摘要:通过分析阀体的结构特性,制定合理的加工工艺路线,设计适宜的加工工装,选用合适的加工刀具,解决了加工中遇到的各类问题,满足了设计图样要求。
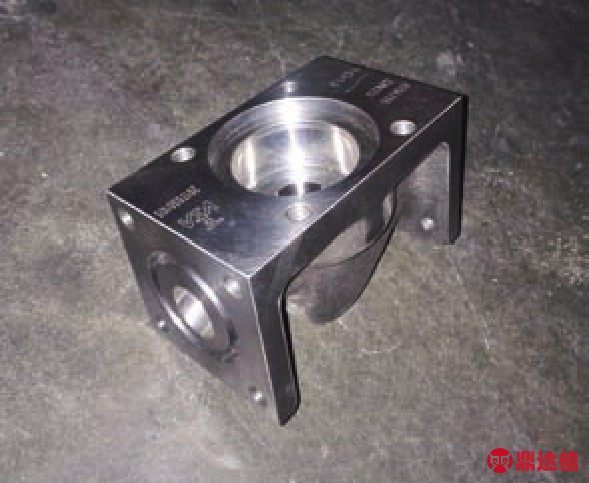
真空阀是指工作压力低于标准大气压的阀门,其一端连接真空泵,另一端连接需要抽真空的腔体或管道、控制开关,被广泛应用于核工业管线上。
1. 阀体结构及工艺难点分析
阀体结构如图1所示,其外形不是回转体,三端待加工面均为方形,加工时不能利用三爪自定心卡盘找正,需要用四爪单动卡盘,但每次生产批量都较大,校正困难,费时、效率低,加工误差大。另外,28°斜孔可以使用角度式平口钳在数控铣床上加工,但我公司角度式平口钳刚性较差,考虑设计工装在车床上加工。
2. 工艺方案
针对设计图样要求,阀体加工可采用以下工艺方案:铣削→划线→粗车中端→精车中端→车左右两侧→钻斜孔→钻、攻螺纹孔。加工工艺并不复杂,只是需要注意各工序的细节。
3. 铣削
如图2所示,铣削的目的是去除大余量,为精加工做准备,铣削出后续加工的定位基准(91±0.1)mm。
4. 精车中端
由于阀体外形结构限制及批量生产需要,特设计了阀体中端精加工工装,如图3所示。其中,60°密封面的加工是难点,密封面宽7mm,较宽,很难保证锥面母线的直线度。
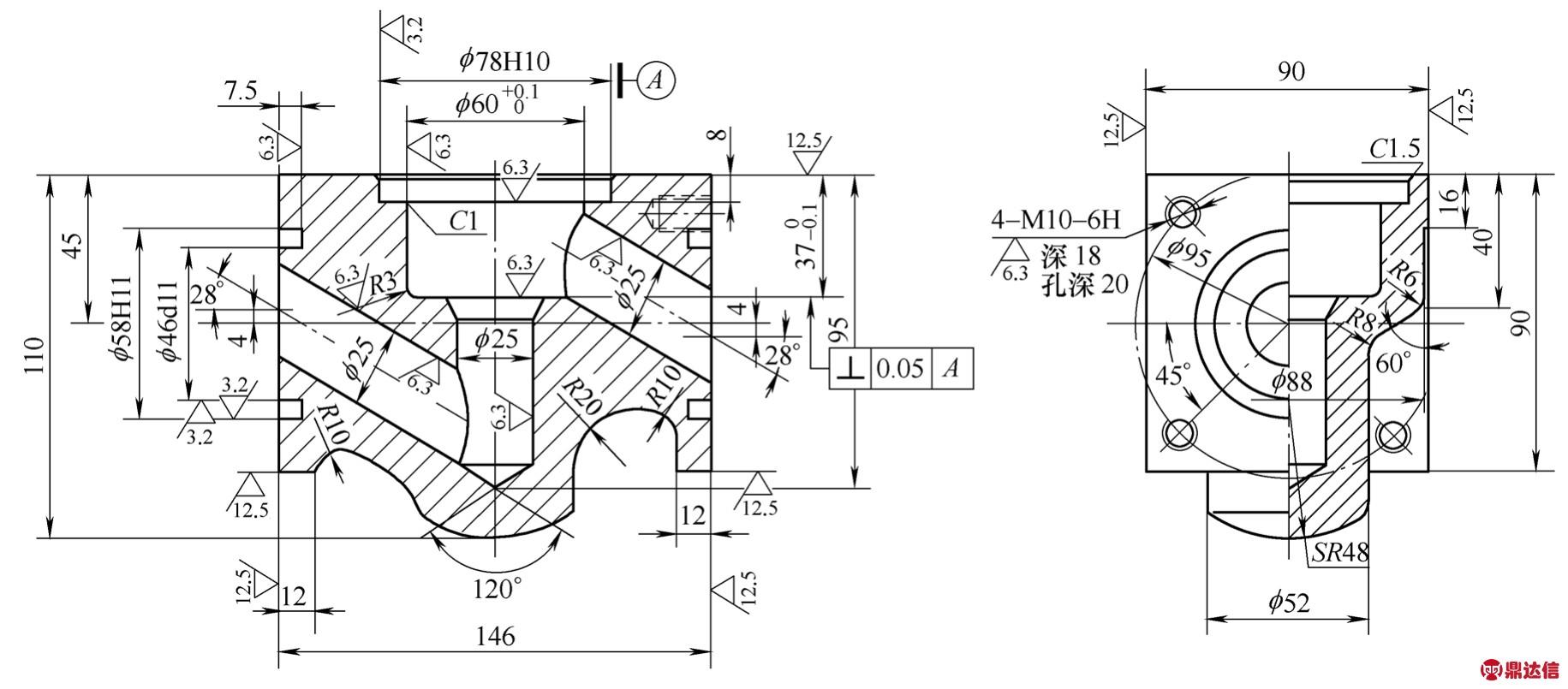
图1
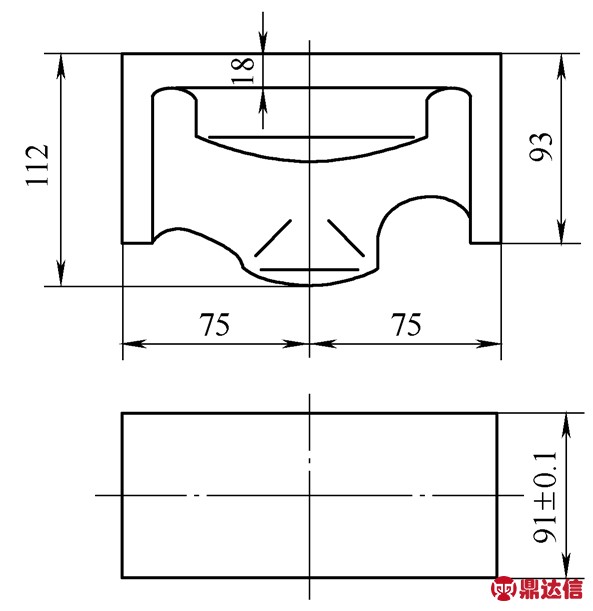
图2
精车中端密封面切削参数:转速900r/min,背吃刀量0.6mm,进给量0.04mm/r,刀尖圆弧半径0.4mm。60°密封面的抛光,抛光次数应尽量少。
5. 精车两侧法兰端面及端面槽
为满足设计要求及批量生产需要,特设计了阀体两侧法兰端面及端面槽精加工工装,如图4所示。加工端面槽时,由于刀具与工件的切削形式是线切削,因而易产生较大的切削力,同时加工时排屑较困难,切槽刀易产生振动和崩刃等现象,造成槽的表面存在振痕,因此,选择结构合理的切槽刀和制定合适的加工方案是端面槽加工的关键。选用新型刀片,采用优良的槽型结构以控制切屑流动和卷曲。特殊的后刀面结构使切削阻力降低20%,减少了振动,提高了工件表面质量。编程采用G74循环指令。在端面上切直槽时,切槽刀的右刀尖相当于车削外圆,所以装刀时注意切槽刀的右刀尖一定要与主轴轴线等高。
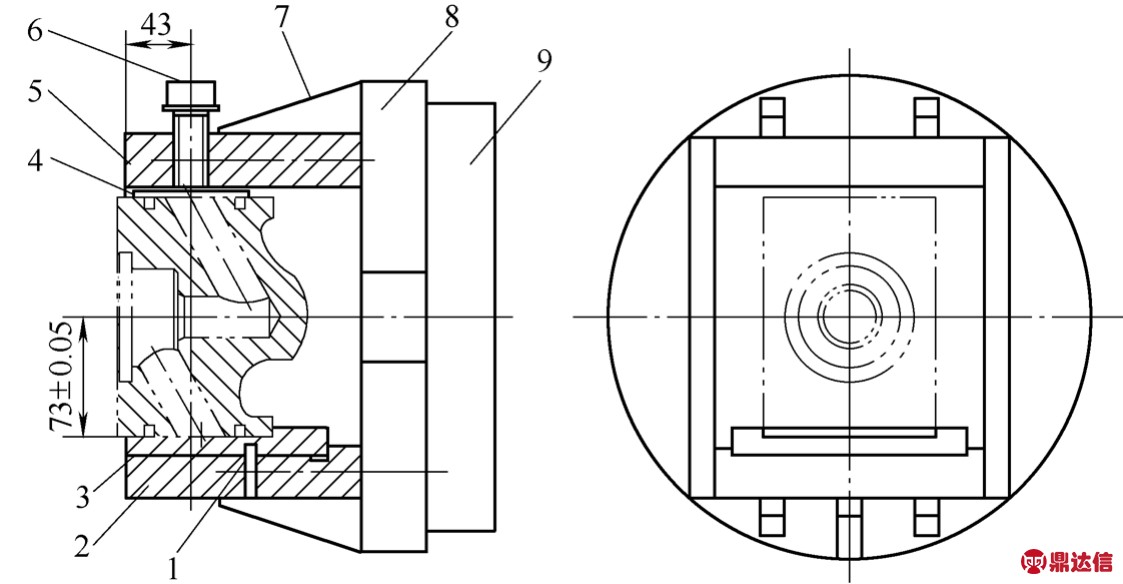
图3
1.定位销 2.下板 3.定位盘 4.压块 5.上板 6.压紧螺栓 7.筋板 8.底板 9.过渡盘
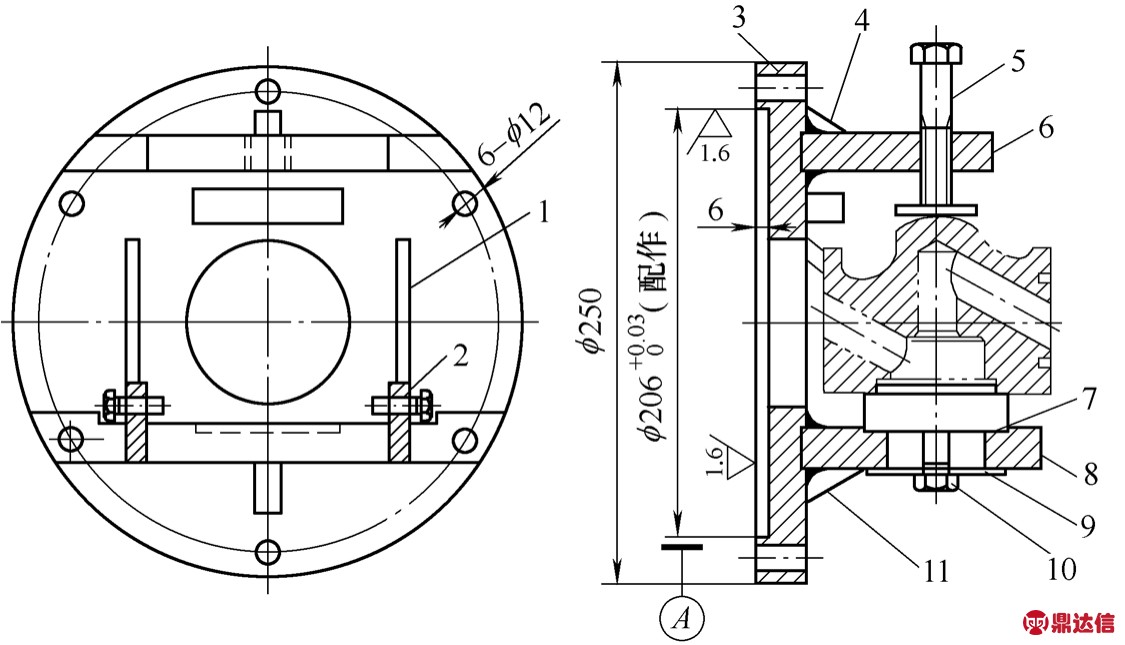
图4
1.拉筋 2.侧板 3.靠板 4、11.筋板 5.M16压紧螺钉 6.上板 7.心轴 8.下板 9.垫片 10.M12螺钉
6. 斜孔加工
斜孔加工工装定位方式同图3,区别在于其工装定位盘的定位槽是28°斜向,相当于斜面钻孔,斜面造成的侧向力可使钻头偏离预定中心,甚至使钻头折断。所以,钻削之前应打一个较大、较深的样冲眼,开始钻削加工时,尽量控制以较慢的进给速度起钻,待钻头切削刃完全参与切削后,再恢复正常进给速度。
7. 结语
我公司供给兰州某公司的真空阀A25K155,其阀体按上述工艺生产,检验合格率达100%。经生产实践证明,工艺路线合理可行,工装夹具设计合理,有效解决了装夹困难的难题,实现了大批量生产,既保证了零件加工质量,又提高了生产效率。