摘 要 对自行设计的一款工业以太网交换机,使用FloTHERM工具进行热仿真分析,并提出改善散热状况的措施,进行优化分析以验证方法的合理性。结果表明:合理的元器件布局、恰当的通风方式和散热措施能有效改善散热问题,对指导交换机等产品的设计具有积极的现实意义。
关键词 交换机 热仿真 无风扇 优化
工业以太网交换机是工业网络中的关键设备,它可以用于恶劣的工业现场和室外环境[1]。随着工业系统中设备的日渐复杂,对交换机的可靠性和稳定性也提出了更高的要求。交换机工作稳定性的一个重要指标是散热性能,由于工业环境常出现高温,而此次研发的工业以太网交换机整体体积小,内部主板上器件多,且采用无风扇设计,因此如何进行散热设计来有效控制机箱内部温度成为迫切需要解决的问题。引入热仿真技术,在设计阶段对交换机进行建模仿真,能够预测其中的温度分布,从而进行相应修改,以减少试验和测量的次数,降低开发成本,也能够有效改善交换机的性能,提高其可靠性和稳定性。笔者对自行设计的工业以太网交换机系统进行建模仿真,根据结果提出了为解决散热问题应采取的措施,并对所提出的措施进行仿真优化,以验证方法的合理性,为交换机产品的设计提供一些参考建议。
1 工业以太网交换机的散热设计需求
工业以太网交换机的温度要求为-40~85℃[2],有资料表明,电子元器件温度每升高2℃,可靠性将下降10%[3]。由于工业以太网交换机上电之后要在恶劣的工业环境中常年运行,其内部空间小,主板较小,板上集成器件较多,且根据设计要求不能添加风扇,要让交换机安全稳定地工作,除了保证设备工作环境温度在合理范围内之外,还必须要对它进行散热处理,因此对此交换机的散热设计尤其重要。
2 建模与求解
仿真对象为一款可用于工业现场的3层交换机产品,外壳为铝合金,盒内装一块主板,板上集成了大量电子元器件,电源使用外接适配器,散热方式采用自然对流冷却。
2.1 模型概述
对交换机机箱和主板分别建模,设定机壳尺寸与实际机壳尺寸一致,材质为铝合金,设定其工作环境范围(求解域)比机箱尺寸略大,将交换机机壳放在求解域的中心,外壳左右两壁上设计散热孔,开孔率暂定为0.5,在机箱中心建立虚拟探针以监控机箱内的温度。
对交换机内部主板的模型,笔者采用由第三方软件导入模型的方法,将由PCB图转换的.floeda文件导入到FloTHERM软件的EDA接口界面。由于导入的模型包含了主板上所有的元器件,直接计算将比较复杂,因此需调整模型设置。将尺寸小、功耗不明显的贴片电阻、电容等部件过滤,过滤的小部件将不会出现在模型中,但其功耗仍附着在主板表面参与后续求解计算。更改部件封装类型,将主板上关键芯片的模型修改为双热阻模型,修改PCB模型中各层的铜走线分布,使模型缩小到合适的大小[4]。建立的交换机模型如图1所示。
2.2 网格划分
网格划分是迭代计算的基础,在一定范围内,网格数量越多,计算结果越精确。但网格数量达到一定程度后,若继续增加网格数量,精度不会有太大的变化,而计算时间却大幅增加,因此合适的网格划分很重要。使用系统划分和局部划分相结合的方法可以保证结果的准确性[5]。
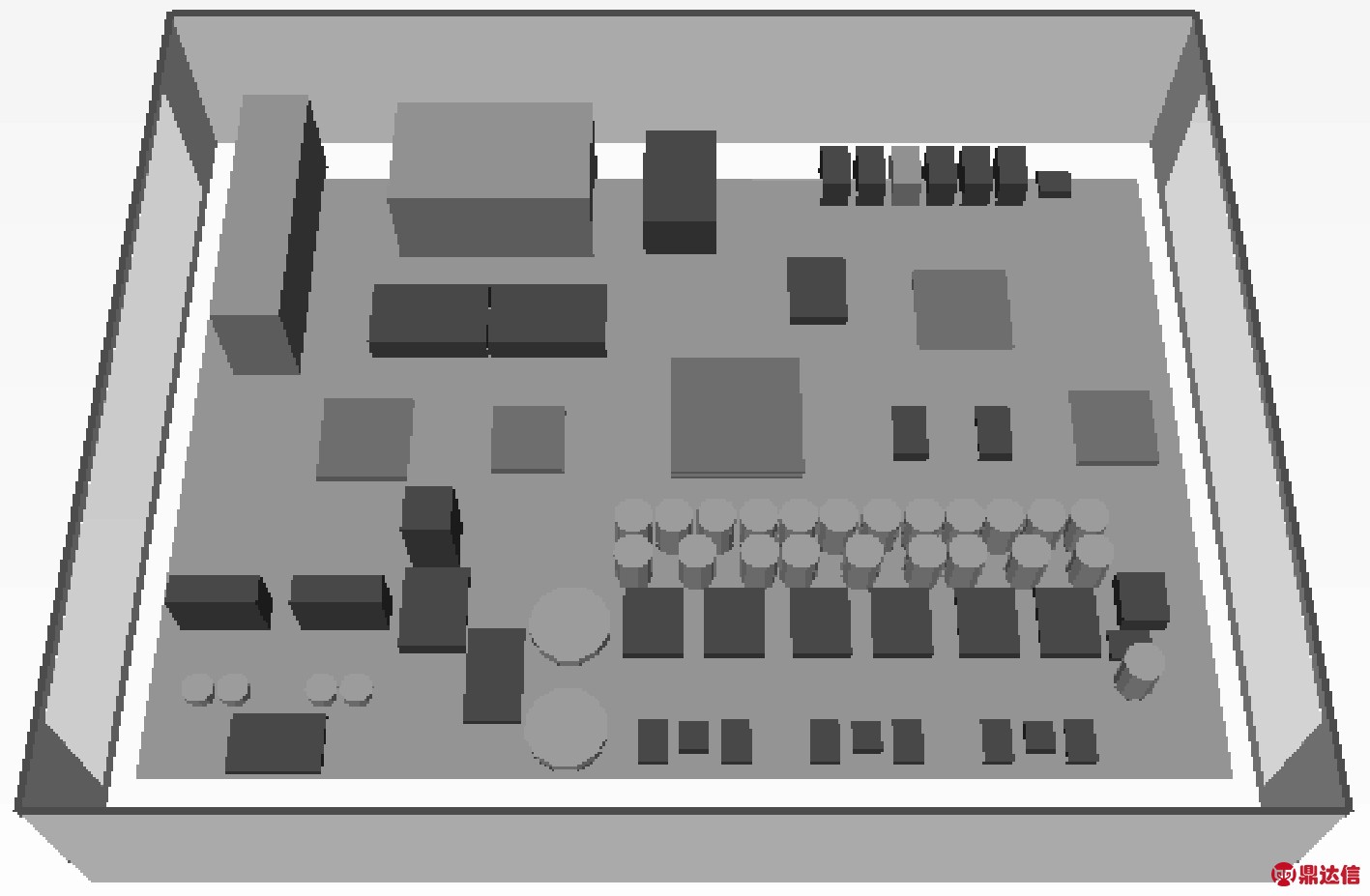
图1 交换机模型
对交换机模型创建系统网格,使仿真模型中的器件沿边界生成Keypoints网格,设置x、y、z3个方向上网格的最大尺寸为20mm,最小尺寸为1mm,并设置相邻网格尺寸平滑过渡,避免相邻网格之间的尺寸比过大。对主板上元器件进行局部划分,设置大尺寸元器件的最小网格尺寸为1mm,网格最小个数为10。小尺寸元器件的最小网格尺寸为1mm,网格最小个数为3。创建PCB板的网格约束,由于计算时需考虑PCB板的热传导,在厚度方向上至少需要3个网格,因此设置PCB板z方向上最小网格尺寸为0.1mm,网格最小个数为3。为进一步提高计算效率,对整机系统进行局域化操作,以去除延伸至求解域边界的网格,网格划分结果如图2所示。
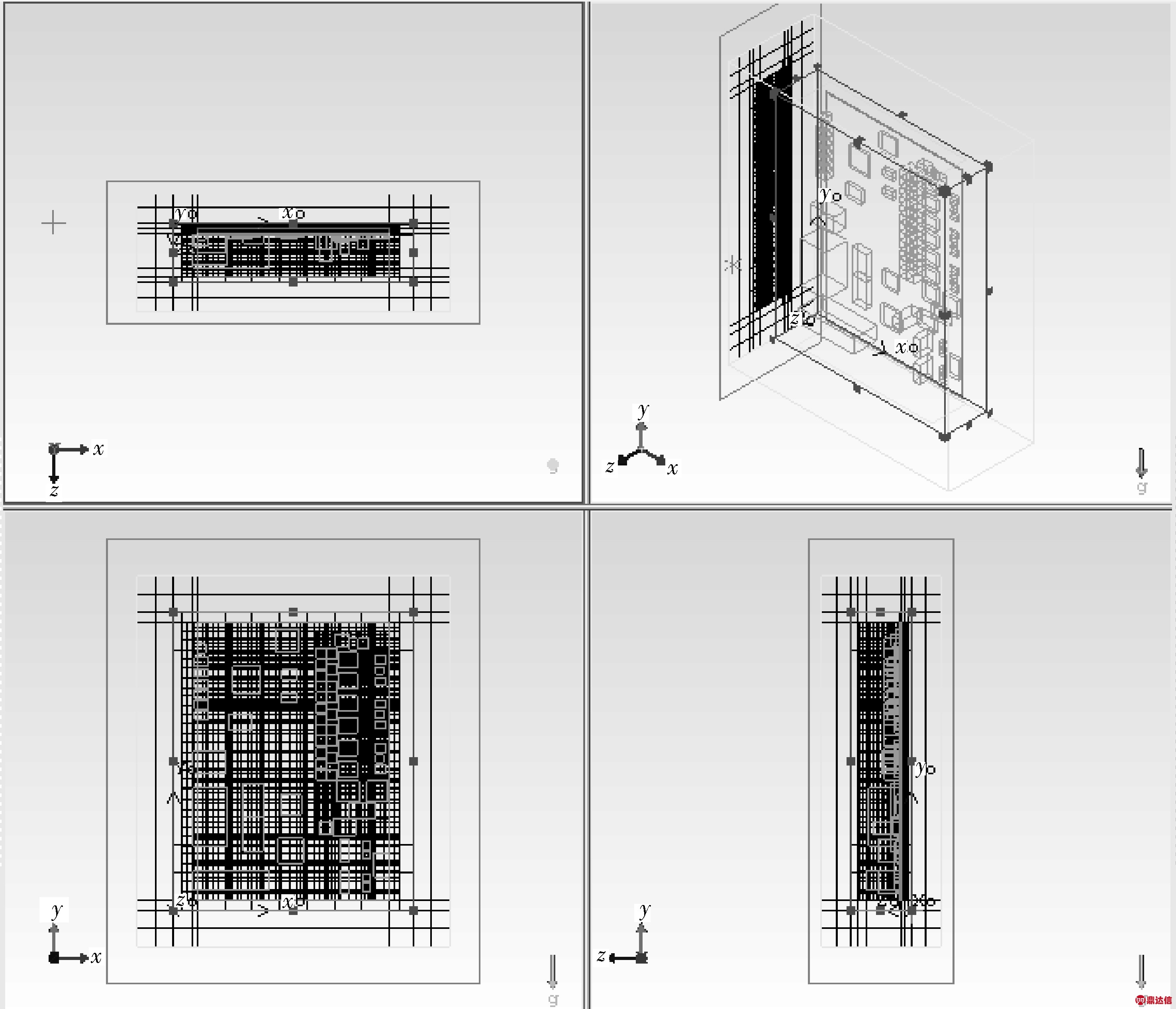
图2 网格划分结果
2.3 求解和结果分析
对划分网格后的模型进行求解,迭代计算得到的残差曲线和监控点温度曲线如图3所示。左侧的残差曲线值已经稳定在数值1上,说明迭代收敛;右侧的温度曲线显示了在当前迭代收敛的情况下各个芯片上和机箱中心的温度值,可以看到监测的温度值已经稳定。图4是过主芯片中心的温度场分布,可以看出温度的高低分布情况。
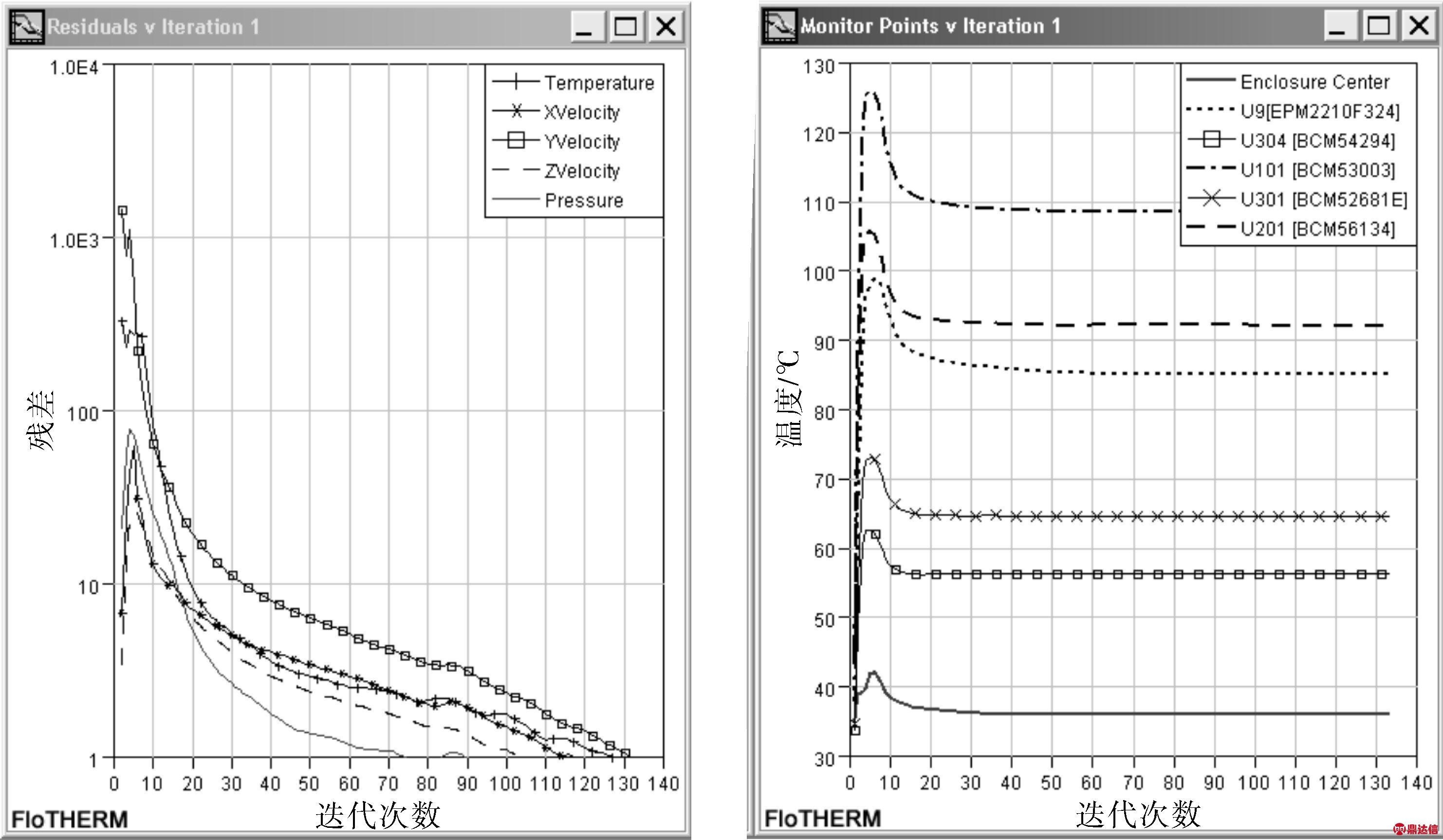
图3 迭代计算残差和监测点温度曲线

图4 机箱中温度场分布情况
由图3求解结果可以看出,芯片U101温度超过100℃,芯片U201温度超过90℃,由于工业级电子元器件的极限工作温度为-40~85℃,因此从仿真结果来看,机箱内温度较高,不符合工业级元器件工作的温度要求,方案需要改进。
3 热设计的优化
常用的加快散热的方法有增加散热孔、添加风扇及添加散热器等,由于设计要求不能添加风扇,因此改进重点在散热孔和散热器,使用Command Center对设计进行优化。
3.1 改进开孔率
由图3可以看出,机箱内关键芯片温度都不低,不利于交换机的长时间运行,因此可修改开孔率以优化散热设计。设定开孔率最小值为0.1,最大值为0.9,将机箱中心温度、芯片U101和U201中心温度同时作为输出变量,求解得到10种方案,结果如图5所示。由图中结果可以看出,两个打孔板的开孔率都为0.82时,机箱中心温度最低。
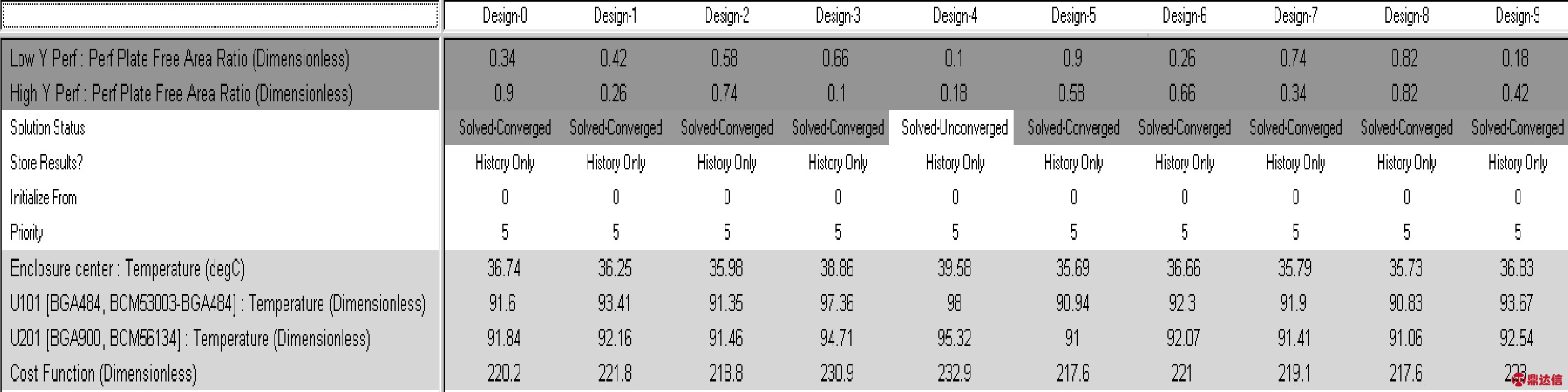
图5 改进开孔率的优化结果
3.2 添加散热器
由图5可以看到,改进开孔率后芯片U101和U201的温度仍高于90℃,比对5个主要芯片的功率可以看出芯片U101和U201的功率确实比较大,因此考虑在这两个芯片上增加散热器。修改主板模型,在芯片U101表面添加散热器,设定散热器尺寸大小与芯片尺寸一致,由于散热器肋片形状为平行矩形直肋时散热效率最高,因此设置散热器类型为平行板,齿数设为4,齿高8mm,齿宽2mm,根据成本和重量综合考虑,选择散热器材料为纯铝。同样对芯片U201添加散热器并设置参数,添加散热器后交换机模型如图6所示。
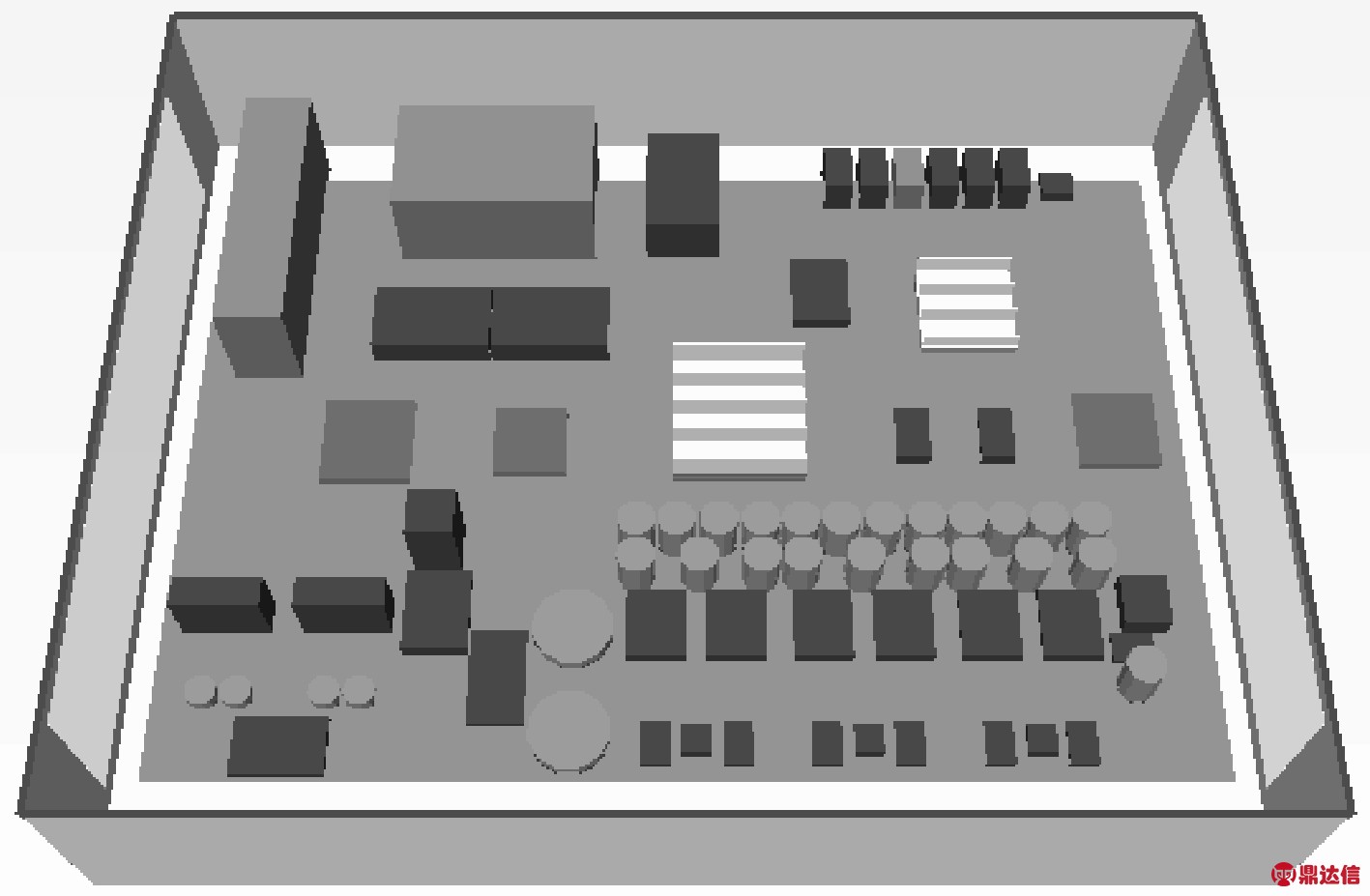
图6 添加散热器的PCB模型
为了保证良好的散热效果,在添加散热器之后,使用Command Center对此方案中散热器肋片的肋高和肋厚进行优化设计,以求达到相对较好的散热效果。设置U101上散热器内部齿数最小值为1,最大值为3,内部肋高最小值为6mm,最大值为10mm,内部肋宽最小值为1mm,最大值为3mm;设置U201上散热器内部齿数最小值为2,最大值为4,内部肋高最小值为8mm,最大值为12mm,内部肋宽最小值为1mm,最大值为3mm。将芯片U101和U201的中心温度同时作为输出变量进行实时监控,设置优化方案的个数为30并求解。图7显示了30种方案中的6种计算结果。
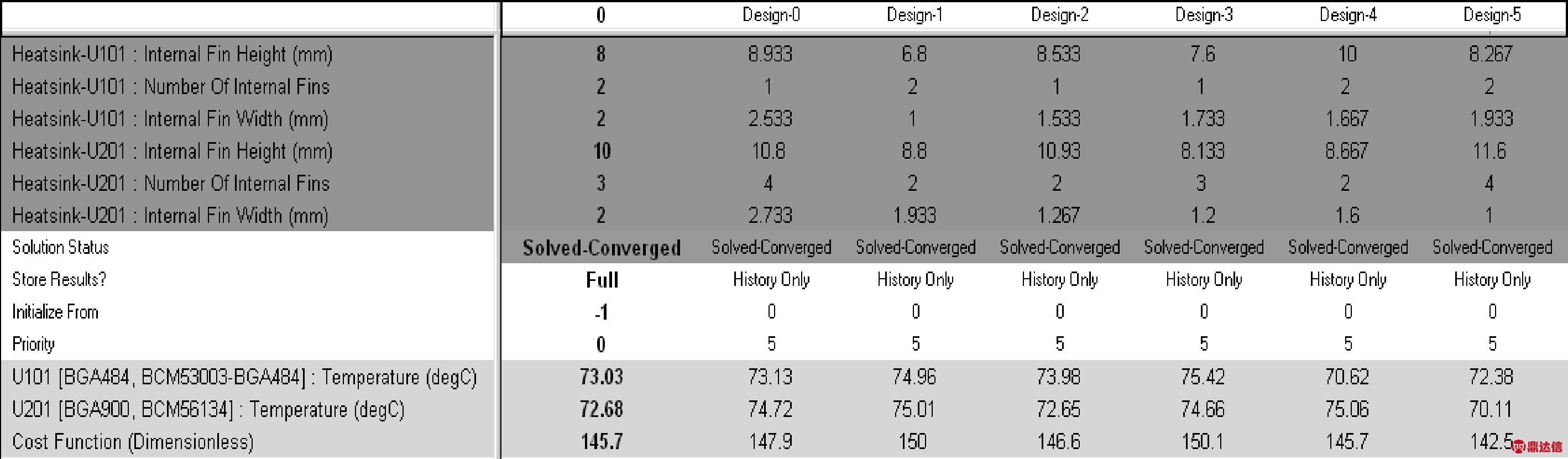
图7 不同方案数据对比
对30种方案的结果进行比较,可以看出其中最优方案为:U101散热器内部肋高8.267mm,内部肋宽1.933mm,内部齿数为2;U201散热器内部肋高11.6mm,内部肋宽1mm,内部齿数为4。按照最优方案给出的优化数据重新计算,计算所得残差曲线和监控点温度曲线如图8所示。

图8 最终残差曲线和监控点温度曲线
根据图8的结果可以看到,受监测的5个关键芯片的温度都在30~85℃,由于工业级电子元器件的极限工作温度为-40~85℃,因此从仿真结果来看,本次改进后的设计符合工业级元器件工作的温度要求。在实际测试中,交换机样机的各项工作参数也都正常,没有出现故障。由此可见,此次优化后的热仿真是有效的。
由仿真结果还可以看到,虽然已经添加了散热器,但是关键芯片的温度仍然都维持在50℃以上,长时间这样工作可能会影响元器件的寿命,从而导致交换机不能正常工作,因此可以在通风和散热方式上再次加以改善,对散热孔进行优化,或者是将散热器的优化方案重新进行设计,进一步加快散热,使产品更好地工作。也可以对交换机内部的电子元器件重新进行布局,合理调整模型的结构,继续分析计算,从而得到最佳方案。
4 结束语
借助FloTHERM软件对自行设计的一款工业以太网交换机进行热仿真分析,模拟出交换机内部的温度场分布,以验证设计是否符合工业现场的要求,并据此提出相应的办法来完善产品设计。引入热仿真分析后,可以大幅提高交换机产品设计的成功率,缩短开发周期,节约开发成本,为设计高质量的交换机产品提供理论指导依据,该方法对交换机设计具有现实指导意义。