摘要:为了探索数控车床加工小直径螺纹工艺研究,本为介绍了一种自动走刀攻螺纹的加工方案。该方案可以实现在数控车床利用程序控制,自动完成中心孔的钻削、螺纹底孔的加工及螺纹的加工,提高了加工效率,并且有效保证了螺纹的加工精度,是一种值得推向整个机加工行业的方案。
关键词:数控车床;程序控制;自动加工
0 引言
车床加工螺纹通常为车削螺纹,由于螺纹的直径原因,对螺纹底孔有着一定的要求,当螺纹底孔小于螺纹车刀的直径时,螺纹将不能够加工。在普通车床上,通常会利用机床的尾座,装上钻夹头,夹持丝攻,通过手摇进给的方式,实现攻螺纹,但这一工艺,对于操作工人的技术水平要求较高,且效率低下。本文通过某一零件为例,如图1所示,详细介绍利用数控车床加工M8直径螺纹的工艺。
1 加工工艺分析
通过分析图纸可得知,该零件为一个回转体轴类零件,零件材料牌号为45号碳钢。零件包含了外圆、倒角、端面螺纹,加工方案为加持工件的左端,伸出卡盘60mm,利用外圆车刀加工断面、外圆及倒角,由于螺纹直径为8mm,螺纹底孔较小,利用数控车削方案不可行。现采用先钻中心孔,钻螺纹底孔,攻螺纹的方案加工。
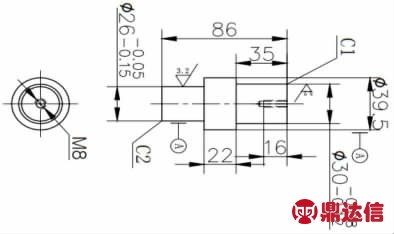
图1 零件图
2 刀具的选择
通过上述的工艺分析可得知,加工该零件总共会应用外圆车刀、中心钻、螺纹底孔钻、丝攻四把刀具。外圆车刀选用75°粗车可转换刀,刀头牌号为WNMG0804,形状为桃型,具有强度高,耐磨性好,可利用面多等特点,如图2所示。中心钻选用90°定心钻,材料为硬质合金加涂层,常用的中心钻定完中心孔后,钻头在钻完孔后,还得利用倒角刀进行孔口倒角,而现选用的定心钻在钻定位孔的时候,孔口会留下45°的倒角,避免了二次倒角,提高了加工效率,如图3所示。螺纹底孔钻选用普通麻花钻,丝攻为螺旋切削丝锥。
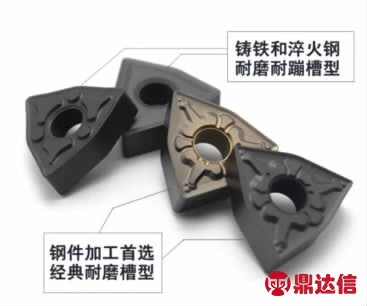
图2 外圆车刀片
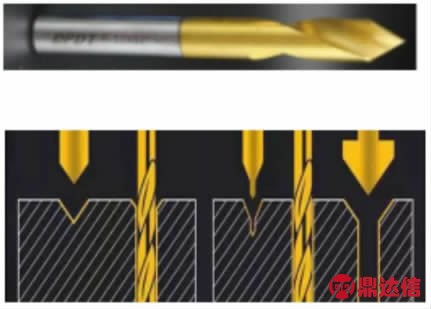
图3 定心钻
3 刀具夹具工装设计
目前市场四工位的车床较多,四工位刀架如图4所示,此零件需要安装四把刀具,由于数控车刀柄特殊结构,四工位刀架一次难以完成四把刀具的安装,为了提高加工效率,设计一款同一工位可以装夹两把刀具的工装夹具,如图5所示。夹具以地面定位,在中间部分根据钻夹头刀柄的大小开设两个孔,每个孔的上方设有两个紧固螺丝,用来锁紧刀柄。两个刀柄孔一定要保证在同一中心高度,便于调节钻头与丝攻和工件中心的高度。该夹具结构简单,制造成本低,同时解决了刀具工位不够的问题。为了提高该夹具的使用寿命,夹具采用淬火处理。
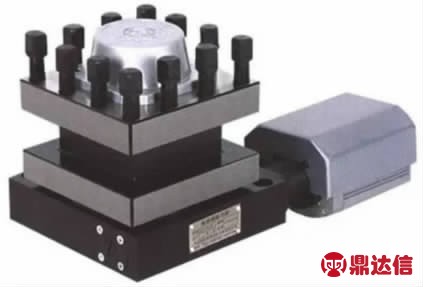
图4 四工位刀架
4 螺纹加工参数计算及程序
根据图纸所示,该螺纹为M8的标准螺纹,查表可得知螺纹螺距为1.0mm。螺纹的加工方法借鉴普通机床攻丝方法,当主轴旋转一周,丝攻X向移动一个螺距值,即1mm。设定主轴转速为每分钟100转,采用G01直线进给,进给速度F=100mm。当螺纹加工到图纸要求时,设置暂停时间,主轴反转,依然保持相同的转速和切削速度直线退出,切记不能用G0的速度退出,否则会把已经加工好的螺牙拉坏。具体程序如下(西门子802C系统):
G54 G90 G94(设定工件坐标系每分钟进给)
G0x80Z100(设定换刀点)
M06 T3D1(调用钻头参数)
M03S1200(螺纹底孔加工转速)
G0X0Z2
G01Z-18F150
G0Z10
M06T3D2(调用丝攻参数)
M03S100(螺纹底孔加工转速)
G0X0Z2
G01Z-16F100
G04 S2(暂停2秒)
M04 S100(主轴反转)
G01Z2F100(直线退刀)
G0x80Z100(返回换刀点)
M05
M30
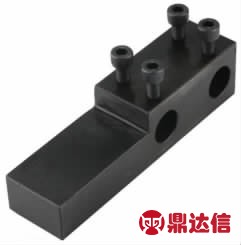
图5 刀具工装夹具
5 结论
数控加工螺纹加工工艺有一定的特殊性,在加工过程中,不仅需要合理的选择好刀具材料,同时还要控制好切削参数以及刀具角度,选择适合的编程指令,并在加工的过程中时刻保持着对生产环节的控制。只有这样全面的对加工工艺进行管理,才可以保证螺纹加工中的效率以及质量。该方案实用于回转体端面小直径螺纹的加工,具有高效、高能等特点,且刀具工装夹具结构简单,制造成本低等优势,具有较高的推向一线加工行业的意义。