摘要:伴随汽车电动化发展和主动安全技术要求,基于真空助力器的传统液压制动系统已经难以满足实际需求。因此,设计了一款电子液压制动助力器,首先剖析其工作原理同时针对电动助力和主动压力控制两种工况给出了完整的设计思路。然后分别提出了基于输出线性化的滑模电流控制和基于抗饱和PI算法的双闭环压力控制,最后通过仿真和台架实验验证了算法的可靠性。
关键词:电子液压制动助力器;滑模控制;双闭环控制;抗饱和PI控制
引言
电子液压真空助力器相较于传统真空助力器主要具有的优点:(1)采用电机驱动作为执行单元,可以进行主动控制,满足汽车主动安全控制和无人驾驶的需求并且具有低延迟和高可控性的特点。(2)传统真空泵或发动机被取代,制动助力系统更加紧凑,系统集成度更高[1]。(3)功能可扩展性,在新能源汽车中可以与驱动电机协调,提高制动能量回收效率,降低能耗[2]。
在工业领域,具代表性的成熟电动助力产品有博世公司的iBooster和大陆公司的MCK-1,已经有产业化应用[3]。学术界相关研究主要集中在液压制动力和再生制动力协调,汽车主动安全控制以及良好踏板感模拟三个方面[4]。吉林大学潜磊等人提出了一种基于控制反馈盘主负面位移差模拟真空助力器踏板感的方法[5]。清华大学赵洵等人提出了一种基于滑模方法控制推杆位移跟踪驾驶员助力意图的控制策略,并进行了台架测试[6]。
真空助力器工作原理,首先通过测量踏板推杆和主缸推头相对距离模拟空气阀和真空阀作用进而设计助力曲线,能够方便识别驾驶员制动意图并实现良好的踏板感受。然后设计了基于滑模控制的反馈线性化电流跟踪方法,结合PI控制器实现主控压力控制。数值仿真和台架实验都表明提出的助力策略和控制方法都具有优异的效果。
1 系统建模与电流控制器设计
采用星型连接的无刷直流电机作为驱动源,电机扭矩首先经过一级齿轮放大,进而通过滚珠丝杆将旋转扭矩转化为轴向作用力进而推动主缸,实现助力,具体实现见图1。
无刷直流电机采用6个MOSFET基于霍尔六步换向逻辑对电压进行斩波进而驱动电机,电机转速可以通过霍尔传感器计算获得,母线电流通过电流采样电阻硬件转化获得。六个状态中每次只有两相导通,因此电机模型类似于直流电机,可以简化:
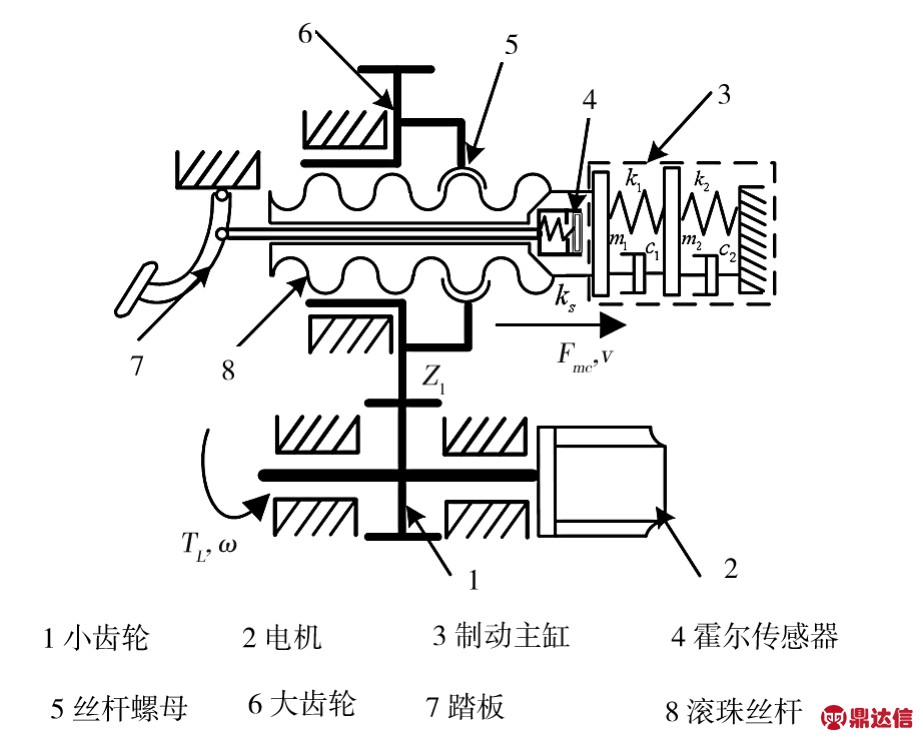
图1 电动液压助力机构

式中:i—电机母线电流,A;Je—等效电机转动惯量,kg·m2;ce—转动阻尼系数;TL—电机负载,N.m;u—斩波后电压,V;Re—电机等效电阻,Ω;Le—等效电感系数,H,Ke—反电动势系数;ω—电机转速,rad/s。
为实现电流控制,仅考虑电压平衡方程,进一步将式(1)表示:

式中:a1=-Re/Le, b1=-Ke/Le,θ=-1/Le,定义误差e=i-ides;ides目标电流。为减小滑模控制抖震,采用积分滑模的方法,定义滑模面:

式中:α>0,代表趋近系数。
对式(3)求导,s=0并令,联合式(3)和式(2),可得等效滑模控制律为

采用指数趋近率s=-εsgn(s)-ks,可以保证系统状态远离切换面时具有较快的趋紧速度,接近切换面时控制率较小,则最终控制率:

将式(5)代入式(2)和式(3)得:
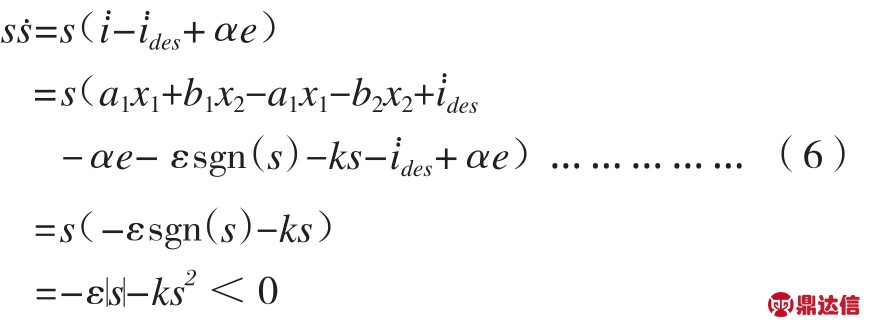
因此,滑模控制器电流跟踪误差最终会趋向于零。
2 主动压力控制器设计
主动压力控制中,核心是调控主缸压力,液压系统具有如下特点:前一阶段由于液压负载没有建立起来,主缸反馈力仅由负载弹簧反馈,相当于前半程系统阻尼小,后半程液压力建立起来后,系统负载会迅速上升,由负载弹簧和液压力共同提供,相当于后半程系统阻尼大。采用分段PI控制方法,削弱系统阻尼变化带来的影响。由于液压系统存在一定的滞后性,因此积分项不宜过大,以避免系统震荡。控制方法:(1)让积分控制仅在误差小于某一值后才起作用,目的是减弱目标变化后积分环节存在带来的延迟。(2)PI控制器最常见的问题是积分饱和,当系统存在输出饱和或非线性问题使得实际控制目标难以跟踪期望时,由于误差存在,积分便会一直积累,当控制目标再次发生变化,控制器需要很长的时间退出积分饱和区,这必然造成控制器性能恶化。因此,通过控制积分作用的范围和幅值大小,以实现良好的控制效果。PI压力控制器为外环,输出为期望电流,滑模电流控制器为内环,通过双闭环控制实现精确的压力控制。对PI控制而言,提高系统响应特性需要提高比例系数和积分系数,这必然会带来超调过大的系数甚至会带来输出饱和甚至震荡。如果引入前馈控制,则可以通过前馈控制介入提高系统响应,同时降低超调。实际电流前馈通过如下方式获得:先以电流为横坐标,液压为纵坐标,标定压力-电流前馈MAP图,实际控制时通过查表获得,输入为期望压力,输出为基准电流。最终,具体控制逻辑见图2。
占空比:

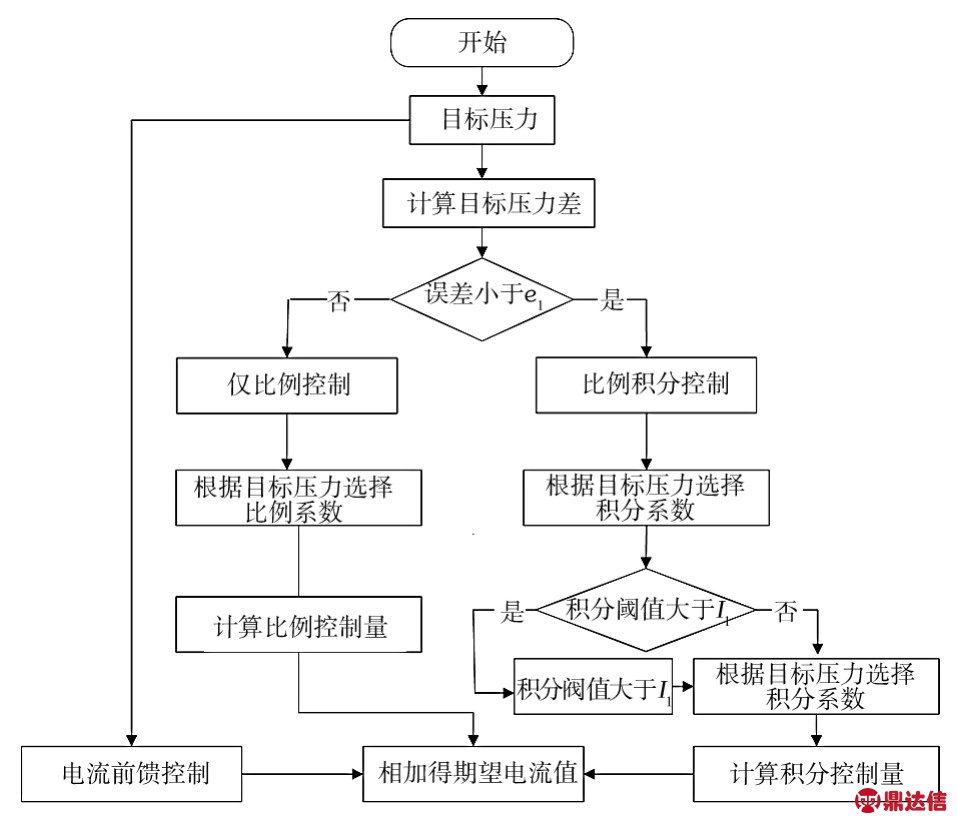
图2 PI压力外环控制逻辑
3 制动助力模块设计
图1采用霍尔传感器测量制动推杆和主缸推头之间的相对距离(图中反应盘省略未画出),在机构上,采取了三段化设计,以开始助力位置为平衡点,传感器示数向前为正值,向后为负值,通过预先标定的方式,将正负最大值分别标定为±100%,传感器100%类比于空气阀完全打开,传感器负值用来反映驾驶员推出制动的紧急程度。
制动助力模块的设计目标主要分为两方面:(1)保证良好的踏板感,满足驾驶员的驾驶习惯;(2)能够建立足够的液压力,满足制动需求,简单而言,就是需要满足安全性和舒适性。将传感器位置量化,然后根据开度设计不同的目标电流值,产生助力。设计助力曲线见图3。
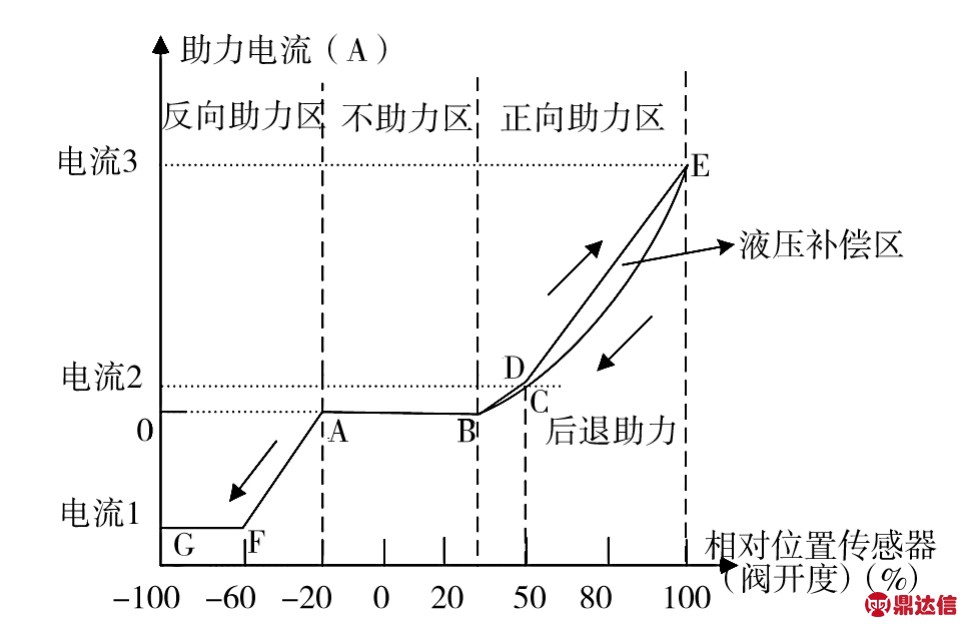
图3 助力曲线
将助力区间分为反向助力区,不助力区和正向助力区3段。当阀开度在AB范围时为空行程阶段,电机并不产生助力,这类似于真空助力器中推动空气阀柱克服阀回位弹簧前进的阶段。当驾驶员踩下踏板后,首先克服AB段的空行程,进入BD段,助力电流开始产生。BD段介入的时刻和电流对应调增值的大小。继续深踩制动踏板,踏板推杆开始接触反应盘,至此阀开度进入DE段,助力电流开始以较大的速率升高。之所以会有电流斜率的变化是因为负载的不同,当踏板行程较小时,回位弹簧产生的负载力大于液压反馈力,从量级上来看是比较小的。当液压力建立起来以后,液压反馈力超过回位弹簧力,且从量级上来看远大于第一阶段。斜率的大小与助力比大小呈正相关。当驾驶员逐渐推出制动时,由于液压存在滞后性,电流下降速率比电流上升速率应该更快,通过减小助力曲线来弥补液压滞后带来的影响。其中后退助力可行区见图3,BDEC围成的区域即表示液压补偿区。从B点到E点这一助力电流上升过程对于紧急制动和缓和制动阶段变化都是一致的。值得注意的是如果系统刚度不够,即使踏板弹簧回弹力和液压反馈力同时作用,踏板回弹速率依然不能跟上驾驶员收脚意图时,就需要额外的主动控制来控制踏板,使其“跟脚”。因此,设计了一段-100~0的位置,当驾驶员快速收脚时,传感器位置会变成负值,当驾驶员缓慢收脚时,传感器数值不会小于零。这一设计便使E-Booster可以反向助力,这在传统真空助力器中是不可能实现的,因为真空腔的压力不可能大于空气腔压力。设计的反向助力曲线见图3AF段,其斜率表示反向助力比。当系统回馈阻尼过小时,增大其斜率,当系统阻尼增大时,减小其斜率甚至在AFG段不助力。电流1表示反向助力的最大值,电流2表示调增值助力电流,电流3表示正向助力最大电流,数值大小及介入区间都可以根据实际情况进行调整。
因此,通过设计合适的助力曲线,理论上可以达到预期助力效果。制动开始介入的BD段助力电流不可以过大,由于此时系统负载较小,当助力电流过大时,会推动主缸推头突然前进较大的距离,但是驾驶员却没有继续增加的助力请求。所以传感器数值会被瞬间拉低,相当于阀开度降低,使助力电流减小,于是在液压反馈力和弹簧反馈力的作用下,主缸推头会被弹回,又导致了传感器数值变大,从踏板动作上来看就是当轻微制动时,会出现震荡的现象,这在实际应用中必然是要避免的,所以,设计助力电流时要结合理论曲线和实际系统特性。
4 算法验证
用MATLAB对所设计的滑模电流控制器的跟随效果进行数值仿真验证。其中滑模控制器参数:α=40 ε=0.1,k=10,仿真中工况理想,暂时采用恒定PI参数,其中kp=90,ki=60。仿真结果见图4。可以看到,压力控制误差小于0.1 MPa,电流控制误差小于0.2 A。分别进行压力跟随阶跃实验和电动助力,台架实验数据见图5。可以看到,阶跃实验中实际压力可以很好的跟随期望压力。助力工况下,期望电流根据位置传感器计算得到,电流可以较好跟随驾驶员制动意图产生助力电流。
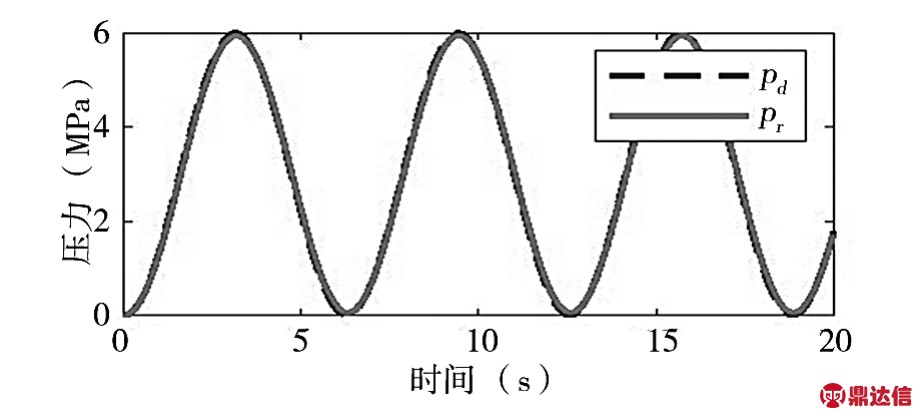
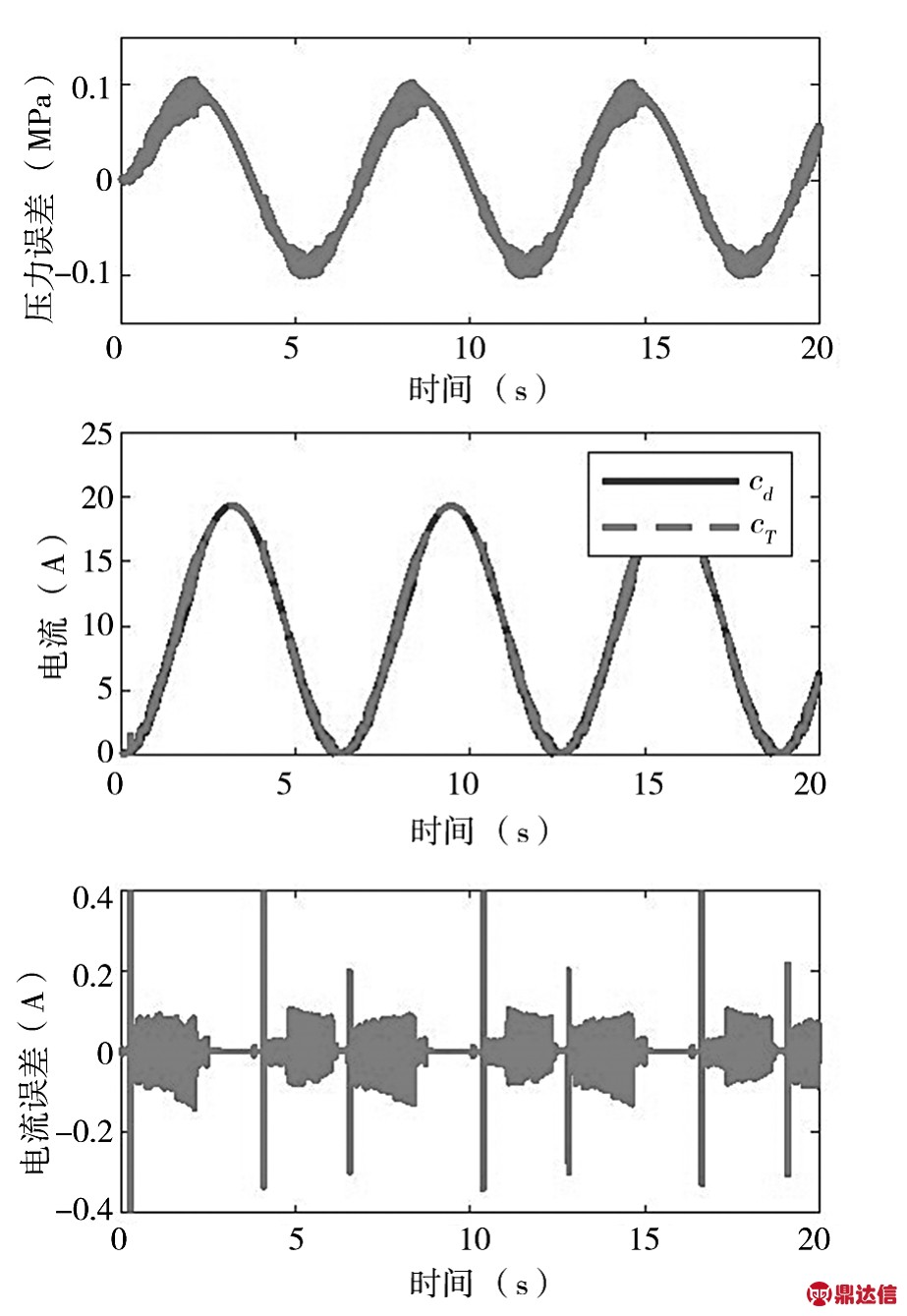
图4 仿真结结果
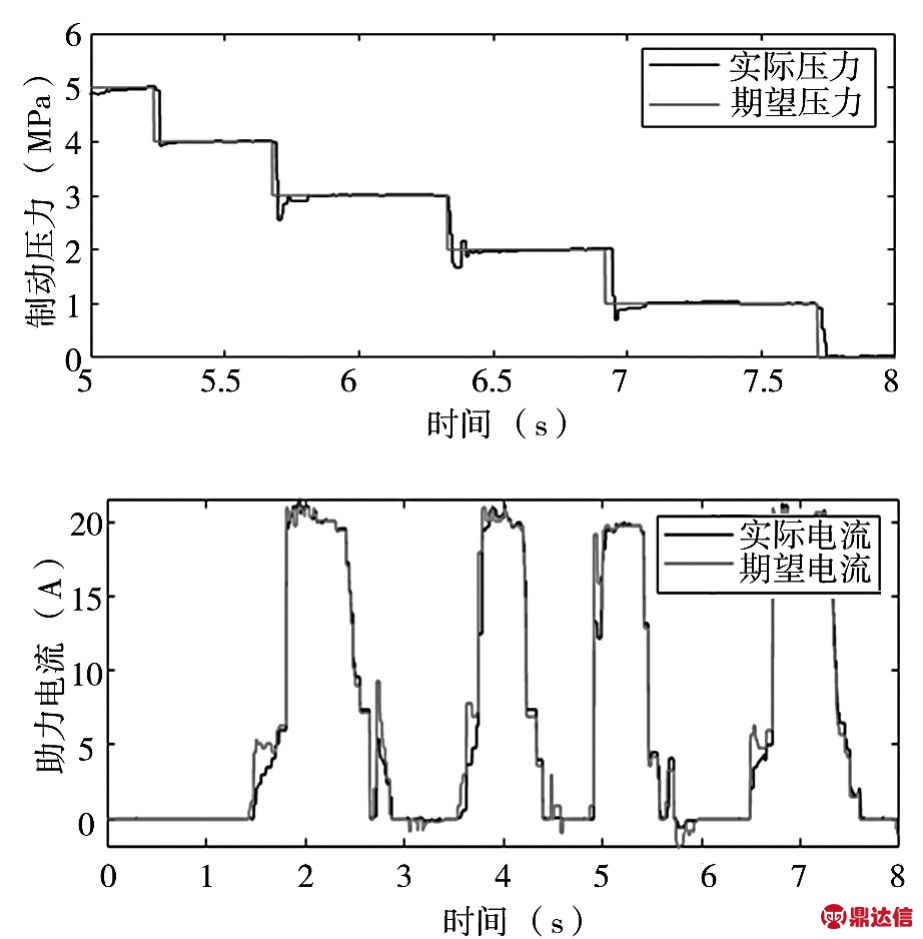
图5 实验数据
5 结语
设计基于真空助力器原理的电动助力器,其积分滑模的电流控制器可以实现精确的电流控制效果,并执行所设计的助力曲线,给驾驶员良好的踏板反馈。双闭环的制动压力控制方法能够实现期望的压力跟随效果,从而可以满足上层主动控制功能要求。最后,数值仿真和台架实验都表明设计的可靠性。