摘 要 提出了一种带耐磨隔热衬里的旋风分离器结构,并基于Fluent软件对旋风分离器内温度场进行了模拟,对旋风分离器内部的温度场分布情况进行了分析。该分析结果可为保温层及减少热损失量设计提供一定的参考。
关键词 旋风分离器 温度场 隔热衬里 耐磨衬里
0 前言
旋风分离器是一种高效、实用、新颖的除尘设备,具有体积小、高度低、集尘效率高、气流阻力低和分离能力强等优点,广泛应用于化工、制药、化学等领域[1]。因其对颗粒物的分离、捕集过程是一种复杂的三维、二相湍流运动,并涉及到气固相互作用,实验数据也不易测量,所以关于旋风分离器的研究至今大多采用经验、半经验的方法[2]。
近十年来,仿真分析在国内得到巨大发展,魏新利等[3]采用不同湍流模型及不同离散方式对旋风分离器的流场进行了数值模拟研究。姜大志等[4]利用模拟结果对旋风分离器入口不同位置气流在分离器顶部的环形空间的轨迹进行了分析研究。而针对旋风分离器温度场的分析极少,且设备往往不是单一的分离器。对于高温介质的分离,设备需要采取相应的保温措施和结构加固措施。
改进后的旋风分离器结构为带耐磨隔热衬里结构,由于其内部介质处于高温高压的复杂工况下,多层保温层结构的旋风分离器的温度分析变得至关重要。本文借助Fluent软件,对高温高压带耐磨隔热衬里的旋风分离器内部温度进行了分析研究,为相关方面的科学研究提供一定的理论借鉴。
1 模型建立
在ANSYS SCDM软件中建立模型,在旋风入口设置强制旋流,428 mm的高位差增加了介质流量及压力,如图1所示。带耐磨隔热衬里结构的旋风分离器结构如图2所示,剖面结构图如图3所示。
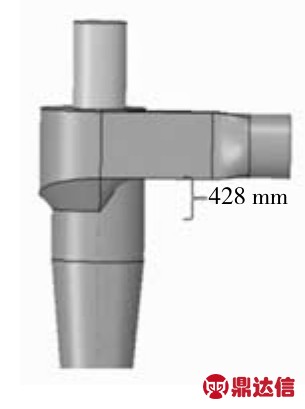
图1 旋风分离器结构
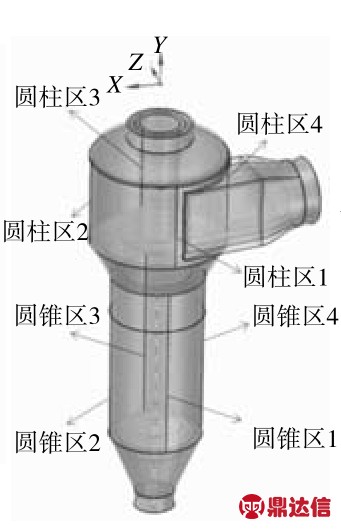
图2 带耐磨隔热衬里 整体结构及路径
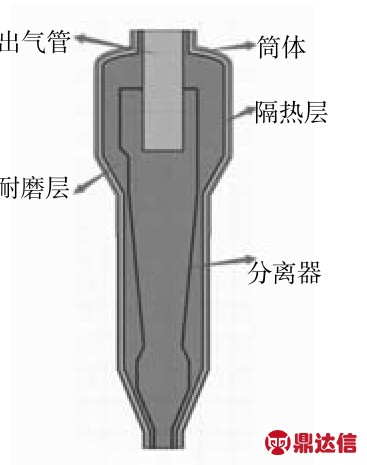
图3 剖面结构图
1.1 网格划分
模型采用ANSYS软件中的Workbench Meshing模块对模型进行网格划分,如图4所示,网格总数为3989640,模型以六面体网格为主,整体网格质量为0.82,满足仿真要求。除了出气管与分离器和耐磨层结构的划分,整体网格以节点共享形式划分。
为了提高计算效率,主要分析了内部流场的变化情况,将耐磨层网格设置疏松,出口管设置密集,同时设置膨胀层。
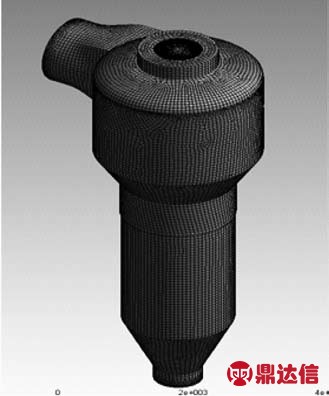
图4 整体网格划分图
1.2 参数
高温高压带耐磨隔热衬里的旋风分离器的工作压力为3.5 MPa,工作温度为730 ℃。高温高压带耐磨隔热衬里的旋风分离器的耐磨层采用Al2O3材料,由于其具有导热系数低、价格便宜等优点,被广泛应用在保温层结构中;筒体结构采用14Cr1MoR合金钢材料,在保证强度、刚度的基础上,采用变截面厚度以减少原材料成本。材料参数如表1所示。
表1 耐磨层及筒体材料参数表

隔热衬里沿着设备外壳内表面径向均匀分布,厚度为90 mm。隔热衬里导热系数如表2所示。
表2 隔热衬里参数表
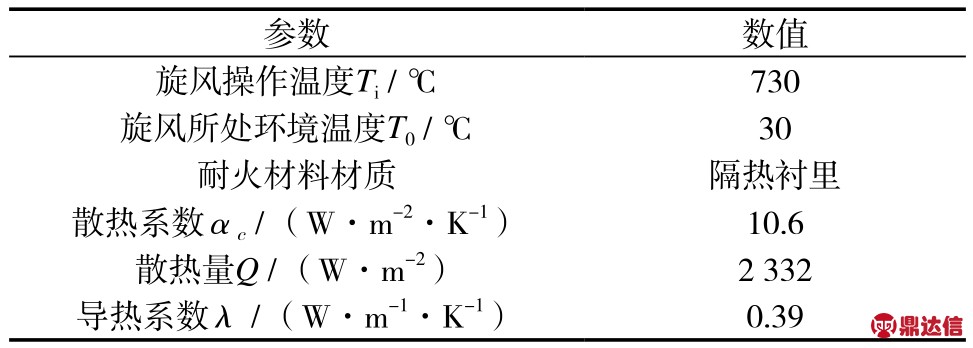
1.3 边界条件
(1) 进口条件
设置速度边界条件,物料进口速度为15 m/s,气流雷诺数Re为[5]:

湍流强度I为:
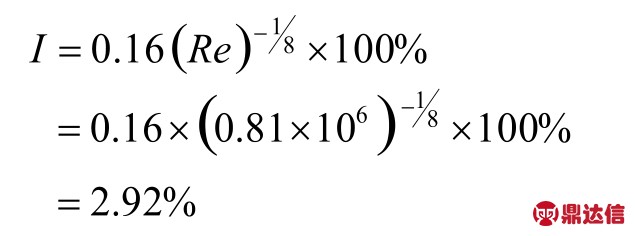
水力直径DHD为:
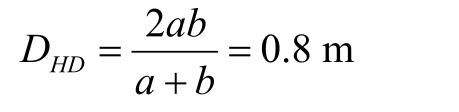
(2) 出口条件
由于出口压力未知,故设置为出流边界,假设出口处的流动为充分发展流动,即流动状态由区域内的流场外推得到,出气管设置为自由出流outflow边界,流量权重设置为1。
(3) 下料口条件
由于下料口没有气体流出,所以设置为outflow边界,流量权重设置为0。
(4) 外部环境对流换热条件
对壁筒体与外部环境(30 ℃)设置对流换热条件。
(5)壁面条件
采用标准壁面函数(Standard Wall Function),设置壁面为无滑移边界,壁面粗糙度参数为0.5。
(6)固体边缘条件
由于固体边缘还与其他固体相连,因此设置绝热条件时需同时考虑到设备或接管的连续性。
(7)固体之间条件
由于模型为固体与固体之间传热,因此需设置耦合条件。
2 结果分析
在流场的数值模拟中遇到的问题主要是由动量方程中的对流项和压力梯度项的离散项处理不当引起的。在各个通用方程的离散项中,差分格式的选择对于计算结果的稳定性和准确性都有很大的影响。采用QUICK格式分析离散项,采用PRESTO格式分析压力项插补项,分析压力速度耦合格,可得到较好的计算结果。
采用压力基求解器,雷诺应力模型(RSM)对旋风分离器中的不可压缩稳态内流旋转流动进行求解。但是由于模型尺寸比较大,划分后网格数接近400万,计算速度比较慢,因此先采用RNG k-e模型进行计算,大约模拟3000步后计算收敛,然后换用RSM求解,直至计算收敛。
2.1 截面温度分布
图6为X轴截面温度分布图,从图6中可以明显看出温度的传递趋势,壁面温度梯度不是很大,趋于均匀化,这是由于内部流场径向速度很小。温度最高处位于旋风分离器内部,为730 ℃。分离器外壁附近温度梯度较大,这是由于环境温度只有30 ℃,与分离器内部温度梯度差较大。同时图6中还能看到外旋下行流及中心线螺旋向上流的分界面,二者存在一定量的温差,上下行流之间发生热交换,导致上行流流体温度升高,下行流流体温度降低。图7为X=0截面上不同高度的温度分布曲线图。
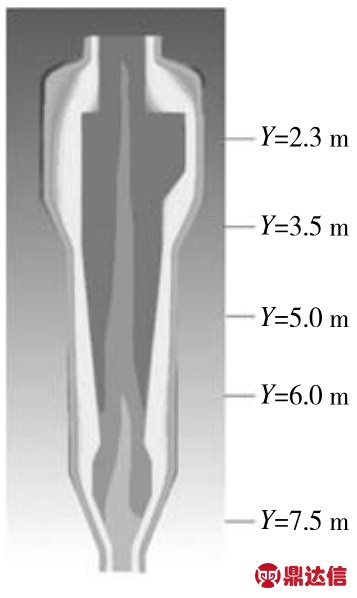
图6 X 轴截面温度分布图
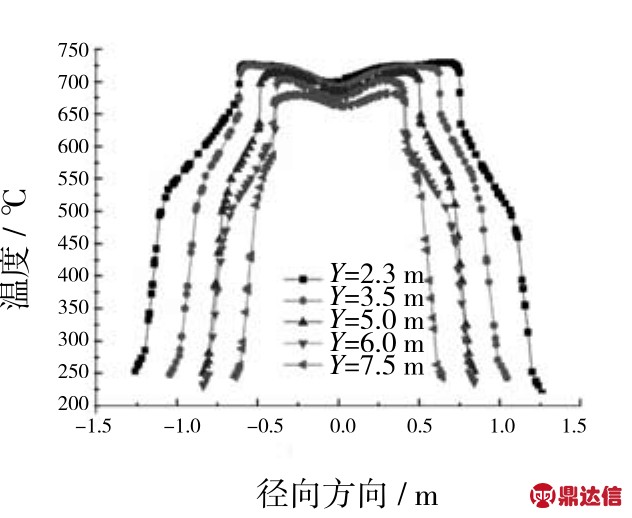
图7 不同高度截面温度分布图
从图7中可以看出:
(1) 温度沿着径向方向呈现“M”型分布,筒体外壁面温度最低,为250 ℃左右。
(2)随着高度的降低(即圆柱向圆锥方向),温度梯度越大,主要原因是随着圆柱区向圆锥区转化时,耐磨衬里厚度越薄。
(3)内部流场温度分布大致是对称的,呈现温度中间低两侧(近壁)温度高的走势,这是因为旋风分离器内的流场为旋转流,同时伴有局部湍流。
(4)分离器内部流场的温度分布差别很小,一般为730 ℃左右,沿着向外侧筒体方向,温度出现3段明显的梯度降低,分别为耐磨衬里、隔热衬里及外部筒体。在耐磨衬里区域,温度降至500 ℃左右,在隔热衬里区域,温度降至300 ℃以下,而外部筒体对温度梯度的影响较小。
2.2 分离器及筒体外壁温度分布
图8为X=0截面分离器外壁轴向方向的温度分布曲线图。从图8可以看出,随着高度的变化,温度变化并没有呈现一定的规律,在Y=-3.3 m截面上外壁温度最高,达到730 ℃。温度最高处位于圆柱区的圆锥收缩口处,主要原因是气体在截面不断缩小的壁面上不断膨胀摩擦,积聚了大量热量。在下收缩口处同样也有一个温度高峰值。在出气口区域内部,温度逐渐降低,原因在于流体在上升的过程中,热量不断的传递给入流流体。
图9为X=0截面筒体外壁轴向方向的温度分布曲线图。温度走势呈现正弦函数分布,在Y=4.5 m截面上外壁温度最高,达到260 ℃,原因在于此处位置温度较高,且耐磨层厚度最薄,为65 mm,导致大量热量传递到筒体外壁。同时在Y=-1.4 m及Y=-6.4 m区域出现温度最低值,主要原因是耐磨衬里厚度过大,热量无法传递。
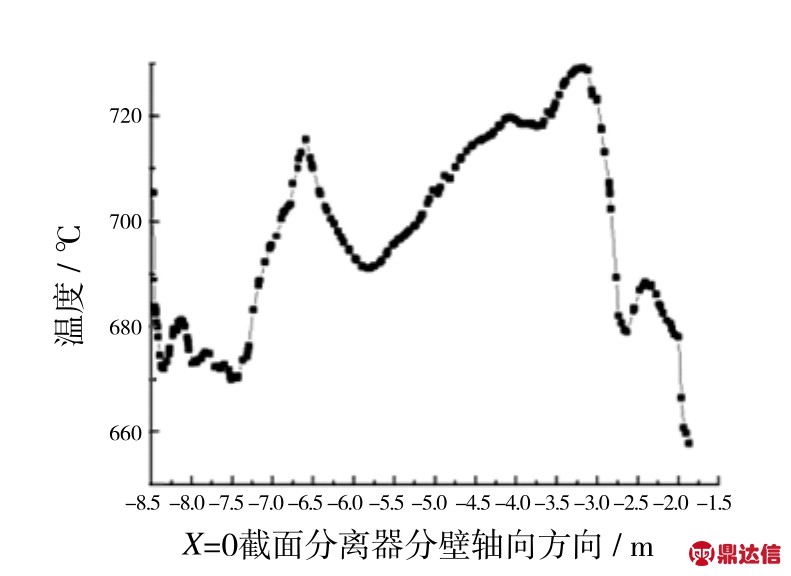
图8 X=0截面分离器外壁轴向方向的温度分布
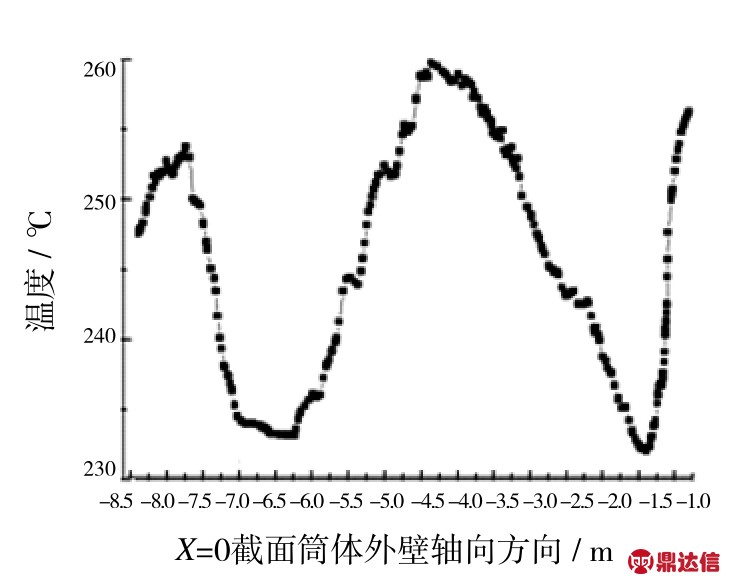
图9 X=0截面筒体外壁轴向方向的温度分布
2.3 筒体外壁温度分布
图10为筒体外壁圆柱区和圆锥区中不同方位同一高度线的温度对比曲线图(圆柱区和圆锥区具体位置可见图2)。圆柱区1选取进气口区,圆柱区2选取流体受压缩区,圆柱区3选取进气口对侧区,圆柱区4选取受压缩对侧区,圆锥区选择与圆柱区相同。从图10可知,筒体外壁圆柱区1和2温度趋势基本相同,随着高度的增加,温度先升高后降低,这主要是受进气口的湍流影响。筒体外壁圆柱区3和4温度趋势基本相同,随着高度的增加,温度逐渐降低。随着高压流体的进入,受压缩区同截面上外壁的温度最高,其次为进气口区域。圆锥区筒体的外壁温度分布走势与圆柱区基本相同,随着截面高度的增加,温度逐渐升高,在Y=4.5 m附近呈梯度升高,这是因为该处的耐磨层厚度最薄。同时二者因高度产生的温差约为50 ℃,外壁筒体温度约为250 ℃。
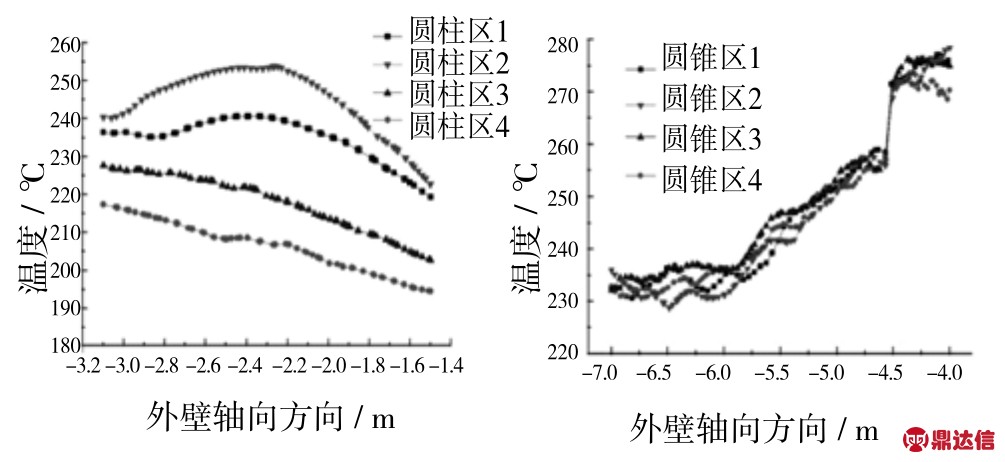
图10 筒体外壁圆柱及圆锥区温度分布曲线
3 结束语
对高温高压带耐磨隔热衬里的旋风分离器结构进行了温度场分析,得到以下结论:
(1)外旋下行流及中心线螺旋向上流存在一定的温差,上下行流之间发生热交换,导致上行流流体温度升高,下行流流体温度降低。
(2)同一截面上温度沿着径向方向呈现“M”型分布,且沿着轴线向下逐渐降低,筒体外壁面温度最低,为250 ℃左右。
(3)在圆柱区的圆锥收缩口处,分离器外壁温度最高;在内部耐磨层厚度最薄(为65 mm)处,筒体外壁温度最高。
(4)在同一高度线的不同方位,流体进入区域温度相对较高,保温层可适当增厚。