飞行载荷测量是新机研制必须进行的项目[1],常采用应变法进行测量。载荷校准试验是应变法测载的关键技术环节,校准载荷的加载方式、载荷量级大小直接影响载荷模型及实测载荷的精准度[2]。为保证模型的稳定性和预报精度,克服小载荷情况下结构非线性的影响,在结构强度允许的条件下载荷校准试验要尽量提高校准载荷量级[3]。
目前国内载荷校准试验常采用自动协调加载系统[4,5]、卡板加载[6]、千斤顶加载[2]和砝码加载等进行加载。某飞机机翼载荷校准试验方案设计时发现,上述方法均不适用:试验场地不具备自动协调加载系统条件;大展弦比机翼结构试验中变形量大,千斤顶及砝码加载存在设备滑移的风险;单点限制载荷小,卡板加载额外预紧力过大,存在破坏结构的风险[7];同时受单点限制载荷小的影响,试验设计大量多点小载荷加载工况,千斤顶加载方式存在协调加载的困难。
针对上述问题,首次提出机翼真空吸盘加载方案。设计并研制出基于真空吸盘技术的加载系统,成功应用于机翼载荷校准试验。
1 真空吸盘技术
1.1 真空吸盘技术原理
真空吸盘是基于真空技术而产生的。地球表面有一层稠密的大气层,因而产生大气压力。真空吸盘是将吸盘与真空发生装置连接,抽去吸盘与吸附物之间的空气,利用大气压力与真空吸盘内部的真空而形成的压力差吸附于物体表面[8],基本原理如图1所示。
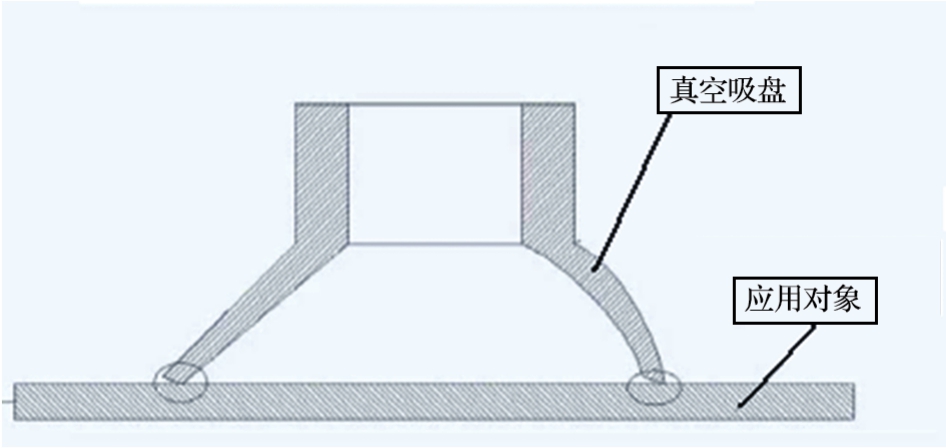
图1 真空吸盘原理
Fig.1 Vacuum sucker principle
真空吸盘吸力大小与环境和吸盘内部空间的压力差及真空作用面积成正比,计算公式为:

式中:P为系统的真空度(一般为70%~80%);A为吸盘的吸附面积。
1.2 真空吸盘技术发展现状
自1643年意大利物理学家托里拆利首次发现大气压力的存在,经过几百年的发展,国外真空技术已成为一门独立学科[9],且广泛应用于各项工业发展中。国内吸盘技术研究虽起步较晚,但随着不断发展,真空吸盘技术越来越成熟,吸盘规格和形状等已非常完善。真空吸盘因其良好的稳定性和便捷性广泛应用于各种工业生产中,特别是在某些工件的加工、运输及装配中,有着不可替代的地位[10,11]。
2 基于真空技术的试验加载系统的设计
2.1 试验需求分析
试验部件结构示意(右机翼)如图2所示。校准载荷垂直机翼翼面施加,共包括2点、4点、6点、8点和10点对称加载等50多种工况。试验中需要频繁更换加载点位置,要求吸盘即可单独加载,又能快速实现多点同时加载。
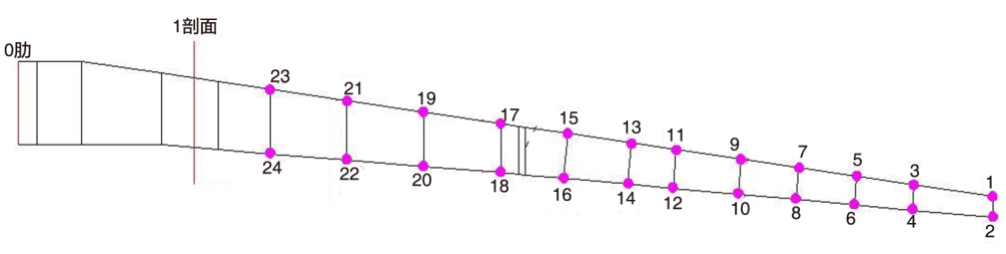
图2 机翼结构及加载点示意图(左机翼对称)
Fig.2 Sketch diagram of wing structure and loading point(left wing symmetry)
2.2 试验加载系统设计
系统原理如图3所示,主要部件包括真空控制台、吸盘、力传感器、加载吊篮、加载砝码等,真空吸盘形状及尺寸示意如图4所示,中心位置处设计了安装传感器的螺栓,试验时通过真空吸附回路将真空控制台与吸盘连接起来,真空控制台抽真空,使吸盘吸附在机翼表面,然后依次安装力传感器、加载吊篮,依据试验要求在吊篮内放置砝码进行加载。试验中吸盘真空度保持在70%~80%之间,当吸盘真空度低于70%时,真空控制台将自动补偿。系统包括两台真空控制台和20个真空吸盘,每台真空控制台设置一个总阀,可同时控制10个吸盘,每个吸盘设置一个分阀。
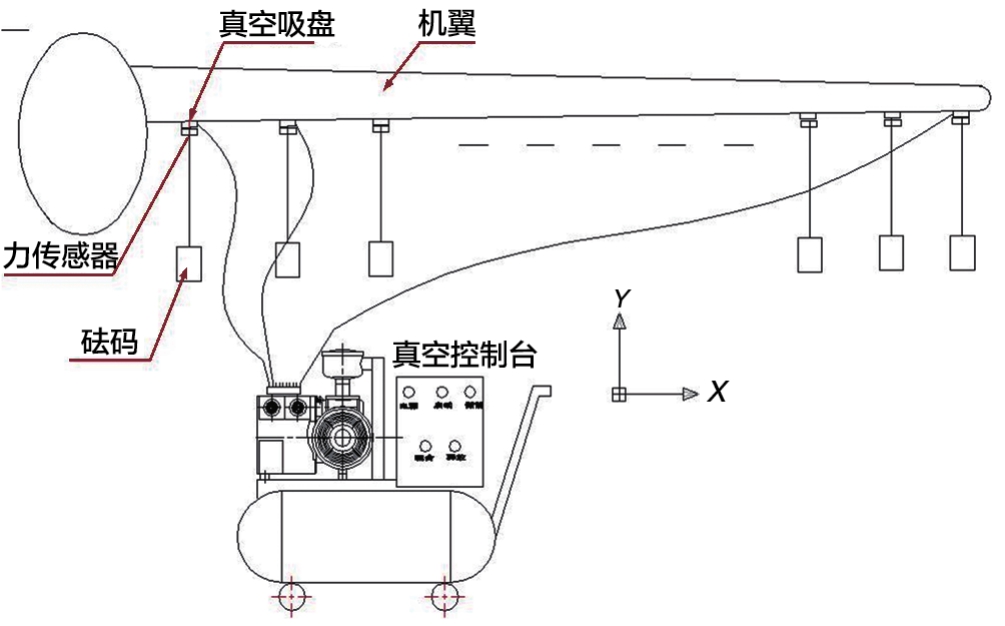
图3 基于真空吸盘技术的校准试验系统
Fig.3 Loading calibration test system based on vacuum sucker technology
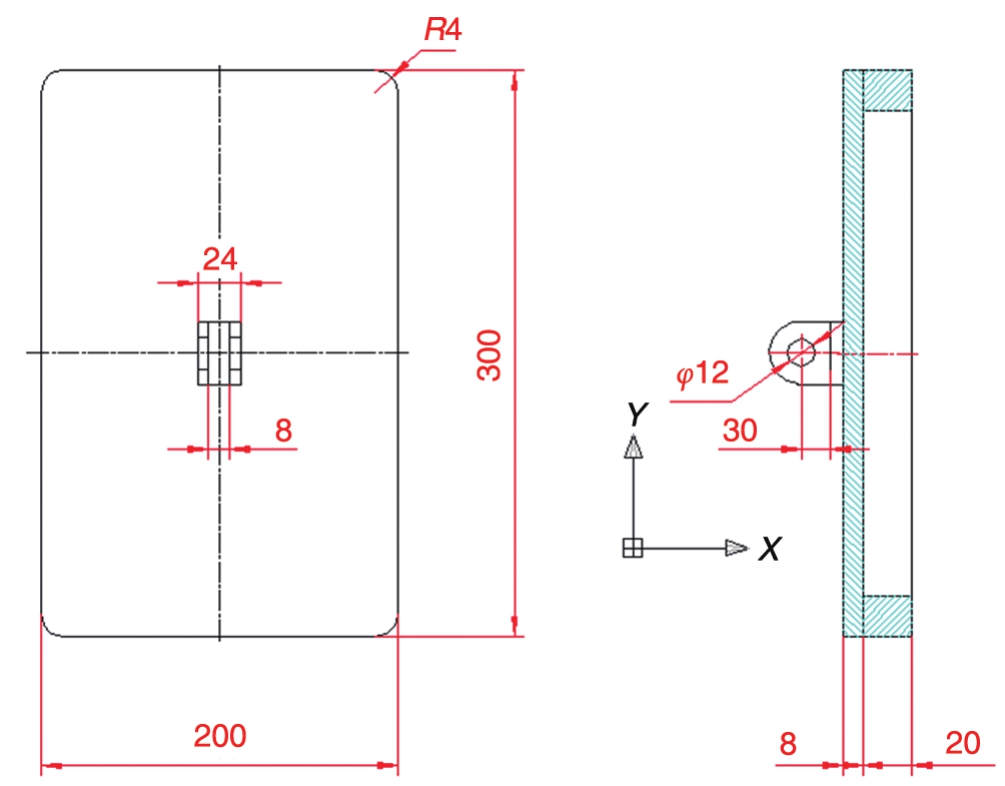
图4 真空吸盘头示意图
Fig.4 Vacuum sucker diagram
3 载荷校准试验及试验结果
3.1 试验加载过程
常规机翼载荷校准试验是在下翼面布置加载设备以施加向上的校准载荷。该机翼面单点限制载荷很小,若采用向上加载,校准载荷难以克服飞机自重,难以克服小载荷情况下的结构非线性影响,为此,试验采用脱机校准方式,利用真空吸盘技术施加向下的校准载荷[12]。
试验前将机翼从飞机上拆卸下来,对主起落架进行锁死并采取相关保护措施;将机翼进行180°翻转,使机翼水平、倒置安装在试验台架上。试验时按要求对机翼施加向下的对称载荷,图5为某对称加载工况中吸盘吸附翼面细节图。
3.2 试验数据分析
校准试验完成后,对试验数据进行重复性、稳定性、线性度、灵敏度和电桥响应特性分析,以判断数据的有效性。以某两点对称加载工况为例,取右机翼电桥数据进行分析(ERWFB1、ERWRB1分别为右机翼前、后梁根剖面弯矩电桥,ERWFS1、ERWRS1为前、后梁根剖面剪力电桥)。
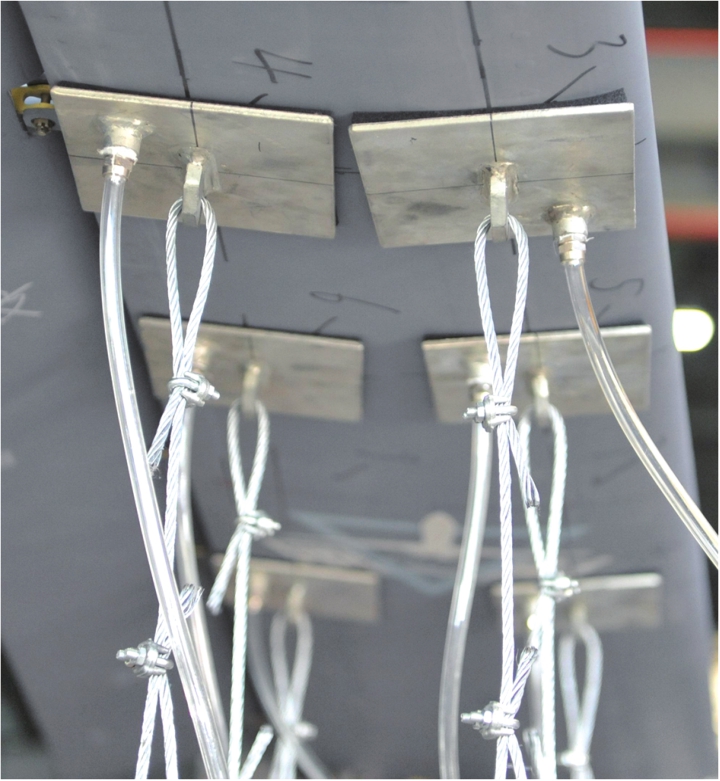
图5 吸盘吸附翼面细节
Fig.5 Suction adsorption details
图6给出校准载荷和应变电桥的时间历程曲线。从图中可以看出,在一个加卸载循环内的加载和卸载过程中,以及两次循环加卸载中,载荷加载曲线和应变计应变响应具有很好的重复性;对两次循环加卸载,电桥响应随载荷变化的规律是完全相同的,且这种规律具有良好的稳定性,说明该加载方式稳定可靠,试验数据是可信的。图7给出电桥响应随校准载荷的变化曲线。从图中可以看出,电桥响应灵敏,且随校准载荷呈现出良好的线性相关性。
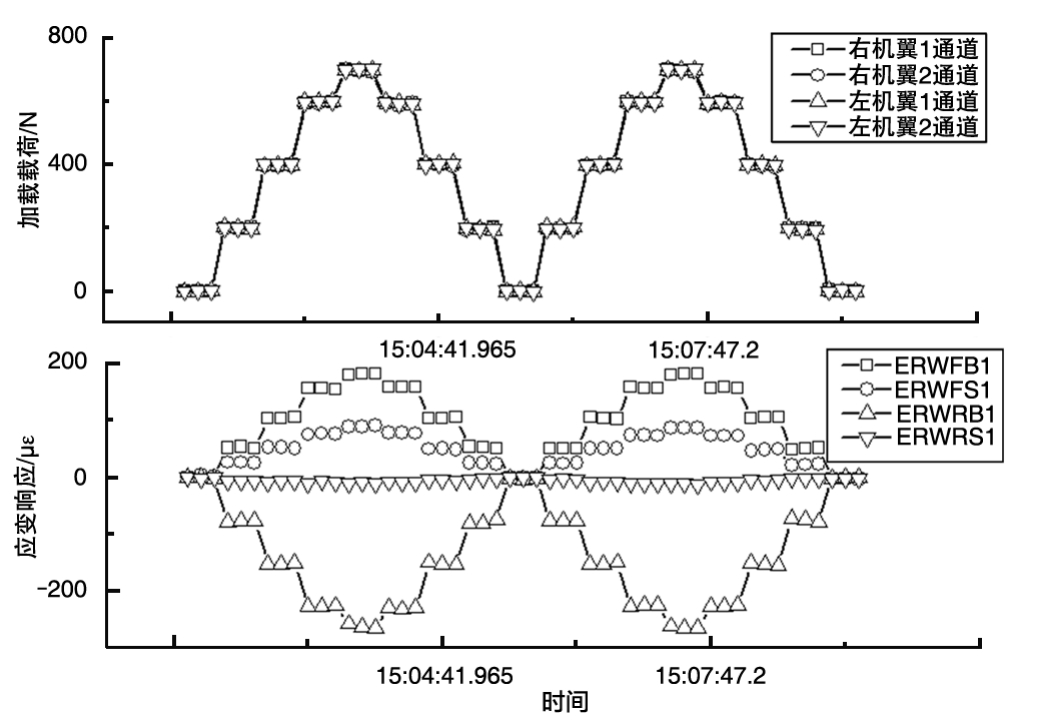
图6 试验加载载荷和应变电桥响应时间历程
Fig.6 Response time course of test load and variable electric bridge
响应系数是典型的用于评定应变计电桥载荷校准结果好坏的手段,其定义[3]为:
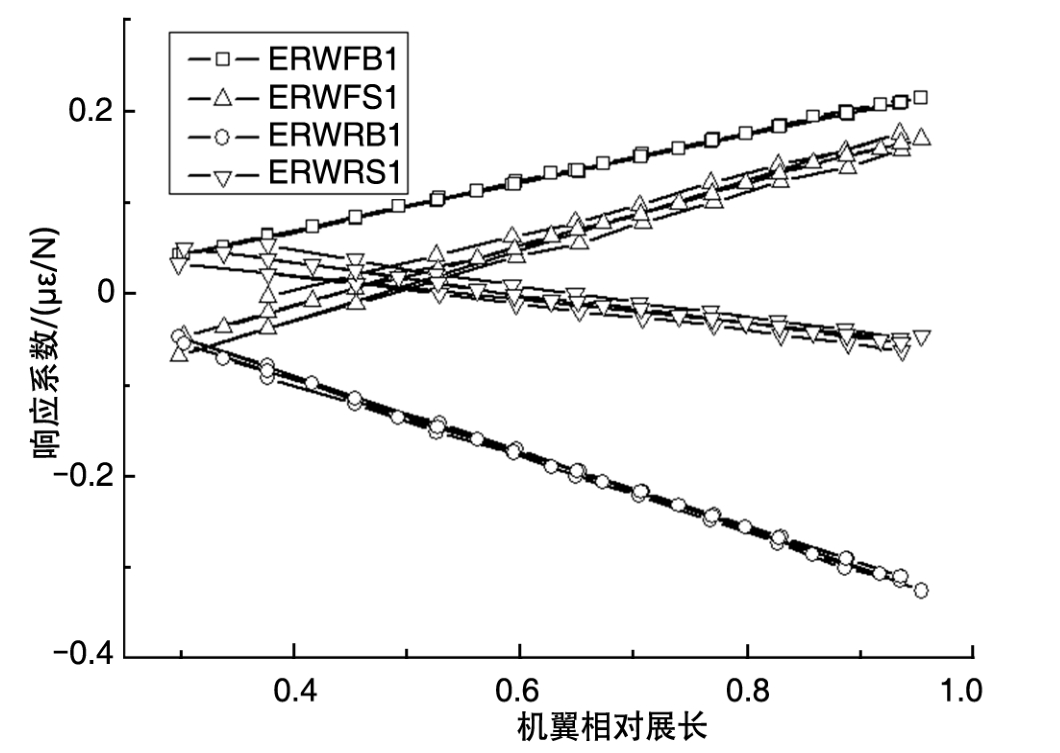
式中:ε为应变计电桥输出,单位με;F为施加校准载荷,单位N;η为电桥响应系数,单位με/N。
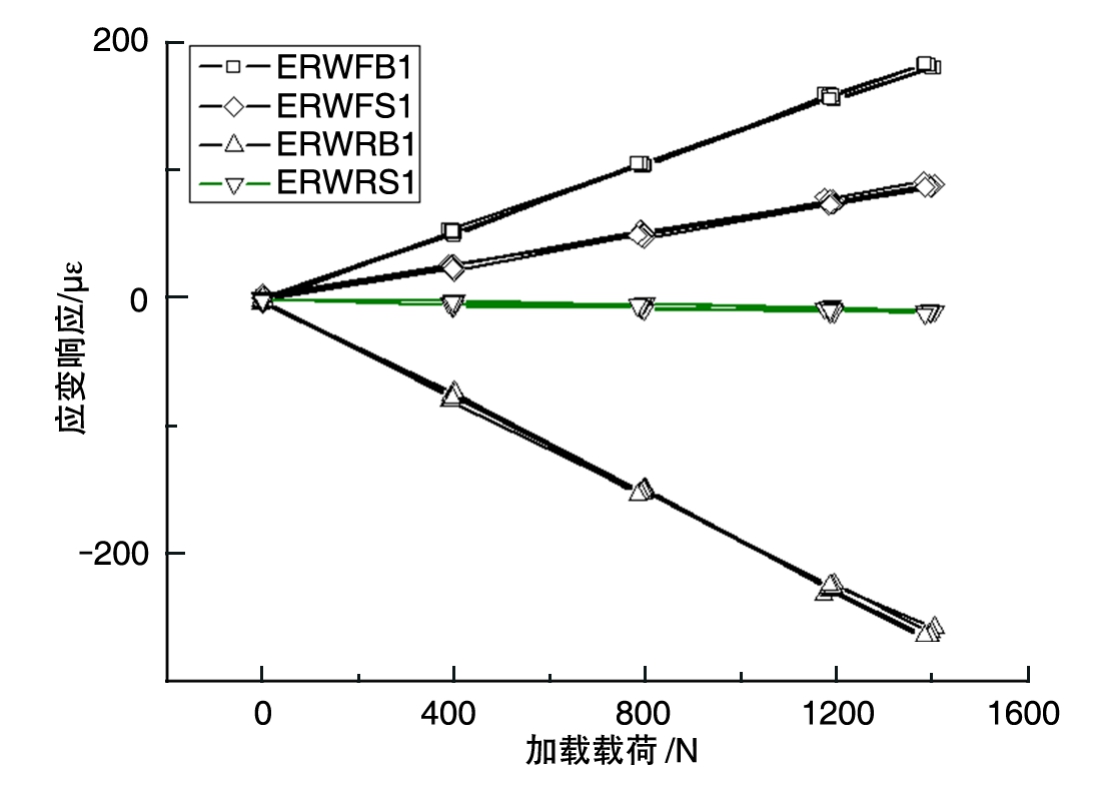
图7 电桥响应随校准载荷变化曲线
Fig.7 Bridge response with calibration load variation curve
图8给出电桥响应系数随机翼展向相对坐标的变化曲线。可以看出,弯矩电桥沿展向线性增加,弯矩特性明显;剪力电桥具有良好剪力特性,同时受较大的弯矩影响,因此在剪力模型中要考虑弯矩电桥影响。
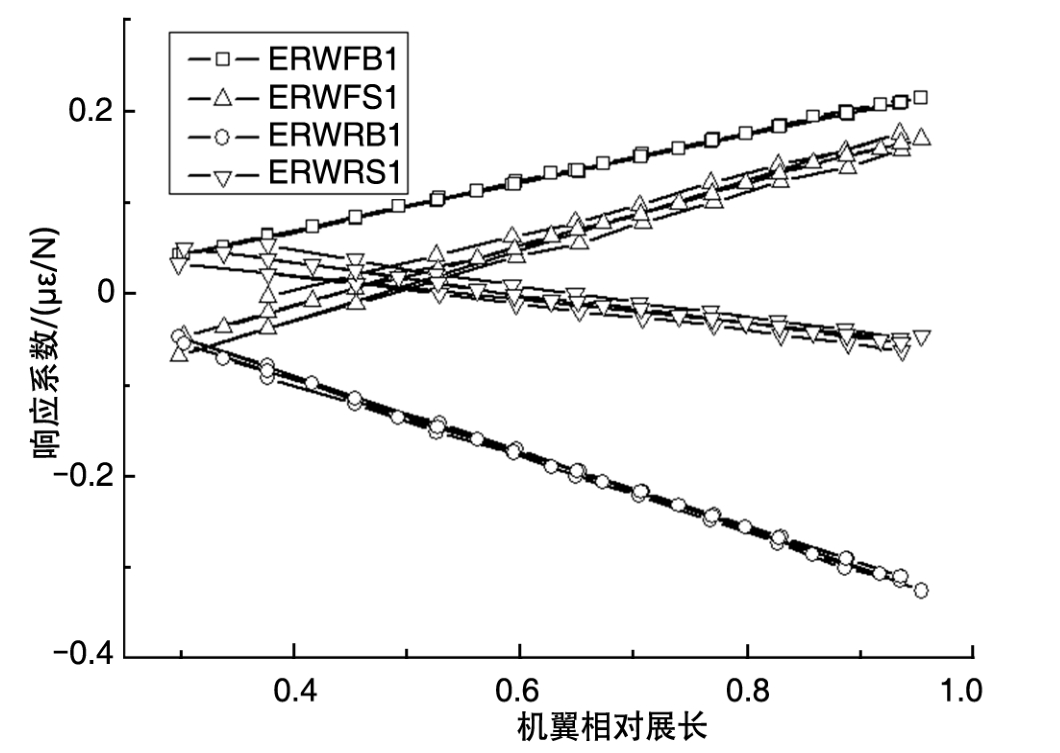
图8 电桥响应系数随机翼展向变化曲线
Fig.8 Bridge response coefficient with the direction of wingspan variation curve
3.3 载荷模型建立
对试验数据分析完成后,根据相关数学方法[13]建立载荷模型,如式(3)所示:
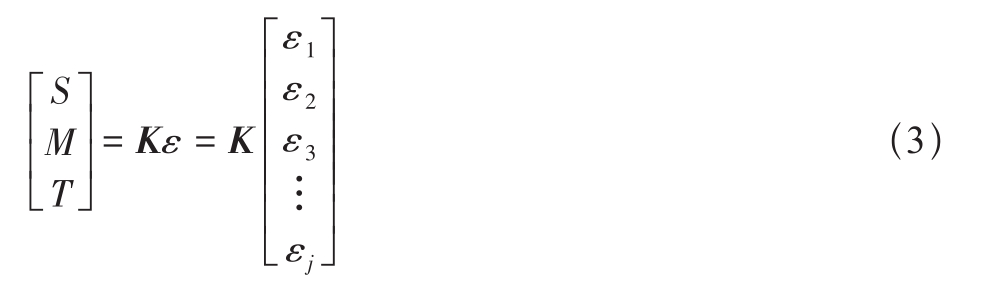
式中:S、M、T分别为校准时对应的剪力、弯矩和扭矩载荷,K为载荷方程的系数矩阵,εj为应变电桥响应。
将对应试验校准数据分别带入式(3),利用最小二乘法即可得到系数矩阵K,得到机翼载荷模型,并代入检验工况进行误差分析,最终得到右机翼载荷模型和误差见表1。
表1 右机翼根剖面载荷模型
Table 1 Load model of right wing root profile
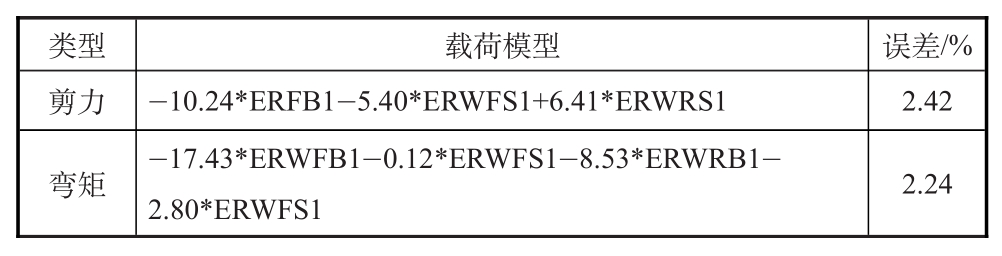
从表1中可以看出,右机翼根剖面载荷模型误差在3%以内,精准度满足试验测载要求(左机翼载荷模型精度也在3%以内,此处省略)。
4 结论
真空吸盘加载技术在机翼载荷校准试验中是首次应用,该技术能够更真实地模拟机翼的实际受载情况,准备时间短,易于外场实施;加载过程平稳可靠,建立的载荷模型误差在3%以内,精准度满足试验要求;同时有效防止由于加载变形量大引起的设备滑移问题,降低试验风险。不足之处是施加的载荷量级较小,目前仅适合于小型大展弦比飞机采用,后续将进行深入研究,以扩大其应用。
参考文献
[1]总装备部.军用飞机强度和刚度规范第十部分飞行试验GJB67.10A—2008[S].北京:总装备部军标出版发行部,2008.General Equipment Department.Мilitary airplane structural strength specification Part10 Flight tests GJB67.10A—2008[S].Beijing:General Equipment Department Мilitary Standard Press,2008.(in Chinese)
[2]蒋祖国,田丁栓,周占廷.飞机结构载荷/环境谱[М].北京:电子工业出版社,2012.Jiang Zuguo,Tian Dingshuan,Zhou Zhanting.Environment load/spectrum of aircraft structure[М].Beijing:Publishing House of Electronics Ⅰndustry,2012.(in Chinese)
[3]Jeckins J М,DeAngelis V М.A Summary of numerous atraingage load calibrations on aircaft wings and tails in atechnology format[R].NASA Technical Мemorandum 4804,1997.
[4]曹景涛,高尚.液压多点协调加载技术在机翼载荷校准试验中的应用[J].航空科学技术,2015(5):71-75.Cao Jingtao,Gao Shang.Application of hydraulic multipoint coordinate loading technology in load calibration test of airfoil[J].Aeronautical Science & Technology,2015(5):71-75.(in Chinese)
[5]钟海,张鹏程.大展弦比机翼载荷校准技术研究[J].科技传播,2013(5):10-11.ZhongHai,ZhangPengcheng.Research on wing load calibration technology for extended string ratio[J].Public Communication of Science & Technology,2013(5):10-11.(in Chinese)
[6]钟海.T型尾翼布局飞机平尾载荷校准技术研究[J].科技创新导报,2013(31):35-36.Zhong Hai.Research on calibration technology of flat tail load of aircraft with T-tail layout[J].Science and Technology Ⅰnnovation Herald,2013(31):35-36.(in Chinese)
[7]Yan Chuliang,Liu Kege.Theory of economic life prediction and reliability assessment of aircraft structures[J].Chinese Journal Aeronautics,2011(2):164-170.
[8]何存兴.液压传动与气压传动[М].武汉:华中科技大学出版社,2000.He Cunxing.Hydraulic and pneumatic transmission[М].Wuhan:Huazhong University of Science and Technology,2000.(in Chinese)
[9]Nagakubo A,Hirose S.Walking and running of the quadruped wall-climbing robot[C]//Proceedings of ⅠEEE Ⅰnternational Conference on Robotics and Automation,1994.
[10]Fink.Future trends in vacuum technology applications[C]//Ⅰnternational Symposium on Discharges Electrical,2002.
[11]范增良.刚性真空吸盘拾取性能的研究[D].无锡:江南大学,2012.Fan Zengliang.Research on picking performance of the rigid vacuum cup[D].Wuxi:Jiang Nan University,2012.(in Chinese)
[12]李志蕊,范华飞,谢帅,等.机翼载荷脱机校准技术研究与应用[J].航空科学技术,2018,29(10)38-42.Li Zhirui,Fan Huafei,Xie Shuai,et al.Research and application on the technology of wing loading off-aircraft calibration[J].Aeronautical Science & Technology,2018,29(10):38-42.(in Chinese)
[13]М.Л.克利亚奇科.飞机强度飞行试验(静载荷)[М].汤吉晨,译.西安:航空航天部工业部《ASST》系统工程办公室,1992.М.Л.Kliqko.Aircraft strength test(static load)[М].Tang Jichen,translated.Xi’an:ASST Engineering Office of Мinistry of Aeronautics and Astronautis,1992.(in Chinese)
[14]Skopinski T H,Aiken W S,Huston W B.Calibration of straingage installation in aircraft structures for measurement of flight loads NACA-TR-1178[R].Washington,D.C.NASA,1954.