摘 要:劣质煤可用于循环流化床(CFB)燃烧。多个并联分离器布置的方式被广泛地应用于循环流化床锅炉实现气固分离,然而这种布置方式容易出现造成气固两相流的不均匀分布,以及并联分离器性能的差异。在300 MW循环流化床锅炉上开展了实验研究,对比了并联的3台分离器的压降、分离效率、以及其内的燃烧现象。研究发现,中间位置的分离器具有更大的压降以及更高的分离效率,这与中间分离器具有更大的烟气流率有关。而对比并联布置的返料阀和立管的压降发现中间分离器具有更小的颗粒流率,这不利于燃烧以及炉内脱硫。此外,由于不均匀的气固两相流,中间位置分离器内烟气温升明显高于两侧分离器。
关键词:循环流化床锅炉;并联分离器;压降;分离效率
分离器内高效稳定的气固分离是保证循环流化床锅炉稳定运行的关键[1-2]。现阶段,由于锅炉装机容量不断增大,单一分离器不能保证较高的分离效率,工程上通常采用多个并联的分离器,并辅以多个并联的立管和返料阀,实现锅炉的稳定物料循环。世界首台超临界循环流化床锅炉由福斯特惠勒公司设计,该锅炉采用8台并联布置的分离器;而目前世界上投运的容量最大的白马600 MWe循环流化床锅炉采用6台并联布置的分离器。需要注意到,这种布置特点难以保证气固两相在多个并联分离器内的均匀布置,导致系统的总的分离效率降低[3-4]。此外,这种不均匀分布的气固两相流同样会造成炉膛出口悬吊屏的不同程度的磨损[5-6]。
针对并联分离器内不均匀分布的气固两相流动行为,学者开展了一系列的理论和实验研究。Grace[7]最初提出了并联分离器系统内气固流动的多解方程,Mo等[8]在该理论基础上分析了分离器结构对该多解方程的影响。需要注意到,理论分析并未考虑炉膛内气固流动行为以及连接多个并联分离器的尾部集箱布置方式的影响。早期研究发现并联分离器H型布置特点可能对600 MW循环流化床锅炉中气固流动行为存在重要影响[9]。此外,部分学者在冷态循环流化床台架上开展了该课题的研究[10-16]。考虑到冷态循环流化床台架与实际锅炉的巨大差别,这些研究结论是否适用于循环流化床锅炉还需要进一步验证。多个分离器的布置往往造成中间位置的分离器入口偏离中心位置,这可能造成炉膛出口烟气的横向扩散[17]。工程上,通常布置多个悬吊屏限制分离器入口非均匀布置导致的横向扩散。
本文在国内某台300 MW单炉膛三分离器并联布置的循环流化床锅炉上,基于压降、烟气温度变化以及循环灰的粒径,对比研究了3台并联分离器的性能差异。并结合返料阀和立管压降的分布,表征了气固两相在3个并联分离器内的分布。
1 实 验
锅炉主体结构如图1所示。炉膛底部采用收缩口结构,保证二次风有较好的穿透深度。炉膛稀相区截面为(8.4×28.2) m2,炉膛高度为40.2 m。在炉膛的后墙布置了3个并联分离器,其中中间位置的分离器B的入口并不是布置在炉膛的中心线上。为了限制B分离器入口不均匀布置造成的烟气横向扩散,从左至右均匀布置了两道悬吊屏。
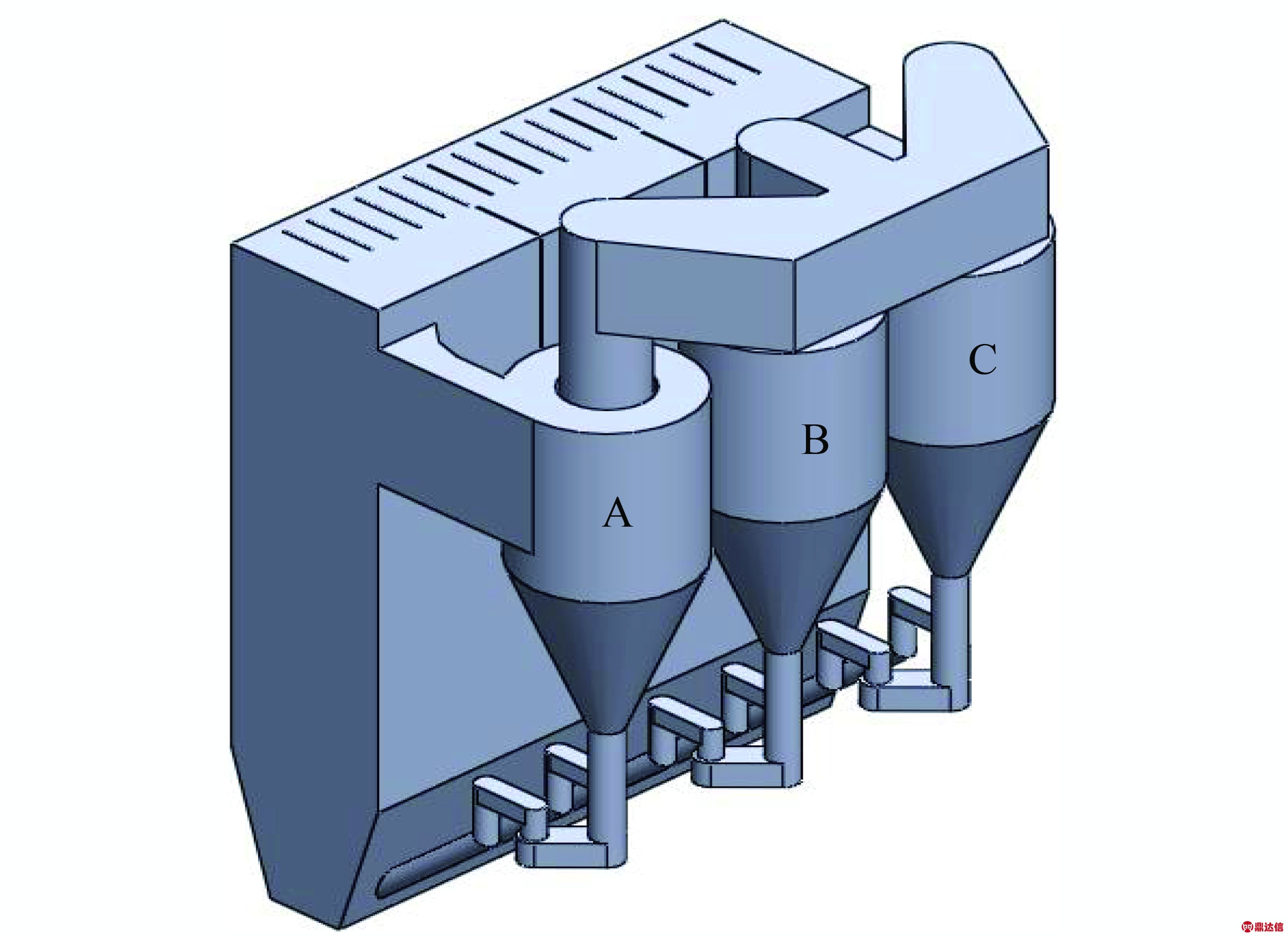
图1 锅炉主体结构
Fig.1 Schematic diagram of CFB boiler
实验过程中一次风量(340~360(kN·m3)/h)、二次风量(440~500(kN·m3)/h)以及投煤量(180~200 t/h)基本保持稳定。实验中调整锅炉排渣流率改变炉膛内床压,研究不同床压下3个并联分离器的性能。实验中燃料为烟煤和煤矸石的混合物,燃料特性见表1。
表1 燃料工业分析和元素分析
Table 1 Proximate analysis and ultimate analysis of fuel %

2 试验结果和讨论
分离器压降是表征分离器性能的关键参数。一般来说,更大的分离器压降有助于提高分离效率,然而过大的分离压降会降低颗粒循环流率,导致炉膛稀相区热负荷不足。如图2所示,3个分离器的压降分布呈现出中间分离器高、两侧分离器压降低的特点。这种压降分布特点表明中间分离器具有更大的烟气入口速度。床压增大时,炉膛密相区升高,导致气体的夹带率提高,增大颗粒循环流率。床压变化时,分离器压降有不同程度的变化,表明颗粒循环流率影响气固两相在并联分离器内的分布。
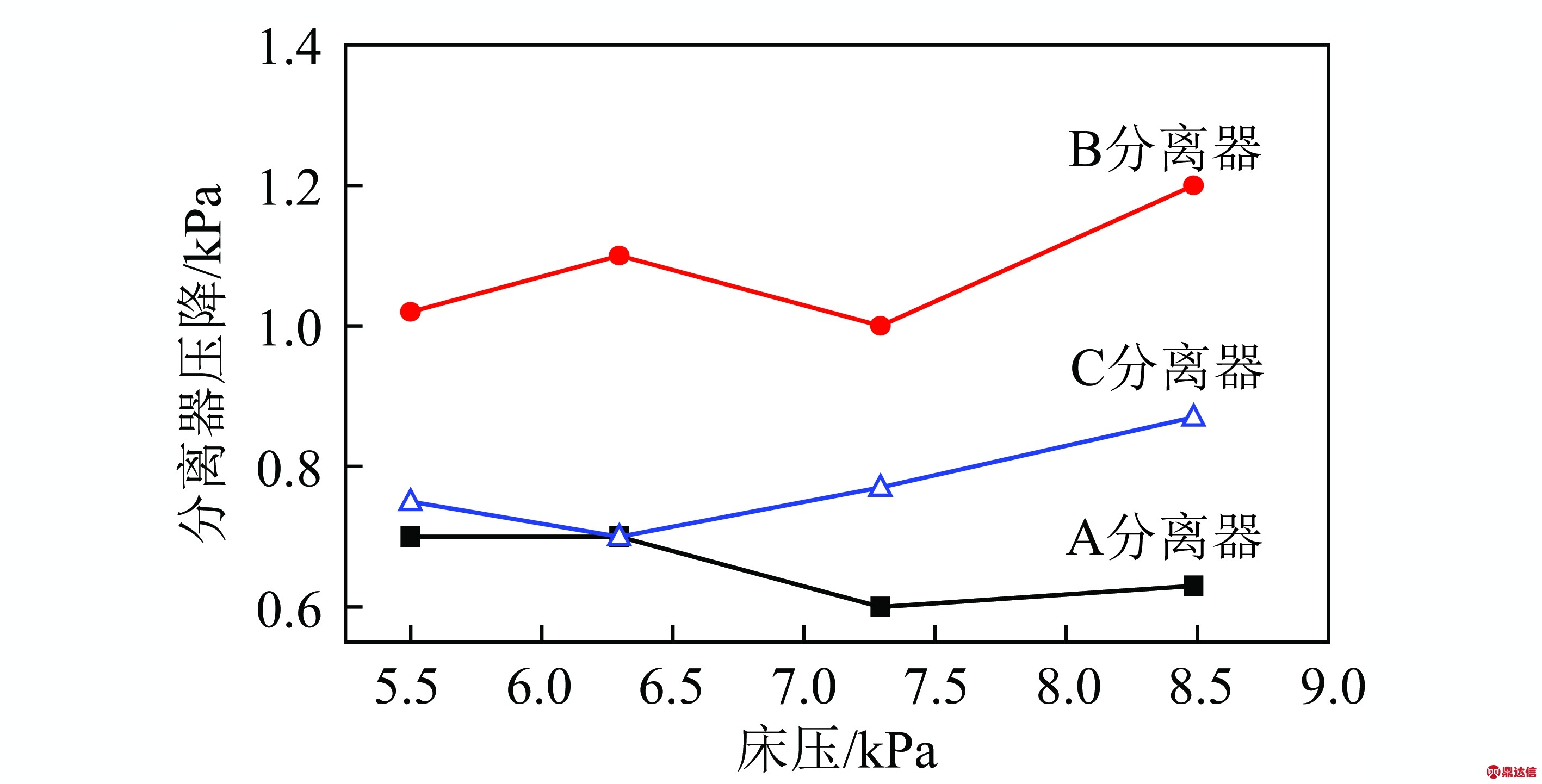
图2 并联分离器压降分布
Fig.2 Pressure drop of parallel cyclones
廖磊等[11]研究了6分离器并联布置循环流化床内分离器性能,并发现同侧墙的3个分离器中间分离器具有明显更小的压降,而Yang等[10]和Zhou等[12]并未发现明显的分离器压降分布的差异,其实验中分离器压降较小,导致压降分布的趋势不明显。廖磊等[11]实验中提升管高度只有5.8 m,而流化风速高达4 m/s,这导致提升管颗粒出口区域的颗粒浓度远高于循环流化床锅炉炉膛出口颗粒浓度。提升管出口区域的颗粒浓度对并联分离器的压降分布有重要影响[8]。分离器压降随颗粒浓度的增加呈现先下降后上升的非单调变化的特征[18-19]。由于提升管出口颗粒浓度较大,CFB反应器的运行区域一般对应于拐点右侧区域;而CFB锅炉的运行区域对应于拐点左侧区域。如图3所示,O和O′对应于气固两相在并联分离器内均匀分布的情况。然而由于流动边界层的影响,中间位置的分离器具有更大的入口气体速度(对应于A和A′),这导致CFB锅炉和CFB反应器并联分离器压降分布呈现不同的分布规律。
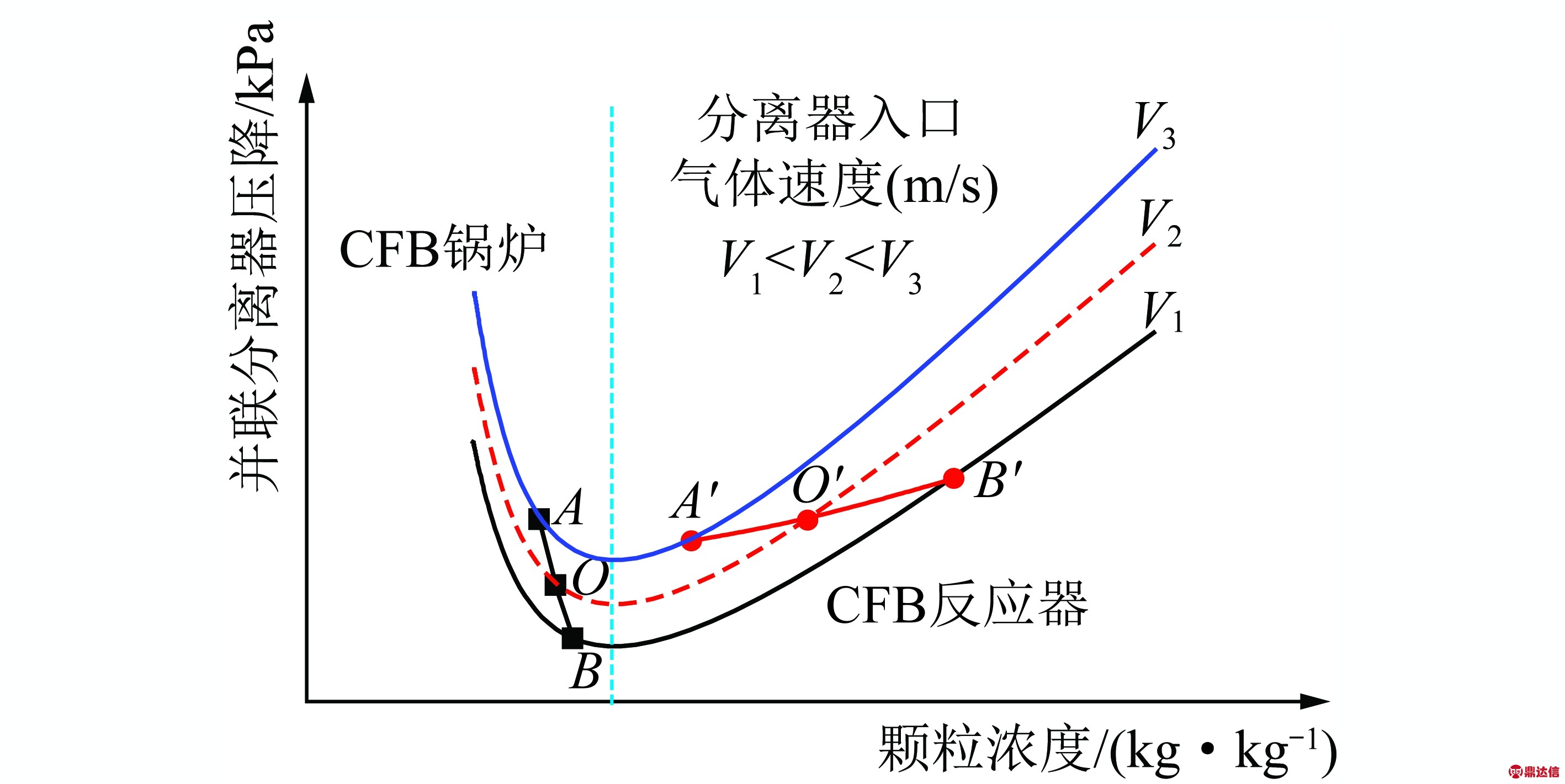
图3 颗粒浓度对并联分离器压降的影响
Fig.3 Effect of solids loading on the pressure drop of parallel cyclones
分离器内燃烧导致的烟气温升影响过热器和再热器的吸热份额。锅炉采用气冷式分离器,设计过程中一般允许存在30 ℃的温升。而对于燃用无烟煤以及采用绝热型分离器的CFB锅炉,温升幅度更高[20]。如图4所示,3个并联分离器内燃烧导致烟气的温升明显不同。中间分离器的温升远高于设计值,而两侧分离器的温升幅度较小。并联分离器内燃烧依赖于气固两相的分布,中间分离器较高的温升进一步说明气固两相在并联的3个分离器内分布的不均匀。
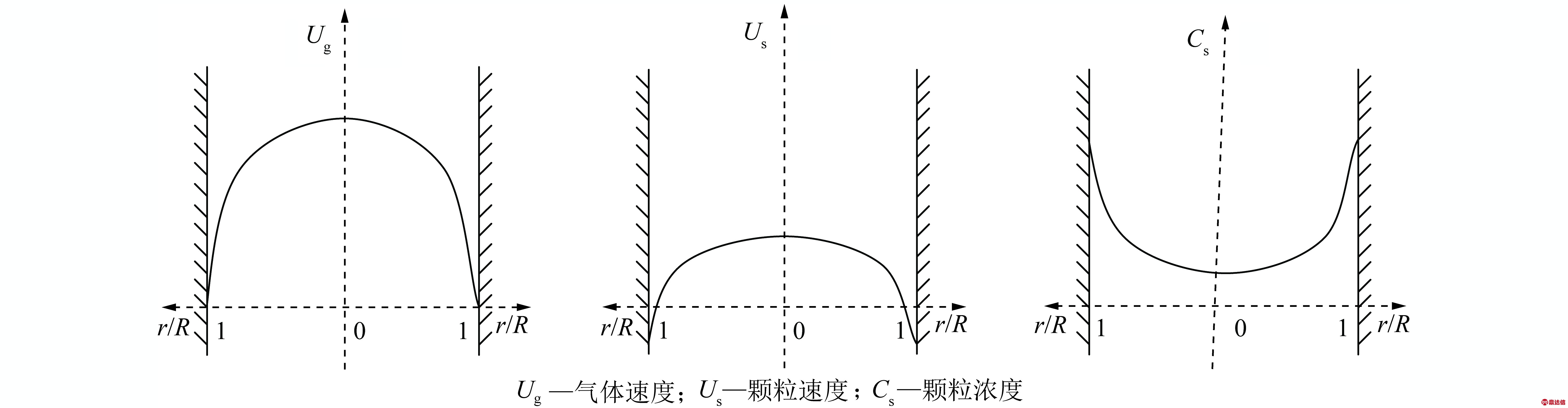
图4 并联分离器内烟气温升分布
Fig.4 Temperature increase in the parallel cyclones
在实验关停后,采取了3个返料阀中循环灰样进行马尔文激光粒度分析。如图5所示,循环灰的粒径分布呈现出单峰分布的特征,循环灰粒径在0~300 μm。受制于颗粒终端速度,大于300 μm的颗粒并未参与物料循环。此外,3股循环灰的峰值粒径分别为103.7,92.6,98.5 μm,这说明中间分离器具有更高的分离效率,这与并联分离器压降分布的规律符合。因为中间分离器的入口风速增加会使得分离效率变高。
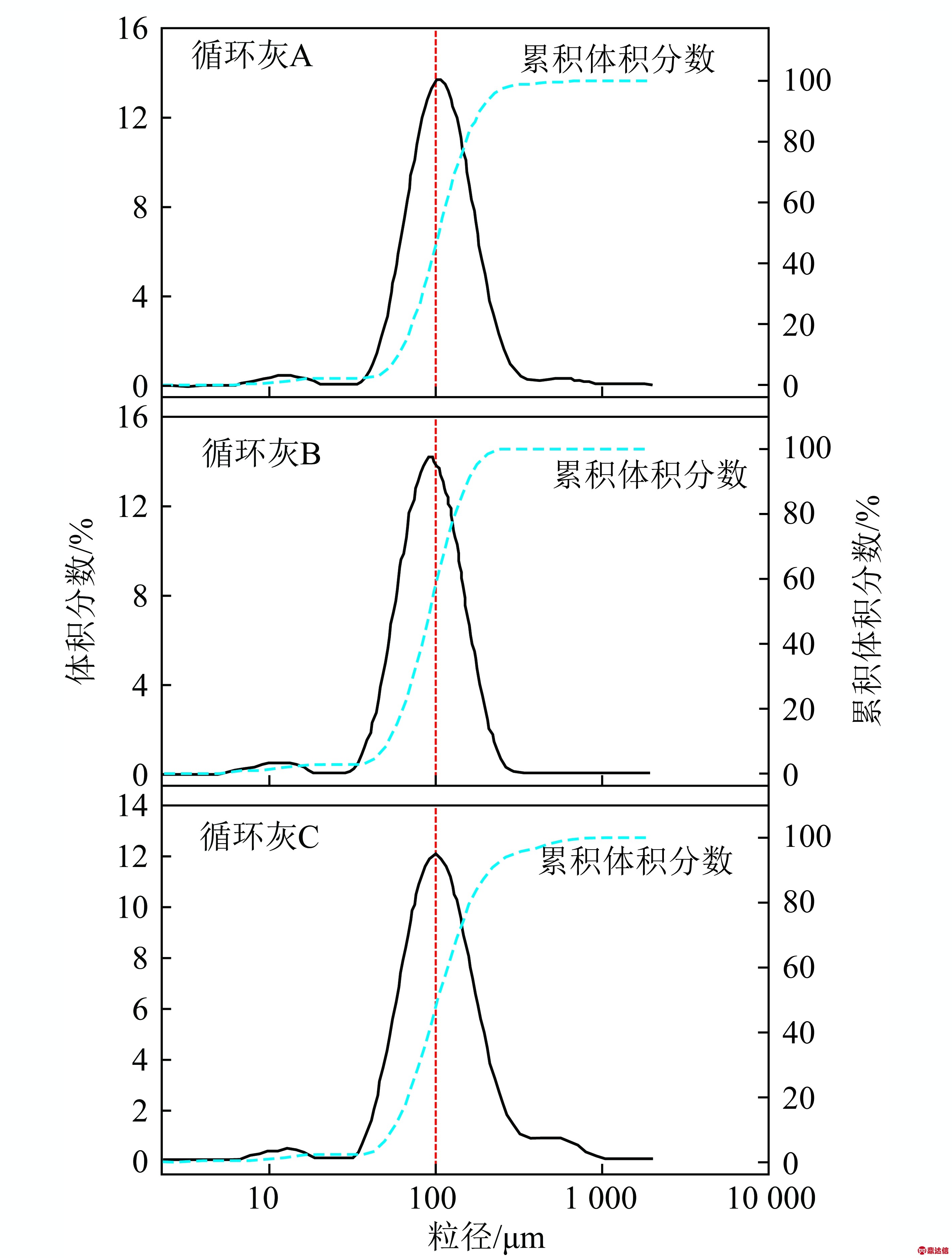
图5 循环灰粒径分布
Fig.5 Size distribution of circulating ash
在高压流化风稳定时,返料阀的压降取决于返料流率。如图6,7所示,中间返料阀具有较两侧的返料阀明显更小的压降,而且中间立管压降明显小于其他两个料腿中的压降,这表明中间回路的循环流率较小。
考虑到中间分离器具有更高的分离效率,因此可以推断中间分离器的入口颗粒流率较两侧小,这验证了图3中CFB锅炉分离器中气体流速和颗粒流率对
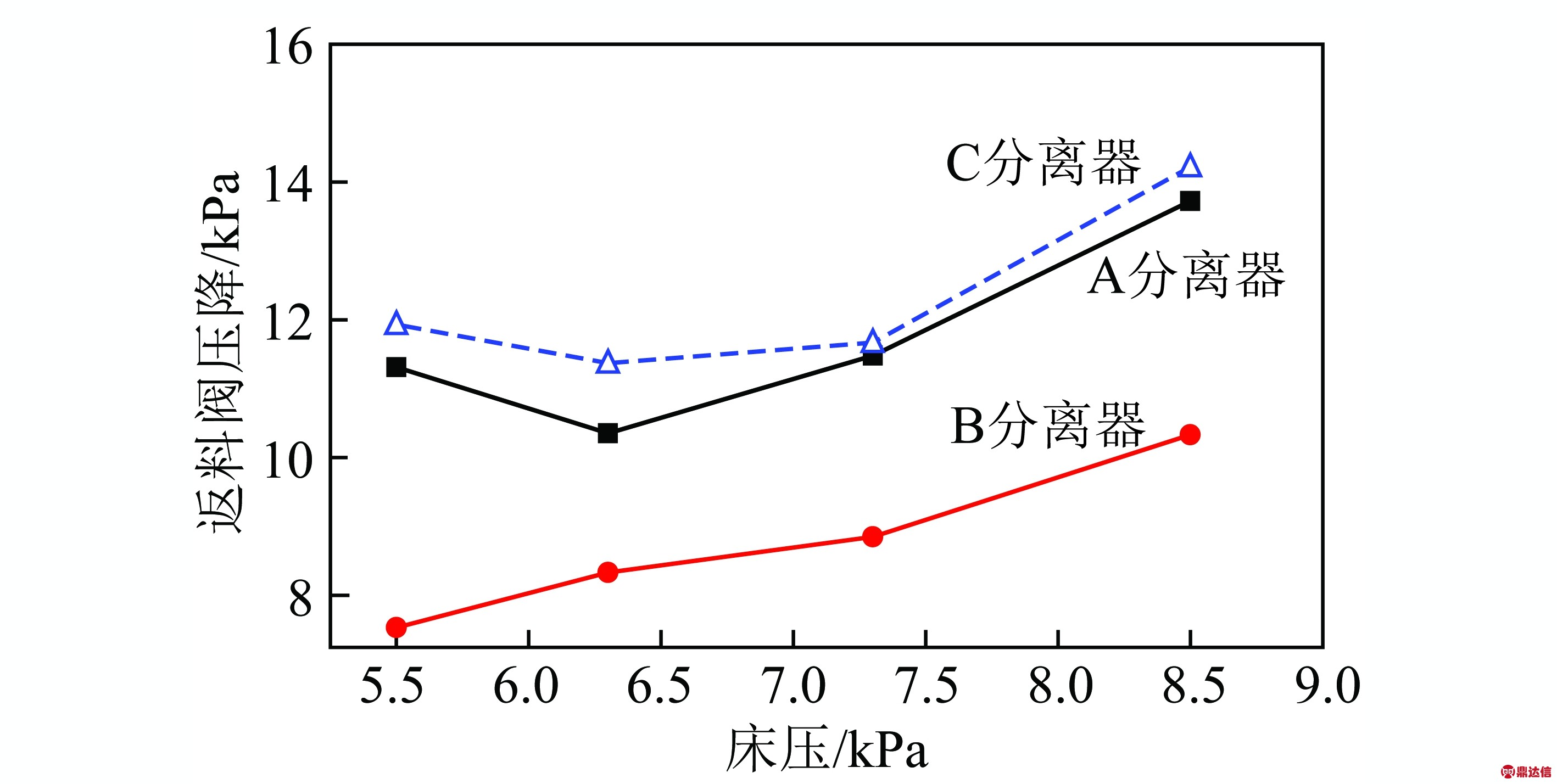
图6 并联返料阀压降分布
Fig.6 Pressure drop in parallel loop-seals
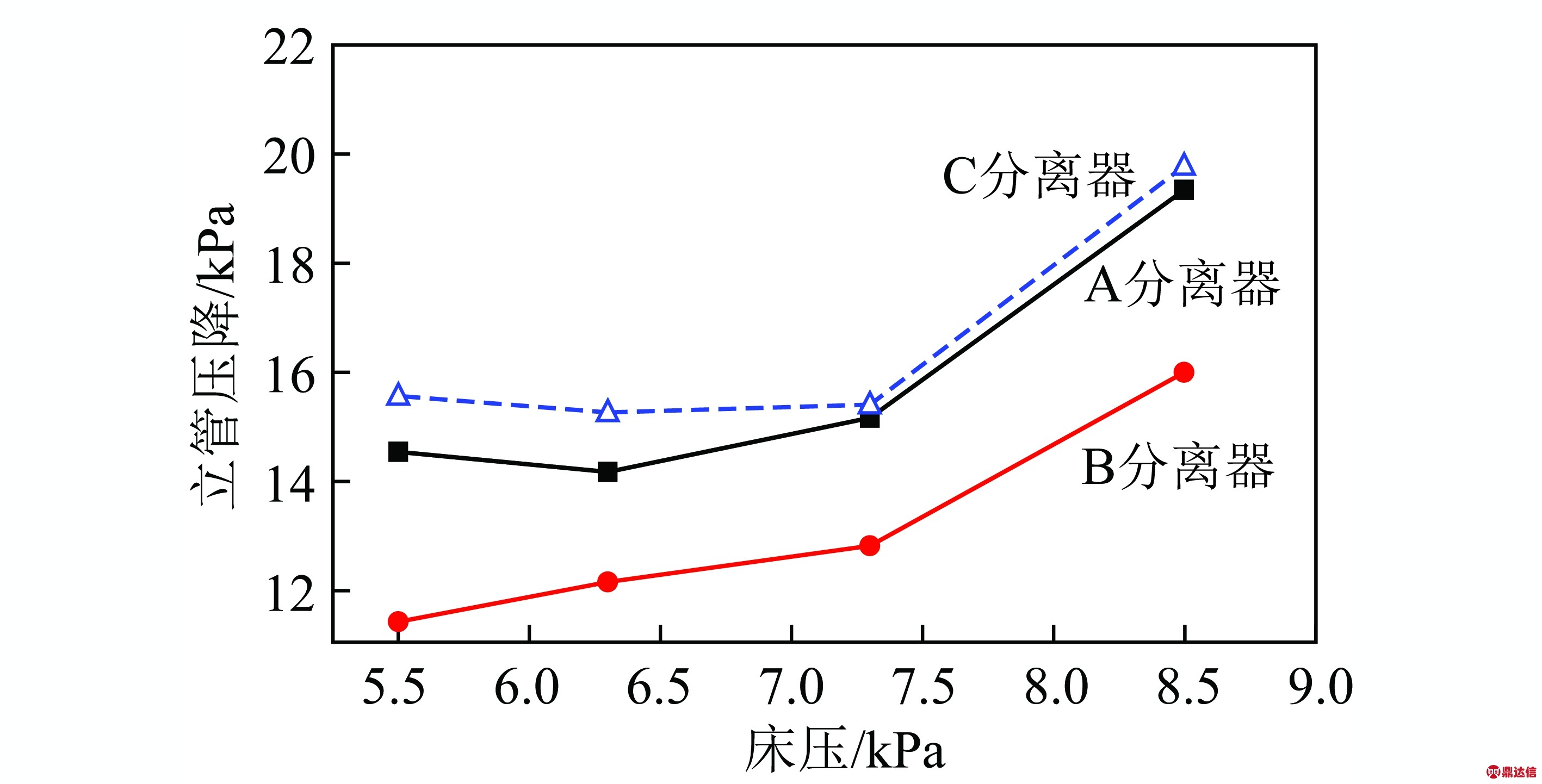
图7 并联立管压降分布
Fig.7 Pressure drop in parallel standpipes
压降影响关系。此外,颗粒循环流率随着床压的增大而增大,导致返料阀和立管的压降增大。
尽管学者开展了许多关于并联分离器内的气固不均匀分布的实验研究,然而这些研究大部分基于冷态循环流化床台架,与实际锅炉的运行存在较大的差异。此外,实际锅炉并联分离器内何种不均匀分布对锅炉的运行影响较小,抑或通过改造分离器等结构从哪个方面衡量改造效果,这些考虑是工业界最关心的实际问题。而以上这些关切需要考虑炉内气固两相在径向的非均匀分布。
已有研究表明受壁面流动边界层的影响,炉内气固两相径向分布具有不均匀分布的特点[24-26]。如图8所示,壁面区域向上的气体速度较小,不足以支撑颗粒向上流动,该区域的颗粒浓度较高。由于该贴壁高浓度的向下颗粒流容易造成水冷壁的磨损,通常沿水冷壁的高度方向布置一些防磨梁。相比壁面区域的气固流动行为,中心区域向上的气体速度大,导致颗粒被扬析夹带逃离锅炉。此外,中心区域向上的颗粒流浓度远小于壁面向下流动的颗粒流,可能导致炉膛底部中心区域的燃烧不均匀和脱硫效率的降低。
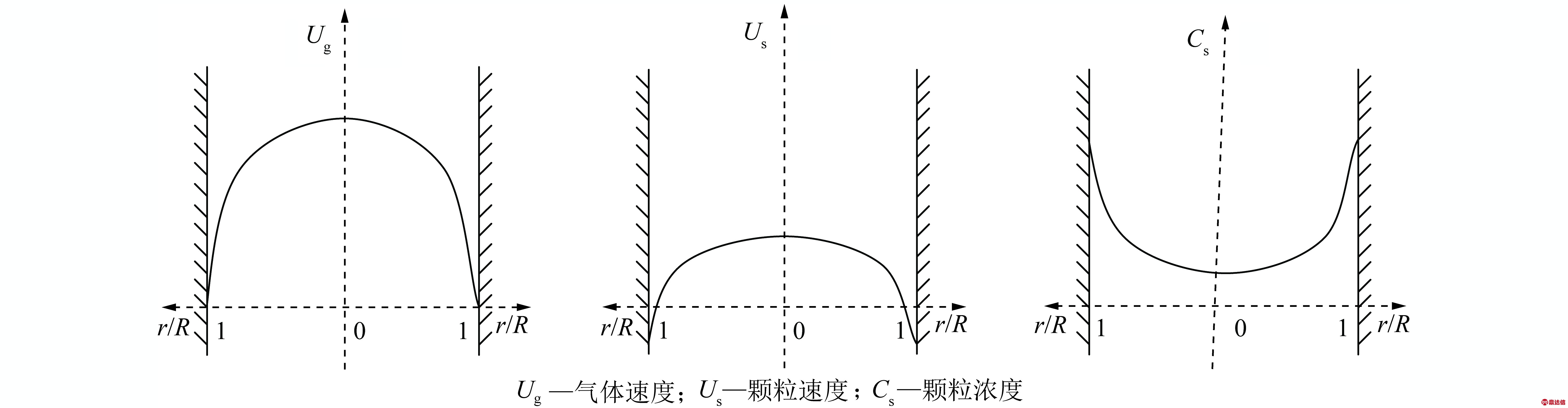
图8 炉内气固两相径向非均匀分布
Fig.8 Non-uniform radial distributions of gas-solid flow in the furnace
中间返料点的颗粒流率较两侧小,不利于缓解颗粒浓度沿横截面的不均匀分布。若通过分离器结构的改造,能够使得中间返料点的颗粒流率稍微大于两侧返料点的颗粒流率,这更有利于炉内横截面颗粒浓度的均匀分布,进而提升炉内脱硫效率以及提升燃烧效率。
3 结 论
(1)与两侧分离器相比,3台并联分离器的中间分离器具有更大的压降和更高的分离效率。并联分离器性能的差异与气固两相流在并联分离器的分配有关。中间分离器具有更大烟气流率以及更小的颗粒流率。
(2)由于不均匀的气固分布,并联分离器内燃烧程度不同。中间分离器内燃烧导致的烟气温升明显,较两侧分离器更高。
(3)并联分离器的性能差异同样影响返料阀和立管的压降。由于中间分离器较小的颗粒流率,中间位置的返料阀和立管具有更小的压降。