摘 要 设计了一种内旋流筛孔柱状气液计量分离器,并通过实验研究入口流型与气、液折算速度对内旋流筛孔柱状气液计量分离器计量效果的影响。结果表明,气相质量流量在0~0.05 kg/s,液相质量流量在0~0.60 kg/s范围内,气相与液相分离效率不受流型或气、液折算速度的影响,分离器能够适应不同流型的分离要求。在分离器处理能力内,气相分离相对误差为2.5%,液相分离误差为3.0%。内旋流筛孔柱状气液计量分离器有较好的分离计量效果,为气液混合流量计量提供良好参考。
关键词 旋流 筛孔 气液分离器 实验研究
随着陆地偏远油田以及海上油田的开发,地层采出物多为气、液以及泥沙的混合物。为满足油井产量计量,分离器作为必不可少的设备,要求其具有结构简单、紧凑、易于安装、低能耗以及分离效率高等特点。为此,气液旋流分离技术已日益成为各个行业研究的热点,此技术广泛应用在石油、化工、环保以及生物等行业[1,2]。
气-液旋流分离器作为一种结构简单、能耗低、质量轻的分离器,现阶段主要应用包括:小型的分离系统,用来去除液体中的大部分气体,减少液流波动;GLCC分离器,具有切向入口,通过离心力与重力的结合,GLCC硬件及软件的发展使其体积减小,改善了普通立式分离器的分离性能[3—6]。
现设计了新型的内旋流筛孔柱状气液计量分离器装置,克服了传统旋流柱状分离器分离液位难稳定的缺点[7,8],与传统旋流分离器不同的是:此分离器气液旋流是在内柱体里的旋流叶片作用下形成的,液体流进外壳体时,通道截面扩大,减小了旋流作用对液位波动的影响,从而产生稳定的液位。除此之外,与传统柱状气液分离器相比,分离器效果不受分离器入口角度的影响。
1 内旋流筛孔柱状气液计量分离器结构与原理
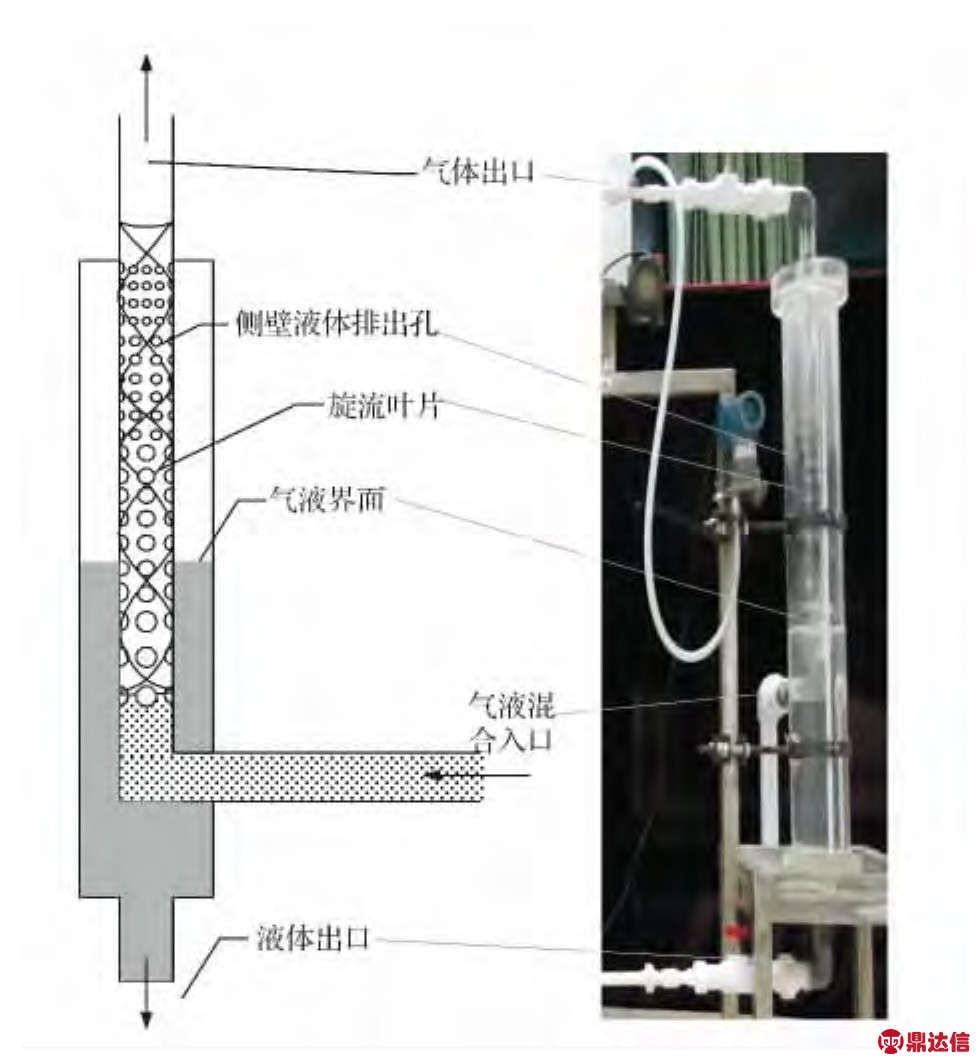
图1 内旋流筛孔柱状气液计量分离器结构图
Fig.1 A chart of swirl vane metering separator
图1为内旋流筛孔柱状计量分离器的结构示意图。分离器由气液混合入口、气相出口、液相出口、外壳体以及内柱体(安装有旋流叶片)等部分组成。分离器入口、气液相出口直径均为30 mm;外壳体直径为120 mm,高度为 1 200 mm;内柱体高度为800 mm,距离外壳体底端300 mm安装。内柱体与分离器的入口以及气体出口相连,柱体内安装旋流叶片,柱体侧壁自下而上设计多排由大到小排列的筛孔。两相流体流经旋流叶片,在离心力作用下,密度较大的液体经分布在内柱体管壁的筛孔流出,由于流通面积的增大,在外壳体中形成稳定的液位,调节液相管路阀门,控制液位稳定,即可由液体支管路的科式质量流量计计量液相分离流量;部分由筛孔进入外壳体的气体,在外壳体中与液体分离,经内柱体上方小孔重新进入内柱体与旋流后留在内柱体中间的气体一起进入气相计量管路,气体分离质量流量由气相管路上的压力、温度与体积流量共同确定。
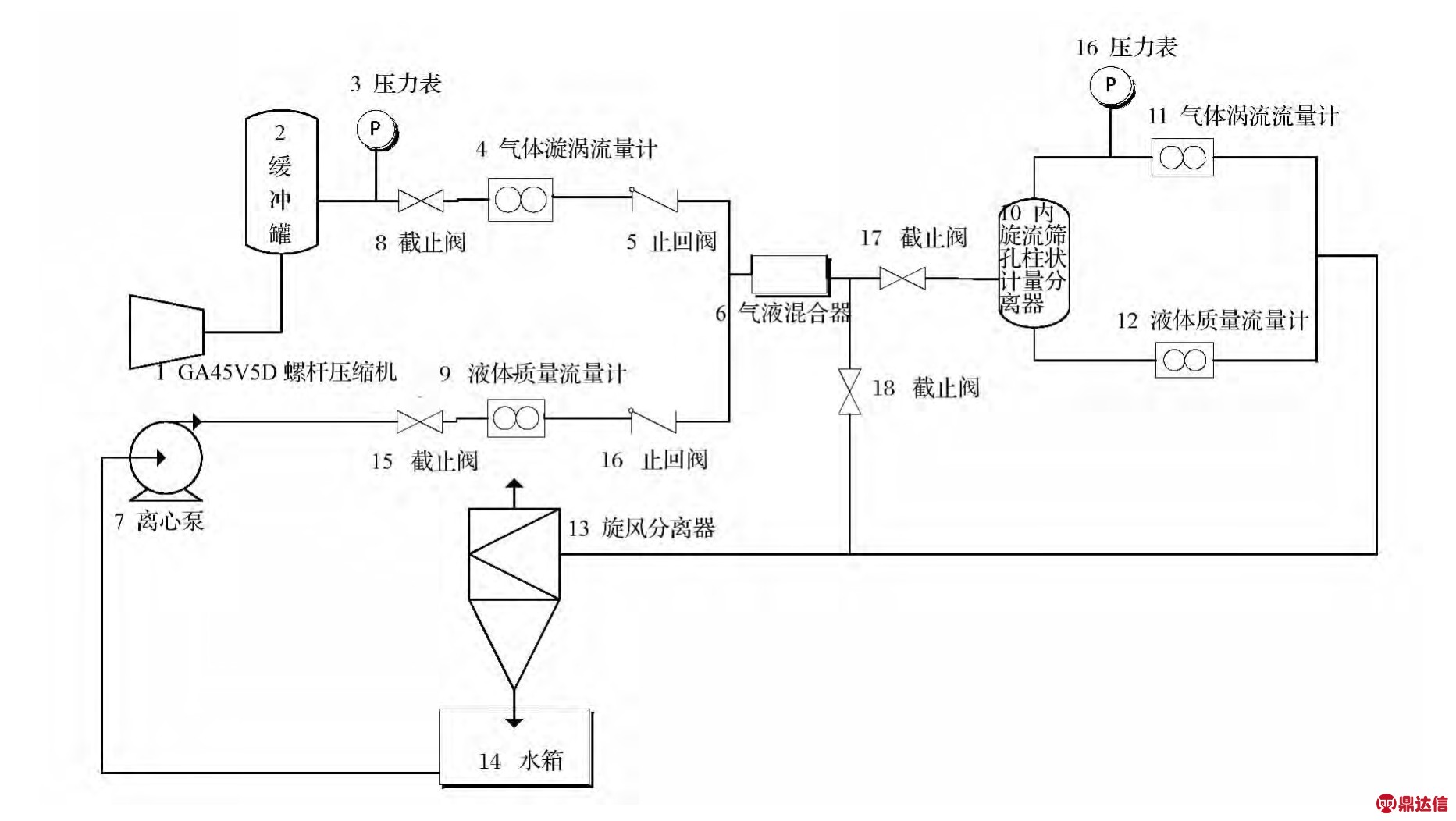
图2 内旋流筛孔柱状计量分离器实验流程图
Fig.2 Flow chart of the Gas-liquid two-phase flow measurements by a swirl vane metering separator
2 实验研究
实验装置主要由泵,压缩机,实验管路以及相关的分离、计量系统组成。详细实验流程如图2所示。
本实验在中国石油大学(华东)多相流实验室气液两相流环道上进行。气体由压缩机1压缩后进入缓冲罐2稳定,经气体调节阀8进入旋涡流量计4进行计量。从水箱14来的液体通过离心泵7增压、经科式质量流量计9计量后与气体在气液混合器6内充分混合。在气液混合器后设置旁通管路,保证实验系统的安全运行。气液混合均匀后经过15 m长的稳定段进入内旋流筛孔柱状计量分离器,保证了进入分离器的气液两相流得到充分发展。
分离器为全透明的有机玻璃材质,便于观察入口流型、控制液位以及记录整个气液分离过程。气液两相流体经分离器旋流分离后进入单相管路进行计量,气相流量使用上海横河机电有限公司的DY025-EALSS4-0D流量计11计量,计量精度为±0.75%,液体流量由艾默生公司生产的CMF025M313NQBAMZZZ质量流量计12进行计量,计量精度为±0.5%。气液流量分别计量后混合流入下游旋风分离器13,分离后气体从旋风分离器上部排空,液体从下部返回水箱14循环。实验过程中,气液流量计以及压力变送器输出信号均为(4~20)mA直流信号,经电流-电压转换后通过Labview实验采集系统进行采集。
3 实验结果
3.1 气、液流量范围
实验中,内旋流筛孔柱状气液计量分离器入口气相折算速度范围为0.65~27.26 m/s,液相折算速度范围为0.01~0.6 m/s。分离器入口气液折算速度在Mandhane流型图上分布如图3所示。
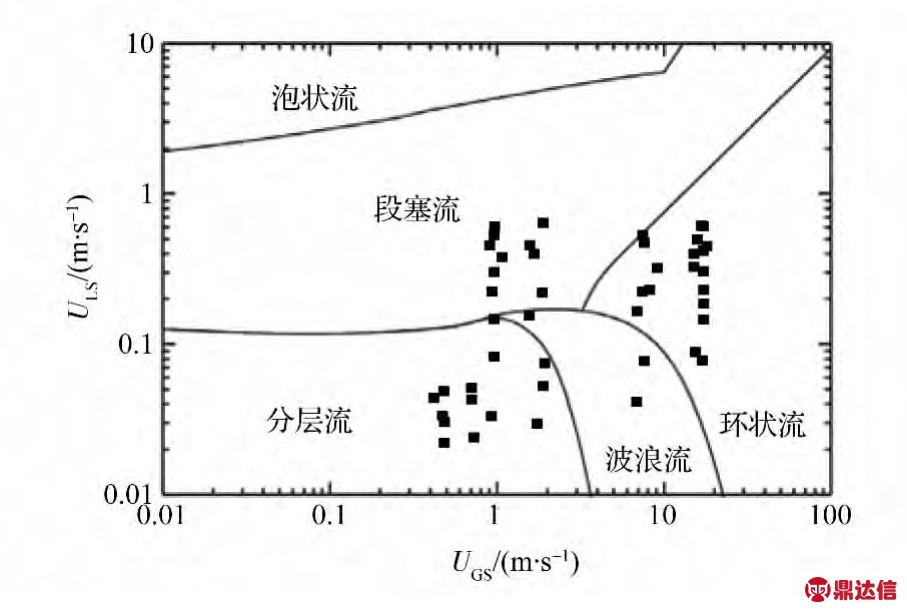
图3 实验测试点在Mandhane流型图上分布
Fig.3 The experiment test scatter distribution on the Mandhane flow pattern map
3.2 气液分离流量与入口流量对比
图4为液相分离流量与气相分离流量的对比,可知气相折算速度在1.3~20 m/s范围内,分离液相流量与入口液相流量比较接近理论直线,气相折算速度为23 m/s时,分离液相流量偏离理论直线较大,主要是因为气相流速的增加,增大了液相的携带能力,部分液体被携带到了气相管路,即此分离器适合处理气相折算速度小于20 m/s的混合流体。
图5为气相分离流量与入口流量对比图,图中在实验范围内气相的分离流量接近入口气相流量,说明具有较好的气相分离计量效果且分离效果不受气液相流量的影响。液相处理能力主要与气相的压力以及外壳体体积有关,在20 m/s内的气相折算速度下,本分离器的液相处理能力为1 700 kg/h(0.47 kg/s),超过此流量后,液体由于不能及时计量,外壳体内盛满液体,影响分离效果。
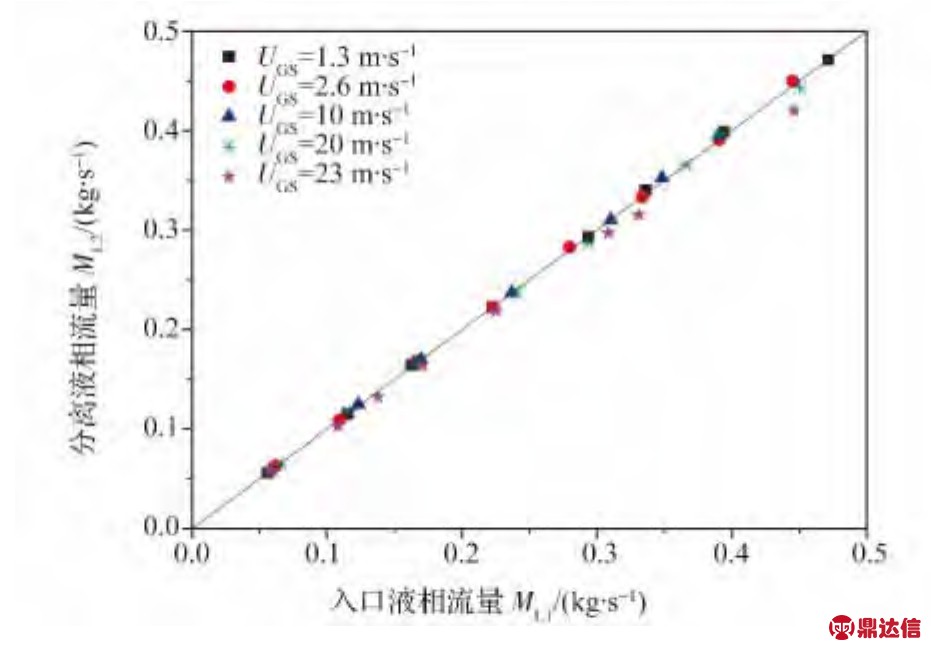
图4 液相分离流量与入口流量对比图
Fig.4 The liquid phase separation flow compared with inlet liquid flow
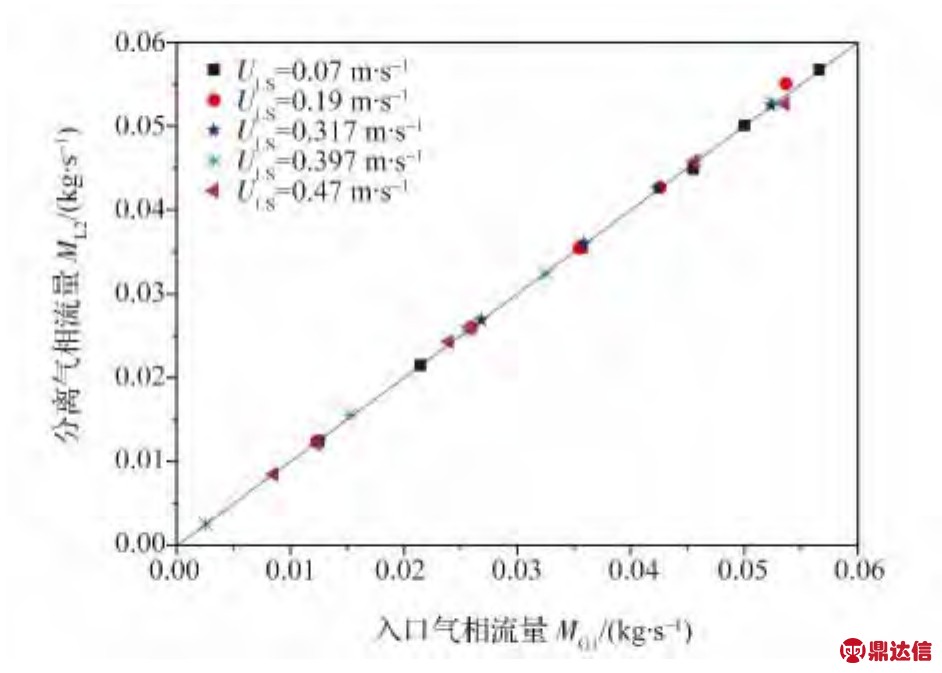
图5 气相分离流量与入口流量对比图
Fig.5 The gas phase separation flow compared with inlet gas flow
3.3 气液分离误差
图6与图7分别为分层流、环状流以及段塞流三种流型下,气液相分离相对误差随着气相折算速度的变化,图中表明液相分离由于受到气相携带作用的影响,在较高的气相折算速度下分离效果变差,且在段塞流时,由于气液两相流固有的波动特性,液相液位也存在一定的波动,使得计量效果变差,但是总体相对分离误差在5%以内。气相分离相对误差不受流型以及气液流量的影响。
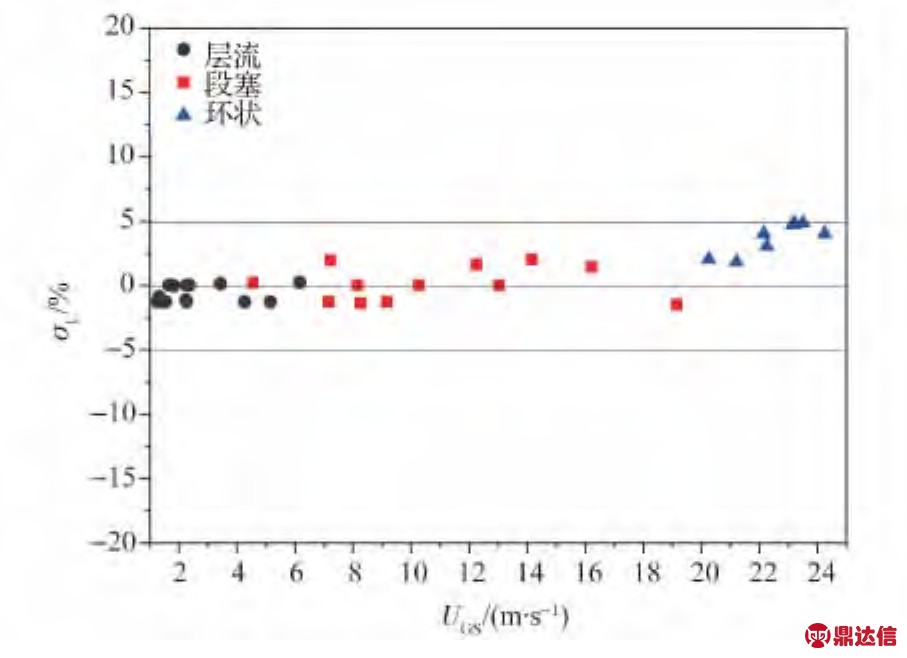
图6 液相分离相对误差随气相折算速度的变化
Fig.6 Change of liquid relative error following gas superficial velocity

图7 气相分离相对误差随气相折算速度的变化
Fig.7 Change of gas relative error following gas superficial velocity
4 结论
(1)设计了一种内旋流筛孔柱状新型气液计量分离器,处理能力为:分离器入口气相折算速度为20 m/s,液相折算速度为0.47 m/s;在实验条件范围内,气相分离相对误差为2.5%,液相分离相对误差为3%,有较好的分离效果。
(2)对于本文设计的分离器,液相分离效率受到气相折算速度的影响,但是在气相折算速度小于20 m/s时,分离误差为3%,气相分离系数不受流型以及气、液折算速度的影响。
(3)内旋流筛孔柱状气液计量分离器具有结构简单、占地少、适应不同流型、计量方便、分离效果好等优点,与传统柱状分离器相比,对气液混合入口方向没有要求、分离液位更容易稳定。