摘 要 当前,入口流量对油水分离器分离性能的影响主要局限于稳态分析,忽视了瞬时流速的脉动变化对分离效率和压降的影响,难以确定脉动流对分离性能的影响程度。为解决这一问题,结合生产实际,开展了脉动流对分离效率和压降影响程度的数值模拟和实验研究。以周期1s、脉动峰值0.1m/s的脉动流速和分流比为输入变量,探讨脉动流对速度、压降和油相体积分数的影响,得出了确切值,并对分离效率和溢流压降进行了实验验证。结果表明:脉动流引发的脉动合速度和切向速度的波动范围均在10%以内,溢流压降平均值的波动范围在7%以下,分离效率提高0.3%左右;脉动流产生的速度和压降的增量随着入口脉动幅值的变化而变化;脉动流对分离器分离性能的影响程度较弱,油水分离器对脉动流的适应性较强;脉动条件下的油水分离是一个动态累积过程。
关键词 水力旋流器 油水分离 脉动流 分离性能 瞬态模拟
轴流式螺旋流道型水力旋流器以其径向空间小、结构紧凑、流场稳定、分离效率高及能耗低等优点[1],得到学者的认可和业界的青睐,在油水分离领域的应用正在逐步深入。影响轴流式分离器分离性能的主要因素可分为结构参数、操作参数(流量、分流比)和介质参数三大类[2]。当其他参数确定后,操作参数即成为主要因素。匹配合适的操作参数,是发挥旋流器最佳分离性能的必要条件。
目前,有关流速对分离性能影响的模拟和实验,不乏稳态下的研究[3~5],但瞬态下的探究并不多见。一般认为,脉动流会对分离效果产生不利影响。倪玲英开展了断续流对分离性能影响的实验研究,指出分离效率下降幅度在5%以内[6];赵立新等的模拟和实验研究表明,脉动流可促进固体颗粒的分离,在含气条件下脉动流对分离性能的影响较弱[7,8];在较低流速和较大入口流量下的脉动流可以改善颗粒分离效果。
实际工况中,旋流器的进口流速常常是脉动变化的。电力系统或用电高峰期的电压不稳定等因素,致使旋流器的增压泵转速不稳定,往往呈周期性波动,由此在旋流器入口形成脉动流。再者,待分离液的油相浓度并非都是均一稳定的。由于入口流量或油相浓度变化的周期越大,越接近稳定流,对分离效率的影响越小,故取较小的周期来评估脉动流对分离效率的影响具有积极意义。笔者为探究轴流式油水分离器在周期性脉动流条件下的适应性,开展数值模拟和实验研究,分析油水分离器的压力场、速度场和分离效率的脉动规律,以确定脉动流对分离性能的影响程度。
1 计算域模型和模拟参数设置
1.1 几何模型
轴流式油水分离器的主要结构由入口段L1、螺旋流道L2、旋流腔L3、锥管段L4及尾管段L5等部分组成。其结构示意图和参数分别见图1和表1。其中,Do为尾管段直径,Dc为公称直径,θ为内锥角。
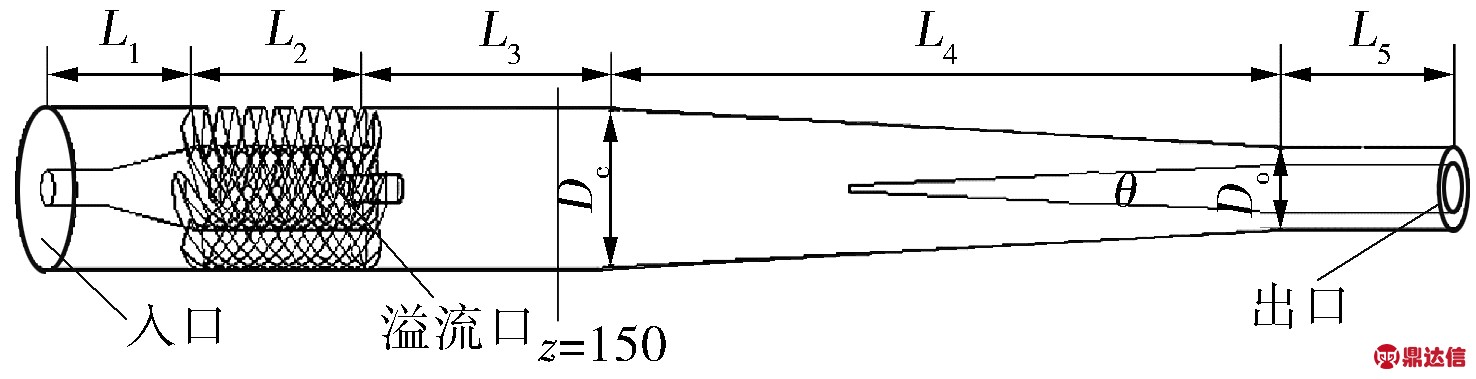
图1 分离器结构示意图 表1 分离器主要结构尺寸

1.2 网格划分
与四面体相比,六面体网格的数量少、计算时间短、离散误差较小,计算时六面体单元内部可以储存多个应力和应变积分点,可以准确描述梯度变化区域,对雷诺应力模型的适应性亦较好[9]。鉴于螺旋流道和内部锥角均具有较大的曲率,为顺应流体流动方向,增强在应变梯度变化大的变形部位的适应性,全部采用ICEM划分六面体网格,并在曲率大的部位适当加密,以确保敏感部位的网格数量,如图2所示。
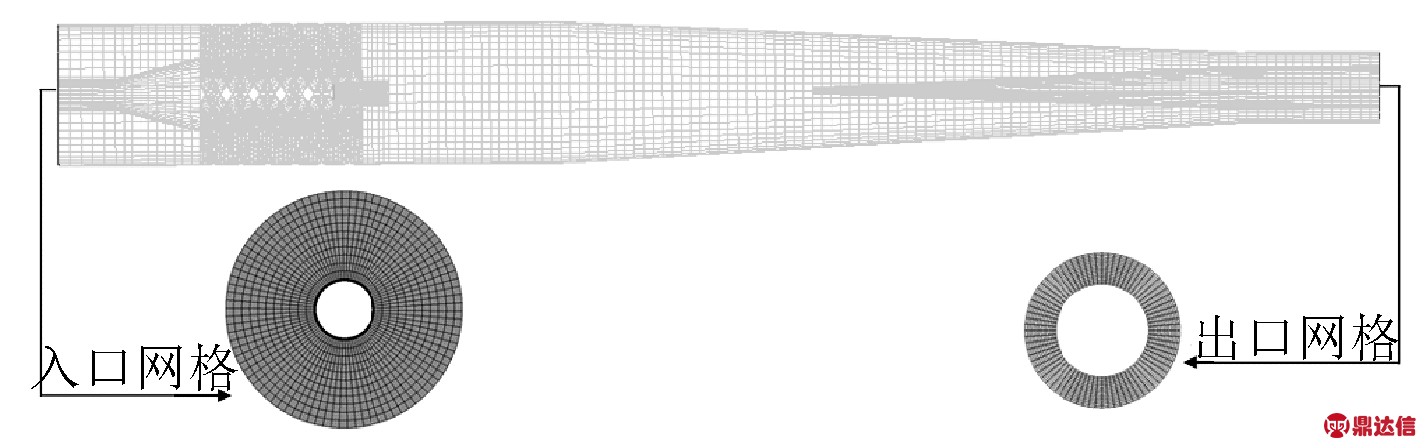
图2 旋流器网格示意图
1.3 网格与时间步长的无关性验证
为验证网格的无关性和时间步长的独立性,在z=150mm处(图1)取一个平行于xoy面的截面,并在x轴正向依次取a、b、c 3个点,其坐标分别为(1.37,0,150)、(1.74,0,150)、(2.19,0,150)。具体位置如图3所示。经计算,在1.2s时,脉动流已流过z平面,模拟中监测油相体积分数,比较1.2s时3个点的油相变化。
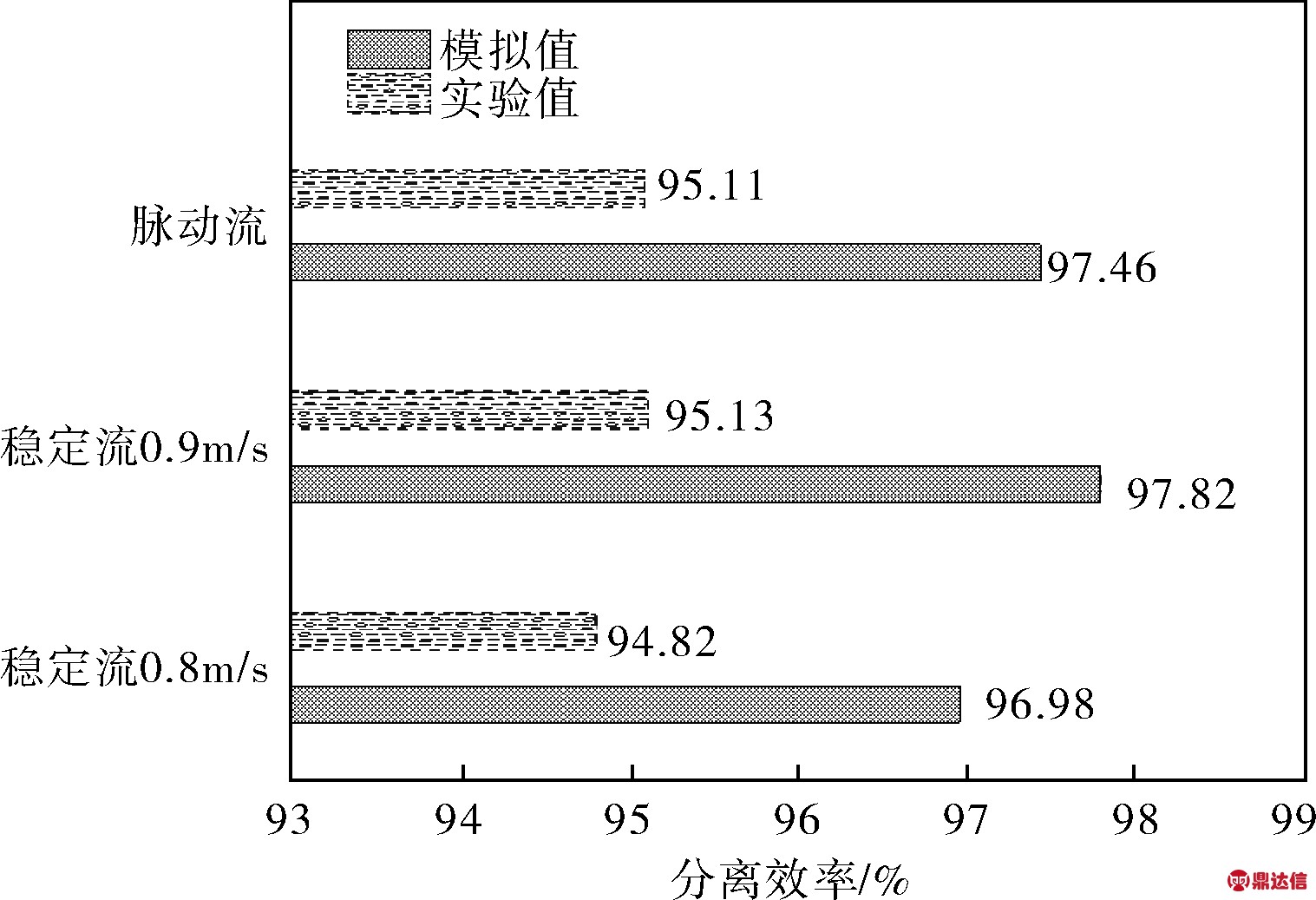
图3 网格无关性的截面及测试点位置示意图
表2为3种密度下的网格信息。当网格数量超过网格一时,a监测点的油相体积分数基本不发生变化,故网格一完全能够满足网格无关性的要求。
表2 网格数量表
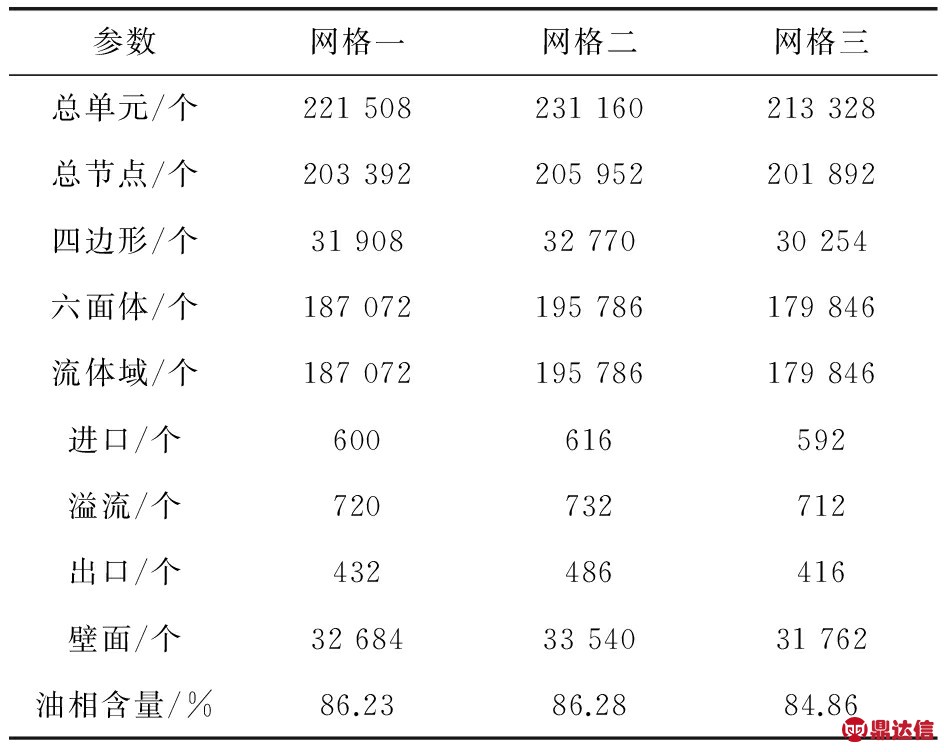
在瞬态模拟中,若时间步长过大,就会导致计算发散,反之,时间步长过小,则会增大离散的时间[10,11];因此分别选取时间步长为0.025、0.050、0.100、0.200s进行验证,测得1.2s时刻的3个监测点的油相体积分数变化如图4所示,可以看出,当时间步长为0.025s和0.050s时,b、c两点的油相体积分数基本不变;随着时间步长的减少,a点的油相变化越来越小,在0.050s时近似趋于稳定,故取0.050s作为离散时间步长。
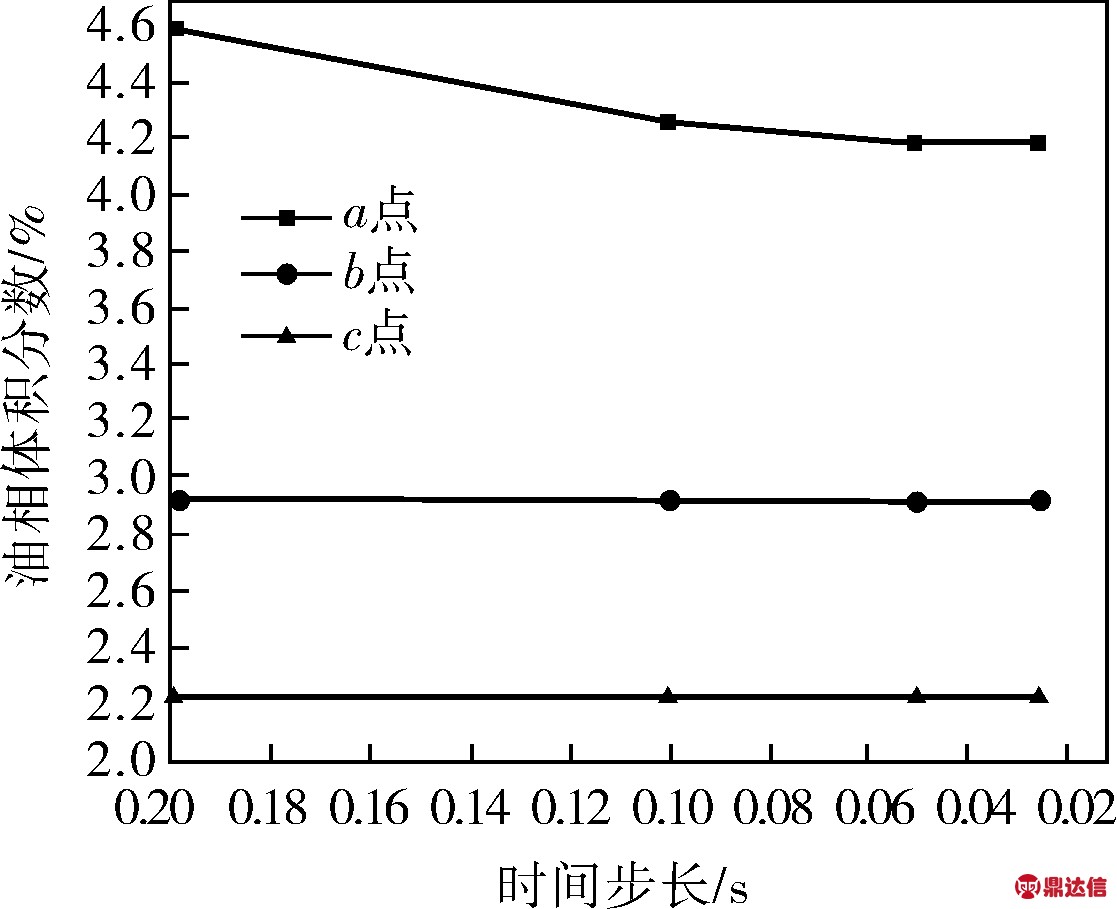
图4 时间步长独立性验证结果
1.4 数值模拟设置
模拟介质为油水两相流,主相为水,次相为油。油相体积分数为2%,水相为98%。物性参数为:水相密度ρ=998.2kg/m3;油滴粒径为0.4mm,粘度μ=1.003Pa·s;油相密度889kg/m3,粘度μ′=1.06mPa·s。
模拟软件为ANSYS Fluent 16.0,湍流模型选用雷诺应力模型(RSM)。因雷诺应力模型能够适应流体密度的变化、流场的旋涡弯曲和张力的快速变化[12],能够模拟复杂流动的时均量和全部的雷诺应力[13],特别适合于流线强烈弯曲、旋涡和旋转的三维螺旋流动[14]。在Fluent提供的3种多相流(VOF、Mixture、Eulerian)模型中,混合模型可以模拟具有相同和不同速度的各相间的耦合,可求解混合相的动量、连续性和能量方程,第2项的体积分数方程等[15],故多相流选用混合模型。离散精度控制在10-7,采用压力-速度耦合的SIMPLE算法、精度较高的QUICK格式、适合螺旋流的压力项PRESTO!,以确保离散的准确性。
1.5 边界条件设置
入口边界为速度入口,出口为自由出流。底流口分流比为80%。溢流口为自由出流,溢流口分流比为20%。分离器壁面按光滑无滑移壁面边界处理。
入口稳定流速v分别为0.8、0.9m/s。脉动流速和周期是参照增压泵的实际转速确定的,设置周期分别为1、4s,周期为1s的脉动时间段为0.4s,水平稳定时间段为0.6s。在v=0.8m/s水平段的基础上脉动幅值为0.1m/s,即脉动流瞬时最大速度为0.9m/s。周期为4s的脉动时间段为1.5s,水平稳定时间段为2.5s。图5为二者在两个周期内的脉动流速曲线。
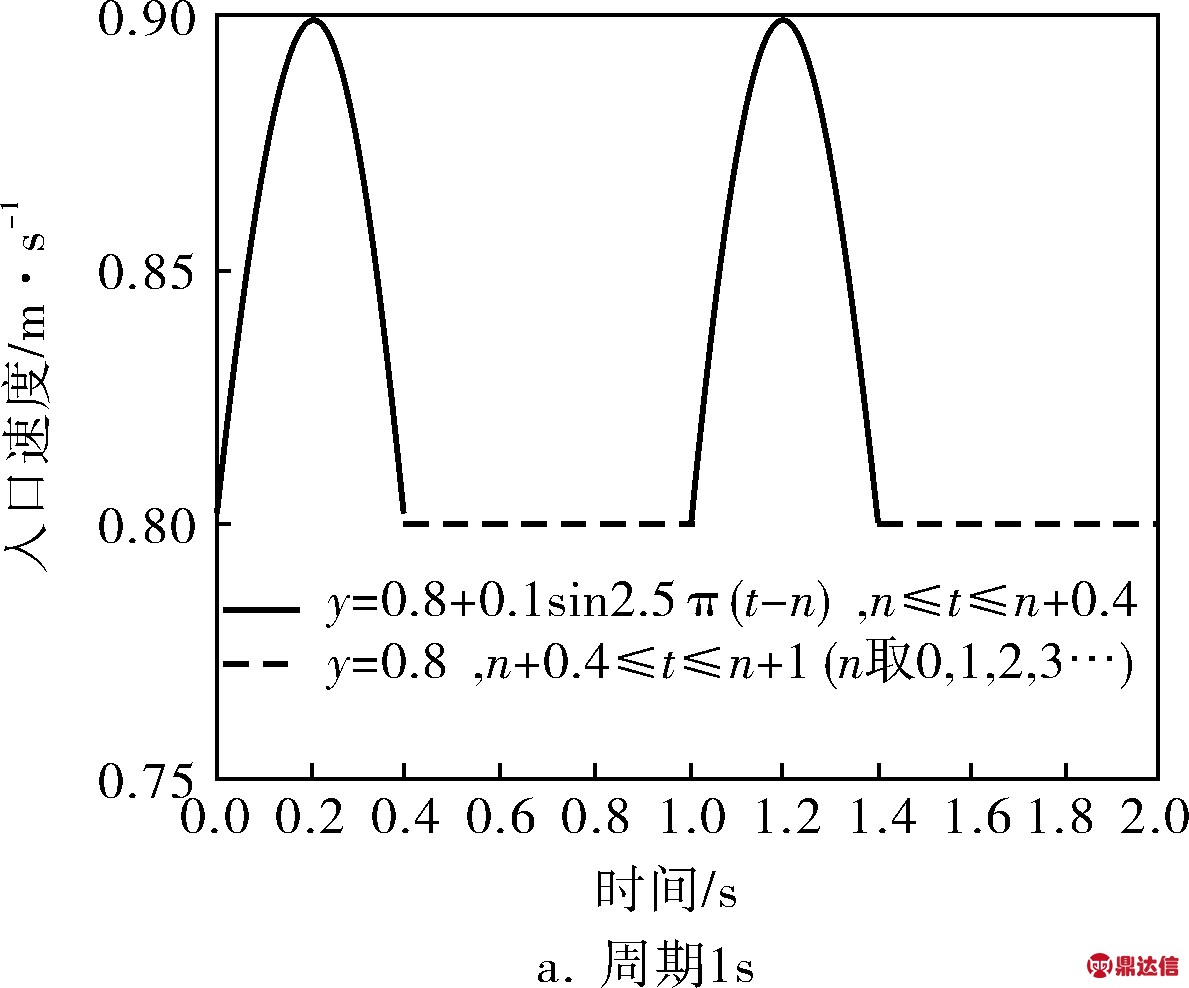
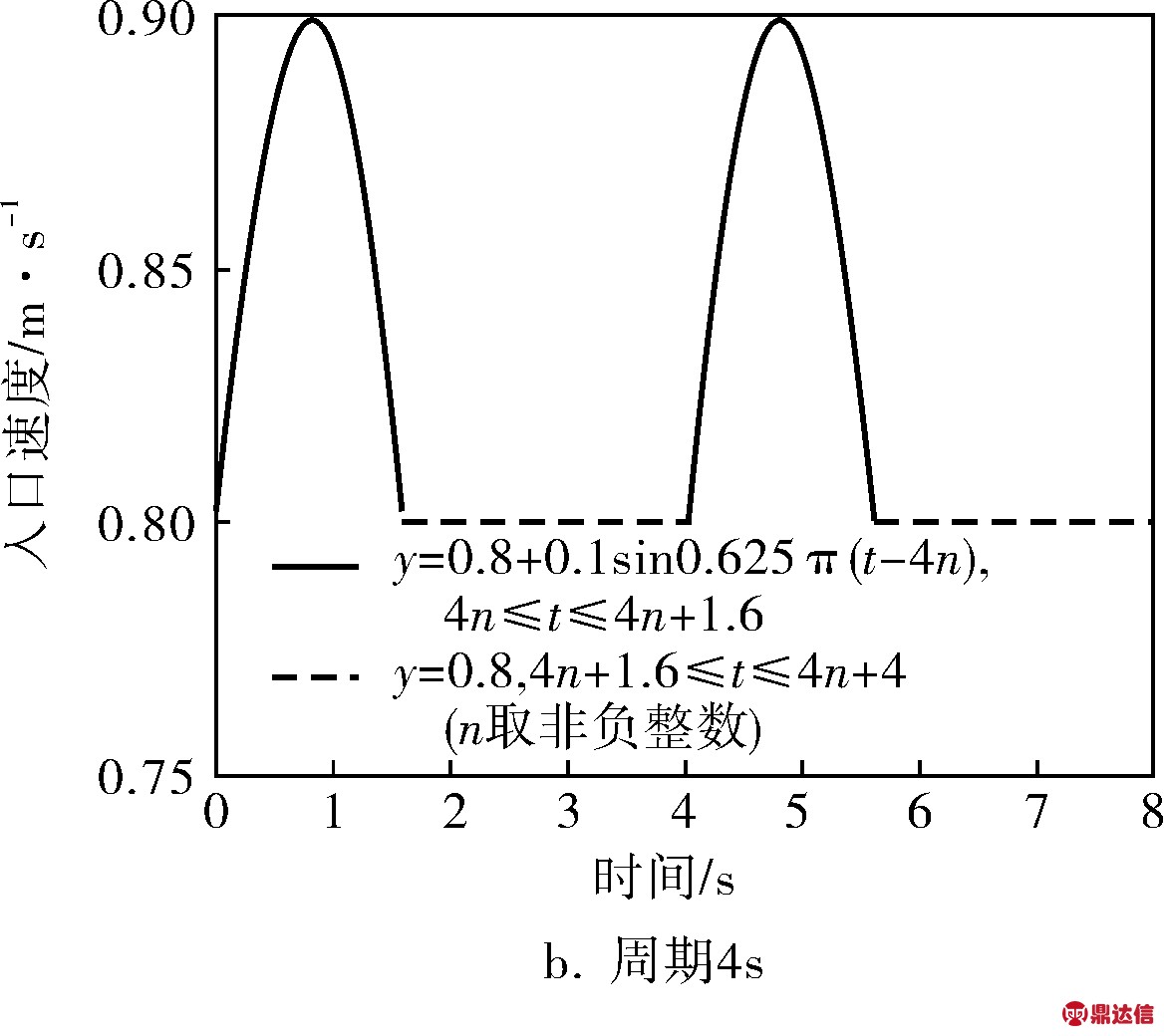
图5 脉动流速曲线
脉动油相浓度是以1.0%的油相体积分数作为基础进行脉动的,脉动振幅为0.01,周期分别为1s和4s。最大油相含量为2.0%,水平稳定时间和脉动时间的设定与脉动速度时间相同。图6为二者在两个周期内的油相体积分数变化图像。
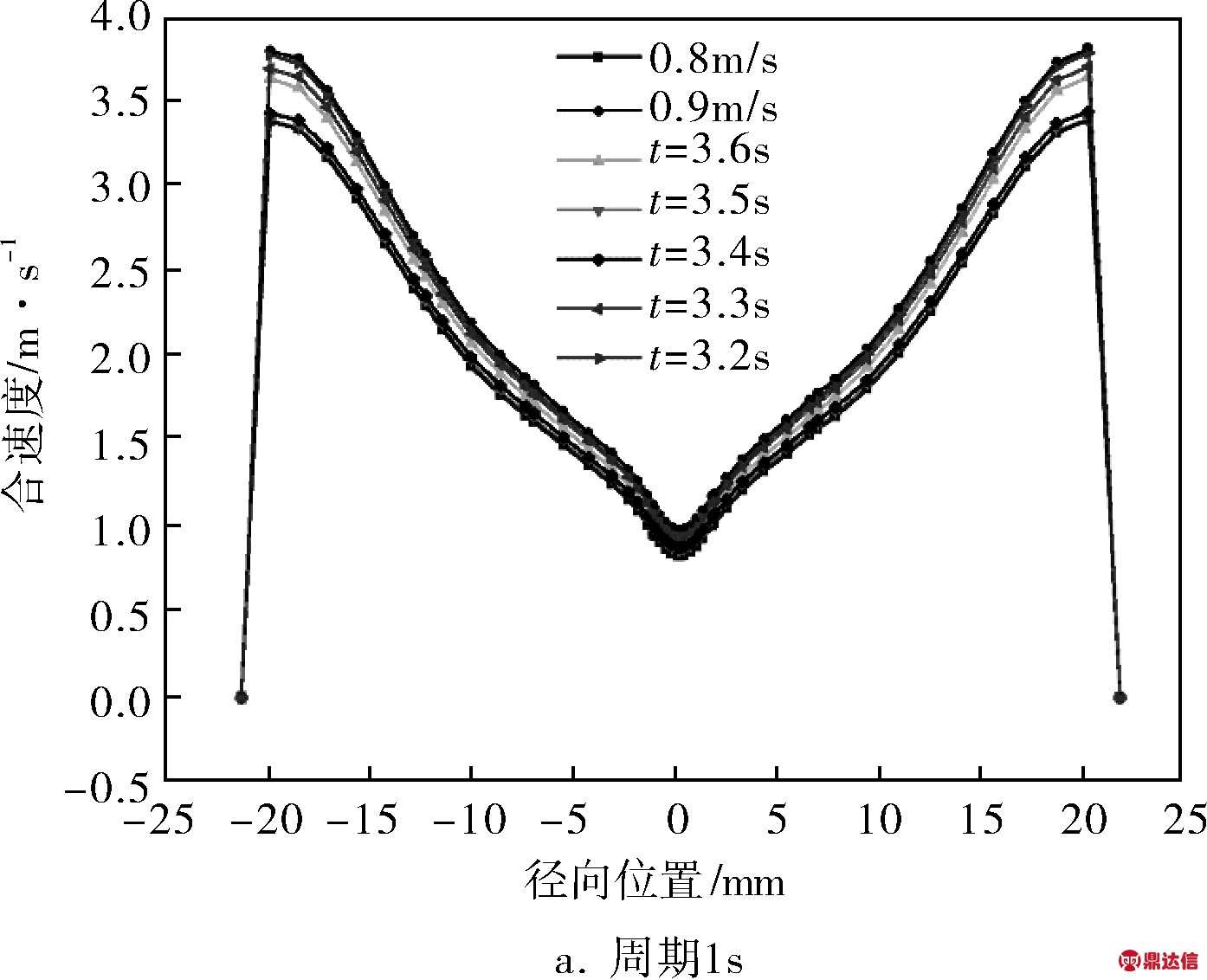
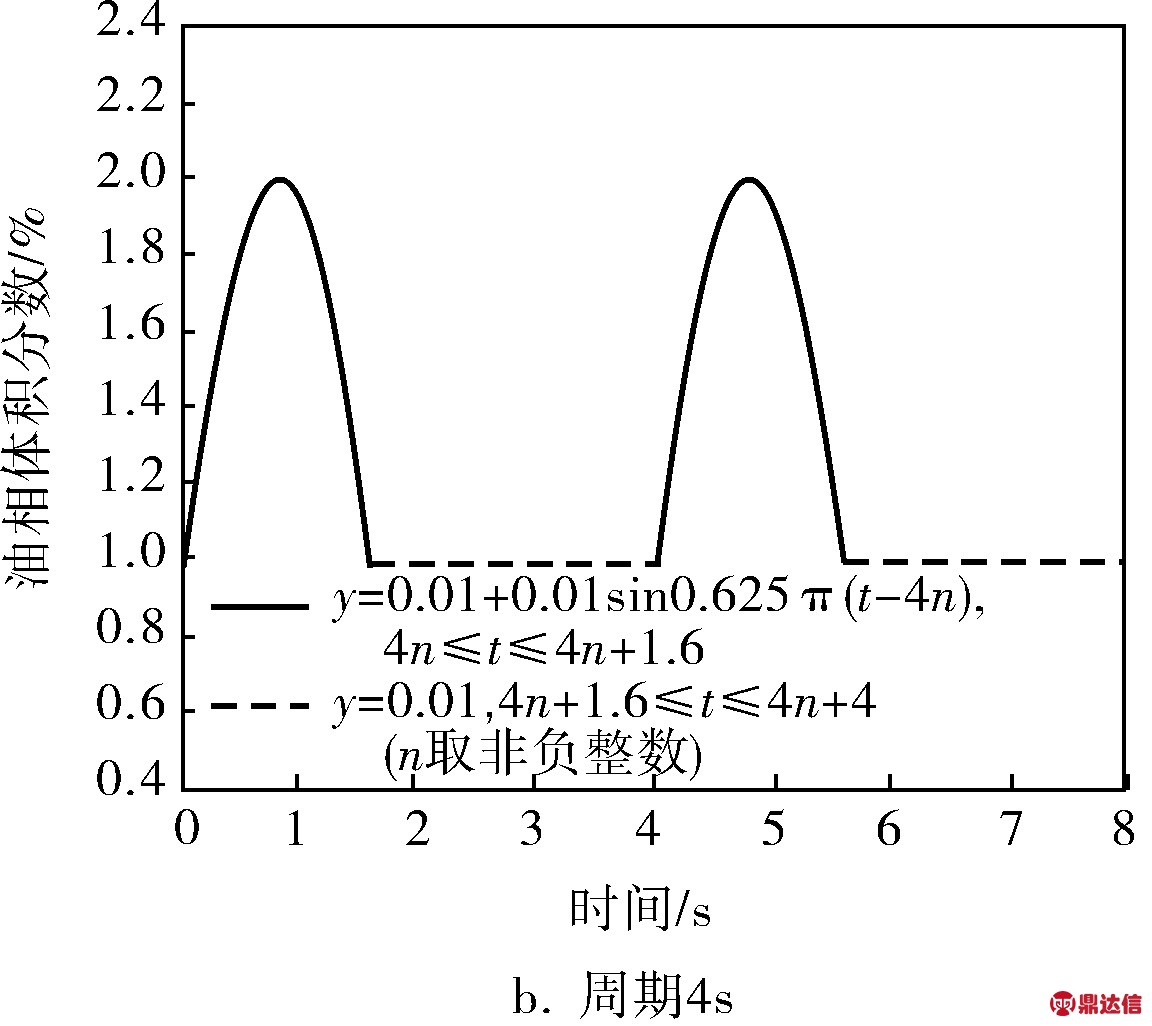
图6 脉动油相曲线
2 脉动流场分析
在瞬态模拟中,确保每个时间步长内均达到收敛,监测溢流口的油相质量流率可得图7。
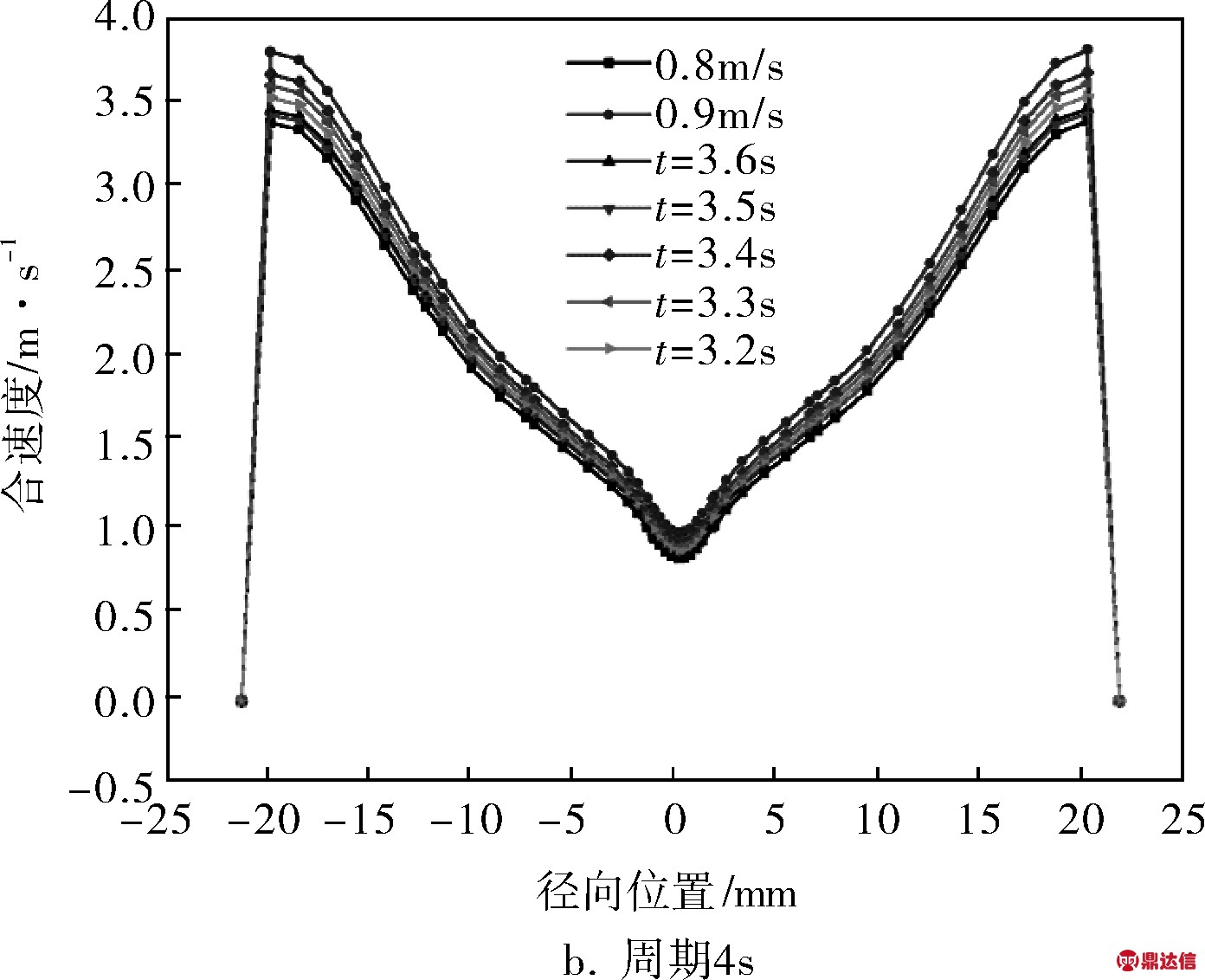
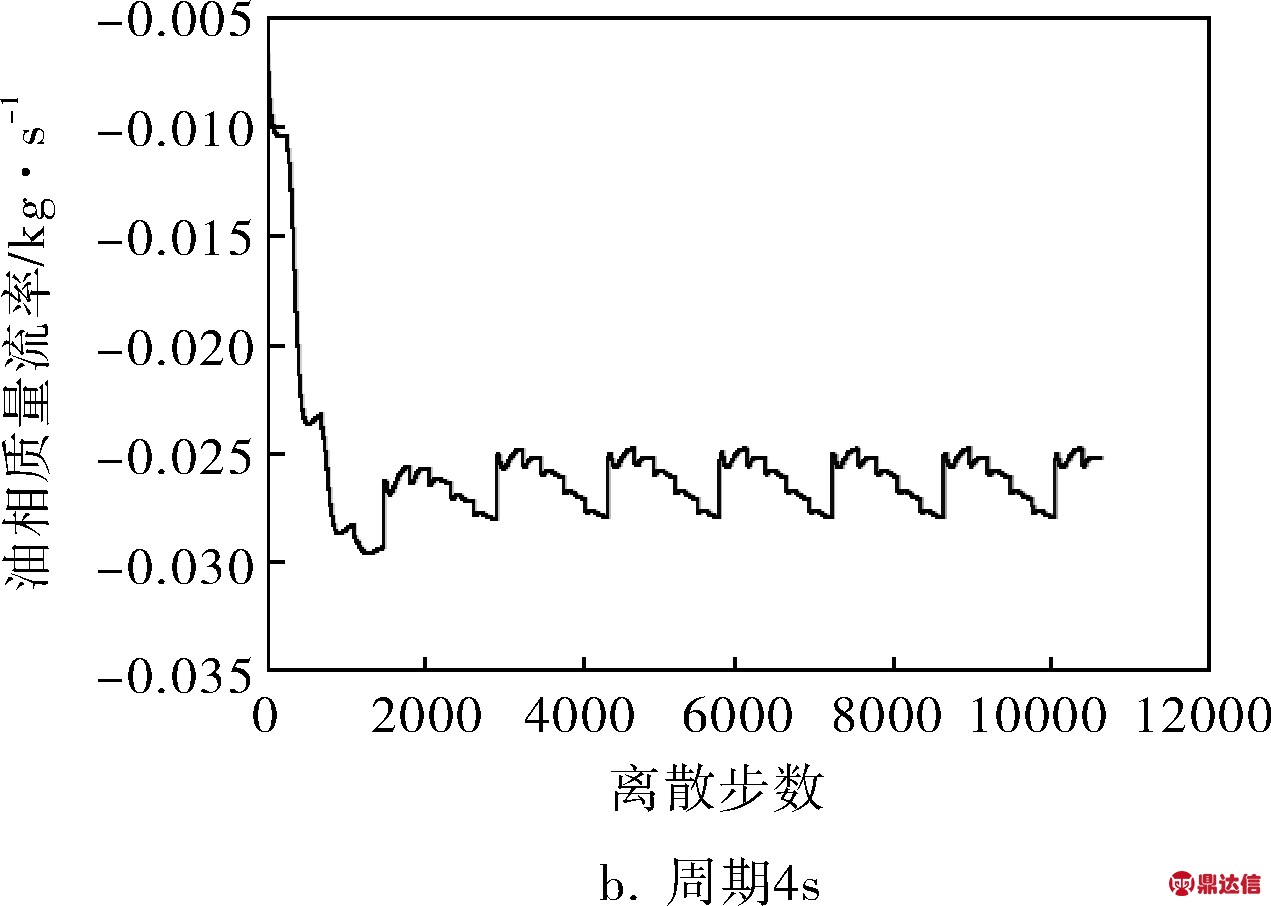
图7 溢流口的油相变化示意图
由图7可知,瞬态离散稳定后,在油水分离过程中,周期为1s的油相析出呈现明显的周期变化的“几”字形,表明入口脉动流量的波动导致了溢流油相的规律性变化。由此可以推知旋流体的瞬时切向速度与瞬时分离效率亦呈周期变化的趋势。而周期为4s的油相“几”字形规律并不明显。周期为1s时,3.2~3.6s间的脉动流速度值大致处于从最大值(0.9m/s)逐渐减小至最小值(0.8m/s)的下降段,分析Fluent离散数值规律可知,在各个周期内的脉动速度下降段,每5次的离散数值是大致相等的,其中的流场变化具有一定的代表性。故以下探讨均以周期为1s时的3.2~3.6s间的流场特性为主。
2.1 速度对比
溢流分流比为20%时,z=150mm截面处合速度的脉动变化曲线如图8所示。与稳定流类似,脉动流在旋流器内形成的旋流速度与切向速度均呈现“M”形的规律性变化,且波动范围变化不大,介于0.8~0.9m/s之间。
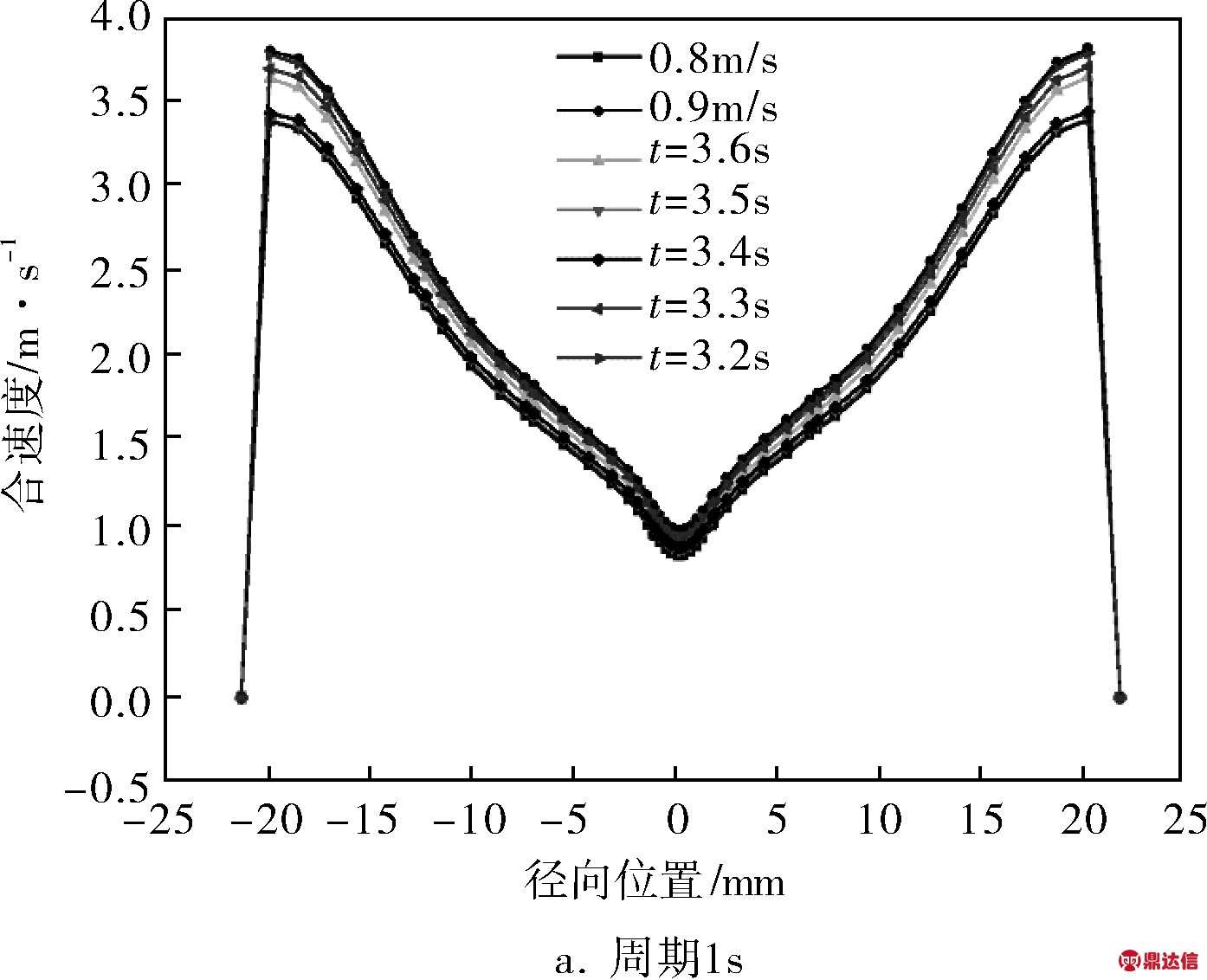
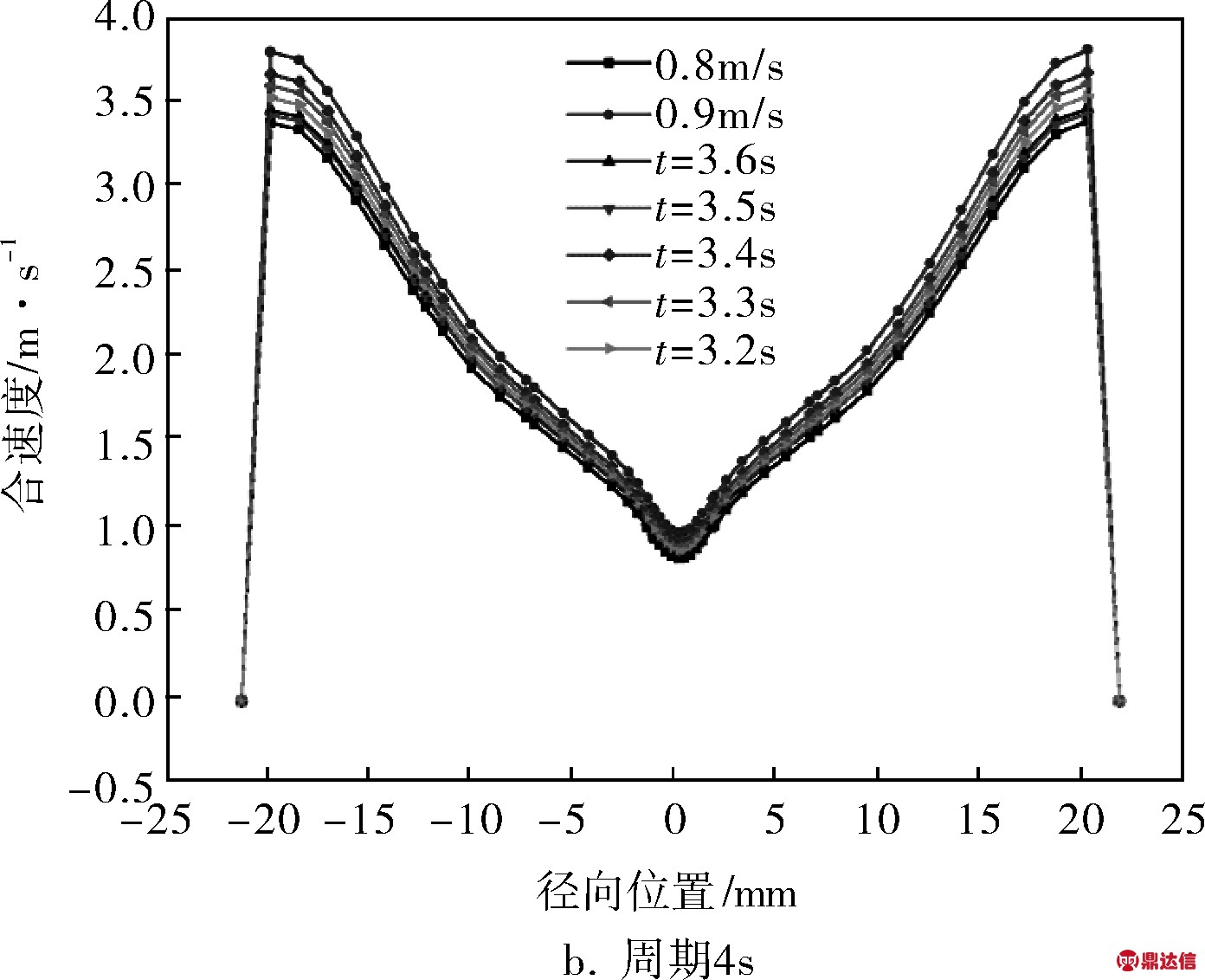
图8 z=150mm处的合速度的脉动变化曲线
z=150mm截面处切向脉动速度的变化曲线如图9所示。在3.2~3.6s时间段,进口的瞬时速度处于下降段,是逐渐变小的,对应的速度和切向速度曲线位置亦是逐一向下排列的、随之减小的,均位于0.8~0.9m/s产生的速度和切向速度曲线之间。经计算,当入口脉动速度幅值为0.1m/s时,周期为1s的脉动流引起的切向速度的波动幅度在10%以内,周期为4s的脉动流引起的切向速度的波动幅度在8%以内,且周期为4s的速度和切向速度值均比1s时的小,数值接近0.8m/s产生的速度和切向速度值。这说明脉动周期越大,旋流器内的脉动速度越接近于稳定流。与稳定流类似,所有切向速度从轴心到壁面处逐渐增大,之后在壁面处重合减小至0。从瞬态角度看来,切向速度的波动会导致油水分离性能的不稳定,但由于从油水混合液进入旋流器开始分离,直至从出口和溢流口排出,持续的时间较短,加之油水分离是一个循环往复的过程,切向速度的波动并没有使分离效率产生较大的跳跃。
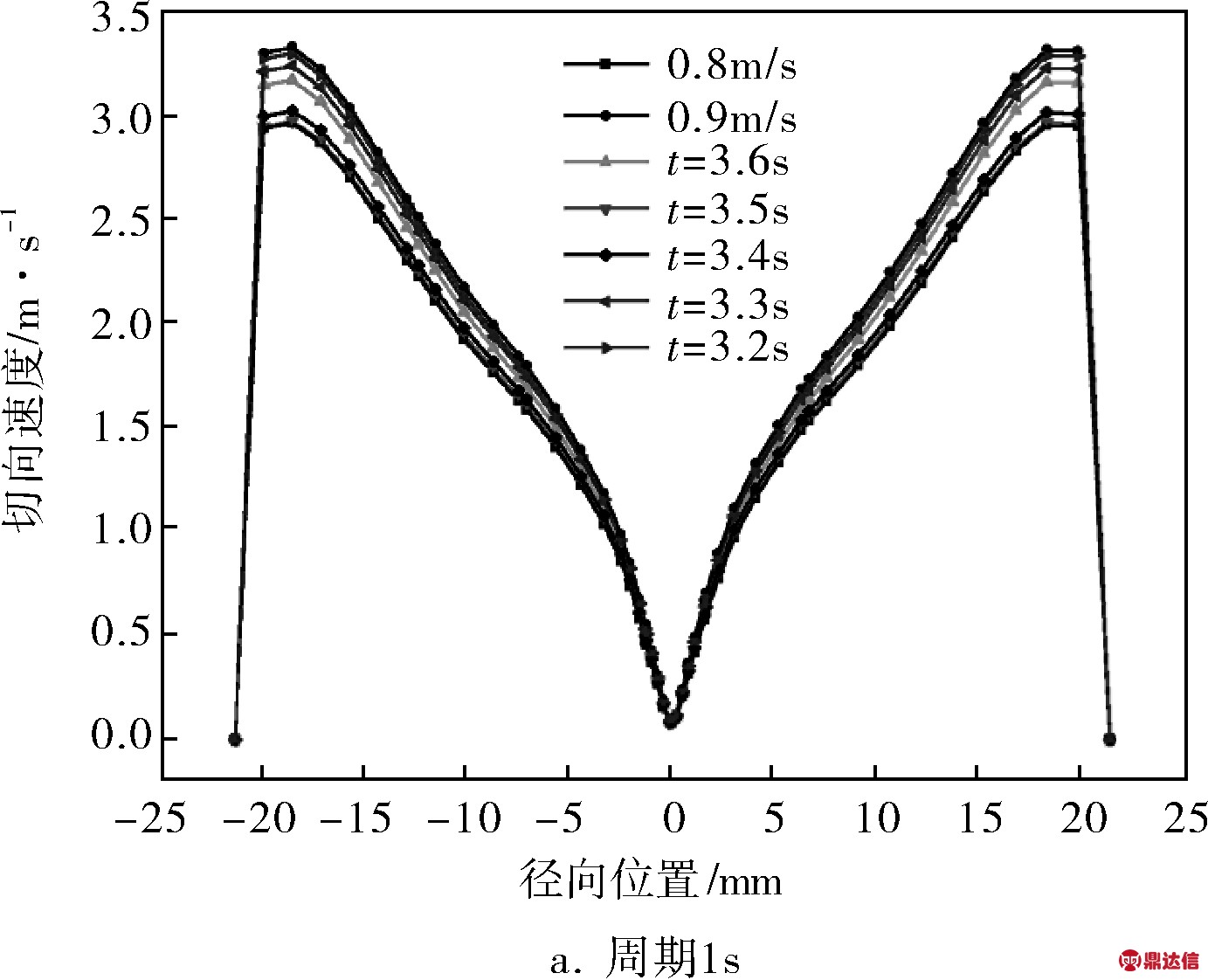
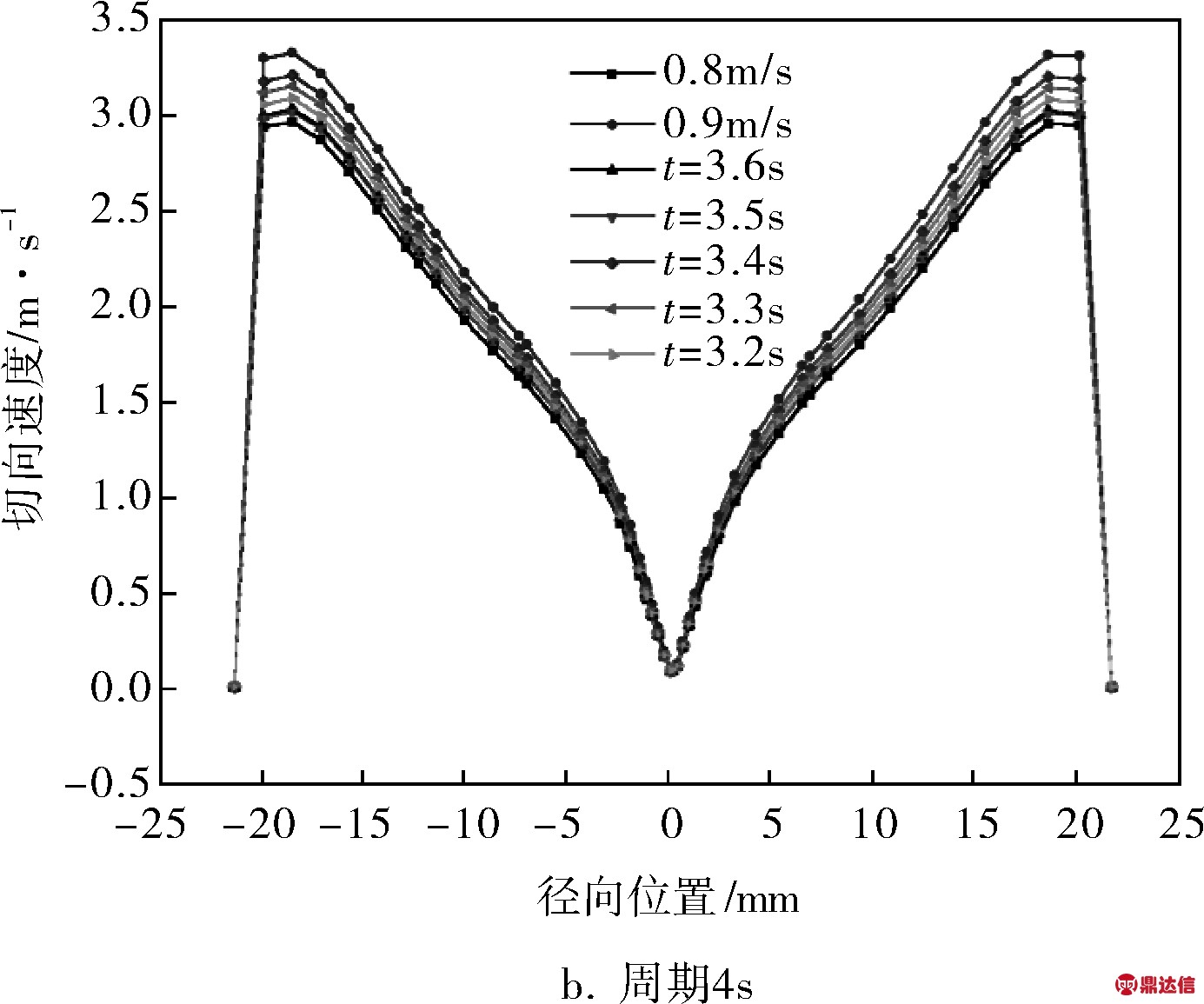
图9 z=150mm切向脉动速度的变化曲线
z=150mm处轴向脉动速度的变化曲线如图10所示,由图可知,脉动轴向速度均介于0.8~0.9m/s之间,脉动波动范围亦较小,脉动部分曲线互相重合,只是周期为4s时的脉动轴向速度数值间隔稍明显。这说明一个周期内的累积效应和流体的相互作用抵消了脉动效应。由于轴向速度与溢流和底流的分配有关,因脉动轴向速度变化较小,对分离性能的影响可忽略。
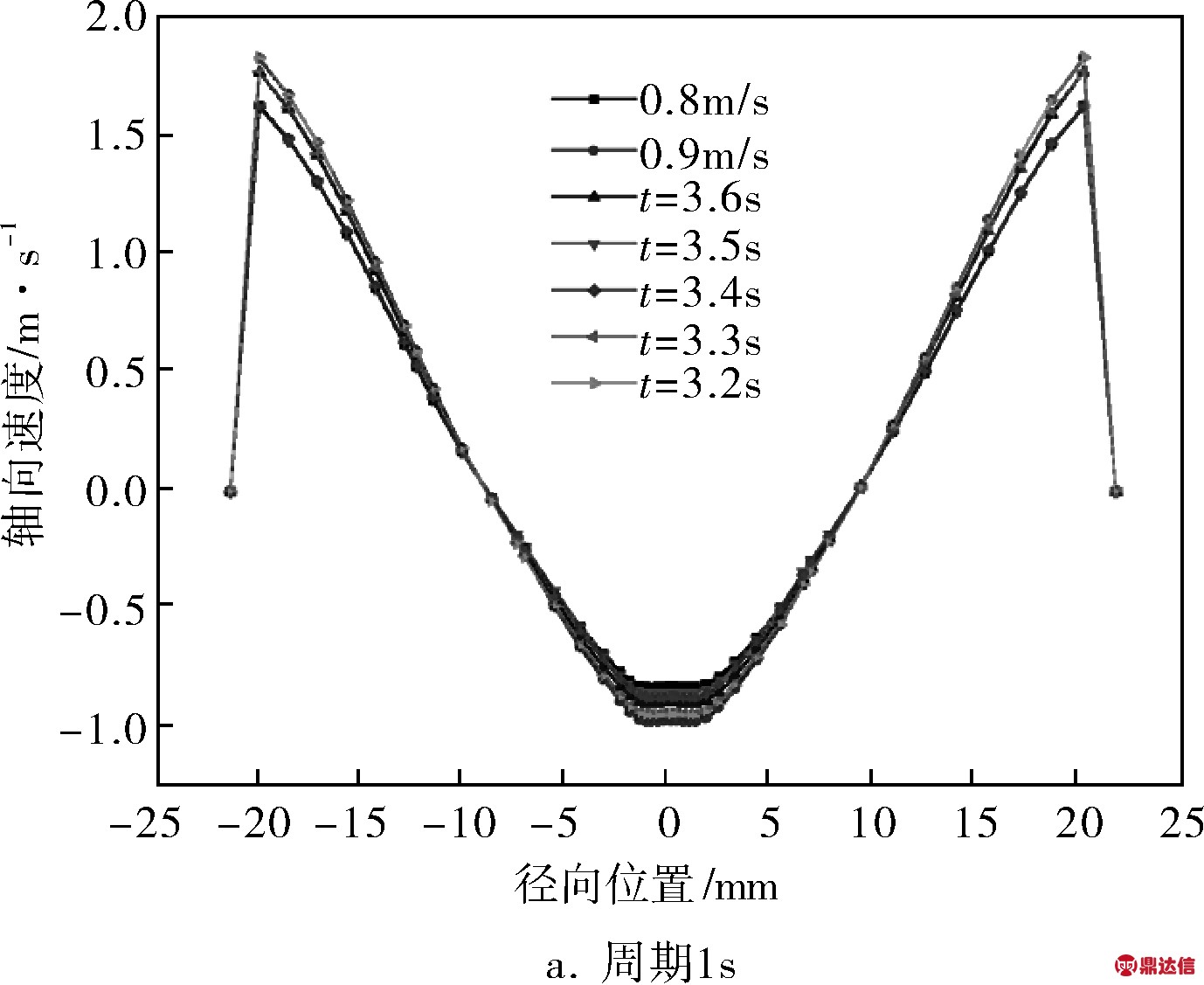
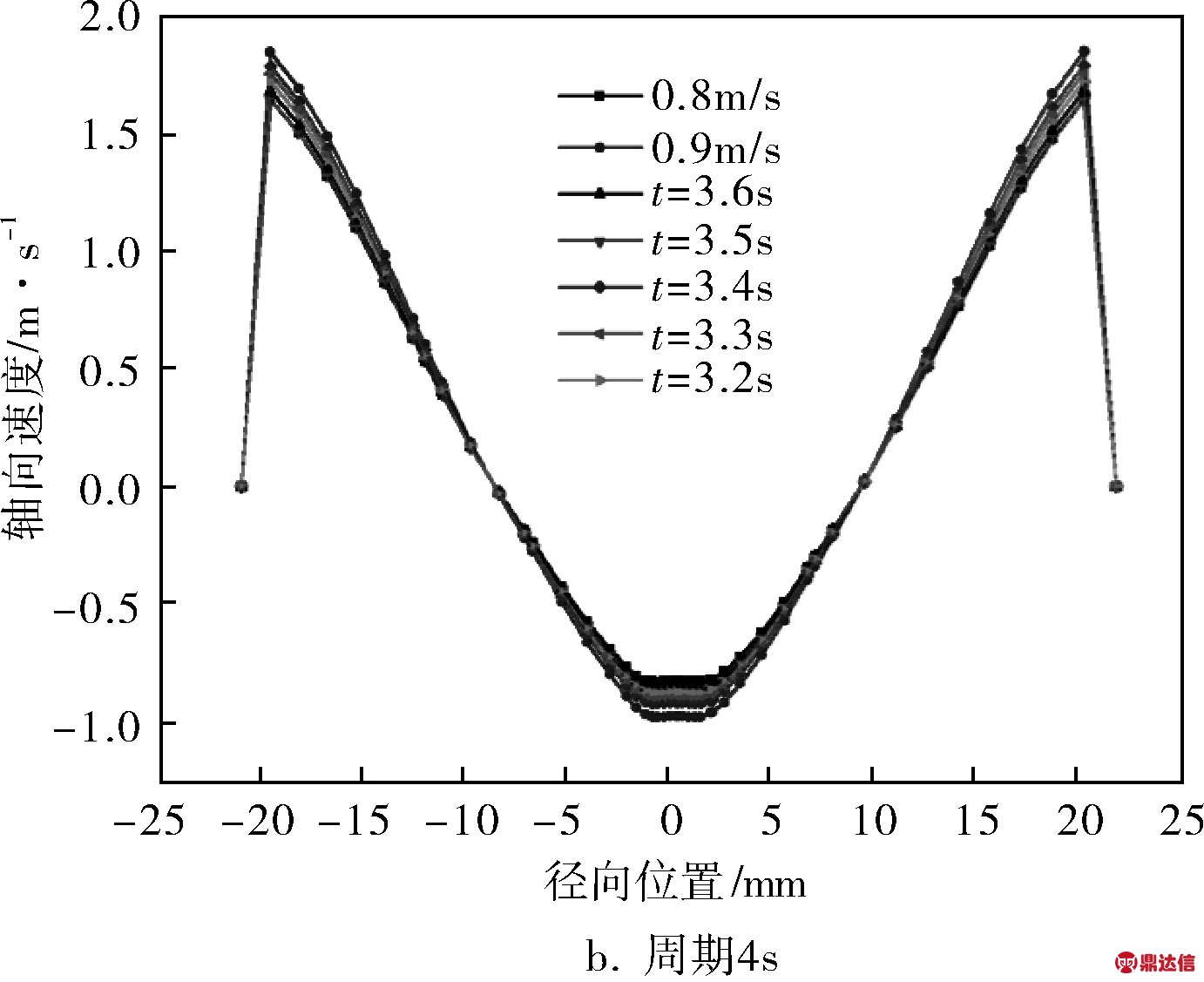
图10 z=150mm轴向脉动速度的变化曲线
2.2 油相体积分数对比
当周期为1s时,旋流器的yoz截面云图和z=150mm处的径向线段的油相体积分布如图11、12所示。从云图上看,从3.2~3.6s时间内,瞬时速度下油相体积分数先减小后增大,虽然3.5s和3.6s时的瞬时切向速度较小,但油相体积分数反而增大,这主要是因为油相体积分数并不能随着瞬时速度立即显现出来,是相对滞后的,并且是一段时间内的累积效应的过程。综合分析图10、11,从整体看,油相含量的变化幅度较小,油核宽度的变化亦不明显。径向的油相分布变化差别也不大,在曲线尖端峰值处,入口速度较大的油相曲线处于顶端之上,稳定流和脉动流的油相体积分数曲线绝大部分重合。这表明整体分离效果保持相对稳定,并未因为脉动流速的改变而发生较大的变化。周期为4s时的油相变化情况与周期1s时基本一致。当增大油相浓度时,尽管z=150mm处的含油量增大,但分离效率降低,因为少部分混合液来不及分离便从底流排出了。
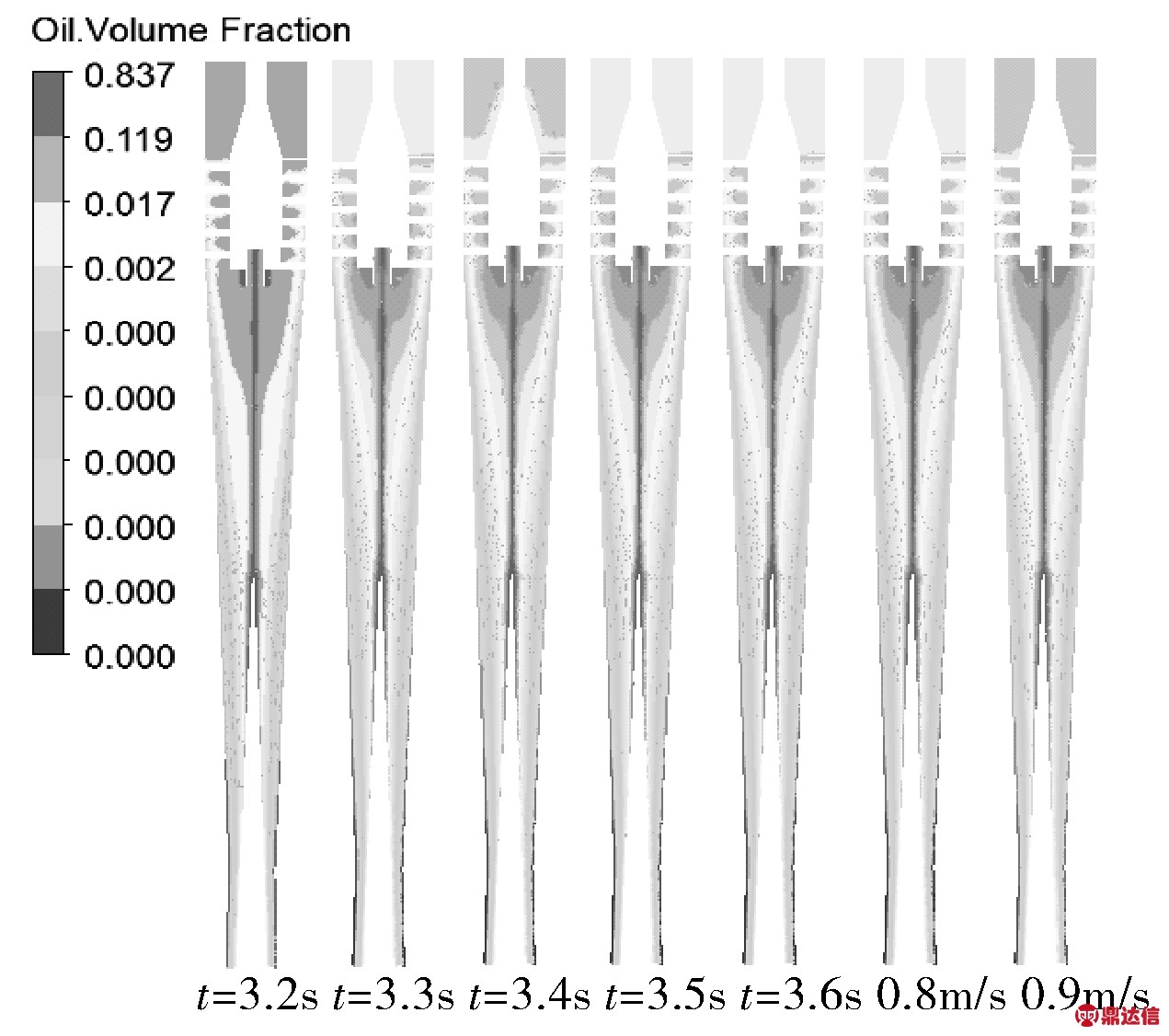
图11 油相体积分数云图
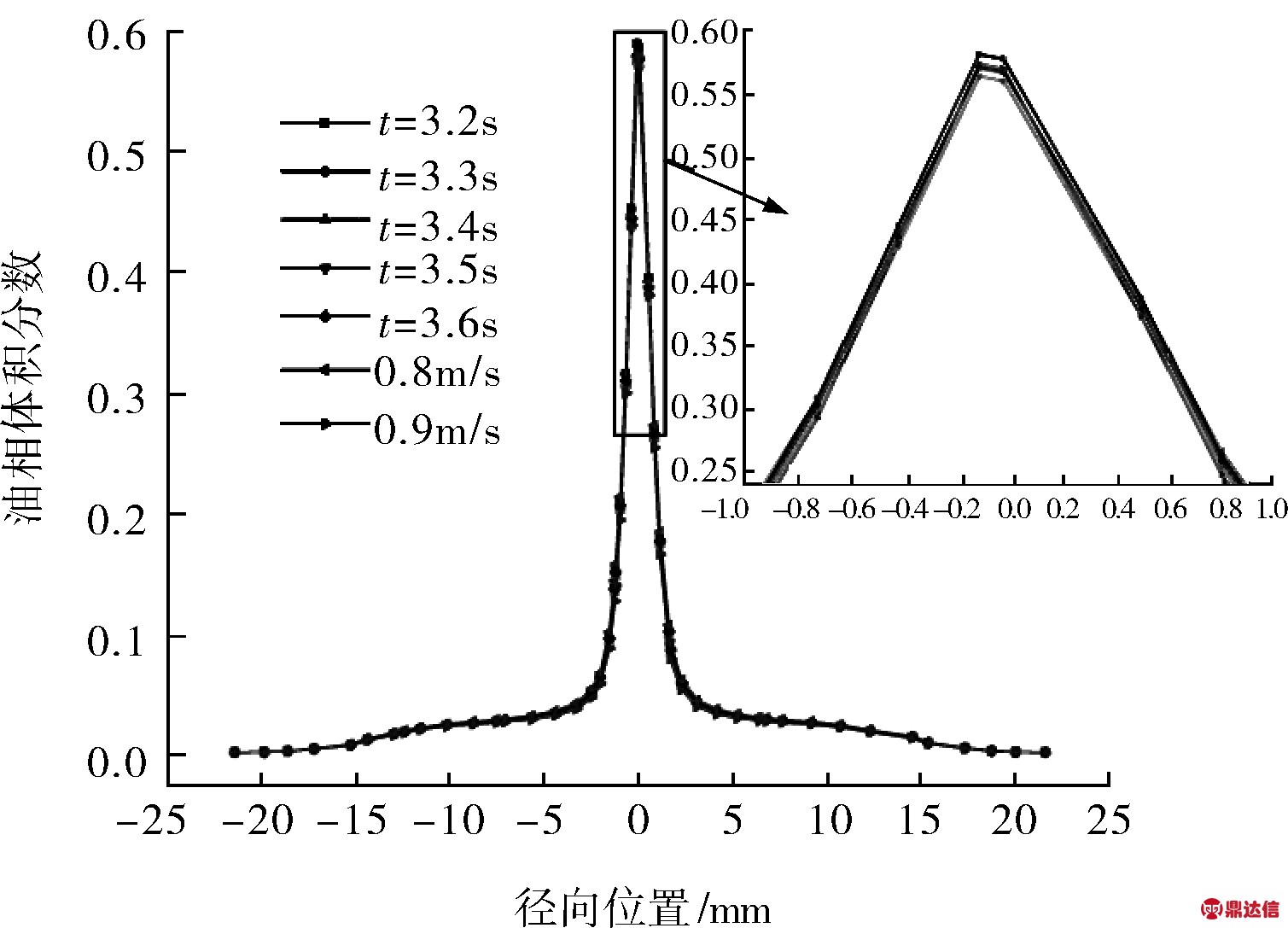
图12 油相体积分布曲线
图13为脉动流速下的分离效率,可以看出,脉动流对分离效率的提高幅度较小,与稳定流效率基本持平。周期越大,效率波动值越小,即对分离效率的影响越弱。
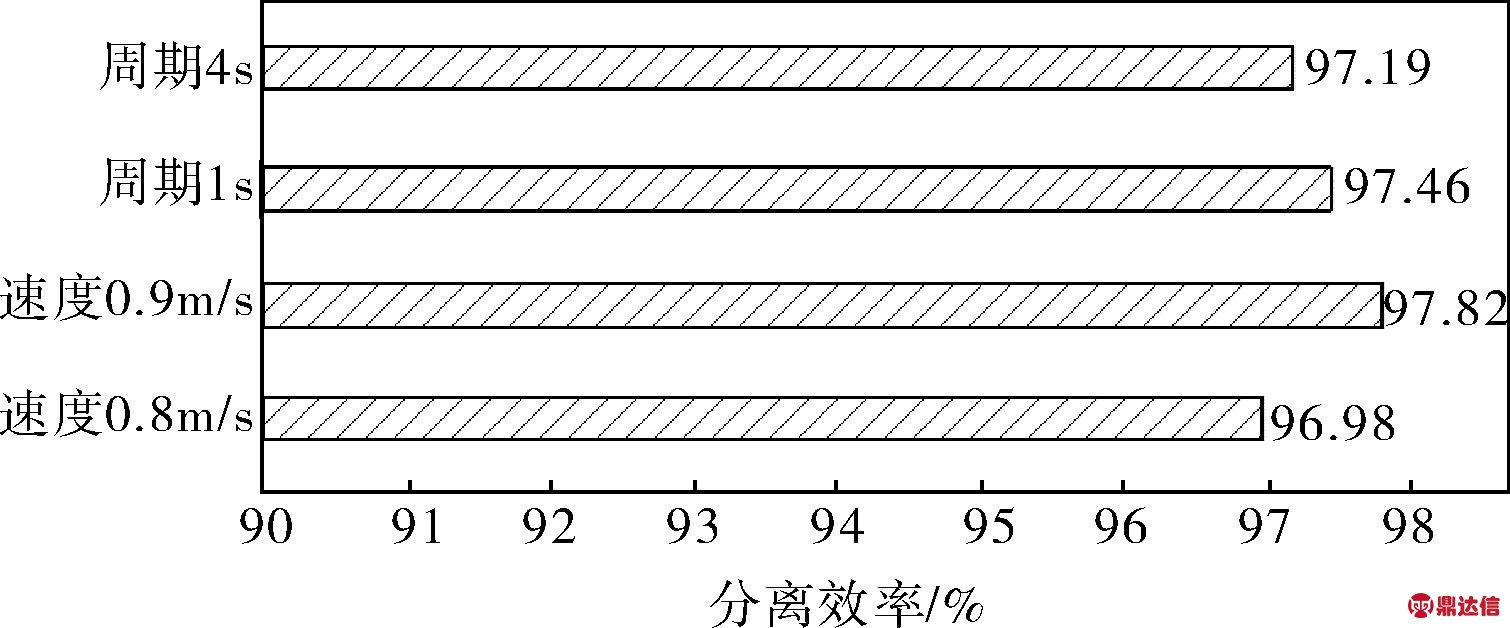
图13 脉动流速下的分离效率模拟值
2.3 压降对比
从能量角度而言,旋流分离所需要的动能是由压力能转化而来的[16]。压降损耗的大小反映了分离性能的优劣。压降一般为进口静压与溢流静压之差。当脉动周期为1s时,分别读取旋流器的进口和溢流口的静压可得出压降损耗,见表3。
表3 溢流压降
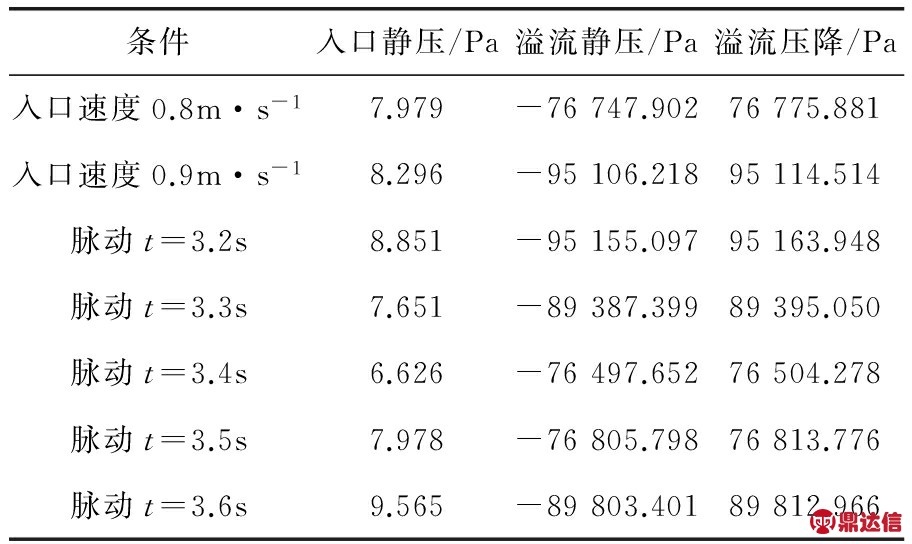
由表3可知,脉动速度诱发了溢流压降的波动,其中,压降最大值与0.9m/s的压降几乎相等,最小值与0.8m/s的压降近似相当,瞬时脉动速度与压降正相关。脉动压降的平均值约为85 537Pa,波动幅值为11%左右;该平均值是影响分离的长效标准数值。压降波动幅值在25%左右,该幅值虽较大,但对油水分离的影响只是一瞬间,从整体看不会对油水分离产生较大影响,因为分离性能是一段时间内的累积效应。当脉动周期为4s时,溢流压降的变化数值与1s时基本一致。由分流比与溢流压降关系图(图14)可知,周期为1s的脉动压降值介于0.8、0.9m/s的压降之间。
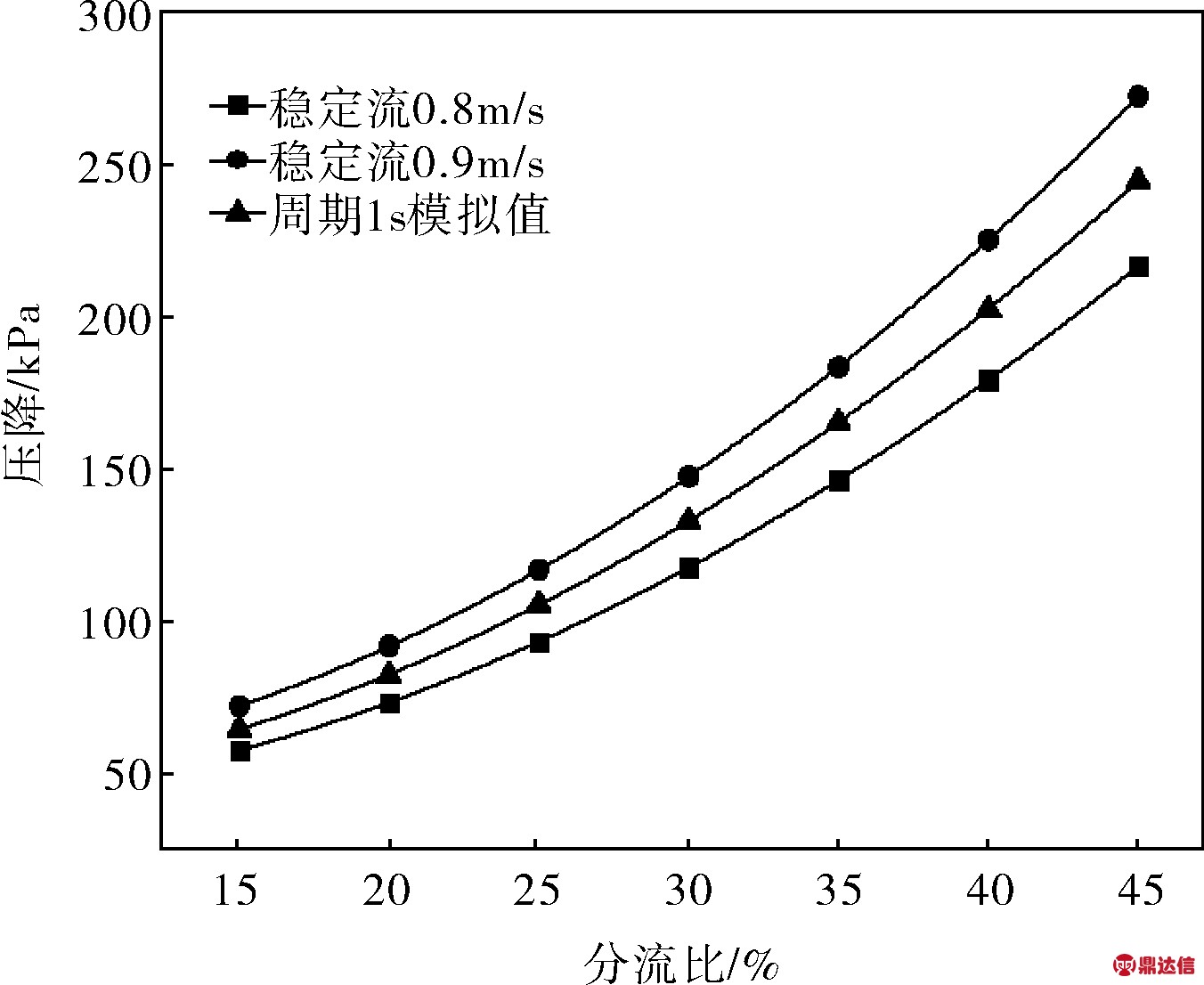
图14 分流比与溢流压降关系模拟值
3 脉动油相浓度的流场特性
图15为脉动油相质量流率变化曲线,可以看出,脉动油相浓度引起的溢流油相质量流率的变化类似于锯齿形,当周期变大时,齿尖变平滑。由此可以推知,周期越大,脉动油相浓度对分离性能的影响程度越小。
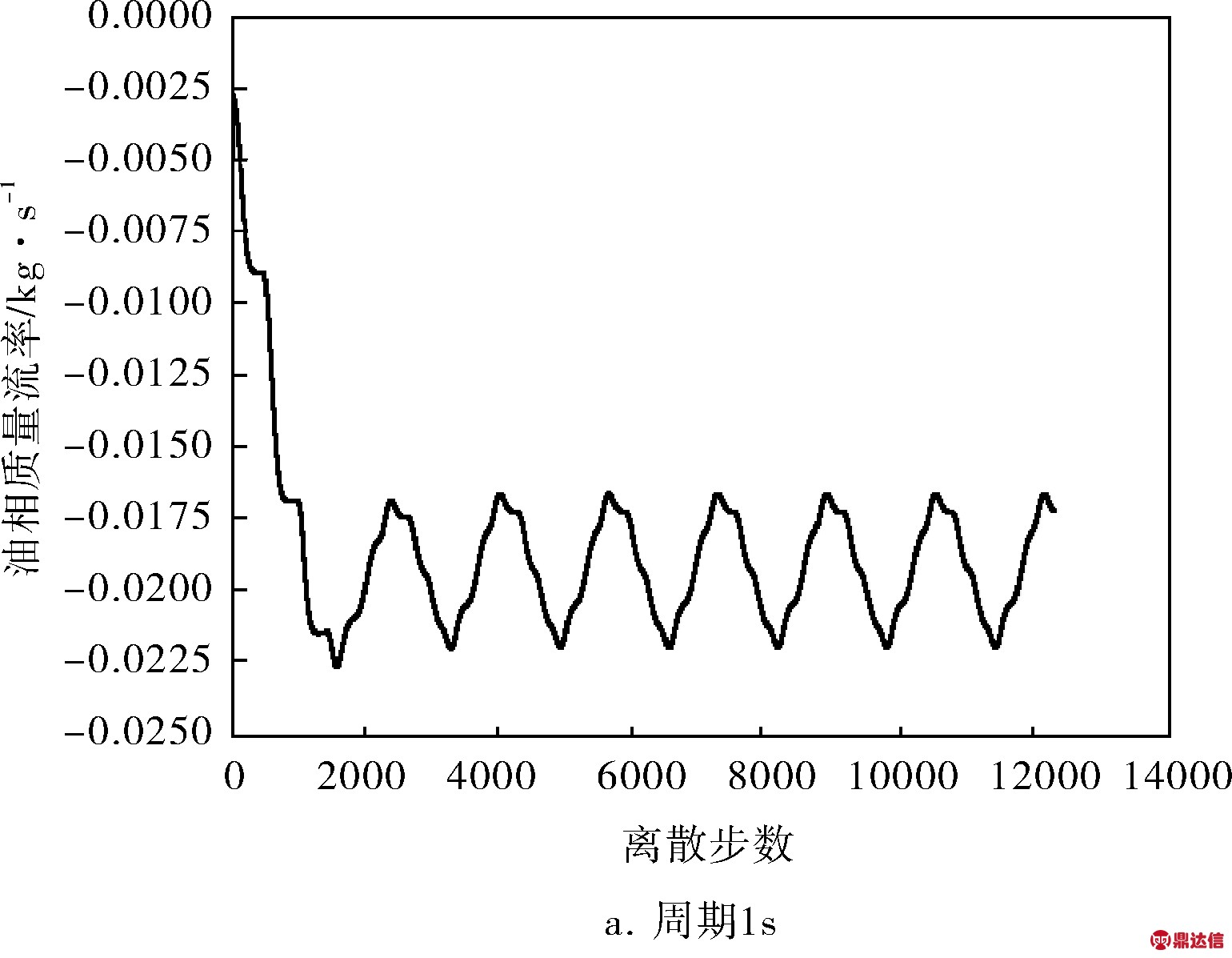
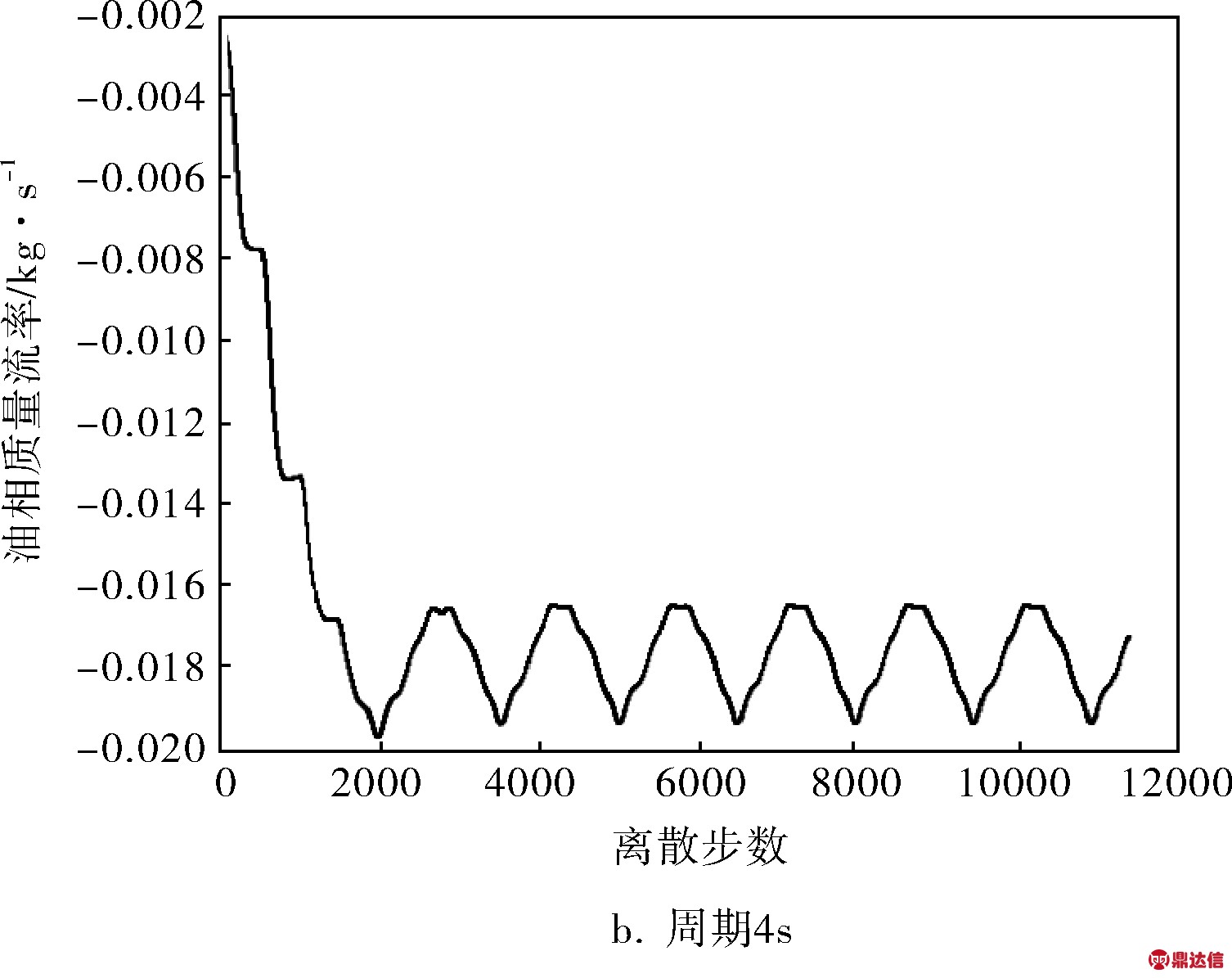
图15 脉动油相质量流率变化曲线
图16为z=150mm处的脉动油相体积分布。由于旋流器是针对较低含油量的优化设计,油相含量对分离效率的影响较大,当油相含量较高时,分离效率降低。但在一定的含油区间(0.01~0.02)内,脉动油相的变化并未导致分离性能的明显变化,而且周期越大,影响越小。对比油相体积分数的最高值可知,总体上油相体积分数相差不大,均在0.5左右徘徊,油相含量介于含油体积分数为0.01~0.02的分离效果之间,周期为1s的油相体积分数略高于周期为4s的油相含量。这是因为在一个周期内的分离过程中,分离时间较短,油相脉动周期较小时,油水来不及充分混合就被分离了,相反,脉动周期较大时,延长了油水之间的混合时间,因而分离效果变化较小。
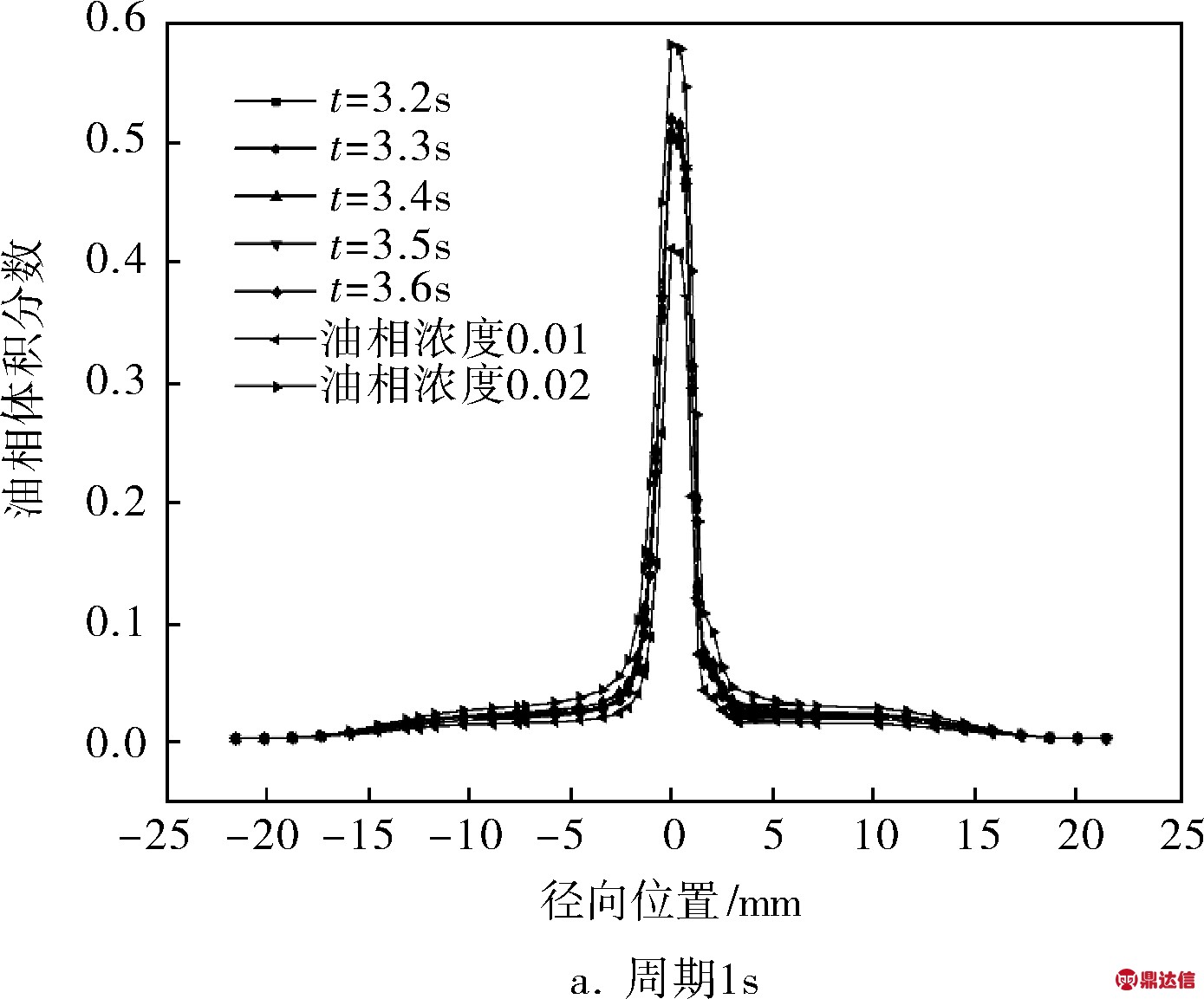
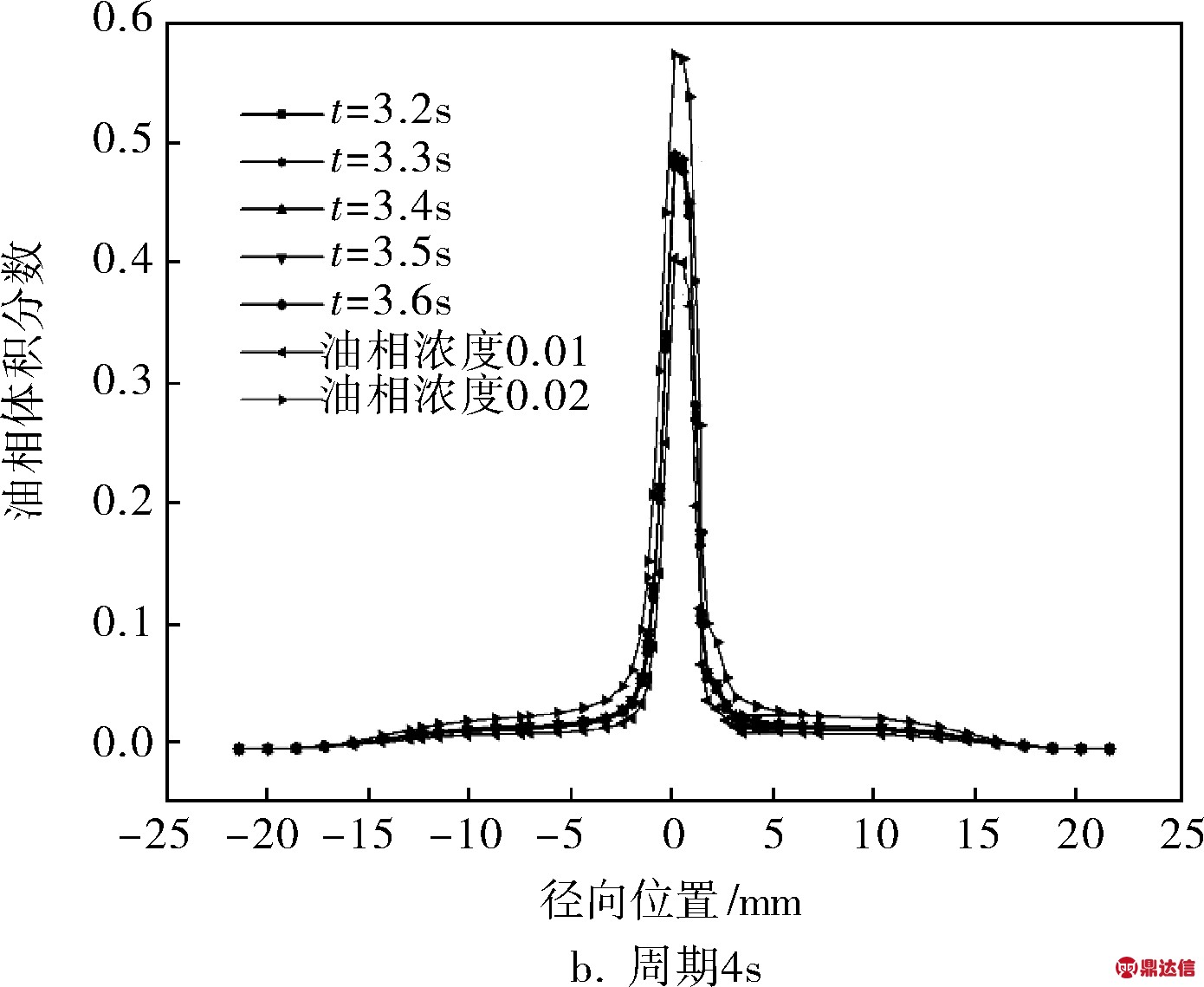
图16 z=150mm脉动油相体积分布
图17为脉动油相体积分数下的分离效率。由图可知,脉动油相浓度对分离效率的降低幅度不大,但比脉动流的波动幅值稍大,降低幅度随着周期的增大而减小。
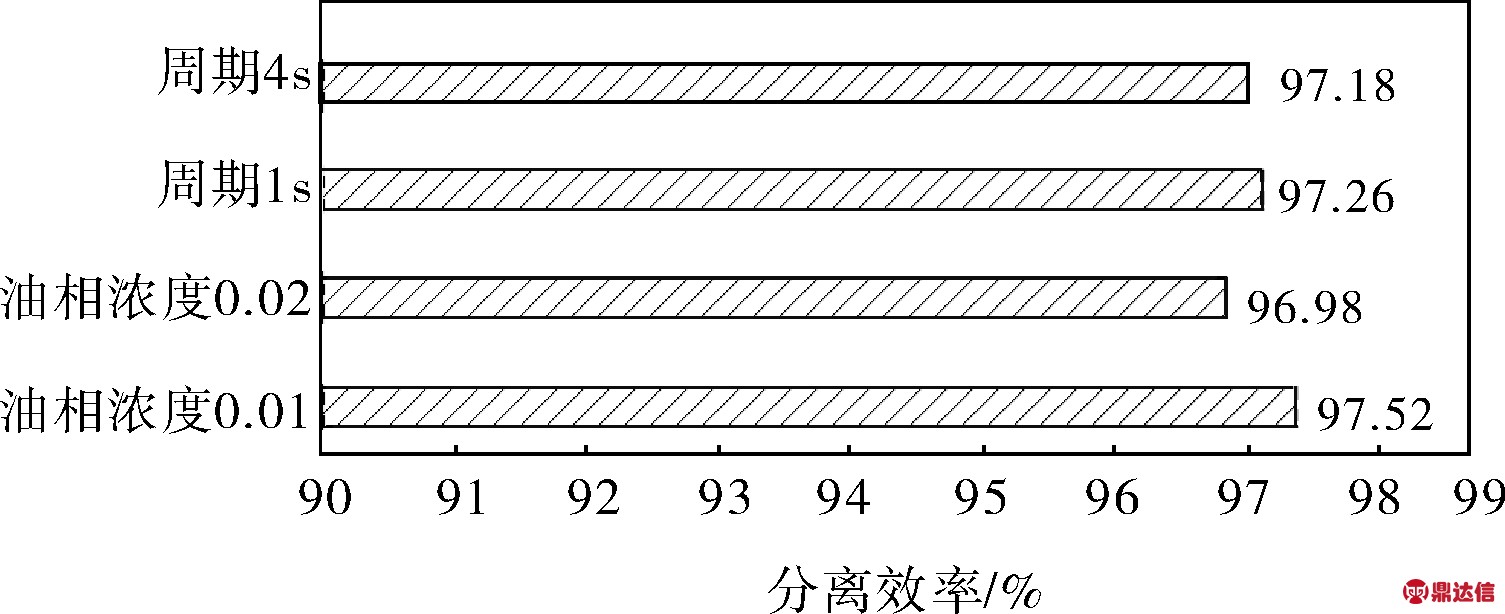
图17 脉动油相浓度下的分离效率模拟值
4 实验验证
为验证数值模拟的可靠性,分别取分离效率和压降两个关键参数进行实验。压降定义为进口静压与溢流静压之差;分离效率定义为溢流含油量与进口含油量之比。脉动实验流程如图18所示。
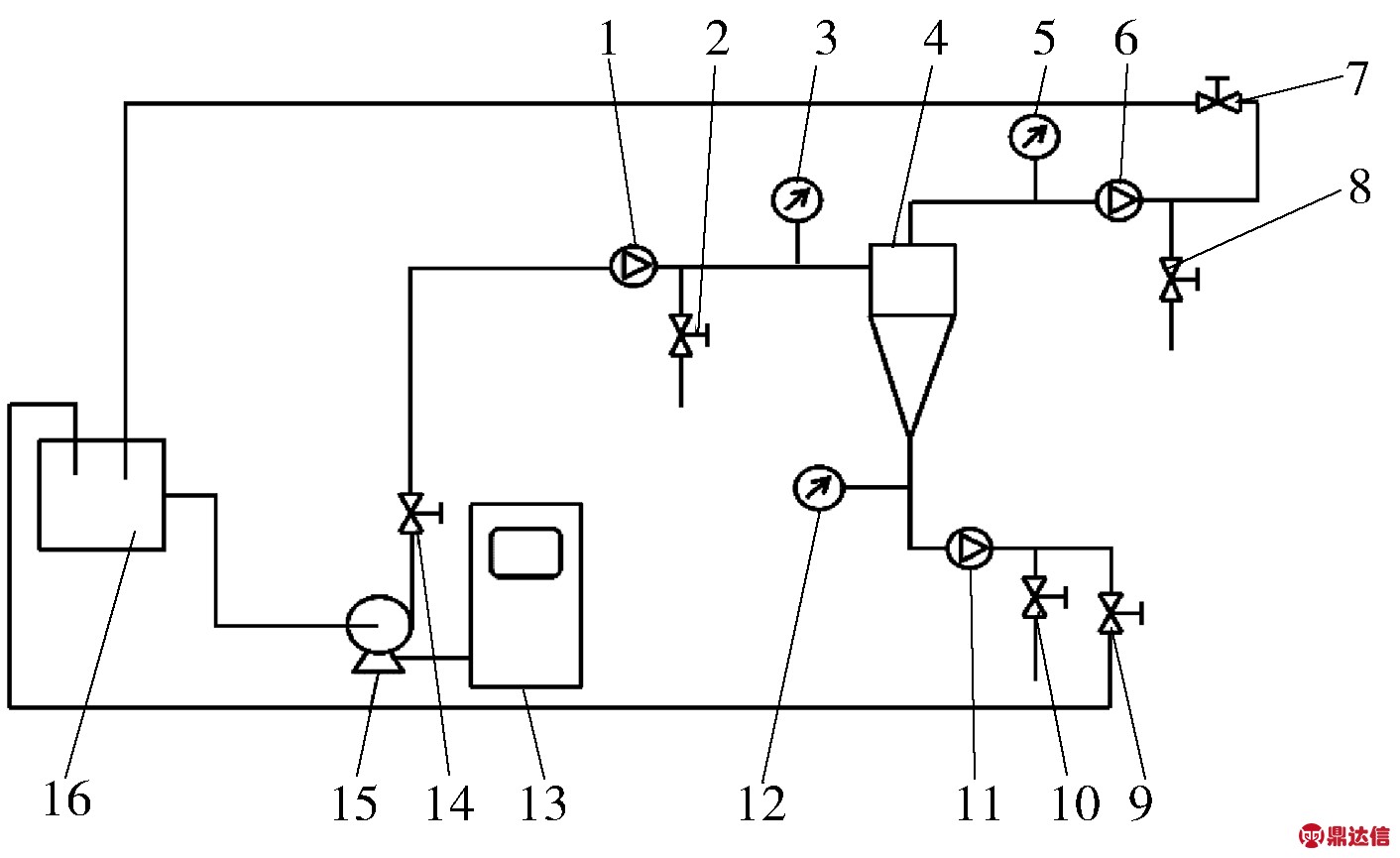
图18 脉动实验工艺流程 1、6、11——流量计; 2、8、10——取样阀;3、5、12——压力计; 4——旋流分离器; 7、9——循环阀; 13——变频器; 14——离心泵阀; 15——离心泵; 16——循环水箱
实验所需的脉动流量(流速)获取方法是,利用PLC模块把模拟电压信号输入至变频器,再由变频器将电压值转换为对应的频率值,进而控制水泵的转速来实现[17]。同时,为防止脉动流变为稳定流,尽可能缩短与进口连接的管路长度。
4.1 分离效率的实验验证
根据增压泵实际脉动运行规律,通过PLC装置调节入口流量脉动周期为1s,脉动流速以水平段0.8m/s为基准,逐渐向上浮动至0.1m/s[18]。入口脉动流速具体变化情况如图5所示。调节溢流分离比至20%,对比分析稳态和瞬态的分离效率。瞬态模拟结果取离散稳定后的平均分离效率,实验过程中分离效率亦取分离稳定后的平均值。图19为模拟和实验分离效率对比。
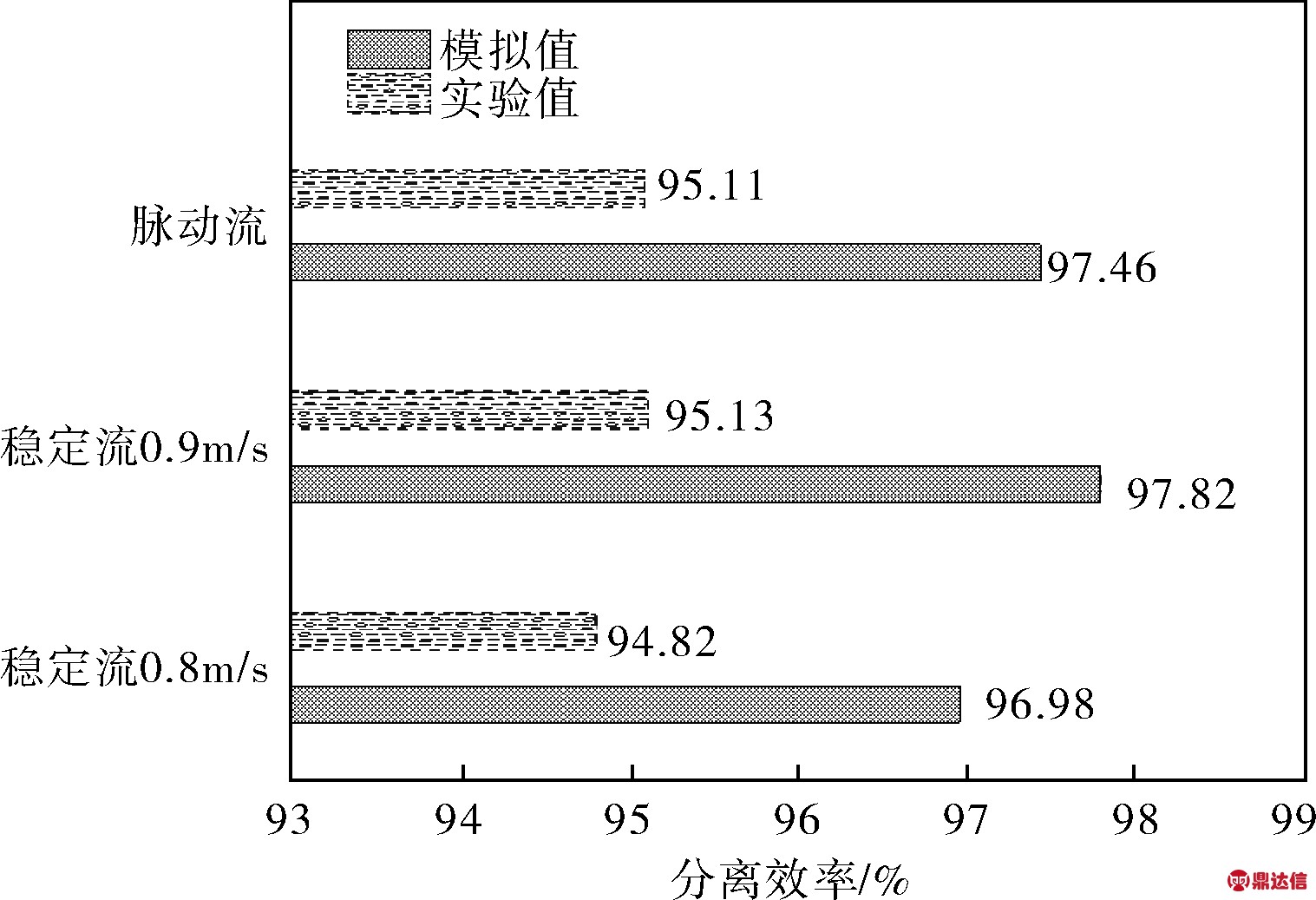
图19 模拟和实验分离效率分布对比
从图19中可以看出,无论是稳定流和脉动流,实验值均小于模拟值,入口速度(或脉动速度)越大,分离效率的增加越缓慢。这是由于数值模拟是理想状态,并没有考虑油滴破碎导致的乳化作用对分离效率的影响[19];入口速度增大,增加的切向速度有利于油水分离,但油滴破碎程度也增大,因此分离效率缓慢增加[20]。对比分析稳态和瞬态数值可知,脉动流整体分离过程是循环往复的,在分离过程中旋流器整体表现的分离效率是综合平均效应,整体效率变化幅度并不大,模拟值大约提高0.4%左右,实验值大约提高0.3%左右。瞬态平均效率模拟值为97.46%,介于96.98%和97.82%之间。以上结果表明,若入口脉动流速幅值变化不大,油水分离器对脉动流具有良好的适应性。
4.2 溢流压降的实验验证
脉动实验的压降值尽可能读取相等时间内的平均值,与稳定流0.8、0.9m/s的压降对比如图20所示。稳定流和脉动流的溢流压降均随着分流比的增大而增大,脉动压降曲线的模拟值和实验值均位于稳定流0.8m/s和0.9m/s压降曲线之间,并且随着脉动速度的增大而增大。相对于0.8m/s的压降,脉动流压降模拟值的波动幅度平均值在9%左右、实验值的波动幅度平均值在7%以内,由于压降和流体动能之间的相互转换,较小的压降波动有利于分离效果的稳定。模拟值和实验值的误差平均值小于5%。这表明模拟结果是可信的。脉动压降实验值比模拟值小的主要原因是实验时管路和阀门有一定压力损耗的缘故[21]。
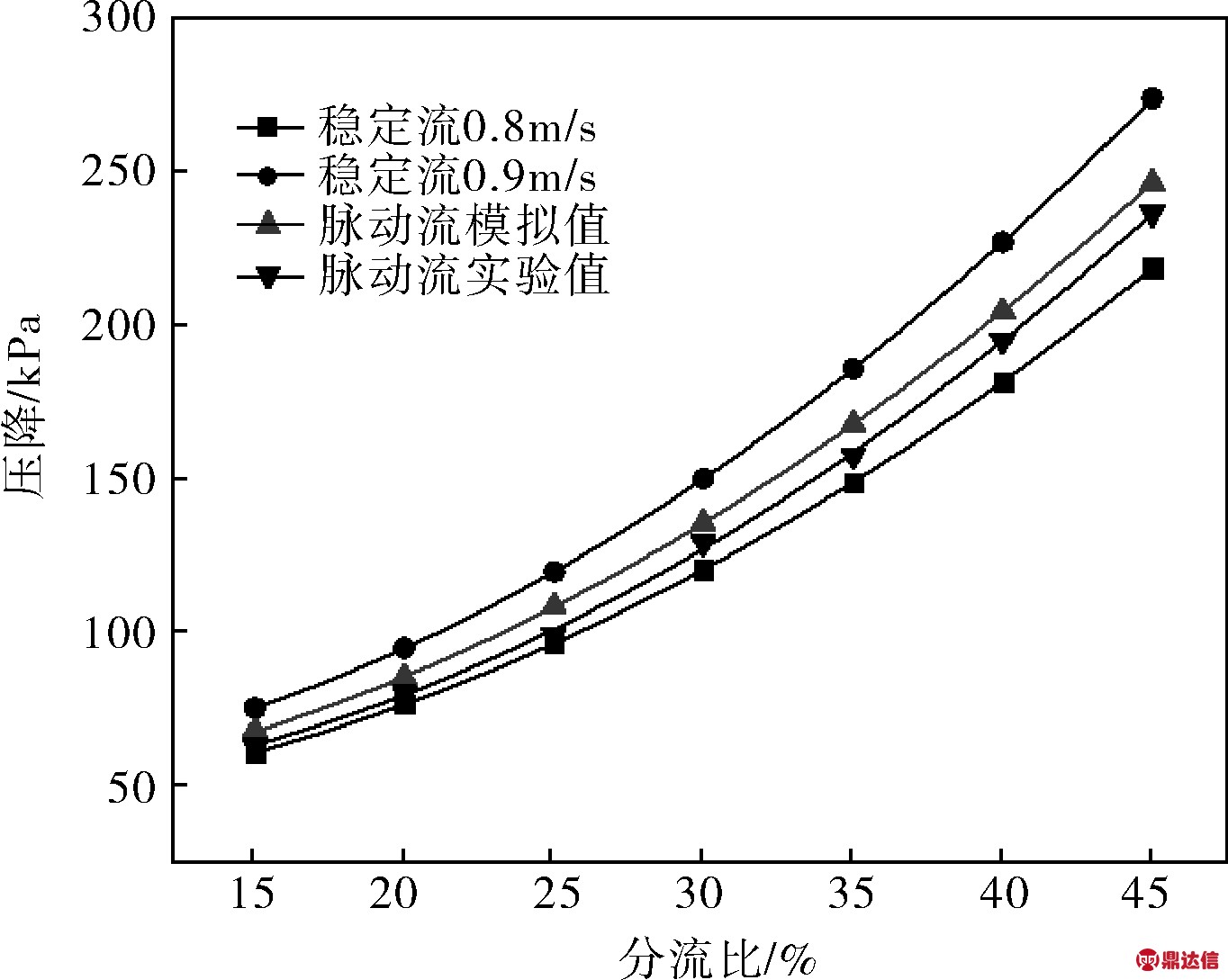
图20 溢流压降分布对比
以分流比为自变量,将各个压降进行拟合,可得二次多项式(表4)。
表4 溢流压降拟合曲线
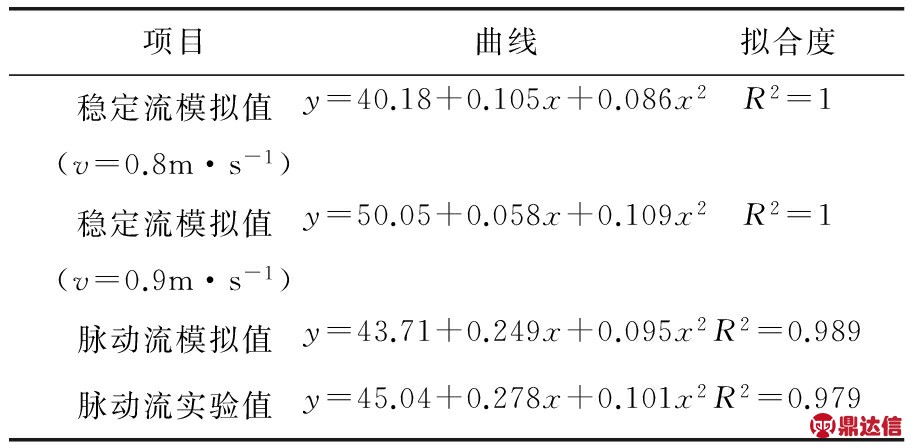
由表4可知,在研究范围内,稳定流和脉动流的分流比和溢流压降之间均符合二次曲线规律,且拟合度较高;脉动流压降的模拟结果和实验数据吻合度较高,数值模拟结果的正确性获得了验证。
综合以上讨论可知,当周期为1s、波动幅值为0.1m/s时,随着入口流速的脉动变化,引起的旋流速度和压降的波动变化不大,油相体积分数变化也较小,导致分离效率在一个较小的范围内增大。水平稳定时间段的流速产生的压降速度和分离效率也是脉动的,这是旋流体内部的实时速度和压力相互作用的结果,旋流器内的油水分离是一个动态累积过程。在特定的脉动条件下,分离效率大体上是稳定的,油水分离器对脉动流量的敏感度较弱,验证了分离器结构的合理性。
5 结论
5.1 脉动流会引起旋流合速度、切向速度、压降和油相体积分数的波动,进而引起分离性能的微小变化;当脉动幅值为0.1m/s时,分离效率大约提高0.3%,因而对分离器的性能影响较弱。
5.2 脉动流的周期性变化导致的溢流压降和分离效率的周期性波动,是一个动态滞后的累积过程。瞬间的高速脉动流引发的压降并不能引起分离性能的即时变化。
5.3 脉动流速持续时间和稳定流速持续时间虽不相等,但分离数值皆为周期循环数值。这说明旋流分离是一个相互影响的过程,脉动分离性能是一段时间内的整体效应。
5.4 在脉动幅值为0.1m/s的条件下,分离器对脉动流速具有较低的敏感度,适度增加脉动流的幅值对增强油水分离器的分离性能是有利的。