摘要:为研究飞轮储能系统(FESS)的性能,设计并制作了一套基于机械轴承的、采用无刷直流电机驱动的飞轮储能系统,对驱动电机及整套系统在转速小于10 000 r/min时的损耗分别进行了测量.分析了电损、风损和轴承损耗3种主要损耗,采用最小二乘法,对电损与转速的关系进行指数函数拟合,对风损、轴承损耗与转速的关系进行了多项式拟合,从而分离了3种损耗.对处于不同待机转速的飞轮储能系统的恒功率放电时间和经历了不同待机时间的能量利用系数进行了计算分析.结果表明:要提高FESS的效率必须采用磁悬浮轴承并将系统置于真空环境中;FESS恒功率放电时间与待机转速成1.8次方关系;待机转速和待机时间是能量利用系数的重要影响因素.研究结果为新能源发电系统对FESS的选择提供了理论依据.
关键词:飞轮储能系统;损耗;无刷直流电机;能量利用系数
风能、太阳能等新能源具有随机性和间隙性的特点,发出的电能有很大的波动,直接影响电力系统的可靠性和稳定性,故需要储能环节来提高电能质量.飞轮储能系统(flywheel energy storage sys-tem,FESS)以其能量密度高、效率高、充放电迅速、维护费用低等优点成为解决电能波动问题的理想选择[1].在电能充足时,驱动电机将带动飞轮加速,电能转化为动能储存;电能短缺时,飞轮带动发电机发电,向系统回馈能量.FESS的高效率是决定其产业化推广应用的重要前提之一,因此研究FESS的损耗构成及影响因素具有重要意义.
FESS的损耗主要分为电损、风损和轴承损耗,其中电损为电机损耗以及控制损耗,风损为飞轮转子与机壳内空气间的摩擦损耗,轴承损耗为飞轮的支撑轴承的摩擦损耗[2].戴兴建等[2-4]从理论上对飞轮转子外壁和端面与气体的摩擦损耗功率进行了推导和实验验证,计算了锥面螺旋槽轴承的摩擦损耗和储能飞轮电机铁损功率,提出了减小轴承摩擦损耗的方法,对12 000~36 000 r/min转速区间的充放电循环效率进行了测量,测得充放电循环效率为41%,电机及控制损耗占49%,风损和轴承损耗之和为10%.王凤翔等[5-6]基于3D流体场模型,对高速永磁电机的转子空气摩擦损耗与转速、表面粗糙度和轴向风速的关系进行了分析,从总损耗中将空气摩擦损耗分离出来,验证了流体场计算的正确性.文献[7]设计了一台无铁心双转子电机,对处于不同真空度条件下的损耗进行了测量,分离出电机的磁滞损耗、涡流损耗和风损.文献[8]研究了用于飞轮的无铁心杯形转子永磁同步电机,采用反电动势计算了空载损耗,运用Poynting定理计算了转子涡流损耗.文献[9]对2种用于飞轮的磁悬浮轴承的损耗进行了比较,给出了飞轮放电时间的计算方法.但以上针对FESS损耗的研究均未涉及待机转速、待机时间与能量利用率的关系.
无刷直流电机(brushless DC motor,BLDCM)具有运行效率高和调速性能好等优点,结构简单、能量密度比高[4],本文选用其作为驱动电机,对电机及FESS进行了能耗测试.采用最小二乘法,拟合出各损耗随转速变化的数值计算法,并对电损、风损和轴承损耗进行了分离.计算不同待机转速的飞轮储能系统在恒功率模式时的放电时间及经历不同待机时间的能量利用系数,为新能源发电系统对FESS的选择提供了理论依据.
1 FESS结构及等效模型
FESS主要由大转动惯量的飞轮本体、电动/发电机、双向逆变器、轴承、真空罩等组成.其基本工作原理是:系统内能量充足时,电机电动运行,驱动飞轮加速,电能转化为机械能储存;而当能量短缺时,飞轮驱动电机发电,经逆变器转换后向电网或独立负载输出电能,同时减速,此时机械能转换为电能释放.
为了产生更大的转动惯量,本实验设计的飞轮为带轮毂的轮缘状飞轮,整个系统结构如图1所示.飞轮的半径为125 mm,厚度为40 mm,转动惯量为0.119 kg·m2.考虑到成本,该系统采用机械轴承,并在自然气压中运行.图中,ω为FESS的角速度.
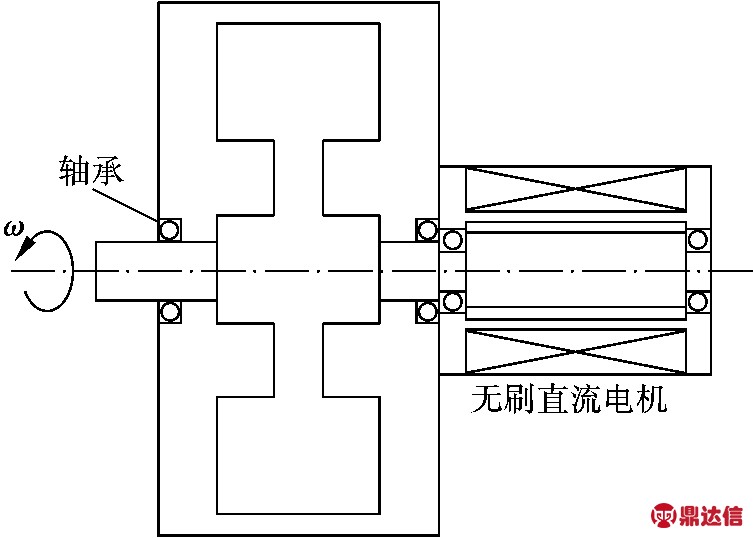
图1 FESS结构示意图
FESS的工作过程大致分为充电、待机、放电3种模式.为了保证安全性,FESS的运行区间限制在最大转速ωmax和最小转速 ωmin之间,若充电达到ωmax,则以此速度待机,一般取 ωmin=1/2ωmax.FESS可释放的最大能量为

BLDCM及其驱动电路的等效模型如图2所示.图中,ux,ix和ex分别为相电压、相电流和相反电动势,x=a,b,c;R为绕组相电阻;L-M 为等效相电感,L,M为每相的自感和互感;C为并联在直流母线上的电容;Vdc为直流母线电压;I为直流母线电流.
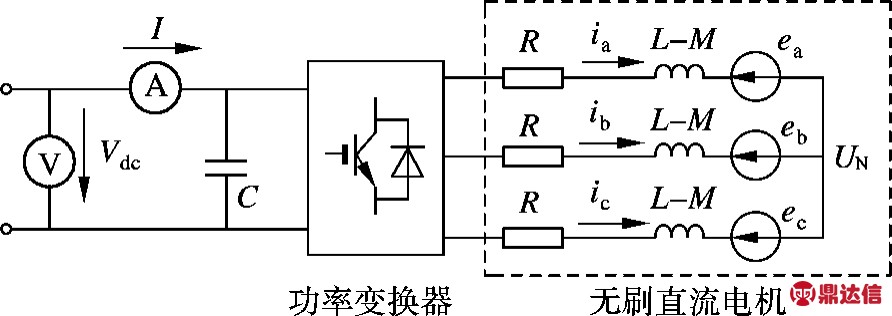
图2 BLDCM及驱动电路等效模型
该电机的运动方程为

式中,Te为电磁转矩,正为电动,负为发电;J为飞轮与电机转子的总转动惯量;Tf为与角速度ω有关的损耗转矩,始终为正.损耗能量pf(ω)=ωTf,损耗的存在造成了能量的损失.
2 FESS损耗实验及分析
2.1 FESS 损耗实验
为测量所设计FESS的损耗,搭建实验系统如图3所示.飞轮本体材料为铸铁,采用HRB深沟球滚动轴承.使用DSP芯片TMS320F2812为核心控制芯片,采用IRFP460 MOSFET开关管,对无刷直流电机进行两相导通六状态满占空比控制,开关频率为10 kHz.放置直流电压表、直流电流表于图2所示位置.调节直流电压,记录转速稳定后的电压、电流及转速.本实验中所设计飞轮及驱动的BLDCM参数如表1所示.
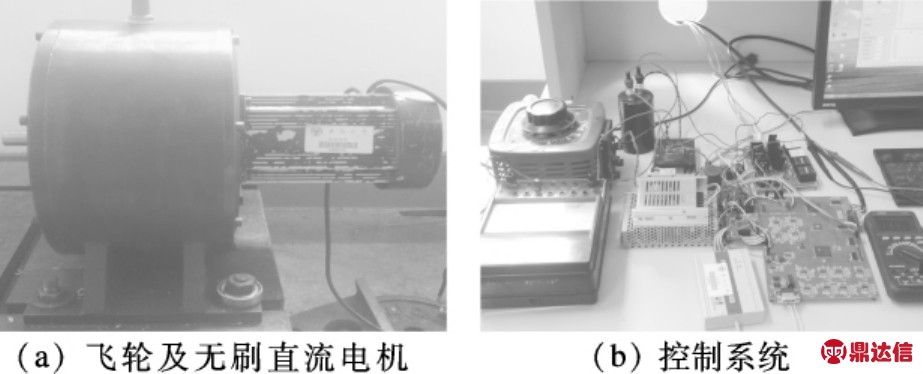
图3 FESS实验系统
表1 飞轮及BLDCM主要参数
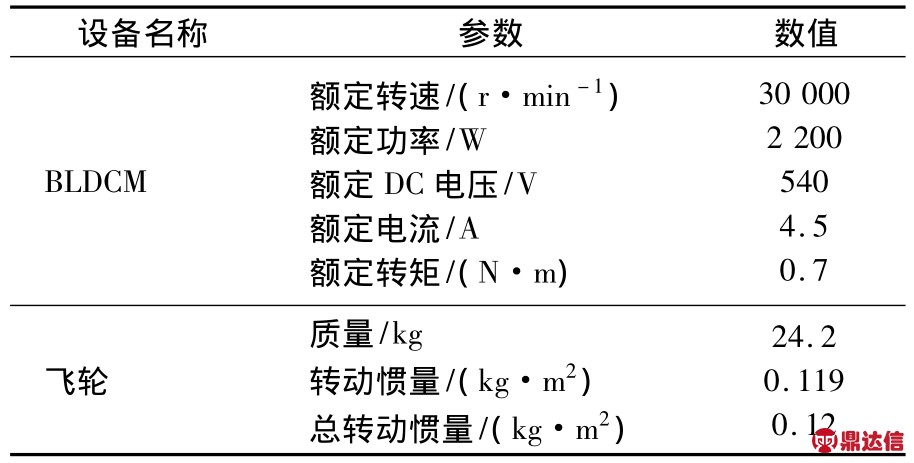
2.2 损耗分析
电损可分为铜耗、铁耗、机械损耗、杂散损耗和控制损耗等,总损耗与转速及气隙磁密有关.对于小型表贴式永磁电机,电枢反应对气隙磁密的影响不大[10],可视气隙磁密为定值,认为电机损耗只与转速有关.本文先对BLDCM单独进行了能耗测试,将电机损耗与角速度进行指数关系的拟合.电机损耗pm可表示为

文献[2]从理论上对飞轮转子外壁和端面与气体的摩擦损耗功率进行了推导,得到了飞轮风损对转速成平方关系的计算公式.文献[7]基于3D流体场模型对高速电机转子的空气摩擦损耗进行了分析,拟合结果显示风损与转速成1.927次方关系.因此本文采用平方关系对风损pair进行拟合,表示为

式中,a2为风损系数.
滚动轴承的摩擦损耗与载荷大小、载荷系数、转速、润滑剂用量等因素有关,总摩擦力矩M的一般计算方法为[11]

式中,μ0为与轴承结构和润滑方法有关的系数;n为轴承转速;υ为润滑剂的运动黏度;d为轴承的平均直径;μ1为载荷系数;P1为轴承载荷.故轴承摩擦损耗pb可表示为

式中,a1,a0为待定系数.
综上所述,FESS 的总损耗可视为 ω,ω1.558,ω1.667,ω2 各分量之和,建立拟合模型为

本文对所设计的FESS在0~10 000 r/min的损耗进行了测量,并采用最小二乘法对测量结果按式(7)进行了拟合,拟合结果为

在不同转速下FESS损耗的拟合值与实测值如图4所示.由图可见,按式(8)计算的FESS损耗的拟合值基本上与实测值吻合.
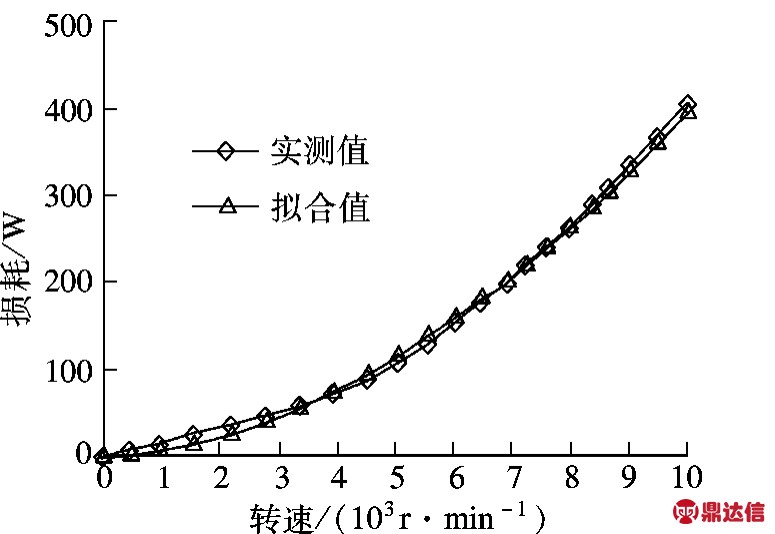
图4 FESS损耗实验值及拟合值
根据式(8)将FESS的电损、风损与轴承损耗三者从总损耗中分离,各损耗分量如图5所示.由图5可见,在转速为0~10 000 r/min的范围内,电损所占比例较小,始终维持在总损耗的15%左右.风能损耗随着转速的升高增加最快,在500 r/min时仅占总损耗的5%左右,在10 000 r/min时达总损耗的43%.轴承损耗一直是比例最大的损耗.故磁悬浮轴承系统与真空罩的使用是提高FESS效率的必要手段.
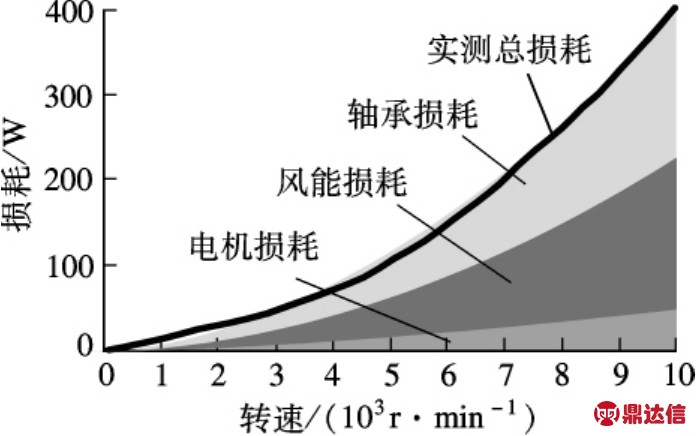
图5 FESS损耗分布
3 能量利用系数计算
由于FESS存在不可忽略的损耗,飞轮的动能在转化为电能的同时,也转化为电损、风损和轴承损耗.待机时间越长,损耗的能量越多;待机速度越大,损耗的功率越大.定义能量利用系数η,即放电过程中转化为电能的能量与待机和放电状态消耗的总能量之比

式中,Pg为放电功率,本文中为定值;Tg为飞轮从ωmax降至ωmin的时间;ps为待机状态的损耗功率;Ts为待机时间.
一般地,按照发电系统功率的1/4配置储能系统[12],本文拟对2 kW的风力发电系统进行平稳发电辅助储能,所分析FESS的额定放电功率为500 W.Tg的计算过程如下.
对式(2)进行变换,可得电机降速的微分方程为
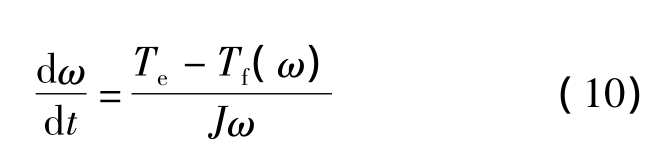
因Tf与ω的关系较复杂,无法按文献[9]中的分离变量法进行计算.本文采用分割近似求和的方法,将(ωmax-ωmin)分割为m个速度区间,每个区间内飞轮的速度变化率由区间两端点速度变化率取平均值近似得到,即Δti区间内的速度变化率近似为则飞轮速度从 ω 降到max ωmin所用的总时间为
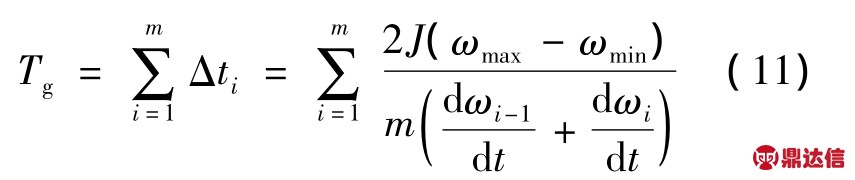
本文计算了所设计的FESS样机分别处于1 000~10 000 r/min的待机速度下以500 W恒功率放电至ωmin的时间,并对不同待机时间情况下各待机转速放电至ωmin的能量利用系数η进行了比较,结果如图6所示.
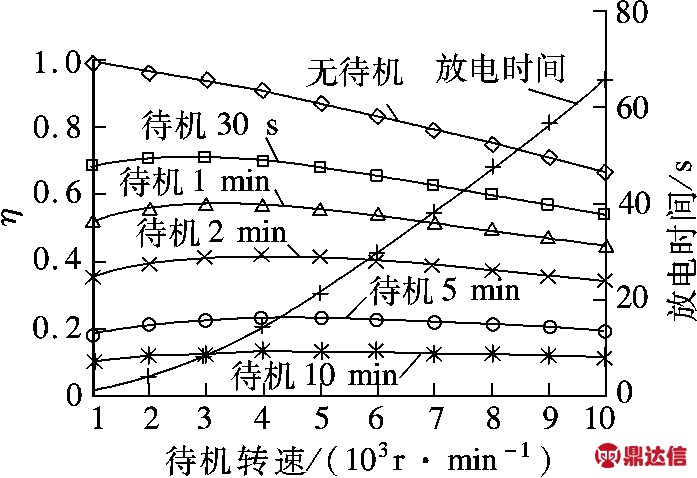
图6 不同待机速度下放电时间及能量利用系数关系曲线
由图6可见,由于不可忽略的损耗原因,FESS恒功率放电时,放电时间并没有达到与待机转速成平方关系的理论值,而是1.8次方关系.随着待机时间的增加,能量利用系数曲线逐渐下移.仅考虑放电过程(无待机),能量利用系数随着待机转速的增加而减小.有待机过程时,随着待机转速的增加,能量利用系数则先增加后再减小,并且获得能量利用系数最高点的转速随着待机时间的增加而增加.
4 结语
1)对FESS的损耗与转速的关系进行了测量与分析,通过数值拟合,给出损耗随转速变化的函数关系,并对电损、风损及轴承损耗进行了分离.分析结果表明,所设计的FESS的风损随转速增加迅速增加,当转速为10 000 r/min时,风损已与轴承损耗基本相等,在转速小于10 000 r/min时,风损与轴承损耗约占系统总损耗的85%,直接影响了储能效率.因此,要提高FESS的效率必须采用磁悬浮轴承,并将系统置于真空环境中.
2)对FESS以恒功率从ωmax放电至ωmin的时间及处于不同待机转速、经历不同待机时间的能量利用系数进行了对比.结果显示,恒功率放电时间与待机转速未达到理论上的平方关系,而是1.8次方关系.对某一待机时间,在转速为1 000~10 000 r/min范围内存在能量利用系数最高的待机转速.随着待机时间的增加,能量利用系数曲线逐渐下移,而获得能量利用系数最高点的待机转速逐渐增加.因此要根据新能源发电系统的实际状况配备相应容量和相应转速区间的FESS,以获得较高的能量利用率.