摘要:结合某集团熔铸车间6台真空自耗电弧炉在熔炼期间频繁烧地线和干扰断电故障现象,通过详尽分析VAR炉的电源结构、炉体结构、总线控制系统和接地系统,结合故障现象特点及故障炉次的熔炼电流、电压、真空等历史曲线,找出补偿电容器组电容损坏造成电压不平衡及抑制谐波失败、闭锁阀导电面密封圈材质选用不当引起接触电压升高及设备制造厂家接地系统设计缺陷等造成故障的根本原因,为钛及钛合金生产中相似设备故障排除提供参考和借鉴。
关键词:VAR炉;总线控制;共模电位差;接触电压
VAR炉是在真空10-1~10-2Pa环境中利用待熔金属制成自耗电极的电弧来冶炼钛、钛合金、铌及其合金等难熔稀有金属的主要设备。由于称重系统智能化技术及自动控制系统日渐成熟,使得熔速控制精准、稳定,从而使熔炼出的合金偏析和夹杂得到有效控制,是目前世界上钛及钛合金主要熔炼方法[1],在国内得到广泛应用。但是由于设备固有特点(大电流产生的强磁场)和总线控制设计瑕疵,非常容易造成熔炼期间干扰断电,严重影响产品质量和成材率。本文通过对几台进口电弧炉故障断电的分析和改进,达到为稀有金属熔炼过程中相似设备故障排除提供参考和借鉴的目的[2]。
1 VAR炉设备结构及故障简介
1.1 直流电源系统构成
某集团8 tVAR炉熔炼电源选用2×20 kA/90 V可调直流电源。主电路采用10 kV经两级降压后通过晶闸管可控整流方案,为抑制谐波和降低电压不平衡,采用12脉冲可控整流,考虑熔炼期间功率因数cosφ较低和抑制谐波需要,装设了并联电容器无功补偿装置[3]。整流电源主电路如图1所示。
1.2 炉体结构及熔炼工艺过程
炉体由支撑框架、炉头、炉室及炉头升降机构及炉头旋转机构组成;炉头顶部装有电极杆对中的X-Y调整机构;熔炼时炉室经由可移动的闭锁阀和铜坩埚组成密闭熔室,闭锁阀上法兰端面带有真空密封槽。
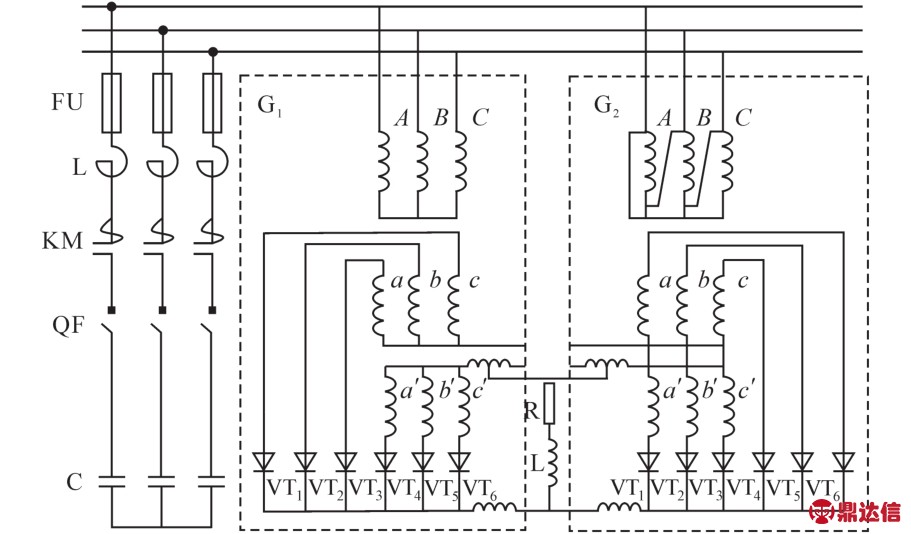
图1 整流电源主电路
Fig.1 Main circuit of rectifier power supply
铜坩埚即铜结晶器,熔炼产生的液态金属在里面冷凝结晶。其法兰端面带真空密封槽,熔炼时放在冷却循环水中,熔炼产生的热量被循环水不断冷却,液态金属在坩埚中自下而上冷凝结晶形成铸锭。
电极杆进给机构主要承载自耗电极及对称水套电缆,并带动其升降。其主要由伺服电机、变频电机、差动齿轮减速机、滚珠丝杆及假电极加紧机构等组成。在初装炉时由变频电机带动快速升降,而熔炼过程中的熔速控制是由伺服控制来完成的。
整流输出直流正极母排通过水套电缆连接至炉室,熔炼时通过闭锁阀和坩埚连接成一体形成电弧正极。整流输出直流负极母排通过水套电缆连接至电极杆,再经过假电极连接到由待熔金属制成的电极构成电弧负极。当正、负电极间小到一定距离时在近100 V引弧电压下起弧熔炼[4-5]。
真空自耗炉熔炼的工艺过程分为4个阶段:焊接、引弧、熔炼及热封顶。焊接的任务就是将组焊好的电极在真空环境下焊接到辅助电极上,达到焊直、焊牢且焊缝不能氧化。引弧的方法是在坩埚底部放少许引弧剂,在引弧电压下借助自耗电极和引弧剂间瞬间接触产生弧光放电,进而达到稳定的电弧燃烧,形成一定量熔池,为过渡到正常熔炼创造条件。引弧结束后熔池溶液覆盖坩埚底后按照工艺设定逐渐增大熔炼电流和电压,进入熔炼期。这期间的熔速与电流、电压有一定对应关系,可以通过电流控制系统、称重系统及电极伺服进给系统进行调控。热封顶又称补缩,目的是为了减少铸锭头部的缩孔,降低头部切除量,提高铸锭成材率[1]。
1.3 控制系统及系统接地简介
本文中VAR炉控制实时性要求较高,故主控制器选用SIEMENS公司的S7-400PLC。控制点多且相对分散,故选用较为先进的双层网络结构。上层工业以太网用于连接PLC和上位机INTOUCH监控软件;下层PROFIBUS-DP网络,用于连接S7-400PLC与现场的楞次伺服控制器、HBM称重控制器、稳弧控制器、编码器及由BECKOFF通讯模块组成各控制子站。设备的接地是将熔炼电源地和控制地分开构成各自独立接地系统,由于熔炼电源直流正极(+)共地,而供PROFIBUS-DP网各个通讯子站及现场控制设备的直流控制电源是负极(-)共地,如图2所示[3,6]。
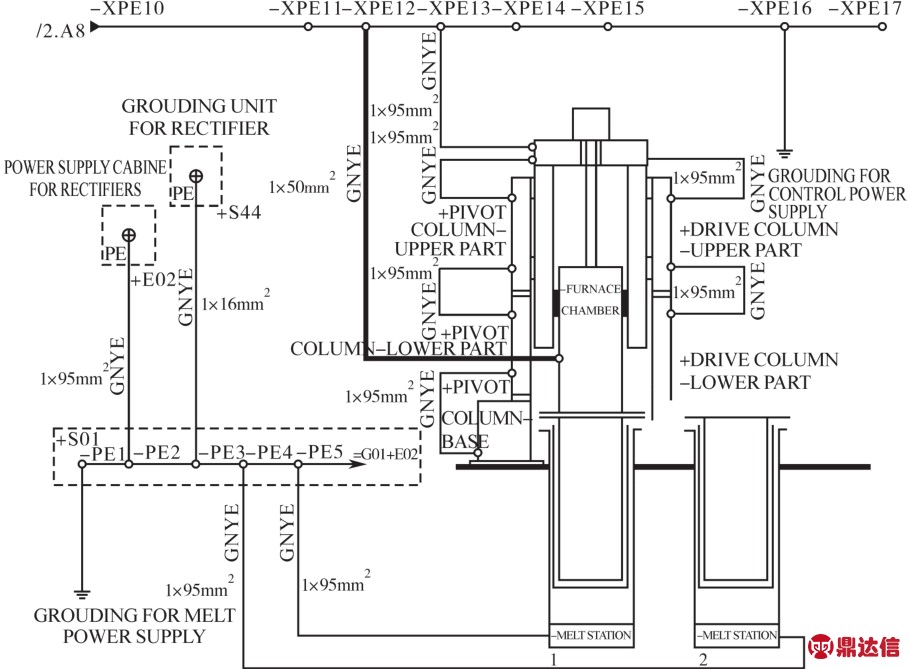
图2 接地系统图
Fig.2 Earthing system chart
1.4 故障简介
故障主要表现为:1)在焊接和热封顶期间干扰断电,这时PLC会产生报警,主要是与整流柜相关的故障信息;2)熔炼期间故障断电并伴有烧炉室引接地线(见图2深色线)、烧闭锁阀支撑及夜间熔炼时闭锁阀和炉室法兰接触处有明弧产生,控制子站,特别是装在炉头上的控制子站通讯模块BK3120的DP接头及控制模块的地线端子处有明显烧痕,这时产生的报警信息主要围绕装在炉头上的控制箱N02~N15所带子站的控制内容。
2 VAR炉故障断电的原因分析
2.1 补偿电容器组的电容损坏造成电压不平衡及谐波干扰的影响
从故障出现的时间造成干扰断电,主要发生在焊接阶段和热封塑阶段,这2个阶段有一个共同特点,即电弧的频繁产生和熄灭会造成主电路超瞬态的开路、短路2种极端状态间切换,随机且大幅度波动的无功功率会引起严重的电压波动和闪变,如下式所示[7]:

式中:d为电压变动;ΔQmax为最大无功变动量;Sc为690 V母线短路容量。
此时的电弧电流处于不规则的急剧变化状态及弧阻的非线性将容易产生11次、13次等特征谐波,特征谐波电流含有量高达13.3%。当连接组为不接地星形的补偿电容器组的每相有电容损坏时会造成断相,谐波电流无法形成回路,得到抑制,这时高次谐波会通过熔炼电源共地的正极(+)(也是控制电源的负极)干扰PLC的PROFIBUS-DP总线控制系统中各个子站的通讯模块的控制电源,使子站通讯超瞬态中断而造成断电,且断电后瞬间恢复通讯,这与出现的故障现象十分吻合。
2.2 接地系统设置不当引起共模电位差的影响
从图2可知,设备熔炼电源地和控制系统地各自单独设置,熔炼电源正极(+)共地;控制电源DC 24 V负极(-)共地;且设计图中要求控制地的接地电阻小于1 Ω,如果是直流和工频50 Hz电源没有问题,但PLC,PROFIBUS-DP网络中通讯模块及现场控制器大多为数字化,其怕干扰的频率为数十乃至数百MHz。所以功能性接地电阻要求很低的直流乃至工频的接地电阻是毫无意义的,不但起不到降低干扰电位的作用,而且浪费财力和人力。通过表1和表2对不同截面接地体随着频率的升高而阻抗却降低很小就很好证明了这一结论。熔炼地和控制地在地中的土壤可以看作是阻抗Zearth(见图4)。当有电流 Iearth流过土壤阻抗 Zearth时,U=Iearth×Zearth,这一压降就是熔炼电源地和控制地共模点位差。当Iearth为干扰电流时,将产生一个干扰电压,通过控制电源的共地负极(-)对PLC及PROFIBUSDP网的各个通讯模块产生干扰。严重时会造成PLC无法访问到外围的各个通讯子站,从而造成断电[5,9]。
表1 25 mm2铜导体在土壤中的电阻和感抗ρ=800 Ωm
Tab.1 Resistance and reactance of 25 mm2copper conductor in soil
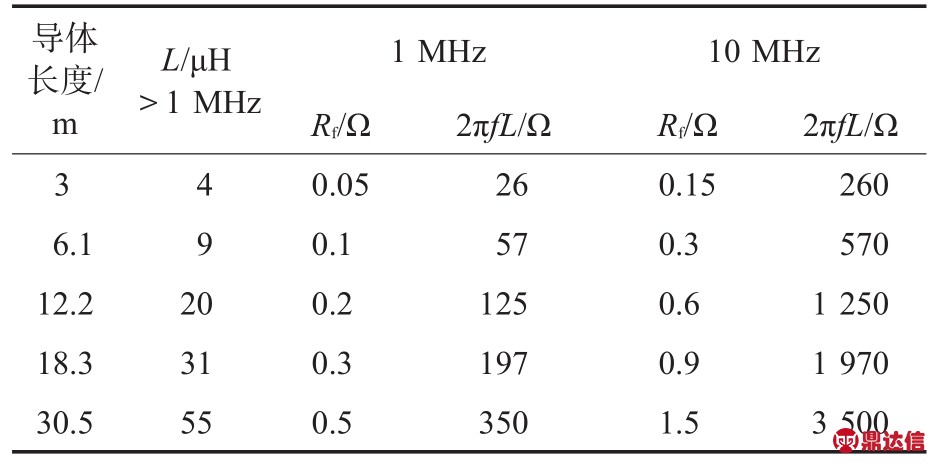
表2 107 mm2铜导体在土壤中的电阻和感抗ρ=800 Ωm
Tab.2 Resistance and reactance of 107mm2copper conductor in soil
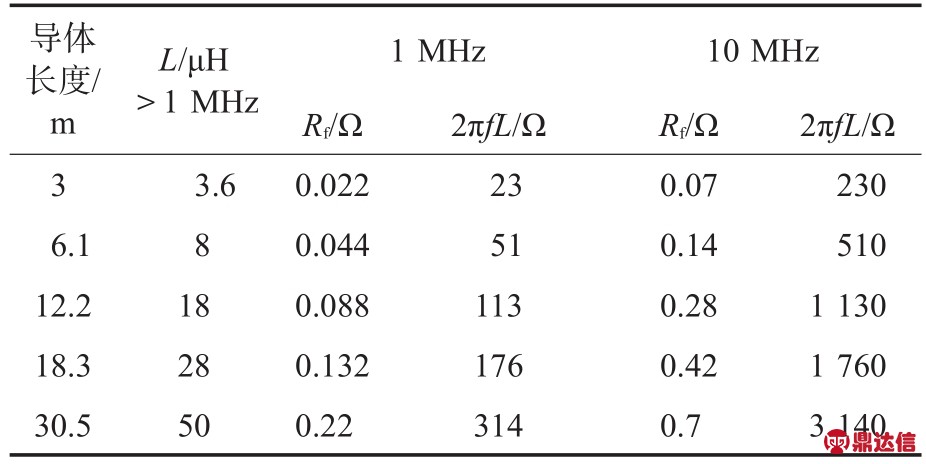
2.3 电弧电流回路接触电压增大的影响
熔炼电源负极(-)从整流柜母排引出后经水套电缆连接到电极杆上再经过辅助电极、熔炼电极形成电弧的负极(-)。熔炼电源正极(+)从整流柜母排引出后经过水套电缆连接在炉室上,在熔炼时通过闭锁阀连接到铜坩埚上形成电弧的正极(+),且正极(+)经过一定阻抗共地(图2中深色50 mm2电缆长50 m)。在熔炼过程中之所以烧炉室上接地线和闭锁阀支撑脚,一定是有较大电流流经这两回路。同时说明在炉室和闭锁阀上对地产生一定电位差,正常情况下电弧电流回路线路压降是非常小的,不超过40 mV,而故障时压降抬升发生在炉室和闭锁阀上,排除了整流柜、母排、水套电缆。闭锁阀上端面铜法兰处有明弧就印证了这一判断,即电位抬升发生在闭锁阀和炉室、闭锁阀和坩埚的接触电压增大产生的。此处会有一个判断误区:既然接触不良为什么真空测漏却满足要求呢?后来发现问题恰恰出在闭锁阀铜法兰端面的密封圈上,密封圈的尺寸虽然没有变化,但是材质比以前使用的要硬,这恰好印证了接触电阻大而密封效果又很好的现象。用万用表测量接触电阻超过0.1 Ω,远远超过了熔炼时压降不超过20 mV的要求,换上以前材质的密封圈后故障消失[8-9]。
3 故障处理
3.1 给补偿电容器组加装不平衡保护
为了能及时监测补偿电容器组电容的状况,加装开口三角形的电压不平衡保护,如图3所示。当补偿电容器组有电容损坏时,通过故障信息提示操作人员及时维护[9]。
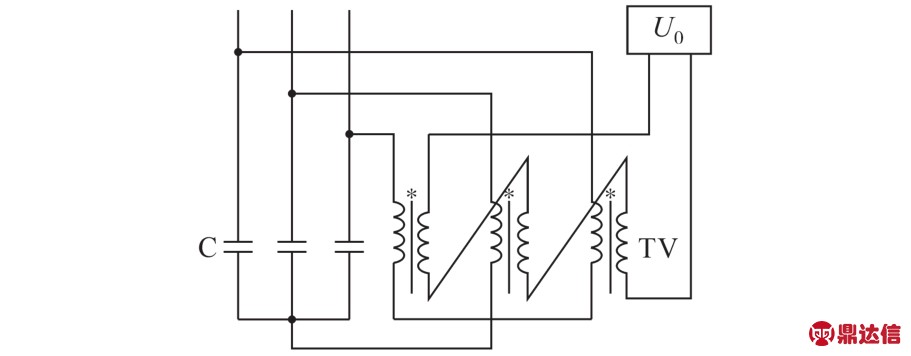
图3 共模电压抑制
Fig.3 Common-mode voltage suppression
3.2 将熔炼电源地和控制地进行等电位连接
为了消除熔炼电源地和控制地之间产生的共模电位差,将熔炼电源地和控制地进行等电位连接,如图4所示,并加装闭锁阀至接地极间接地线,以便消除接触电压降。完善操作规程,在完成装炉后,熔炼送电前用欧姆表测量炉头和坩埚间的接触电阻,保证熔炼期间接触电压不超过20 mV。

图4 电压不平衡保护
Fig.4 Imbalance voltage protection
4 结论
通过对VAR炉的电源、炉体结构、控制系统及接地系统等方面的分析。最终检查出补偿电容器组电容损坏造成电压不平衡及抑制谐波的失败、接地系统设计不当和由于密封圈材质的变化造成接触电压抬升是造成焊接补塑时干扰断电、熔炼时烧地线和烧闭锁阀支撑等故障的根本原因。更换损坏电容、更换密封圈及加装等电位连接线及闭锁阀接地线后故障消除,为类似设备的故障排查提供参考和借鉴。