摘要:为强化气液离心分离过程,实现在大直径分离器内的气液旋流高效分离,设计构思了一套多旋臂气液旋流分离设备,为气液分离大型化设计提供了一种新思路。在纯气流条件及不同的旋流臂喷出气速下对该分离设备进出口静压差进行了测量,实验结果表明,旋流分离设备静压差在整个运行过程中较为稳定,有较强的可预测性,无量纲标准偏差维持在2%以内,总压降与旋流臂出口气速呈现出良好的平方关系。进一步将总压降分解为入口及旋臂摩擦损失、分离器空间内摩擦损失和出口管路摩擦损失三个部分进行详细测量,获得了各部分压降与旋流臂出口速度头的定量关联模型,发现分离器空间内摩擦阻力损失在总压降中占比最大。GLVS总压降主要受旋流臂出口气速影响,加入液相后对压降影响很小。该旋流分离设备的阻力系数与普通旋风分离器相当,根据四组不同结构尺寸的旋流头得到了阻力系数与旋流头关键设计参数的关联式,为进一步结构优化提供了参考。
关键词:离心分离;压降;模型;预测;气液两相流
引 言
多相流分离问题一直是化工、能源等领域的研究重点。其中气液分离应用场所有很多,如费托合成反应器产生的高温油气在循环换热后进行气液分离[1],加工重质油的加氢单元中循环氢脱硫塔末端对循环氢和氨液进行分离[2],使用压缩机等设备前对输送气体夹带的液滴进行分离[3],催化裂化烟气脱硫洗涤塔对烟气与碱液进行分离[4]等。针对不同的应用背景,气液分离设备的结构和原理一般不同。气液分离设备主要利用离心分离、惯性分离、填料式分离和多种分离方法耦合的方式进行分离操作[5-6]。由于气液两相流体力学理论发展的限制,很难直接采用理论方法定量分析影响分离效果的因素,因此目前对气液分离器大多是从实际应用和实验研究的角度出发,根据不同的操作工况和被分离物质及预期分离效果的要求去设计气液分离器,然后通过实验对分离器的分离效果和性能做出评价。重力沉降器通常应用在天然气开采运输等液滴尺寸较大的场所,Wiencke[7]对立式和卧式的重力分离器在不同工艺参数条件下的结构设计进行了详细的阐述,同时建议在气液两相入口处添加丝网等内构件来提高分离效率。虽然重力沉降器结构简单,能耗较小,但是气液混合物需要较长的停留时间才能达到良好的分离效果,因此分离设备体积大,占用空间较大,分离效率低,且对粒径小于100 μm的液滴分离效果较差。相比之下,基于离心分离机理的旋风分离器具有结构简单、操作稳定、分离效率高等特点[8]。Sagot等[9]通过对一组20~45 mm直径的旋风管式分离器研究发现,分离效率曲线的无量纲斜率与截面Reynolds数相关,并依此建立了分离效率模型和压降损失模型,对其设备结构能够进行良好的预测,但是未报道模型的普适性。Gao等[10]通过在一个直径为65 mm的切向入口式柱状气液分离器上,从实验和模拟的角度均发现,在分离中位粒径约60 μm的液滴时,当入口气速超过16.8 m/s时,分离效率有所下降。他们认为是由于入口速度过大,增加了液滴破碎的可能性,从而使分离效率降低。Shan等[11]在研究液滴喷涂材料时发现,液滴的碰撞聚合与破碎对最终形成的液滴粒径是具有决定性作用的。在分离过程中,被分离介质的粒径分布与设备的分离效率和压降是密切相关的。Wang等[12]在一个环形流通区域内模拟旋风分离器中的旋转流动,他们从液滴碰撞、液滴破裂和液滴与壁面的碰撞这三个角度来模拟液滴的运动情况,较为充分地考虑到液滴在旋转分离运动过程中可能会发生的形变,从而建立了一个分离效率模型来预测旋风分离器的分离效率。因此在气液分离体系中,设计新型气液旋流分离器时要控制入口管和旋流臂的设计气速,不宜过高,尽量避免液体破碎现象导致的分离效率下降的情况。
很多学者在实验室规模下研究气液分离器时,虽然在实验条件下都可以取得较高的分离效率,但是在工业应用时依旧会出现分离效率低、分离设备运行不稳定的情况,如进压缩机前液滴分离不完全,对叶片产生腐蚀,降低压缩机寿命;催化裂化烟气洗涤塔烟囱排放大量未分离液滴,从而产生落雨、结冰等现象。一方面是由于从实验室规模到工业应用过程中,分离设备的放大受到气液两相流理论的限制,不能够很好地实现大型化的外推设计,另一方面受分离器本身的结构限制,不能使之大型化,如PV型旋风分离器,在保持较优的分离效果的前提下,筒体直径最大不超过1.2 m。因此在工业应用时,为了尽可能地降低放大效应的影响,多采用多组小直径旋风管或旋风分离器的并联结构。虽然可以取得较好的分离效果,但当气液分离负荷较大时就会出现分离器的数量很多,导致入口流量分配不均、排液口窜气等大幅度降低分离效率的问题,同时也使分离器的结构更复杂。基于气液分离体系存在的液滴在分离器内随机性强、规律难以掌握的实际问题,研究者们多采用借鉴相同分离机理的气固分离体系中优化结构的分离器类型加以优化的方法开发高效的气液分离设备,如切向入口的旋风分离器[13],轴流式导叶式旋风分离器[14]等,它们的设计理念都成功应用在气固和气液两种体系的分离且取得了良好的分离效果及工业应用价值。在气固分离体系,本研究团队开发的用于催化裂化提升管末端的名为VQS(vortex quick separator)[15-16]和 SVQS(super-vortex quick separator)[17-19]的气固分离设备具有卓越的分离性能,利用旋流臂等结构来实现气固的高效分离。目前这两种快分系统在我国已经成功应用在近30套工业装置,取得了巨大的经济效益,达到了国际领先水平。该结构的气固快分系统,成功替代了多组常规旋风分离器,能够在分离效率略有提高的基础上,大幅度简化设备结构。前人的研究发现气液分离体系与气固分离体系的差异,主要表现在固体可以在较高的气速下保持其颗粒和粒团的完整性,而液体在一定条件下会发生碰撞聚并现象,也可以在表面张力的限制和高速气流的剪切作用下,发生破碎现象[20]。对于分离过程来说,被分离物质的粒径越小,能够被分离下来的概率越小,即分离效率也越低。在VQS和SVQS气固分离设备中,旋流臂出口气速最优约为22 m/s。应用到气液分离时,旋流臂出口的设计气速应较气固分离设备的低,从而使液体的粒径分布在进入分离器时保持相对稳定。
为了实现大直径旋液分离系统的强化、满足装置大型化的设计要求,迫切需要开发基于多旋臂的气液旋流分离高效设备,以简化设备结构,强化在大直径分离设备内的气液分离过程。因此相比于应用成熟的VQS和SVQS气固分离设备,在保证处理量的前提下,本实验结构主要通过增大入口管和旋流臂出口面积来降低入口管和旋流臂出口气速,以期避免液体的破碎现象。压降作为分离器性能的重要指标之一,在分离器开发应用过程中具有重要意义[21]。分离器设计完成后,可以通过分离器的压降特性来初步了解分离器的性能[22],以期为之后的改进做参考。
1 实 验
多旋臂气液旋流分离器压降特性实验在大型冷模实验平台上进行,实验装置及流程如图1所示。
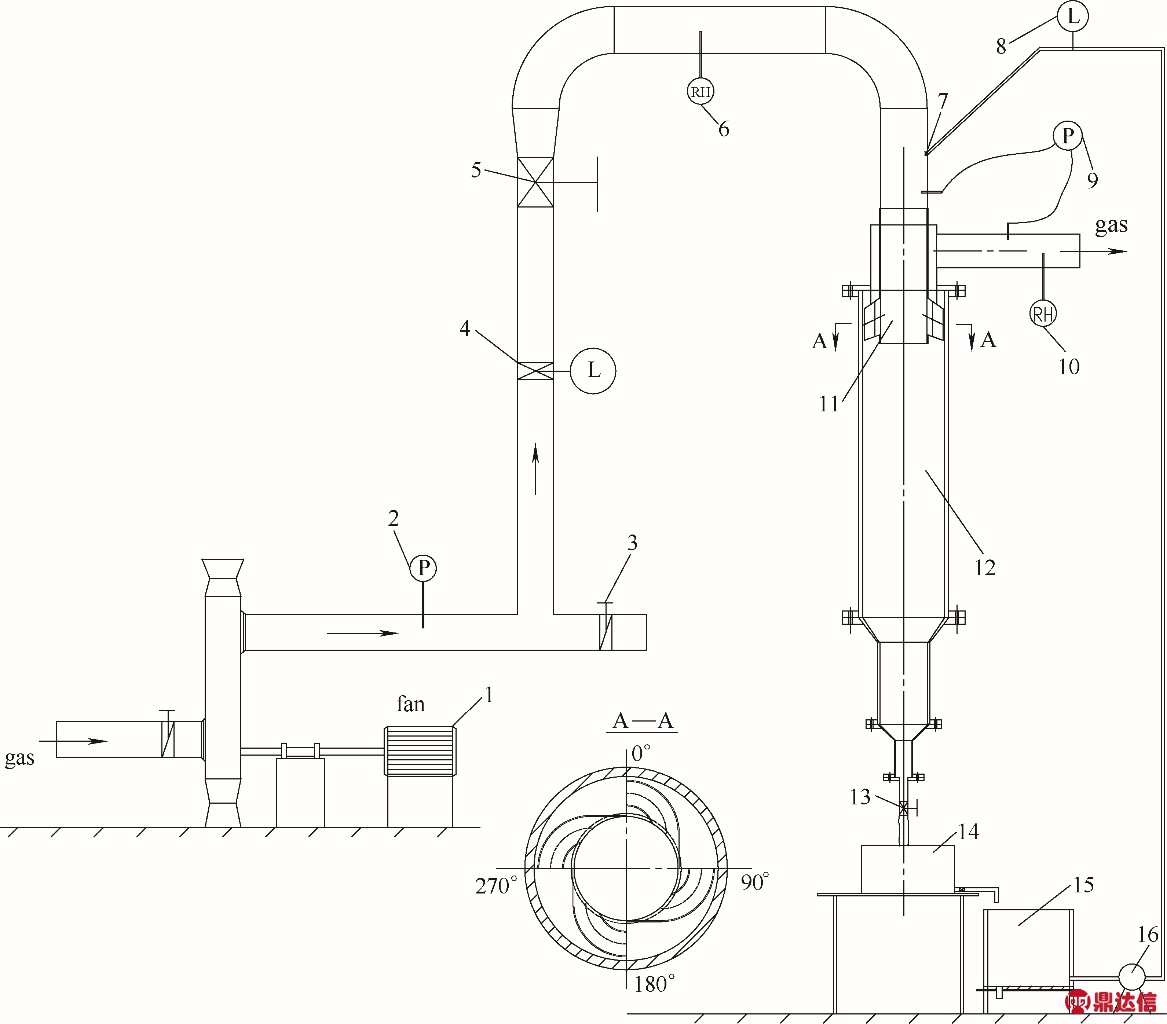
图1 多旋臂气液旋流分离器实验流程图
Fig.1 Schematic diagram of the experimental apparatus
1—鼓风机;2—压力表;3—放空阀;4—智能型涡街流量计;5—调节阀;6—入口湿度计;7—超声波喷嘴;8—液体流量计;9—压差表;10—出口湿度计;11—旋流头;12—分离空间;13—排液阀;14—计量罐;15—水箱;16—水泵
实验所用设备的分离空间由φ500 mm×2000 mm的有机玻璃制成,以便于观察其内部流动状况;气体进口管路采用φ299 mm×8 mm的碳钢制成;旋流头选用304不锈钢材质,其出口采用4个旋臂,每个旋流臂的出口尺寸为192 mm×64 mm,水平排气管采用φ219 mm×6 mm的304不锈钢制成。实验采用正压操作,即利用鼓风机提供主风,在调节阀和放空阀共同调节下,气体经过智能型涡街流量计计量后进入旋流头。气流在进气管末端旋流臂的作用下,沿切向进入分离空间,并在筒内经过一系列运动后,进入分离空间顶部的环形排气管,即竖直排气管与进气管(外直径299 mm)之间的环形间隙。最后经过与环形排气管相接的水平排气管排入大气。
设备压降由标智511型高精度数显压差计进行实时记录,压差计量程为10 kPa,精度为±0.3%满量程(± 25℃),分辨率为10 Pa,响应时间为0.5 s,记录频率为1笔/秒。两个压差测点分别设置在旋流臂出口中心上650 mm处的进气管(内直径Di=283 mm)上和距环形排气管连接位置1350 mm处的水平出气管(内直径Do=207 mm)上,压差计所测结果为设备进出口两测点间的静压差ΔP。气量Qi由智能型涡街流量计进行计量。智能型涡街流量计记录气流经过它时产生的振荡频率,根据卡门涡街原理换算成工况流量,再根据其本身测量工况气流下的温度和压力换算成标况流量,并将示数传输到流量控制仪上,从而实现对气体流量的调控和记录。
实验设定标况流量范围为1000~3000 m3/h,对应入口气速(入口静压测点位置)为4.42~13.25 m/s,对应旋流臂出口气速ui为5.65~16.95 m/s,对应筒截面气速为1.42~4.25 m/s。具体参数见表1。
2 结果与讨论
2.1 设备静压差测点位置的确定
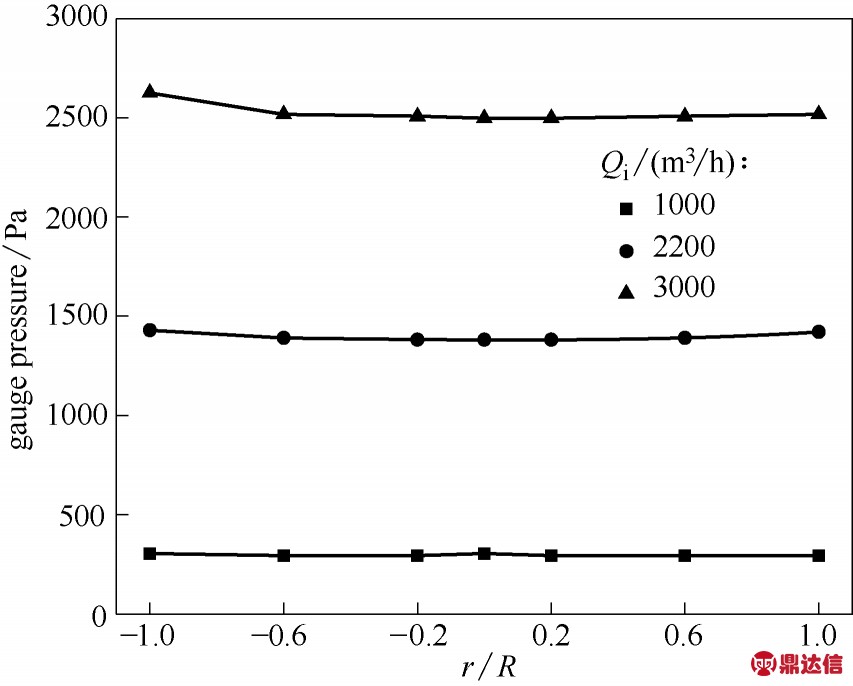
图2 不同入口气量下入口管表压随径向位置的变化
Fig.2 Inlet tube gauge pressure vs radial position at different air flow rates
为了确定进出口管路上具有代表性的压力径向位置测点,在纯气流的情况下,对进出口管路的不同径向位置测点的表压进行测定。其中,R表示管路的内直径,r表示引压管水平插入深度,管路的边壁分别对应r/R=-1.0和r/R=1.0,则r/R=0时表示压力测点在管路的中心位置。由图2的测量结果可知,在测量截面内,入口管静压沿径向分布比较均匀,受边壁效应下的气流不稳定流动影响较小,说明所选截面合理,与测量传统旋风分离器进气管静压时情况相似。由图3可知,出气管静压分布沿径向略有波动,但大致呈中心对称分布。水平出气管与环形排气管的垂直连接方式,使气流改变了运动方向,即在水平出气管测点截面处的气流流动形式已经由其上游环形排气管中的强旋转气流转化为水平气流。同时,气量越大,在气流转变方向的时候就会越剧烈,导致在测点截面内测量静压时径向波动较大。另外,从图中可以得到,在实验气量范围内,出气管中心处的静压值变化梯度较小,适合作为测点位置。相比于测量传统旋风分离器中出气管旋转气流的静压,本实验选择出气管的静压测量截面干扰更小,更为准确。因此本次实验将进出口管路上的静压测点均设置在管路的中心,即r/R=0位置处。
表1 实验参数设计
Table 1 Experimental parameters design

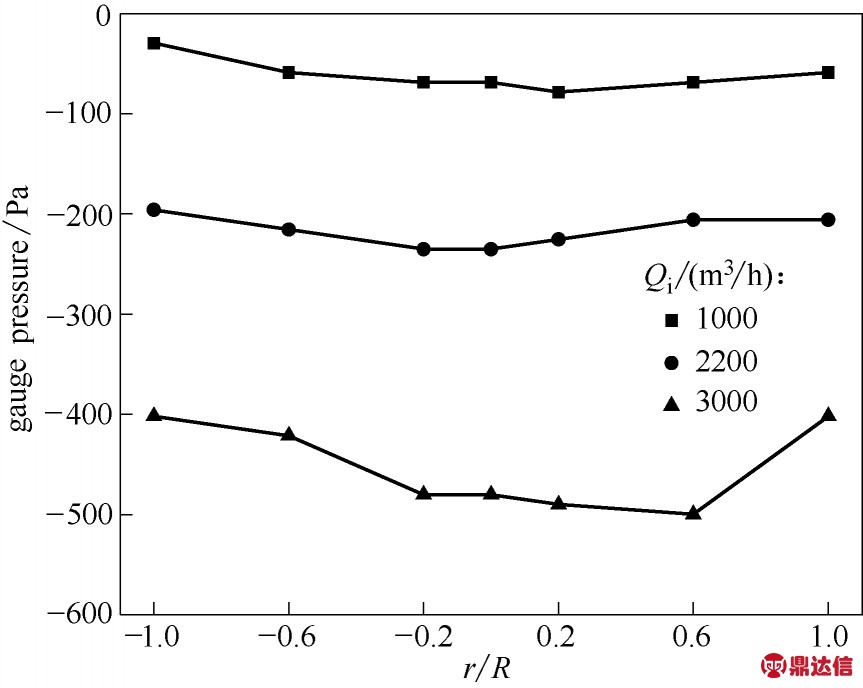
图3 不同入口气量下出口管表压随径向位置的变化
Fig.3 Outlet tube gauge pressure vs radial position at different air flow rates
2.2 设备静压差及其稳定性分析
在纯气流状态下,对设备在1000~3000 m3/h入口气量下的进出口静压差进行了测定。待设备运转稳定后,每个气量记录450笔左右的静压差数据,由于考虑测量仪器在开始和结束时可能的测量误差,截取其第51~400笔数据,即共350笔数据作为实验测量结果,见图4。由图4可以看出,实验气量下的设备实时静压差均稳定在对应气量下静压差时均值ΔP附近,这说明设备在实验气量下运行状态比较稳定。将设备静压差的时均值对入口气量作图,如图5所示,随着入口气量的增大,设备静压差也随之增大,变化趋势初步分析为抛物线型变化关系,又因为入口气量与入口气速是呈正比的关系,因此,即应存在如下线性变化关系

图4 不同入口气量下设备静压差随记录时间的波动状况
Fig.4 Fluctuation of static pressure drop vs recording time at different air flow rates
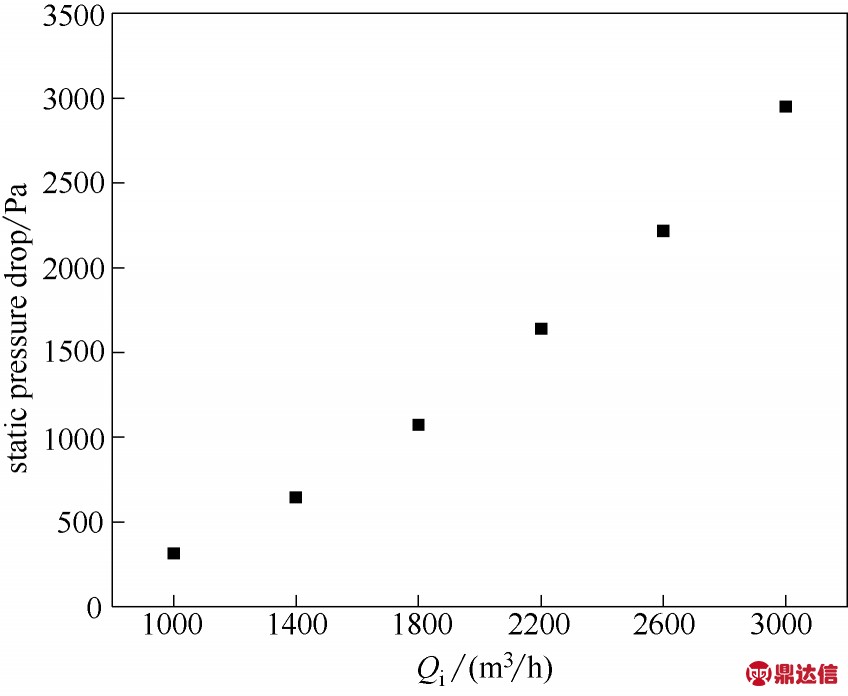
图5 设备静压差随入口气量的变化
Fig.5 Static pressure drop vs inlet gas flow rates

类比于研究旋风分离器的文献所得到的压降影响关系,即将压降通常表征为与入口速度头的线性关系式。即

从图4中可以看出,随着入口气量的增大,设备静压差波动的绝对值也逐渐增大,在入口气量为3000 m3/h时,静压差波动的绝对值达到最大,最大测量值与最小测量值之差为117.6 Pa,设备静压差随时间不稳定波动的状况可以用标准差σ来进行描述,本实验的标准差σ计算公式为
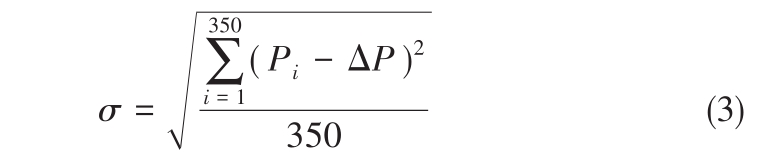
设备静压差时均值ΔP及对应的标准差σ计算数据见表2,从表中可以看到,标准差随着入口气量的增大而增大,最大波动情况出现在入口气量为3000 m3/h处,不同气速下的静压差标准差σ均在20 Pa以内。根据图6所示,标准差随着入口气量呈现递增的趋势,但是随着入口气量的增大,气体流速随之增大,设备静压差也相应增加。
根据以上分析,标准差仅能表示测量数据相对其算术平均值偏离程度的绝对大小,并不能代表压降波动在设备运行时总压降中所占据的比例,不适合用来表征设备静压差在不同入口气速条件下的稳定性能。因此通过无量纲标准差σ′,用于描述压降波动在设备整体压降上所占的程度,以方便对不同入口气量下设备的静压差稳定性进行比较。无量纲标准差σ′的计算方式为
表2 设备静压差稳定性表征
Table 2 Stability characterization of static pressure drop
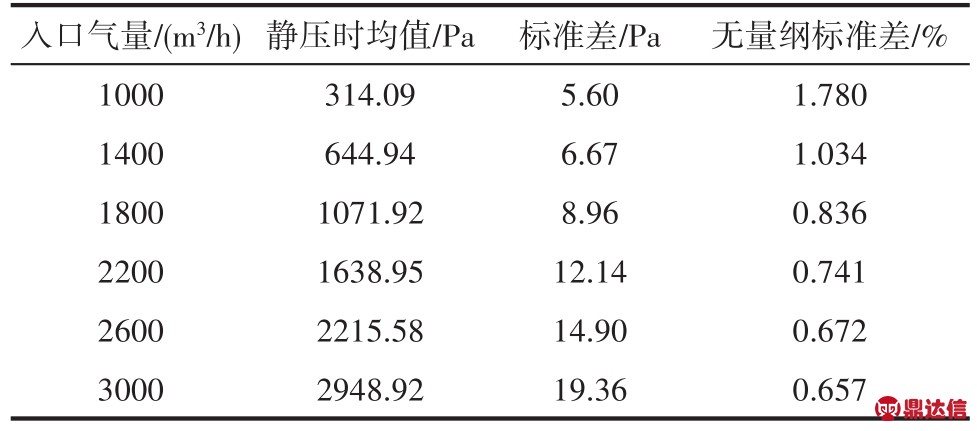

所得各实验气量下设备静压差无量纲标准差列于表2中,从表中可以看出,无量纲标准差均小于2%。从图7中可以看到,无量纲标准差保持相对稳定且有逐渐下降的趋势,表明气量越大,设备运行越稳定。综上,在实验气量范围内,考虑到仪器本身的测量误差以及鼓风机提供气流及气流流动的不稳定性,可以认为在整个实验过程中,设备静压差的波动状况十分微弱,设备运转相对稳定,设备压降性能表现出较大的可预测性。
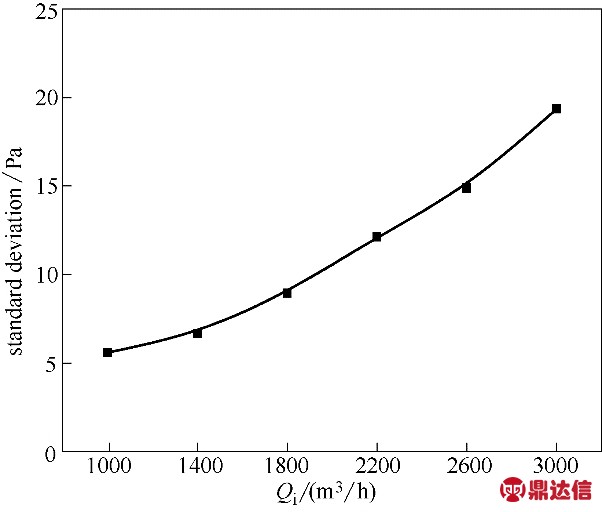
图6 标准差随入口气量的变化
Fig.6 Change of standard deviation with gas flow rates
2.3 各段压降测量结果分析
将进气管静压测量截面作为起点,以出气管静压测量截面作为终点,按照气体的流动路径将总压降划分为以下3个部分(图8):
(1)进气管测量截面至旋流臂出口,代表入口和旋臂压降损失P1;
(2)旋流臂出口至环形排气管下沿,代表分离器内内外旋流摩擦损失造成的压降损失P2;
(3)环形排气管下沿至出气管测量截面,代表排气管压降损失P3。
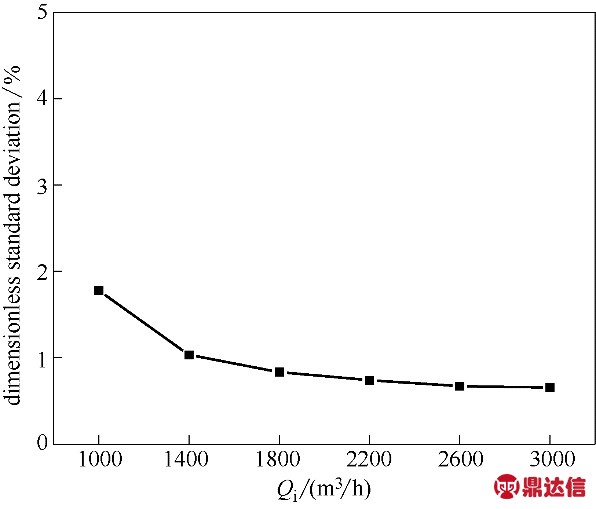
图7 无量纲标准差随入口气量的变化
Fig.7 Change of dimensionless standard deviation with gas flow rates
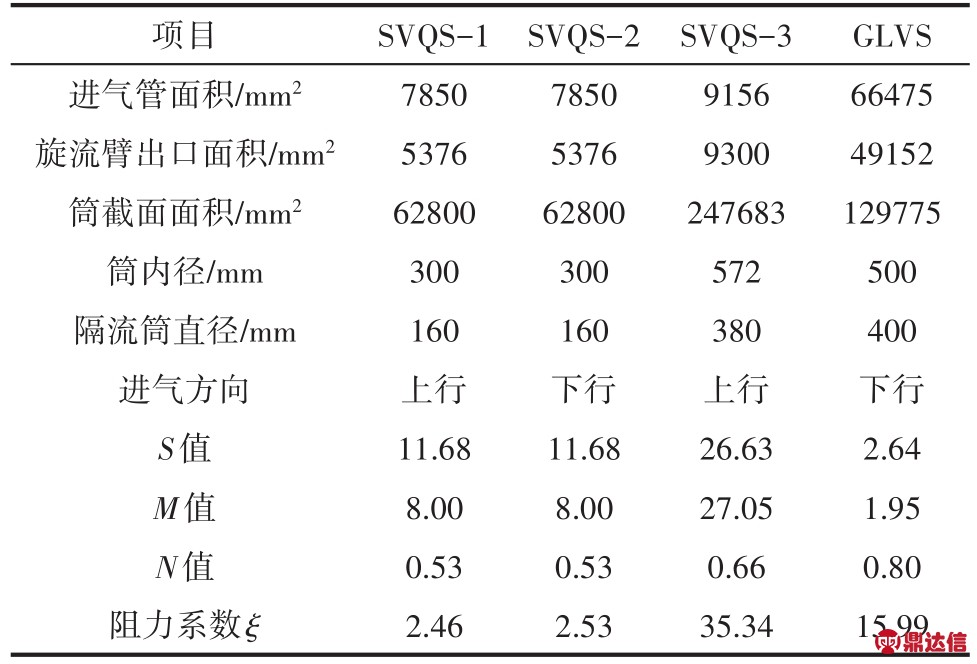
图8 分段压降测量时测点位置
Fig.8 Segmental pressure drop measuring points
由分段测量得到的总压降ΔP′的计算式为

与测量得到的总压降的误差比例ε的计算式为

将实验所得测量数据列于表3。
由表3首先可以看到,分段测量的压降总和与测量的总压降值之间的误差较小,均小于7%,满足进一步分析要求。从表3还可以看到,分离器空间内摩擦损失所占比例是最大的,约为57%,这是由于气流在分离空间内的复杂的运动形式决定的。这其中包含气流旋转带来的摩擦损失,气流与壁面之间的摩擦损失,也有气流在运动过程中速度的变化等带来的摩擦损失。这与常规旋风分离器中旋流体的摩擦损失占主要比例的情况是一致的。
表3 分段压降测量值
Table 3 Measured values of segmental pressure drop
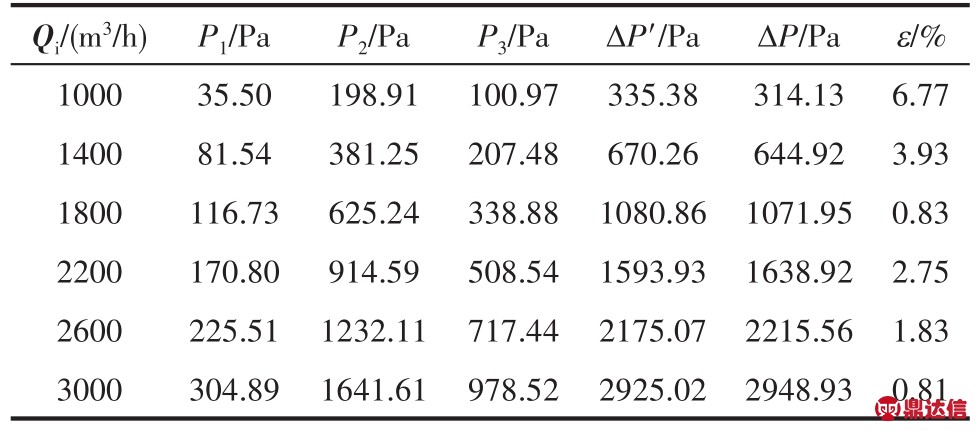
与常规分离器不同的是,排气压降损失略大。这是由于本设备环形排气管下沿处流通面积较小,阻力较大。另外,经过环形排气管后,气流由竖直运动方向转为水平运动方向,同样也造成了一定的损失。但是这一部分的压降损失是可以通过优化排气管的结构来降低的。
将各段压降对旋流臂出口速度头作图9,发现线性关系良好,即满足

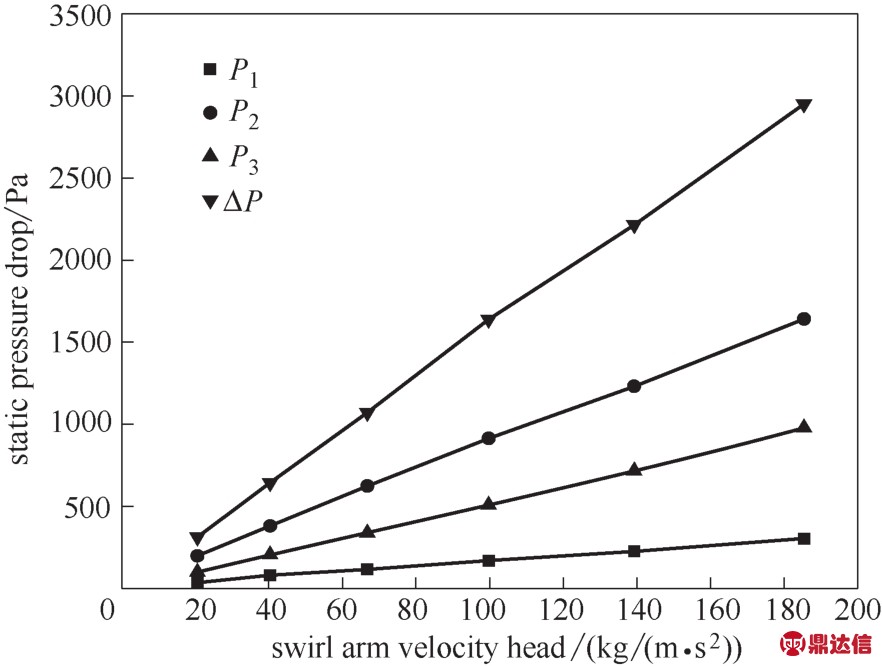
图9 各段压降与旋流臂出口速度头的关系
Fig.9 Relationship between segmental pressure drop and velocity head of swirl arm
将上述线性拟合关系式系数列于表4。
根据R2可以判断,数据拟合关系良好。该分离器总的阻力系数ξ约为16,常规旋风分离器的阻力系数ξ一般在10~20之间,即本设备与单个旋风分离器的压降损失接近。在气固分离实践中发现,多旋臂的SVQS分离设备可以有效代替多组旋风并联操作,其最大分离器直径可以达到5.7 m。一方面减少了由于多组旋风分离器带来的进气不均和窜气等使分离效率下降的现象,另一方面也简化了分离设备结构,降低了设备投资,具有较大的经济效益。因此可以推断在气液分离体系中,多旋臂的旋流分离设备也会具有以上优点。
表4 各段压降阻力系数
Table 4 Segmental pressure drop resistance coefficients
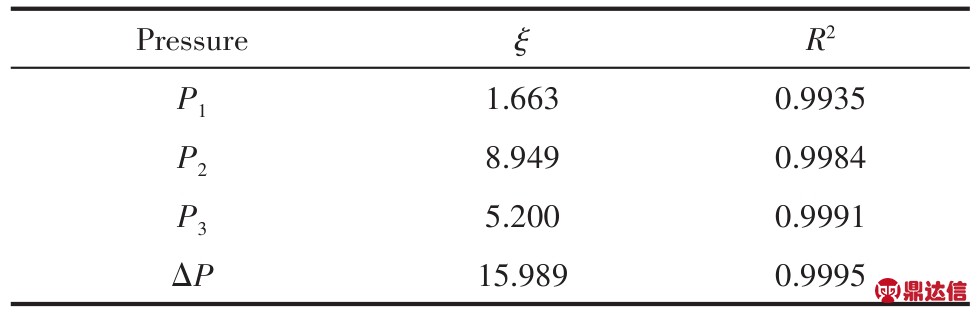
2.4 多旋臂气液旋流分离器与气固SVQS设备的压降对比情况
同一个SVQS设备在纯气流时的压降与气速相关,不同的SVQS设备压降则与设备本身的结构有一定关系,特别是与旋流头处的关键尺寸信息相关。关键尺寸信息包括进气管面积Si,旋流臂出口面积Sv,筒截面面积Sc,筒内径D和隔流筒直径De,在进气方向上可设置为上行或者下行。在对上述关键信息进行整理时,采用将变量无量纲的方法,定义如下参数
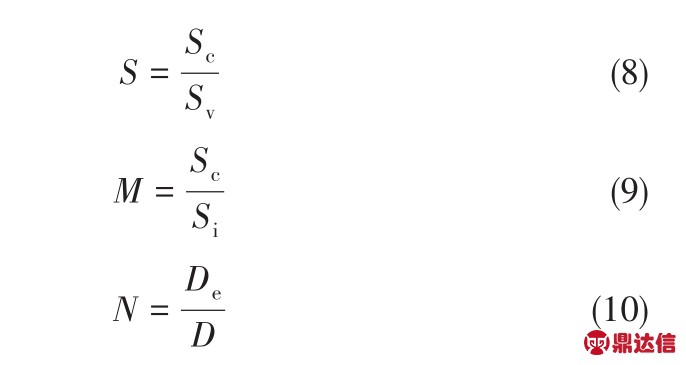
周双珍等[23]研究了进气方向不同的两种相同结构尺寸的气固SVQS分离设备在纯气流时的压降,其中SVQS-1是上行式,SVQS-2为下行式。黄世平等[24-25]提出的用于气固分离的SVQS-3设备,它的筒直径为572 mm,具体结构尺寸见文献。他们虽然没有测量纯气相时设备的压降,但是入口固体浓度在0.36~1.35 kg/m3这一较低的范围内时,所测得的压降与纯气相时压降是接近的,可以与其他结构纯气流条件下的数据做对比。他们的结构参数及本实验的结构GLVS的参数汇总如表5所示。
将上述4个结构在纯气流条件下的压降数据汇总如图10所示,按照上文提到的计算阻力系数ξ的方法,将4个结构的ξ列于表5中。
从表5和图10可以发现,同一设备的压降随着旋流臂出口速度头的增大而增大。另外可以发现,阻力系数与结构参数密切相关,将阻力系数与上述无量纲参数写成以下数学关系式

根据式(11)计算得到的阻力系数与通过数据拟合得到的阻力系数之间的误差不超过0.5%,能够良好预测不同结构参数对旋流头压降的影响程度。
表5 旋流头结构参数汇总
Table 5 Summary of swirl head structure parameters
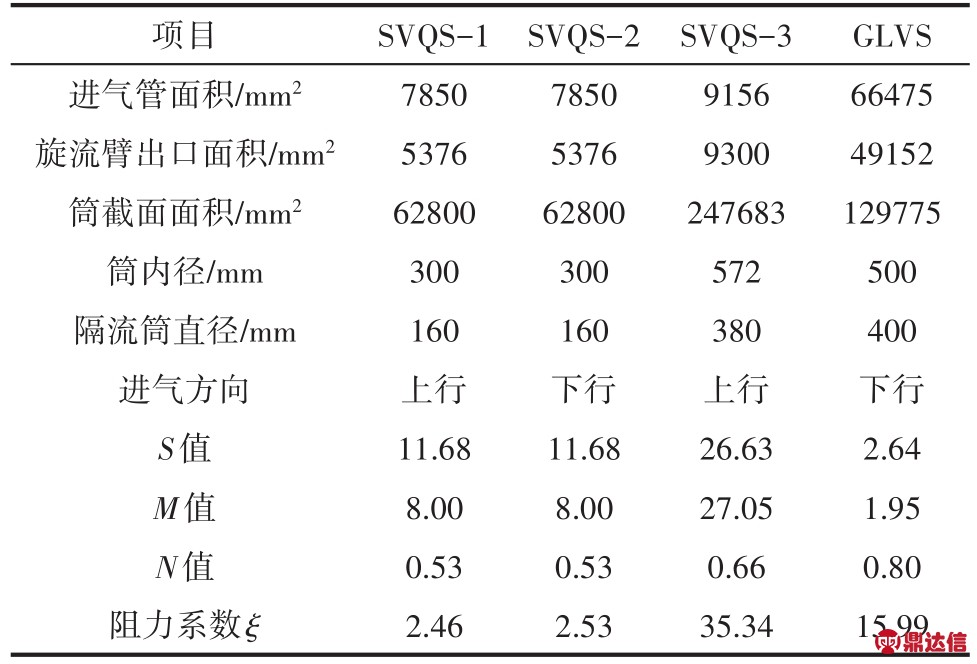
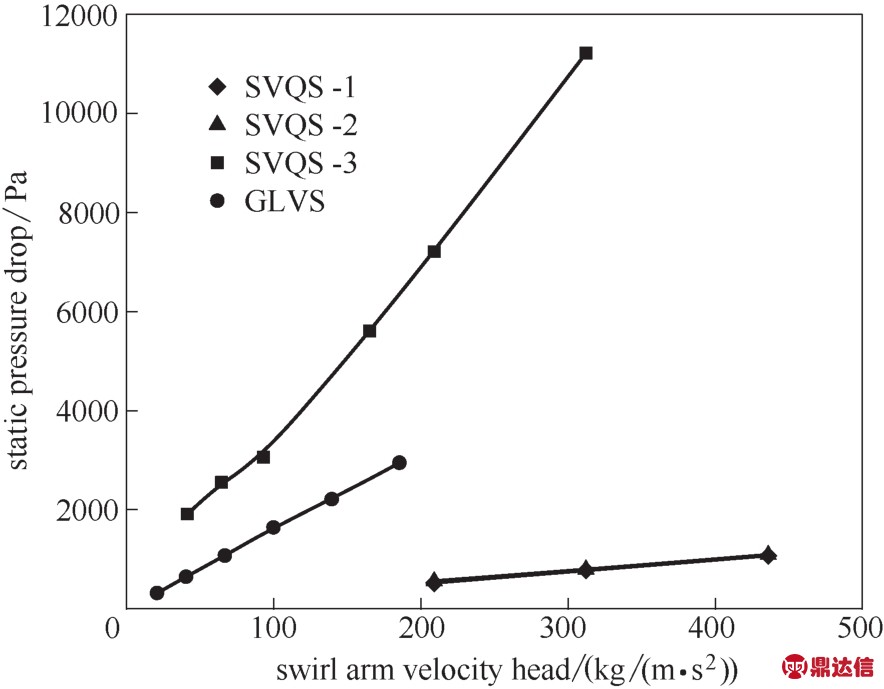
图10 不同旋流头结构下的压降随旋流臂出口速度头的关系
Fig.10 Relationship between pressure drop of different structures and velocity head of swirl arm
2.5 气液混合分离时GLVS的压降
黄世平[25]在SVQS设备上通过实验发现,在气固分离体系中,相同的入口气速条件下,气固两相进料时比纯气流时分离器压降大。也就是说,固体颗粒的加入增大了分离器的压降。基于此,本实验考察了液滴的加入对GLVS压降的影响情况。实验中液滴由超声波雾化喷嘴产生,其流量由液体流量计控制。实验中控制不同操作气速条件下液滴浓度Ci为60 g/m3,探究了在不同旋流臂出口气速下的GLVS压降变化情况,并将得到的结果与纯气流时GLVS的压降进行对比,实验结果如图11所示。结果发现,加入液相后总压降大小与纯气流时压降大小差异不大。因此,GLVS总压降基本由旋流臂出口气速决定,加入液滴后,并不会影响分离器的压降。
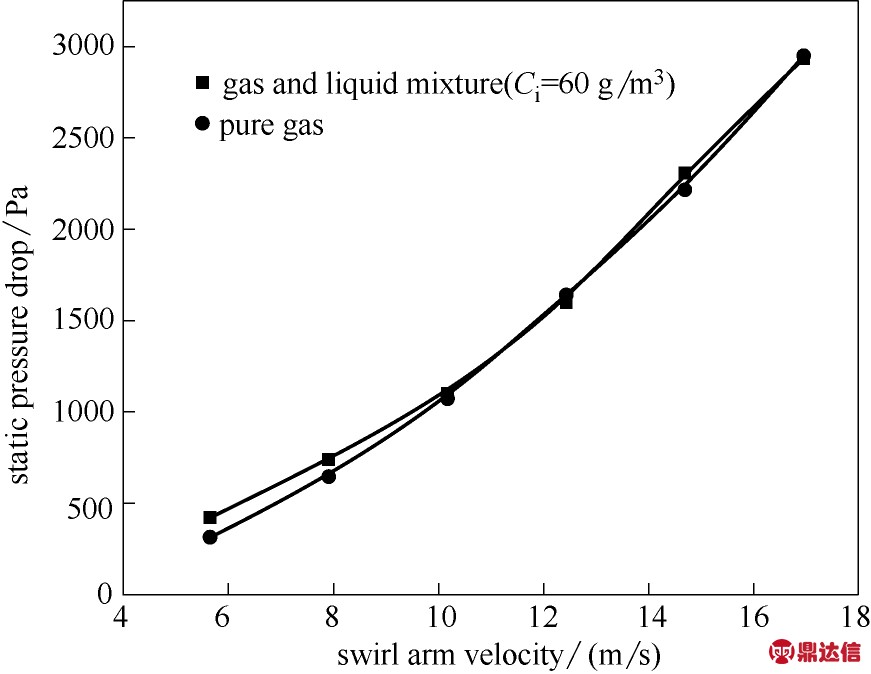
图11 加入液相后GLVS压降变化情况
Fig.11 Change of total pressure drop after feeding liquid
3 结 论
(1)为考察设备静压差ΔP与气液旋流分离器旋流臂出口气速ui的关系,分别对不同入口气量Qi下的静压差数据进行了测量,利用无量纲标准差σ′描述设备静压差在一定气量下运行时的稳定性能,结果表明设备整体运转稳定,σ′维持在2%以下。
(2)设备压降与旋流臂出口气速呈现出良好的二次抛物线关系,与普通旋风分离器压降方程相似。通过线性拟合,得到多旋臂气液旋流分离器的阻力系数约为16,且拟合关系良好,说明设备压降具有较好的可预测性。
(3)根据气体的运动路径将总压降划分为三部分进行测量,发现该分离器中筒体内的摩擦损失产生的压降最大。
(4)通过分析4个不同尺寸的旋流头结构的阻力损失,获得了阻力系数与关键结构参数的经验模型,可预测旋流结构尺寸参数对分离器压降的影响程度。
(5)GLVS设备总压降主要受旋流臂出口气速影响,加入液相后对总压降影响不大。
符号说明
Ci——液滴浓度,g/m3
D,De——分别为筒截面内径和隔流筒内径,mm
Di,Do——分别为进气管内径和水平出气管内径,mm
P1,P2,P3——分别为入口压降损失、旋流体摩擦损失和排气管压降损失,Pa
ΔP——设备静压差,Pa
ΔP′——分段测量静压差之和,Pa
Qi——进气量,m3/h
R,r——分别为管路内径和引压管水平插入深度,mm
Si,Sv,Sc——分别为进气管面积、旋流臂出口面积和筒截面面积,mm2
ε——误差比例
ξ——阻力系数
ρ——气体密度,kg/m3
σ——静压标准差,Pa
σ′——无量纲静压标准差