摘 要:介绍一种可替代人工的全新碳纤维自动化上浆工艺,由真空取料、自动配料、料液循环供给及料液液位检测等环节组成,料液的循环补给采用了智能型PI控制算法进行控制,整套上浆工艺流程通过PLC进行自动控制,包括电机及各类阀门及检测装置。此系统可完全替代传统的人工上浆工艺,且在碳纤生产过程中增强了生产安全性,节省人力提高效率得同时也提高了产品的质量。
关键词:碳纤维;上浆液;智能PI控制;恒温;稳定;自动配料
0 引言
碳纤维的上浆是碳纤维生产的最后工艺,所谓上浆就是把浆液(sizing)均匀附着在碳纤维的表面上。上浆的稳定性和均匀性是影响碳纤维质量的关键一环,浆液能在每根单碳纤维丝表面形成一层薄薄的皮膜,使碳纤维在深加工中不起毛,且集束性好,耐磨性好,开纤和扩幅好,与基体树脂的润湿性好,相亲相容,界面粘结牢固,可有效传递载荷,是连接碳纤维与基体树脂之间的桥梁。
1 碳纤维上浆工艺现状
本系统应用前的配料上浆方法是两名工人配合将各种物料分别用桶多次称量,然后人工将物料提到混合釜上方从进料口加入混合釜中,然后操作断路器启动电机,开始搅拌,搅拌均匀反应完成后,手动打开放料阀,把物料放入缓冲罐中待用,这种混合均匀反应完成的物料称为上浆液(sizing);浆液放入生产线上的上浆槽内,碳纤维从上浆槽浆液中穿过,完成上浆工艺,由于碳纤维在经过上浆液时,上浆液会附着在碳纤维上产生消耗,上浆液液位会慢慢降低,上浆槽液位变低时,由人工感官判断,从缓冲罐放入一定量的上浆液,这样操作无法实时跟踪精确控制,会人为造成液位忽高忽低,严重影响上浆质量;同时跟踪检测到一年四季气候的变化,即环境温度的变化也会影响上浆质量。
生产线上的上浆槽装置,如图1所示。缓冲罐里的上浆液通过管道放入液位槽,液位槽中有部分浸入上浆液的导丝辊,碳纤维通过导丝辊进入上浆液浸润上浆。
此时影响上浆质量有3个因素:一是上浆槽的液位变化,要控制在90%±2,另一个是上浆液在液位槽中相对静止容易形成沉淀,第3个是环境温度也很大程度影响上浆液的粘度,温度要恒定在25°C±2,以上3个因素要严格控制在参数和要求范围内,才能保证上浆液的稳定和上浆的质量,进而保证碳纤维的质量。
2 工艺改进技术方案
针对以上工艺进行论证和讨论,继而进行设计改造。
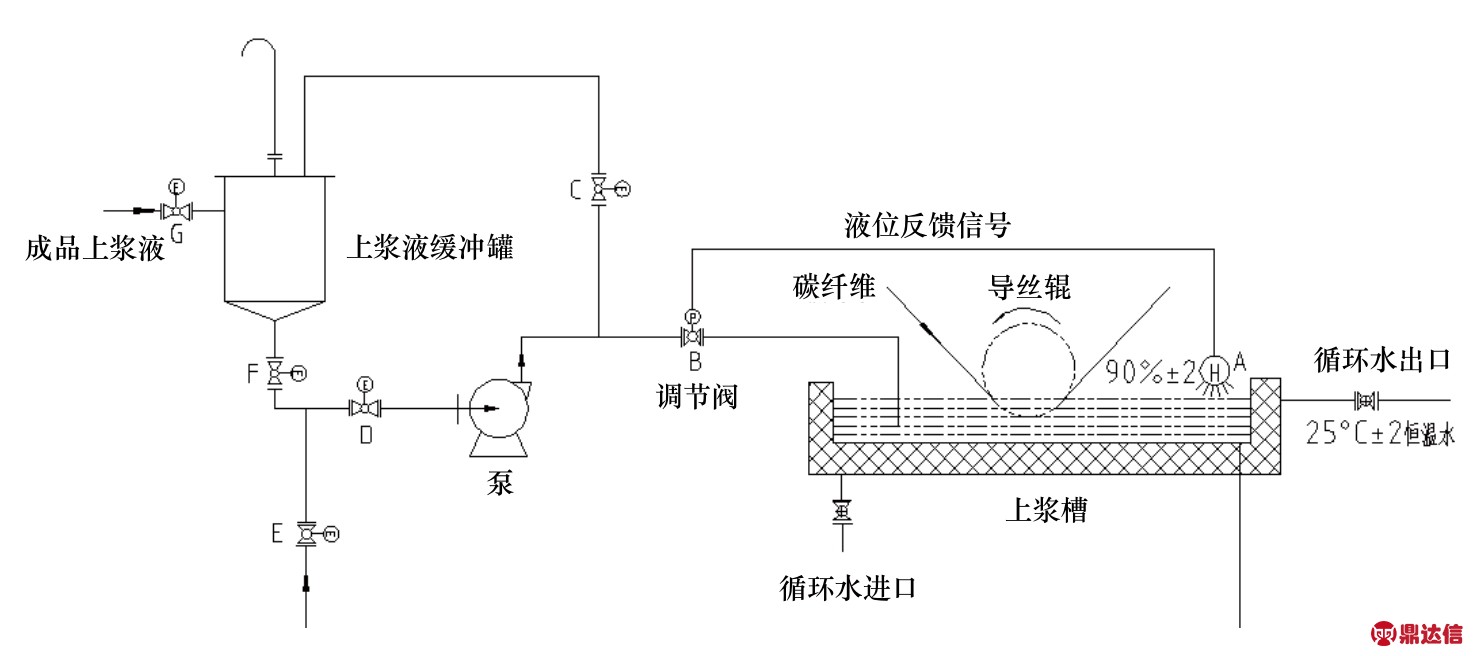
图1 上浆槽装置
2.1 系统组成
本配料上浆系统由以下单元构成:控制系统单元、配料称重单元、混合搅拌单元、储液搅拌单元、真空供给单元、恒温循环水系统、上料循环单元和液位控制单元。
2.2 控制系统
控制单元含控制电柜,内部含有断路器、接触器、继电器、开关电源、变频器、滤波器、PLC、触摸屏等电气元件,通过航空插头连接器连接电缆,与现场电气设备连接(电机、电磁阀、调节阀,超声波液位检测等),进行控制、数据采集与反馈,使控制系统防护等级达到IP55以上的等级。触摸屏为主操作单元,屏上显示整个配料上浆系统全局图,每个单元都可以通过点选相应图标来进入功能选项区,来进行监视和控制。
2.3 技术方案
我们采取真空吸取的方法,把物料输送到高位称重配料罐内进行称重计量。如图2所示,真空单元主要由真空泵9和一个真空缓冲罐8构成,两台真空泵一备一用,当出现故障时可以即时切换保证配料正常运行。真空泵抽吸真空缓冲罐内空气形成负压,真空缓冲罐顶部有管路通往配料罐A和B,为其提供上料所需的负压。真空缓冲罐顶部有真空度检测与控制P,入口有真空电磁阀V0,当真空缓冲罐的真空度达到设定值,则PLC会控制真空马达9停止运转,将电磁阀V0关闭,封闭储罐防止真空度跌落,达到节能目的;当开始使用或者真空度下跌到设定值时,PLC则控制启动真空马达运转,同时打开电磁阀V0。
A、B和C料罐配有精确的称重系统、专用配料控制器和称重模块,精度可达到0.01kg。配料罐A、B为料液罐,配料罐C为纯水罐,每个配料罐底部安装四个称重模块进行精确称重计量,称重模块数据传送到控制柜上的称重控制器上,料罐上方真空管及进料管都装有电磁阀门,下方出料管也各装有电磁阀门进行放料开关控制,电磁阀下方管路接入位于配料罐下方的混合罐3,混合罐上方安有搅拌电机进行搅拌,混合罐3下方出料口管路分为两路,一路为清洗维修使用的排放废料管路,通过手动阀门控制排放到废料回收池,另一路通过电磁阀门控制通往下方的上浆液缓冲罐。
图1中上浆液在泵→阀门C→上浆液缓冲罐→阀门F→阀门D,形成循环,保证浆液不能形成沉淀;泵→调节阀B→上浆槽→阀门E→阀门D形成循环,通过超声波液位检测变送器与调节阀B,共同组成负反馈PI(比例积分)控制,精确调节上浆槽的液位。
3 具体操作步骤
在控制柜上有远程电源启动按钮,按动此按钮,启动电源,约10秒左右的系统自检后,触摸屏正常显示,这时操作触摸屏,点击真空泵电机图标M1(M2),打开电机操作界面,点击“开”按钮,真空泵电机开始运转,此时可以在同一界面设定电机工作频率,对应真空缓冲罐中的负压设定值P,真空泵抽取真空缓冲罐内空气形成负压,当真空度P检测到已达到设定要求的上限值时,电机M1(M2)会自动停止运行,进气阀V0会自动关闭,当真空度P降到设定的下限值时,电机M1(M2)会自动启动,进气阀门V0也会自动打开,从而保证真空缓冲罐内负压的供给。
点击屏幕上配料罐图标A,进入自动配料页面(每个配料罐对应一个配料界面),设定好所需料液重量,点击“开始”,此时控制器PLC会先给出指令控制配料罐上端真空阀V2打开,将配料罐抽成真空,当真空度达到,控制器给出第二个指令将进料管口的电磁阀V1打开,此时开始进料,当称重模块检测到进入的物料重量已达到设定数值,控制器会自动将进料口阀门V1和真空阀V2快速关闭。以此类推,其他两个B和C配料罐进料也是相似原理。
当三个ABC配料罐均已加好料,控制器PLC会自动识别加料完成信号,接着给出控制信号将配料罐下方各自的出料阀门、上方的排空阀(消除真空)及混合釜上方进料阀门都打开,配料罐内的料液由于重力作用自动流入混合釜内,配料罐称重显示清零后说明出料完成,控制器给出信号控制上述打开的阀门关闭,然后启动搅拌电机M5进行混合搅拌。
当搅拌时间达到要求,控制器继续控制搅拌电机停止运行并将混合釜下方阀门V14打开,反应混合充分的料液即上浆液流入缓冲罐内备用。
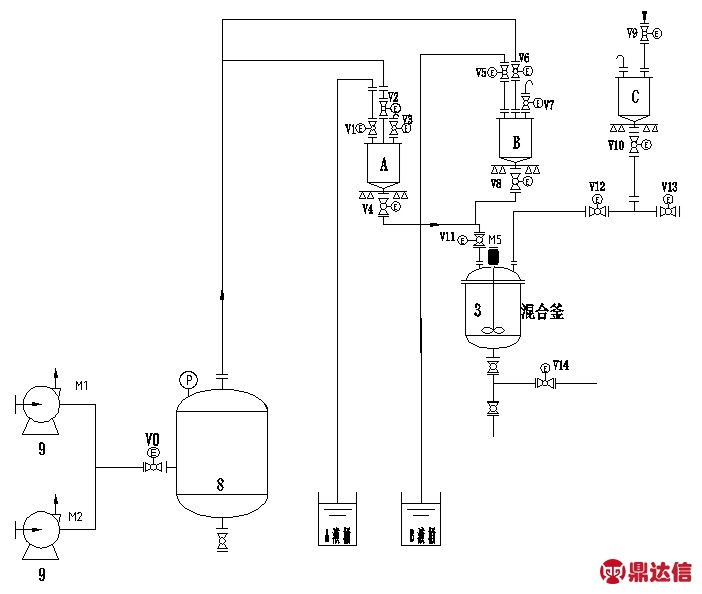
图2 真空配料装置
如图2所示,操作触摸屏,点击调节阀B图标,进入液位控制画面,画面有调节阀B开度和液位高低设定对话框,有调节阀B开度和液位反馈的实时显示数据,画面还有PI(比例积分)的自学习功能按钮,启动自学习功能,系统会根据工况自动寻找最佳的PI(比例积分)参数,减少人为干预,达到自动精确控制。并且,自学习完成后,PI参数自动显示在屏幕上,方便控制。如果需要手动,则点击画面上的PI按钮即可。
完成自学习功能后,设定好所需液位,有效PI功能,超声波液位变送器A会检测液位数值,并将数值实时传送给控制器PLC,控制器将实时数据和设定液位数值进行比较,当实时液位大于设定值,控制器发出指令将调节阀B减小开度或关闭,当实时液位小于设定值,(图1),控制器发出指令,调节阀B开度增大,补充上浆液到液位槽,维持恒定液位高度。
4 结论
本系统为一种改进的碳纤维上浆工艺,是PI(比例积分)控制,属于智能型的控制功能。PLC控制器会根据实际液位数值与设定值之间差值大小来控制调节阀B开度的大小,当实际数值远低于设定值时,调节阀B会被控制全开,当实际数值逐渐接近设定值时,调节阀B开度也会跟随逐渐变小,直至实际值与设定值相等时,调节阀B也会完全关闭。环境温度的变化会影响上浆液的稳定性,因此上浆槽设计加装夹层(如图1所示),夹层中通入恒温水,温度控制在25°C±2范围内,位于恒温水槽中的水,夏天通过冷冻机冷却,冬天通过流体加热器加热,保证液位槽内的浆液温度维持恒定,不超过25°C±2范围。
此上浆系统,系统解决了碳纤维上浆工艺问题,保证碳纤维的质量,为碳纤维的应用奠定坚实基础,产品合格率提升了30%。