摘 要: 使用高温高压蒸汽推动汽轮机可以实现能量的转化,而针对蒸汽的调控直接影响到能量的转化效率和系统的安全性。减压阀作为蒸汽辅助动力系统的核心部件,主要对高温高压蒸汽进行调控,使其压力和温度等参数被调节到特定范围。节流特性是减压阀的主要性能指标,以一种新型多级角式减压阀为研究对象,采用计算流体力学方法,考察了笼罩式阀芯和节流孔板的间距对节流特性的影响,具体分析了不同间距下流动特性、湍流耗散率、温度特性和压比特性等节流性能。研究结果为后续开展类似减压阀的节流优化设计提供参考。
关键词: 减压阀;多孔板;笼罩式阀芯;节流特性;计算流体力学
引言
蒸汽作为一种动力和热力源应用于电力、冶金、船舶(舰艇)等国民经济和国防建设领域。例如,热电厂中的高温高压蒸汽推动汽轮机用于实现能量转化。为了对蒸汽管道中蒸汽的温度、压力、流量进行调节,实现特定参数下蒸汽的应用,需采用减压阀等对蒸汽进行调节,这也直接影响到能量的转化效率和系统的安全性。随着超超临界大容量发电机组、石油天然气工程和百万吨级乙烯工程等国家重点工程的发展, 各种高温高压等复杂工况机组不断出现,对减压阀的需求不断增加,性能要求也不断提高。
基于以上背景,本研究以一种新型多级角式减压阀为研究对象,采用计算流体力学方法,考察了笼罩式阀芯和节流孔板的间距对节流特性的影响,为后续开展类似减压阀的节流优化设计提供参考。
1 计算模型
1.1 减压阀
在蒸汽热力系统中,过热蒸汽相较饱和蒸汽具有高温度、低密度等特点,因此被当作远距离输送的动力能源,但其热效率远低于饱和蒸汽,不适用于下游用户,因此需要对其温度和压力进行调节;而减温减压装置作为关键装备,能对电站工业锅炉等处输送来的高温高压过热蒸汽进行调节,以达到下游用户要求的热力参数。
减压阀作为减温减压装置中的核心部件,主要是通过节流元件来改变阀门流道横截面积,使流体通过时的速度及动能发生改变,从而引起压力损失,达到减压的目的。减压阀还需要依靠自身或外部的控制与调节系统的调节,保证阀后压力在一定的误差范围内恒定[1-2]。
本研究主要针对一种新型的多级角式减压阀开展研究[3-6],其结构示意图如图1所示,其主要的组成部分有阀体、笼罩式阀芯和节流孔板。其中,笼罩式阀芯和节流孔板是作为该阀的两种主要节流元件[7]。阀门入口流道直径为190 mm,长度为200 mm,出口流道直径为285 mm。其中,本研究模型的笼罩式阀芯采用双层笼罩结构,开孔沿周向均匀排布,与传统阀芯相比具有良好的节流特性以及减振降噪的特点[8]。
节流孔板的结构同样如图1所示,其直径为285 mm,厚度为30 mm。孔板上孔的直径为15 mm,两个孔的间距为32 mm。节流孔板与阀体焊接固定不动,通过小孔对阀门内部流体起到节流作用,从而达到降压的效果。
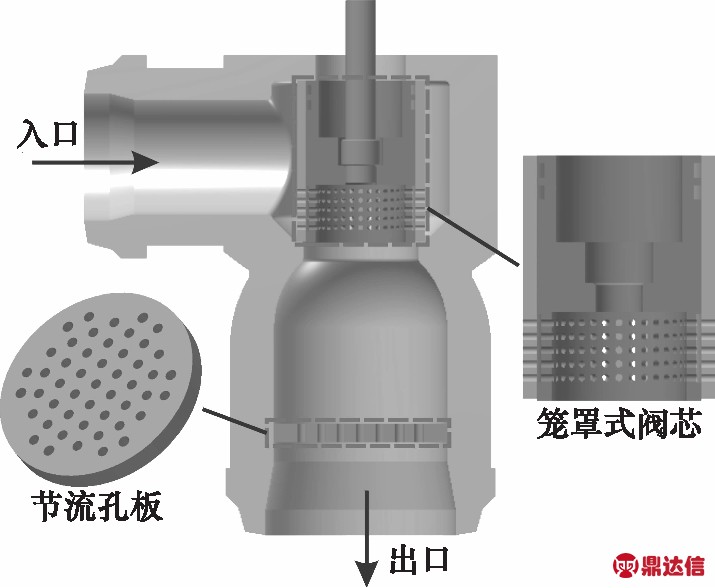
图1 多级角式减压阀的结构示意图
如图2所示,为该多级角式减压阀所对应的流道模型。可以发现,高压高温过热蒸汽主要在笼罩式阀芯和节流孔板处发生节流,而节流孔板与笼罩之间的距离(即与阀芯的距离)直接关系到两次节流作用的相互影响。因此,本研究主要考察阀芯和节流孔板的间距对节流特性的影响。如图2左侧所示,调整节流孔板上表面到阀腔区域中椭圆体部分下底面的距离来控制节流孔板的位置,分别设置为0, 50, 100, 150 mm。图2虚线部分呈现的是50 mm距离的流道模型。值得一提的是,改变节流孔板位置的同时并不改变整个流道模型的高度。
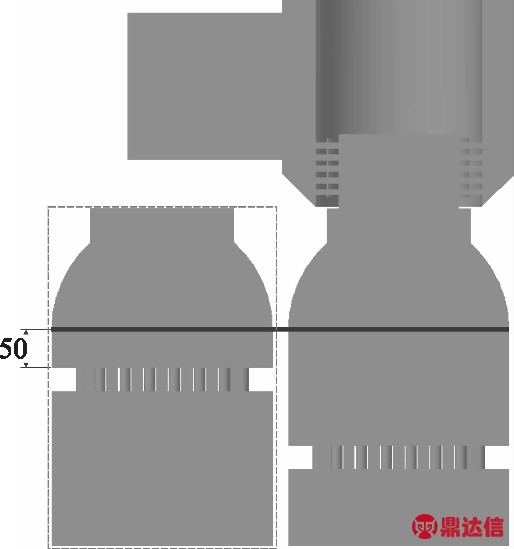
图2 多级角式减压阀的流道模型(mm)
1.2 数值方法
本研究研究的流体介质是高温高压的过热蒸汽,温度为793 K(520 ℃),压力为10 MPa,且该气体为可压缩气体。在模拟时设置为理想气体(Ideal-gas)。选择压力入口和压力出口作为进出口的边界条件。出口压力统一设置为1 MPa,温度为793 K。由于高压差的存在,流体呈现高速流动的状态,而本研究主要关注其最终稳定的状态。因此,Fluent求解器的设置为Density-based(基于密度),Steady(稳态)。湍流模型选择RNG k-epsilon湍流模型。由于涉及温度场的计算,需要打开能量方程[5]。
由于整个阀门的流道模型为轴对称结构,计算时只选取了实际流动区域的一半,因此需要把该模型的中心对称面命名为Symmetry, 入口平面命名为Inlet,出口平面命名为Outlet,其余平面皆为光滑无滑移壁面。
由于本阀门流道模型结构复杂,涉及众多小孔和曲面结构。在保证网格质量的前提下,本研究选用四面体网格,从而更好地适应小孔和曲面结构。为消除网格数目对数值模拟结果产生的影响,同时提高计算效率,开展网格独立性研究非常重要。选择开度为100%的流道模型来进行网格无关性验证。将最小网格尺寸从0.002 m调至0.003 m, 间隔0.0002 m,并以出口流量(Outlet flux)作为考察对象,结果如表1所示。
表1 不同网格数下的出口流量
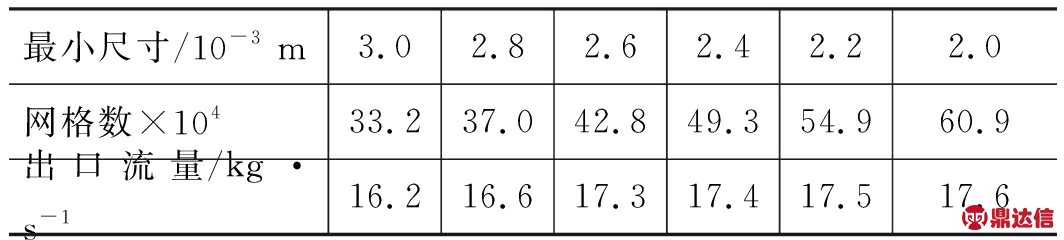
从表1中可以发现,当网格数大于49.3万时,出口流量的变化趋于稳定。最终选择Min size为0.0024 m作为最终的网格划分方法。
2 节流特性
2.1 流动特性
如图3所示,阀腔中心的高速流体遇到节流孔板时,会出现分离现象,一部分流体通过节流孔板通道流向出口流道,而另一部分流体由于节流孔板通道截面积大小有限,被迫挤压到阀腔两侧的低压区域,沿着近壁面低压区域形成漩涡。随着节流孔板位置的下移,阀腔中部高速流体区域的宽度在不断减小,并且该区域中最大流速也在不断降低。通过进一步观察发现,节流孔板位置越低,阀腔内漩涡的面积就越大。
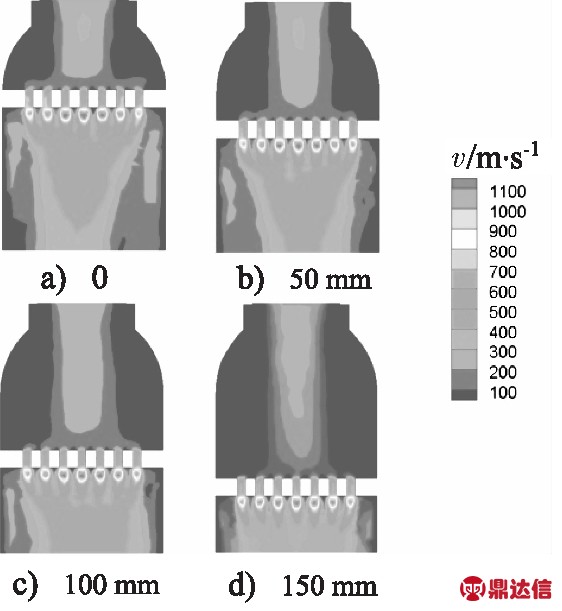
图3 不同节流孔板位置下对称面速度分布
然而,节流孔板位置的变化并不改变流道内最大速度出现的位置,但对于最大流速的大小产生了影响。随着节流孔板的下移,最大流速呈现明显的下降趋势。如表2所示,当节流孔板位置刚好在椭圆形阀腔下表面处,流速可高达1182 m/s。当节流孔板与双层笼罩距离较近时,阀腔内形成的高速流可以短时间内再次在孔板处完成二次节流,使速度得到再次提高。而节流孔板与双层笼罩距离较远时,高速流在阀腔内需要流动较长距离,速度有所下降,因此其节流孔板后的最大速度也会下降。
表2 不同节流孔板位置下最大速度和最低温度

2.2 湍流耗散率
湍流耗散率峰值的位置与节流孔板和阀芯的位置相互对应。从图4可知,随着节流孔板的下移,湍流耗散率ε不断增大,双层笼罩处(Y为0.2 m)的ε变化并不明显,但节流孔板处ε明显增大。
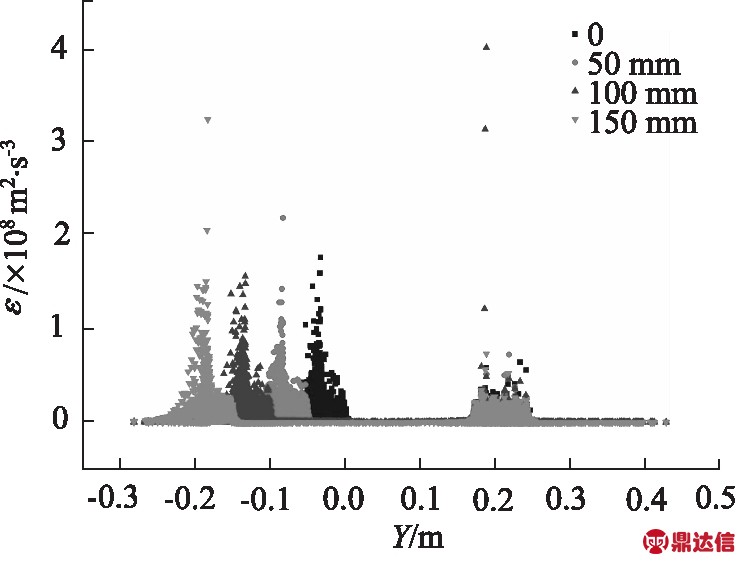
图4 不同节流孔板位置下湍流耗散率分布
2.3 温度特性
流场温度的分布与速度场相类似。如图5所示,随着节流孔板位置的下移, 阀腔中心的低温带宽度不断减小,节流孔板出口处的低温带的温度不断上升。从图5和表2提供的最低温度变化情况可知,最低温度在节流孔板下移的过程中越来越大,最大可以达到481 K。
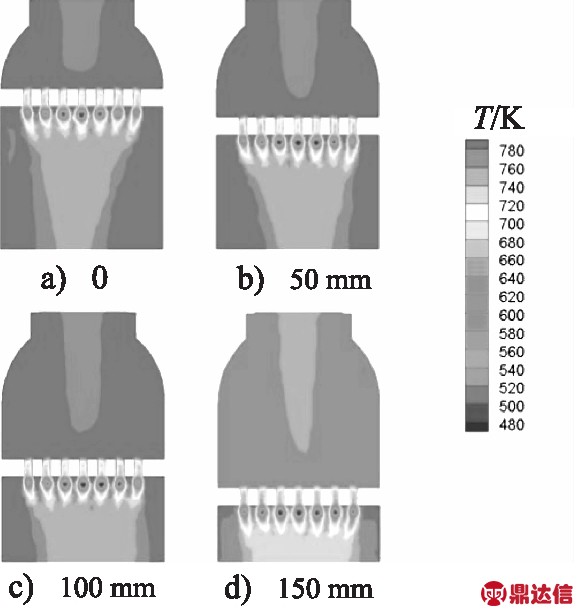
图5 不同节流孔板位置下流道对称面温度分布
2.4 压比特性
如图6所示,随着节流孔板的下移,一级减压后的压力p有小幅度的上升。4种节流孔板位置下流道压力分布情况基本相似,只是二级减压发生的位置随着节流孔板位置的下移而不断变化。从图中可以发现,随着孔板位置的下移,二级减压段减小的压力p逐渐增大,且在达到出口压力p后又继续向下减小了一定数值,最后又都在出口处稳定在1.0 MPa。从图6可知整个阀门各级节流元件的压比特性跟节流孔板的位置存在比较明显的关系。
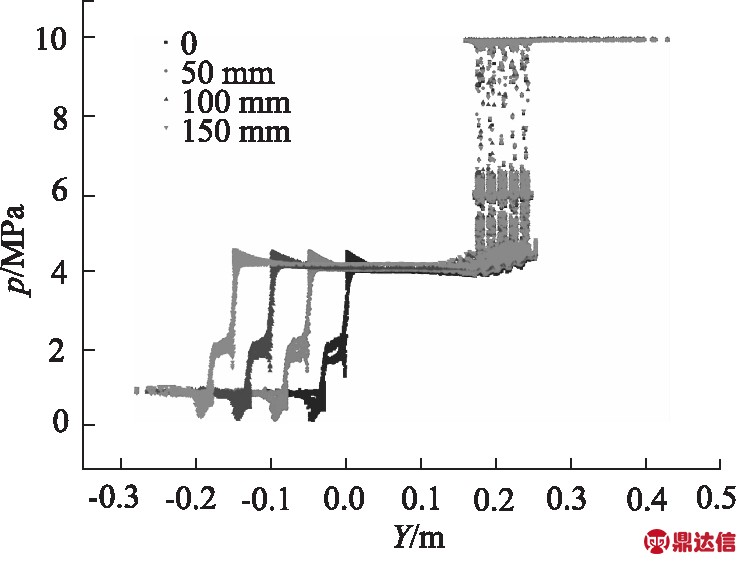
图6 不同节流孔板位置下Y方向上压力分布情况
表3更直观地表明了当节流孔板位置越靠近笼罩式阀芯,阀芯一级减压效果越好。当节流孔板位置刚好在椭圆形阀腔下表面处,压比系数可以达到0.25。节流孔板位置每下移50 mm,压比系数基本会下降0.005左右,可以表明节流孔板位置与该系数存在一种类似线性的关系。
表3 不同节流孔板位置下的减压比
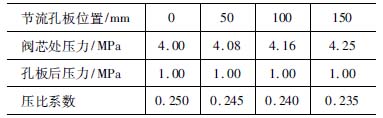
3 结论
在该新型多级角式减压阀中,笼罩式阀芯与节流孔板之间的间距对阀门节流特性影响较大。具体结论如下:
(1) 节流孔板位置的变化并不改变流道最大速度和最低温度出现的位置,但对于这两个参数的大小产生了影响;
(2) 随着节流孔板位置的下移,流道内阀腔上部两侧的低压区域逐渐消失;阀腔两侧的漩涡越来越大,阀腔中部的高速流宽度变小,流道的最大速度也不断减小;湍流耗散率不断增大,尤其是节流孔板处的湍流耗散率;阀腔中央低温带宽度不断缩小,流场最低温度不断增大;
(3) 节流孔板位置下移对于流道压力分布情况变化的影响并不明显,但笼罩式阀芯处(一级减压)的减压效果会逐渐下降。