摘要:以包含锥螺纹、分段螺纹的双头螺纹转接头塑料件为例,结合实践经验与CAD/CAE技术,通过分析螺纹转接头的结构工艺,确定了成型方案,再通过模拟螺纹转接头的注射成型过程,获取了注射模结构设计的理论依据,最后采用一模四腔、S形流道平衡式浇注系统布局,以及哈夫滑块为主的成型结构的单分型面两板式注塑模,妥善地解决了特殊螺纹塑料件成型与脱模困难的问题,为类似的塑料件产品的模具设计提供参考。
关键词:锥螺纹;分段螺纹;双头螺纹转接头;注射成型;模具设计
在注塑模具设计过程中,塑料件上带有特殊螺纹结构时,成型与脱模结构设计的合理性对产品的质量和模具的使用寿命有显著影响[1–3],如何能正确、迅速、低成本地设计出具有特殊螺纹结构的注塑模一直困扰着模具设计者[4]。笔者以包含有锥螺纹、分段螺纹的双头螺纹结构的螺纹转接头塑料件为例,运用计算机辅助设计与计算机辅助工程(CAD/CAE)技术,结合实践制造经验,通过分析螺纹转接头的结构和工艺判断与选择成型方案,再通过数值模拟螺纹转接头的注射成型过程,获取注塑模结构设计的理论依据,最终妥善地解决了特殊螺纹结构螺纹转接头塑料件的成型与脱模困难问题,完成了注塑模具的整体设计。
1 螺纹转接头结构与工艺分析
图1为螺纹转接头零件图,从图1可知,该螺纹转接头为双头三角形外螺纹,左端(大端)外螺纹连续分布在连接槽的外侧面上,右端(小端,图中A处)外螺纹为了满足工作需要以及连接时有适当的弹性变量,沿着圆周方向被分割为六段,成为分段螺纹,且该分段螺纹前半部分为锥度螺纹,后半部分为等径直螺纹。由于螺纹转接头安装使用过程中需要承受一定外力,因而在靠近大端的螺纹转接头体外表面上设置有正六边形结构,不但可以提供作用力所需的作用面,而且六边形结构可以防止塑料件在模具内转动。除了螺纹结构外,螺纹转接头内孔还有锥度要求,且要求有较高的同轴度。
螺纹转接头的总体尺寸及公差要求见图1,其中最大直径为62.2 mm,最高为76 mm,客户提出的主要生产技术要求如下:(1)不允许有注塑缺陷,如缩水、流痕、波纹、银纹、表面剥离、气泡等;(2)分型面毛边小于0.1 mm;(3)浇口处须削平;(4)未注圆角为R0.5 mm;(5)未注脱模斜度为0.5°;(6)未注尺寸公差依照GB/T 1804–2000公差数值表,精度等级为4;(7)所用材料为聚甲醛(POM),使用美国杜邦公司生产的型号为Delrin 500T的POM,采用注射成型;(8)塑料件表面要求为亮面;(9)大批量生产,能一模生产四件等。
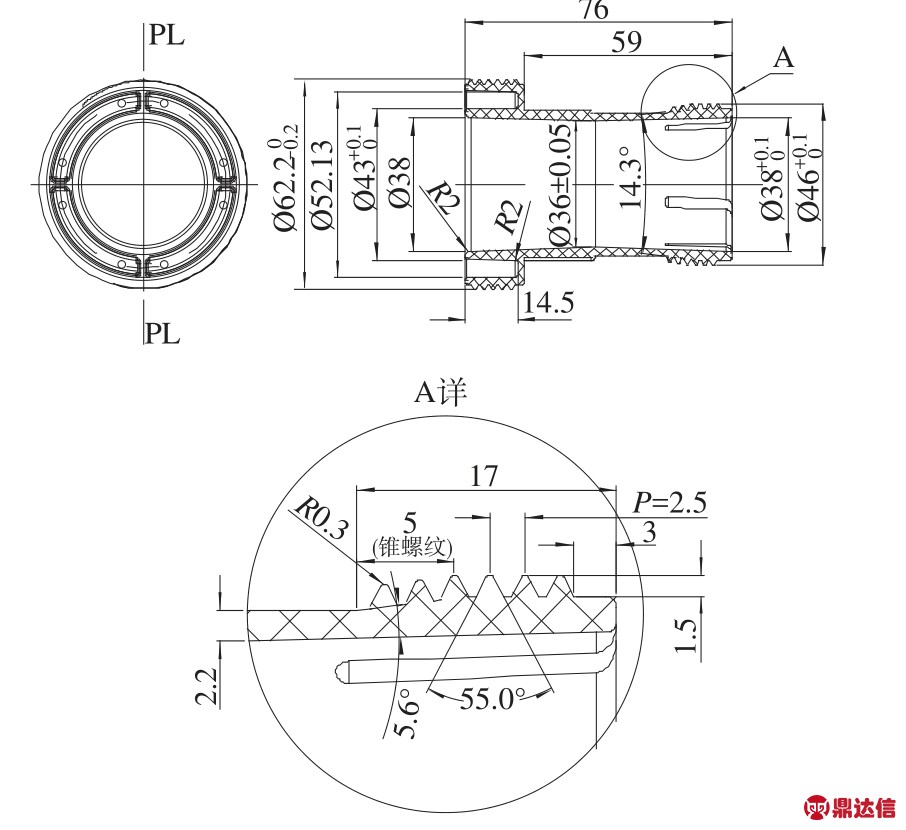
图1 螺纹转接头零件图
2 模具成型结构分析
在模塑产品和模具的设计中,分型面的选择相当重要,它是决定模具结构形式的一个重要因素[5],然而同样一个产品的拔模方向不同,分型面的选择就不同,不同分型面的选择将会影响后续设计的每个环节:如型芯型腔及镶件的设计、型腔数量与排列方式、浇注系统的位置、冷却系统及排气孔等设计。分型面的设计需要依据产品的特征来进行,分型面和产品表面相交的轮廓线为分型线,一般两板式模具的分型线都垂直于平面,与拔模方向平行,而有复杂外观表面的塑料件产品的分型线可能在多个平面上,但在模具设计上为了使模具的结构简单并降低制造成本,一般都会将分型面设计为单一平面,也就是位于和拔模方向垂直的平面上。
对于螺纹转接头塑料件有2处需要拔模,分别为螺纹转接头的内孔与外螺纹,且要求一次的完全生产动作周期能制造4个螺纹转接头塑料件,单纯只考虑塑料件的外观特征时,在设计上内孔与外螺纹都可以作为基本拔模方向,即螺纹转接头可以水平或垂直放置在模具型腔内进行注射成型,但是拔模方向不同,分型面则不同,模具架构也完全不相同。在众多的考虑因素下,选取内孔为基本拔模方向,外螺纹为辅助拔模方向,更有利于保证产品质量与简化模具结构,图1中的PL表示分型面的位置,同时螺纹转接头的最大边界即为分模线。
分型面确定后就可以考虑模具核心部分型芯型腔的结构,型芯型腔在模具闭合之后形成有塑料件产品形状的中空内腔型,是塑料熔体在模具内充填后冷却成型的位置。在此根据分型面与拔模方向来创建型芯型腔,塑料件内孔由动定模型芯碰撞成型,其中定模型芯需要设计锥度结构,塑料件外螺纹与外表面采用哈夫滑块成型,采用两斜导柱引导两成型滑块的方法,由于成型时注塑压力较高,动模板需要设置承压结构,根据生产技术要求,采用一模四腔关于模具中心对称的一字排列、S形流道的平衡式布局,图2为动定模型芯与哈夫滑块结构三维示意图。除了成型结构外,顶出脱模结构也是该塑料件设计的难点,常用的螺纹脱模方式有两种:一种是让模塑产品在充填后,将塑模产品以逆时针旋转后取出;另一种是增加一个拔模方向,也就是利用侧向移动来完成,本塑料件的成型方式刚好满足第二种脱模的需求,不但模具结构简单而且制造成本也较低。
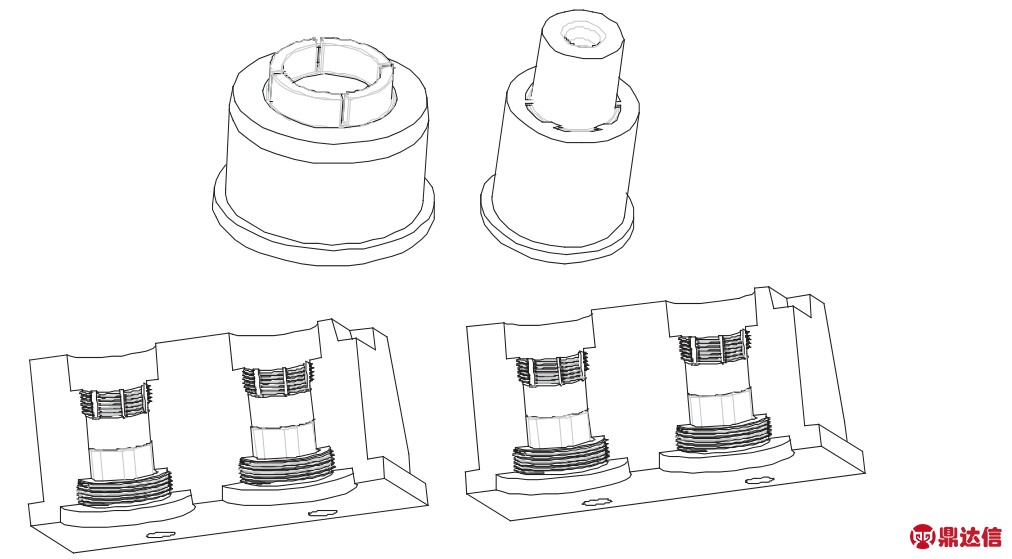
图2 动定模型芯与哈夫滑块结构
3 塑料件成型模拟分析
螺纹转接头塑料件在注塑成型后常常会有不良的现象产生,模具设计者往往依靠自己的经验,分析产品的各种设计因素进行不断地修改补救,不仅增加了模具的开发成本,而且延长了模具的开发时间。为了避免出现反复试模、修模的问题[6],采用Moldflow模拟塑料件的成型过程,通过数值模拟分析可以预测塑料熔体流动充填的效果,尽早发现不良原因和修正注塑缺陷[7–8]。模具成型结构方案确立后,就可以运用Moldflow软件进行CAE分析,一般进行最佳浇口、填充、流动、冷却和翘曲分析[9–10]。
3.1 浇口位置分析
在进行数值模拟分析前,首先要建立螺纹转接头有限元数值模型,在此运用Solidwork绘图软件创建塑料件的实体模型,删除一些如倒圆、倒角等不重要的特征,再另存为STL格式导入Moldflow进行网格划分。为了方便计算,使用双层面网格类型,产生的塑料件网格数为18662。使用POM,通过软件推荐与实际经验相结合的办法选用工艺参数,即可进行计算机数值模拟分析。图3为螺纹转接头最佳浇口位置分析云图。
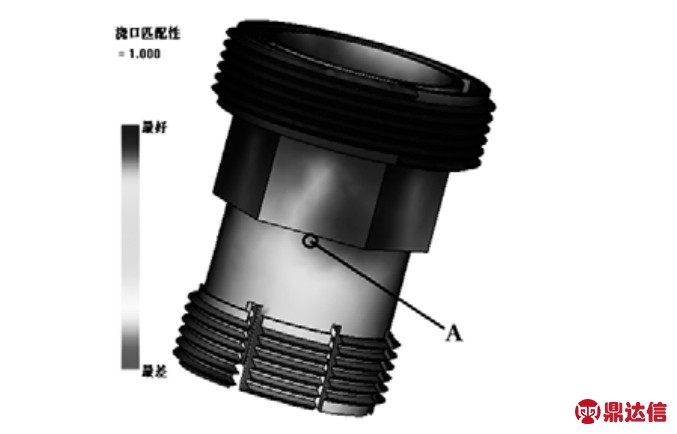
图3 塑料件最佳浇口位置分析云图
浇口位置的选取对塑料件的成型质量影响很大,从图3可以看出,螺纹转接头大端外螺纹部位显示颜色较深,为最佳浇口选择区域,小端外锥螺纹与分段螺纹部位显示的颜色较浅,不宜设置浇口。由于大端螺纹部位结构复杂,壁厚也稍大,在此处设置浇口比较容易完成充模,但是考虑到螺纹转接头的结构特殊性,浇口如果设计在大端,则小端外螺纹的流动阻力最大,不利于锥螺纹与分段螺纹的成型,会导致塑料件两头螺纹的成型质量不同,进而影响塑料件的安装使用。综合考虑各种因素以及熔体流动平衡性,选取塑料件中部深浅颜色交界处的外圆表面位置为进浇点,如图3中A点所示,由于分段螺纹成型比较困难,因此A点略偏向小端,浇口形式为标准侧浇口。
3.2 系统模型创建
完成浇口位置设计后,再根据模具结构分析结果可知,一次分流道需要开设在哈夫滑块顶面,模具开模时一次分流道即完成分型,二次、三次分流道应该设置在两哈夫滑块之间,以便通过侧分型运动取出浇注系统凝料。对于冷却系统设计,依据简单与实用的原则,在塑料件外侧开设直通式冷却水路,上下均匀分布在哈夫滑块内部,并且需要保证水路中心与塑料件表面距离相等。另外为了避免塑料件内孔,即动定模型芯的冷却能力不足,因此必须在型芯上开设水道,由于型芯体积较小,容纳水路的空间有限,在此优先考虑使用隔板式水路进行冷却,为了避免隔板底下的水路管道与一次分流道交叉,把一次分流道设置为曲线形式,但仍采用平衡方式进料,最后建立的系统的数值模拟分析模型如图4所示。
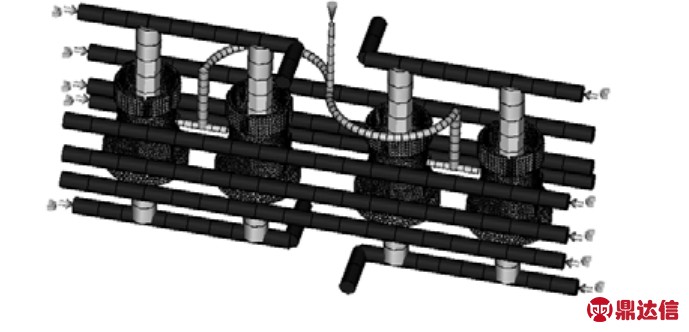
图4 系统有限元模拟分析模型
3.3 流动充填分析
运用Moldflow软件进行流动充填分析,可以获取POM从喷嘴到填满型腔整个过程的信息,通过查阅模拟分析结果,可以判断型腔是否充满,熔体流动是否平衡,流动行为是否合理。图5为塑料件充填时间分布云图,从图5中塑料件各部位的颜色深浅以及标注的充填时间可知,螺纹转接头两端螺纹的成型时间相差不大,大端外螺纹充填完成时间是4~7 s,小端锥螺纹及分段螺纹完成充填时间是6~10 s,总体上看,数值模拟的颜色深浅过渡缓和,表示熔体平缓地充满整个型腔,流动行为较合理。
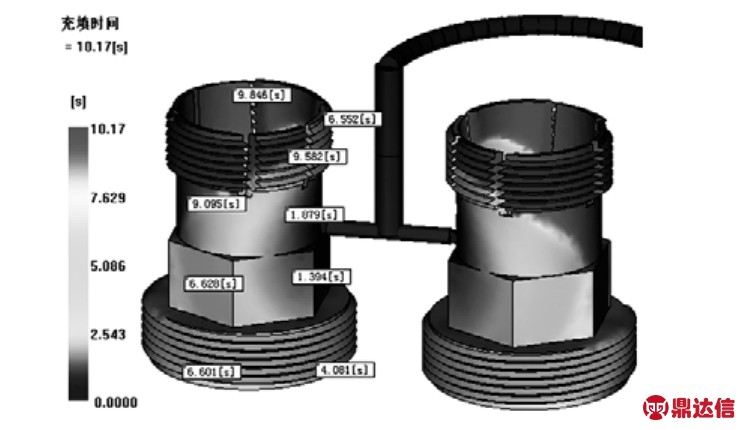
图5 塑料件充填时间分布云图
图6为塑料件熔接线与气穴的分布云图。
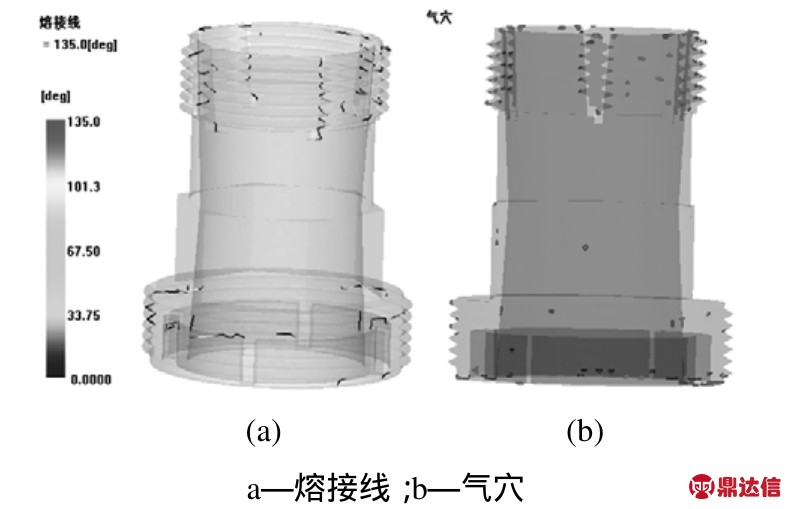
图6 塑料件熔接线与气穴分布云图
熔接线的分布状况也是衡量塑料件质量的重要指标,明显的熔接线会造成塑料件的强度降低及外观缺陷[7],图6a为塑料件熔接线分布图,由图6a可以看出,熔接线主要产生在螺纹上,但无论是大端外螺纹还是小端螺纹,大部分的熔接线都处于塑料件边缘或模具结合部,如螺纹牙顶、分段螺纹边界等,再通过熔体流动前沿温度分析可知,发生熔接线的区域的熔体温度高,且一直保持在熔融状态,属于热熔接线,热熔接线的熔合性好且痕迹不明显,对螺纹转接头的力学性能影响不大。
除熔接线之外,气穴对螺纹的连接强度与刚度影响也很大,图6b为塑料件的气穴分布,从图6b可看出,气穴分布与熔接线类似,主要分布在大端外螺纹顶部、小端锥螺纹与分段螺纹的顶部或边界上,极个别的气穴分布在螺纹转接头的回转体上,由于这些位置都是塑料件型腔与型芯的结合面,即型芯型腔与侧滑块的结合面,在实际应用中可以利用零件间的配合间隙进行排气,且效果好,因而可以判断塑料件产生的气穴较少,型腔型芯布局选择方案合理。
3.4 冷却系统分析
注射成型过程中模具的温度随着熔体充填而上升,若不去除多余的热量,则模具温度会持续升高,从而影响塑料件的冷却固化;反之,若模具冷却系统带走太多的热量,也会影响成型产品的品质,因此必须对冷却分析结果进行仔细探讨。使用水为冷却介质,入水口温度设置为25℃。
衡量模具的冷却系统设计是否合理,主要考核以下几点:第一,冷却水在管道内运动为湍流模式,冷却水出入口处温差在规定范围之内。通过Moldflow对冷却过程的分析可知,冷却水雷诺数为144000,能保证冷却水在冷却管道产生湍流,通过计算冷却水出入口温差为0.59℃,完全小于冷却系统设计规则要求中的3℃;第二,冷却水能使模具与塑料件的温度分布合理。图7为冷却后模具与塑料件的温度分布云图。
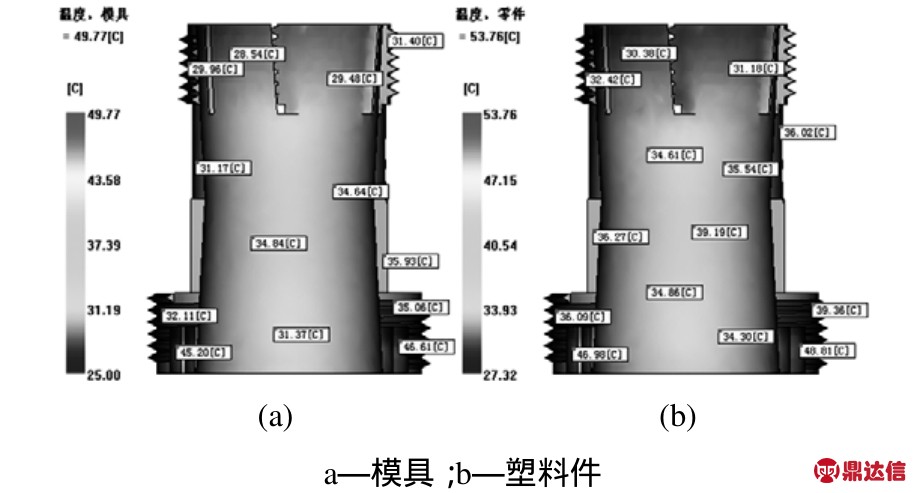
图7 冷却后模具与塑料件温度分布云图
从图7a可以看出,模具的整体温度低于目标模温70℃,模具的最高温度(约为50℃)位于塑料件大端连接槽内,也就是动模型芯上端的四个弧形镶件表面上,由于该处离冷却水管最远,因而冷却慢。哈夫滑块的表面温度为30~35℃,与型芯的最大温差不超过20℃,且图中模具内外表面温度均匀有序变化,说明在冷却水的影响下,模具各个部位的传热散热效果均衡。
从图7b可以看出,除了塑料件大端连接槽显示温度高于40℃外,其余各表面温度都比较接近,温度在30~40℃之间,且过渡较柔和,说明冷却管道对塑料件各部位的冷却能力相当,有助于缓和冷却不均引起的残余应力问题。此外,保压冷却后塑料件的最高温度为53.76℃,明显低于模流分析设置的顶出温度110℃,符合脱模条件。通过冷却分析可知,塑料件在冷却过程中没有发现明显的热点或冷点位置,塑料件的温度与模具温差小于10℃
3.5 翘曲变形分析
注射成型过程中,塑料件内部应力分布不均会引起翘曲变形,图8为所有因素引起的塑料件总变形,最大变形量为0.7391 mm,主要分布在塑料件大端外螺纹与小端部分分段螺纹的直螺纹上,这些区域刚好是塑料熔体最后填充的位置,流程较长,熔体压力损失也比较大,因而熔体不易补充和压实从而造成收缩。收缩不均是造成塑料件翘曲变形的主要因素。螺纹转接头其它部位的翘曲变形量均小于0.5 mm,这是由于保压压力都可以直接作用、补缩容易的结果。最后经过设计审核,塑料件的变形量具备一致性和均衡性,变形量较小,满足产品的质量要求。综上所述,根据模具成型结构分析结果创建的有限元分析系统设计合理。
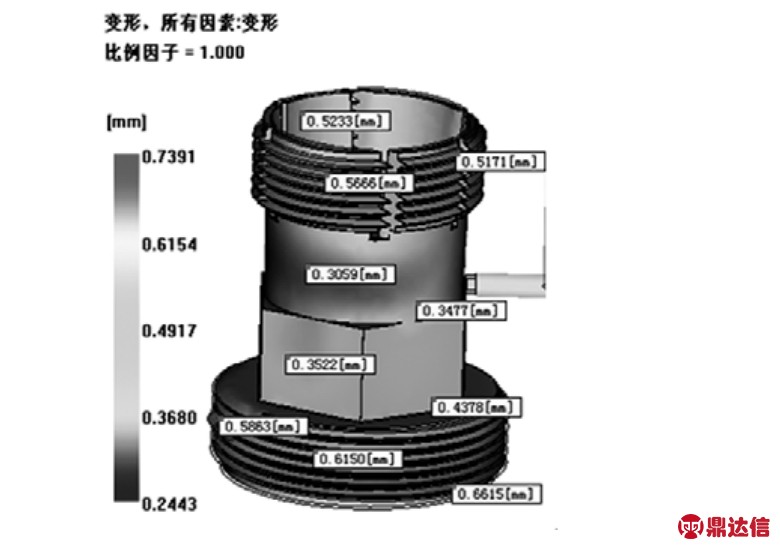
图8 所有因素引起的塑料件总变形
4 模具结构设计与工作原理
通过对螺纹转接头的成型结构分析与成型数值模拟,验证了成型结构方案的可靠性,获得了POM熔体进入模具型腔后的充填流动行为,评估了熔接痕和气穴可能出现的位置及其给模具结构、成型工艺设置提出的要求,测试了模具冷却系统对注塑产品质量的影响以及成型过程中产品温度分布状况,还模拟计算了螺纹转接头可能产生的翘曲状况和变形分布,最后进行产品的模具设计,模具的总体结构如图9所示。
由图9可看出,该模具为一模四腔结构,主流道位于模具中心位置,以塑料件垂直中截面为分型面,由动模型芯5和定模型芯3、哈夫滑块17构成模具成型结构,锁紧力由动模板15和定模板20合模时直接提供,哈夫滑块设计有独立的滑块冷却水路4,所有哈夫滑块定位装置设计在定模部分,滑块沿锁紧面斜面方向松开,垂直于开模方向弹出,且每个哈夫滑块都设置有限位块,在开模时产品尚未完成侧抽情况下,哈夫滑块应贴着定模板20斜面向外滑动,否则容易发生卡模,或引起产品质量问题。总之,该模具的哈夫滑块设计是重点,浇注系统与冷却系统正如数值模拟所示,模具属于单分型面两板式注塑模。
螺纹转接头螺纹内轮廓由动定模型芯成型,外轮廓由哈夫滑块成型,为了保证螺纹成型不错位,塑料件内孔需具备一定的同轴度以及正确的锥度,不但要保证成型哈夫滑块的运动精度,而且要确保滑块在注射成型过程中,在成型压力的作用下不会发生侧移,所以必须加强滑块的定位与导向。在此采用双边T型槽导向,定模板锁紧块与哈夫滑块22°斜面配合并设计锁位,斜导柱16与哈夫滑块20°配合,且斜导柱16与导向孔双边只留间隙1 mm,防止开合模过程中发生侧移。滑块依靠固定在定模侧的一对斜导柱,通过开合模动作完成侧向运动,实现塑料件分型,由于动定模型芯、哈夫滑块属于碰穿式分型面,因此在滑块与定模板锁紧块的接触面上设置有尼龙阻尼装置18,不仅能缓和开合模时成型零件碰撞,而且能改善模具零件间的摩擦。另外为了避免两组滑块之间运动干涉,在模具中心位置设置滑块挡板30,也避免了侧隙流胶和封胶面的损伤。
塑料件外表面冷却水路等距布置在哈夫滑块17上,定模型芯隔板水路2和动模型芯隔板水路6分别由定模座板1与支承板14引入,水流方向两者不同,图9中正负号表示水流方向相反。塑料件从模具中推出由顶针8完成,按塑料件的形状,顶针在圆周均匀布置,每个塑料件有8个顶针,为了避免哈夫滑块17回位时铲到顶针8,通过设置先复位弹簧13和复位杆26机构,保证顶针8先复位,其它结构详见图9。
5 结语
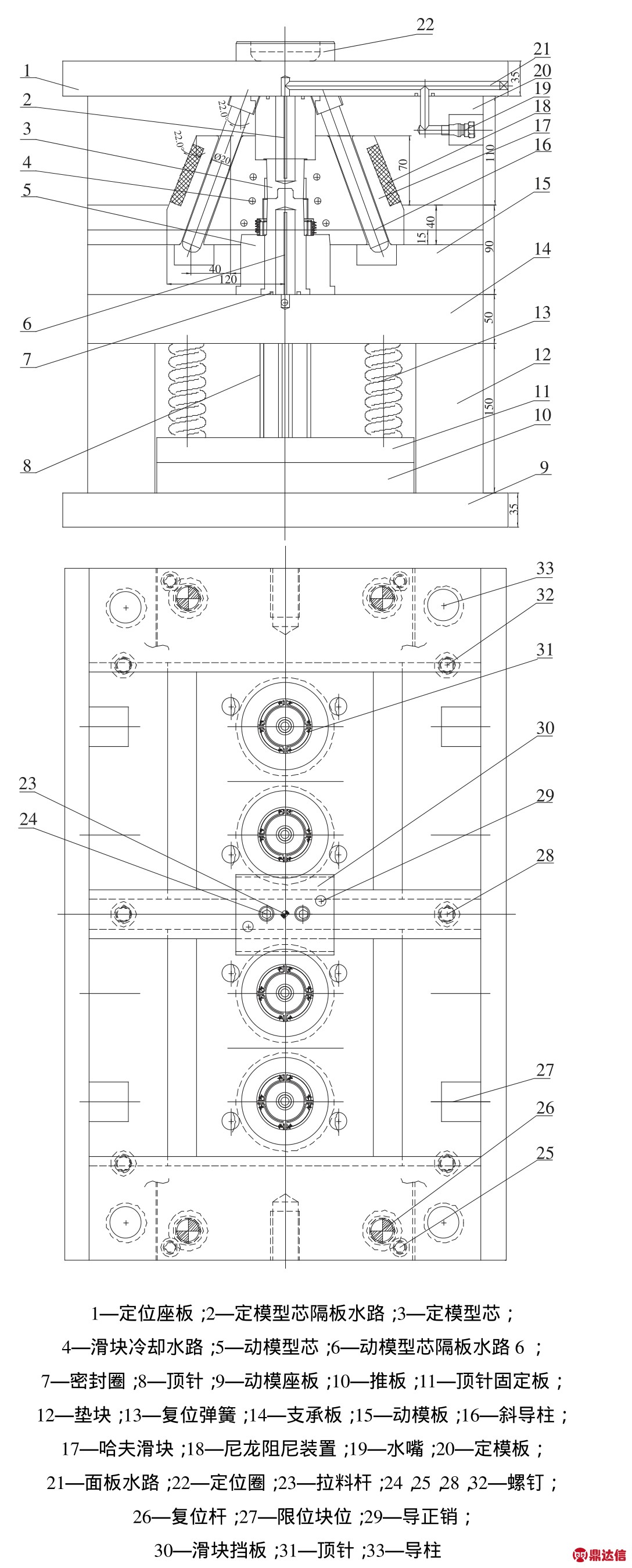
图9 模具装配图
含锥螺纹、分段螺纹的双头螺纹转接头塑料件结构复杂,根据其结构形状及技术要求,依靠实践经验与CAD/CAE技术,正确判断塑料件拔模方向和选择分型面;再根据螺纹结构特征与分型面的相互关系,创建模具的核心部分动定模型芯结构和哈夫模块;然后运用模流分析软件对塑料件进行注射成型过程模拟,验证了成型结构方案的正确性,获得了POM熔体进入模具型腔后的充填流动行为;最后综合塑料件成型工艺分析、模具成型结构分析、模流分析结果,完成注塑模具的总体设计,妥善地解决了特殊螺纹结构塑料件的成型与脱模困难的问题,避免了使用液压、马达、链传动、齿轮传动等复杂模具结构。经生产实践证明,该模具结构精巧,动作平稳可靠,螺纹转接头满足使用要求,该设计方案不但缩短了模具开发周期,而且降低了模具的设计和制造成本,为类似产品模具研发提供了参考。