摘要:旋流分离器目前已作为一种高效节能的新设备进入含油污水处理的工业应用阶段。借助于计算流体动力学(CFD)的方法,得到了两种旋流分离器内切向速度分布、轴向速度分布,以及变流量下的压力曲线与效率曲线。结果表明:同向出流旋流分离器的倒锥在旋流腔和大锥段上部,对切向速度的影响不大,在大锥段的下半部分,从截面Ⅱ开始,双锥旋流分离器的切向速度迅速下降,而同向出流旋流分离器的倒锥结构使得切向速度维持在一个较高水平;在旋流腔和大锥段,双锥旋流分离器的轴向速度要大于同向出流旋流分离器的轴向速度,同向出流旋流分离器的倒锥结构没有使轴向速度增加,倒锥结构对切向速度影响更明显。同向出流旋流分离器的底流出口截面尺寸小,故其压力损耗大,同向出流旋流分离器的内置倒锥结构对旋流腔和锥段的压力损失影响较小。两种结构旋流器的简化效率曲线表明,双锥旋流分离器比同向出流旋流分离器更适应处理量相对较低的情况,其处理范围更广。
关键词:污水处理;旋流分离器;同向出流;双锥;速度;压力
目前,石化炼油厂含油废水还普遍采用能耗高、油水分离时间长、占地面积大的“老三套”处理方案,处理过程中极易产生污染大气的浮渣[1]。中石化长岭分公司的延迟焦化系统可利用旋流除油技术将含油污水分离,分离出的污油回炼,处理后的水作为切焦和冷焦用水。该系统节省了污水处理费,减轻了企业污水处理厂负荷,实现了含油污水零排放的目标[2]。随着废水排放负荷加重及废水中污染物成分的日趋复杂,作为高效节能环保设备的水力旋流旋流分离器得到广泛应用。
计算流体动力学和计算机科学的迅速发展,为采用数值模拟方法解决流体力学问题提供了极大的便利[3],同时计算机数值模拟也已成为研究旋流分离技术的主要方法之一。数值模拟技术不仅可降低研究成本、提升研发速度,还可充分认识旋流分离器内的流场和流体流动规律,因此对于旋流分离技术研究人员来说,学习和掌握数值模拟的研究与使用方法非常重要[4-5]。
水力旋流分离器的主要优点包括结构简单、紧凑,分离器内部无运动部件,且在理想工况下分离效率高。水力旋流分离器的原理是利用不互溶多相流间不同相的密度差来进行分离。随着基础理论研究和测试技术的不断进步,许多学者对旋流分离器做了很多研究工作,希望在保证不降低其分离效率的前提下,最大限度地降低能耗,提高其使用范围,以达到增产节能的目标[6]。
针对双锥旋流分离器与同向出流旋流分离器这两种模型,借助于计算流体动力学(CFD)数值方法,分别研究了处理量变化对旋流分离器运行速度、压力降以及分离效率等分离特性的影响规律,以探究两种旋流分离器的处理量适用范围。
1 模型尺寸与参数设置
研究基于以往优化设计的一种双锥型油水旋流分离器(其流体域模型如图1a所示),以及一种同向出流油水旋流分离器(其流体域模型如图1b所示),均采用切向入口形式。两种旋流器的二维尺寸标注分别如图1c与1d所示。针对同种工况,为保持模拟分析结果的对比有效性,将两种旋流器的主直径保持一致,其他主要结构参数设置分别如表1所示。
表1 结构参数设置
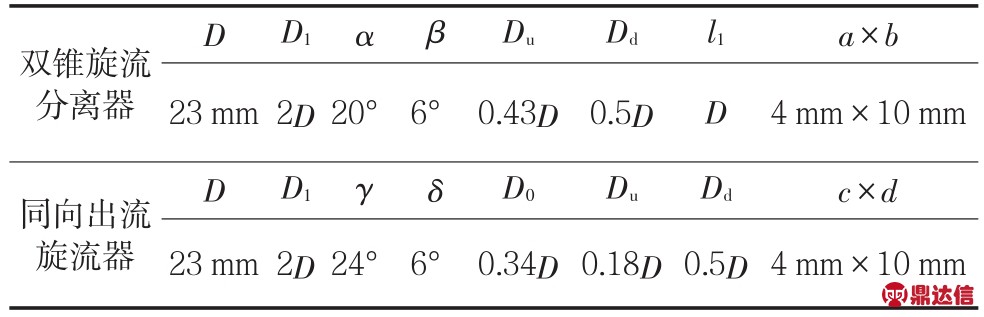

图1 旋流分离器结构
2 网格划分与参数设置
2.1 网格划分
采用三维建模软件SolidWorks进行建模,然后将建立的旋流分离器流体域三维模型导入到FLUENT的前处理器Gambit中进行网格划分。双锥旋流分离器网格划分如图2a所示,同向出流旋流分离器网格划分如图2b所示。相比于非结构网格,结构网格在计算中更精确,收敛性也更好[7],因此本研究采用铜钱结构化网格划分形式(图2c)。同时,为更好地捕捉边界特征以及提高网格划分精度,采用分段网格划分和局部加密的方法,对旋流分离器切向入口、溢流口、旋流腔和底流口进行分段划分,并对溢流口局部网格进行加密处理。
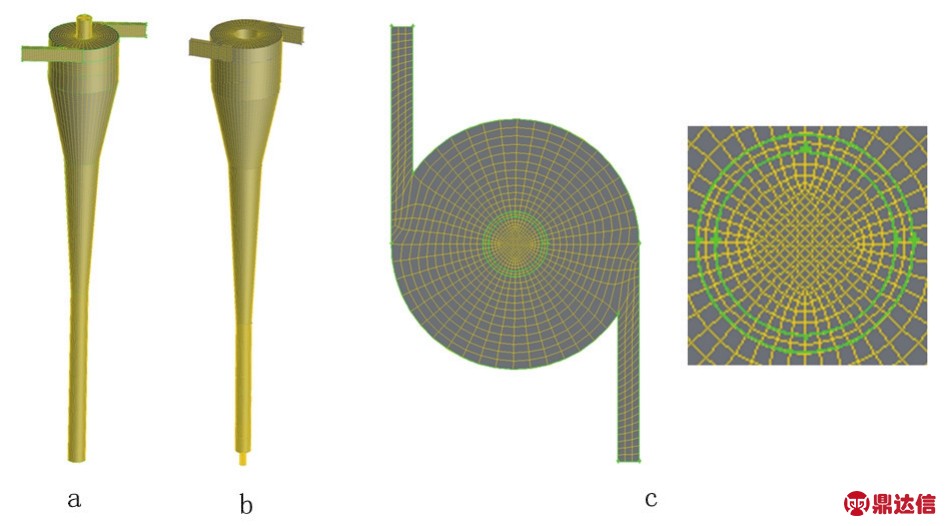
图2 网格划分
2.2 介质物性参数及初始条件设置
数值模拟流体介质为油水混合物,水相的密度为998.2 kg/m3,动力黏度为0.001 1 kg/(m·s);油相的密度为870 kg/m3,动力黏度为0.72 kg/(m·s)。湍流模型采用雷诺应力模型,多相流模型采用混合相模型。选择速度入口为入口边界条件,入口油相体积分数为10%,处理量为3.0 m3/h,入口法向速度分量由入口流量与总入口横截面积确定,其计算式择自由出流为出口边界条件[8],壁面边界无滑移、不可渗漏,残差精度设置为1×10-7。
处理量Q为旋流器的主要操作参数之一,在旋流器几何结构一定时,其具有一个最佳的处理量变化范围。处理量的适度增加有利于液滴向旋流器中心迁移[9],但处理量过高会引起压力损失大、乳化现象严重,不利于分离;处理量过低则会发生流速不够导致不足以形成一定强度的涡旋,也不利于分离[10],故对处理量进行优选对于旋流器的分离具有重要意义。在进行变处理量模拟时,保持分流比不变,对处理量分别为2.5、3.0、3.5、4.0、4.5 m3/h时的分离效果进行数值模拟对比分析。
3 计算结果分析
3.1 速度分布
水力旋流器的切向速度决定了离心力的大小,是分离的关键[11]。水力旋流器的轴向截面速度分布图可反映流场的稳定程度。旋流器内液滴所受离心力及其离心加速度的大小主要是由切向速度的分布状况来决定的,同时切向速度的大小及分布情况也会影响径向速度和轴向速度的分布,因此精确测定并深入分析切向速度分布规律是速度场研究乃至旋流器研究中最主要的基础工作之一[12]。
在对旋流分离器内部速度场分析过程中,设定旋流腔顶部中心为坐标原点,沿着底流口方向为z轴正方向,选取截面Ⅰ(z=40 mm)和截面Ⅱ(z=80 mm)进行研究和对比。在分流比不变的情况下,改变入口流量得出截面Ⅰ、截面Ⅱ双锥旋流器的切向速度分别如图3a、3b所示,截面Ⅰ、截面Ⅱ同向出流旋流器的切向速度分别如图4a、4b所示。
从图3a和4a可以看出,随着流量的增加旋流器内部流体的切向速度均逐渐增大,且近壁处切向速度远大于零,保证了分离的动力。对比图3a与图3b发现,同流量下截面Ⅰ的最大切向速度均高于截面Ⅱ,这是由于截面Ⅱ(位于大锥段)相对截面Ⅰ(位于旋流腔)速度在不断地衰减,图4a与图4b也有相同规律。在靠近轴心附近切向速度接近于零,也表明在越靠近中心的地方,角动量损失越大,这时液滴自身的旋转运动能力比较小,有利于形成稳定的油核。
由图3a和图4a对比可以看出,在截面Ⅰ处同流量下双锥旋流器的切向速度均略高于同向出流旋流器的切向速度;但在截面Ⅱ处,对比图3b与4b时则相反,说明同向出流旋流器内置的倒锥形式一定程度上可以补偿能量损耗。在一定范围内,切向速度越大,越有助于旋流器的分离。
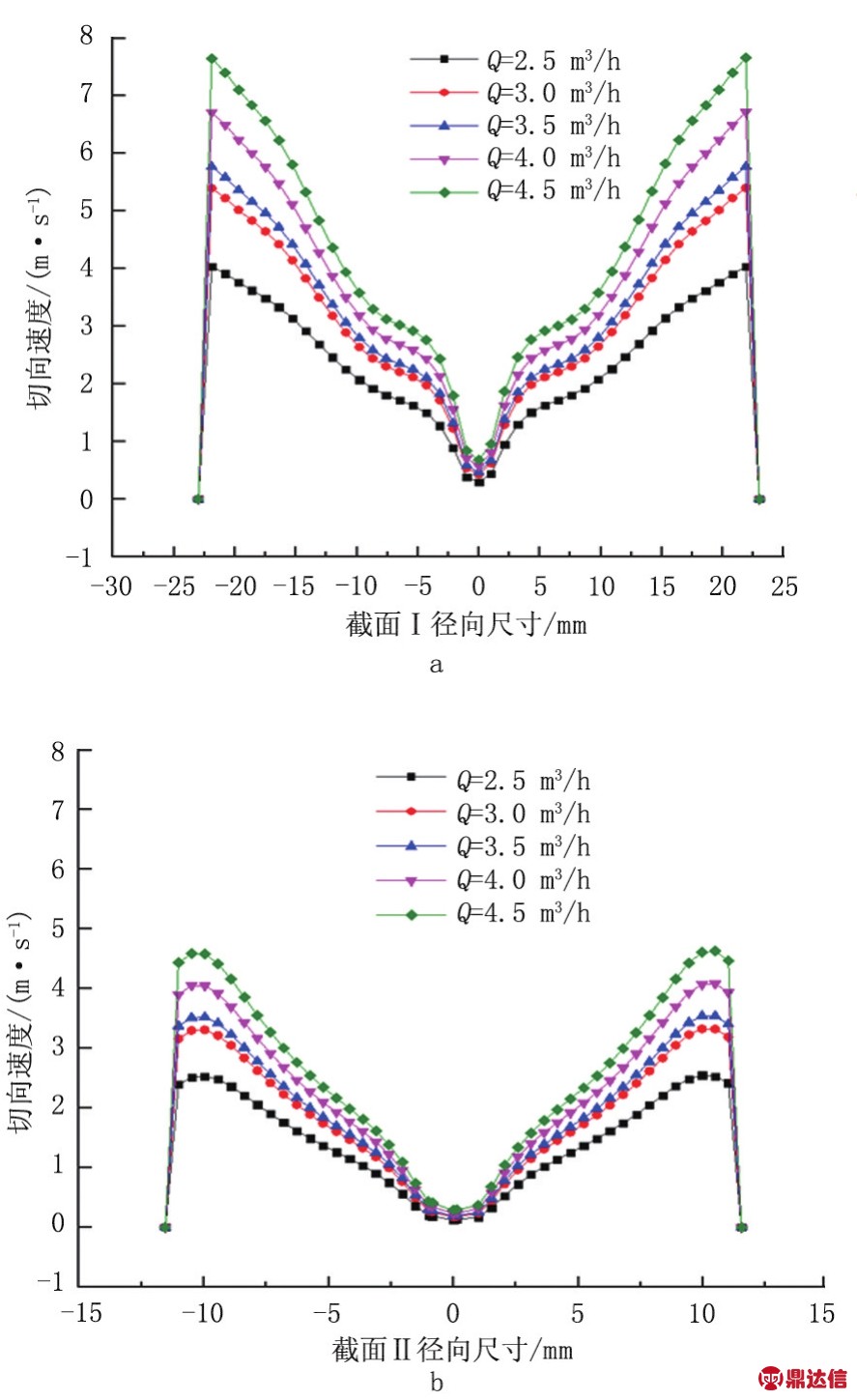
图3 双锥旋流器切向速度分布
轴向速度关系到介质在旋流器中停留的时间,而且轴向速度在旋流分离中还起到重要的输运作用,即连续不断地将已分离的物料输送到相应的出口,以便维持分离的继续进行。
图5a、图6a是两种结构旋流器在截面Ⅰ的轴向速度,图5b、图6b是两种结构旋流器在截面Ⅱ的轴向速度。可以看出无论在哪个截面上,两种旋流器内的轴向速度远小于切向速度。从图5a看出,双锥旋流器在截面Ⅰ径向位置位于±17 mm时,轴向速度出现了第一次变向的现象,轴向速度为0,并在±5 mm处出现了第二次变向,说明零轴速度包络面并非是一个平面,同一水平面会出现两个零轴速位置,呈现“零轴速包络区间”。同向出流旋流器也在接近倒锥的中心处出现了第二次零轴速位置。对比图5a和图6a,同向出流旋流器的轴向速度在靠近边壁处的向下最大速度比双锥旋流器小,说明内置倒锥结构使得径向距离缩小,液滴运移至中心的速度减小。从图5b、图6b可以看出,两种结构旋流器在截面Ⅱ的轴向速度均为向下速度,说明此处已不发生物料的径向运移。
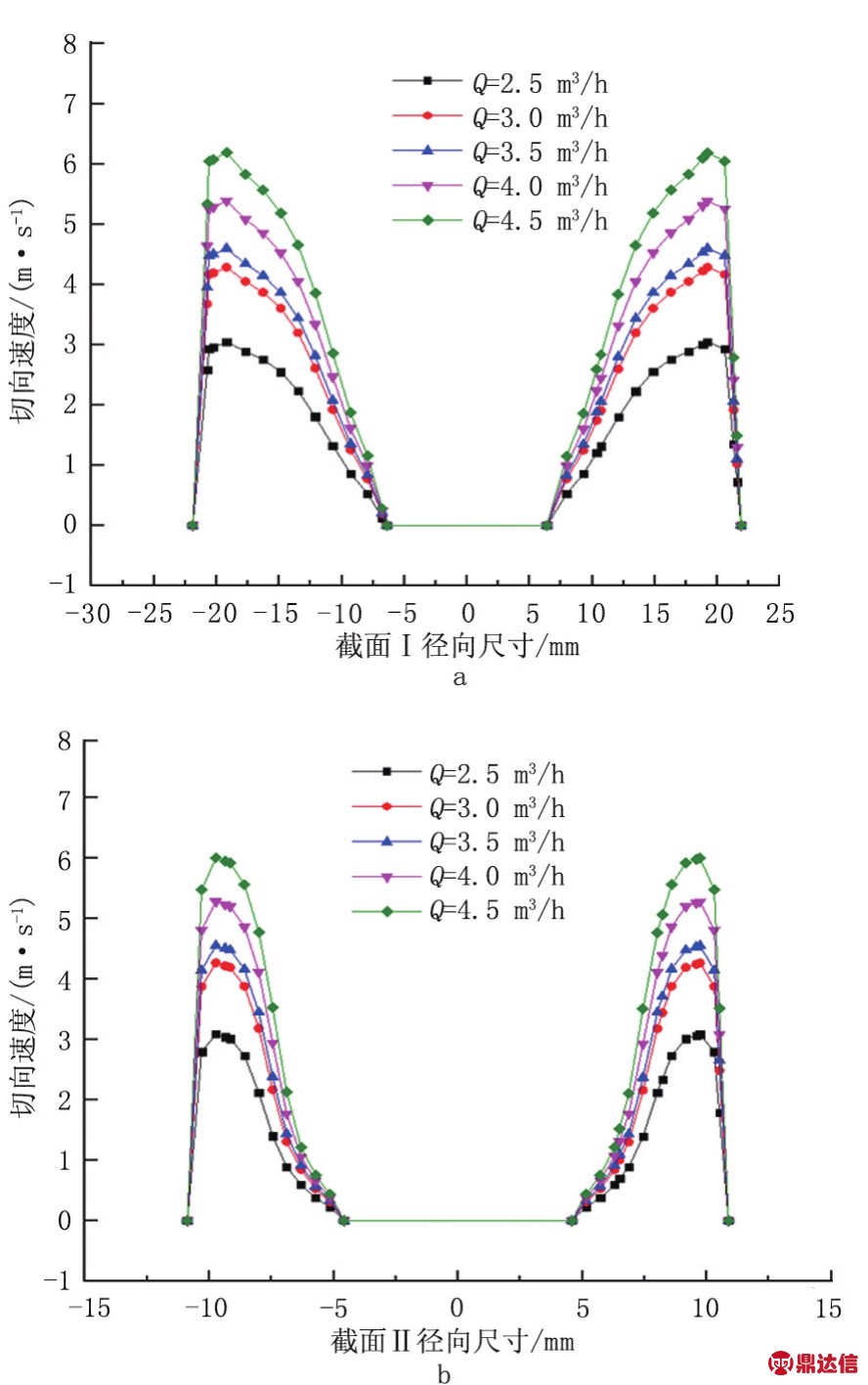
图4 同向出流旋流器切向速度分布

图5 双锥旋流器轴向速度分布
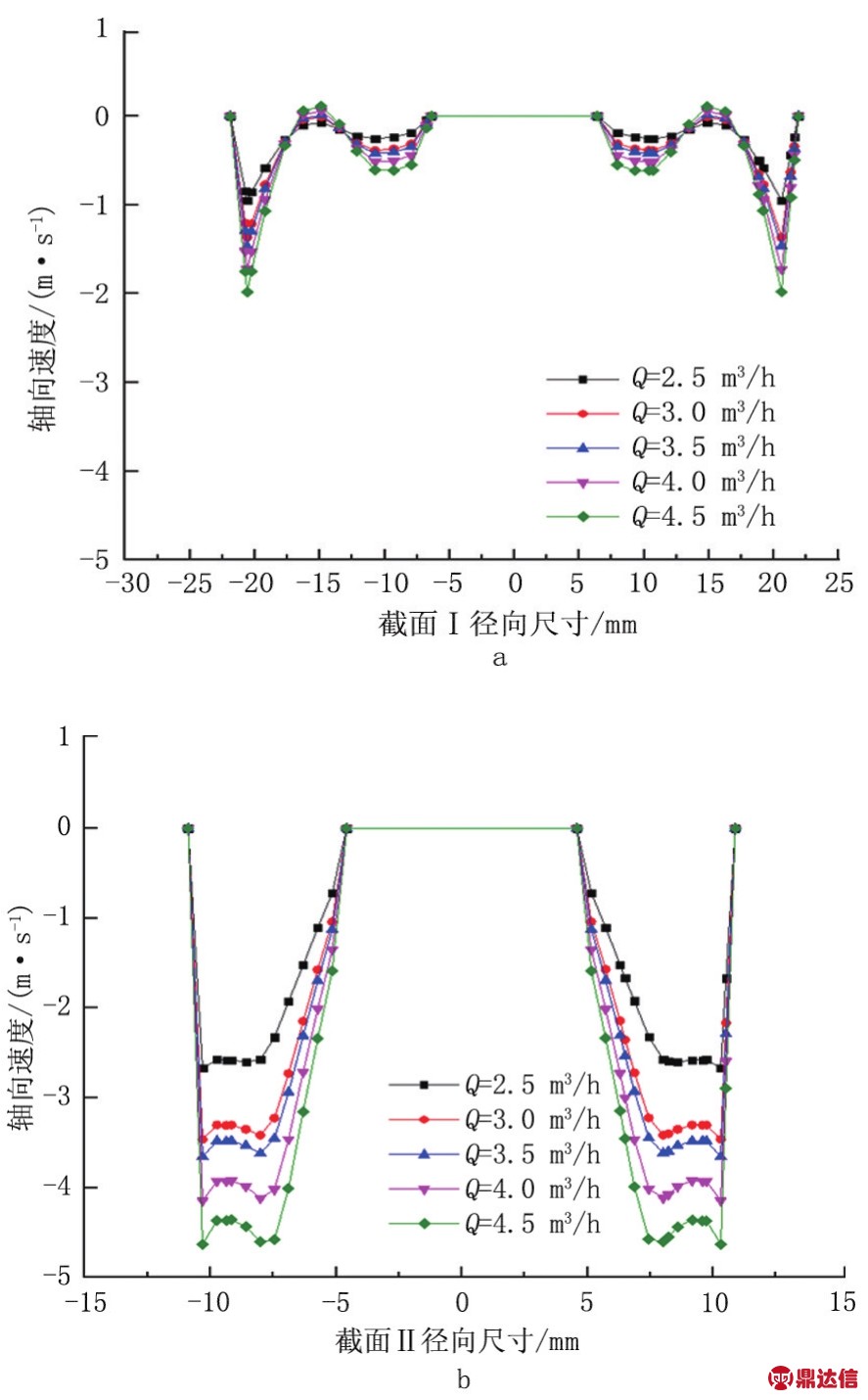
图6 同向出流旋流器轴向速度分布
3.2 压力损失
了解油水旋流分离器内的压力场分布规律,能够更加深入地揭示旋流器内部能量耗散规律和流动规律[13]。液-液旋流分离器的底流排出大量液体,入口与底流口之间的压力差表示液体流经水力旋流器时损失的能量大小。设旋流器入口压力为pi,底流口压力为pd,压力损失定义为

图7是当分流比固定为25%、流量为3.5 m3/h时的压力损失分布云图,其中图7a、7b分别为双锥旋流分离器壁面压力损失云图与横截面压力损失云图,7c、7d分别为同向出流旋流分离器壁面压力损失云图与横截面压力损失云图。取两种结构中最大的压力损失范围为基准,从图中可以看出,旋流器内的压力基本呈中心对称分布,在同一轴向位置上,随着位置半径的减小,由壁面到中心轴,压力损失逐渐增高。双锥旋流分离器在底流管处压力损失最大为0.12 MPa,同向出流旋流分离器分布在同一方向的溢流管压力损失最大为0.6 MPa,是双锥旋流分离器压力损失的5倍。

图7 压力损失分布云图
图8 是不同处理量下两种结构旋流器的压力损失曲线。两种结构旋流器随着处理量的增加,压力损失均呈上升趋势,主要原因是随着流量的增大,入口流速增加,造成摩擦损失、动能损失和湍动能耗等的增加。双锥旋流分离器的压力损失均低于同向出流旋流分离器,且双锥旋流分离器在处理量为4.5 m3/h时,其压力损失最大达到0.17 MPa,但小于同向出流旋流分离器的最小处理量下的压力损失。双锥旋流分离器压力损失增幅小于0.15 MPa,而同向出流旋流分离器的压力损失增幅大于0.3 MPa,增幅是双锥旋流分离器的2倍。
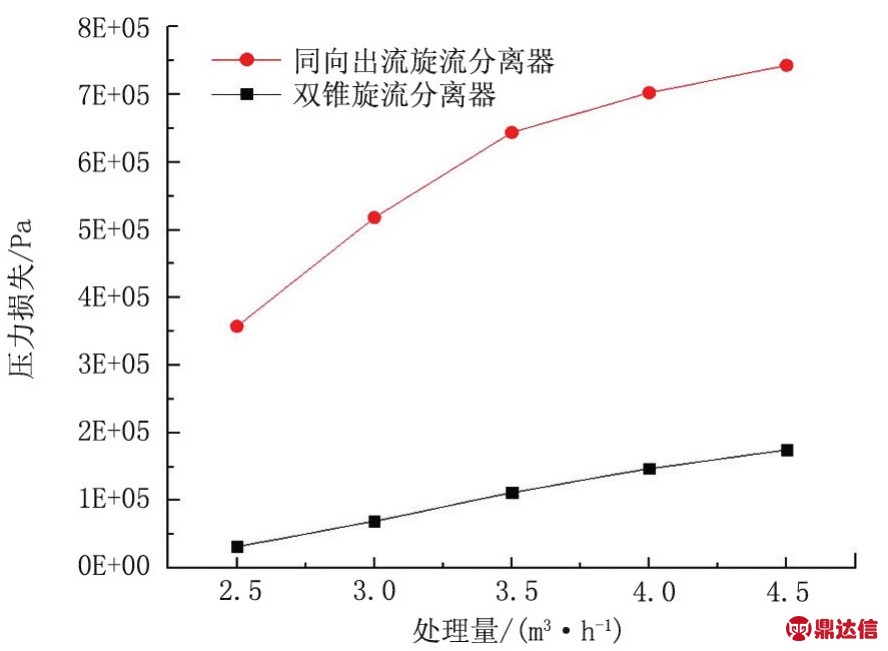
图8 不同处理量下压力损失曲线
对比两种结构旋流器的小锥段压力损失,同向出流旋流分离器小锥段的压力损失要高于双锥旋流分离器,这是由于内置倒锥的结构在一定程度上补偿了能量损耗,使其速度保持在较高的水平,从而使同向出流旋流分离器的分离效率稍高于双锥旋流分离器。
3.3 油相体积分数
通过对两种不同结构的水力旋流器模型的内部流场进行仿真模拟,可预测两种结构旋流器的分离效果。图9为入口分离液体油含量为10%、入口流量为3.5 m3/h时旋流器对称剖面上含油体积分数分布云图。从图中可以看出很明显的近壁含水层和中心油核。
图9a为双锥旋流分离器的油相体积分数分布云图,9c为同向出流旋流分离器的油相体积分数分布云图。经分析可知,近壁含水层水的体积分数接近100%,密度低的油相向中心的低压区聚集[14],即在中心油核处,双锥旋流分离器含油体积分数达到98%左右,同向出流旋流分离器达到99%左右,中心油核含油率从10%提高到了95%以上,两种结构旋流分离器均有较好的处理效果。
图9b、9d分别是运用Tecplot后处理软件对其对应的旋流腔与底流口进行具体显示的结果。对比分析4张图可以清楚地看出油相和水相的分布层次,而且可以看到旋流分离时液流的分布基本对称。同向出流旋流分离器由于溢流口与底流口在同一方向,油相聚集在内置倒锥周围,越靠近溢流口处油相体积分数越大;而双锥旋流分离器的油相主要富集在旋流腔和大锥段中心处,说明分离主要在锥段完成。
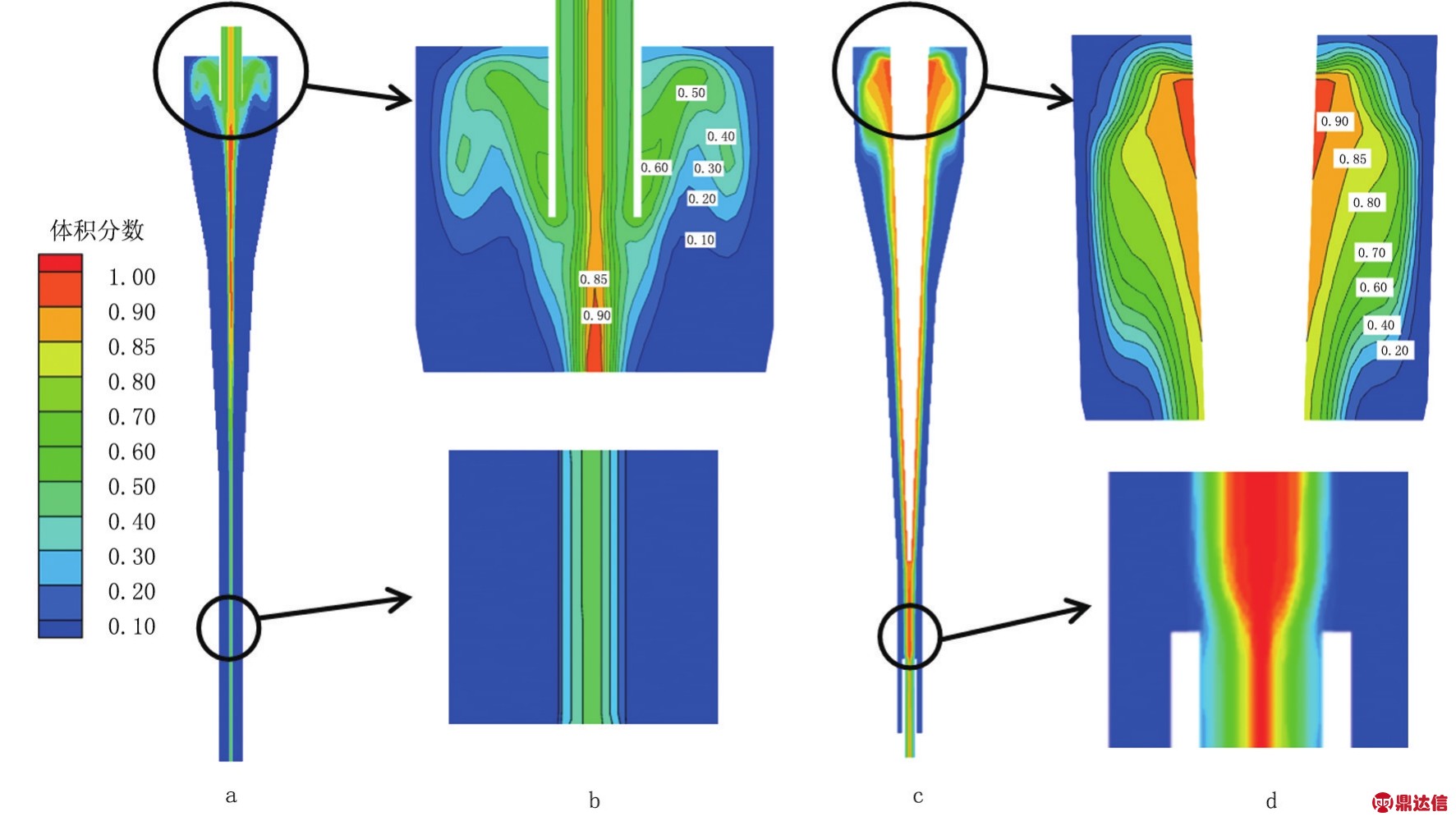
图9 油相体积分数分布云图
3.4 分离效率
分离效率是衡量水力旋流器分离性能的重要指标。简化效率的定义为[9]

式中:Εj为简化效率,%;Cd为底流含油体积分数;Ci为入口含油体积分数。
两种结构旋流器在不同处理量下的分离效率如图10所示,随着处理量的增加,两者效率均有不同程度的增加。其中,当处理量由2.5 m3/h增加到3.0 m3/h时,同向出流旋流分离器的效率增加幅度较大,从3.0 m3/h开始效率维持在99%左右,有小幅度提高;而双锥旋流分离器处理量从2.5 m3/h增加到3.5 m3/h时,其分离效率呈线性增加,从3.5 m3/h开始增加变缓。两种结构旋流器的简化效率曲线表明,同向出流旋流分离器比双锥旋流分离器更适应处理量相对较低的情况,其处理范围更广。
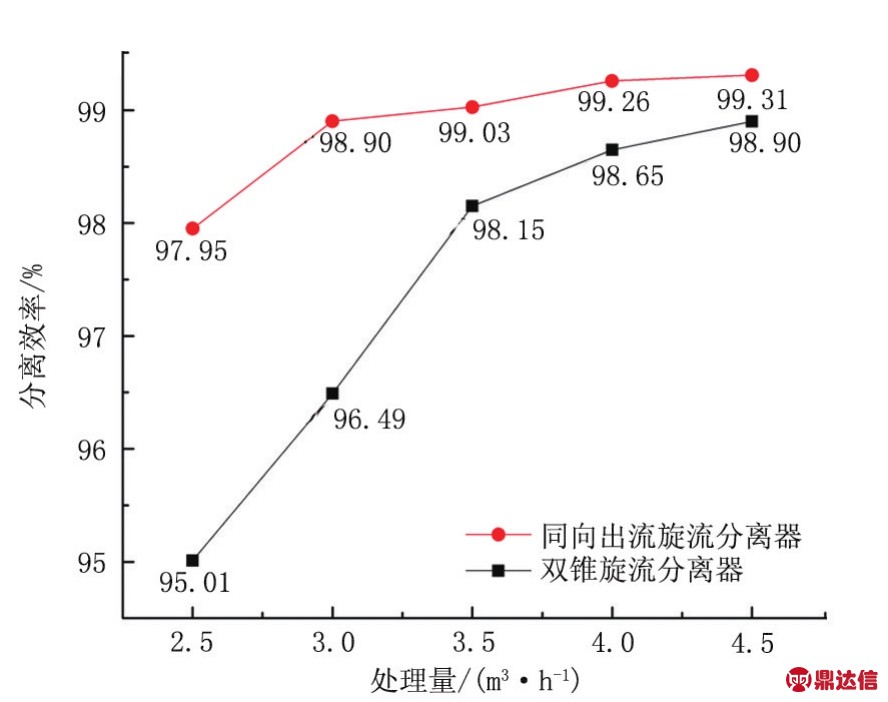
图10 不同处理量下简化效率曲线
4 结论
(1)同向出流旋流器的倒锥在旋流腔和大锥段上部,对切向速度的影响不大。在大锥段的下半部分,从截面Ⅱ开始,双锥旋流分离器的切向速度迅速下降,而同向出流旋流器的倒锥结构使得切向速度维持在一个较高水平;在旋流腔和大锥段,双锥旋流分离器的轴向速度要大于同向出流旋流器,同向出流旋流器的倒锥结构没有使轴向速度增加,倒锥结构对切向速度影响更明显。
(2)同向出流旋流器的底流出口截面尺寸小,故其压力损耗大。同向出流旋流器的内置倒锥结构对旋流腔和锥段的压力损失影响较小;随着处理量的增加,同向出流旋流分离器压力损失的增幅大于双锥旋流分离器的2倍。
(3)两种结构旋流器的简化效率曲线表明,双锥旋流分离器比同向出流旋流器更适应处理量相对较低的情况,其处理范围更广。