摘要: 为实现电磁阀减压过程的精确控制,提出阶梯减压控制方法,并对控制参数进行了试验标定。通过对电磁阀阀芯受力与电磁阀液压响应特性分析,指出可通过调节电磁阀压力控制状态和控制信号状态持续时间得到不同的压力变化率,为阶梯减压控制实现提供依据。电磁阀压力控制状态采用延迟开闭控制方法。电磁阀控制信号状态持续时间受压力变化速率和开关延迟现象的影响,其中影响压力变化速率的阀口流量系数,影响开关延迟现象的开启延迟时间与关闭延迟时间通过试验标定。借助试验台架,对电磁阀不同速率的压力变化试验进行测试,结果表明所提出的阶梯减压控制方法能够很好地跟随目标压力,试验偏差可以维持在1 MPa以内,控制精度高。
关键词: 液压调节单元; 阶梯减压控制; 控制参数标定; 流量系数; 压力变化率
引言
电磁阀作为液压调节单元电子稳定控制(Electronic stability control,ESC)的主要执行部件[1-2],在进行车身稳定性控制[3-5]、ABS控制[6-11]等需要液压调节单元参与的过程中,都需要通过对电磁阀的控制得到精确的目标轮缸压力。目前对于ESC电磁阀的控制,通常采用线性压力控制,其实质是通过控制电磁阀线圈电流进行轮缸压力跟随控制[12-13],但线性压力控制受到轮缸压力体积(Pressure volume,PV)特性的影响,压力变化速率的可调范围受限[14],同时线圈电流容易受到温度和驱动电压变化的影响。
为避免制动轮缸PV特性和电磁阀工作环境的影响,针对电磁阀减压控制,本文提出从压力控制状态切换和控制状态持续时间的角度进行阶梯控制的方法,并对状态持续时间中控制参数进行试验标定,利用不同减压速率的压力变化试验进行验证,以期为阶梯减压控制方法的实现提供依据。
1 电磁阀基本构型和受力分析
电磁阀利用动铁与定铁在电磁场的作用下,克服阀芯上所受到的其他阻力,从而实现电磁阀进液孔和出液孔的导通与关闭[15-17]。在阀芯的运动过程中,主要受到电磁力Fm、弹簧力Fs、液压力Fh、摩擦力Ff和阻尼力Fv的作用,阀芯极限位置时还受上限位的作用力F′N和阀座的作用力FN,受力分析如图1所示。
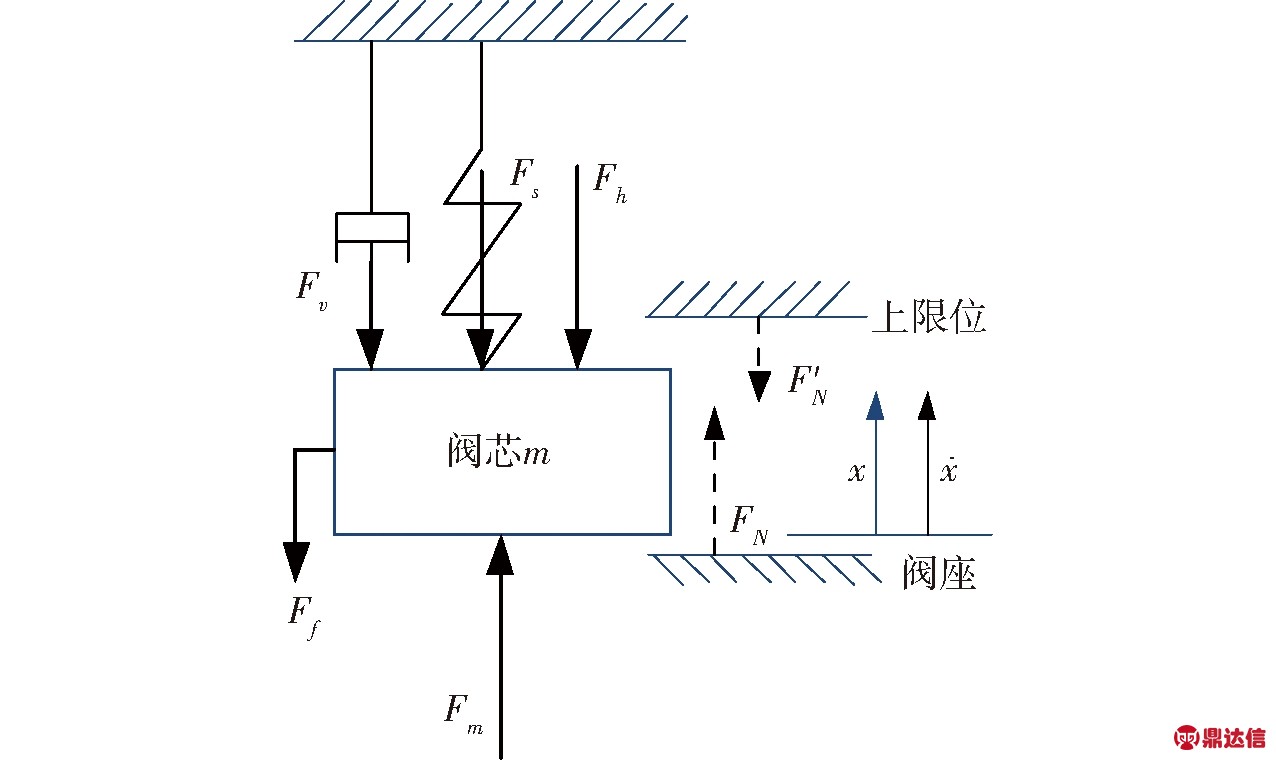
图1 电磁阀阀芯受力分析
Fig.1 Analysis on force of spool
根据阀芯受力有关系[18-20]
(1)
式中 m——阀芯质量 x——阀芯位移
由于弹簧力、摩擦力、阻尼力与液压力相比,数量级较小,因而电磁力主要用于克服液压力。其中电磁力与阀芯的位移和电流成正比,液压力与阀口两端压力和阀芯有效受力面积成正比。
通过阀芯受力分析可知,阀芯的位移以及位移变化速率的大小受电流和阀口压差等因素的综合影响,并影响电磁阀的响应特性。
2 电磁阀液压响应特性分析
为了获得电磁阀阶梯减压控制的控制变量,需要对电磁阀的液压响应特性进行试验研究[21-22],为此搭建了ESC液压调节单元的试验台架。
取占空比为D,频率为f,通过给定不同的占空比和频率,在同一个初始轮缸压力下,进行轮缸的减压试验,如图2所示。

图2 电磁阀的液压响应曲线
Fig.2 Hydraulic response curves of solenoid valve
由图2可知,控制频率和占空比对于轮缸压力变化率有较大影响,以D=0.01,f=25 Hz与D=0.04,f=10 Hz轮缸压力曲线变化为例,虽然一个周期内电磁阀供电时间相同,但轮缸压力变化速率不同。具体原因可由图3分析得到,这主要是由电磁阀的开启与关闭延迟时间导致的。
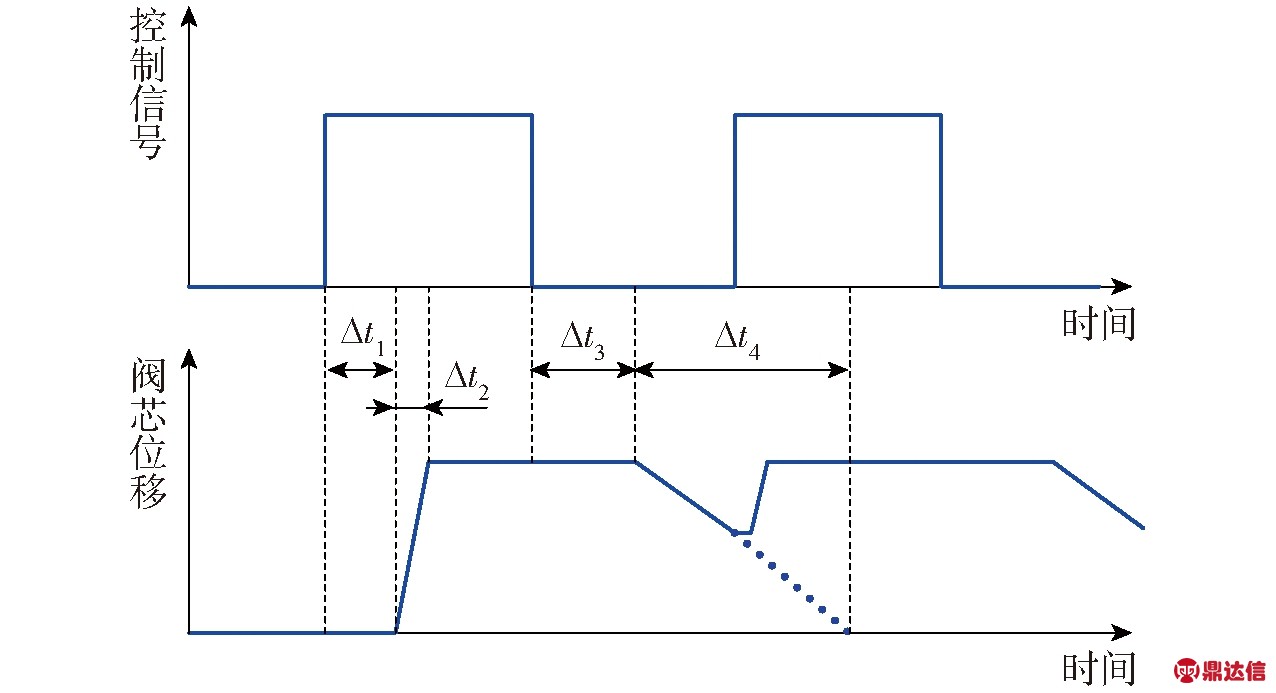
图3 阀芯运动响应示意图
Fig.3 Schematic diagram of spool movement response
电磁阀开启延迟时间为
ton=Δt1+Δt2
(2)
式中 Δt1——阀芯开启滞后时间
Δt2——阀芯开启运动时间
电磁阀关闭延迟时间为
toff=Δt3+Δt4
(3)
式中 Δt3——阀芯关闭滞后时间
Δt4——阀芯关闭运动时间
以关闭延迟时间为例,当电磁阀关闭时间Toff≥toff时,电磁阀的阀芯位移可恢复至初始状态,电磁阀完全关闭,此时轮缸压力表现出间断性变化,压力变化率小;当电磁阀的关闭时间0<Toff<toff时,电磁阀的阀芯位移还未达到初始状态就要继续开启,电磁阀并未完全关闭,此时轮缸压力连续变化,压力变化率大。
根据上述分析,对于电磁阀的阶梯控制,可通过调节电磁阀控制信号状态持续时间,并考虑电磁阀开启和关闭过程延迟时间的影响,实现轮缸压力变化率的调节。
3 电磁阀阶梯减压控制
阶梯减压控制需要确定两个关键控制量,即压力控制状态和状态持续时间。
3.1 压力控制状态
压力控制状态判断用于实现轮缸减压和保压过程的切换,在进行压力控制状态判断时需要考虑到控制状态的切换频率,由于电磁阀主要控制元件为MOSFET,在频繁的开关过程中,容易产生较大的驱动端热负荷,严重影响到电磁阀的使用寿命,本文将选取压力开关延迟控制方法,以便减小控制状态的切换次数,如图4所示。

图4 压力控制状态切换
Fig.4 State switch of pressure control states
Δp为压力偏差,是制动系统实际压力与目标压力之间的差值,Thd_dec为保压至减压过程的切换门限,门限值的选取需要考虑压力的波动和电磁阀开闭时间引起的压力变化。
3.2 状态持续时间
在状态持续时间内,阀口处于完全开启状态,压力变化速率将以当前状态的最大速率进行变化,同时由于阀口的开启与关闭过程中存在延迟现象,容易导致出现压力超调现象,因而在状态持续时间的确定中,当前状态的压力变化速率和开关延迟现象都需要考虑,状态持续时间为
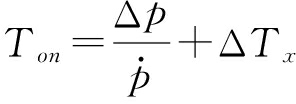
(4)
其中
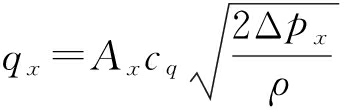
(5)
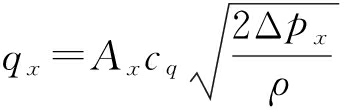
(6)
式中 Ton——状态持续时间
当前状态的压力变化率
ΔTx——电磁阀开启和关闭过程延迟时间
cq——流量系数
ρ——制动液密度 Ax——流通面积
Δpx——阀口工作压力
通过轮缸PV特性转换得到。
联立式(5)、(6),可得

(7)
式(7)中,其他参数可通过电磁阀体参数、传感器信号、轮缸特性得到,而阀口流量系数cq无法确定,成为压力变化率确定的关键,可通过试验标定的方法得到。
在电磁阀开启与关闭过程中,由于电流响应延迟和阀芯位移惯性,导致阀口不能及时地开启与关闭,其间会导致液压响应的延迟,如图5所示。
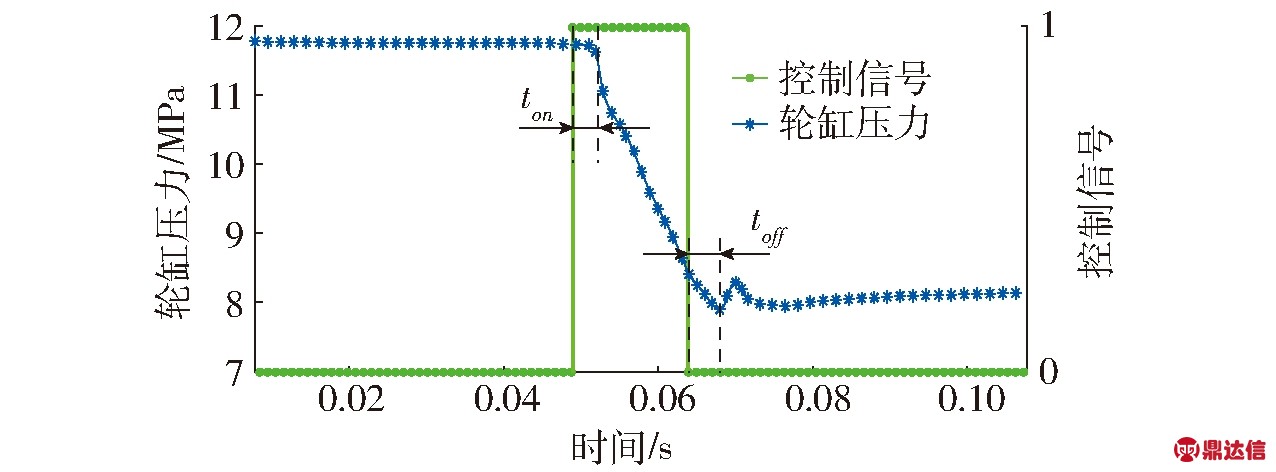
图5 控制信号下轮缸压力变化
Fig.5 Wheel cylinder pressure changes under control signal
在减压过程中,开启延迟时间内轮缸压力并没有进入减压阶段,关闭延迟时间内轮缸压力依然处于减压过程中,因而需要确定这两个延迟时间常数,从而修正状态持续的时间。
在电磁阀开启和关闭过程延迟时间ΔTx计算中,电磁阀前一周期工作状态对其影响较大,若电磁阀前一周期处于关闭状态,则ΔTx=ton-toff;若电磁阀前一周期处于开启状态,则ΔTx=-toff。可利用台架试验对ton和toff两个时间常数进行试验标定。
4 控制参数标定
根据电磁阀阶梯减压控制分析可知,需要标定阀口流量系数cq和电磁阀开启延迟时间ton与关闭延迟时间toff,最终得到精确的状态持续时间Ton。
4.1 阀口流量系数cq
阀口流量系数cq与液流雷诺数有关,当雷诺数Re>105时,阀口流量系数可认为是一个常数,通过试验标定的方法可以确定[23],如图6所示,图中pwhl为轮缸压力,pout为低压蓄能器压力, dx为阀口流通直径,u为输入变量。利用实际压力曲线的变化率与估算压力曲线的变化率进行标定,通过修正cq,可得到理想的结果。
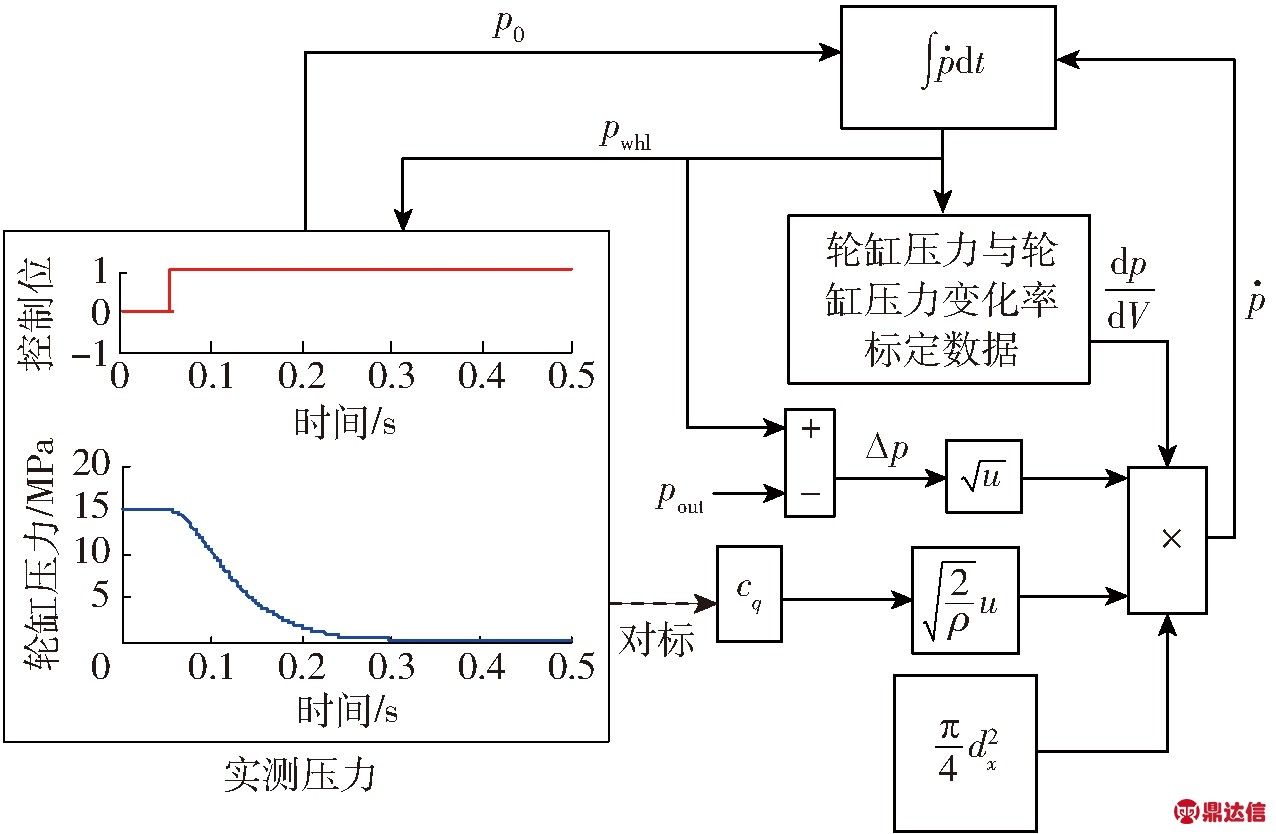
图6 阀口流量系数标定
Fig.6 Flow coefficient calibration of valve port
在进行阀口流量系数cq标定过程中,实际压力曲线与估算压力曲线可实时在线获得,利用图6所述方法,获取的实测轮缸压力,通过压力变化率的积分,得到轮缸的估算压力,利用轮缸的估算压力与实测压力的贴合程度选取合适的阀口流量系数cq。具体的标定结果如图7所示,通过修正cq,获取轮缸从15 MPa减压过程中实际压力曲线与估算压力曲线,相比cq选取0.6或者0.8,cq选取0.7时与实测值更加贴合,可将其作为阀口流量系数的标定值。
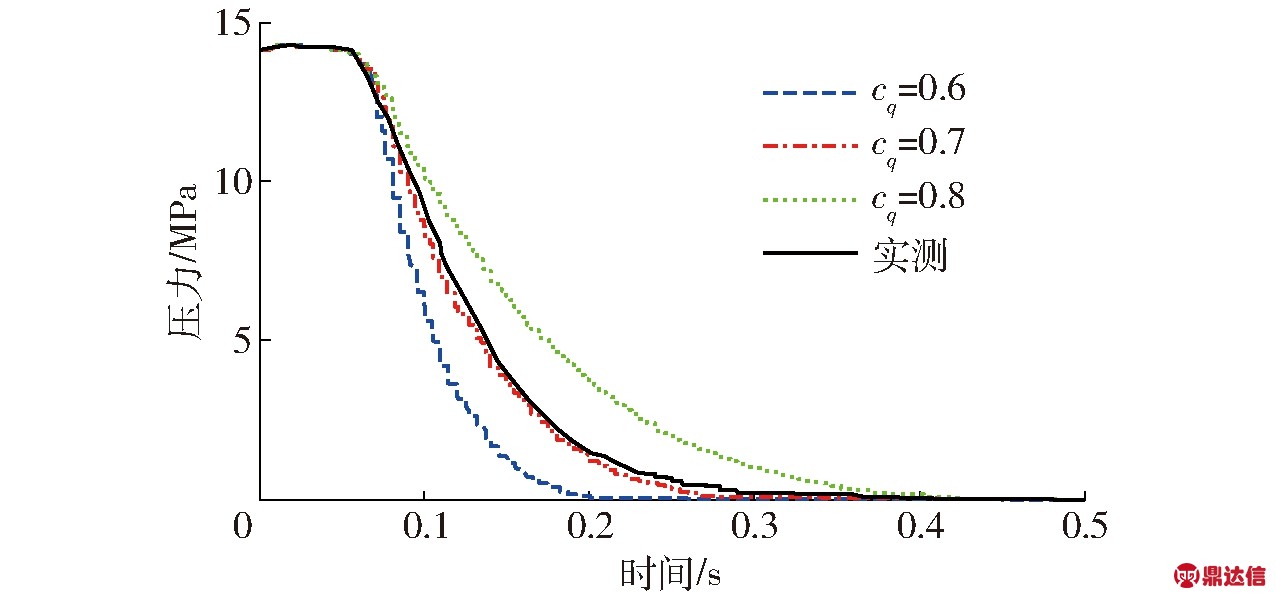
图7 不同流量系数下的压力估算曲线
Fig.7 Pressure estimation curves of different flow coefficients
4.2 电磁阀开启延迟时间ton与关闭延迟时间toff
由阀芯受力关系可知,电磁阀阀芯的运动受到阀口压差的影响,在不同的阀口压差下,电磁阀的开启与关闭时间不同,可通过给定不同阀口压差下驱动信号与轮缸压力变化之间的时间差求得。
由于电流响应延时和阀芯位移耗时使得常闭电磁阀打开与关闭过程存在延时,给定轮缸初始压力为12 MPa,电磁阀在给定的时间段内进行阶梯减压,如图8a所示,通过8个阶梯减压过程,实现了轮缸的减压。通过局部分析电磁阀阶梯减压过程,以第2个阶梯减压过程为例,如图8b所示,可以看出,在电磁阀压差为7.055 MPa时,电磁阀开启时间为4 ms,在电磁阀压差为4.683 MPa时,电磁阀关闭时间为3 ms。
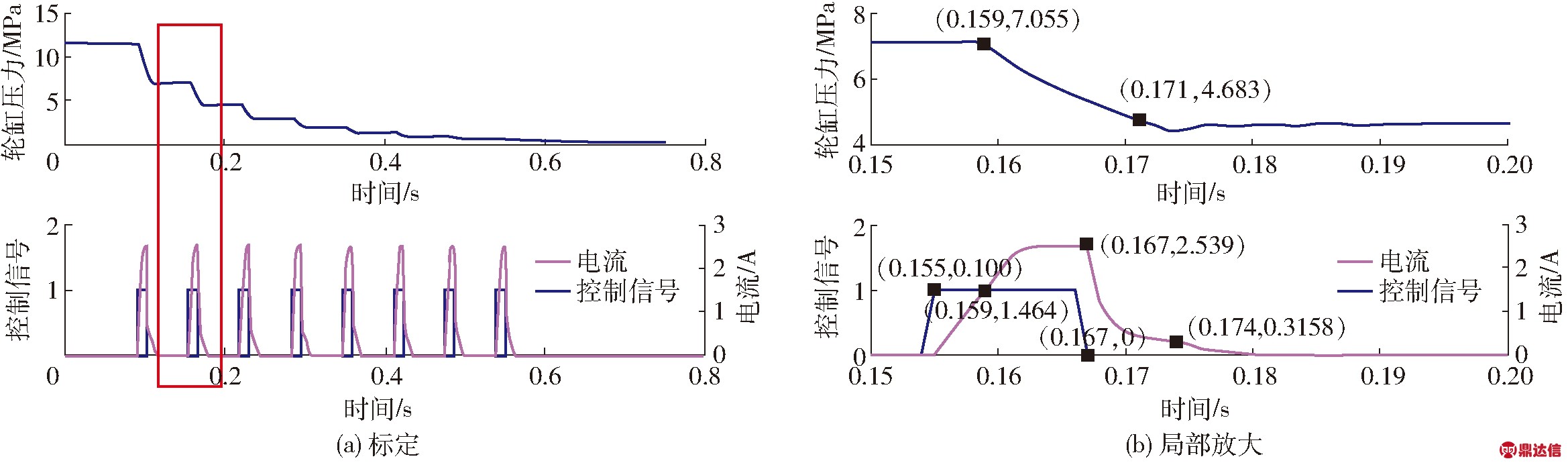
图8 电磁阀阶梯减压过程
Fig.8 Step pressure control process
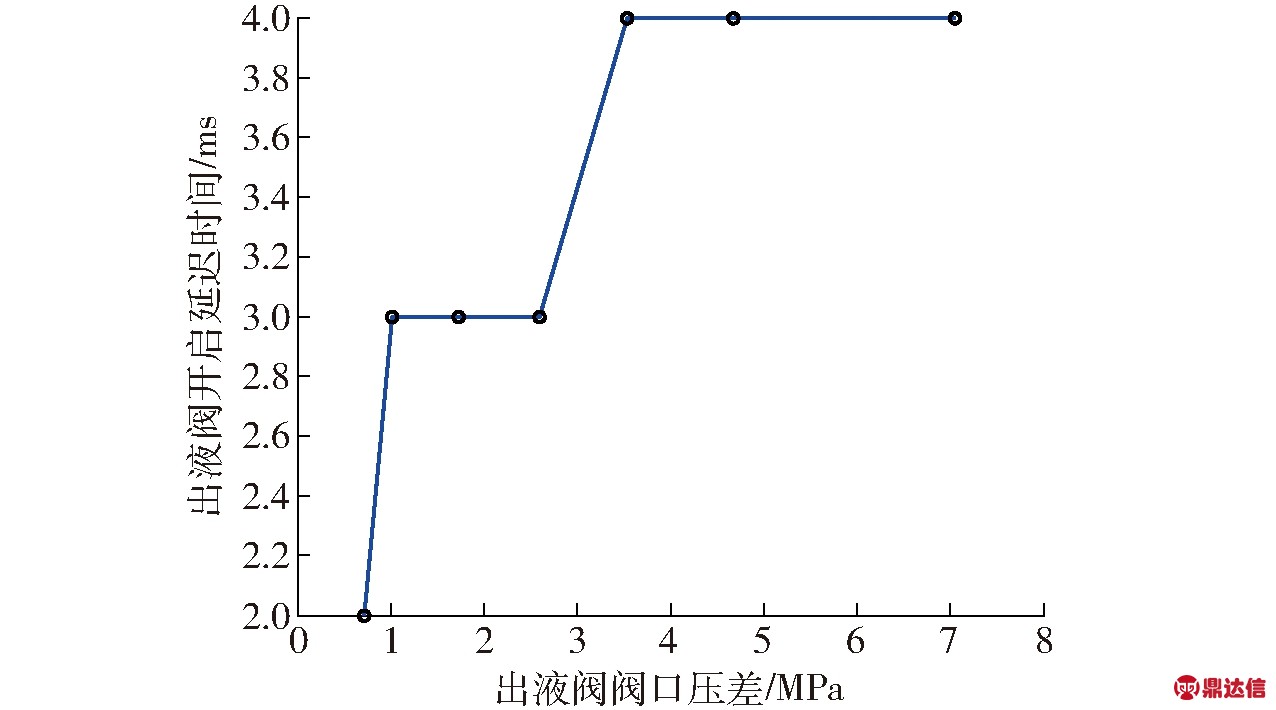
图9 电磁阀阀口压差与开启延迟时间
Fig.9 Relationship of pressure drop and opening delay time
统计电磁阀不同压差条件下的开启延迟时间和关闭延迟时间,如图9、10所示。对于开启延迟时间,电磁力需要克服阀口液压力,延迟时间会随着阀口压差的增大而逐渐增大(图9);对于关闭延迟时间,液压力促使阀口回到初始状态,延迟时间随阀口压差的增大而逐渐降低(图10)。因而在进行电磁阀开启与关闭过程延迟时间获取时,可利用当前阀口压差状态,通过插值法获取相应状态下的延迟时间。
5 试验验证
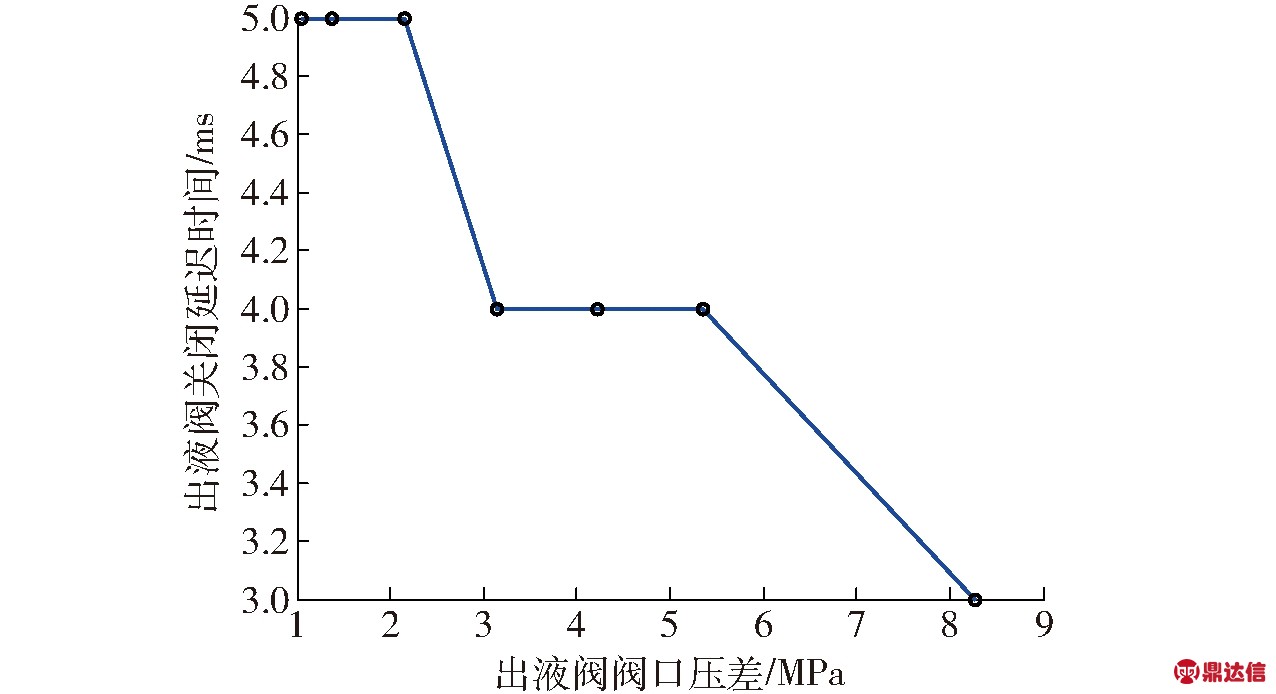
图10 电磁阀阀口压差与关闭延迟时间
Fig.10 Relationship of pressure drop and closing delay time
利用实车液压单元和回路,将MicroAutobox作为控制单元,驱动单元采用Rapid Prototype实现电磁阀开闭时间控制,搭建了液压制动系统的半实物仿真试验台架,试验台架如图11所示,测试了轮缸压力对于不同压力变化率的跟随情况。
在阶梯减压试验过程中,轮缸初始压力8 MPa左右,让轮缸压力分别跟随3、6、12 MPa/s的减压速率进行减压,试验结果如图12所示。
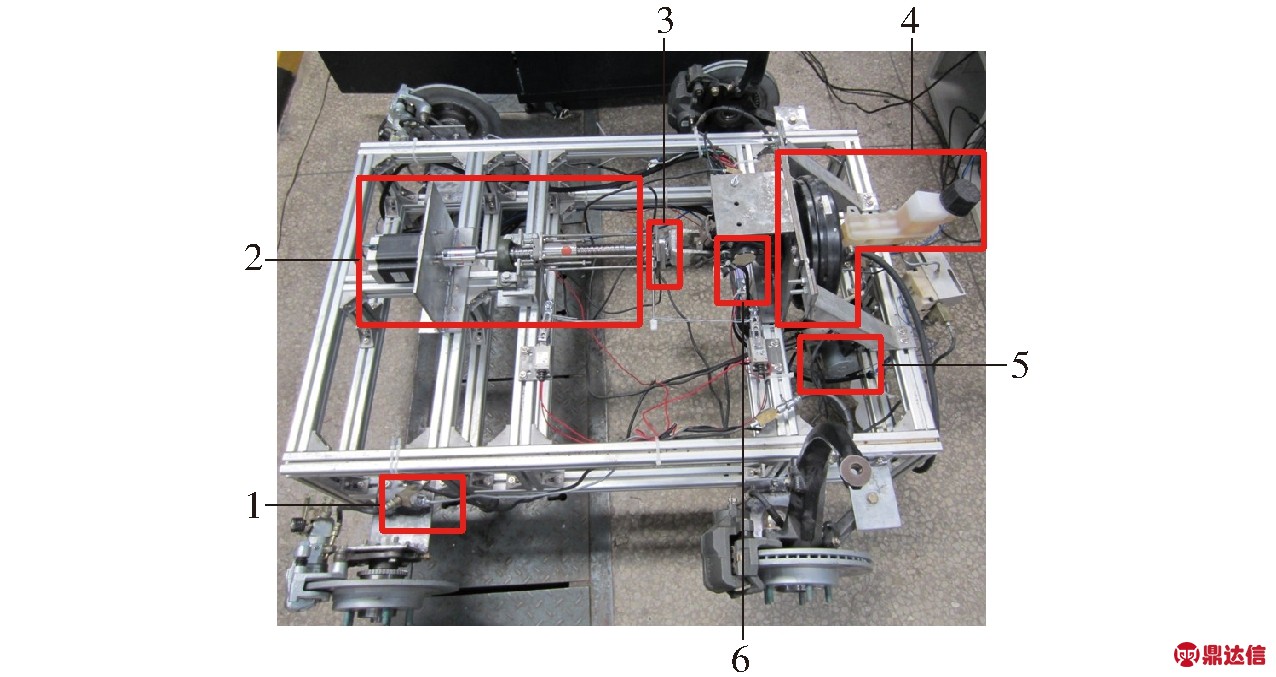
图11 试验台架
Fig.11 Test bench
1.压力传感器 2.制动实施装置 3.踏板力传感器 4.制动操纵机构 5.ESC 6.位移传感器
在不同的减压速率需求下,轮缸压力都可以很好的阶梯跟随目标压力的需求,试验偏差都可以维持在1 MPa以内。同时在相同的减压区间变化时,随着减压速率的增大,电磁阀开启次数变少,开启时间增长,减压速率的变化越接近电磁阀口的最大减压速率,控制越精确。
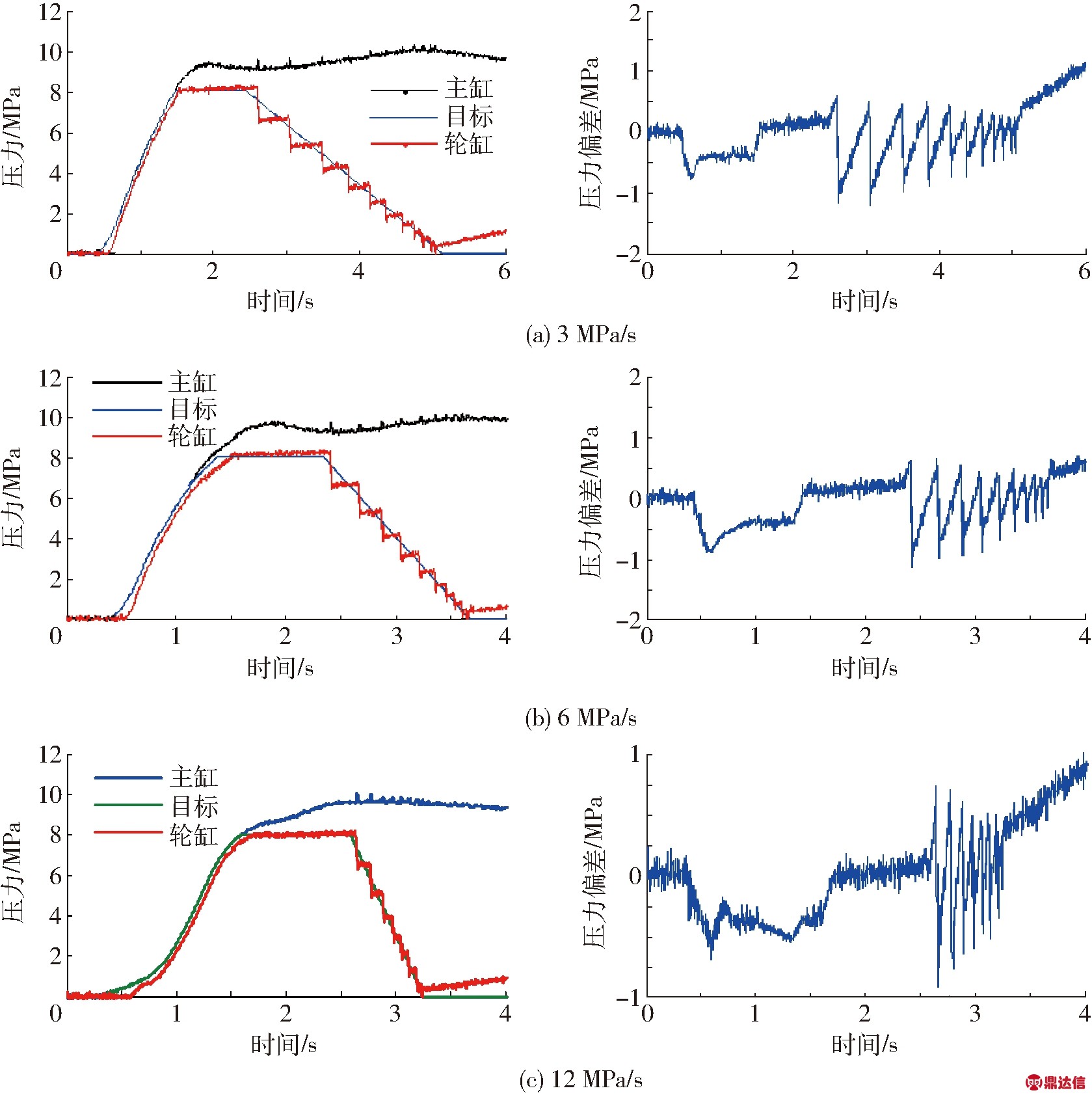
图12 不同减压速率下的轮缸压力变化曲线和压力偏差
Fig.12 Pressure change curves of wheel cylinder and pressure deviation
6 结论
(1) 提出了在阶梯减压过程中,可通过控制压力控制状态和状态持续时间实现。在状态持续时间计算中,考虑到了当前状态的压力变化速率和开关延迟现象的影响,使得阶梯压力控制效果更加精确。
(2) 给出了阀口的流量系数cq、电磁阀开启延迟时间ton、关闭延迟时间toff的标定方法,为阶梯压力控制参数的选取提供了试验依据。
(3) 利用台架试验进行了电磁阀不同减压速率下的压力变化控制,试验结果表明,该控制方法目标压力跟随性好,控制精度高。