摘 要 改善柔性卷绕镀膜设备放卷室和工艺真空室、收卷室和工艺真空室之间隔离阀设计,以增强隔离阀密封性能,在柔性卷绕镀膜设备放卷室和工艺真空室、收卷室和工艺真空室之间各增加一个隔离阀,在生产完一卷膜材后只需对放卷室和收卷室进行破真空处理,大大缩减了工艺真空室的抽气时间,提高生产产能。
关键词 柔性 镀膜 真空 隔离
0 引言
电子产品都在向轻量化、超薄厚度、大尺寸方向发展,市场上对于柔性导电ITO膜的需求也在逐步增加,如何提高产能是目前所需迫切解决的问题。
目前柔性透明导电薄膜沉积技术已经在触摸屏行业广泛推广,柔性透明导电膜通过卷绕镀膜设备镀制,柔性透明导电薄膜基材都是PET(Polyethylene terephthalate,聚对苯二甲酸乙二醇酯)等柔性材料。为攻克柔性卷绕镀膜中生产完一卷膜后全部破真空产能低的难题,在柔性卷绕镀膜设备放卷室和工艺真空室、收卷室和工艺真空室之间各增加一个隔离阀,这样在生产完一卷膜材后只需对放卷室和收卷室进行破真空处理,大大缩减了工艺真空室的抽气时间,提高生产产能。
1 柔性ITO导电镀膜生产流程
柔性ITO导电镀膜生产流程见图1。
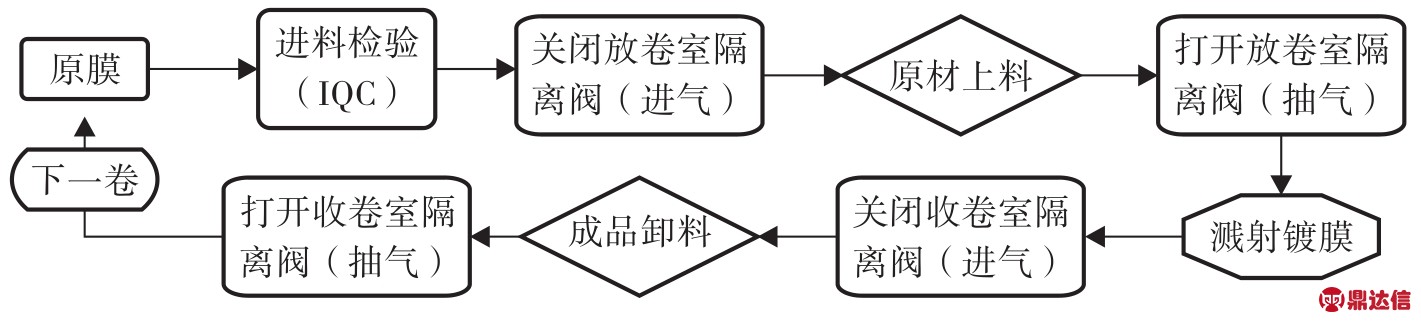
图1 卷绕镀膜生产流程图
真空溅射镀膜工艺:
用高能粒子轰击固体表面时能使固体表面的粒子获得能量并逸出表面,沉积在基片上。溅射现象于1870年开始用于镀膜技术,由于提高了沉积速率,1930年以后逐渐用于工业生产。
通常将欲沉积的材料制成板材──靶,固定在阴极上。基片置于正对靶面的阳极上,距靶几厘米。系统真空抽至高真空(≤10-6hPa)后充入10- 3hPa的气体(通常为氩气),在阴极和阳极间加几千伏电压,两极间即产生辉光放电。放电产生的正离子在电场作用下飞向阴极,与靶表面原子碰撞,受碰撞从靶面逸出的靶原子称为溅射原子,其能量在1至几十电子伏范围。溅射原子在基片表面沉积成膜,溅射化合物膜可用反应溅射法,即将反应气体 (O2、N2、H2等气体)加入Ar气中,反应气体及其离子与靶原子或溅射原子发生反应生成化合物(如氧化物、氮化物等)而沉积在基片上。沉积绝缘膜可采用高频溅射法。基片装在接地的电极上,绝缘靶装在对面的电极上。高频电源一端接地,一端通过匹配网络和隔直流电容接到装有绝缘靶的电极上。接通高频电源后,高频电压不断改变极性。等离子体中的电子和正离子在电压的正半周和负半周分别打到绝缘靶上。由于电子迁移率高于正离子,绝缘靶表面带负电,在达到动态平衡时,靶处于负的偏置电位,从而使正离子对靶的溅射持续进行。采用磁控溅射可使沉积速率比非磁控溅射提高近一个数量级。
溅射的先决条件就是真空,溅射镀膜的基础是辉光放电:低压气体中显示辉光的气体放电(空气中的电子大概在1 000对/cm,由于高压放电现象在低气压状态下会产生辉光现象)现象,即稀薄气体中的自持放电(自激导电)现象。指的是不依赖外界电离条件,仅由外施电压作用即可维持的一种气体放电。
本司工艺是待设备本底真空度达到2.3×10-6 hPa时,充入工艺气体至工艺真空,打开阴极和传动辊开始镀膜;PET基材经过等离子设备预处理后,工艺室的阴极依次镀制SiOx、 Nb2O5、SiO2、ITO膜系。
2 溅射镀膜真空隔离技术
(1)上料
首先需关闭放卷室隔离阀对放卷室进气,待放卷室达到1.0×103 hPa时方可打开放卷室门并安装卷材,卷材安装完毕后,真空泵会对放卷室抽真空,当放卷室真空度达到一定数值时(放卷室与溅射镀膜室真空度相当),放卷室隔离阀打开;此时放卷室、溅射镀膜室同步抽真空。当本底真空≤2.3×10-6hPa时,方可通入溅射气、工艺气体进行生产制作。
(2)卸料
一卷膜溅射镀膜完毕后,关闭收卷室隔离阀对收卷室进气,待放卷室达到1.0×103hPa时方可打开收卷室门,并卸料。卸料完毕后真空泵会对收卷室抽真空,当收卷室真空度达到一定数值时(收卷室与溅射镀膜室真空度相当),收卷室隔离阀打开。
收放卷室抽气、进气过程中,腔体真空隔离异常重要。以放卷室为例:如若放卷室隔离技术水平较低,进气时由于隔离阀两侧存在较大的压差,空气会进入中间溅射镀膜室,影响溅射室真空,当重新抽真空时真空度起点高,抽空时间长。
(3)真空隔离阀
作为真空隔离阀,首先它应该具有密封的性能,还要考虑其大气和真空的压差以及膜材较薄和弯曲的特性问题,因此采用高强度硅胶管进行相邻真空室的膨胀密封。考虑到硅胶管的膨胀变形性,在排气采取抽气泵抽离的方式并加工固定形状的支撑管对其进行限制行程范围。
真空隔离阀由硅胶管、固定管、抽气泵电磁阀等组成。该装置装在卷绕镀膜设备放卷室与工艺真空室、收卷室与工艺真空室之间。工作时是在需要进行真空密封时通过压缩气的充入使硅胶管膨胀,从而达到密封的效果,不需要密封时通过抽气泵抽气把硅胶管内的压缩气抽离,从而达到打开的状态。硅胶管采用整注的方式进行加工,表面光洁度可以保证,其次就是硅胶可以很规律的进行填充。如图2所示。
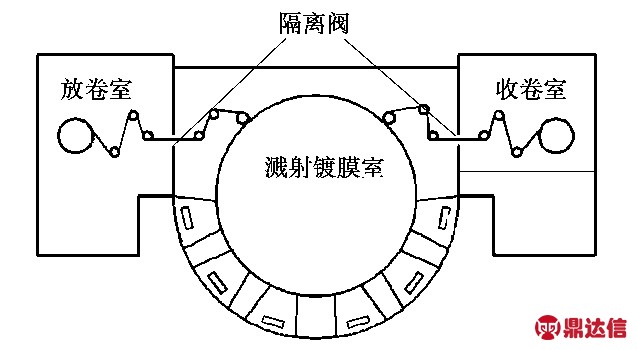
图2 镀膜设备结构示意图
2.1 溅射镀膜生产设备设计
此工艺采用真空卷绕磁控溅射技术,具有以下特点:
① 溅射所获得的薄膜与基片结合较好;
② 溅射所获得的薄膜纯度高、致密性好、成膜均匀性好;
③ 能够精确控制镀层的厚度,同时可通过改变参数条件控制组成薄膜的颗粒大小。
2.2 真空度对溅射产品质量的影响
真空卷绕磁控溅射技术最重要的条件是“真空”,真空度主要影响产品:附着力、透过率、方阻、b值、镀层硬度等产品硬性指标。
在真空镀膜中杂质气体分子的多少直接影响成膜质量,而卷绕镀膜是把整卷的膜放到真空室内。生产中放卷过程(需要把卷材拉开)会产生很多的杂质气体,因此真空是溅射镀膜的先决条件。
3 隔离阀应用效果比较分析
3.1 收、放卷室进气时真空度变化
隔离阀使用前后,收、放卷室进气时,溅射镀膜室的真空度变化见图3。
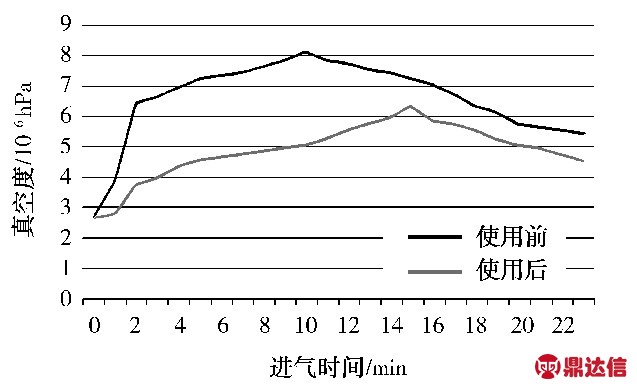
图3 收、放卷室进气时溅射镀膜室的真空度变化
从图3中可见,隔离阀使用前,收、放卷室开始进气时,真空波动较大从2.6×10-6 hPa升至8.2×10-6 hPa然后减低到5.3×10-6 hPa。曲线可见进气时,气流对中间镀膜室真空冲击较大,且最终真空度较差。隔离阀使用后,收、放卷室进气时,真空波动较小从2.6×10-6 hPa升至6.3×10-6 hPa然后减低到4.6×10-6 hPa。中间镀膜室真空也会出现波动,但是波动曲线平稳,最终真空度落点也相对较低。
3.2 收、放卷室换卷后抽气时真空变化
隔离阀使用前后,收、放卷室换卷后抽气时,溅射镀膜室的真空变化见图4。
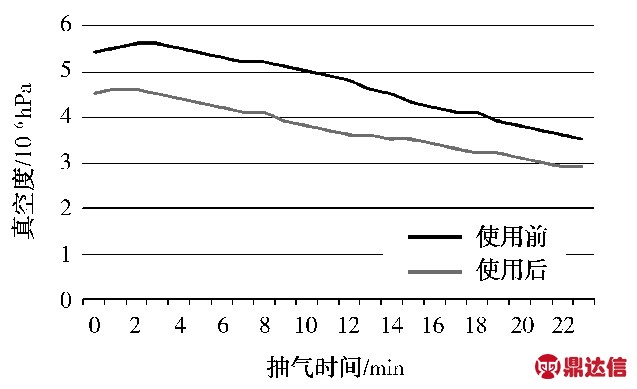
图4 收、放卷室抽气时溅射镀膜室的真空变化
从图4中可见,隔离阀使用前,收、放卷室开始抽气时,中间镀膜室真空起点高,抽气时长22 min左右,真空从5.3×10-6 hPa逐步减低到3.6×10-6 hPa,达到镀膜工艺真空点时间较久。隔离阀使用后,收、放卷室抽气时,中间镀膜室真空起点低,抽气时长22min左右真空从4.6×10-6 hPa逐步减低到2.8×10-6 hPa,图中曲线对比,若溅射室真空达到镀膜工艺真空点2.3×10-6 hPa时,使用此隔离技术后每次抽气时间可缩短15 min左右,每卷膜需收放卷室各进气、抽气一次,测每生产一卷膜可节约30 min时间。按每卷膜900 m、身缠速度4 m/min计算,可提升产能约13.33%。
4 结语
ITO Film在国内市场具有较大的发展空间,其市场份额在不断扩大。对于国内的ITO Film生产商,将是一个良好的发展契机。但ITO Film的市场竞争压力也是非常之大,目前国内ITO Film生产项目比比皆是;而且来自国外厂家的竞争更为明显。国内生产ITO Film的厂家最为明显的劣势是产品质量以及设备产能。因此,要在ITO Film行业里提升自己的竞争力,就必须增加设备产能抢占市场份额,提高产品质量开发具有较强性价比的ITO Film产品,才能在未来的竞争市场中获胜。
卷绕镀膜设备采用此种装置可以提高产能,达到降低生产成本的目的,而且中间工艺真空室在做完一卷膜后不需要进行破真空处理,也保证了真空环境从而达到提高产品质量的目的。
真空隔离技术极其重要,它不仅实现了溅射镀膜室对外界杂质气体(空气中的水、氧气等)的隔离,还在一定程度上缩短了设备抽真空时间;既排除了杂质气体对产品溅镀时的干扰,也在一定程度上提升了产能。