摘要 传统减压阀组为链传动系统,使用中存在系统易发生故障、阀门轴端密封失效和阀板结垢等问题。轻型免维护减压阀组,设备运行状态平稳,日常维护工作量为零,解决了结垢问题,应用前景良好。
关键词 减压阀组 链传动 结垢 免维护
ABSTRACT Traditional valve unit is chain transmission,the failure were happened easily in use,such as the valve shaft seal failure and the scale formation of valve plate and other failures.Light maintenance-free valve unit works s moothly,routine maintenance workload is zero,the problem of the scale formation is solved,the application prospects are well.
KEYWORDS Pressure readucer unit Chain drive Scale formation Maintenance-free
1 引言
经过扩容改造,首钢从 20世纪 90年代开始有五座高炉,1#、3#高炉 2536m3,2#高炉 1726 m3,4#高炉 2100 m3,5#高炉 1036m3。除 2#、3#高炉煤气系统采用干、湿法并用除尘外,其余三座高炉均采用湿法除尘。
最初,五座高炉顶压控制设备——减压阀组均采用传统阀组(以下简称传统阀组),传动方式为链式传动装置。2#高炉 2002年大修改造后,引进使用了轻型免维护阀组 (以下简称新型阀组),此后,2005年 1#高炉利用 7天检修机会也将传统阀组改造为新型阀组。
通过两种阀组的应用实践比较,可以说各有利弊。如果轻型阀组在个别环节上继续加以改进和完善,将在今后的应用中更具有发展优势。
2 两种阀组的工作原理和结构比较
高炉减压阀组安装在重力除尘器和煤气洗涤塔之间的半净煤气管道上,是高炉控制顶压的关键设备,见图 1。
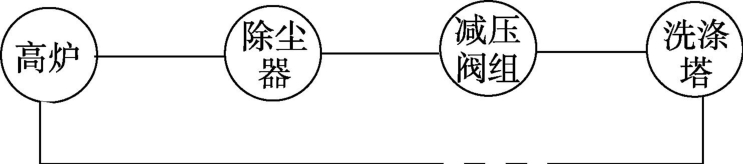
图1 减压阀组安装位置
传统阀组和新型阀组基本结构形式类似,由常通管 (一般Φ300)、自动调节阀 (一般Φ500)和3个大阀 (直径一般 (D1~D3)Φ800~Φ1000)组成如图 2所示,自动调节阀和 3个大阀均采用蝶阀。顶压调节以自动调节阀为主、3个大阀为辅,通过控制阀门开度,调节管道系统煤气量,以达到控制煤气系统内部压力的作用。
结构区别在于,传统阀组三个大阀传动形式为链传动,电机、减速机、传动链都布置在阀组外部的传动平台上,由传动链带动阀体旋转;新型阀组三个大阀为电动头传动,结构更紧凑。另外,传统阀组阀板较厚,而新型阀组阀板较薄,以自动调节阀为例,传统阀组自调阀阀板采用通轴方式,阀板最厚达 150mm;而新型阀组厚度仅为28mm,新型阀组更轻便灵活。同时,传统阀组各阀体两侧导出管较长,而新型阀组非常短,导致整体设备尺寸和重量差别较大。以 1#高炉为例,使用传统阀组整体设备长度 (阀组两侧管道大兰盘之间)达到 4.2m,而改造后新型阀组长度仅为1.1m,设备则重由 8.4t减为 2.5t。自动调节阀均采用自动气动调节,由钢丝绳拉动拐臂,带动阀板旋转。
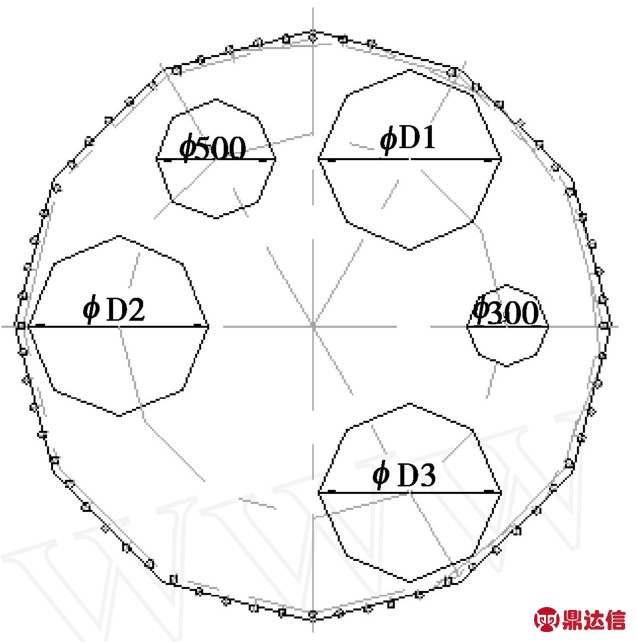
图2 减压阀组结构示意图
3 现场应用情况
20世纪 90年代开始,首钢五座高炉顶压调节均采用传统阀组,运行特点为:阀体受煤气中含尘量影响较少,阀门运行较为可靠,干法除尘系统阀门破损多为气流冲刷所致,湿法除尘阀门损坏多为阀板结垢增多,造成阀板两腮因积灰转动受阻、导致销轴切断,阀板与轴脱开。另外,因外部工况环境差,传统阀组传动系统又裸露在外,使用中传动系统易发生电机、减速机损坏、传动链绷断等故障,阀门轴端密封也经常出现密封失效、串风等问题。需定期进行阀体更换、传动系统检修和更换密封等维护工作。
2002年 2#高炉和 2005年 1#高炉使用新型阀组后,运行特点为:阀门运行平稳可靠,两座高炉均为湿法除尘系统,2#高炉新型阀组投用后,5年内阀门没有进行任何检修维护。直至 2009年停产前,仅更换了一个Φ500自动调节阀。1#高炉2005年 10月投用新型阀组后,至 2007年 5月阀组运行平稳,设备处于免维护状态。借鉴 2#高炉成功经验,在后期新基地建设中,首钢秦钢、首钢迁钢等地 1200m3~2650m3的 4座高炉陆续采用了新型阀组,使用效果良好。
但自 2007年 5月之后,1#高炉新型阀组三个大阀 (Φ850)经常出现阀门卡阀现象,直至最后完全被卡死。2007年 6月~2008年 3月,先后更换了Φ850阀门 4个,但因治标未治本,问题没有缓解。直至 2008年 4月,利用 5天检修机会,再次将新型阀组更换为传统阀组,但阀门卡阀现象没有消除。
首钢三高炉因采用干法除尘工艺,一直使用传统阀组,使用情况较好。5#高炉 2005年停产,传统阀组在使用中未出现严重卡阀现象。四高炉使用传统阀组,在 2007年底停产前后期也出现了严重的卡阀现象。
4 应对措施
针对传统阀组在使用中出现的传动系统易发生故障、阀门轴端密封失效等问题,首钢采用了传动系统定期检修措施。传动链每周加油润滑,阀门轴头每半个月加油润滑,利用每两月一次例修机会对电机进行吹扫、减速机进行打盖清洗。
针对传统阀组在干法除尘系统中易出现的阀板和倒流管冲刷严重问题,首钢利用每两月一次例修机会,采取对阀板和倒流管冲刷出的沟痕部位进行焊碳化钨修补措施,冲刷严重时更换阀门和倒流管。
针对传统阀组在湿法除尘系统中阀板易结垢问题,一是采取阀体定期清洗措施,利用每两月一次例修机会,对阀板及两腮部位采用高压水车冲洗;二是采取阀门定期更换措施,大致一年左右,对三个大阀和Φ500自动调节阀进行更换。
新型阀组在 2#高炉 2002年~2009年使用中和#高炉在 2005年~2007年 5月使用中,因运行平稳,基本处于免维护状态。
2007年 5月份后,1#高炉开始出现阀组大阀卡阀现象,被迫更换回使用传统阀组,不但大阀卡阀现象没有缓解,Φ500自动调节阀也开始出现严重卡阀现象,常因阀组阀门卡死高炉被迫安排检修处理,正常的检修秩序被打乱,严重威胁高炉正常生产。对此,首钢对辅助调节作用的三个大阀,采取了在高炉正常生产情况下,每天现场人为干预、大范围活动一次,缓解由于阀体长期不动、积灰多而卡阀的情况,但是,基本一个月左右就会出现阀门卡死问题,尤其是Φ500自动调节阀阀体厚,因积灰被卡死的几率明显高于其它 3个大阀。2009年 6月,对传统阀组的Φ500自动调节阀进行了改造,将新型阀组Φ500自动调节阀安装在传统阀组上,以上问题得以缓解,通过强化日常维护和冲洗,目前两个月一次例修周期基本能够保证。
5 现场实践分析比较
通过多年的现场实践比较,传统阀组与新型阀组各具特色,但新型阀组具有优势。
传统阀组需定期进行相关维护;新型阀组因在材质上、密封上进行了改进,阀体轻便,运行平稳,在干法系统中耐磨性提高,在湿法系统中结垢情况也比传统阀组要好得多,一般情况下处于免维护状态。
传统阀组传动方式简单更为直观,传动系统故障比较容易检修处理,故障排除较为简单;新型阀组执行机构由电传动头来完成,因电传动头与阀板轴直接固定,一旦电传动头内部发生故障,现场不易维修,只有作更换处理。
2008年首钢组织攻关组,对 1#高炉减压阀组结垢问题进行科研攻关,确定了阀体结垢原因:一是高炉超期服役 (设计 10年,目前使用超过了15年),煤气洗涤系统能力降低,洗涤、洗净效果变差,导致半净煤气系统中含尘量、含水量增大;二是由于原燃料成分变化,料中金属含量增加,导致煤气系统灰尘中锌金属富集,经过对减压阀组上积灰成分的化验分析,ZnO含量达到 45%以上,最高达到 55.8%。ZnO属不易溶解、洗涤的金属成分,且与灰垢一起板结在阀体上后,质地十分坚硬,极易导致阀体卡死;三是新型阀组在系统设计中含有喷水装置,对阀板及两腮部位进行不间断冲洗,有效消除积灰板结问题,但是由于一高炉粗煤气系统后端排水能力设计不足,且不易改造,所以无法安装喷水装置。
6 结语
通过现场实践总结和理论分析,新型阀组在干、湿法除尘的高炉系统中均可适用,而且在设备运行质量、减少维护工作量等方面,更具优势。但是,对于除尘系统老化、洗涤效果差的高炉系统,必须加装喷水,才能保证系统的正常运行。