0 引言
随着美国工业互联网与德国工业4.0计划的提出,我国于2015年颁布了《中国制造2025》,将 中国制造2025 定位于国家战略高度,其核心是加快推进制造业创新发展、提质增效,实现从制造大国向制造强国转变。加快智能制造是实施中国制造2025的主攻方向,当前,在以中高速、优结构、新动力、多挑战为主要特征的产业新常态下,发展智能制造是重塑我国制造业竞争优势的新引擎,因此,智能制造被业界普遍认为代表了中国制造业的未来方向[1]。2017年7月国务院新发布的《新一代人工智能发展规划》中,对智能制造发展提出了具体的目标和任务,通过推进智能制造关键技术装备、核心支撑软件、工业互联网等系统集成应用,从而逐步建立智能制造标准体系,推进制造全生命周期活动的智能化。
桥门式起重机是工业生产中最基本的物料搬运设备,其应用领域涵盖工矿企业、港口码头和建筑工地等几乎所有生产活动,起重机市场需求与国民经济发展程度高度相关,发达地区市场规模大,发展中区域增速快,起重机可以说是人类工业文明发展中不可或缺的 伟人之臂”。
与制造业发达国家相比,我国起重机制造行业还存在很大差距,在专业协作化水平、装备自动化程度、流程监测与管理和信息集成等方面问题突出。目前,桥门式起重机行业增长乏力,只有积极应对智能制造发展的挑战和机遇,突破起重机智能制造的关键技术,及时完成产业结构升级,才能踏上制造强国之路。
1 起重机智能制造技术概述
1.1 起重机智能制造模式的内涵
所谓智能制造,是指 智能制造 是基于新一代信息技术,贯穿设计、生产、管理、服务等制造活动各个环节,融合了制造技术、自动化技术、系统工程与AI等学科,具有信息深度自感知、智慧优化自决策、精准控制自执行等功能的先进制造过程、系统与模式的总称,其核心是通过信息物理系统(CPS)实现人、设备与产品的实时连接、相互识别,从而构建一个高度自动化和柔性化的新型制造模式[2-4]。
结合智能制造概念的内涵,形成起重机智能制造模式的内涵及建设思路,首先应基于智能制造理念的基础上,结合起重机制造技术的特点,将制造过程中的工艺设计流程、生产信息和管理物流信息进行梳理和整合,然后建立智能制造系统,突破智能制造过程中关键技术,实现从设备、监控、车间到企业的自下而上的系统集成,逐步从数字化工艺和装备技术向高度自动化、柔性化的智能制造模式升级。
1.2 起重机智能制造的基本特征
基于前文对智能制造的研究成果,起重机制造企业又具有其发展现状和需求的特殊性,综合考虑,起重机智能制造主要具备以下几个基本特征:数字化、集成化、自动化、可视化、网络化等五个基本特征。可以概括为:是以数据驱动的,以知识为核心的,以数字化为基础的,信息全面集成、生产和决策自动化、管理在线动态可视化、网络高效协同的数字化、集成化、自动化、可视化、网络化的智能综合体。
起重机智能制造的基本特征具体指以下几个方面:数字化应全面而深入,在CAD、CAM、CAPP、CIMS等方面实现无纸化设计,此外,企业在智能制造过程中的模型库、工艺库等,以及运营、维护和管理所涉及的信息均实现经验的数字化;集成化应保证在各层之间进行数据的无障碍交互和共享,并能全局实现整体优化;自动化包括了基于物联网技术的数据采集自动化、基于智能装备和生产线的生产自动化、基于智能管理和决策系统的管理和决策自动化三方面要求;可视化应保证数据的采集和处理、智能的人机交互、生产状态的信息可实时以图表、视频形式呈现,为管理人员提供一个可交互的虚拟工厂场景;网络化应能够通过物联网实现对整个生产过程的实时动态管控。
1.3 起重机智能制造应用现状简介
现阶段的桥门式起重机设计制造技术不断发展,在设计手段、工艺制定、加工等方面已有了很大的提高,整体技术水平处于数字化阶段并日趋成熟完善,数字化技术主要体现在建模、结构仿真等设计环节,以及板材切割、钢结构焊接等制造环节。
1)精细等离子切割机和高精度激光切割机
桥门式起重机的板材切割主要采用的是精细等离子切割机和高精度激光切割机(见图1和图2)。等离子切割是利用高温、强电场条件下产生的等离子弧,经压缩作用,产生高温和高速气流,使工件切口处的金属局部熔化并被吹离基体而形成割缝,精细等离子电源输出电流最高可达300 A,切割厚度可达50 mm。激光切割主要利用经聚焦后的高功率密度激光束照射工件,材料熔化后经高速气流吹除熔融物质。激光切割的切割质量高且无热变形,表面粗糙度一般能控制在Ra12.5以下。精细等离子切割机和高精度激光切割机均采用通用型编程软件或专业型数控切割编程软件,按照数控切割工艺进行排料、切割工艺选择,转化成数控加工G代码指令完成下料工艺的自动化流程。
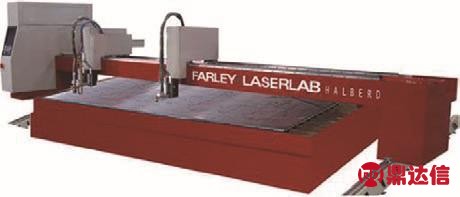
图1 精细等离子切割机
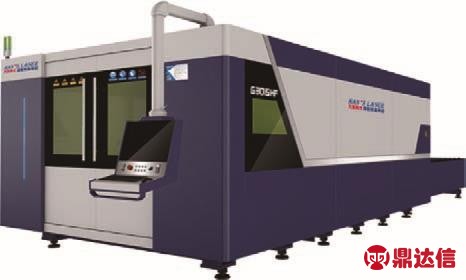
图2 超高速光纤激光切割机
2)主梁一体成型技术
桥门式起重机采用主梁的U型槽构件采用冷弯成形工艺[5],改变传统主梁制造采用冲压成形、多段拼接的工艺,使任意跨度的单梁起重机主梁U型槽可实现无焊缝加工(见图3)。U型槽冷弯成形生产线的基本配置主要有开卷机、矫平机、剪板机、钢板对中装置、成型主机、U型槽输送辊道等。主梁一体成型技术使起重机制造自动化水平得到了重要提升。
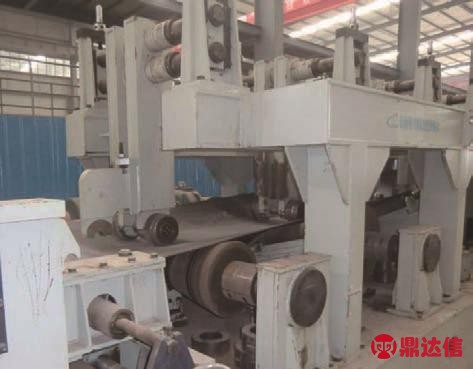
图3 主梁冷弯成型设备
3)焊接工作站
起重机的钢结构焊接可通过焊接工作站来实现(见图4)。焊接工作站包括焊接机器人系统、机器人控制装置、高压接触传感器、电弧传感器、龙门架、冷却水箱、变压器、机器人行走装置、外部轴变位机、功能软件包等组成,是生产线上一个相对独立的工作系统,主控系统和工作站之间通过信号、数据交换来完成生产线的协调工作,可实现修正偏差、自适应焊接工艺等,是具有较高柔性的生产系统。
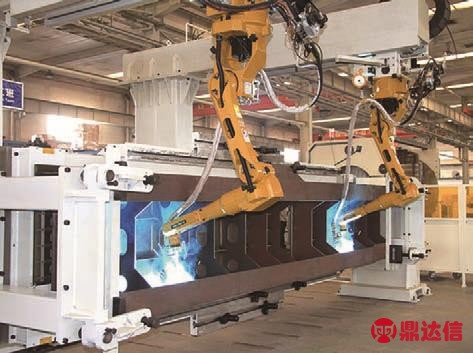
图4 焊接机器人在焊接起重机梁
4)专用工装及夹具
采用移动镗床与浮动镗孔工装配合的起重机整体加工工艺可以很好的保证设备精度,而且效率得到很大提高[6-7]。该工艺在完成起重机桥架焊接后,利用专用移动平台去精准移动镗床,利用安装在工件上的专用浮动镗孔装置完成对起重机台车长距离支撑孔的镗削(见图5)。该加工工艺使大吨位起重机装配后的精度有效提高,也使制作工期大大缩短。
2 起重机智能制造系统的顶层设计
桥门式起重机的智能制造系统是一项集中了数字化、网络化、信息化的多领域协同驱动过程。协同过程小至在企业内部各部门之间进行,大到企业与企业之间多领域的开展。本文结合起重机制造特点和技术发展现状,按照功能特点将起重机的智能制造系统划分为智能设计协同、智能加工与装配协同和组织协同三个阶段,这三个协同阶段各自具有典型特征,构成了起重机智能制造系统的基本框架[8]。
在起重机行业中,桥门式起重机是标准化产品,其加工集中在桥架制造和零部件制造两个方面,桥架制造包括板材切割、主端梁及支腿焊接等环节,零部件制造主要包括卷筒、车轮组、传动轴等数控机加工,桥架和零部件经装配后完成整机制造。
2.1 基于MBD模型的起重机智能设计协同
起重机模型的数据集成是产品设计协同的基础。产品几何形状的设计先后经历了二维图纸、二维数字化图纸、三维数字模型的产品数字化定义过程,这些信息也称之为几何信息。此外,起重机制造的工艺设计信息也需要数字化定义,这些信息属于非几何信息。起重机智能设计协同是指以协同的方式建立起重机数字化模型和数字化工艺设计信息的过程,通过利用MBD技术集成的三维实体模型的方式,详细规定起重机模型中产品尺寸、公差、制造技术要求等产品几何设计信息和非几何制造工艺信息的三维表达。
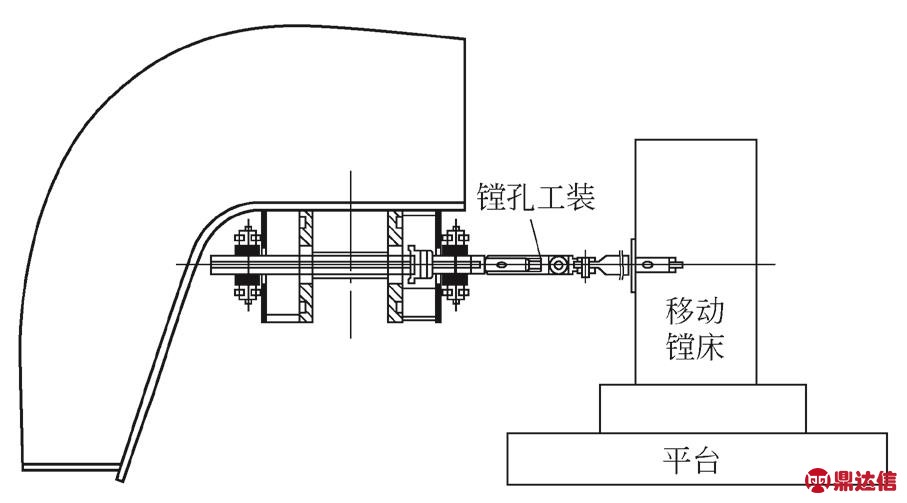
图5 桥架整体加工工艺
通过参数化建模完成产品几何信息和非几何信息的MBD数据模型库建设,并利用多学科仿真分析系统完成对该起重机桥架和零部件的强度、刚度等验证。在此基础上,根据验证完的MBD模型中的非几何制造工艺信息生成该起重机的工艺规程,主要包括下料工艺规程、焊接工艺规程和机加工工艺规程等(见图6)。
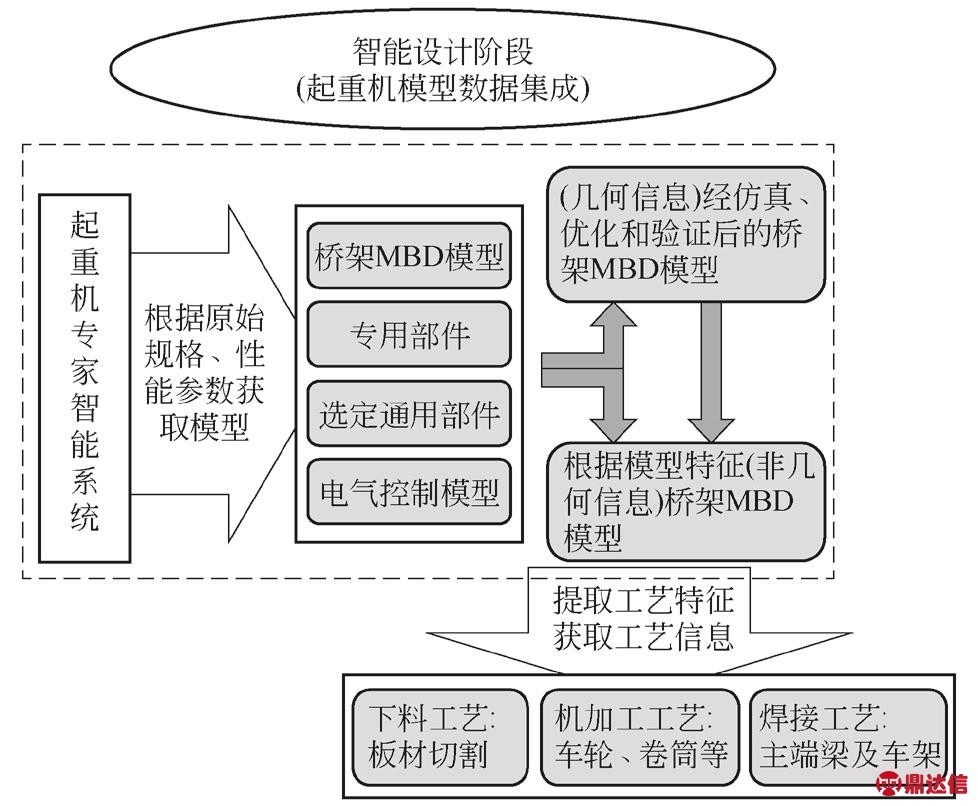
图6 基于MBD模型的起重机智能设计协同流程
2.2 起重机智能加工与装配协同
起重机加工与装配协同是起重机加工制造与装配过程的协同。结合起重机的制造工艺特点和小批量产出特性,一方面完成对起重机桥架等零部件的制造,另一方面完成对分组零件的实时装配,经过加工和装配的协同工作,最终完成对起重机整机意义上的制造。
起重机的智能加工与装配系统是基于智能设计的数据基础上,对起重机工艺模型的仿真验证,利用智能工装系统完成自动化加工流程,对加工过程进行实时监测控制,能根据专家库知识和经验对加工过程进行自适应调整的智能系统[10]。起重机的智能加工系统重点体现在刀具、工件、工装协同工作识别系统、系统实时状态监测与自适应调整系统、智能工装技术等部分。
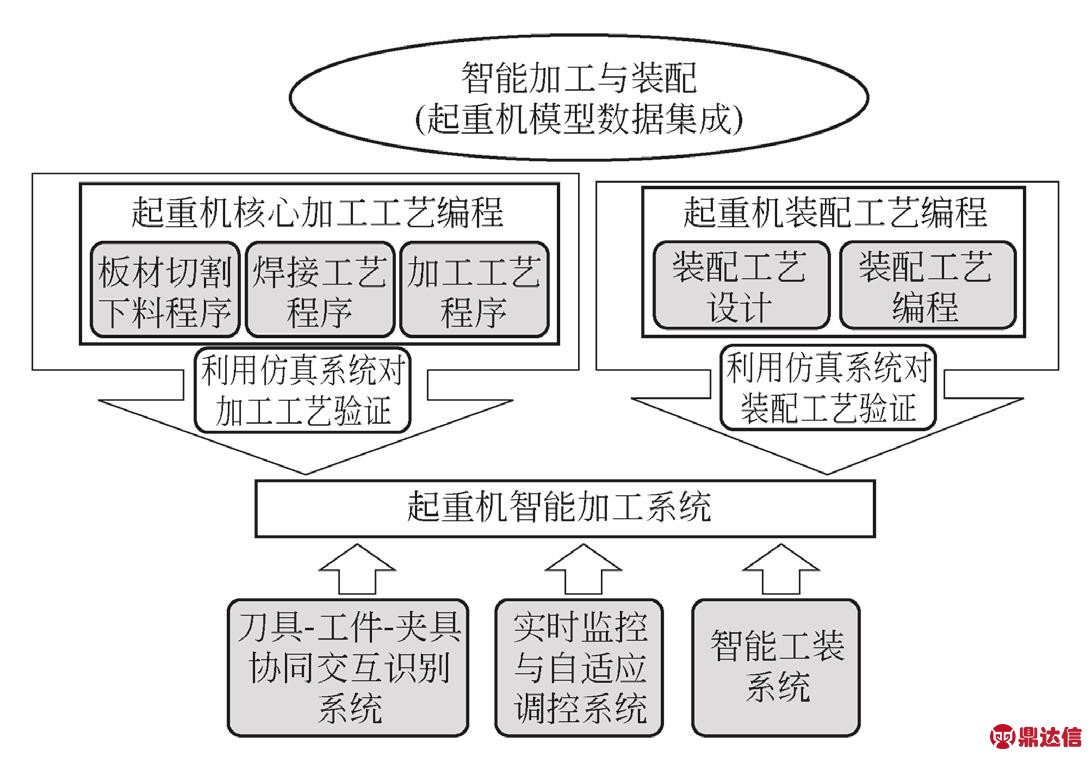
图7 起重机智能加工与装配协同流程
2.3 基于CPS系统的起重机智能制造协同
CPS系统指的是信息物理融合系统 (Cyber-Physical System),信息物理融合系统是一个综合计算、网络和物理环境的多维复杂系统,通过3C(Computation,Communication,Control)信息技术的有机融合与深度协作,实现对物理环境的状态感知、实时分析、科学决策和精准执行。CPS系统是实现设备和产品的实时连接、相互识别和有效交流,实现了信息世界与物理世界的融合,进而构建一个高度灵活的个性化、数字化的智能制造系统[9]。
在基于CPS的起重机的智能制造系统中(见图8),起重机制造所使用的加工设备、设施和材料构成了该系统的物理环境,CPS系统利用物理环境中的嵌入式模块,如CNC模块、传感器识别模块、机器人模块、数控加工模块以及运行维护模块等,通过网络通信系统将起重机的设计、制造、装配、运维、服务等过程中产生的海量数据进行实时汇总,在信息层对大数据进行挖掘、处理与优化后,从而实现对物理层的起重机制造系统的控制、决策和服务,该系统能够实现起重机制造过程中的物理层、网络层和信息层的协同与深度融合。
3 起重机智能制造关键技术
3.1 智能制造设备的机器视觉技术
机器视觉能模拟人类的视觉功能,通过图像获取技术、处理技术、图像的配准以及与智能装备联合控制等来实现实时感控能力,机器视觉技术使自动化生产线具备强大的感知能力,并能摆脱预先设定的运动轨迹,通过感知能力自动识别并处理场景信息,完成对指定物体的监测与控制,使其生产过程更加智能化和柔性化[10]。
当前我国智能制造装备业发展迅速,对机器视觉检测与控制等智能技术有着巨大和迫切的需求。起重机智能制造的机器视觉技术属于特定领域应用,该技术应用还没有形成统一的体系。鉴于该领域的制造装备属于复杂光机电系统,对检测实时性、准确率和重复性要求等级高,因此,需针对起重机智能制造装备的特定需求,逐步建立完善的机器视觉监控方法体系,从而有助于加速对相关装备的开发。
3.2 面向智能的专用柔性工装夹具
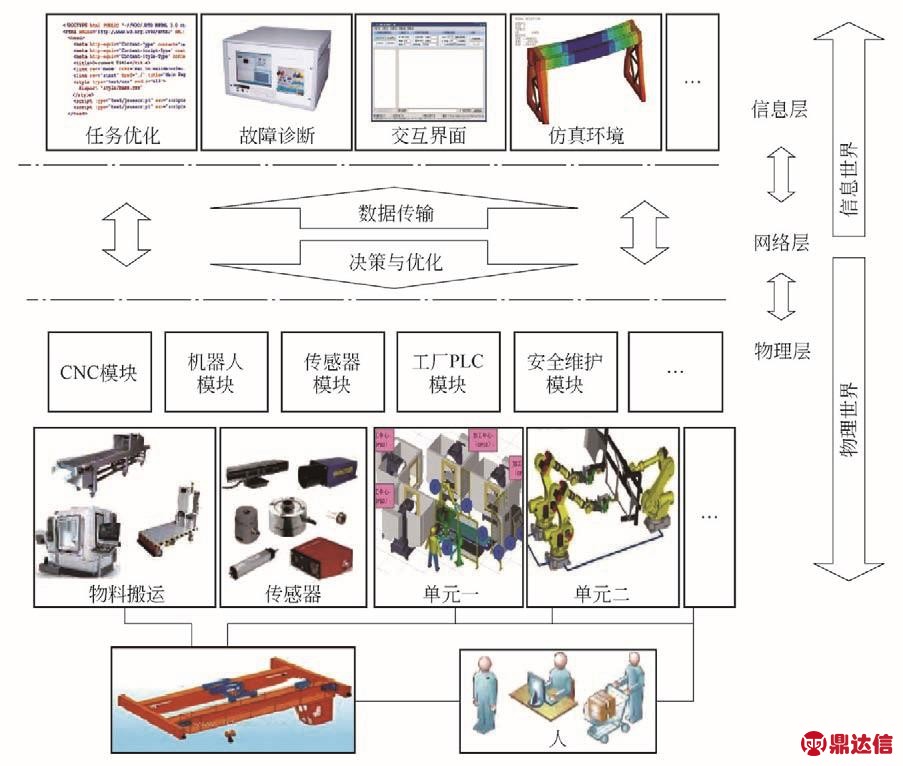
图8 基于CPS的起重机智能制造协同系统流程
起重机的钢结构件整体重量偏大,在钢结构件的焊接过程中,需要克服大型钢结构整体翻转、长形板材组焊过程中的形变、狭小空间焊接等不利因素,特别是主梁上翼缘板焊接路径为非线性曲线,需施加预应力进行焊接,这些工艺特点最终导致起重机钢结构件自动化程度低、焊接精度不易保证和制造成本居高不下等限制[11]。
面对起重机智能制造的驱动,设计自动化程度高的专用工装夹具是实现起重机智能制造的重要基础和保障。通过专用搬运机器人完成钢结构装配的预定位,利用专用夹具完成精确定位,焊接机器人实现各部位的精准焊接等,开发出专用的起重机智能工装夹具,将会极大地影响整个制造环节的效能。
智能工装夹具一般具有可重构的功能,可以实现机械装配中工装与零件 一对多 的自适应模式,柔性程度高,还可实现工装的数字化定位,具有传统工装不可比拟的优势。柔性工装夹具主要有四类典型结构:多点阵真空吸盘式柔性工装、分散式部件装配柔性工装、行列式柔性工装及大部件全自动对接平台。
3.3 系统状态监测与自适应调整
传统起重机加工制造过程中,在振动、温度等综合环境变化的影响下,会造成零件最终加工精度的降低。因此智能加工系统应具备实时监测功能,控制系统能根据监测得到的实际工况以及学习获得的工艺知识对工艺参数进行在线优化与反馈控制,为切削参数优化、加工误差补偿等智能决策过程提供支持[12]。
起重机零部件规格大,焊接加工中对预应力要求比较高,对实时温度、预应力、形变等状态的监测是极为重要的,同时,针对实时工况变化采用智能化方法对工艺过程进行自主学习及决策控制是需要攻克的关键技术。
3.4 工业软件的融合与统一
工业软件是各类工业生产环节规律的代码,是制造技术发展过程中最显著的特征之一,也是新一代信息技术的核心与灵魂。在信息物理系统中,从研发设计、生产制造到管理服务等各个方面,系统对人、设备、网络的感知和控制离不开对工业技术模块化、代码化和数字化的定义。目前工业软件的融合还有诸多问题,一是国产基础软件对核心技术掌握不够深入,产品性能、稳定性和成熟度等与国外主流产品仍存在一定差距;二是国外企业在技术、产品和市场上长期领先,国内产品在短时间内很难抢占市场;三是各环节链企业缺乏深度合作意愿,难以形成系统化合作模式,还需在完善基础软件产品生态、支持开放的开发模式、加强各软件协调发展等方面进行深度整合和协作。
4 结束语
起重机智能制造的进展势必得益于智能制造技术的整体发展和推广,对于起重机制造企业来讲,应根据自身企业的技术现状,制订由点到面的智能化发展规划,同时,智能制造生产线或智能工厂的运行也离不开企业自身的研发,在新技术的推广中,企业应积极研发柔性工装夹具,为全面推行智能化做好技术准备。
参考文献
[1]顾寄南,尚正阳,唐仕喜,等.当前智能制造若干关键技术综述[J].机械设计与制造工程,2017,46(9):11-15.
[2]宋红晓,王利刚.智能制造技术与系统的发展与研究[J].中国新技术新产品,2017(6):127-128.
[3]杜宝瑞,王勃,赵璐等.智能制造系统及其层级模型[J].航空制造技术,2015(13):46-50.
[4]赵敬云,李强,朱绘丽.桥式起重机主梁一次成型技术应用与仿真分析[J].河南机电高等专科学报,2015,23(4):1-4.
[5]安存胜,聂福全.超大型起重机桥架整体加工工艺及装备[J].金属加工(冷加工),2016(9):41-44.
[6]陈冰.面向智能制造的航空发动机协同设计与制造[J].航空制造技术,2016(5):16-21.
[7]周秋忠,樊庆春.MBD支持的产品协同设计及协同信息表达[J].制造业自动化,2016(5):16-21.
[8]岳伟.智能加工技术研究进展与关键技术[J].工具技术,2015,49(11):3-6.
[9]蒋国平,樊春霞,宋玉蓉,等.复杂动态网络同步控制及其在信息物理系统中的应用[J].南京邮电大学学报(自然科学版),2010,30(4):41-45.
[10]王耀南,陈铁健,贺振东,等.智能制造装备视觉检测控制方法综述[J].控制理论与应用,2015,32(3):273-276.
[11]张田会.基于本体和知识组件的夹具结构智能设计[J].航空制造技术,2016,22(5):1 165-1 178.
[12]张定华,罗明,吴宝海,等.智能加工工艺引领未来机床发展方向[J].航空制造技术,2014(11):34-38.