摘要:为了研究真空腔弱面材料厚度对瓦斯抑爆性能的影响,设计了瓦斯爆炸实验 Ⅰ 型管道,开展了无真空腔瓦斯抑爆实验和弱面材料厚度为0.1、0.2、0.3 mm条件下的真空腔瓦斯抑爆实验。实验结果表明,真空腔能够有效抑爆,当弱面材料厚度为0.1 mm时,真空腔抑爆效果最好,最大火焰信号强度仅为0.14 V,并在F6测点及以后趋于熄灭状态,所有测点的最大超压值均在0.08 MPa以下,达到了抑爆目的。
关键词:真空腔抑爆;弱面材料;厚度;瓦斯爆炸;爆炸火焰;爆炸超压
煤矿瓦斯爆炸是我国煤矿井下常见的灾害之一,容易造成大量的人员伤亡和财产损失。瓦斯爆炸发生后,如何进行有效抑爆是国内外学者研究的重点[1-9]。真空腔抑爆技术是利用真空腔内负压特性,使弱面材料破裂,将瓦斯爆炸产生的冲击波和火焰吸入腔体,从而达到熄灭火焰、衰减冲击波的目的。弱面材料的厚度直接影响弱面材料的破裂时间及弱面材料对瓦斯的抑爆性能[10-11],因此,笔者设计了真空腔抑爆实验,研究弱面材料厚度对真空腔抑爆性能的影响,可为弱面材料的设计提供指导。
1 真空腔抑爆实验[12-13]
1.1 瓦斯爆炸实验系统
瓦斯爆炸实验系统主要由实验Ⅰ型管道、真空腔、点火系统、配气及抽真空系统、弱面、压力测量系统、火焰测量系统,以及动态信号采集分析系统等构成,如图1所示。
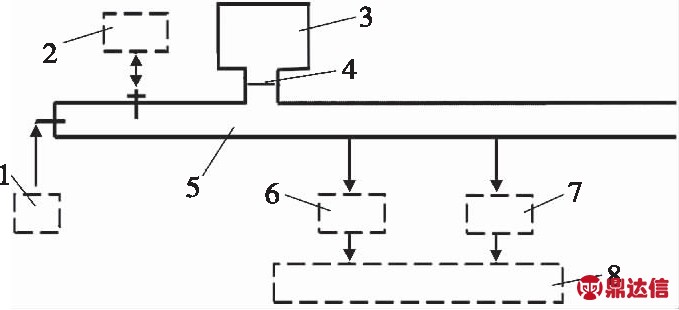
1—点火系统;2—配气及抽真空系统;3—真空腔;4—弱面材料;
5—实验Ⅰ型管道;6—压力测量系统;7—火焰测量系统;
8—TST6300动态信号采集分析系统。
图1 瓦斯爆炸实验系统示意图
实验Ⅰ型管道总长为11.5 m,由横截面积为 80 mm×80 mm的平直方管构成,管道呈Ⅰ型。由于本次实验研究开放状态下的瓦斯爆炸,所以管道点火端封闭,另一端完全开放。真空腔布置在距点火端3.25 m处。真空腔为圆柱形腔体,其直径为 300 mm、长度为50 mm。真空腔一端封闭,另一端通过接头与实验管道相连,接头与实验Ⅰ型管道之间放入装有弱面材料的法兰盘。为提高瓦斯爆炸强度及瓦斯爆炸速度,在距点火端1 m范围的实验管道内布置了障碍物。
在以往的真空腔抑爆实验中,弱面材料通常选取退火玻璃,但退火玻璃的稳定性较差,容易造成实验结果不准确,因此在本次实验中对弱面材料进行改进,选用聚四氟乙烯薄膜作为新型弱面材料。聚四氟乙烯薄膜具有耐高温、强度高、无污染等特点,曾作为原子弹、炮弹等的防熔密封垫圈,是真空腔抑爆实验理想的弱面材料。本次实验选用的聚四氟乙烯薄膜有3种规格,厚度分别为0.1、0.2、0.3 mm。在实验前,对3种不同厚度的聚四氟乙烯薄膜进行耐压强度测试,结果表明:0.1 mm薄膜的耐压强度为0.04~0.05 MPa;0.2 mm薄膜的耐压强度为0.08~0.09 MPa;0.3 mm薄膜的耐压强度为0.15~0.16 MPa。实验过程中,瓦斯爆炸后产生的冲击波正压会使弱面材料破裂,不同厚度的弱面材料耐压强度不同,导致破裂时间不同,对瓦斯抑爆的效果也不同。通过对比实验,研究弱面材料厚度对真空腔瓦斯抑爆性能的影响。
为了直观看到瓦斯爆炸效果,在实验Ⅰ型管道上布置了压力传感器和火焰传感器。压力传感器为CYG100型高频压力传感器,量程为0~1.5 MPa,精度小于0.4% FS,响应时间小于1 ms;火焰传感器为CGY100 型火焰传感器,采用光敏三极管作为感应元件,可以准确捕捉火焰信号,信号采集的时间间隔最短可达1 μs。压力传感器和火焰传感器在实验Ⅰ型管道上的布置如表1、表2及图2所示。
表1 CYG100型高频压力传感器布置位置

表2 CGY100型火焰传感器布置位置


图2 压力传感器和火焰传感器布置位置示意图
实验过程中采用2台TST6300动态信号采集系统对爆炸压力信号和火焰信号进行收集,并通过以太网与上位机通信,采集原始数据以便后期分析。
1.2 实验步骤
1)系统调试。先不连接真空腔及弱面材料。向实验 Ⅰ 型管道内充入正压气体对系统进行气密性检验。测试压力信号和火焰信号,调试、检查实验系统。
2)配气。在配气袋内配制甲烷体积分数为9.5%的瓦斯气体。
3)无真空腔瓦斯爆炸实验。在不安装真空腔的情况下,将实验Ⅰ型管道开口端用法兰盘封闭,用真空泵将实验Ⅰ型管道抽真空,充入配制好的9.5%瓦斯气体,实验前将开口端的法兰盘取下,进行点火爆炸实验[14]。
4)有真空腔瓦斯爆炸实验。将真空腔安装在实验Ⅰ型管道上,法兰盘内嵌有厚度为0.1 mm的聚四氟乙烯薄膜,用真空泵将实验Ⅰ型管道和真空腔抽真空,真空腔的真空度为-0.05 MPa。在实验Ⅰ型管道内充入配制好的9.5%瓦斯气体,实验前将开口端的法兰盘取下,进行点火爆炸实验。重复以上实验步骤,将厚度为0.2 mm和0.3 mm的聚四氟乙烯薄膜分别嵌入法兰盘内进行有真空腔瓦斯爆炸实验。
2 实验结果及分析
2.1 爆炸火焰分析
在无真空腔及真空腔的真空度为-0.05 MPa[15]时,不同弱面材料厚度条件下的各测点最大火焰信号强度如图3所示。
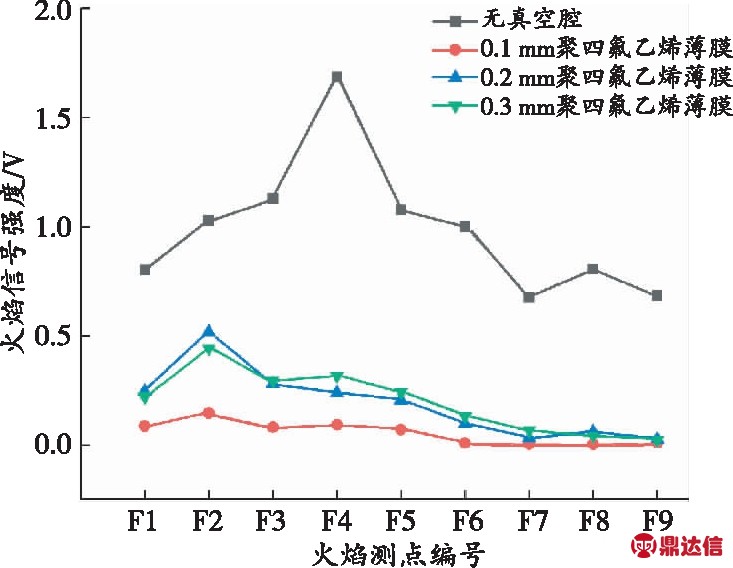
图3 无真空腔及在不同真空腔弱面材料厚度条件下的各测点最大火焰信号强度
由图3可知,无真空腔条件下,各测点的火焰信号强度均明显高于有真空腔条件下的火焰信号强度,表明真空腔对瓦斯抑爆效果显著,有效抑制了火焰。无真空腔时,各测点均出现了火焰信号,火焰信号强度为0.67~1.68 V;火焰信号强度从F1测点开始逐渐升高,在F3与F4测点之间急剧升高,在F4测点达到最大值1.68 V,随后急剧降低、缓慢降低,在F7测点达到最小值0.67 V,接着缓慢上升后又缓慢降低。有真空腔时,聚四氟乙烯薄膜厚度为0.1、0.2、0.3 mm时,火焰信号强度变化曲线趋势相似,总体趋势都是先升高,在F2测点达到最大值,随后逐渐降低,偶有小范围的升高,但总体趋势降低并最后趋于无火焰状态。其中,聚四氟乙烯薄膜厚度为0.2、0.3 mm时,各测点的火焰信号强度曲线偶有交叉,但整体上0.2 mm薄膜厚度的曲线位于0.3 mm薄膜厚度的曲线之下,表明0.2 mm薄膜厚度的灭火效果比0.3 mm薄膜厚度的灭火效果要好;薄膜厚度为0.1 mm时,各测点的火焰信号强度均明显低于薄膜厚度为0.2、0.3 mm时的火焰信号强度,在F2测点火焰信号强度最大值为0.14 V,远低于薄膜厚度为0.2 mm时的0.52 V和薄膜厚度为0.3 mm时的0.44 V,并在F6测点及以后趋于熄灭状态,灭火效果优于薄膜厚度为0.2 mm和0.3 mm时的灭火效果。
2.2 爆炸超压分析
在无真空腔及真空腔的真空度为-0.05 MPa时,不同弱面材料厚度条件下的各测点最大超压如图4所示。
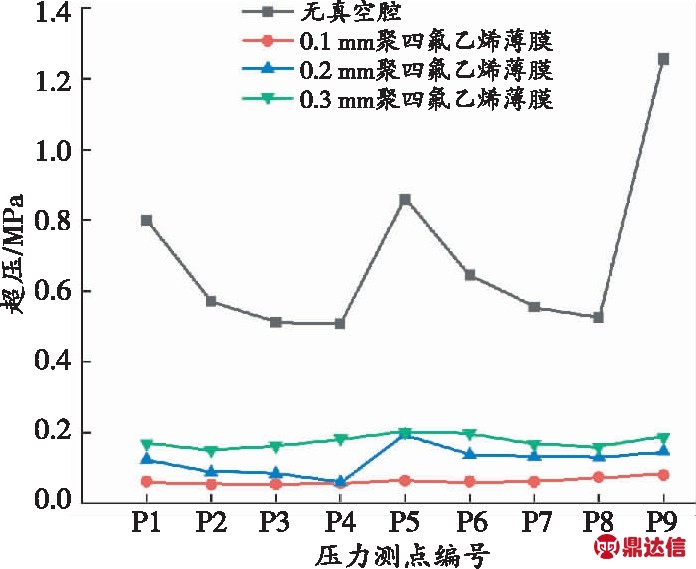
图4 无真空腔及在不同真空腔弱面材料厚度条件下的各测点最大超压
由图4可知,无真空腔条件下,各测点的最大超压值均高于有真空腔条件下的最大超压,说明真空腔能有效衰减管道内的瓦斯爆炸压力,抑爆效果显著,具有较好的泄压作用。无真空腔时,各测点的最大超压为0.51~1.26 MPa,超压最大值和最小值分别出现在P9测点和P4测点,最大超压值曲线大致呈“W”型分布。有真空腔时,薄膜厚度为0.2 mm条件下各测点的最大超压值曲线波动较大,最大超压值为0.06~0.20 MPa,最大超压值曲线在P1测点到P4测点缓慢下降,P4测点达到最小超压值0.06 MPa,然后急剧上升至P5测点达到最大超压值0.20 MPa,接着下降而后缓慢上升;薄膜厚度为0.1、0.3 mm时的最大超压曲线为扁平状“W”形曲线,各测点最大超压值波动较小,变化趋势类似,都是先缓慢下降,再缓慢上升,接着缓慢下降再缓慢上升。
由图4可以看出,整体抑爆效果优劣依次为有真空腔条件下0.1 mm厚度薄膜>0.2 mm厚度薄膜>0.3 mm厚度薄膜,无真空腔时抑爆效果最差。其中,薄膜厚度为0.1 mm时,真空腔抑爆效果最好,所有测点的最大超压值均在0.08 MPa以下,具有极好的泄压作用。
实验在真空度为-0.05 MPa条件下完成,综合分析爆炸火焰和爆炸超压,可以看出有真空腔时的抑爆效果优于无真空腔时的抑爆效果,有真空腔时薄膜厚度为0.1 mm的抑爆效果优于薄膜厚度为0.2 mm和0.3 mm的抑爆效果。由此表明在耐压强度允许的条件下,弱面材料越薄,瓦斯抑爆效果越好。而0.1 mm聚四氟乙烯薄膜耐压强度为0.04~0.05 MPa,能够承受真空度为-0.05 MPa的负压,比0.1 mm更薄的聚四氟乙烯薄膜在抽真空时容易破裂。
3 结论
1)利用瓦斯爆炸实验Ⅰ型管道,进行了有、无真空腔的瓦斯爆炸实验。有真空腔时,爆炸火焰强度和爆炸超压均比无真空腔时明显降低,真空腔能够有效衰减火焰和超压,可以达到抑爆的目的。
2)通过改变真空腔弱面材料的厚度,分别进行了薄膜厚度为0.1、0.2、0.3 mm的瓦斯抑爆实验。实验结果表明,薄膜厚度为0.1 mm时,真空腔的抑爆效果最好,最大火焰信号强度仅为0.14 V,并在F6测点及以后趋于熄灭状态,所有测点的最大超压值均在0.08 MPa以下,有极好的泄压作用。整体抑爆效果优劣依次为0.1 mm厚度薄膜>0.2 mm厚度薄膜>0.3 mm厚度薄膜。
3)通过不同薄膜厚度弱面材料的真空腔瓦斯抑爆实验,发现弱面材料越薄,抑爆效果越好,在能够承受真空腔内负压的条件下,应尽可能选取最薄的弱面材料来实现最优抑爆效果,后续需进行实验来进一步验证实验结论。