摘要:以电磁阀、推力器为例,阐述环缝典型结构真空电子束焊接工艺,发现影响焊缝质量的主要因素是焊接过程中产生的气孔缺陷。分析焊接气孔产生主要原因为硅油使用不合理、内腔未处于真空状态、退刀槽位置不合理以及清根后留有空腔。通过采取合理的焊接工艺措施,可以很好地控制接头中的气孔缺陷,保证焊缝的力学性能,满足设计使用要求。
关键词:电子束焊;焊接结构;密闭空间;焊接气孔
0 前言
电子束焊接(Electron Beam Welding)除具有输入能量密度高、加热面积小、焊接速度快、焊缝热影响区窄、工件变形小等特点外,还具有电子束穿透深、焊缝深宽比大、电子束控制方便以及真空环境中焊缝不受污染等特点。电子束焊接适用于精密焊接、穿透及深度(大厚度工件)焊接、高效率焊接和特殊焊接等。涉及的材料有高熔点金属、高弹性合金、不锈钢、高强钢、有色金属及其合金和陶瓷等非金属材料;涉及的工件结构多种多样,以中小型精密零件为主。
本研究从电磁阀、推力器的焊接实例入手,讨论影响电子束焊接质量的几个工艺因素。焊接接头经CT探伤后发现,影响焊缝强度的主要因素为焊缝内部的气孔缺陷。因此,为了保证焊接接头的力学性能,分析焊缝内部气孔的成因及防止措施是本研究探讨的重点。
1 焊缝结构特点及技术难点分析
1.1 焊缝结构特点
焊接材料的化学成分如表1所示。焊缝结构均为锁底结构,结构件的焊接结构如图1所示。
电磁阀主要由不锈钢和软磁合金两种材料组成,推力器主要由铌合金和钛合金两种材料组成。由图1a可知,结构件本身存在封闭的内腔,图1b中焊缝A、B、C结构下面有退刀槽。但是焊缝B相比于焊缝A、C距离退刀槽较远,图1c有推力器焊接结构清根后造成的空腔。
表1 焊接材料的化学成分

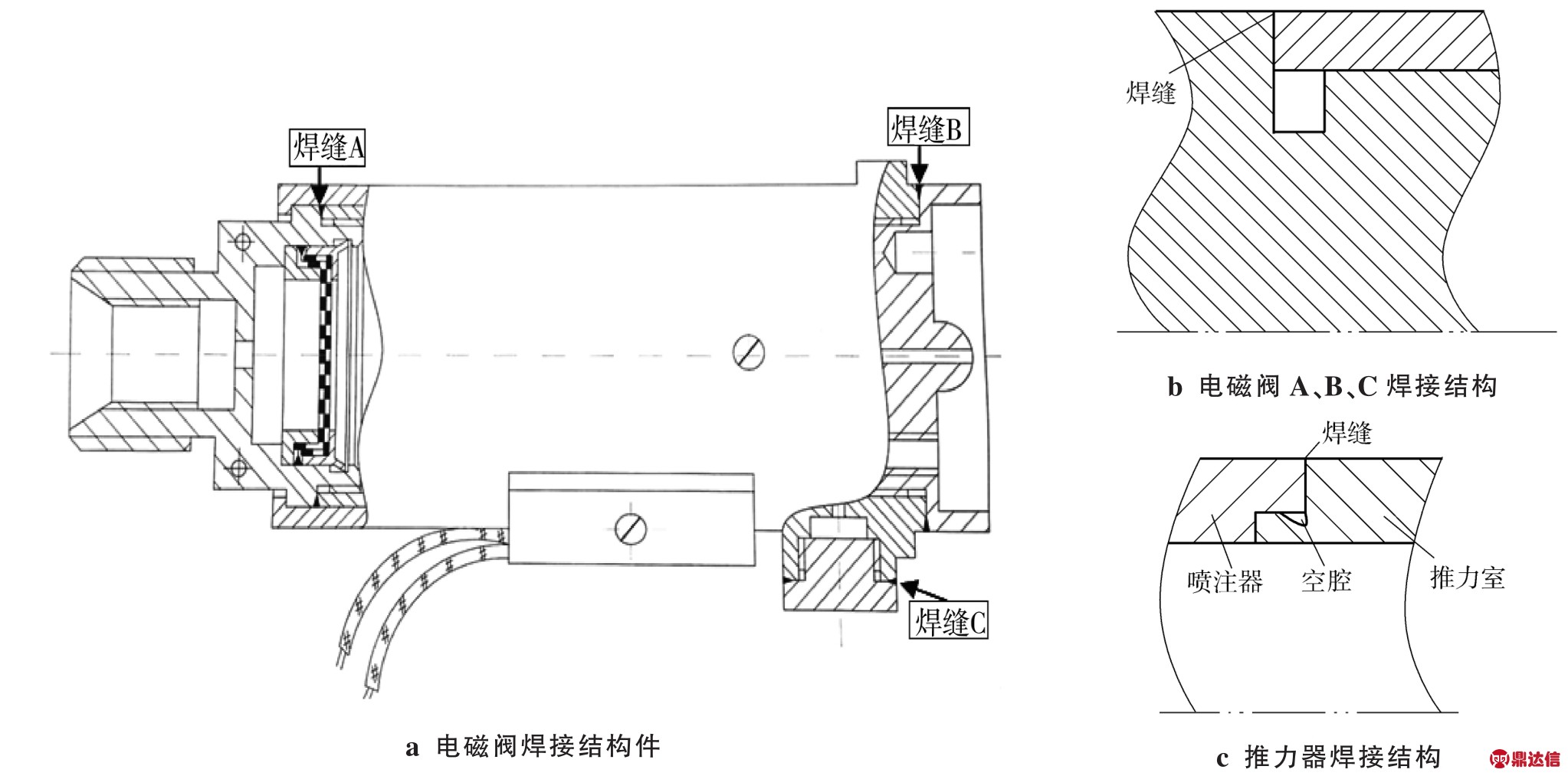
图1 结构件的焊接结构
1.2 技术难点
在焊接上述结构件过程中可观察到熔池熔滴飞溅、焊缝凹陷(见图2a),产品要求焊缝表面与基本金属接近齐平。同时,结构件焊接后,焊缝容易存在气孔(见图2b、2c)等缺陷,对于推力器产品的焊缝,必须经过补焊才能进一步提高产品合格率。重复焊接使焊缝的热输入增大,可以修饰焊缝表面和消除表层气孔。但是多次重熔容易造成焊接接头晶粒粗大、合金元素(特别是易挥发元素)的烧损,影响焊缝的强度和塑性,因此不能多次重复焊接。但是对于焊缝A、C,补焊无法消除焊接气孔(见图2d)。
因此,必须从结构件本身的结构特点以及焊缝接头结构出发,分析焊接缺陷产生原因,提高一次焊接合格率,避免补焊,提高生产效率。
2 解决措施
为了使电子束焊接方法成为焊接结构件的重要加工手段,应提高焊缝质量,杜绝焊接气孔的存在,减少有益元素的烧损,使焊缝金属得到合适的化学成分。因此,应加强焊接区金属的保护,使其不受到氧化、氮化等有害作用。
由于电子束焊接是在真空度高于0.1 Pa的真空室内进行,气体只可能来自焊接结构件。焊接区域存在大量有机物,有机物分解形成气体,同时由于焊接速度快、热输入量小,气体来不及从熔池逸出,造成焊接气孔,严重影响焊接接头的力学性能。从焊接结构可以看出,密闭空间中存在着大量空气,这可能是焊接气孔产生的主要原因之一。为防止焊缝气孔,可从以下4个方面着手:(1)合理使用润滑油,增加焊接区域的清洁度;(2)排除密闭内腔的气体,减少空气在焊接结构件中的含量;(3)改进焊接结构设计,使密闭空间远离焊缝,避免影响焊缝质量;(4)提高加工精度,避免清根留下空腔。
2.1 焊缝区域的清洁
真空电子束焊对零件焊接面的清洗要求较高。由于电子束焊接过程中将金属加热成金属蒸汽,同时焊缝表面的夹杂、油、锈、水等也被加热蒸发形成蒸汽,在焊接过程中这些蒸汽共同填满焊缝,造成气孔、夹渣等缺陷,影响焊接质量。因此应增加焊缝区域的清洁度,防止留有油、夹杂和水。
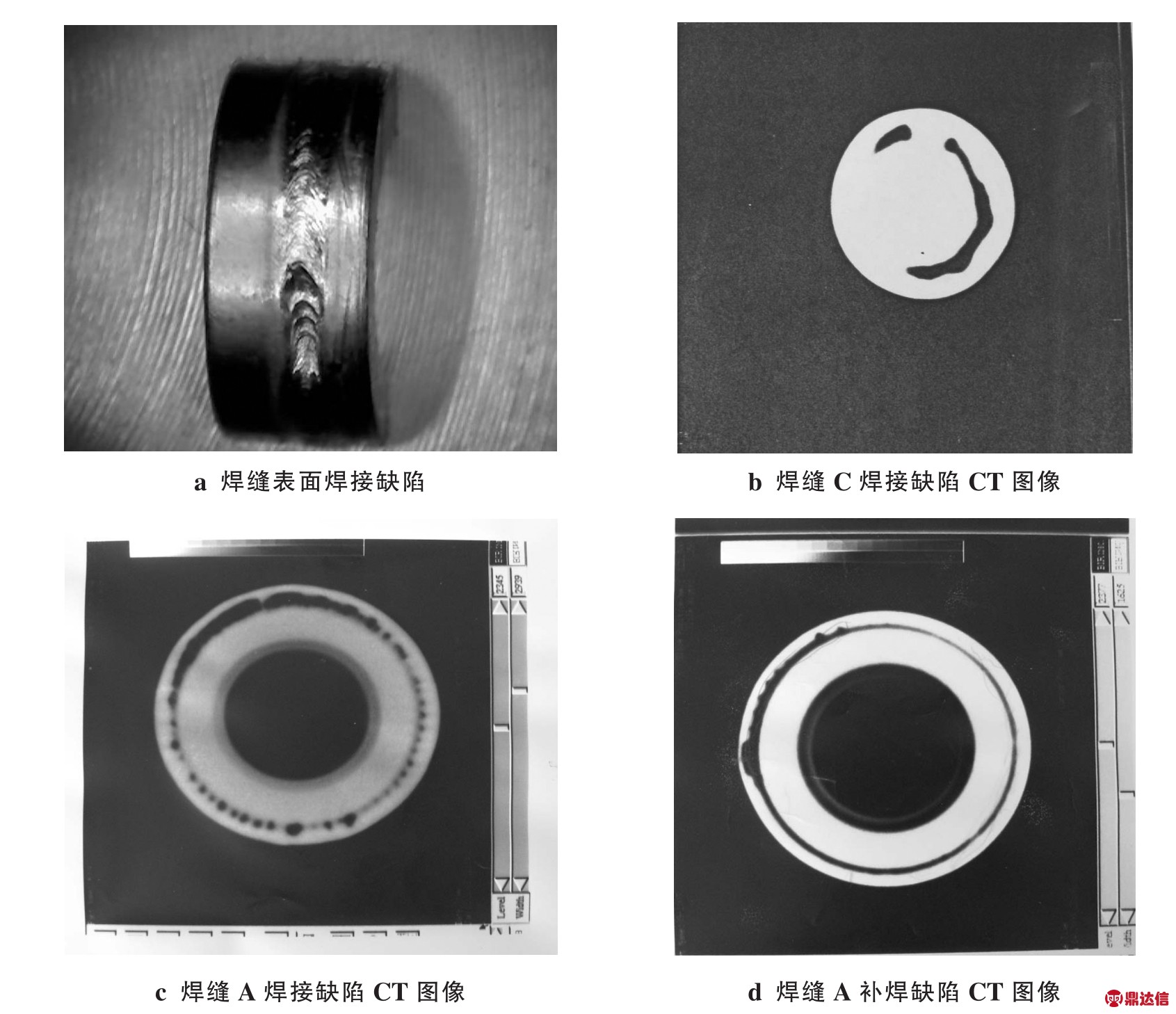
图2 焊缝焊接缺陷照片
在以前的产品装配过程中润滑油使用过多,导致其在焊缝区域的吸附较多,影响焊接质量。因此在满足加工条件下,合理减少润滑油的使用量,有利于提高产品焊缝区清洁度,从而减少焊接过程中润滑油受热分解产生气体进入焊接金属熔池,形成焊接气孔。对于真空电子束焊接设备,焊件表面的清理要求更加严格,否则不仅会导致焊缝缺陷和机械性能劣化,而且影响抽气时间与焊枪运行稳定性,同时加剧真空泵油的老化。
2.2 焊缝区精确加工
电子束焊接热源的热流沿厚度方向施加影响,产生较大的焊缝深宽比,是一种体积分布热源。熔池的温度分布很不均匀,前半部分因高温而进行金属熔化、气体吸收有利于吸热反应,熔池的后半部分由于温度下降而进行金属凝固、气体逸出,有利于放热反应。
焊缝连接处在材料加工过程中存在清根留下的空腔,造成连接处下部结合不紧密,留有配合间隙,存在大量气体,焊接过程中这些气体在温度场的影响下加热膨胀并形成气流吹向熔池,同时,液态金属溶解气体量随着温度的升高进一步增加。熔池的液态金属吸收周围的气体,并与周围空气发生激烈的相互作用使得焊缝金属中的氧、氮含量显著增加,当焊缝金属凝固时,超过溶解极限的气体就会析出。同时,有益元素因烧损和蒸发而减少,致使焊缝金属的塑性和韧性急剧下降,并造成熔滴飞溅,从而破坏焊接过程的稳定性。待焊工件的接缝区应精确加工,精确加工后的焊缝示意如图3a所示,连接处无缝连接,避免因存在气体形成焊接气孔。
2.3 机械机构设计的改进
从焊缝结构A、B可以看出,环形焊缝下面有环形退刀槽,退刀槽内含有大量空气,焊接连接处连接较为紧密,在工作室抽真空过程中不易抽到空腔内的气体,使真空度较低。空气(主要是N2、O2、H2O等)以及水蒸气(分解产物有H2、O2等)对焊缝质量的影响较大。
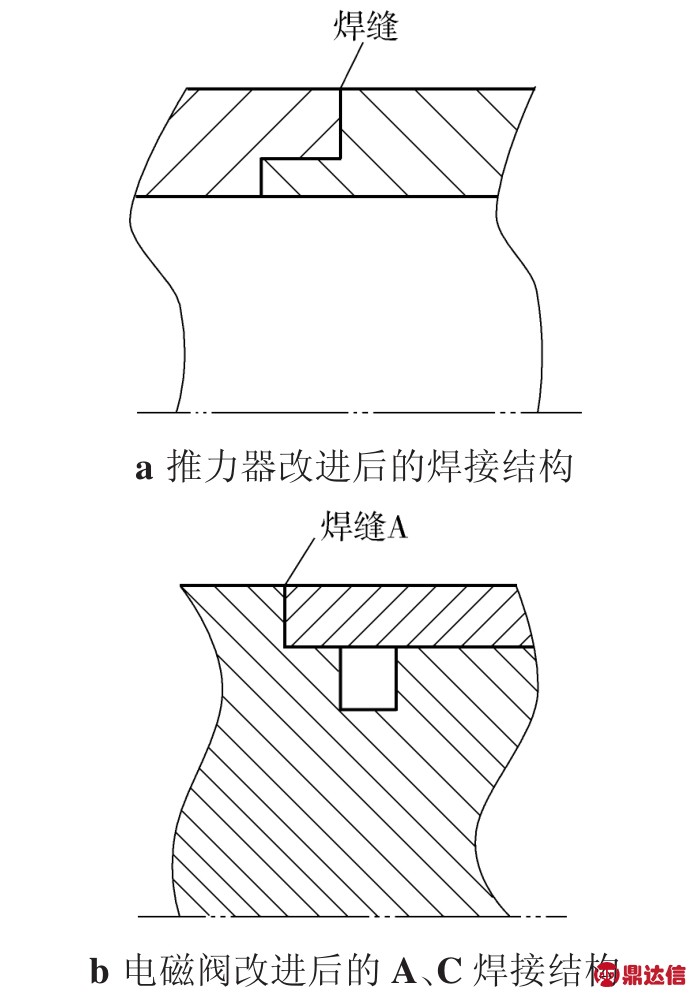
图3 改进后的焊接结构示意
从焊接材料成分可以看出,存在与氮发生作用的金属,如 Fe、Si、Cr、Ti等,它们既能溶于氮,又能与氮形成稳定的氮化物,氮在液态金属中的溶解度随着温度的升高而增大。
氧来源于水分、空气,焊接时能与焊接材料中的Al发生激烈的氧化反应,所形成的氧化物容易造成夹杂、未焊透等缺陷,Fe、Ni、Ti等金属可以有限地溶解氧。在焊接过程中,氧能烧损合金中的有益合金元素,导致焊接金属性能变坏。
焊接时,氢主要来源于焊接材料中的水分和有机物、周围空气中的水分,能够溶解于 Al、Fe、Ni、Cr等金属及其合金中,由于氢的作用可能产生气孔,导致焊接接头性能变坏。
液态金属在高温时可以溶解大量气体,而在凝固结晶时气体的溶解度突然下降,这时过饱和的气体以气泡形式逸出,如果焊缝金属的结晶速度大于气体的逸出速度,就会在焊缝中形成气泡。为消除气体对焊接金属的有害作用,必须改进机械结构设计,加强焊接区的保护,防止空气进入焊接区与液态金属发生作用。
相对于焊缝A,焊缝B结构距离焊接部位较远,影响较小,且因整体结构的需要未对其进行改进,改进后的A焊接结构如图3b所示。
焊后产生的主要焊接缺陷是气孔,是由于产品内密闭空间内存在的气体所致。若采用的焊接工艺参数和机械结构不当,焊缝中会出现大量较为集中的气孔缺陷。同时,焊缝金属易下塌,焊缝正面凹陷。为了达到环线焊缝最佳焊接效果,焊缝结构和配合间隙的设计至关重要,既要考虑结构件在整机中的作用,又必须满足被焊材料可焊性和具体焊接工艺的要求[5]。因此在实施焊接前,需通过工艺试验确定合理的结构和间隙尺寸,与工程设计人员共同讨论焊接件的焊缝结构。
2.4 内腔呈真空状态
电磁阀体为密闭空腔型结构,当阀体外部处于高真空状态时,内部仍然是低真空状态,内腔空气不易抽出,焊接时熔池会发生溅射现象。必须通过通电释放内部的大量气体,处于高真空状态,才能避免气体对焊缝质量的影响。
电子束焊接前首先将工作室内抽真空,真空度高于0.1 Pa,然后对电磁阀线圈进行通电使阀门打开,排除阀体内腔的气体,开阀门时间约为1 min,否则会对阀体内的高分子材料造成影响;接着焊接焊缝A、B,可以获得满意的结果,既能达到内腔呈真空状态的目的,又可以保证焊接时不发生焊缝溅射。
焊缝A、B焊接完成后进行CT探伤,发现焊缝A无气孔,合格率达到100%;而焊缝B由于连接区有退刀槽,虽然距离焊缝较远,但是仍然会有影响,其合格率约为90%。然后将焊缝A、B合格的结构件再按照上述步骤进行焊缝C的焊接,经检测焊缝C的合格率达到100%。由于焊缝A、B已经焊接完,内腔在第一次抽真空后,内腔空气不易抽出,第二次抽真空,真空度明显降低,达到0.4 Pa。可见焊接焊缝C时,内腔低真空度对焊缝质量影响很大。
电磁阀电子束焊焊缝金相照片见图4,推力器焊缝金相照片见图5。可以看出,焊接接头成形良好,焊缝几何尺寸对称,其边缘熔合较好,表面较为平整,避免了飞溅等环境污染。改进后的措施主要解决了焊接气孔等问题,合格率几乎达到100%。
在实践中探索并综合分析减少焊接结构件内存在密闭空间对焊缝质量的影响因素。可以看出焊接时金属熔池对空气的敏感度相当大,因此应尽可能采用高的真空环境进行焊接,有效控制焊缝中气孔的产生。
3 结论
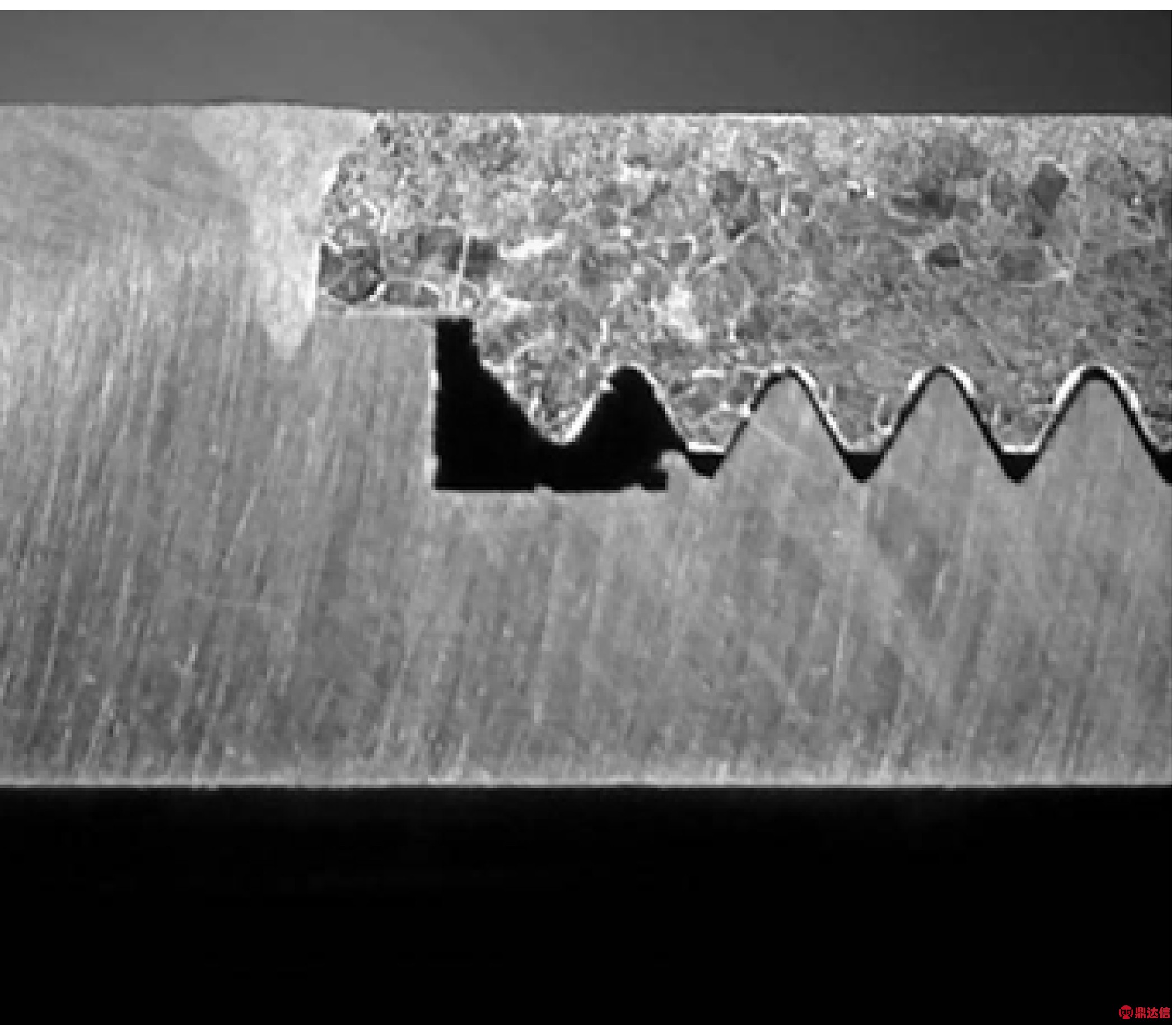
图4 焊缝A、C改进后焊缝金相照片
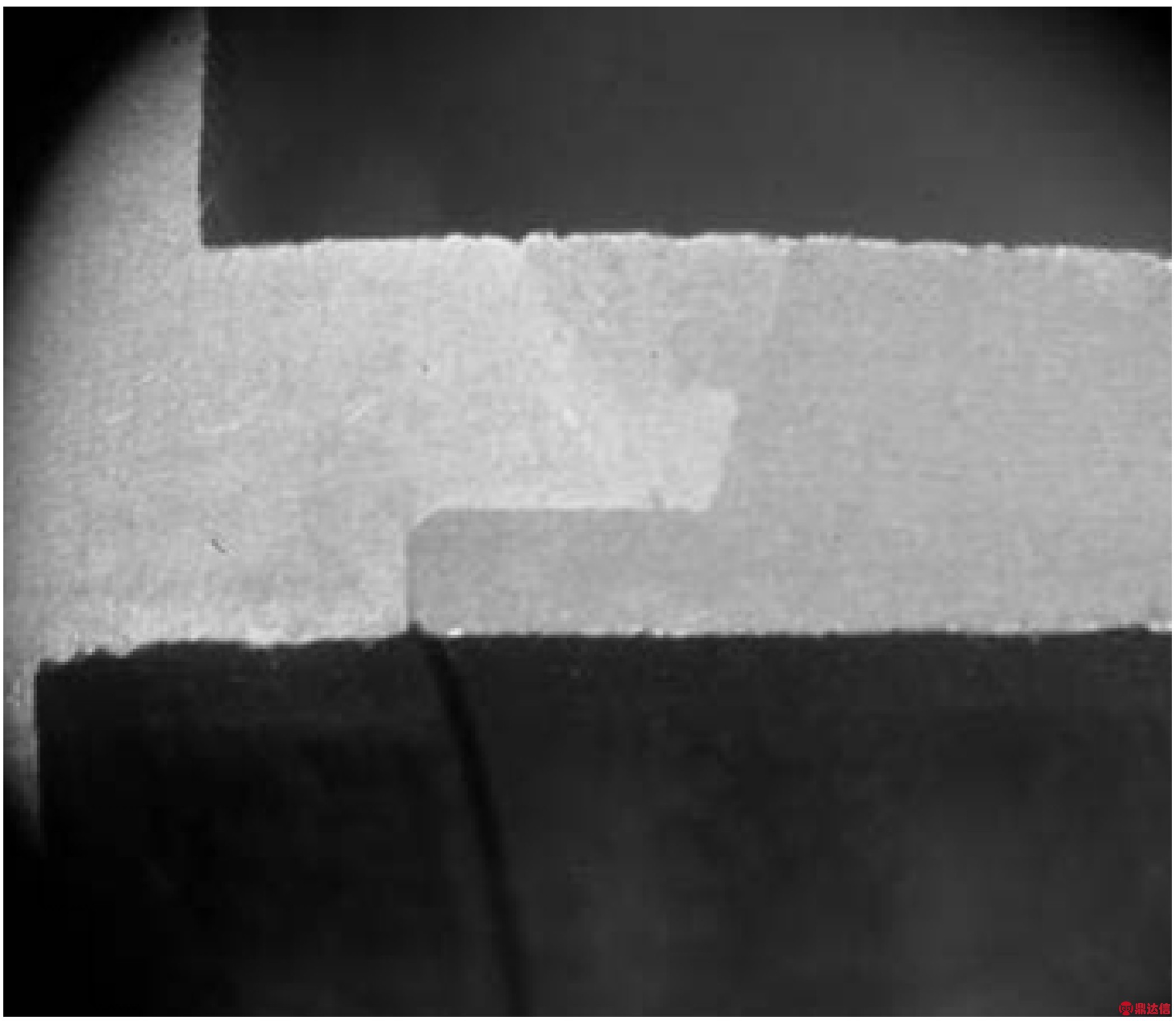
图5 推力器焊缝改进后金相照片
针对环缝结构真空电子束焊接在焊接过程中产生焊接气孔的情况,分析原因为硅油使用不合理、内腔未处于真空状态、退刀槽的位置不合理以及清根后留有空腔等。采用焊接前提高焊接结构件表面的清洁度、零件内的密闭内腔通电打开阀门抽真空、退刀槽的位置后移以及提高加工精度等措施,焊缝经过CT探伤完全符合技术要求,焊缝表面光滑美观,熔合良好,组织致密,无气孔。既提高了效率,又降低了成本,同时提高了焊接接头的力学性能。综上所述,抑制气孔缺陷的措施效果明显。