0 引言
随着国民经济的发展和人民物质文化生活水平的不断提高,人们对电力的需求量愈来愈大,促使电力事业迅速发展,电网不断扩大,致使真空断路器的需求越来越大。目前,我国生产真空断路器的厂家较多,品种也比较繁杂,但真空断路器工频耐压的检测主要还是人工将断路器运到特定地点,然后手工接线进行检测,这种方式存在着效率低、劳动强度大、高压危险等缺点。
针对真空断路器结构复杂、沉重,制造、装配工艺要求高这些特点,设计了一条真空断路器自动生产检测线。在线自动检测就是在实际生产条件下,对生产装配过程中的真空断路器进行一系列性能测试。本文主要介绍了生产检测线中的工频耐压的检测设备。
在线检测,要求检测全部自动化,节拍与整线协调一致,且检测安全、可靠。
耐压测试项目:
1)在合闸状态,断路器整体对底盘车1分钟42kV工频耐压;
2)在分闸状态,静触头对动触头间1分钟42kV工频耐压;
3)在分闸状态,动触头对底盘车1分钟42kV工频耐压。
1 设备的工作流程及主要功能
1.1 工作流程
当断路器在输送线上传送到一次回路耐压测试工位时,由停止在输送线断开处的平移小车接料,小车上的工位阻挡器进行缓冲减速并挡停,小车上的顶升平移装置将断路器与工装板顶起后,平移小车自动移动到隔离安全网内的一次回路耐压测试平台处,将断路器连同工装板放置在测试工作台上,平移小车由测试工作台自动退回到接料处,电极转换机构将高压检测电极与断路器一次回路紧密连接,然后进行各项耐压检测。检测完毕,电极转换机构将高压测试电极与断路器一次回路断开。平移小车将断路器运回主输送线,如产品测试合格,则继续流向下一工位;不合格的产品,将在预留出口被自动送出。
1.2 主要功能
本设备自动化程度要求较高,测试的产品型号多,工作流程也比较复杂。主要功能如下:
1)具有自动和手动控制两种功能,并能实现二者的自由切换;2)接料、放料位置能够自动控制且停位准确;3)一次回路、二次回路自动接通,避免了人工接线;
4)实时监控产品检测情况,一旦出现异常,可准确定位故障点;
5)具有急停和复位功能;
6)安全性和可靠性高;
7)检测结果数据通过专用网络实时上传到上位机。
2 设备机械设计
本检测设备主要由平移小车、绝缘导轨、工频耐压测试台、一次回路电极接通机构、二次回路自动接通机构、高压隔离防护网等构成,如图1所示。
2.1 平移小车
原位设在与主输送线同一中心线上,接料平台采用滚筒,一端安装阻挡装置,由电机通过滚子链驱动带链轮的滚筒,接送断路器。接料后,举升装置将断路器顶起,另一电机驱动小车,将断路器从主线移送到耐压测试位。为防止小车意外冲出导轨,在原位、检测位两端安装行程限位开关和缓冲块,起到电控、机械双重保护作用。
2.2 一次回路电极接通机构
产品测试时,需接通一次回路以测试产品的耐压性能。接通电极在气缸的作用下,沿直线轴承运动,实现测试电极与产品电极的接触。由下行气缸推动静触头接通电极机构,以适应多种规格的产品,保证通电电极间安全间隔距离。
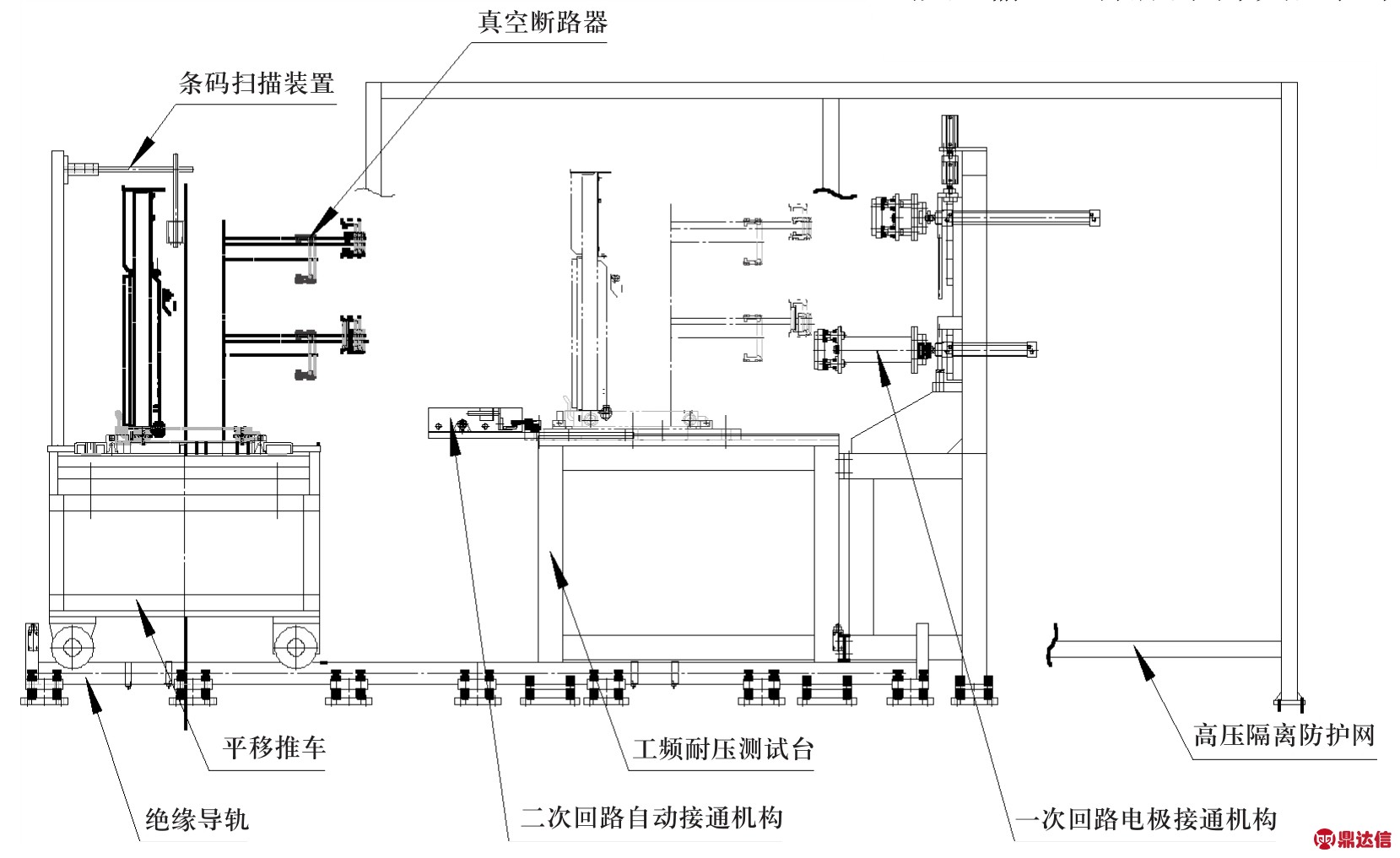
图1 耐压检测设备结构图
2.3 二次回路自动接通机构
产品在测试过程中,需要合闸储能时,由气缸推动插接机构,使插头对正工装板上的二次回路插座,插入气缸将二次回路接头插入工装板上的插座内,接通电气回路。
2.4 高压隔离防护网
工频耐压测试工位周围设置2米高的隔离防护网。隔离室靠近输送线一侧设置自动平移门,用于产品进出。为便于操作人员进出隔离室进行维护作业,在隔离室另一侧设置装有带安全锁的进出门,只有当安全锁锁上时高压发生器才能启动工作,当门打开时高压发生器不能启动,可防止检修进出门被意外开启。
2.5 设计中停位准确定位的考虑
断路器在主输送线处接料,在检测平台放料,在不增加定位机构的情况下,就要求平移小车停位准确。由于平移小车运送的断路器重量较大,由于惯性的作用很难保证位置的准确。在本设计中利用变频器控制电机减速停止,在接料和放料两个位置各安装两个位置传感器,且两个位置传感器分开一定距离,当小车送料到位时首先感应到第一个传感器,此时利用变频器使电机减速,当感应到第二个传感器时电机制动,小车停止确保产品上料的准确性。小车返回时相同。
3 设备电控设计
本系统采用日本OMRON公司的CP1H,是一款性价比高、功能完备的通用控制器。其特点是结构紧凑,自带24点输入、16点输出和4路模拟量输入。集成了开关量控制、模拟量控制、高速计数、4轴高速脉冲输出、串行通信等功能于一身,CP1H指令丰富,采用任务编程方式,并支持功能块编程方法使编程更加清楚、简便。CP1H取消了手持编程器配置,没有通常的外设接口,取而代之的是USB端口。支持 hostlink、nt link、 compobus/s、devicenet、 profibus-dp、controllerlink、 ethernet、 协议宏、modbus-rtu 等多种通讯方式及串行plc连接功能;支持cpm和cj1系列plc的扩展单元。
3.1 控制方式
该检测设备具有手动、自动两种控制方式。其中手动方式,可以通过触摸屏手动按钮对各执行机构(气缸、电机等)进行单独控制,以适用于调整、维修和紧急情况。一般使用自动方式,操作面板上的自动按钮选择自动挡,整套设备由PLC控制,按照前述工作流程进行检测。PLC控制系统逻辑图如图2所示:
3.2 程序设计思路
本控制系统采用顺序控制设计方法,根据上述的工作流程,细分为执行单一功能的子模块,按照检测的时间顺序和相互逻辑关系,主程序将依次调用子模块。
程序流程图如图3所示。
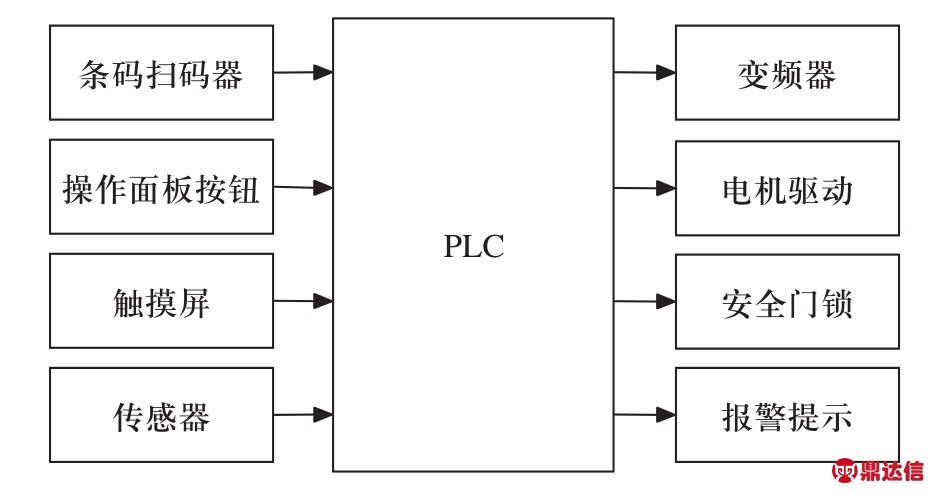
图2 PLC控制系统逻辑图
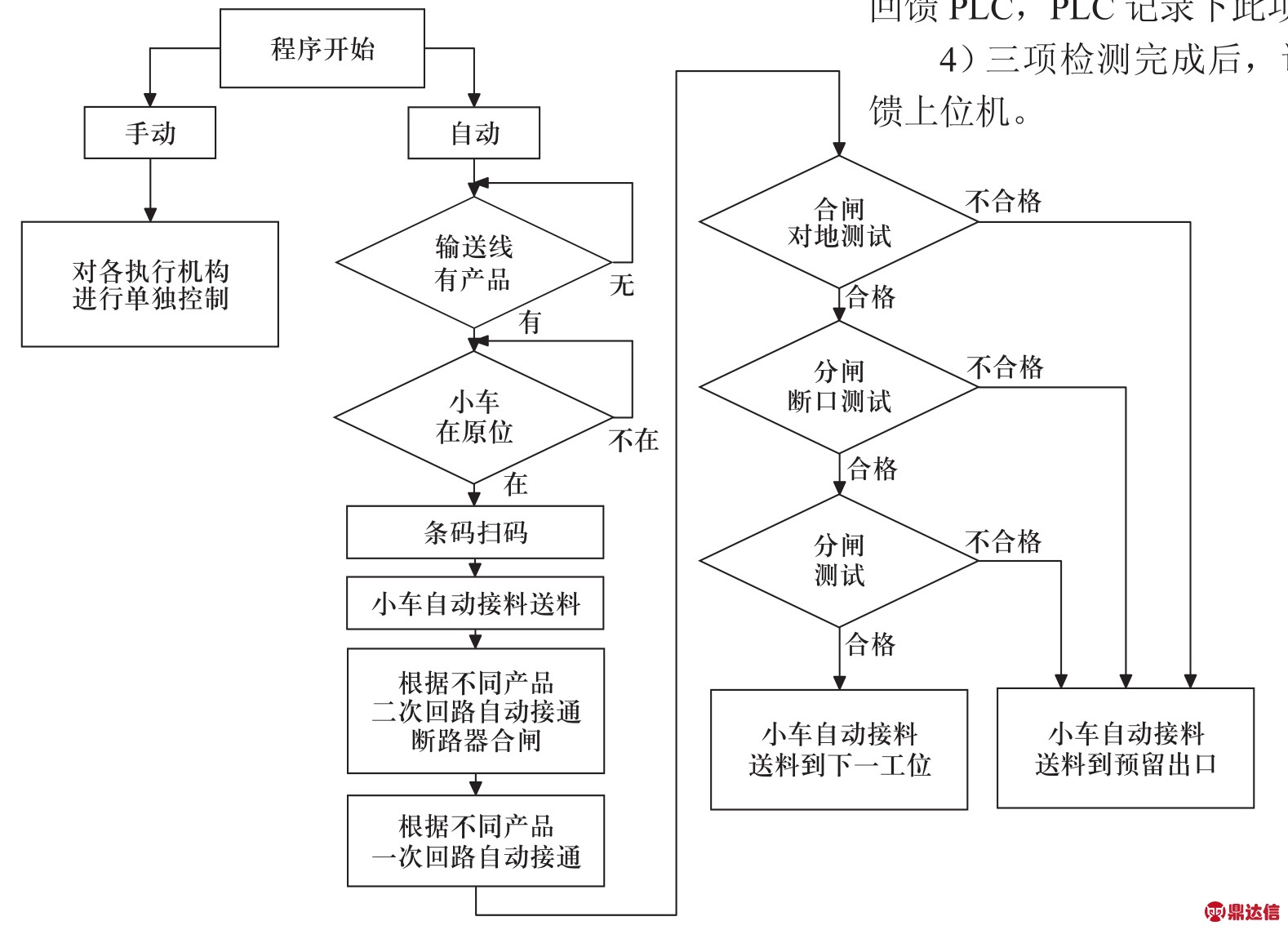
图3 主程序流程图
3.3 耐压测试说明
1)产品在合闸状态,由机械结构将产品的三个极柱的动触头短接并与高压测试仪的高压输出端的“+”连接,同时将高压输出端的“-”与产品的底板(底盘车)连接后,PLC通知高压测试仪开始测试,高压测试仪输出1分钟的测试电压,本项测试完成后,高压测试仪将测试结果(合格/不合格)回馈PLC,PLC记录下此项检测结果。
2)产品在分闸状态,由机械结构将产品的三个极柱的静触头短接并与高压测试仪的高压输出端的“-”连接,同时将产品的三个极柱的动触头短接并与高压测试仪的高压输出端的“+”连接后,PLC通知高压测试仪开始测试,高压测试仪输出1分钟的测试电压,本项测试完成后,高压测试仪将测试结果(合格/不合格)回馈PLC,PLC记录下此项检测结果。
3)产品在分闸状态,由机械结构将产品的三个极柱的动触头短接并与高压测试仪的高压输出端的“+”连接,将高压输出端的“-”与产品的底板(底盘车)连接后,PLC通知高压测试仪开始测试,高压测试仪输出1分钟的测试电压,本项测试完成后,高压测试仪将测试结果(合格/不合格)回馈PLC,PLC记录下此项检测结果。
4)三项检测完成后,设备将三项检测结果反
3.4 动作互锁的考虑
1)本系统所涉及的电机正、反转控制,均需互锁保护。
2)安全门锁锁上和高压发生器启动,进行互锁保护。当安全门被打开时,有红色报警灯闪烁提示,高压发生器无法启动,只有等安全门被锁上时,高压发生器才可以工作。
3)动作顺序的互锁,即先后动作互锁,没有前面的动作,后续的动作就无法执行。本系统中,小车不回到原位,输送线的产品就不可以放行。
3.5 故障应急处理
当遇到电气、机械故障或意外情况时,设备终止当前进行的动作并报警,同时在触摸屏上显示故障点,然后进入手动方式进行故障处理。例如:产品、小车不到位报警,检测电极接通机构故障,以及其他意外情况。
4 结束语
针对国内真空断路器生产迅猛发展现状,设计了一条断路器生产检测线,其融合了机械、电气、计算机、自动控制等技术,其中工频耐压检测使用一套OMRON PLC 进行控制,并配有weinview的10.4寸彩色触摸屏,利用条码扫描装置直接读取产品型号,能够实现断路器在生产检测线上的自动上下料和自动检测。与之前的人工手动接线检测相比,大大提高了工作效率和可靠性,降低了工人的劳动强度和工作环境的危险,从而降低了企业的生产成本。本检测线已在国内断路器生产厂家成功应用,基于其工作特点,它的应用前景也将非常广泛,类似的生产厂家均可适用。