本文介绍了一种新型的真空锻造复合轧辊制备工艺,通过该工艺制备了芯部为42CrMo、复合层为高耐磨性Cr5钢的复合轧辊。结果表明:锻后退火态Cr5/42CrMo复合轧辊复合层与芯部的结合率达100%,且拉伸试样断裂位置均在芯部42CrMo一侧,抗拉强度达656.7MPa,真空锻造复合轧辊制备工艺的研究为大型复合轧辊的制备提供了广阔的前景。
轧辊作为轧钢生产中主要消耗备件之一,轧辊质量不仅关系到轧钢生产成本和轧机生产作业率,还很大程度上影响轧材质量。传统单一材质合金轧辊制造工艺主要为整体铸坯再锻造成形,为了使轧辊工作层具有良好的耐磨性和热硬性,往往在铸坯过程中添加大量合金元素。例如在高速钢轧辊中添加W、Mo、Cr、V等合金元素,通过控制碳、合金元素的含量,可以得到高显微硬度共晶碳化物来提高轧辊的硬度和耐磨性。但由于铸坯凝固过程中冷却速度快,这些合金元素及它们的碳化物来不及扩散,从而在铸坯中产生严重的偏析现象,且轧辊尺寸越大,中间疏松、夹杂、组织不均问题越严重,大大降低了轧辊锻造成材率,制备的轧辊也难以同时满足轧制过程中对其耐磨性和韧性的双重要求,而复合轧辊,由于芯部和工作层可以选用不同的材质,再通过一定的制备工艺将两者有机地连接起来,这样既满足了轧辊表面高耐磨性、芯部高韧性的要求,大大地提高了轧辊的使用寿命,是未来轧辊的研究方向。
目前制备复合轧辊的工艺主要为铸造工艺,但铸造工艺有其自身无法解决的问题,例如离心铸造法(CP)虽然具有生产效率高、成本低及适合于大批量规模生产等优点,但是该工艺存在着铸件工作层偏析严重、尺寸精度不高、稳定性差等问题。连续浇注复合铸造法(CPC)所制备的复合轧辊克服了常规离心铸造方法所产生的合金偏析问题,但其明显的不足在于其成本高、生产效率低。电渣重熔法(ESR)可以通过采用不同的自耗电极制成具有梯度分布的复合轧辊,但其缺点是生产效率低、且很难实现大型复合轧辊的制备。使用喷射沉积成形法(Osprey)制备的复合轧辊组织细化,析出相均匀弥散,不足之处在于该方法生产的轧辊外层组织不够致密,且生产成本高,工艺复杂,不利于轧辊的大批量生产。
为了提高轧辊性能、生产效率和实现复合轧辊的大型化,本文提出了一种新型复合轧辊制备工艺,即真空锻造复合轧辊制备工艺,通过对该工艺的研究表明其生产效率高、适应于大规模生产,制备的复合轧辊界面结合性能好,且填补了锻造复合轧辊的空白。
试验方法
本次真空锻造复合轧辊制备工艺研究以合金结构钢42CrMo为芯部,以高耐磨性的Cr5钢为复合层,在真空条件下将芯部、复合层端部焊接密封,然后高温锻造成形使芯部和复合层界面实现完全冶金结合。
芯部、复合层材质的选择
试验所选用复合层材质的化学成分如表1所示,芯部、复合层的尺寸如图1所示。
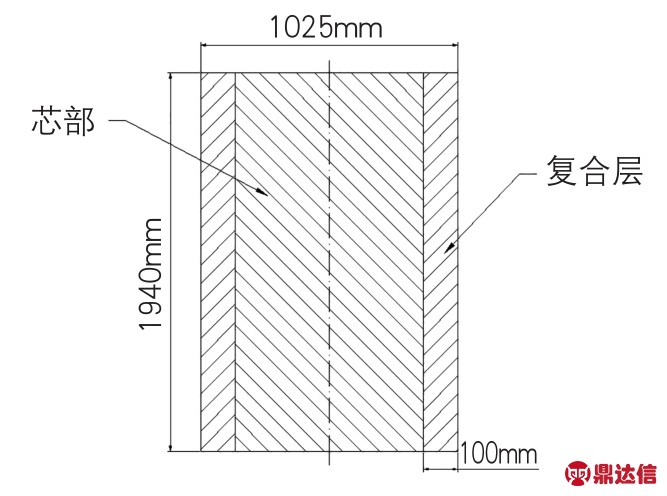
图1 芯部、复合层组坯后的纵向剖面图
Cr5/42CrMo真空锻造复合过程
首先通过机械打磨方式将芯部外表面、复合层内表面及两端端部打磨干净,保证其表面无尘土、油渍等污染物,将芯部嵌套在复合层内组合成坯料。将坯料转移到真空炉中进行预热,达到预热温度后保温一段时间取出,转移至真空电子束焊机的真空室内,待真空室达到预定真空度后,进行焊接密封,得到复合坯料。由于密封过程是在高真空环境下进行的,大大降低了界面在后续高温锻造过程中被氧化的可能性,将复合坯料进行高温加热,到达锻造温度后取出进行高温锻造,使界面达到完全冶金结合,锻后退火到室温,图2为芯部、复合层真空锻造复合过程示意图。
初始态(锻后退火态)复合轧辊试验结果与分析
界面微观组织
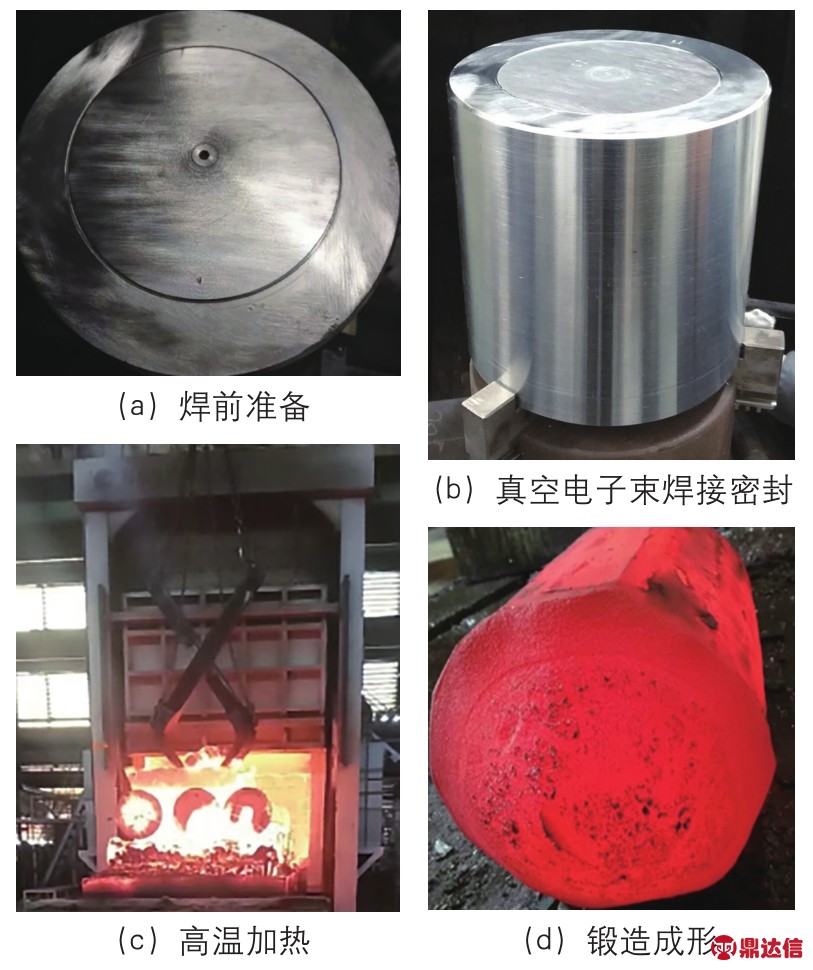
图2 真空锻造复合过程示意图
复合率是复合轧辊重要的性能指标,界面复合率通过超声波探伤对锻造退火态复合轧辊进行全面积超探,其复合率达到100%。在复合界面处用线切割的方法切取试样,试样尺寸15mm×10mm×10mm。试样经研磨、抛光、腐蚀后在奥林巴斯BX53M光学显微镜下进行微观形貌观察,复合界面的显微组织如图3所示。从图中可以看出,复合界面结合良好,未发现存在任何不结合点或微裂纹,双金属实现了完全冶金结合。
界面力学性能分析
工艺成功与否取决于两种材料的结合状态,为了验证初始态复合轧辊界面的结合情况,沿复合轧辊界面切取拉伸试样。
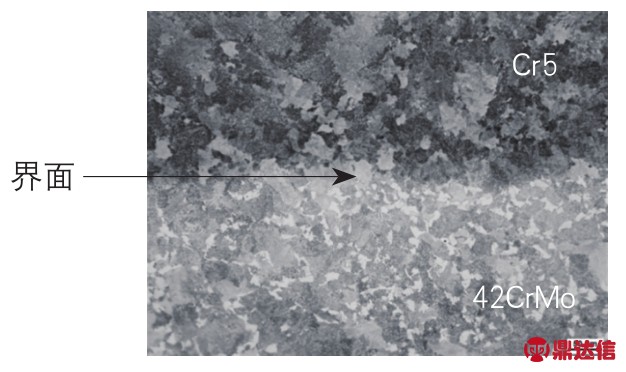
图3 退火态Cr5/42CrMo轧辊复合界面微观组织
表1 复合层的化学成分(质量分数%)

表2 拉伸试验结果

沿复合轧辊径向切取三个拉伸试样,且图中标记部位为芯部与复合层的界面,在4206-006实验机上进行拉伸试验。图4为试样拉伸断裂后的宏观形貌,通过观察可以看出,拉伸断裂位置均在芯部42CrMo一侧,说明界面的抗拉强度比芯部42CrMo好,且在断裂前都发生了颈缩,Cr5/42CrMo拉伸断裂试样的拉伸测量数据的各个参数见表2。
复合轧辊热处理及其性能检测结果
热处理工艺
复合轧辊的热处理是在QR-30型热处理炉内进行,其淬火和回火工艺如图5所示。
界面显微组织
将经过热处理后的试样预磨和抛光,然后在奥林巴斯BX53M金相显微镜下观察,复合界面显微组织如图6所示,与锻后退火态相比,两侧组织发生了明显变化,且能观察到明显中间扩散层。
界面结合区的显微硬度
为了研究轧辊界面结合处附近的显微硬度分布,采用FM-700显微硬度计对热处理后的复合轧辊界面及界面两侧进行硬度测量,测量结果如图7所示。
由图7可以看出,在复合界面Cr5一侧的显微硬度值接近670HV,而42CrMo的显微硬度接近440HV,界面中心的显微硬度值在510HV左右,符合轧辊使用要求。
结论
⑴通过真空锻造复合工艺实现了复合层与芯部的完全冶金结合,且复合率到达100%。
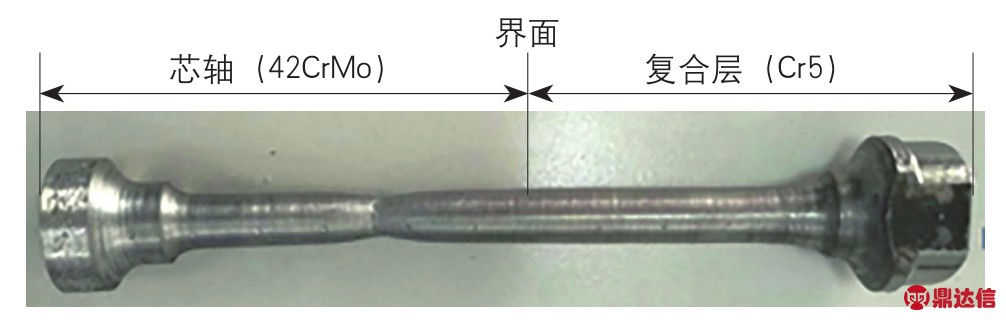
图4 Cr5/42CrMo拉伸断裂试样
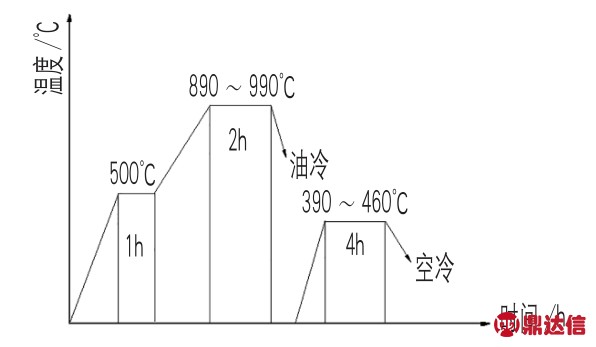
图5 Cr5/42CrMo复合轧辊淬火、回火工艺图
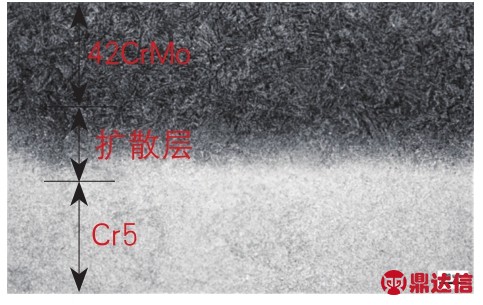
图6 复合轧辊热处理后的界面示意图
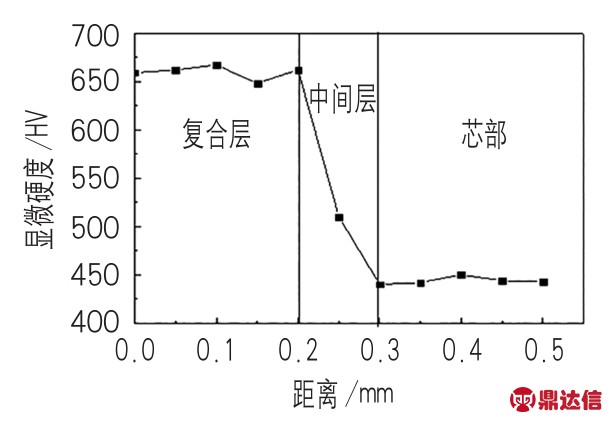
图7 Cr5/42CrMo界面附近显微硬度
⑵锻后退火态的复合轧辊拉伸试样均断裂在芯轴42CrMo一侧,其抗拉强度达到656.7MPa。
⑶经890~990℃淬火和390~460℃回火后,复合界面Cr5侧显微硬度接近670HV,42CrMo侧约为440HV,而界面中心的显微硬度值在510HV左右。
⑷真空锻造复合轧辊制备工艺的研究将为大型复合轧辊的制备提供广阔的空间。