摘 要 通过对油气水三相分离器工作原理的研究,介绍了与其工作性能密切相关的主要内部构件——入口构件、整流构件、聚结构件的有关内容和研究现状。并针对目前分离器存在的常规性问题和运行潜在问题进行了讨论,最后在这些问题的基础上展望三相分离器未来的研究重点和发展方向。
关键词 三相分离器 油气水分离 内部构件 运行问题 发展趋势
油田油井采出液通常是无法直接使用的,它是原油、天然气、水及泥砂等的混合物,只有经过繁琐的工艺处理后,才能储存、向外输送或者销售。
作为采油平台上第1个处理井液的设备[1],三相分离器的作用就是利用油、气、水三相之间性质的不同分离油井采出液,油气水的分离效率或者分离器运行性能将直接影响到外输原油和气体的品质[2]。但是仅通过单一的筒体完成这个复杂的分离过程,设备体积会很大,而且分离效率低。实际工程中为了提高油田采出液的分离效率,并尽量减小设备体积、降低成本,常添加一些内部构件,其中对分离器工作性能影响较大的是入口构件、整流构件和聚结构件[3]。
最初的油水分离装置是油水分离池,然后经历了API型隔油分离池、PPI型平行板油水分离器和CPI型波纹板油水分离器的发展历程,不断的优化和改进,使得分离器的分离性能不断提高,但仍存在分离效率低、适应范围窄、抗波动能力差等常规性问题以及泡沫原油、液体携带、乳状液等潜在运行问题。为此,笔者通过讨论研究现存问题,从而预测未来高效三相分离器的研究重点和发展方向。
1 油气水三相分离器工作原理
按照外形,三相分离器可以分为立式、卧式和球形。立式分离器比卧式占据空间更小,为了更彻底地清除沉降的固体杂质,立式分离器在容器底部设置排污口,因此适用于原油处理量小、含较多固体杂质的油田;卧式分离器拥有较大的气液界面,气泡可以更好地从液相中析出,而液滴沉降方向与气体运动方向垂直,液滴从气体中分离变得容易,因此卧式更适合于处理乳化或含有气泡的油井采出液。立式虽然占据空间较小,但是操作高度较高,如果没有特制的操作平台和梯子,则很难对内部装置实现有效的控制,成本较高[4]。而对于球形分离器,其分离性能并不理想,且尺寸计算过程复杂,难以加工,成本相对较高。故在实际油田工程中,立式和卧式分离器较为常见。
笔者以卧式重力分离器为研究对象进行说明。卧式重力分离器(图1)内部按照功能可以分为4个部分:入口分流区、集液区、重力沉降区和除雾区。油井采出液首先进入入口分流区,与入口构件相互作用以实现气体和液体的预分离[5]。预分离后的液相落入集液区,经过重力沉降作用,油滴聚结并上浮形成油层,水滴聚结并沉降形成水层,上层的油液溢过堰板进入其后油室;通过浮子即液位感应装置感应油水液面的高度,并分别通过两个液位控制阀实时排出液体。预分离后的气体首先进入重力沉降区,气相中粒径较大的液滴在重力作用下实现沉降;然后进入除雾区,经除雾器除去较小的液滴,并由压力控制阀控制排出气体以保持容器中压力的稳定[6,7]。
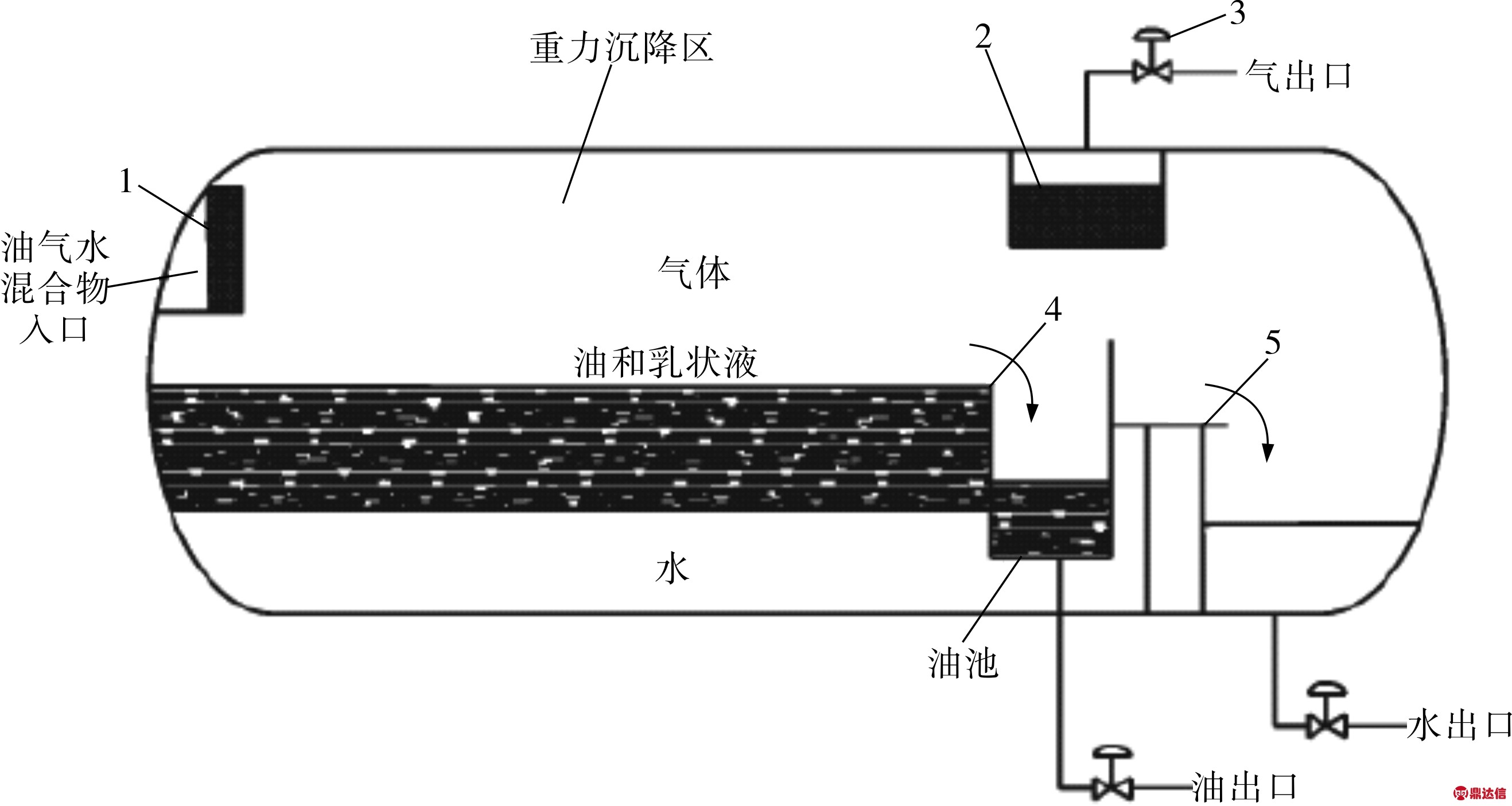
图1 卧式重力分离器结构示意图
1——入口构件; 2——除雾器; 3——气体压力控制阀; 4——挡油堰板; 5——挡水堰板
三相分离器的相分离需要以一个相对稳定的流场条件作为基础,同时一些实际的外部条件和因素也需要理想化,而针对出口处有关的压力控制、液位控制等操作,同样需要内部流场的稳定。为了能够顺利实现分离器的分离性能,需要添加一些必要的内部构件来减少达到稳定所需要的时间和成本,保证分离器的工作性能,使内部环境更适合分离的进行[8]。内部构件主要包括入口构件、整流构件、聚结构件、除雾器、防涡器、喷砂嘴及防浪板等,其中前三者对于三相分离器流动性能和分离性能的影响最大,也是相关领域研究的重点。
2 入口构件
入口构件安装于分离器入口分流区,也就是分离器的初始段。油井采出液进入分离器,撞击入口构件后动能速度减小,对内部流场的冲击也相应减弱;同时撞击使得气体迅速改变方向流过进口构件,而液体则落至容器底部,实现了一定程度的气液预分离[9]。入口构件的性能会影响后续的气液分离、油水分离和整个分离器的主体尺寸。
典型入口构件形式(图2)有碰撞式、离心式、孔箱式及弯管式等。
碰撞式入口构件是一种典型的入口构件,主要碰撞体是平板、角铁、锥体及弯头等。油井采出液进入分离器后作用于入口构件,在相同速度下,密度高的液体能量较高,不像气体那样易改变方向,这样就实现了气液的预分离。在选择这种形式的入口构件时,要考虑它是否满足运行时流体的冲击能量负荷要求。
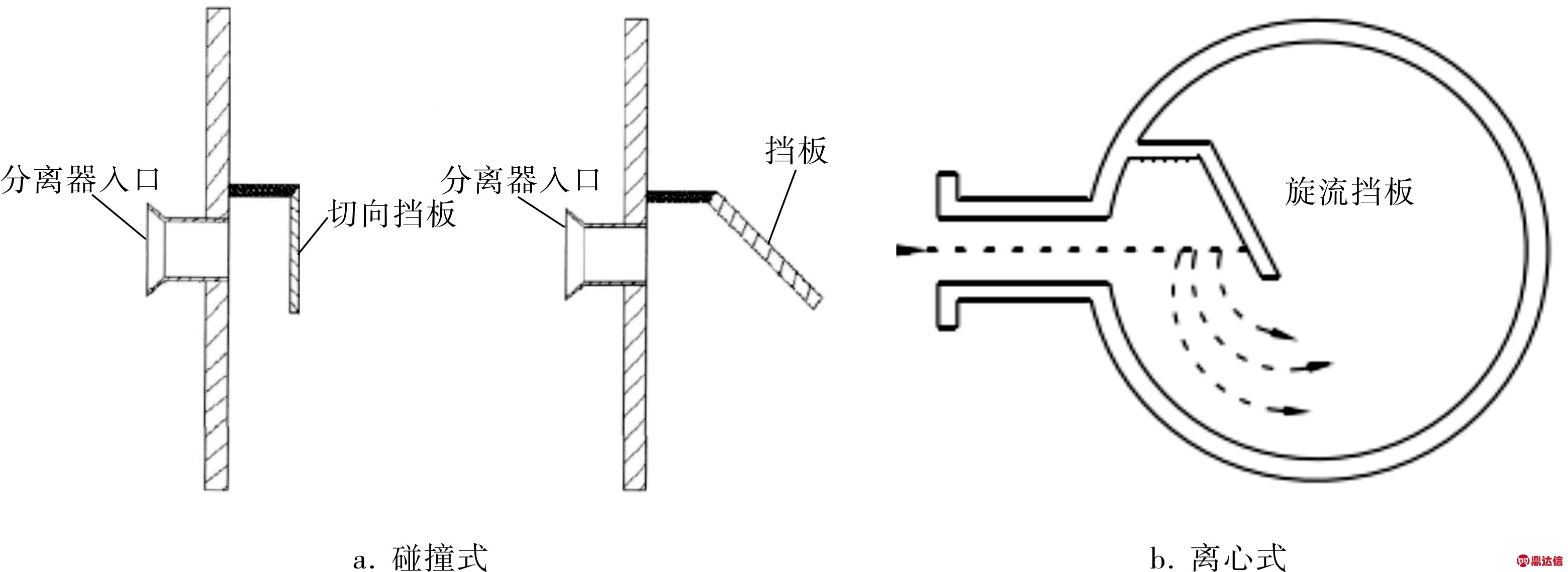
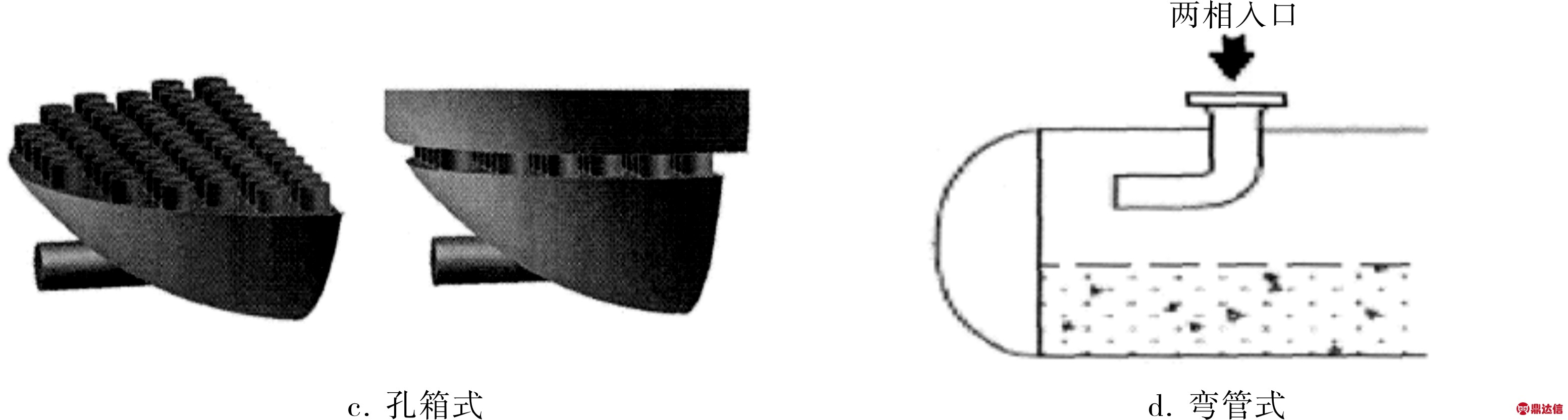
图2 4种典型入口构件形式
离心式入口构件具有旋流式的喷嘴或者沿分离器壁有着切向的流体轨道,依靠混合液切向进入分离器产生的旋转运动,使气体和液体因为受到不同大小的离心力而发生分离[10]。但因为该形式入口构件对流量过于敏感,故不适用于在低流量的情况下工作。
孔箱式入口构件分为上孔箱式和下孔箱式,两种形式结构类似,但安装位置不同。孔箱式入口构件可以有效地减少一次涡流的产生,但因为没有类似于碰撞式的剧烈冲击,气液预分离效果有所减弱。下孔箱式具有较好的重力消能和水洗作用,可以促进油相中水滴的聚沉。
弯管式入口构件工作原理类似于碰撞式,可以有效减小入口流体的流速,不会因为流速过大导致入口液相的汽化。
入口构件不是根据某一项特定的因素选择的,而是要综合考虑相应的生产条件、采出液具体成分、分离器尺寸、布置成本及经济性等。不同油田的不同三相分离器,采用的入口构件形式和尺寸也是不同的[11]。
文献[12]应用流体分析软件Fluent对安装有斜挡板式、下孔箱式、叶片式入口构件的分离器进行了内部流场的仿真模拟研究。结果显示,斜挡板式的上方和下方会产生涡流,预分离后的液相落到分离器底部会产生较大的涡流,严重扰乱了分离器内部流场的稳定性;流体在下孔箱的内部会有部分涡流产生,但经由孔板流到分离器内部后,流动状态有了较大的改善,并且没有很大的湍流强度,产生的重力消能和水洗作用也会加快油水的分离;流体经叶片式入口后分散均匀,几乎没有漩涡产生,在集液区也没有剧烈的扰动存在,在3种构件中表现最好。王超针对挡板式、上孔箱式和下孔箱式入口构件的分离器进行了仿真研究,所得流场结果基本相同[13]。王晓静等则研究了3种开孔率分别为20%、30%、40%的新型液盒式入口构件,Fluent仿真结果显示,开孔率为30%的入口构件,喷射高度较高,重力消能和水洗作用得到了充分利用,流场速度分布比较均匀,实现了一定程度的预分离效果;而开孔率为20%和40%时,产生的返混和旋涡情况严重,不利于油水两相的分离[14]。
3 整流构件
整流构件常安装于筒体较长的卧式分离器的集液区,大多是一些简单的开孔平板和栅板,并与液流方向垂直放置[15]。除了可以阻挡采出液中混含的砂子等固体杂质、保护后方的聚结构件不受影响外,流经整流构件的流体流型会变得更加规整,稳定流场防止波浪(波浪会使液位控制器、液位安全阀和溢流口不能正常工作)的产生。
1980年107个国家通过的《马尼拉世界旅游宣言》则指出:“更深刻地了解国民性、把每个公民与其同胞联系在一起的凝聚力、文化和民族归属感,是促使每个人参加国际旅游和国内旅游的主要原因”。
王超应用Fluent软件对分别含有上述5种整流构件的流场进行了数值模拟,并设置了没有整流构件的对照组,发现所选取的5种整流构件对分离器内部流场流型均有一定的影响,其中田字板型整流构件的整流效果是最好的,过程中几乎很少产生涡流,流体流经之后流型更加规整,速度和方向一致性提高,圆筒型次之[13]。李东芳等的研究结果也表明,田字板型整流构件有效抑制了分离空间内的返混流动,流场流动特性较好[16]。
鞠微研究了构件长度对于流场稳定性和整流构件工作性能的影响,选用田字板型和圆筒型两种形式并设置了50、150mm两种长度[12]。结果发现,相对于50mm田字板型整流构件,增加长度到150mm之后,流场情况并没有较大变化;而150mm圆筒型整流构件对于流场的整流效果和流型规整能力相比50mm时要好,流动也更加平稳,原因是流经圆筒型整流构件的流体除了具有垂直于板方向的轴向速度之外,还存在绕各层连续圆筒面的径向流动,较短的整流件不足以在短时间内消除这部分流动,构件加长则可以改善速度方向的不确定性,从而达到整流的效果。
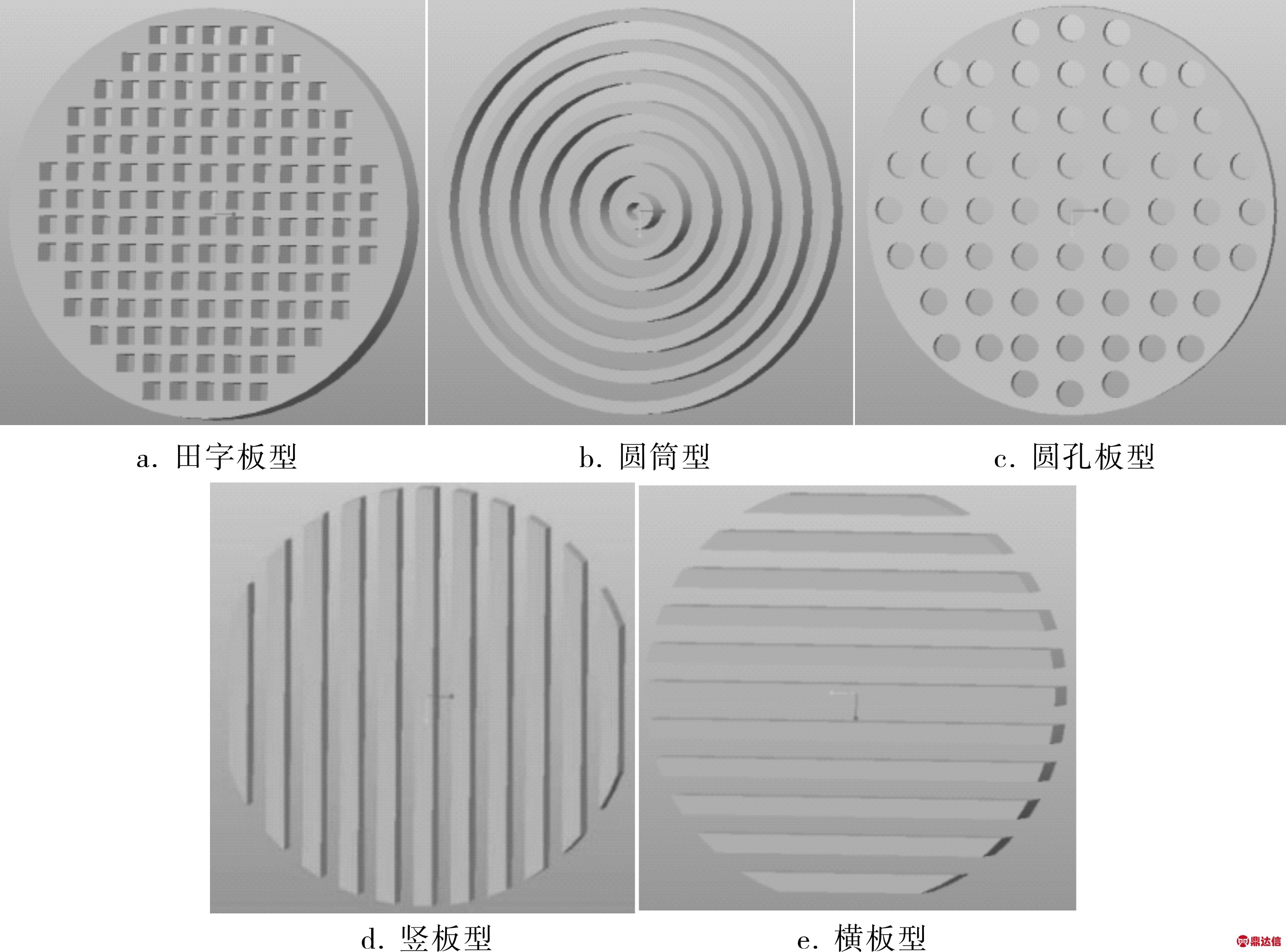
图3 常见的5种整流构件结构形式
王晓静等对均匀分布型、上密下疏型和内密外疏型栅格式整流构件进行了研究,发现整流构件的引入可以有效改善轴向速度分布的不均匀性,且上密下疏型和内密外疏型对流场稳定性的提高更加有效,效果均优于均匀分布型[14]。
4 聚结构件
聚结构件是一种与油水分离效率密切相关的核心内部构件,常安装于整流构件的后方。聚结构件将重力分离和聚结分离相结合,油相中的水滴或水相中的油滴通过聚结构件聚结形成较大尺寸的液滴,从而使这些较大的液滴在重力作用下更容易沉降或上浮。
聚结构件一般分为板式聚结构件和管式聚结构件两类。其中管式聚结构件占用空间较大,造成分离器体积过大,经济性较差,所以就实际工程应用来说,板式聚结构件的应用更为广泛。常见的类型有平行板隔油池、波纹板隔油池和交叉流分离器[17]。图4为板式聚结构件运行截面图,依靠重力分离原理使油滴上浮到聚结板的表面从而发生聚结沉降。以平行板式聚结构件为例,V形平行板沿水流方向放置,薄油层会向上移动聚集到板的下部和两侧,固体杂质向板中部移动并沉积到分离器底部,由于板间距较小,所以可以在分离器里安装更多板,从而使油滴聚结达到最大化。
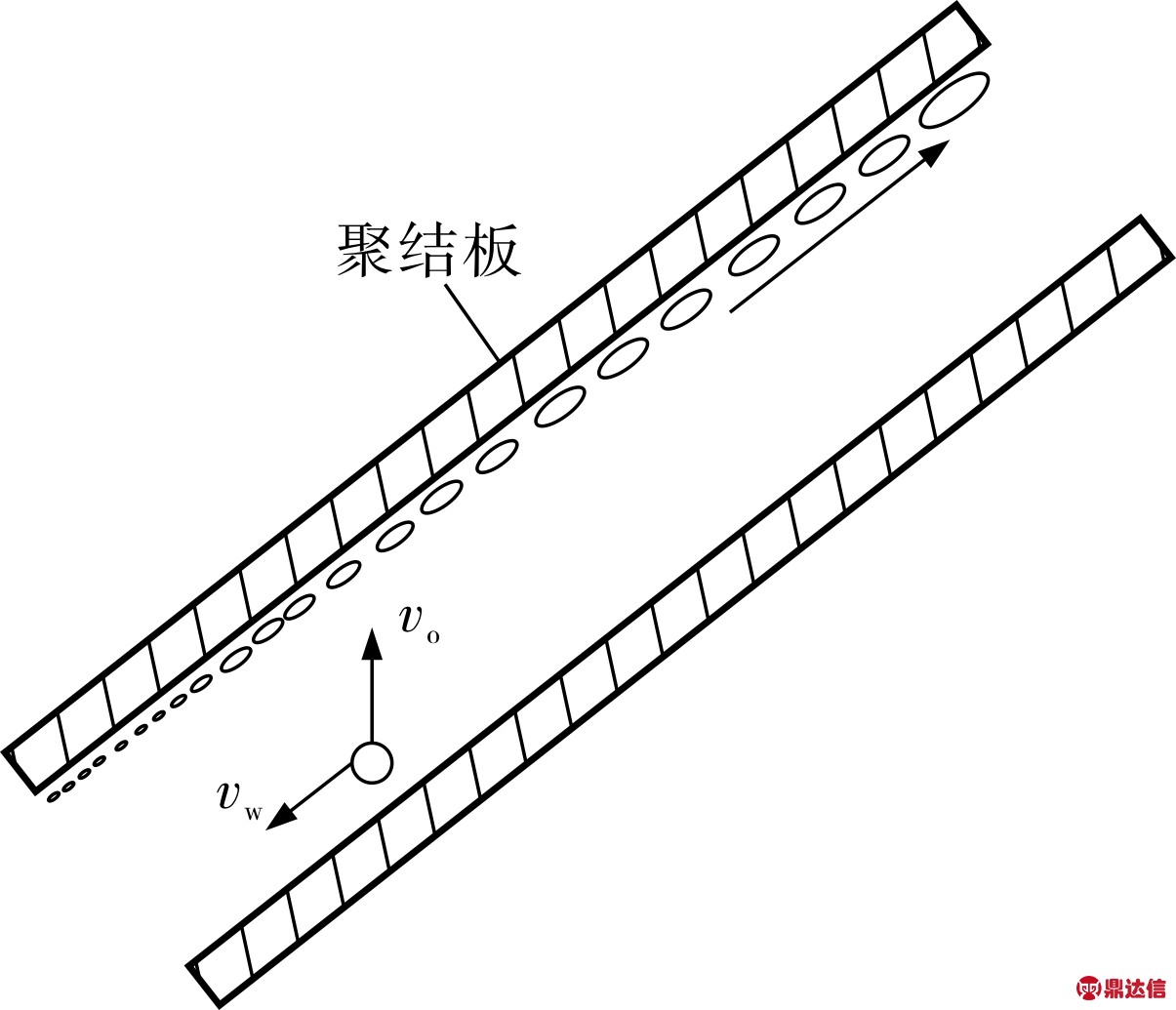
图4 板式聚结构件运行截面示意图
vo——油滴上浮速度; vw——水流速度
根据Stokes定律,油滴的分离效率只与油水物性、油滴浮升面积和油滴的粒径有关,而与浮升的高度无关,这就是通常所说的“浅池原理”(图5)。应当注意的是,Stokes公式适用的粒径范围是1~10μm的小液滴,但从现场的实验表明,30μm以上作为可以脱除的油滴直径才是可行的,小于30μm时油滴的浮升过程会受到平台振动、微小压力波动等的阻碍[17]。
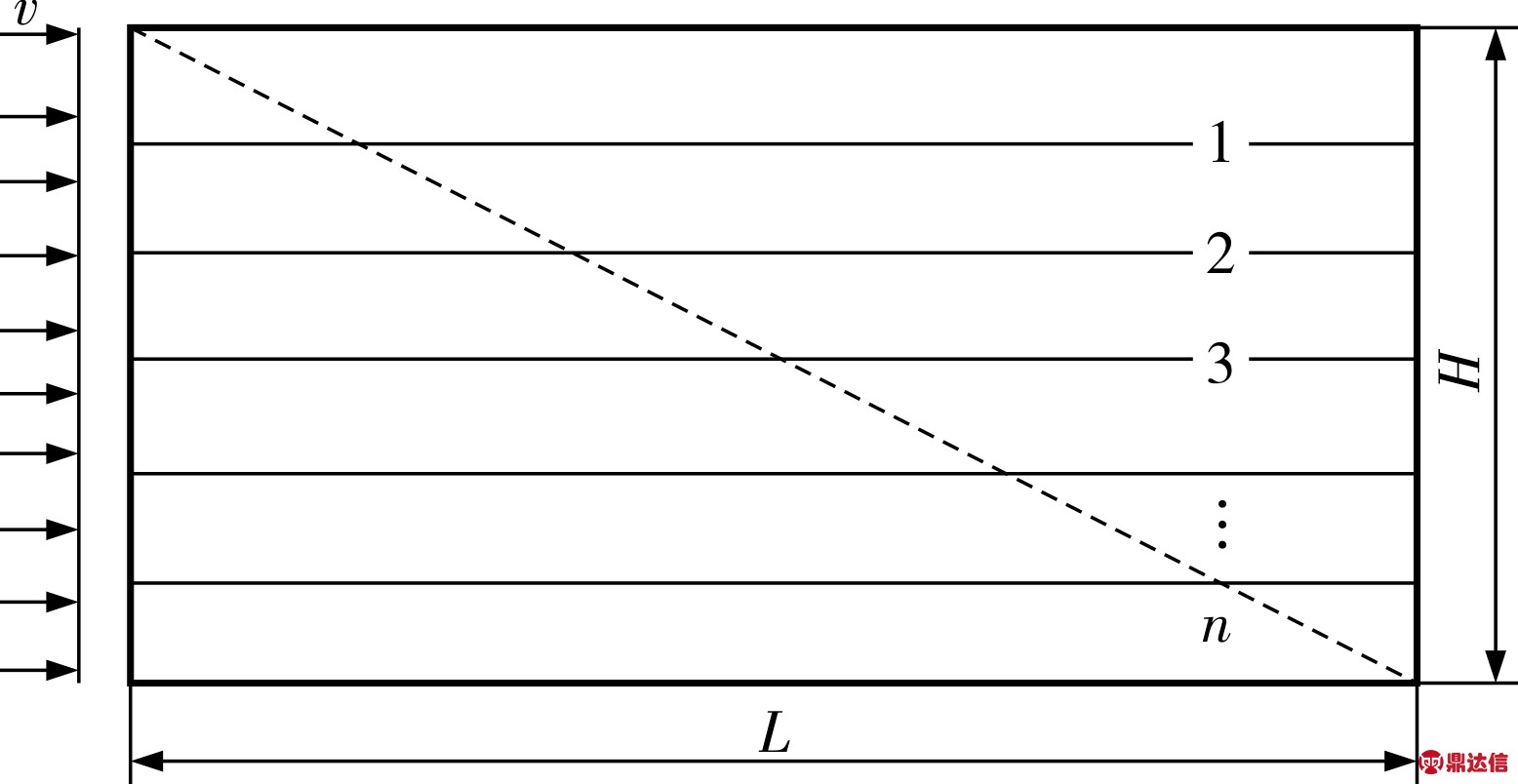
图5 浅池原理示意图
v——液滴运动水平速度; L——池长;
H——池深; n——分层数
由相关实验研究结果表明,分离器聚结构件性能的影响因素主要有聚结板的结构形式、板长度、板间距、倾斜角度、板间负荷、板面粗糙度及聚结板材料等。侯先瑞的研究结果表明,合适的孔隙率、符合分离器空间的板长度和板组数目、较为稳定的亲油性材料、较大的板面粗糙度、合理的聚结负荷,都会提高聚结构件的分离性能,加快油水分离过程[18]。
针对国内外聚结构件的研究,在结构形式上,英国Fram公司在20世纪70年代初期研制了一种聚结构件分离器(由玻璃纤维材料制成),该构件采用V形布置,板上开有液孔,油滴聚结后能穿过孔板汇聚。张黎明等对常见的平行波形板、蛇形背向平行板及交错搭接波纹板等进行了数值模拟和实验验证,发现随着板间流量的增大,聚结板分离效果下降,出现对粒径选择性的单一分离作用[19]。在材料方面,王敏等在镀锌板表面涂上一层亲油性涂料作为聚结板,除油效果良好,耐腐蚀,工作性能稳定[20]。张鹏飞等则是将亲油性材料聚丙烯一面进行氧化处理使之具有亲水性,另一面不作处理,实验发现安装有这种聚结构件的分离器比普通聚结构件分离器的分离效率提高了25%,处理流量也提高了40%[21]。
5 存在的问题
经过多年的发展,目前三相分离器的分离效率不断提高,运行性能不断改进,但仍然存在着许多尚未完全解决的问题,主要分为常规性问题和潜在运行问题。因三相分离器对油田工程的重要性,这些问题的解决也是迫在眉睫,对于油田产油率和经济效益的提高至关重要。
目前存在的常规性问题主要有:
a.分离效率低下。随着油田开采进入中后期,由于水驱采油和地下水的渗入,采出液含水率大幅提高[22],致使原分离器的分离性能无法满足分离要求,分离效率下降。
b.适应范围窄,抗波动能力差。目前的分离器都是根据某一个具体的油田专门设计的,仅考虑了油田的实际开采条件和采出液的成分性质,普遍适用性较差,因此很难直接应用于其他油田。
c.设备体积庞大。一般的三相分离器体积都比较大,尤其是卧式,如果应用在空间稀缺的海洋平台,则经济性和实用性都不理想[23]。
d.设计依靠经验。目前来说三相分离器还没有行之有效的统一的国家设计标准,设计时往往依靠设计者的实际工作经验进行验证。
通过深入研究油气水三相分离器结构、分离物料和国内外的相关前沿发现,除了上述常规性问题之外,运行时还可能存在一些潜在问题,主要包括:
a.泡沫原油。原油中含有的CO2、矿物有机物及无机物等杂质都会引起原油泡沫。
b.石蜡。集液区的聚结构件和气出口处的捕雾装置会因为石蜡的堆积而影响性能。
c.砂子。采出液从地下采出后难免混有砂子等固体杂质,容易引起阀门失灵、聚结构件等内部构件损伤。
d.乳状液。乳状液是一种稳定的油水混合物,在单纯的重力作用下不能实现分离。乳状液的形成条件包括两种互不相溶的液体和乳状剂(稳定剂),并且需要充分混合,使得非连续分散相均匀分散于连续相中。
e.液体携带。游离液体伴随着气相从分离器逸出时会发生液体携带,导致仪器指示高液位,且会损害内部构件,产生泡沫,堵塞油水出口或者流量超过容器设计值。
f.气窜。游离气体伴随着液体一起流出时会发生气窜,导致指示液位偏低,产生不利于油水分离的涡流,造成液位控制失灵。
g.液体段塞。在两相流管线的低点非常容易存积液体,当这部分液体液位升高到阻碍气体流动时,液体就会因为在管路里被气体推进而形成段塞。
6 三相分离器的研究重点和发展趋势
从目前油气水三相分离器的研究现状来看,未来高效三相分离器的发展主要集中在以下4个方面:
a.针对分离器入口构件、整流构件及聚结构件等内部构件,研究新材料、新结构和新技术,提高相关构件工作性能,并尽可能减小构件尺寸,实现轻量化、经济性。
b.从整体设计层面来看,分离器设计更加合理规范化,形成行之有效的统一的国际设计标准,摆脱设计依靠经验的桎梏。
c.重力场中的聚结机理理论分析体系更加完善,相关理论催生的新型聚结构件可以缩短分离时间,提高分离效率,降低人力物力成本。
d.除了重力场之外,大力发展离心场、电场中的聚结分离,研究新型三相分离器将重力、离心、电脱、化学方法、生物分离、气浮及吸附等结合,综合各种技术提高分离效率。
总的来说,科学技术和人的认知是不断进步的,随着人们对于分离器机理的研究和分离技术的创新,在未来,普适性强、结构紧凑且方便维护维修的新型高效三相分离器的设计研制将成为国内外相关领域专家学者和工程技术人员研究的重点。