〔摘 要〕 分析了某厂1号机组在基建调试中发生的锅炉汽水分离器贮水箱水位异常原因,提出了相应的改进措施并总结了经验教训,为热工调试人员快速处理类似事件提供借鉴。同时,提醒调试人员在基建调试期间要重视需要补偿测量参数的DCS校正逻辑及相关功能块参数的设置。
〔关键词〕 汽水分离器;贮水箱;水位异常;单室平衡容器差压水位计;补偿校正
0 引言
某厂2台350 MW超临界机组采用上海电气集团生产的SG-1131/25.73-M4422锅炉。在锅炉启动阶段和低于最低直流运行工况(30 % BMCR)时,水在水冷壁内吸热形成汽水混合物后汇集至水冷壁上集箱,通过上集箱引出管进入汽水分离器,在汽水分离器内汽水分离。分离后的蒸汽引至过热器,水则通过贮水箱、大气式扩容器至冷凝器,进行工质和热量的回收。
该贮水箱高度19.8 m,配置3个远传水位计,采用单室平衡容器差压测量方式,汽侧安装冷凝器,汽侧和水侧仪表管均安装保温装置和电伴热。电伴热为不锈钢铠装电伴热,采用数字式温控器控制,测温元件为PT100热电阻,安装在变送器保温柜出口约1.5 m处,位于仪表管水平段,距离仪表管垂直段约30 cm。
1 故障概述
2018-02-05,该厂1号机组基建整套启动并网,负荷为43 MW,主汽压力为13.1 MPa,主汽温度为434 ℃,锅炉汽水分离器贮水箱水位2在DCS显示11.1 m,水位1,3显示约10.5 m,持续20 min基本没有变化,直至主汽温低保护动作,触发MFT,锅炉灭火,机组停运。
结合运行工况及相关参数,相关专业人员分析认为当时的贮水箱水位应为满水位,水位测量存在较大的误差。
2 检查分析
2.1 水位变送器现场检查
由于3个水位测量显示基本一致,可首先排除变送器本身故障以及仪表取样管路泄漏这些原因。
(1) 锅炉停炉后,将分离器贮水箱放水完毕,现场对3个变送器的水侧放水。变送器1,3有少量气体排出后出水,水质较差,而后变为蒸汽;变送器2放出的是蒸汽带水。由此可判断水位测量变送器的水侧仪表管存在蒸汽,水侧压力(负压侧)较实际压力偏小,导致变送器测量差压变大,显示水位较实际真实水位低。推断水侧仪表管存在蒸汽的原因是:水侧仪表管内的水被电伴热加热汽化,在水侧仪表管内产生汽阻,导致差压变大,从而使显示水位低于真实水位。
(2) 对变送器取样管进行静压检查,发现实际静压为25 MPa,而变送器铭牌标示静压为17.3 MPa,变送器测量精度受到影响,造成显示水位低于真实水位。
(3) 检查水位测量装置保温情况,发现冷凝罐和冷凝罐下正压侧取样管有保温装置,影响了正压侧凝结水冷凝,造成测量误差。
(4) 检查水位测量装置及取样管路的伴热情况,发现水位显示异常时,电伴热控制器设置停运温度为30 ℃,测量元件温度为16 ℃,取样管伴热效果不到位,影响测量结果。水位测量正负压侧取样管路伴热和温度设置不合理,造成水位计负压侧高温,使负压侧仪表管内水的密度变小,影响变送器测量的准确性,导致变送器测量值显示偏小。
(5) 水位变送器投运前,未进行冲洗、排污、排气等检查,引起测量误差。因为投运前检查工作不到位,导致取样管里有气泡或者杂质,造成取样管气塞或者堵塞。
2.2 水位补偿公式逻辑组态检查
2.2.1 水位补偿公式
水位异常时,DCS组态中的水位补偿公式:
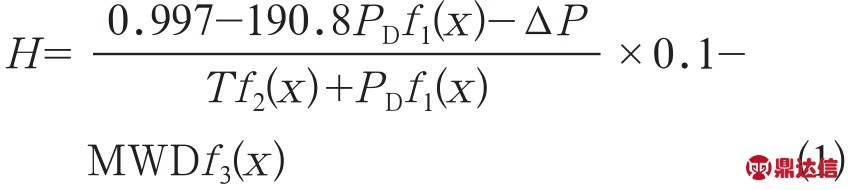
式中:PD——分离器压力,MPa;PDf1(x)——分离器压力补偿函数;T——补偿温度,℃;Tf2(x)——温度补偿函数;MWDf3(x)——机组功率补偿函数。各参数补偿函数如表1-3所示。
表1 分离器压力补偿函数

表2 温度补偿函数

表3 机组功率补偿函数

由式(1)可知:水位异常时,机组功率值为43 MW,根据表3可知,机组功率补偿函数MWDf3(x)输出值为0,初步分析水位误差主要是为压力、温度补偿不当产生的。
检查DCS中锅炉分离器贮水箱水位计算逻辑及各功能块的参数设置发现,温度补偿逻辑中品质检测功能块的量程上限设置为100 ℃(默认值),使得参与补偿的温度限制在100 ℃内。同时,温度补偿逻辑中品质检测功能块的速率报警限制设置为0 ℃,速率报警时间范围设置为2 s,超速率报警持续时间设置为5 s。
这种参数设置可以实现的功能是:在2 s内,温度变化超过0 ℃就会触发5 s坏质量信号;若在2 s内温度仍有变化,仍存在坏质量,则输出的补偿温度一直维持坏质量前一刻的温度值。这就造成该温度补偿值一直保持在机组点火前的温度值。但当水位异常时,实际温度已经达到330 ℃,使补偿后的计算密度远大于实际密度,进而导致水位计算值偏小。
2.3 仿真试验及综合分析
(1) 输入水位异常时的水位差压实际值、参与补偿的分离器压力实际值和温度实际值330 ℃进行仿真测试,水位显示为15.44 m,而当时工况水位显示10.5 m,所以因温度补偿逻辑中品质检测功能块参数设置不当,引起贮水箱水位显示值较真实的水位值偏低约5 m。
(2) 仿真时发现,当时工况下的压力、温度补偿密度校正计算系数较标准密度表计算校正系数偏大,仿真计算校正系统偏大约0.1,引起贮水箱水位显示值较真实水位偏低约1.7 m。进一步检查发现,温度校正时公式(1)的分母在DCS组态时使用了加法块。
(3) 根据伴热电缆性质、温度设置、正负压侧取样管伴热和保温情况分析,由于高温导致水位负压侧仪表管内水柱密度变小,影响变送器测量的准确性,引起变送器测量值较真实值偏大,水位计算显示值较实际水位低约1 m。
(4) 水位计投运前未进行取样管排空,负压侧取样管内存有空气气泡,变送器铭牌标示静压与变送器取样管实测静压不一致。这也会引起变送器测量值偏低。
综上所述,累计偏差约8 m,导致当时工况下的实际水位约为19 m,而DCS组态计算输出显示只有10.5 m。产生偏差较大的原因是温度补偿逻辑中品质检测功能块参数设置不当。
3 改进措施
(1) 更换贮水箱水位测量变送器,保证变送器能耐受取样管静压要求,保证其测量精度。
(2) 拆除冷凝罐和冷凝罐下正压侧取样管的保温层,减少测量误差。
(3) 检查伴热系统投用情况,在满足防冻的前提下,伴热投运温度设置为低于5 ℃,停运温度设置为20 ℃,确保不会因加热温度过高导致水密度影响水位测量结果,确保测量的准确性。
(4) 修改温度补偿逻辑中品质检测功能块参数,量程上限由100 ℃修改为500 ℃,速率报警限制由0 ℃修改为16 ℃。
(5) 核对贮水箱图纸和水位计算书,确保计算公式与本项目所配套的汽水分离器及贮水箱相符。水位补偿正确公式为:
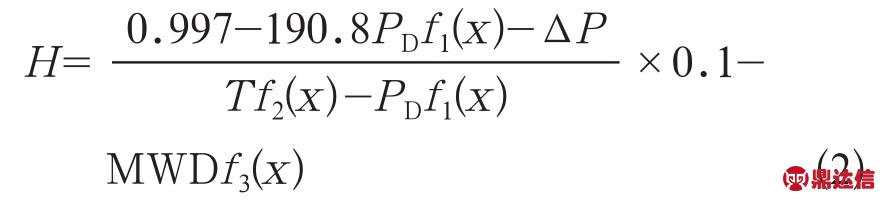
(6) 根据公式(2)修改DCS组态,将温度校正回路中的加法模块修改为减法模块。
4 经验教训
(1) 按照国能安全〔2014〕161号《防止电力生产事故的二十五项重点要求》6.4.6条要求,严格按照运行规程及各项制度对水位计及其测量系统进行检查及维护。机组启动调试时,应对分离器贮水箱水位校正补偿方法进行校对、验证,并进行水位热态调整及校核。新机组验收时,应附加水位计安装、调试及试运专项报告,并将其列入验收主要项目之一。
(2) 基建机组调试时,应重视需要进行补偿的测量参数(如汽包或分离器水位、主汽流量、风量等)的补偿公式及组态逻辑中相关参数设置的正确性。
(3) 锅炉分离器贮水箱水位(差压变送器)一般应采用压力补偿。同时,水位测量也应充分考虑平衡容器的温度变化造成的影响,必要时采用补偿措施,但参与补偿的压力和温度测点分别至少配置2点。DCS组态中增加测量信号故障品质检测和冗余信号选择判断逻辑,使得压力、温度信号可靠参与补偿,保证差压水位的计算准确性及实际水位的正确性。
(4) 当DCS中函数块可设置折线点较少时,尽量采用多点分段拟合曲线函数补偿方式,使每个密度补偿参数最接近其实际工况下的密度,达到准确测量贮水箱水位的目的。
(5) 锅炉分离器贮水箱水位测量系统,应采取正确的保温、伴热及防冻措施,以保证汽包水位测量系统的正常运行及正确性。
(6) 锅炉分离器贮水箱水位测量变送器选型时,要注意与水位测量取样管的静压一致,以保证水位变送器的测量精度和水位测量的准确性。
5 结语
经过现场测试、在实施DCS组态逻辑和参数优化等措施后,该厂1号机组锅炉分离器贮水箱水位在机组再次启动调试时显示已正常。同时,本措施为避免该类型异常事件的发生及快速有效处理,具有一定的指导意义。