[摘 要]复合罩体零件由T2 铜罩和7A09 铝罩经过真空固相扩散焊连接成形。综合运用金相显微镜、显微维氏硬度计、扫描电子显微镜、X 射线能谱仪、X 射线衍射仪对焊缝微观组织结构进行研究。结果表明:焊缝由多种脆性相组成,焊缝与母材之间形成了明显的扩散层,焊缝及扩散层宽度约0.3 mm;两侧扩散层宽度及组织呈明显差异,铝侧扩散层宽度远大于铜侧扩散层,在铝侧扩散层生成了以网状特征为主的脆性相,并在焊接温度和应力的共同作用下晶粒发生了动态再结晶,扩散层与焊缝组织呈明显的过渡梯度,铜侧扩散层生成了致密带状脆性相,过渡梯度不明显。
[关键词]固相扩散焊;焊缝;微观组织;脆性相
0 引言
真空扩散焊是一种在一定温度、压力和时间条件下,使同种或异种金属、非金属材料接触面间的原子相互扩散,实现连接的工艺方法,该过程包含了复杂的物理化学变化。该方法是实现性能差异较大的异种材料大面积连接的有效方法,具有连接强度高、焊接变形小、接头质量稳定可靠等优点,广泛应用于航空航天、仪表及电子、化工、核工业等领域[1]。
复合罩零件由铜罩(T2 纯铜)与铝罩(7A09超硬铝合金)异种材料、异形曲面结构件组成,要求铝罩与铜罩接触界面无间隙、无滑移,铝罩与铜罩的连接有一定的连接强度,连接后能够进行机械加工。由于Al、Cu 材料物理性能差异较大,尤其是熔点和线膨胀系数差异较大,且Al、Cu 之间容易形成脆性化合物相等特点,采用常规的熔焊方法易产生低熔点共晶化合物,从而降低接头力学性能,诱发缺陷,另外,焊接热输入难以控制,焊接变形导致界面形位精度不能满足设计要求,采用真空扩散焊接是实现该零件的合适工艺方法。
目前,国内铝-铜异种材料扩散焊研究尤其是工程应用研究较少,且主要集中在纯铝、Al-Mg系列铝合金及纯铜材料上,对Al-Zn-Mg-Cu 系可热处理强化超硬铝合金与T2 铜扩散焊鲜有报道。本研究以现实需求为背景,综合运用多种测试分析手段对7A09/T2 真空扩散焊焊缝组织、结构、成分以及形成规律进行研究,掌握组织特征以及性能,在工程实践中具有一定的指导意义。
1 试验材料和方法
1.1 试验材料
试验采用牌号7A09 铝合金和T2 铜,尺寸均为直径50 mm 棒材,退火态(M),材料化学成分如表1。
表1 材料化学成分(质量分数/%)
Table 1 Results of chemical composition analysis (mass fraction/%)

经过多次试验筛选和优化,结合接头剪切试验结果,确定焊接温度485 ℃,焊接时间20 min,压力8 MPa。铝罩、铜罩分别经过机械加工后用丙酮擦洗去除油污,再分别用H2SO4溶液、HCl溶液清洗铜罩和铝罩表层氧化膜,将零件装入复合罩扩散焊模具进行扩散焊接,检测结果表明焊合率达95%以上,且扩散面有一定的连接强度,焊接的零件实物如图1 所示。
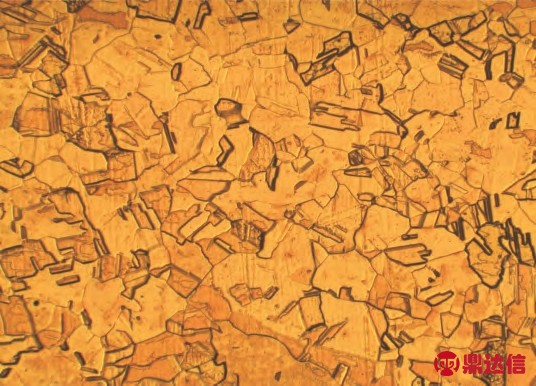
图1 真空扩散焊零件外形
Fig.1 Vacuum diffusion parts
1.2 试验方法
零件扩散焊接完成后,采用切割机将接头沿垂直于结合面的轴线方向在大、中、小端切取试样,经过磨制、抛光,再分别用低浓度混合酸溶液和FeCl3溶液浸蚀,运用金相显微镜对焊缝组织进行观察,显微维氏硬度计对脆性相硬度进行测定,扫描电子显微镜(SEM)及能谱仪(EDS)对焊缝形貌及成分进行分析,X 射线衍射仪(XRD)采用剥层的方式对焊缝结合面物相结构和组成进行分析。金相组织观察浸蚀剂为(HF +HNO3+HCl+H2O)溶液。
2 试验过程及结果
2.1 显微组织观察
接头整体宏观形貌见图2,Al、Cu 之间发生了扩散。焊缝从上至下明显分为3 个区域,依次为Cu 侧扩散层、焊缝中心、Al 侧扩散层。焊缝中心区域呈湖泊状特征,宽度约60 μm。近Cu 侧形成一条光亮带扩散层,扩散层较浅,深度约20 μm,铝合金一侧则形成网状特征的扩散层,扩散层深度远大于Cu 侧,深度约200 μm(图3)。
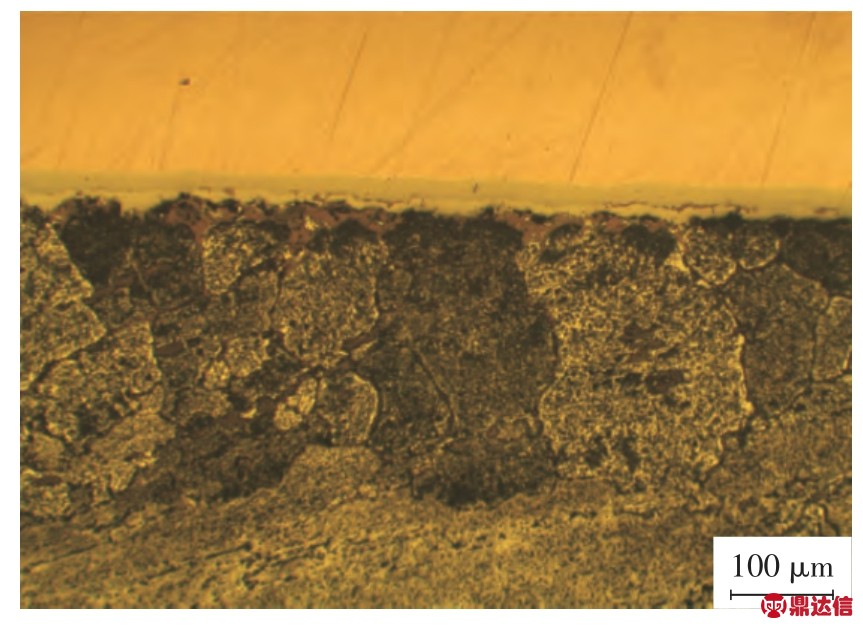
图2 接头宏观形貌
Fig.2 Macroscopic appearance of welded joint
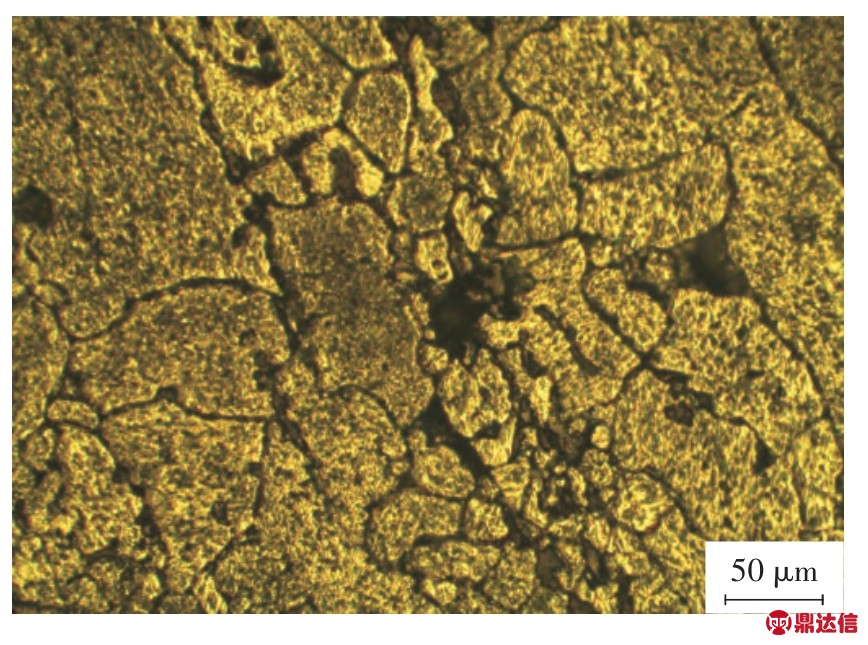
图3 Cu 侧扩散层特征
Fig.3 Characteristics of copper side diffusion layer
在Al 侧扩散层,Al 基发生了动态再结晶并形成了等轴粗晶组织,晶界明显有析出相。结合Al-Cu 相图分析,在515 ℃时,形成金属间化合物θ(CuAl2)相,θ 相具有金属间化合物普遍特性,熔点高、硬度高、脆性大,常以弥散强化方式作为合金系的强化相,θ 相的数量应控制在一定范围,若数量过多,未溶的相将积聚粗化,合金性能显著下降,如沿晶析出,合金性能进一步恶化[2],从分析来看,网状相应主要为θ 相。
在Cu 侧扩散层,形成了深度仅约20 μm 的致密光亮带,分析认为应为高温条件下7A09 合金中的Al、Zn 原子扩散至Cu 基体形成了单相固溶体或以化合物为基的固溶体。结合Cu-Al 合金相图可知,生成相有α、β 和γ2。其中α 相为Al在α(Cu)中形成单相过饱和固溶体,但仅限于Al元素含量低于9.4%。当Al 元素含量高于9.4%时,生成β 相,β 相是以电子化合物Cu3Al 为基的固溶体,高温下稳定,冷却过程中发生共析反应,共析产物为α 相和γ2相。γ2相是以电子化合物Cu32Al19(有的资料认为是Cu9Al4)为基的固溶体,Al 元素含量可在一定范围变化,该相具有复杂立方晶格,性能极硬而脆[3],运用显微维氏硬度计对该相进行硬度测试,测得硬度值为HV25540,高于铝铜基体硬度10 倍,硬度测试也进一步印证该光亮带为γ2相。
7A09 铝合金属于Al-Mg-Cu-Zn 系合金,主要强化相有η、T、S,显微组织见图4,强化相大量析出分布于基体,并有积聚粗化趋势,这主要由于较高的加热温度引起的。7A09 铝合金固溶处理温度通常为460~475 ℃,而焊接加热温度已超过固溶处理温度上限并达到了485 ℃,在此高温下,组织对温度极为敏感,即便保温时间短暂,组织也会明显粗化[4]。Cu 基显微组织见图5,为单相α 组织,可见大量的孪晶晶界。
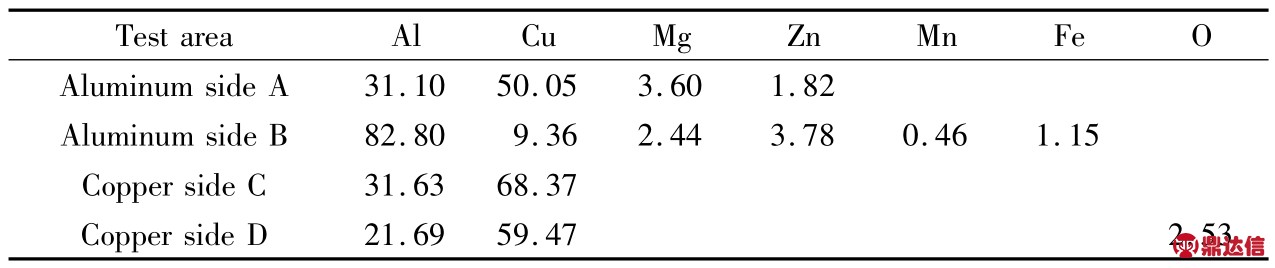
图4 7A09 母材显微组织
Fig.4 Microstructure of 7A09 Aluminum base metal
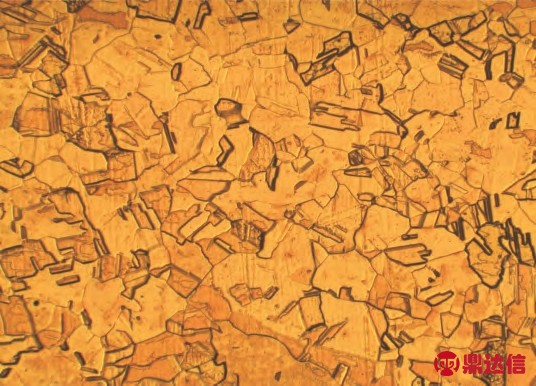
图5 T2 纯铜显微组织
Fig.5 Microstructure of T2 copper
以上观察发现,近Cu 侧扩散层较窄,测得宽度约20 μm,Al 侧扩散层则相对较宽,测得约200 μm,Cu 侧扩散层深度仅为Al 侧扩散层深度的1/10。其原因应与Cu、Al 原子扩散速度有关,有研究表明,Cu 原子在Al 中的扩散速度远大于Al原子在Cu 中的扩散速度[5]。此外,Al 的熔点远低于Cu 的熔点,因此在同样温度和压力下,Al 表面层中的晶体缺陷浓度比较高,这些因素促使首先在Al 侧形成过饱和固溶体,析出第一种新相的晶核,随着反应扩散过程的进行,新相的晶核沿着接触面和它的厚度方向长大[6]。
2.2 焊缝结合面电镜微观及能谱分析
将焊缝沿结合面在剪应力作用下人工打开,并在电镜下观察,形貌如图6 所示。可见,断面呈类似麻坑特征。采用EDS 能谱仪对断面特征区进行成分分析,结果见表2。在Al 侧断面,特征A区形成了Cu 的金属间化合物,特征B 区含一定量的Cu 以及Al 基体其他元素;在Cu 侧断面,特征C、D 区Al 含量较高,应形成了Al-Cu 金属间化合物。EDS 分析结果表明,Al、Cu 原子发生迁移,界面有扩散发生,从界面元素分布来看,大致沿焊缝与Cu 侧扩散层界面分离。
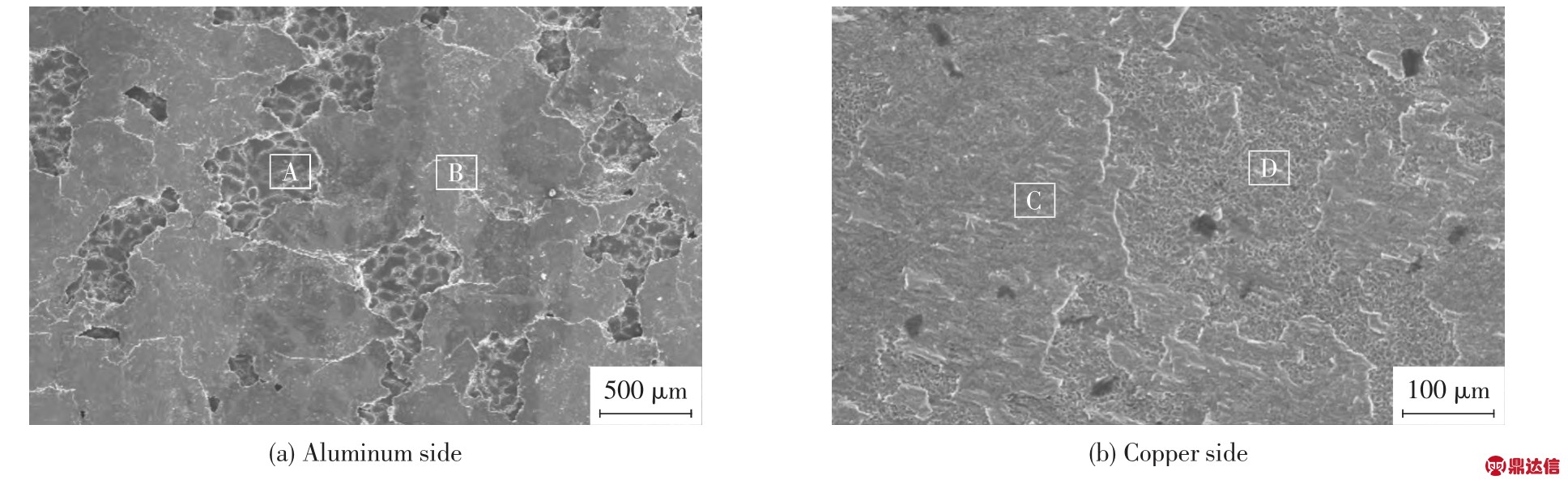
图6 断面微观形貌
Fig.6 SEM microstructure of combination zone
表2 结合面EDS 能谱分析结果(质量分数/%)
Table 2 Results of EDS analysis of combination zone (mass fraction/%)
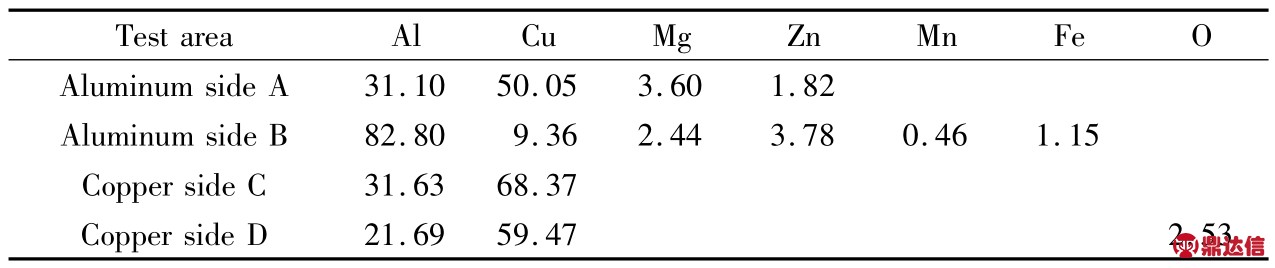
2.3 X 射线衍射剥层物相分析
将焊缝沿结合面人工打开,分别获得Al 侧、Cu 侧焊缝结合面,采用800#金相砂纸逐层磨制结合面,再分别进行XRD 物相分析,分析结果分别见表3、表4。
表3 7A09 铝侧剥层XRD 分析结果
Table 3 Results of XRD analysis of 7A09 peel sides

由表3 可知,在Al-3 层,铝基体α(Al)开始出现并成为主要相,该层应为焊缝中心向扩散层的过渡层,即Al-1、Al-2 层为焊缝中心,其主要组成相为γ2(Cu9Al4),其次是 θ (CuAl2)、η2(CuAl)和Cu6Al4,从Al-3 层向内,应为扩散层,主要相为γ2、θ、β 相,且越往内,含量越低。
表4 T2 铜侧剥层XRD 分析结果
Table 4 Results of XRD analysis of T2 peel sides
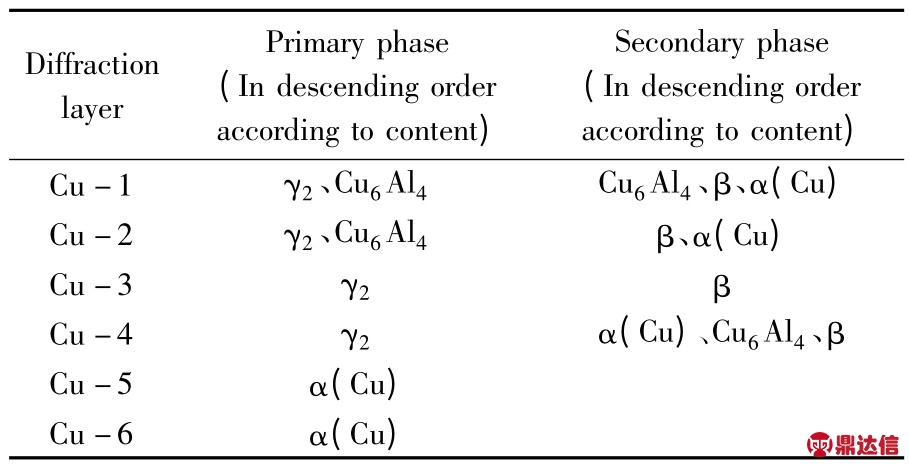
由表4 可知,焊缝中心与扩散层无明显的过渡层,结合金相观察分析的情况,从Cu-1 层开始就应为Cu 扩散层,扩散层主要组成相为γ2(Cu9Al4)、Cu6Al4,其次是β 相。
通过对断面X 衍射剥层物相分析可知,裂纹沿焊缝中心与Cu 侧扩散层界面扩展,在焊缝中心区形成了多种金属间化合物,在Al 侧扩散层,主要由α(Al)相和少量金属间化合物组成,而在Cu 侧扩散层,完全由金属间化合物组成,因此,裂纹沿焊缝中心与Cu 侧扩散层形核并扩展应与其由脆性相主导的界面有关[7]。
有研究表明,Al-Cu 扩散焊时金属间化合物的行为按4 个阶段递进:第一阶段为表面形成物理接触,即在温度、压力和真空度的作用下,使得Cu、Al 表面去除吸附层和氧化膜形成物理接触;第二阶段为接触表面的活化,即接触表面层发生蠕变变形,大量晶体缺陷出现,温度促使晶体缺陷密度进一步增加,并促使其接触表面加速移动,表面释放出能量,形成活化中心;第三阶段发生Cu、Al 原子的相互扩散,即在已形成金属键的地方,Cu 原子便向Al 中扩散,形成固溶体α(Al),与此同时,Al 原子向Cu 中扩散,形成α(Cu);第四阶段发展为反应扩散,出现新相[8],即从扩散进入第三阶段开始,由于焊缝中心为物理的直接接触面,元素扩散所需能量最小,因此,该区域反应最充分也最剧烈,故生成的金属间化合物种类最多。
3 结论
1)7A09 铝合金与T2 铜合金真空扩散焊焊缝依次由Al 侧扩散层、焊缝中心和Cu 侧扩散层组成,焊缝中心宽度约60 μm,近Cu 侧形成一条光亮带扩散层,扩散层较浅,深度约20 μm,铝合金一侧则形成网状特征的扩散层,扩散层深度远大于Cu 侧,深度约200 μm。
2)焊缝区域生成大量的金属间化合物。Al侧扩散层主要组成相有γ2(Cu9Al4)、θ(CuAl2)、β(Cu3Al),焊缝中心主要组成相有γ2(Cu9Al4)、θ(CuAl2)、η2(CuAl)和Cu6Al4,Cu 侧扩散层主要组成相有γ2(Cu9Al4)、Cu6Al4,β(Cu3Al)。
3)Al 侧扩散层与焊缝中心有明显的过渡层,而Cu 侧扩散层与焊缝中心无明显的过渡层。