摘要 针对洗衣机内胆圆筒的焊接,设计了整套自动化焊接设备,主要包括板料上料工位、卷绕工位、搬运工位、夹紧夹具、焊接工位及下料工位。其中板料上料工位采用批量上料,然后真空吸附对单个板料进行上料。通过卷绕工位,实现将平板材料卷绕成圆筒状,然后经过夹紧夹具对圆筒实现横向及纵向的夹紧。采用氩弧焊机对焊缝进行焊接,经过检测,焊缝达到密封效果。
关键词: 圆筒 卷绕 焊接 自动化
0 序 言
洗衣机内胆材料一般为不锈钢圆筒,焊接前为不锈钢板材,通过卷板机将板材卷绕成圆筒,然后进行焊接,形成密封的圆筒[1-4]。氩弧焊优势主要有:焊缝一致性好,操作方便,设备成本低,便于自动化集成,氩弧焊技术在家用电器及五金件的焊接应用非常广泛[5-8]。
传统的焊接生产大多采用手工加工或者简单的半自动化方式生产,存在着工艺落后、生产效率低、人力资源浪费、劳动强度高、焊接质量不稳定等问题,已经无法满足家电企业的现代化生产的需要[9-12]。针对以上问题,需要设计一条自动化焊接生产线,以最终达到提高生产效率、降低劳动强度的目的。
文中重点介绍了洗衣机内胆圆筒构件自动化焊接生产线的结构,达到减少人工操作、提高自动化程度的目的。
1 技术要求
待焊产品为洗衣机内胆,为一圆筒形零件。焊接前为冷轧板,材质为Q235A,外观尺寸为1 500 mm×1 000 mm×0.5 mm。原材料经过激光切割成型,可保证切割后的尺寸适合焊接,最终焊接成型后圆筒直径尺寸为φ477 mm±2 mm。焊接成型后,需对成品进行外观检测和泄露测试,以不渗水为检验标准。焊接前材料及焊接成品示意图如图1所示,图1a为焊接前的板料,图1b为焊接后的成品。
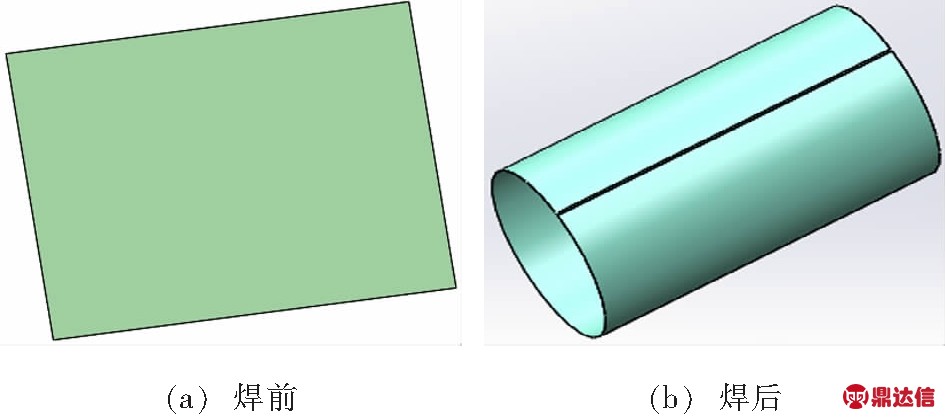
图1 焊接产品
2 总体设计
圆筒焊接成型需要经过两道工序:卷绕成型和焊接。由于板料尺寸较大,卷绕后存在一定的公差,并且板料较薄卷绕后中间部分可能鼓起等因素,选择对工件高低不敏感的氩弧焊接方式,并设计了专用的自动化设备。
设备主要由板料上料工位、卷绕工位、搬运工位、焊接工位、下料工位以及相应机加件等组成,如图2所示。设备运行时,上料工位内的板料被运送到卷绕工位内,卷绕工位将上一工位输送来的板料卷绕成圆形,卷绕完成后搬运工位将卷绕后的板料运送到焊接工位内。此后焊接工位开始对其进行焊接,焊接完成后,焊接工位可将成品推出至搬运工位,然后再流入到下料工位,此后人工取料。
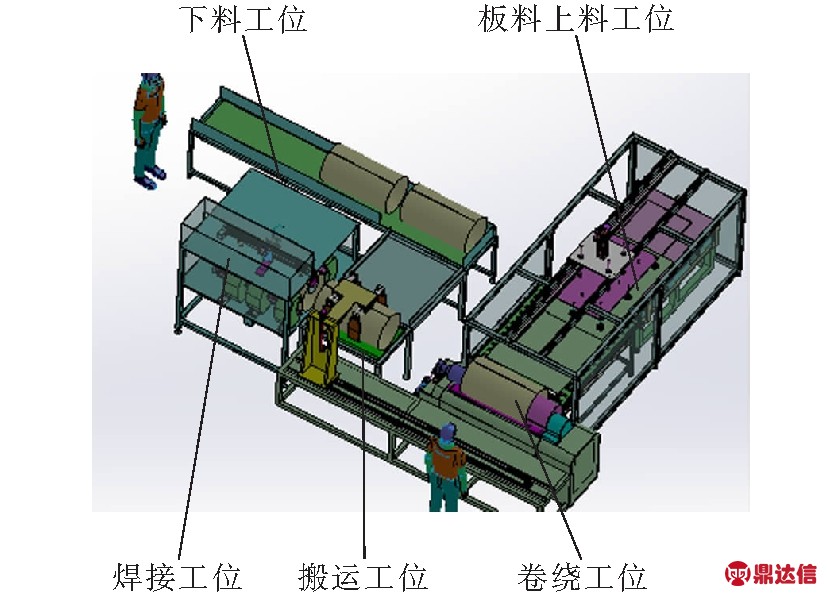
图2 设备总体机构图
2.1 板料上料工位设计
由于板料较大且较薄,单个上料容易损坏板料的平整度,且较为浪费时间。文中所述机构可一次性存储多件板料,一次上料可满足较长时间生产所需,且上料一致性好,不会对板料造成损伤。
如图3a所示,板料上料工位主要由存储机构、抓取机构、二次定位机构以及相应机加件等组成。设备运行前,将一批物料用叉车放置在存储机构上,如图3b所示。此后抓取机构内的气缸带着真空吸盘和直线运动副(导向用)向下运动直到吸盘接触到板料,然后抓取机构内的真空发生器开始工作,与之连接的15个真空吸盘(呈均匀分布)开始将板料吸附住,能够尽可能地使板料各部分受力均匀,最大程度的减少其变形。每次取走一个板料,电动推杆都在4个直线运动副的导向下向上运动一个板料厚度的距离(0.5 mm),因为真空吸盘高度位置不变,这样可保证每次都能使真空吸盘和板料很好地接触。每个板料被真空吸盘吸住后,抓取组件内的电机开始工作,驱动齿轮齿条运动副在线性滑轨的导向作用下将被吸附的板料搬运到二次定位机构的下方。
如图3c所示,二次定位机构主要由动力滚筒、夹板、正反螺纹副、直线运动副(导向作用)以及相应机加件等组成。在此机构内没有板料时,两块夹板之间的距离较大(大于板料宽度),这样可以保证每次抓取机构都能将板料放入到二次定位机构内。当传感器检测到板料被放入到机构内后,两块夹板在正反螺纹副和直线运动副的作用下开始向中间运动以实现对板料位置的二次定位,与此同时动力滚筒开始运动,将经过二次定位后的板料运送到卷绕工位。
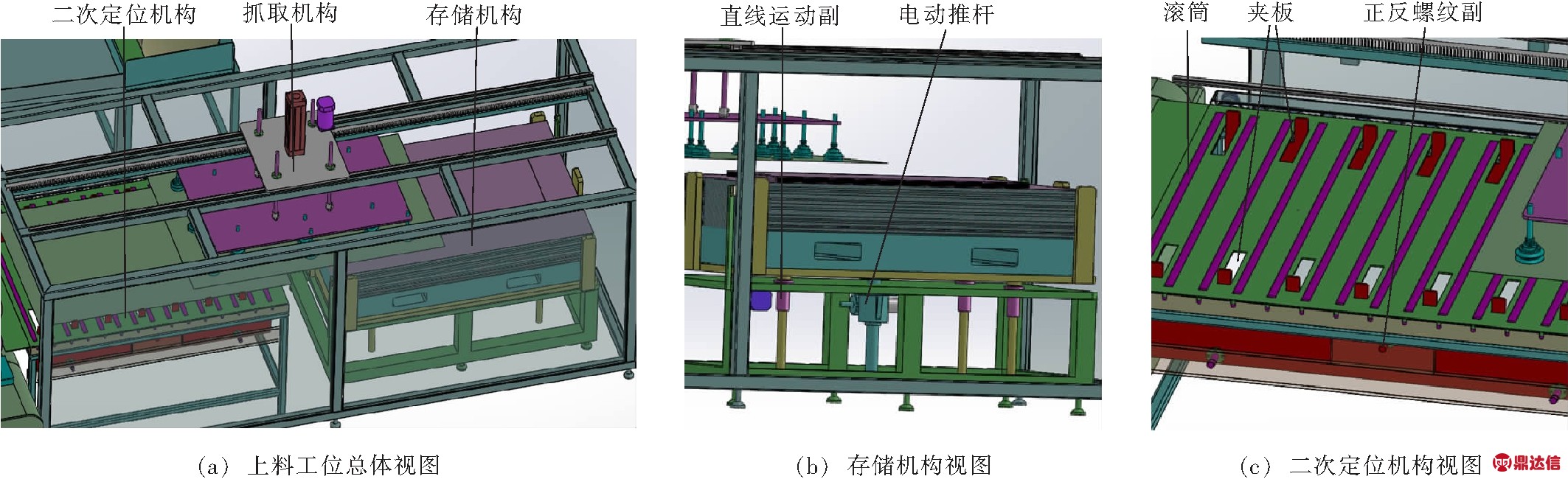
图3 板料上料工位机构图
2.2 卷绕工位设计
卷绕工位主要由机架、轴承座、主动轮、从动轮、气缸1、气缸2、翻转块、电机、滑轨以及相应机加件等组成,如图4a所示。其中,主动轮的一端安装在轴承座内,此端还连接有电机,电机可为主动轮提供卷绕时的动力。轴承座宽度较大,可保证主动轮一端固定在轴承座内,整个主动轮能较好的保持其位置精度和结构强度。如图4b所示,气缸2和翻转块连接在一起,当气缸2的活塞杆伸出时,翻转块可将主动轮的另一端包裹进去。当卷绕完成后下料时,气缸2活塞杆缩回,此时翻转块将会和主动轮脱离。卷绕前,在板料上料工位内滚筒的作用下,板料被推入到卷绕工位。此时,气缸1开始向上运动,在直线运动副的导向作用下,将两个从动轮往上顶,使板料能够同时和主动轮以及从动轮接触,气缸1配备单独的调压阀,可调整其输出力,从而达到对板料卷绕效果的调整,卷绕机构放大图如图4c所示。
2.3 搬运工位设计
如图5a所示,搬运工位主要由传动机构、抓取机构以及相应机加件组成。传动机构主要由同步带,同步轮以及两个直线运动副(线性滑轨)组成,可实现较为精密的长距离传送;抓取机构主要由电机、滚珠丝杆、线性滑轨、气爪、夹爪以及相应机加件组成。搬运工位工作时,夹紧机构内气爪带着夹爪将卷绕好的板料夹紧,然后卷绕工位内的气缸1下降,搬运机构内的电机驱动滚珠丝杆运动,将板料向上提升一段距离将其从卷绕机构内取出,此时传动机构内电机驱动同步轮,将卷绕好的板料运送到焊接机构内。待焊接完成后,搬运机构将成品取出并送入到下料机构内,夹紧机构如图5b所示,图5c为夹紧机构放大图。
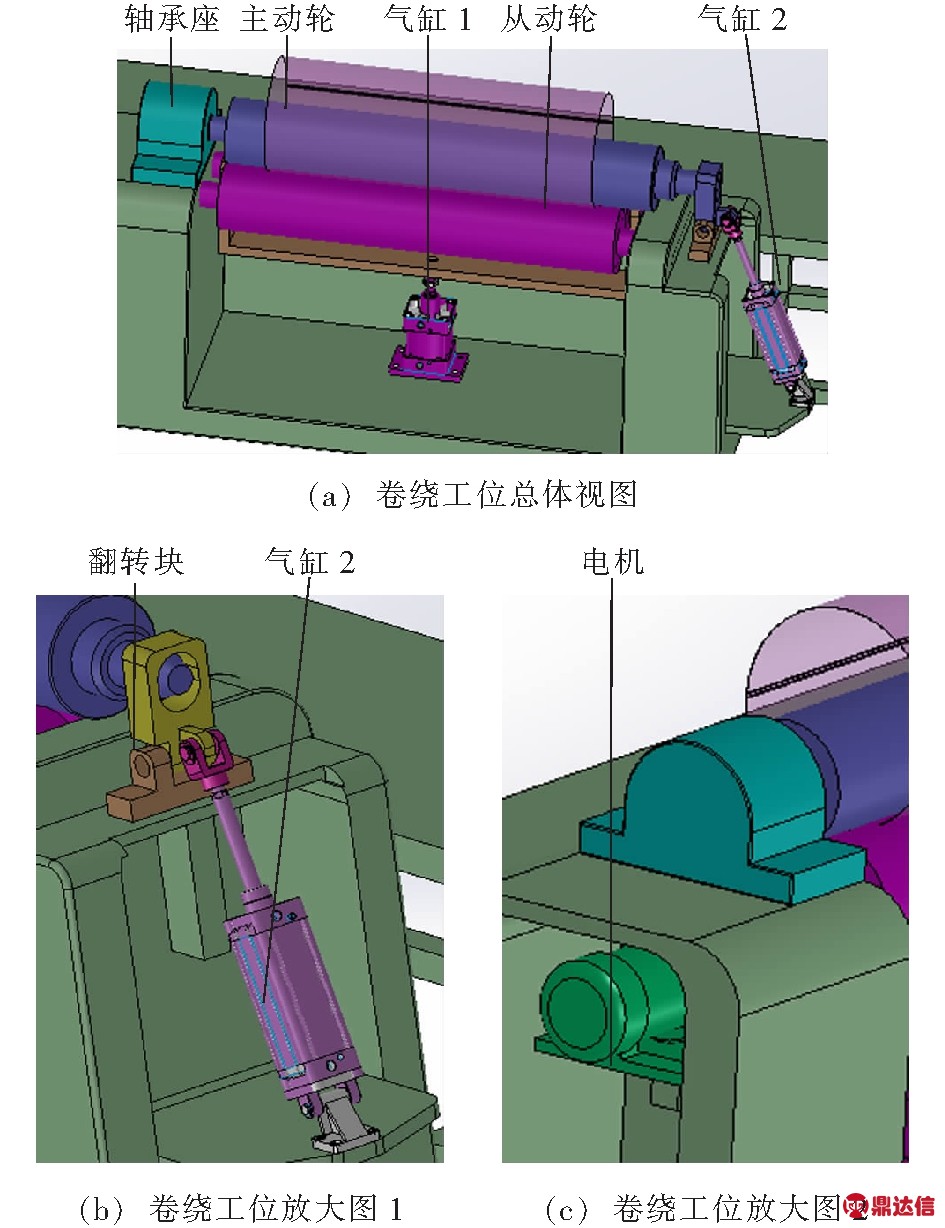
图4 卷绕工位机构图
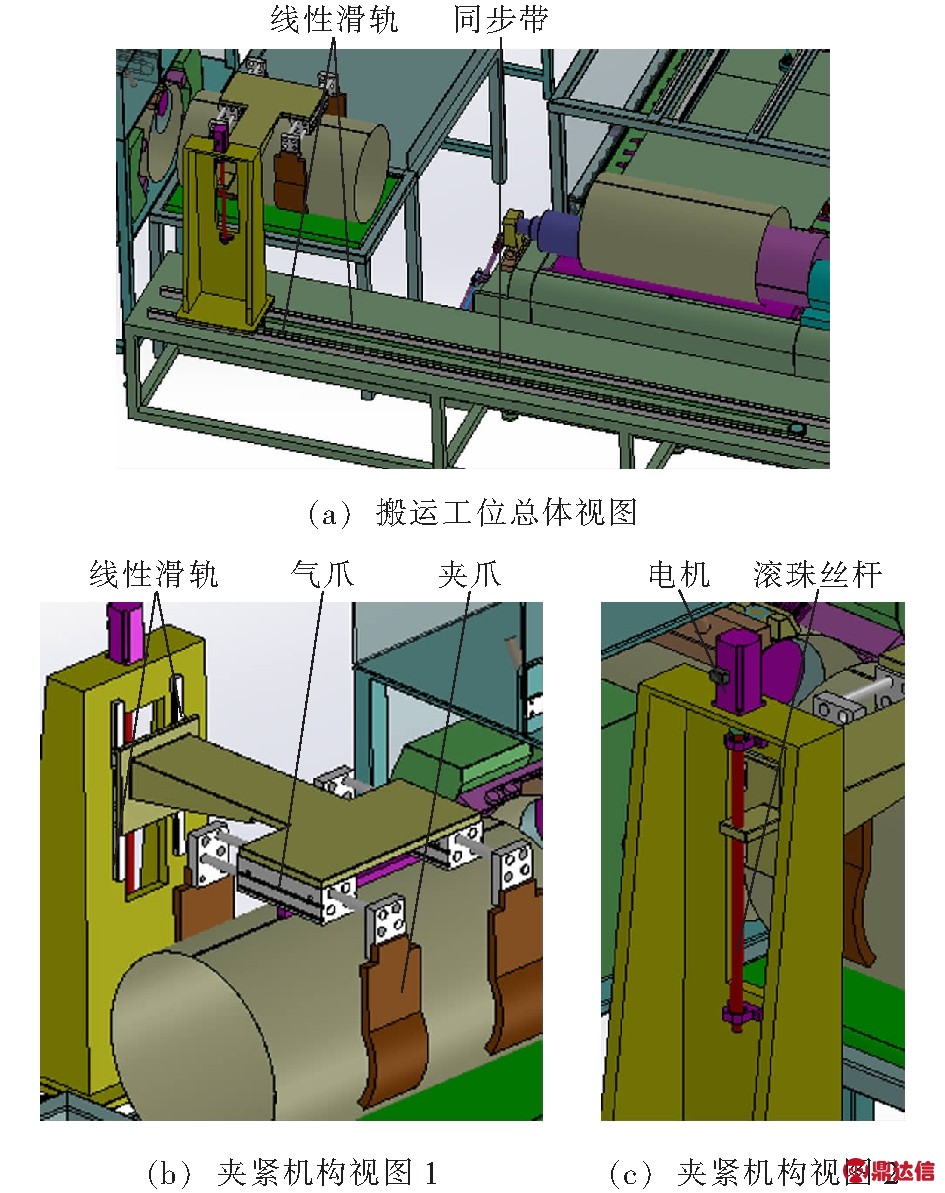
图5 搬运工位机构图
2.4 夹紧机构设计
夹紧机构1主要由正反丝杆螺母副、驱动轮组件、固定座、直线运动副以及对应机加件组成。其中,驱动轮组件固定在固定座,固定座固定在直线运动副(线性滑轨)上。驱动轮组件内含有多个动力滚筒(滚筒较短),动力由该机构内电机提供,如图6所示。
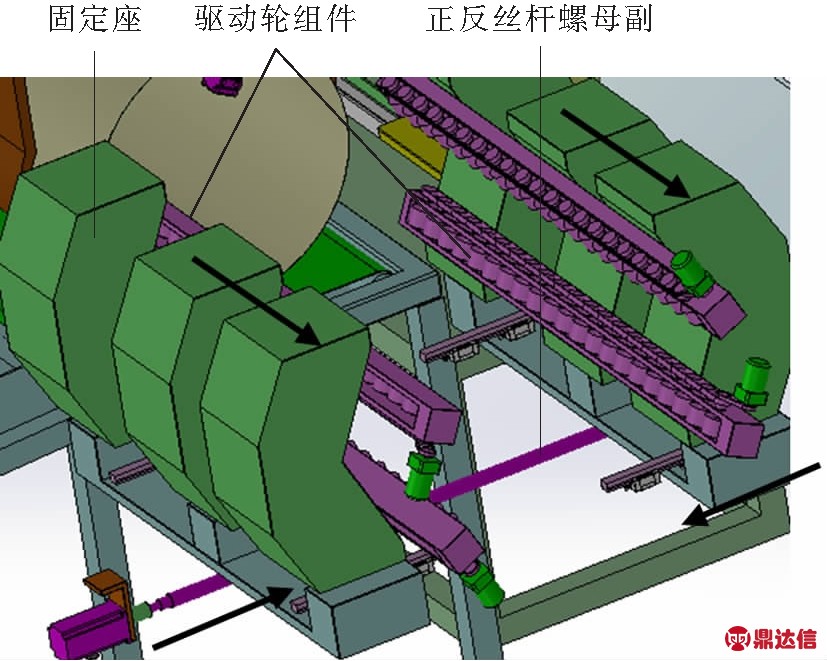
图6 夹紧机构1示意图
当卷绕好的板料经由搬运工位运送到此处前,正反丝杆螺母副在电机作用下开始运动,此时左、右两边固定座背向运动,彼此远离。当板料被运送到机构内后,丝杆螺母副开始反转,直至驱动轮组件将其夹紧,此后搬运组件内气缸开始松开,驱动轮组件内电机开始运动,将卷绕好的板料完全运送到焊接机构内指定位置。
夹紧机构2主要由气缸和2个直线运动副、压块以及对应机加件组成。板料被固定后,需要为焊接做准备,因为焊接方式采用搭接焊接,故搭接处需将其定位及压紧。板料在定位辊和压块的作用下完成轴向的夹紧。其中,定位辊起到对板料定位作用,保证搭接的重合宽度大于1 mm,固定在夹紧机构1内的固定座尾部上,通过悬臂连接伸入到如图7所示位置机构开始运动时,气缸在直线运动副导向作用下带着压块下压,将焊接处压紧。
2.5 焊接工位设计
如图8所示,焊接工位主要由夹紧机构1、夹紧机构2、焊枪组件等三大部分组成。其中,夹紧机构1可对卷绕后的板料实现径向方向的夹紧,夹紧机构2可对板料实现轴向方向的压紧。待两个方向均被夹紧后,焊枪组件即可开始焊接,焊接的同时随动压紧焊缝,避免板料变形及间隙,保证无漏焊现象。
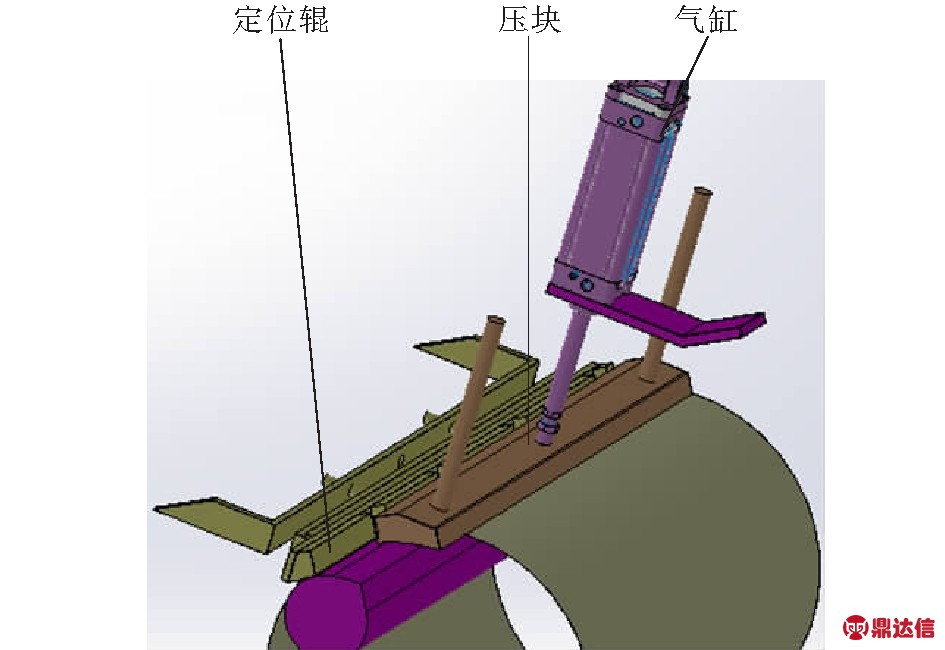
图7 夹紧机构2示意图
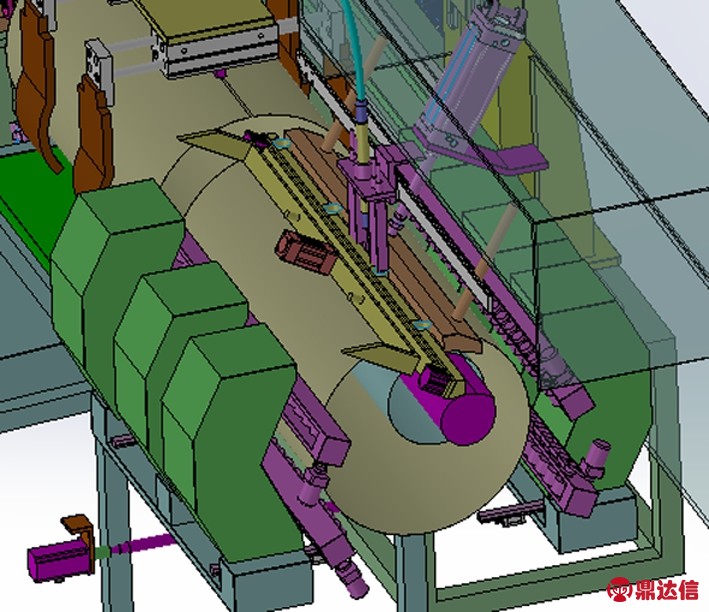
图8 焊接工位机构图
2.6 下料机构设计
板料焊接完成后,搬运机构将其取出,然后放在搬运机构上,经由搬运机构内的皮带线流入到人工取件位置,下料机构如图9所示。
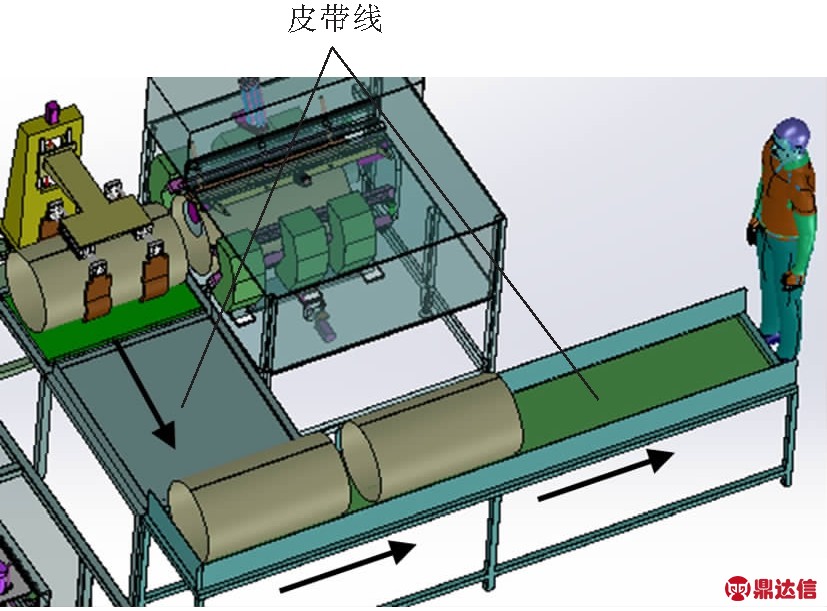
图9 下料机构图
3 结 论
(1)采用手动对板材进行批量上料,然后自动完成单个产品的上料,经过卷绕机构,形成圆筒结构,在搬运机构作用下,运动到焊接工位。在夹紧机构的固定及定位后,采用氩弧焊机实现焊缝的密封焊接。
(2)该机构关键的机构为夹紧机构,采用夹紧机构1实现工件径向夹紧,夹紧机构2实现工件横向夹紧,抵消焊接过程中产生的热变形,保证焊缝的质量。经过实际生产检测,该系统生产的产品良品率达到99%。