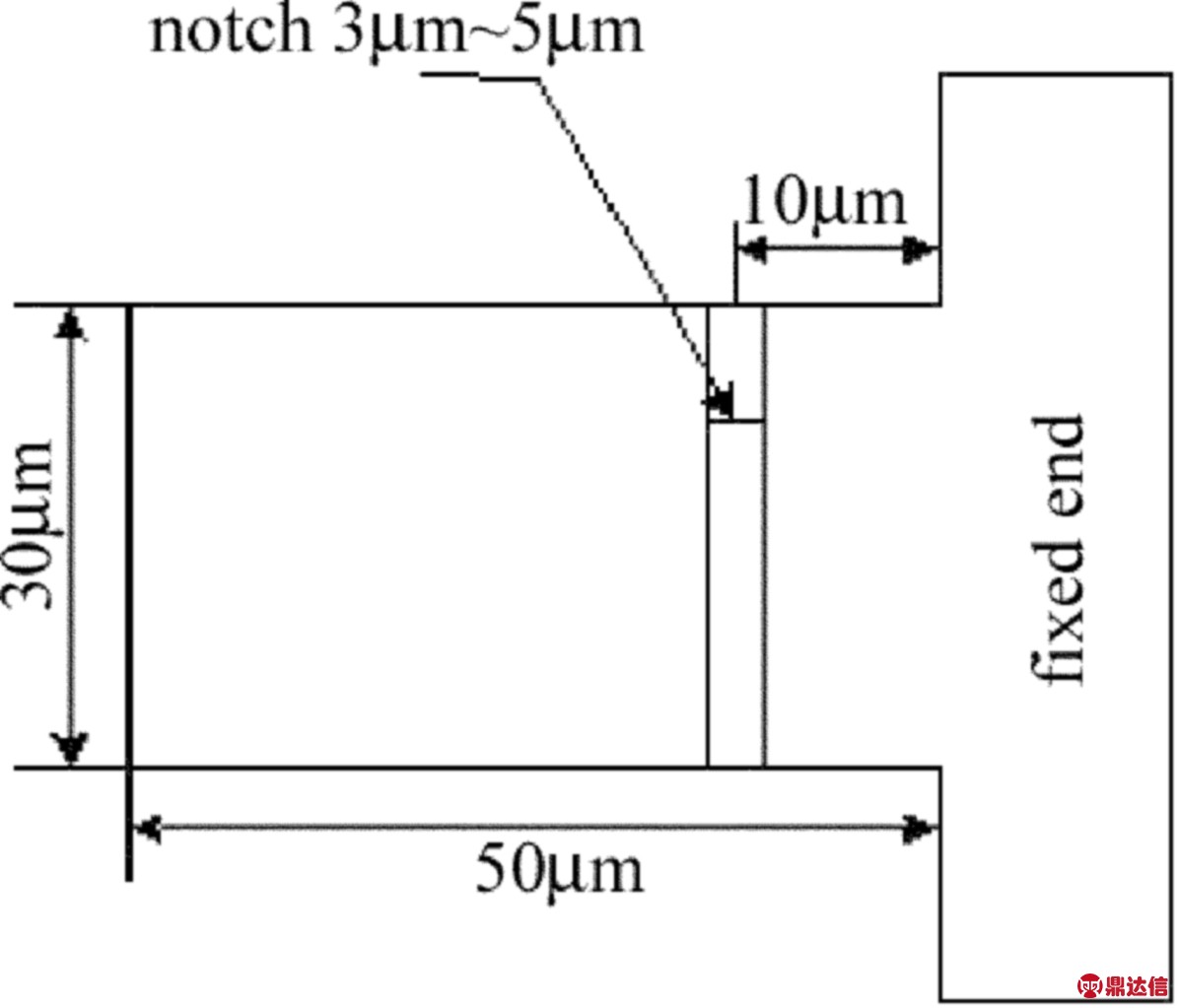
Fig.5 Schematic diagram of the designed microcantilever
Table 1 Processing parameters of microcantilever

微型悬臂梁试样1# 的加工中选用了高能量密度和高扫描速度的参量组合。扫描速率200μm/s条件下,蚀除速率进入饱和状态时相应的激光能量密度为150J/cm2,实验采用的能量密度800J/cm2远高于此值。另外,试样1#采用非常低的激光能量密度来保证应力槽的宽度要求(3μm~5μm)。实验加工的微悬臂梁如图6a所示,过高的激光能量密度导致了缝宽变大,从而严重影响了悬臂梁的尺寸精度和形状,并且锥度较大,应力槽的形貌也不理想。
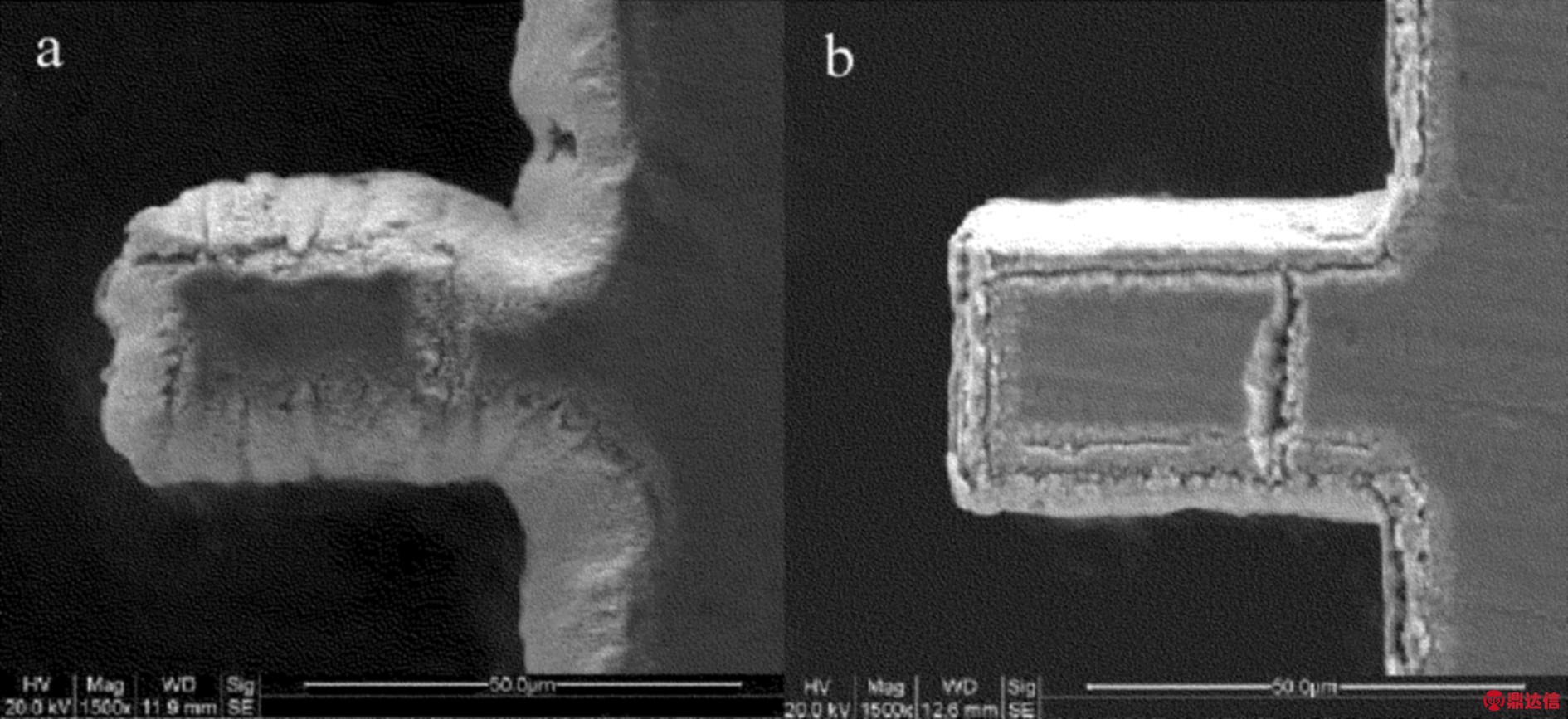
Fig.6 SEM images of microcantilever micromachined with
a—F=800J/cm2,v=200μm/s(body);F=3J/cm2,v=70μm/s(stress notch) b—F=100J/cm2,v=50μm/s(body);F=6J/cm2,v=30μm/s(stress notch)
试样2#实验中,加工微悬臂梁基体选用了较低能量密度与低扫描速度的参量组合。扫描速率50μm/s条件下,蚀除速率在入射激光能量密度高于约75J/cm2时进入饱和状态。考虑到蚀除速率的饱和效应,试样2#采用了较低的激光能量密度值100J/cm2。为了克服试样1#中应力槽深度不够的缺陷,在试样1#的参量基础上提高了激光能量密度并且降低了扫描速率。实验加工的微悬臂梁如图6b所示,能量密度的降低极大地改善了切割质量,微悬臂梁的形状尺寸和加工要求匹配较好,并且锥度较小。由于降低了激光扫描速率,微悬臂梁拐角处由于步进电机加、减速引起的加工缺陷被极大改善,应力槽的深度也满足需要。理论上,在相同的扫描速度下,采用更低的能量密度可能可以得到更好的加工质量,但是能量密度过低会导致蚀除速率过低,这在实际加工中是需要避免的。
3 结 论
研究了采用脉宽50fs、重复频率1kHz、中心波长800nm的飞秒激光加工不锈钢材料时,各加工参量对加工质量与蚀除速率的影响。研究结果表明,切割缝宽主要取决于激光能量密度的大小,扫描速度和重复扫描次数对缝宽的影响不显著。蚀除速率随激光能量密度的增大会出现饱和现象。扫描速度越慢,蚀除速率就会在较低的能量密度条件下达到饱和状态。此外,高扫描速率下(v>100μm/s),由于步进电机加、减速引起的拐角处加工缺陷较严重,低扫描速率(v≤50μm/s)加工质量得到较好改善。利用优化后的加工参量F=100J/cm2,v=50μm/s(梁体)、F=6J/cm2,v=30μm/s(应力槽),加工出了高质量的微米量级不锈钢悬臂梁。
飞秒激光微加工作为一种新型的微细加工方法,很多方面还处于探索阶段。尝试新材料的加工以及制作具有一定功能的微零件和微系统,将是飞秒激光微加工领域的研究重点之一。