摘要:在高黏度原油环境下,三相分离器出口油含气率经常过高,造成系统运行不稳定。为此,从设备结构、操作液位和分离元件三方面对出油含气率进行试验分析,并对大港油田家10站三相分离器进行改造。结果表明,在三相分离器气入口端增设气体预脱装置,增加原油的分离停留时间及改变分离元件间隙可以很好地解决三相分离器出口油含气率过高的问题。
关键词:三相分离器;含气率;操作液位;聚结器;分离元件
在油田常用的原油预处理工艺流程中,三相分离器是重要的分离设备。它主要是利用重力分离原理,通过罐内分离元件对原油中的油、气、水三相进行分离[1]。在高黏原油处理过程中,三相分离器出口油含气率经常过高,造成工艺流程不稳定和严重的安全隐患。分离器结构、分离器操作液位和分离元件不合理是造成出口油含气率过高的主要原因。本文以大港油田家10站三相分离器为例,采用试验的方法研究解决分离器出口油含气率过高的问题。正常运行。
家10站三相分离器主体按照标准《压力容器(GB 150—2011)》 [2]与 《卧式容器 (NB/T 47042—2014)》[3]设计制造。主体材质为Q345R,分离元件材质为304L。三相分离器设计压力0.6 MPa,操作压力0.4 MPa,直径3 000 mm,长度8 000 mm,采用BH-1型分离元件,结构如图1所示。
1 家10站三相分离器现状
经过30多年的开采,大港油田采油三厂所辖开采区域已经属于高黏稠油区块。家10站原油三相分离器投产运行一段时间后,出口油含气率较高;操作液面由正常控制液位1 m增至1.5 m;操作压力由正常控制压力0.4 MPa增加到0.55 MPa;出口油排液流量降低;混输泵压力由0.85 MPa升至1.5 MPa,频率由42 Hz升至50 Hz,造成系统不能
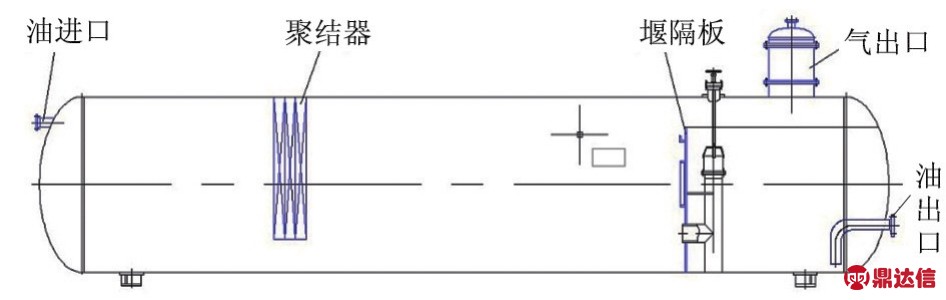
图1 家10站三相分离器结构
2 出口油含气率影响因素试验
2.1 操作液位
三相分离器液相停留时间的计算公式[4-5]为
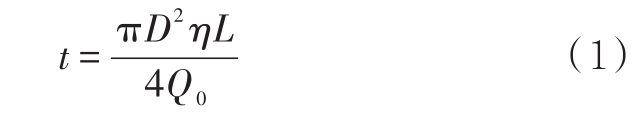
式中:t为液机停留时间,min;D为筒体直径,m;η为液相面积比率;L为筒体长度,m;Q0为液体流率,m3/min。
由式(1)可见,在不改变三相分离器结构尺寸和工艺操作参数的条件下,增加液相面积比率可以有效增加三相分离器液相停留时间,从而防止三相分离器满罐情况的发生。为了更好地分离气相中的液相油滴,保证气相质量,一般情况下将液相面积比率控制在0.5左右。
在不改变三相分离器本体尺寸的情况下,增加堰板高度[5]可以增加液相停留时间,但是必须对三相分离器进行改进,以弥补气相空间减少造成的气相分离面积不足的问题。
结合立式气液分离器的结构原理[5-6],对三相分离器的进气方式进行改进(图2)。在进口处设置气体预脱装置(件1),在保证气相分离效果的情况下,将家10站三相分离器堰板高度提高至2400 mm(0.8D),以增加液相停留时间。
经现场试验测定,在操作压力为0.4 MPa、操作温度为45℃条件下,停留时间可以增加到9 min,并且停留时间越长出口油含气量越少,出口油离心泵的流量由5.1 L/min增加到9.2 L/min,折损率由72.1%降低到49.7%。试验测定的液相停留时间与出口油含气率之间的关系如图3所示。
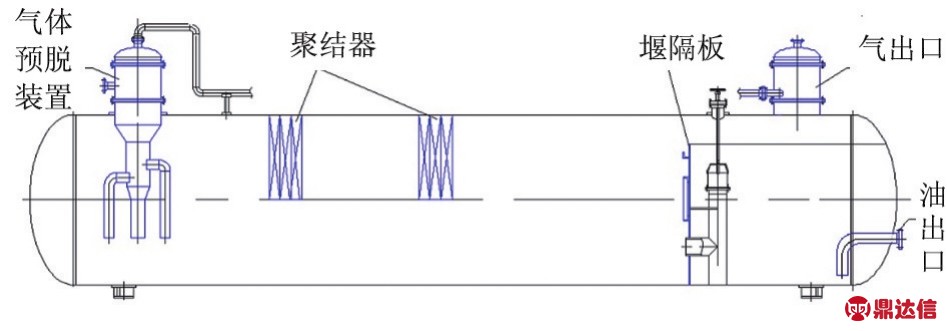
图2 家10站三相分离器改进结构

图3 液相停留时间与出口油含气率之间的关系
2.2 增设分离元件
在原家10站三相分离器设计过程中,主要考虑了2个方面:①操作过程中聚结器之间的液面会低于进液侧和出液侧的液面高度,造成聚结器分离面积使用率低于设计值;②在操作流量过小的情况下,聚结器之间阻力过大而使得液相通过率减少,会造成分离效果不佳。基于上述原因,按照设计经验,两组聚结器之间一般至少保持在1倍设备直径的距离[7]。结合分离器的尺寸,所以本分离器只设置了一组分离元件。
经现场测算,家10站三相分离器单个聚结器前后液面差约为150 mm,低于非高黏原油三相分离器中聚结器的前后液位差(300 mm),说明家10站原油在三相分离器中基本可以实现等液位流通。
对大港油田板一联合站运行情况良好的2个三相分离器进行测量,通过测算板一联合站2个距离为0.7D的三相分离器的液位差均未超过300 mm,有效保证了聚结器分离效果,而且聚结器的数量增加,可使液体接触聚结器的面积增大,保证气液分离效果。如果按0.7D的距离设置聚结器,以家10站的分离器长度可以多设置一组分离元件,因此将家10站三相分离器的分离元件增为2个[8]。
现场试验数据表明(图4),相同液相停留时间情况下,2个分离器可以成功地将出口油含气率控制在0.019(体积分数),出口油离心泵的流量由5.1 L/min增加到14.2 L/min,折损率由72.1%降低到22.4%。
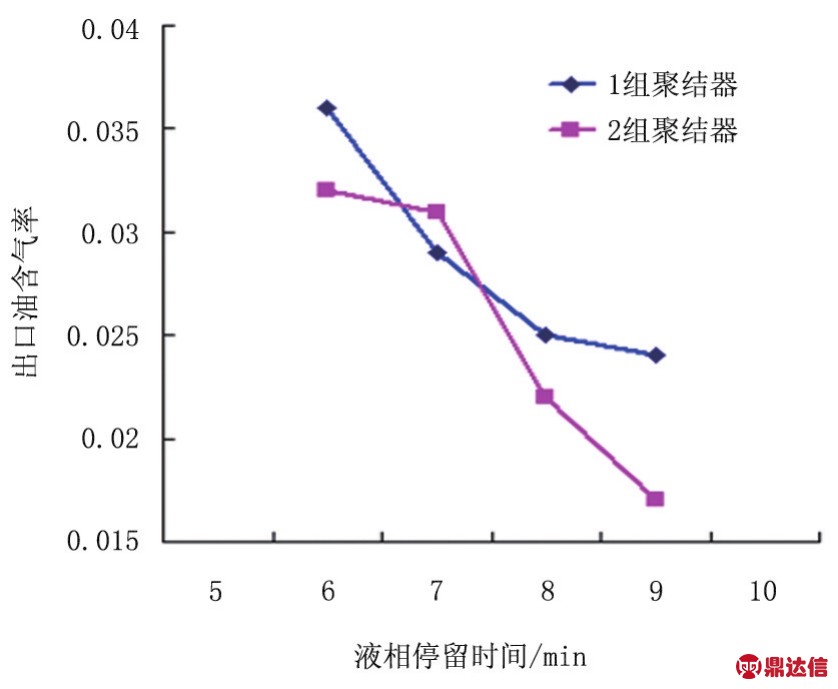
图4 聚结器数量与出口油含气率之间的关系
2.3 分离元件选型
在分离元件选型过程中,考虑到要实现流体与聚结器波纹板充分碰撞和吸附分离作用,该分离器采用BH-1型分离元件,波高10 mm,波纹板间距为10 mm;但此分离元件用于高黏原油工况时容易堵塞流通通道。图5为使用后的分离元件。
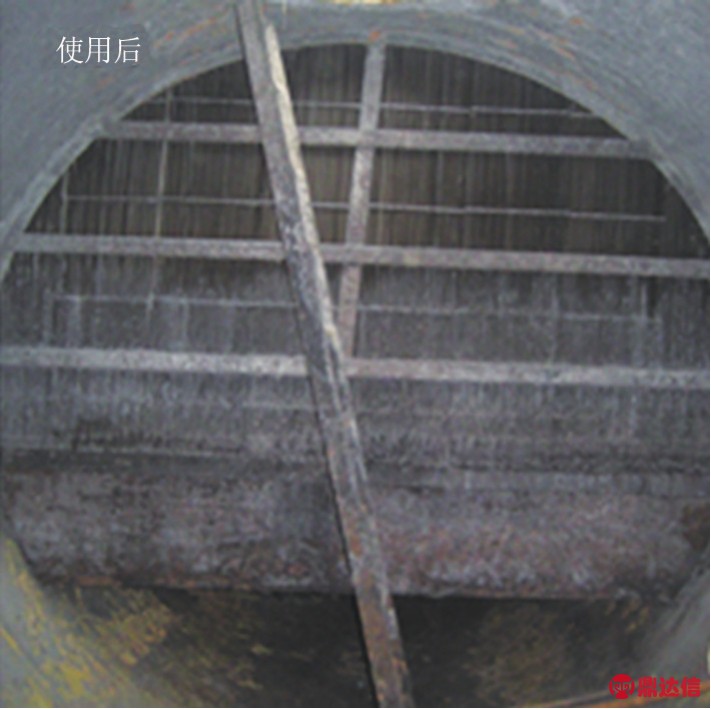
图5 使用后的分离元件
为此,需对聚结器进行优化:增加聚结器波纹板间距到20 mm,同时波纹角度从常规的45°改成30°,使得聚结器的比表面积由255 m2/m3改为213 m2/m3,空隙率由94.2%改为90.2%。
聚结器优化后,在保证有效碰撞面积的同时,增大了孔道面积,使得聚结器在应用过程中不会因为堵塞而使分离效率下降,从而造成出口油含气率升高[9-11]。
操作时间为9 min,在使用2个新型聚结器后,根据现场试验测定的数据(图6),出口油含气率已完全控制在0.02 m3(气)/m3(油)以下,出口油离心泵的流量由5.1 L/min增加到17.1 L/min,折损率由72.1%降低到6.5%,并且没有随着使用时间的增加而使得出口油含气量增加。
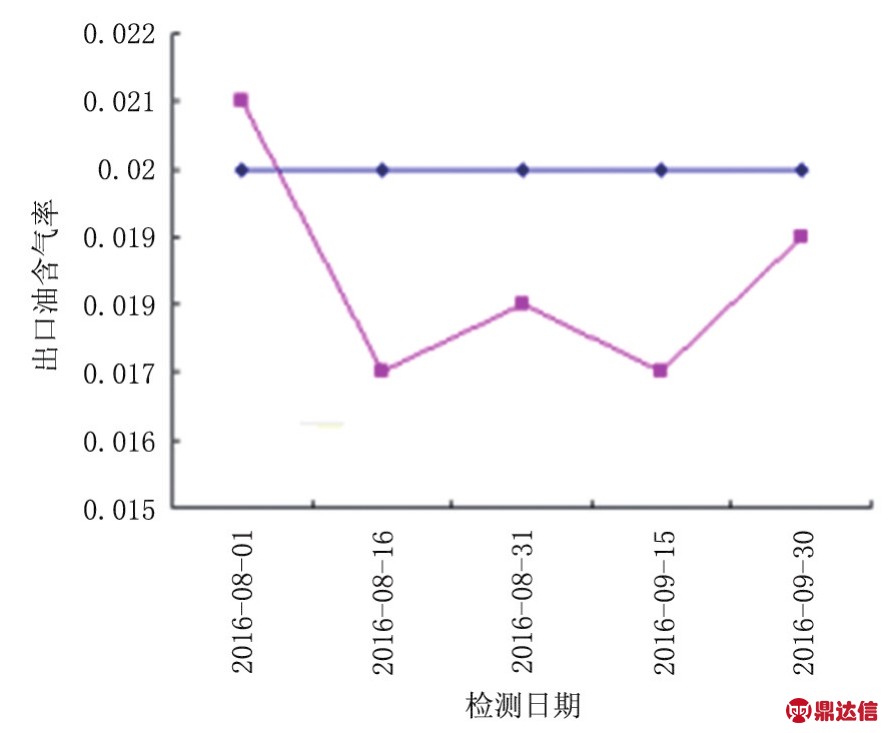
图6 聚结器优化后分离器出口油含气率
3 结论
试验分析表明,三相分离器结构、液位高度和分离元件是影响三相分离器出口油含气率的主要因素。
从三方面对家10站三相分离器进行改造:①改变三相分离器的进气方式,在进气口增设气体预脱装置;②将聚结器波纹板间隙由10 mm增加至20 mm;③聚结器由1个增加到2个。改造完成后分离器运行情况良好,满足了站场原油处理的要求。
三相分离器的选型设计要考虑结构、液位高度与分离元件这三个因素。分离元件的选型要考虑介质的黏度,由于试验条件的制约,此次试验未考虑油气比和气体性质对分离元件选型的影响。为防止分离元件堵塞导致分离效率下降,可以增加波纹板间距和分离元件的数量。