摘 要:基于榆神矿区浅埋深、煤层特厚坚硬的赋存条件,针对超大采高综放开采首采工作面智能化开采所面临的难题,提出相应的解决对策,提高工作面自动化、智能化程度,减少工作面人员数量和劳动强度。讨论了超大采高综放工作面液压支架结构形式对智能化开采、支架-围岩“小结构”支护系统稳定性和顶煤冒放性的影响,认为两柱掩护式液压支架、整体式二级护帮板结构更适合超大采高综放工作面。针对顶煤冒放成拱问题,分析顶煤成拱形态和破拱措施,提出尾梁“小拱小摆、大拱大摆”的智能化摆动策略,提高顶煤冒放性和放煤效率。针对现阶段超大采高综放开采首采工作面顶煤冒放运移规律掌握不足、煤矸识别技术尚不成熟的情况,阐释了煤岩分界模糊段概念,将待放出顶煤分为纯煤段和煤矸分界模糊段,并提出纯煤段采用无需人工干预的智能化记忆放煤,煤矸分界模糊段采用人工干预反馈式放煤,在减少人员劳动量的同时保证顶煤采出率和降低含矸率。建立在线灰分检测智能评价和人工现场及时评价相结合的放煤效果综合评价系统,通过放煤键盘和反馈评价器及时、精准地控制放煤过程并给予反馈评价。针对采放不协调问题,提出和分析分区段成组放煤措施,提升放煤效率,促进采放协调。超大采高综放首采工作面智能化技术研究可为相似条件综放工作面提供参考和借鉴。
关键词:特厚煤层;坚硬煤层;超大采高;智能化开采
0 引 言
煤矿生产劳动强度高、工作环境恶劣、危险性高,将工人从艰苦的环境中解放出来、达到“无人则安”的自动化、智能化矿井始终是现代化煤矿发展的方向[1-3]。我国近年来已发展70多个不同程度的自动化采煤工作面,如黄陵一号煤矿、滨湖煤矿等薄及中厚煤层自动化综采工作面,转龙湾煤矿、红柳林煤矿等厚及特厚煤层自动化综采工作面,塔山煤矿、同忻煤矿等特厚煤层大采高自动化综放工作面。
在大采高智能综放开采和硬煤放顶煤开采方面,相关学者进行了大量研究,并尝试突破放煤过程中的煤矸识别问题。王国法等[4]分析和讨论了特厚煤层大采高综放自动化开采技术与装备;王家臣等[5]提出了顶煤冒放的BBR理论,分析煤岩分界面演化规律,通过采出率和含矸率评价顶煤冒放效果;马英[6-8]提出依据煤和矸石与支架尾梁碰撞时振动信号的不同来进行煤矸识别;马端志等[9]认为两柱式大采高强力放顶煤支架由于易实现自动化、智能化控制,将成为大采高自动化综放工作面的首选架型;苏林军等[10]讨论了放顶煤液压支架的创新与发展,并着重阐述的大采高放顶煤液压支架的关键技术;宋庆军等[11-12]提出并试验了基于振动和声波的多传感器信息融合方法来进行放煤过程中的煤矸识别;牛剑峰[13]阐述了自动放煤控制原理和自动放煤控制策略,开发了综放工作面自动化放煤系统;范志忠[14]介绍了自动化大采高综放工作面关键技术,认为自动化大采高综放工作面可实现采放平行作业,并指出了当前存在的问题;任怀伟等[15]对8 m超大采高工作面智能开采技术及智能化围岩控制关键技术给出了具体构建,包含支架支护质量监测和智能耦合控制系统、采煤机记忆截割与精准定位、刮板输送机负荷反馈和煤流检测系统、可视化监控和“三机”(采煤机、液压支架和刮板输送机)协同智能控制技术。
但目前超大采高智能化放顶煤工作面开采尚无成熟经验,笔者在超大采高智能化开采的基础上[15-18],分析特厚坚硬煤层超大采高自动化综放开采存在的煤矸识别、采放不协调等问题,提出相应对策,建立综合反馈评价体系,在保证采出率和煤质的前提下尽可能地提高自动化开采程度。
1 超大采高综放采煤法及液压支架
1.1 超大采高综采放顶煤采煤法
超大采高综采放顶煤采煤法将超大采高综采采煤法(机采割煤高度6.0 m及以上)与综采放顶煤采煤法相结合,是针对榆神矿区埋深较浅、结构简单、坚硬且整体性较强的特厚煤层顶煤悬顶距离长、冒落块度大等原因造成顶煤冒放性差问题,提出通过进一步增大采高提高资源采出率和开采效率的策略。增大采高不仅能通过“多割少放”提高开采效率、促进采放协调,而且可以增强工作面矿压显现程度、增大顶煤冒放空间和放煤口尺寸,提升煤流速度和流畅度,提高顶煤的破碎程度与冒放性。另一方面,支架结构尺寸的增大可提高工作面整体设备尺寸、配套能力和可靠性,如采煤机功率和前、后刮板输送机的槽宽、运量和功率。由4、5、6 m机采割煤高度的有限差分法数值模拟结果(图1、图2)可知:顶板下沉量、工作面压力和塑性区范围随机采割煤高度增加而增大,顶煤变形破坏区和破碎程度增大;采高对超前支承压力集中区范围和应力峰值影响较为显著,应力峰值由41.8 MPa增加到43.2 MPa,应力峰值集中区范围增大约2倍,且峰值应力范围在顶煤中,有利于顶煤的破碎。此外,超大采高工作面在放煤口尺寸、工作阻力、顶煤回采区等因素上也具有较大优越性[19-20]。
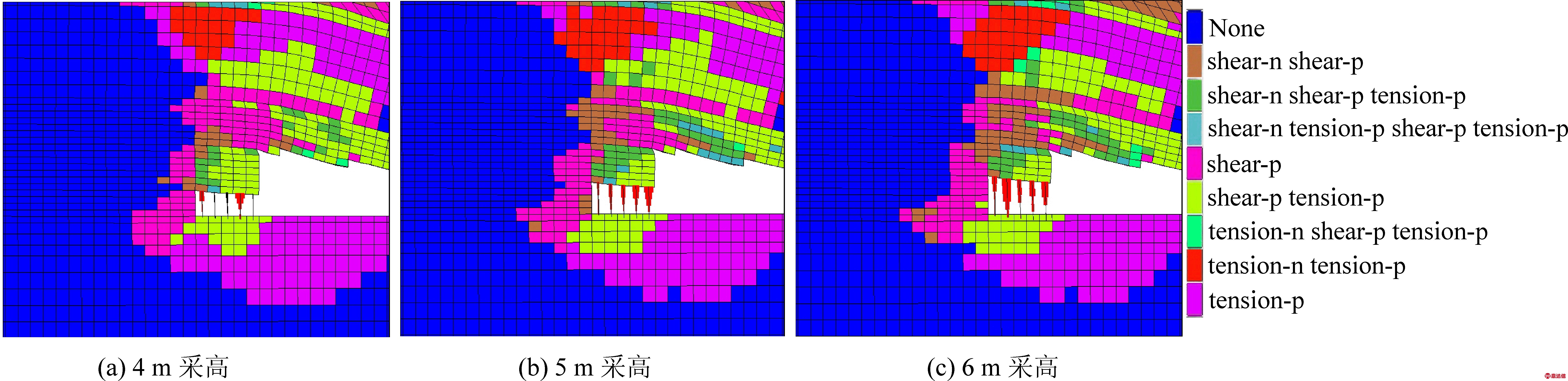
图1 采高与围岩塑性区关系
Fig.1 Relationship between cutting height and plastic zone of surrounding rock
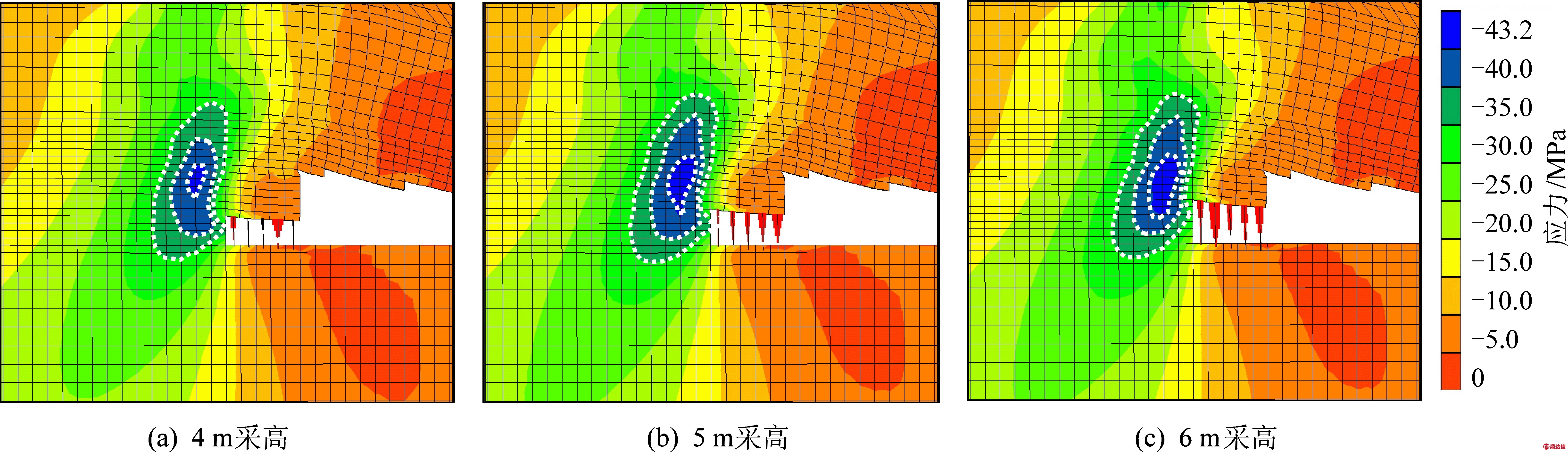
图2 割煤高度对围岩垂直应力分布影响云图
Fig.2 Influence of cutting height on vertical stress distribution nephogram of surrounding rock
目前,超大采高一次采全高工作面已能够实现单机设备自动化、智能化控制和设备间智能化协调联动,超大采高综放工作面实现自动化、智能化生产的关键是实现自动化放煤。而当前智能化煤矸识别技术尚不成熟,可靠性有待提高,利用现有煤岩识别技术进行完全智能化、无人化放煤难度大、准确率低。此外,顶煤在冒放过程中,将对支架-围岩“小结构”系统稳定性形成动态扰动,因而超大采高综放工作面煤壁片帮和端面顶煤冒顶问题仍是工作面稳定性控制的重点。
1.2 超大采高放顶煤液压支架
放顶煤液压支架除具有支撑顶板和煤壁、维护支架-围岩“小结构”支护系统稳定性外,还具有推移前部刮板输送机和拉移后部刮板输送机功能。因此,液压支架自身稳定性、适应性和耦合控制难易程度不仅决定了工作面支架-围岩“小结构”的稳定性和可靠性,还影响工作面各设备工序间良好的协同。针对超大采高工作面围岩稳定性降低,片帮、冒顶危险性大等问题,借鉴超大采高工作面智能化系统成熟的控制经验,通过液压支架-围岩智能耦合控制系统可及时有效地维护煤壁和顶板稳定。超大采高综采放顶煤工艺由于割煤高度增大、一次采出厚度大(割煤+放煤),对支架-围岩“小结构”支护系统强度、刚度和稳定性耦合具有更高的要求,既要保证支架前方煤壁和顶板结构的稳定性,又要对支架上方顶煤完整结构进行破碎,还要使支架后方的顶煤能够及时垮落并顺利放出,因此对支架结构、护帮板结构和尾梁结构的设计均有更高要求。
1.2.1 两柱强力放顶煤液压支架
目前,两柱强力放顶煤液压支架已在神树畔煤矿、双山煤矿和大唐龙王沟煤矿等矿井成功应用,支架最大支撑高度5.3 m,工作阻力达18 000 kN,克服了两柱掩护式放顶煤液压支架工作阻力低的缺点。由于两柱掩护式液压支架在智能控制方面具有良好的优越性,目前美国几乎所有长壁工作面均采用两柱掩护式液压支架[21],国内实现自动化、智能化开采的工作面多使用两柱掩护式液压支架,且超大采高(割煤高度6 m以上)工作面多使用两柱掩护式液压支架。两柱掩护式液压支架具有以下优点:①支架前端支顶力大、支护效率高、控制煤壁片帮和架前冒顶能力强;②顶梁位态调整幅度大、适应外载变化和自身调节能力强,适应围岩能力强;③结构简单、单排立柱易实现自动化、智能化控制,可建立保持支架顶梁平直的立柱与平衡千斤顶关系,根据围岩情况及时进行自适应调整[22]。因此,超大采高智能化放顶煤工作面宜选两柱掩护式超大采高放顶煤液压支架。另外,支架结构设计需要将智能化控制考虑进去,通过支架结构优化使智能化控制简单、方便、稳定性强,使支架结构与控制系统相适应,提高支架的可控性。
1.2.2 液压支架整体式二级护帮板结构
超大采高开采情况下,由于采高大、梁端距大,造成工作面容易发生片帮和冒顶,而结构和参数合理的护帮机构可及时有效地维护煤壁稳定,防止煤壁片帮伤人和损坏设备。根据8.2 m超大采高工作面生产经验,由于煤层整体性强、煤体较硬,煤壁稳定性较好,三级护帮机构对煤壁稳定性起到了较好的维护作用。开采过程发现,仅依靠二级护帮板而不打开三级护帮板的情况下,煤壁稳定性仍可得到较好的维护。另一方面,二级护帮板结构简单,伸出和收缩动作较快,工序流程少,能及时对煤壁进行维护,更有利于实现快速控制。故选用二级护帮板既可满足煤壁维护要求,又便于智能化控制的实现。
如图3所示,超大采高工作面液压支架护帮板与支架顶梁的连接方式主要有2种结构形式:整体式结构和分体式结构。整体式结构护帮板与伸缩梁铰接,护帮板运动从属于伸缩梁运动,整体式结构对煤壁的贴合效果较好,护帮、护顶效果较好,特别是能有效地维护煤壁上部区域,通过智能化控制还可实现伸缩梁和护帮板联动。
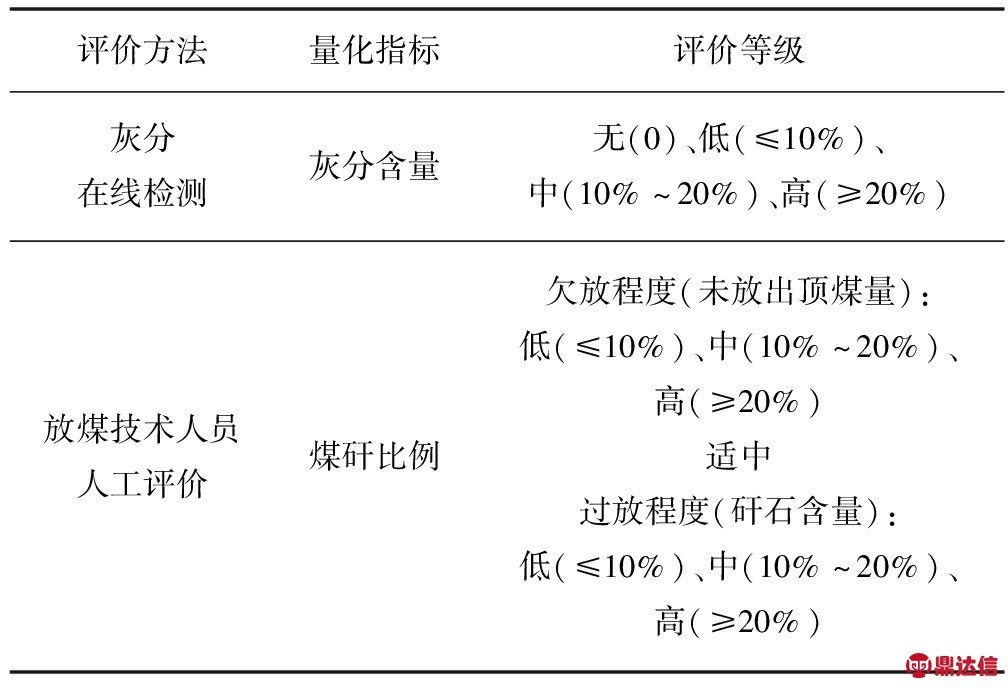
图3 不同结构形式护帮机构对比
Fig.3 Comparison of different structural forms of face sprag
此外,整体式由于悬挂于伸缩梁上,可以随着伸缩梁的伸出而移动,灵活性更强,适应性更强。如图4所示,煤壁发生不同程度片帮的情况下,伸缩梁和护帮板可以通过配合使得护帮板更贴合煤壁,因而在结构上能与煤壁达到更好的耦合状态。故护帮板采用二级整体式设计,能更加贴近煤壁,可与不同的煤壁结构形态相适应,耦合性更强,联动控制效果更优。
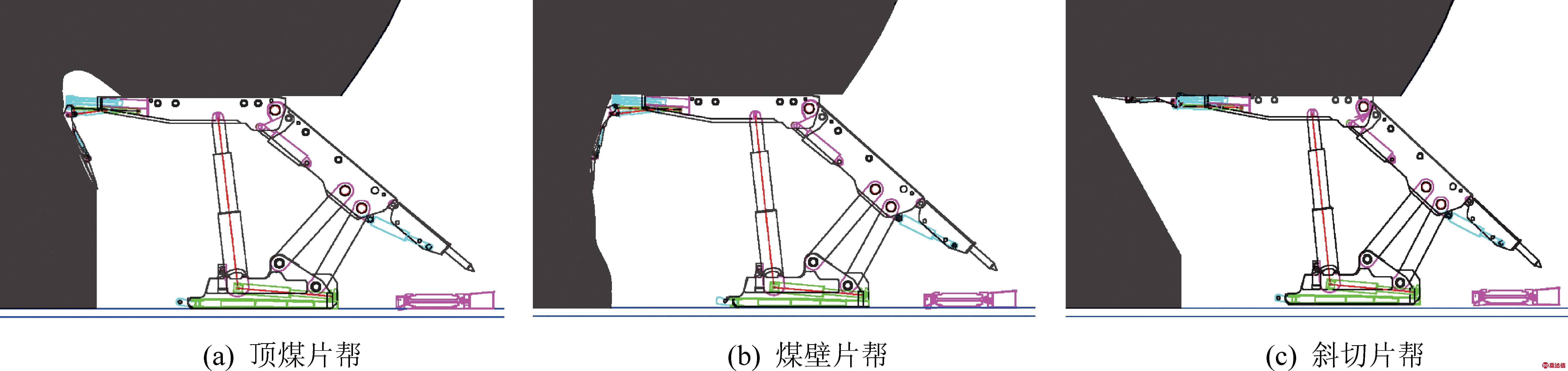
图4 不同片帮形式下护帮机构与煤壁结构耦合
Fig.4 Coupling of face sprag mechanism with different coal face structures
1.2.3 液压支架尾梁结构
支架尾梁结构即支架放煤机构,直接关系到支架放煤口大小和顶煤的成拱与破拱。如图5所示,与普通放顶煤液压支架相比,超大采高放顶煤液压支架后部有更大放煤空间,放煤机构尺寸更大,可选用更大缸径尾梁油缸,不仅有利于提高可放出顶煤最大块度和顶煤放出速度,还可对放煤口范围内顶煤形成的拱结构产生更大扰动,更容易破坏顶煤平衡拱基底。采用的小插板放煤机构结构简单,放煤过程只需尾梁摆动,可控性强,易实现智能化放煤控制。
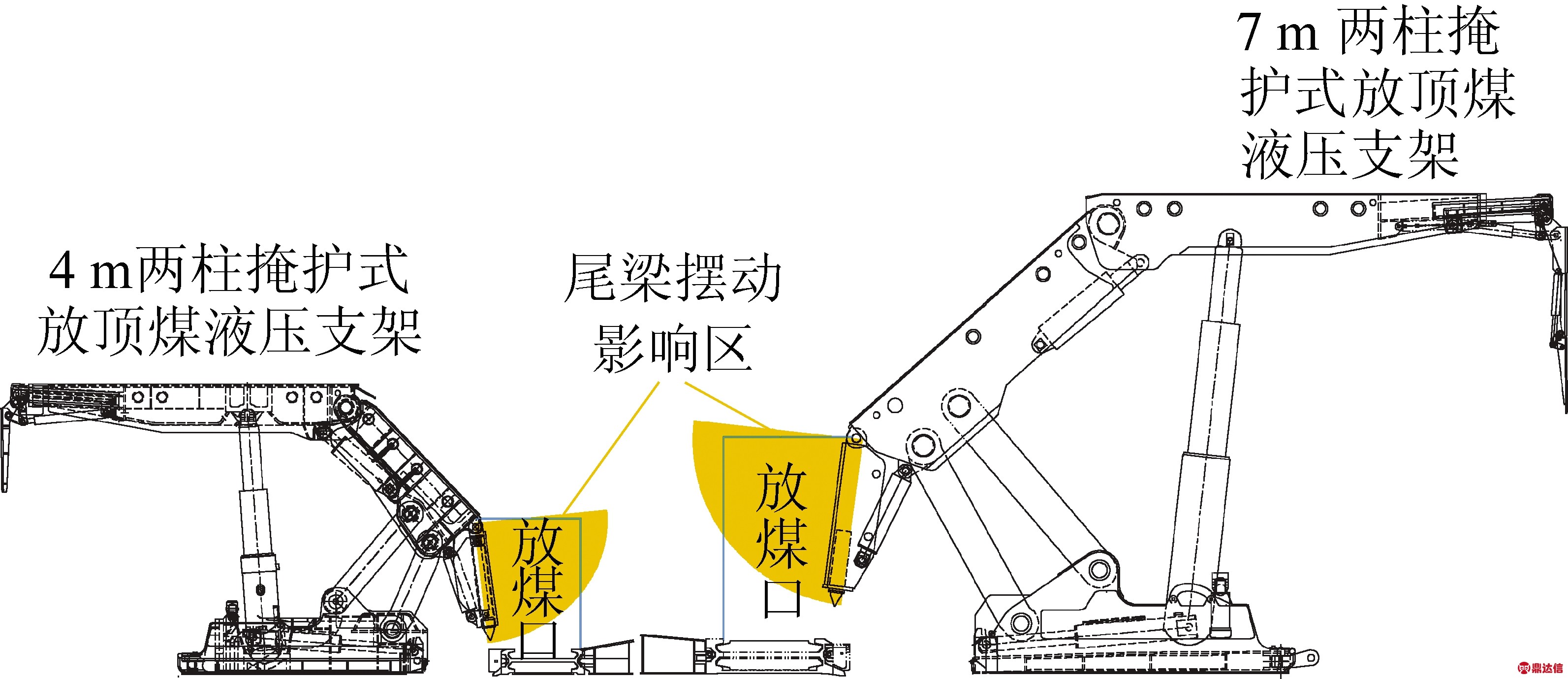
图5 不同结构高度液压支架放煤机构对比
Fig.5 Comparison of top-coal caving mechanism of hydraulic support with different structure height
2 自动化放煤技术
自动化放顶煤工作面割煤时无需对煤层顶板煤岩分界面进行识别,而将采煤机割煤时的煤岩识别技术难点转移到顶煤冒放阶段的煤矸识别上。由于工作面后方空间狭小、可见度低、煤矸成不规则块体复杂运动状态等因素,造成工作面后方煤矸识别难度增大。在未完全掌握顶煤实际冒放运移规律和煤矸识别技术不成熟的情况下,单纯地依赖记忆放煤和现有煤矸识别技术可能导致顶煤“欠放”或“过放”。特别是对于完整性较强的坚硬特厚煤层,由于顶煤悬顶长、冒落块度大、容易成拱等原因,还需通过尾梁摆动来破拱和破煤,进而提高放煤效率和顶煤采出率。对此,分析坚硬特厚煤层超大采高自动化放煤开采将遇到的问题,提出相应解决方法。
2.1 纯煤段自动化记忆放煤
煤矸识别是实现智能化高效综放的“卡脖子”技术环节,国家“十三五”重点研发计划项目“千万吨级特厚煤层智能化综放开采关键技术及示范”[23]将煤矸识别作为一个子课题进行重点研究,将煤矸冲击振动和高光谱的煤矸精准识别技术进行融合,以期通过“耳听、目测”实现放煤过程中煤矸的精准识别。成熟的煤矸识别技术是实现完全自动化、智能化放煤的关键,现有煤矸技术识别及智能化放煤技术在硬煤超大采高工作面的适用性仍需进一步研究,如张良等[24]提出“振动方式进行煤矸识别在顶煤硬度较大时区分度低,识别存在较大的困难”。鉴于此,笔者提出在生产初期采用前期记忆放煤与人工反馈式干预放煤相结合的放煤技术。
记忆放煤是通过支架智能放煤系统记录人工放煤控制方式,并结合放煤效果对放煤参数进行调整,从而形成相应的记忆放煤参数,后续放煤过程根据放煤参数通过智能控制系统指导放煤机构执行相应动作,实现放煤过程依据记忆参数进行无人工干预的自动化放煤方式。但工作面顶煤厚度等条件发生变化时,需要重新调整记忆放煤参数以适应外部条件的变化。
顶煤冒放的复杂性和差异性导致的煤矸分界面不清晰、不规律和不固定,因此考虑通过扩大煤矸分界面范围来定义煤矸分界模糊段以指导自动化放煤。如图6所示,假设煤矸有明确的分界面,则自煤矸分界面向纯煤区和纯矸区各延伸30%左右的顶煤放出量,从而保证煤矸分界模糊段外为纯煤或纯矸。纯煤段不存在煤矸识别问题,可实现完全的无人自动化放煤。
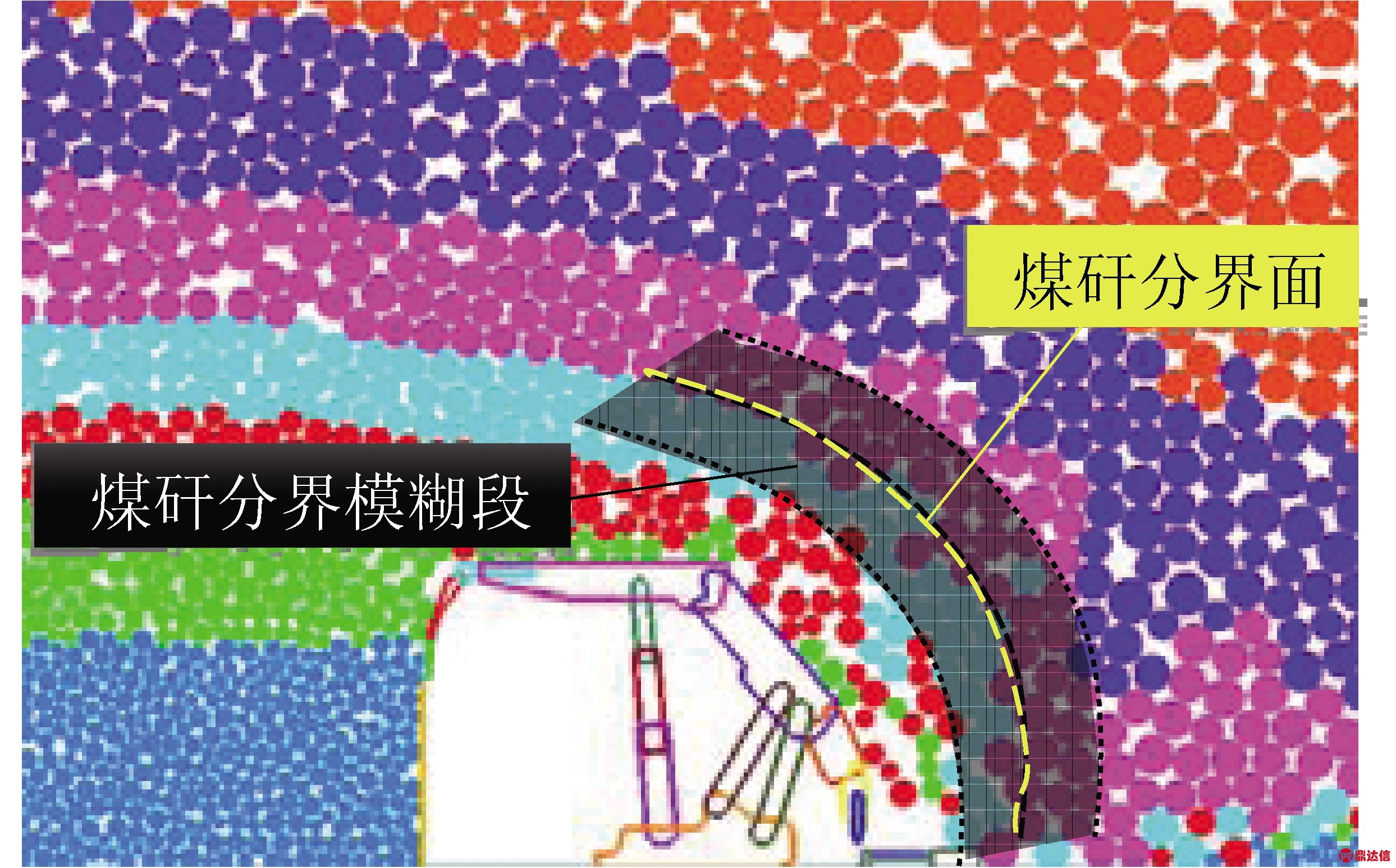
图6 煤矸分界模糊段示意
Fig.6 Schematic of coal-gangue demarcation fuzzy segment
2.2 煤矸分界模糊段人工反馈式干预放煤
人工反馈式干预放煤是在煤矸识别技术尚不成熟的阶段,根据顶煤冒放运移规律和煤矸分界面演化规律,采用多轮放煤方式,在前几轮纯煤段采用记忆放煤方式实现完全自动化、无人化放煤,而最后一轮煤矸分界模糊段采用人工放煤方式,达到既保证采出率又降低含矸率的目的。多轮放煤的优势在于顶煤能够较均匀地放出,维持较好的煤矸分界面。
如图7所示,顶煤在冒放过程中将经历纯煤段、煤矸混合模糊段和纯矸段,据此提出采用时序控制的纯煤段全自动化放煤和煤矸分界模糊段采用人工干预放煤的放煤策略。首先,技术人员采用多轮放煤方式进行多个循环的放煤,支架记忆放煤工序和放煤时间,在放煤过程中摸索出顶煤冒放运移规律和煤岩分界面演化规律,最终将放煤次数维持在2~4轮,并使前1~3轮放煤过程中能放出70%左右的纯煤,通过智能放煤系统记忆此工序参数。之后纯煤段即可采用此记忆程序进行无人化放煤。剩下的约30%的煤处于煤矸分界模糊段,且由于放煤过程中煤矸运移规律的复杂性,导致放煤规律呈现差异化。最后一轮仍继续采用自动化记忆放煤可能出现以下5种情况:①全部纯煤;②煤多矸少;③煤矸各半;④煤少矸多;⑤全部为矸。鉴于煤矸分界区具有较大的模糊性和随机性,故煤矸分界模糊段采用人工反馈式放煤方式来保证放煤质量,同时为下阶段智能化、无人化放煤积累大数据。
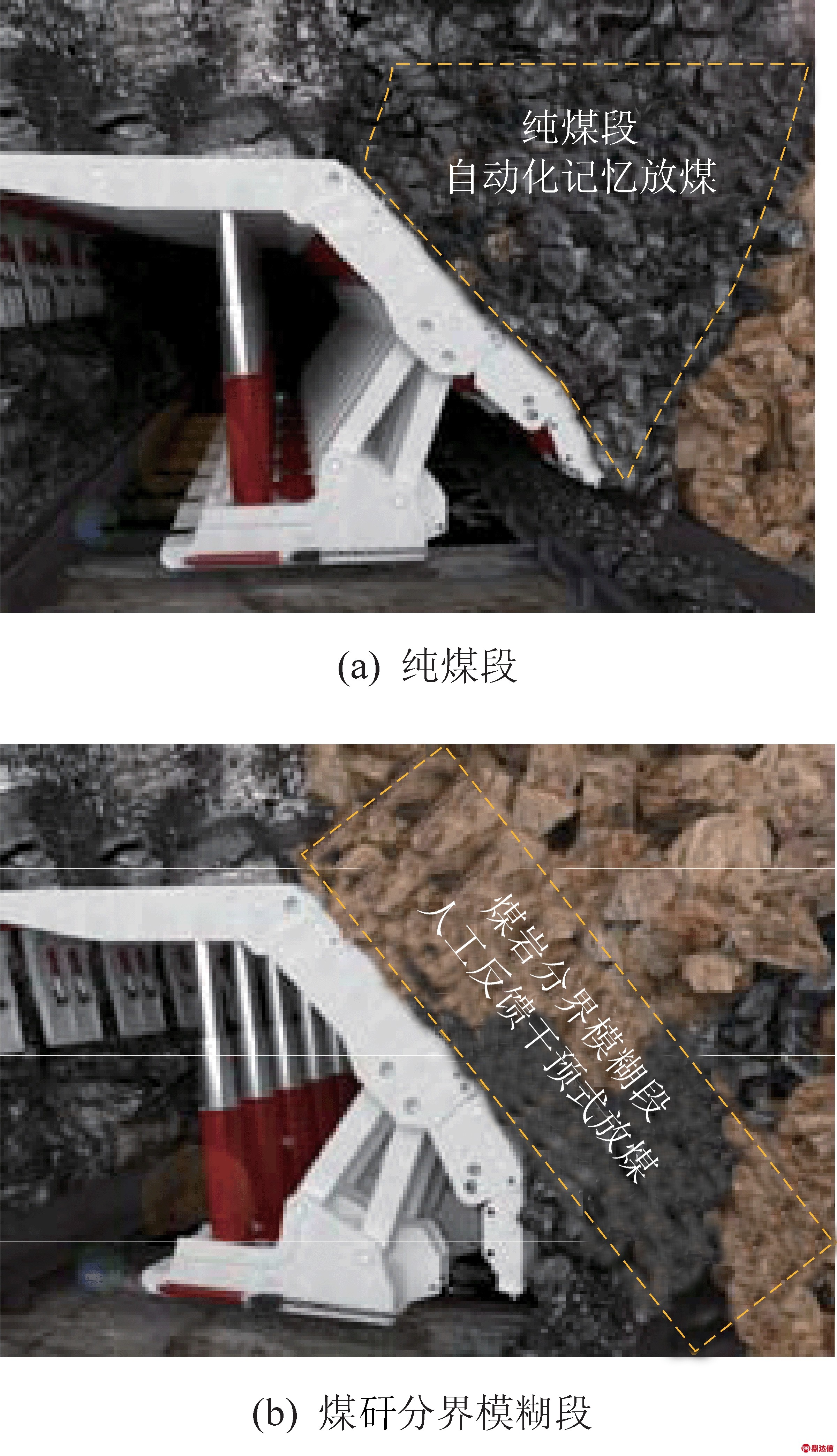
图7 记忆放煤与人工反馈式干预放煤
Fig.7 Memory coal drawing and manual feedback intervention coal drawing
2.3 智能化摆动尾梁
虽然增大采高可以增强顶煤冒放性,但由于坚硬顶煤完整性强和硬度大,顶煤冒放过程中仍难以避免大块煤的产生和成拱现象的出现。放煤过程中支架尾梁的摆动(图8)能起到破煤和破拱作用,且尾梁摆动范围越大扰动效果越好。对于尾梁摆动的频率可根据现场实际情况进行调节,通常下位顶煤块度较小而上位顶煤块度较大,因此摆动频率可逐渐增大。
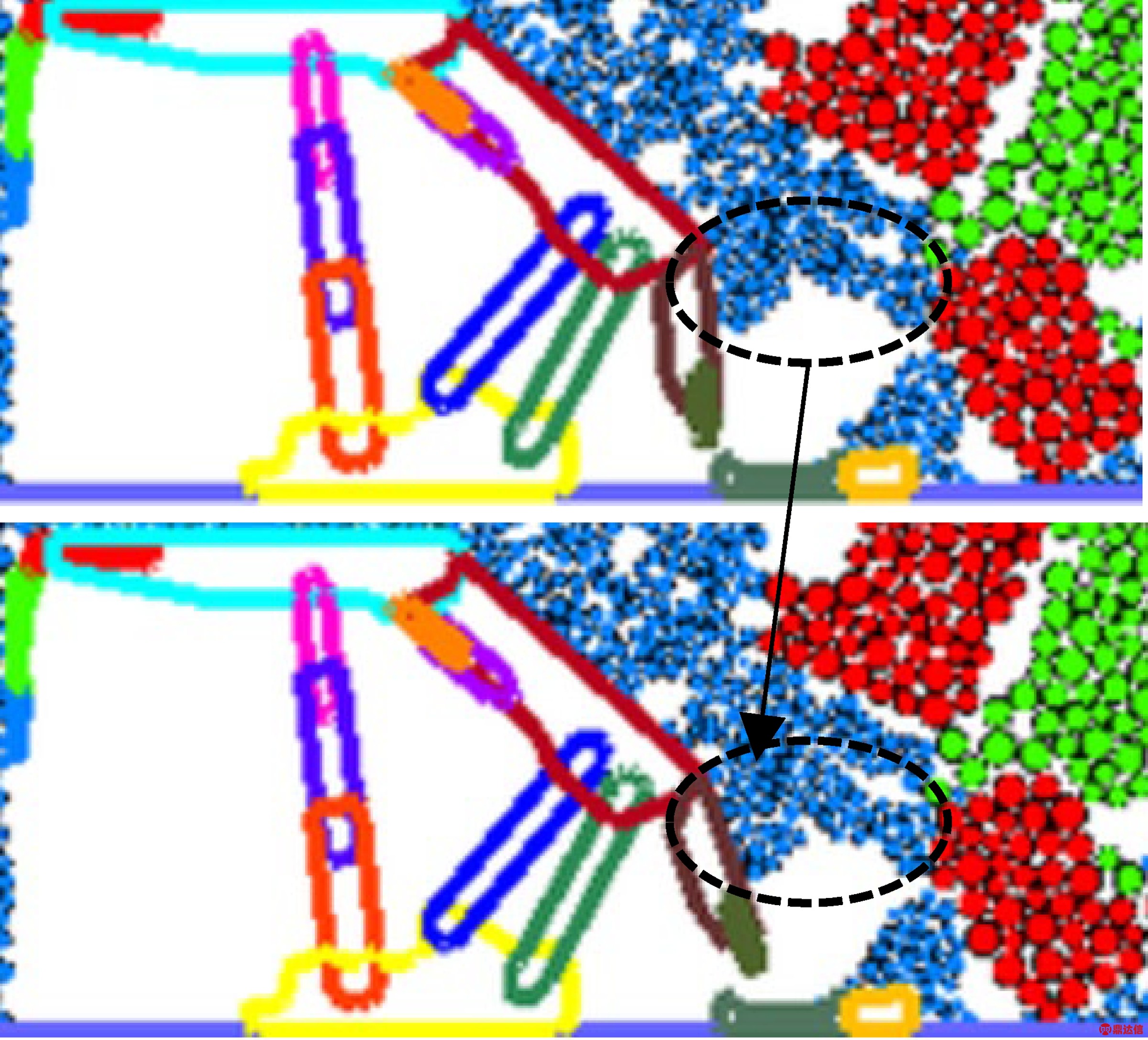
图8 支架尾梁摆动破拱示意
Fig.8 Schematic of rear canopy swing and arch breaking
对于小块散体拱而言,拱的稳定性差,尾梁小幅度的摆动即可实现破拱;而对于大块煤和矸石组成的较稳定拱而言,尾梁需要有较大的摆动和破煤能力才能破煤、破拱,即尾梁智能摆动采用“小拱小摆、大拱大摆”策略。对此,编写简单的放煤控制程序即可通过电液控系统实现,放煤过程中可设置如下尾梁摆动程序:尾梁向上摆动10°左右时,如果监测到尾梁受力较小,表明成拱的稳定性差或者未成拱,此时尾梁可以反向摆动;而如果尾梁受力较大,表明成拱稳定性强,此时需进一步增加尾梁的摆动幅度至30°~40°后再反向摆动。
2.4 智能化放煤系统
自动化放煤的更高级目标是实现智能化放煤,对于首采面来说,建立良好的记忆学习算法和大数据评价反馈体系是工作的重点,为之后实现完全智能化、无人化放煤奠定基础。高级智能化放煤控制技术需建立在完善的智能放煤算法、精准的智能感知系统和大数据评价反馈体系基础上,通过对放煤过程的自学习、自适应控制,使放煤过程中的感知、决策、执行、反馈等环节统一为闭环控制系统。如图9所示,通过基于放煤过程前期液压支架放煤机构状态感知,中期记忆放煤控制、后期的放煤效果感知反馈,实现放煤过程智能化控制。智能化放煤原理如图10所示。
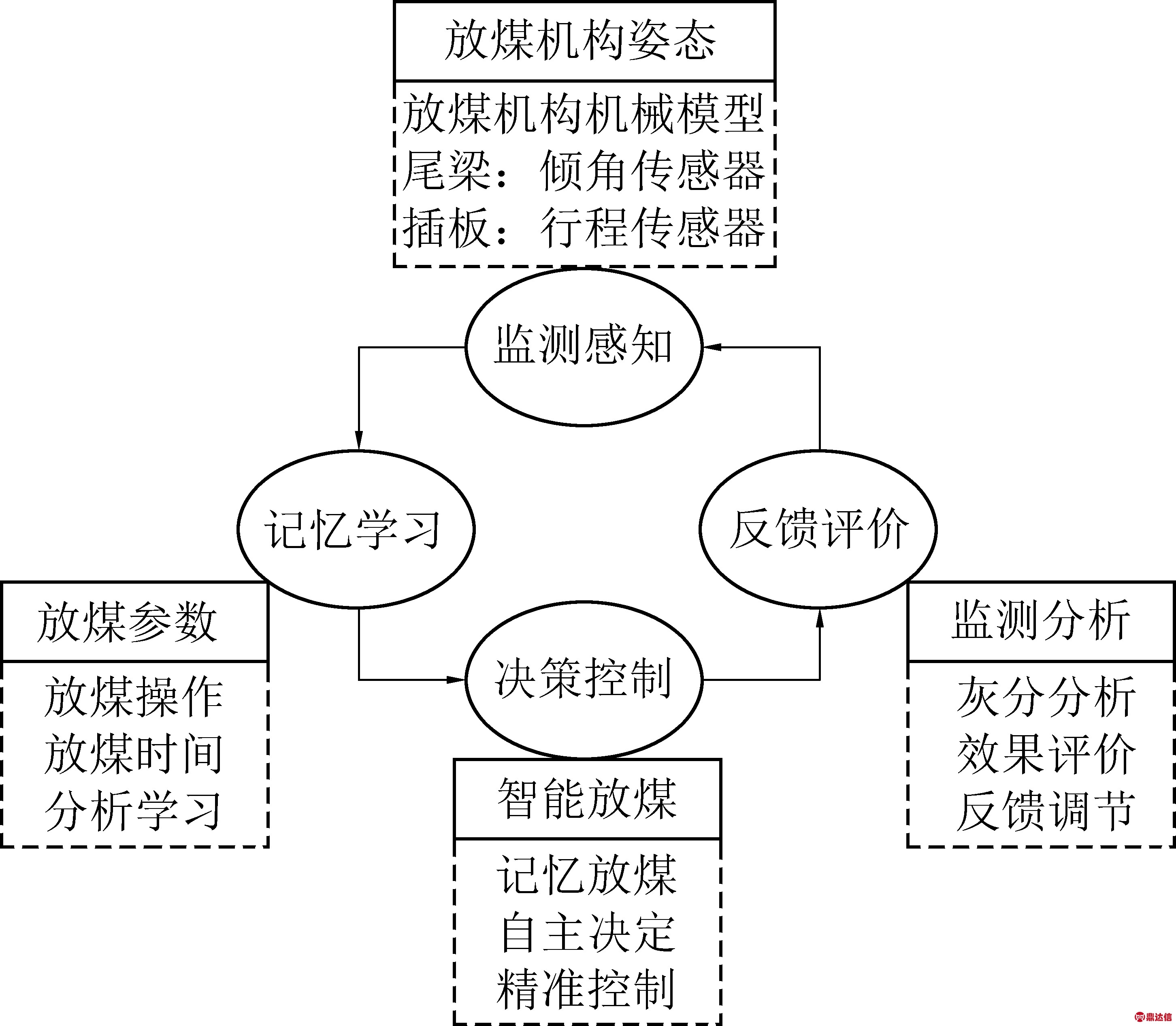
图9 智能化放煤原理
Fig.9 Intelligent top-coal caving principle
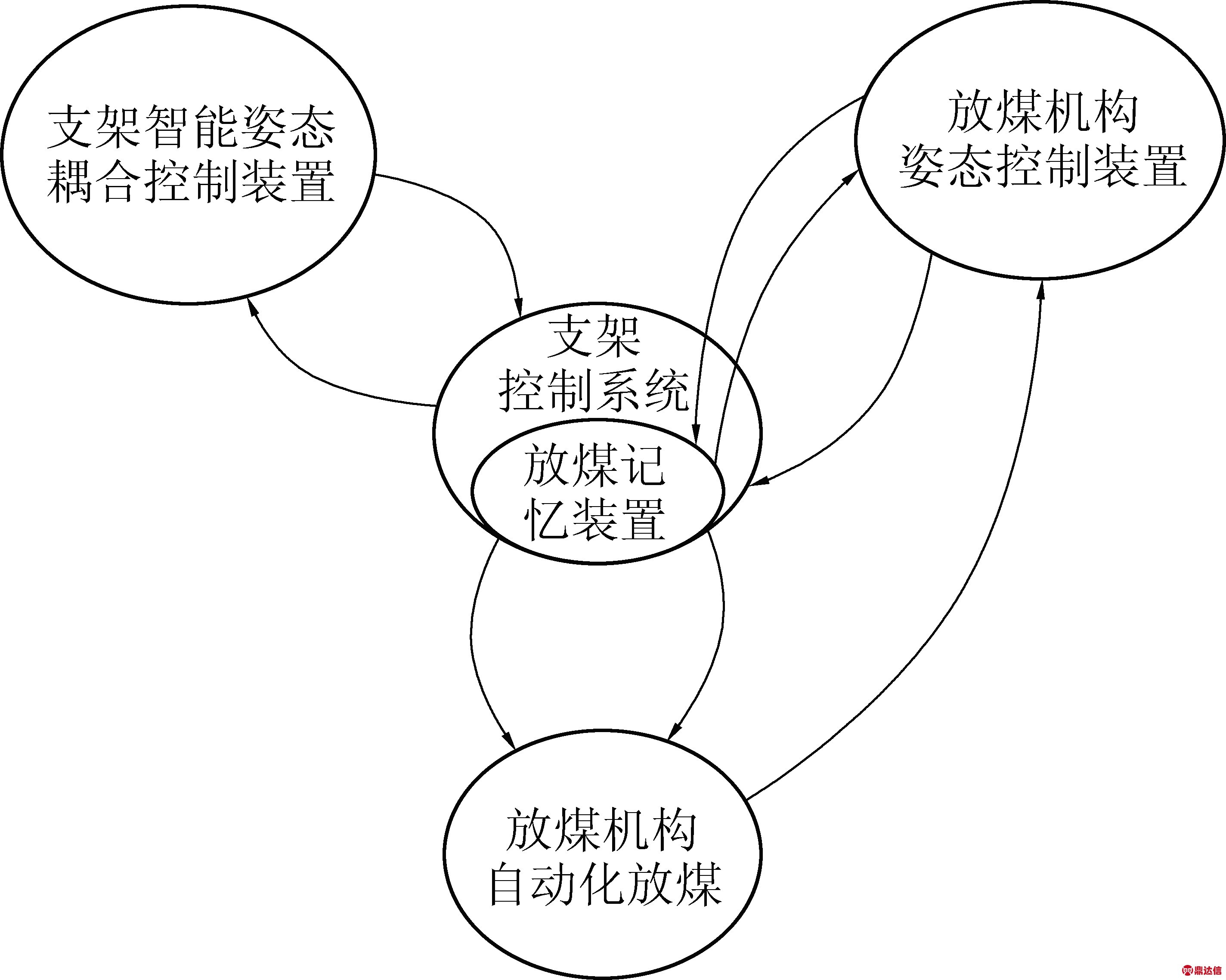
图10 智能化放煤原理
Fig.10 Principle of intelligent top-coal caving
3 放煤效果综合反馈评价系统
放煤效果综合评价见表1,根据评价等级进行相应量化处理并反馈给智能记忆放煤算法。
表1 放煤效果综合评价
Table 1 Comprehensive evaluation of drawing effect
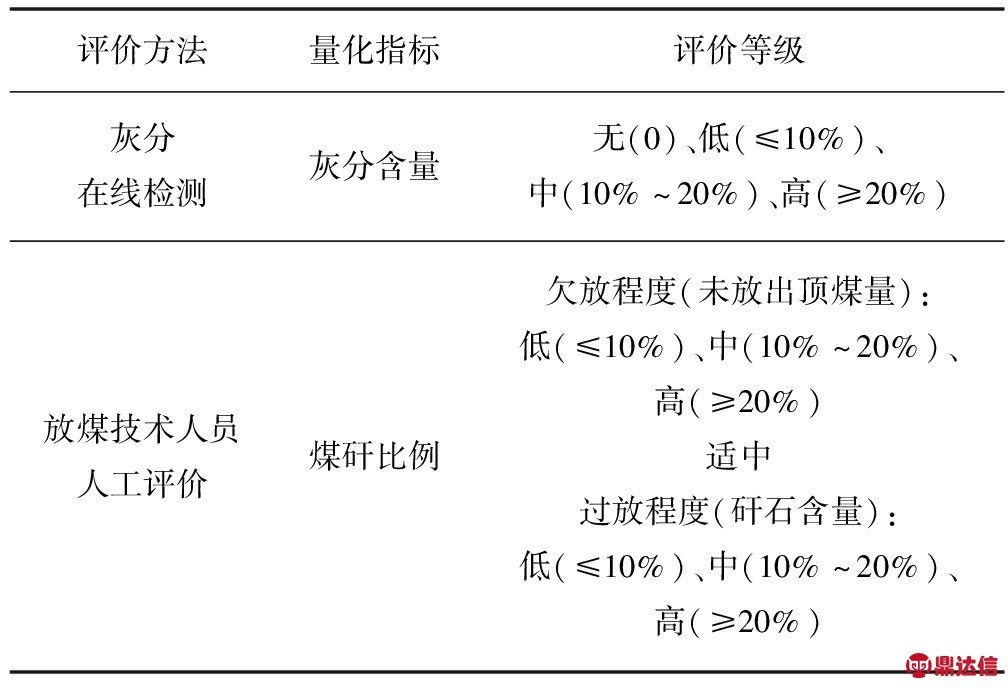
放煤效果综合评价包含2个部分:①灰分检测在线智能评价;②人工反馈式干预放煤与实时评价。每个放煤循环结束后需及时对放煤效果进行综合反馈评价,把放煤效果反馈给智能记忆放煤算法,通过算法对自动放煤程序进行优化。
3.1 灰分在线检测自动评价
在综放工作面支架后部放煤口布置灰分识别传感装置,用来进行煤矸灰分识别,通过灰分识别传感装置实现放煤后期煤矸含量定量检测,以传感装置测得的灰分指标来评价放煤控制工艺是否为最优控制效果,进而反馈指导放煤控制工艺进行工序优化,实现对后部煤流灰分在线检测,评价后部顶煤放出效果[25]。通过这种方法实现生产过程中煤矸放落状态整体感知,评估放煤工艺的整体效果,同时可通过系统设定灰分阈值等手段,指导现场及时调整放煤口控制工艺,提升放煤效果。
3.2 人工反馈干预式放煤与实时评价
灰分检测只能评价是否过放,对于只放出纯煤的欠放状态由于不含矸石而无法给予准确评价。此外,灰分检测系统无法识别顶煤冒落成拱和大块煤堵塞放煤口现象。
因此,需根据人工评价对放煤效果进行综合评价。人工仅需对最后一轮煤矸混合模糊段进行放煤和评价,评价包含2部分:前几轮自动化放煤效果和本轮人工放煤效果。通过给电液控制系统配置无线接收器、遥控发射器等装置后,放煤技术人员通过操作面板的按键,可实现遥控放煤操作,保证操作工人可灵活选择观察角度并对放煤过程实现精准控制,同时对相应支架放煤效果给予准确评价。人工反馈干预式放煤实时评价如图11所示,放煤遥控器用于控制支架放煤机构放煤,放煤效果反馈器用于对放煤效果进行量化评价。
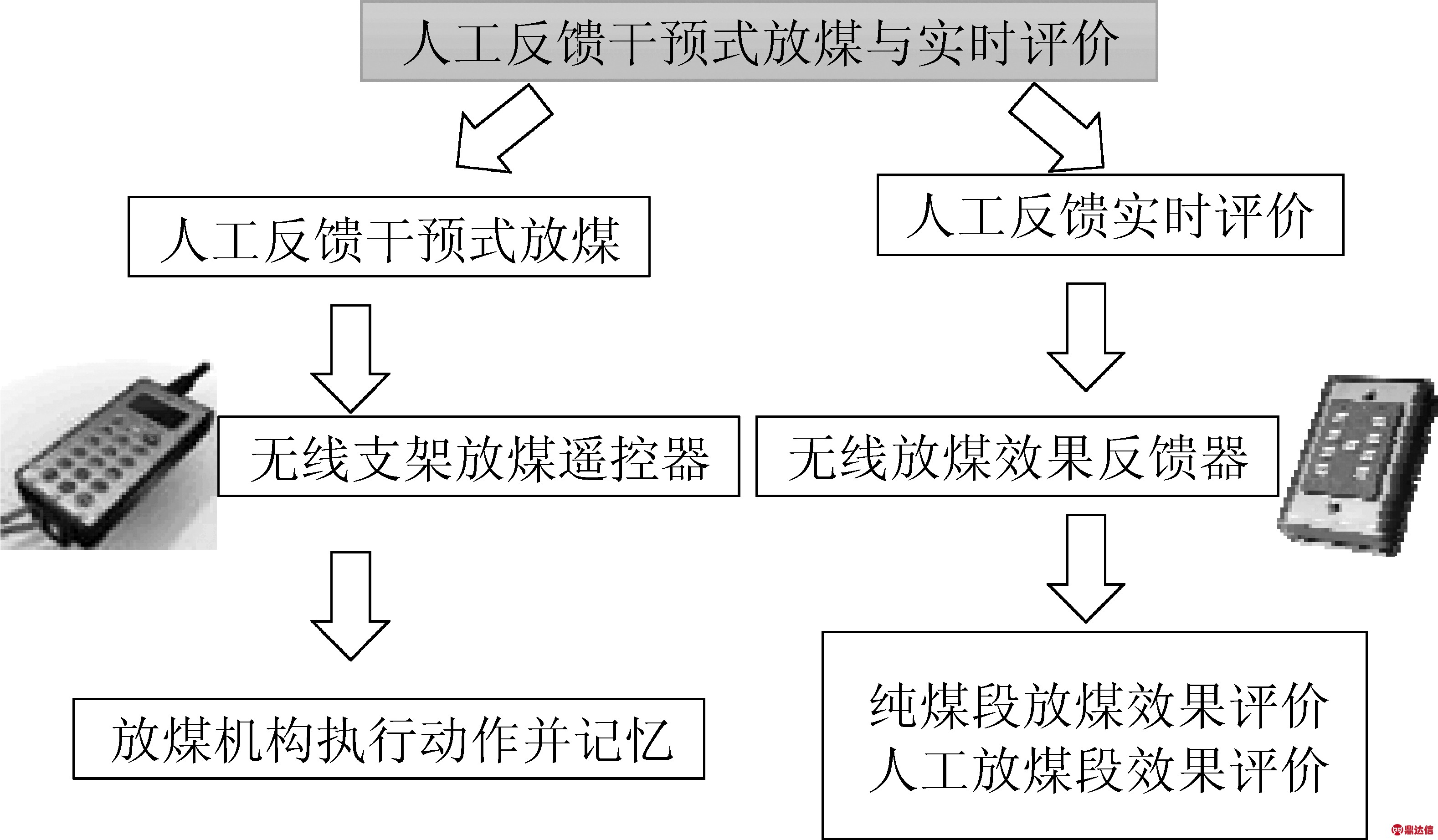
图11 人工反馈干预式放煤实时评价
Fig.11 Real-time evaluation of manual feedback intervention top-coal caving
4 智能化采放协调
目前,放顶煤工作面普遍存在采放协调问题,采煤机连续割煤速度快,而支架放煤过程复杂、放煤时间长成为放顶煤工作面高效推进的制约因素。对此,可采取如下措施来减少放煤时间:①增加机采割煤高度以实现“多割少放”;②增加放煤口尺寸以提高放煤速度;③提高后部刮板输送机宽度、链速和功率以加快支架后方煤流运输;④跟机移架后即自动放煤。
此外,还可采用工作面内多区段自动化成组放煤(图12),多区段是指将工作面分为多个放煤区,多个放煤区同步放煤,成组放煤是指1个区段内多个支架同步放煤,这种操作靠人工较难实现,而通过自动化程序实现较易。可根据工作面长度和刮板输送机运输能力等因素确定工作面区段数目和成组放煤数目,通常来说工作面可划分为3~5个区段,成组放煤的支架数量可取2~4个。成组分区段放煤将增加放煤效率,因此刮板输送机需要更大运量和功率,并且增加了刮板输送机过载的可能性。对此,需实时监控刮板输送机负荷量和刮板链受力情况,当达到警戒值时应反馈支架放煤程序,立即减缓或停止放煤来防止刮板输送机负载过高而“压死”或断链事故发生。对于超大采高放顶煤工作面而言,由于支架结构尺寸整体增大,支架后方空间提升,因而可以布置尺寸、运量和功率更大的刮板输送机,满足多区段成组放煤时对后部刮板运输机的要求,提高设备的稳定性和可靠性。金鸡滩矿7 m 超大采高放顶煤工作面后部输送机型号为SGZ1400/3× 1600,槽宽1 400 mm,功率达到4 800 kW,为目前世界上使用的最大功率的后部刮板输送机。
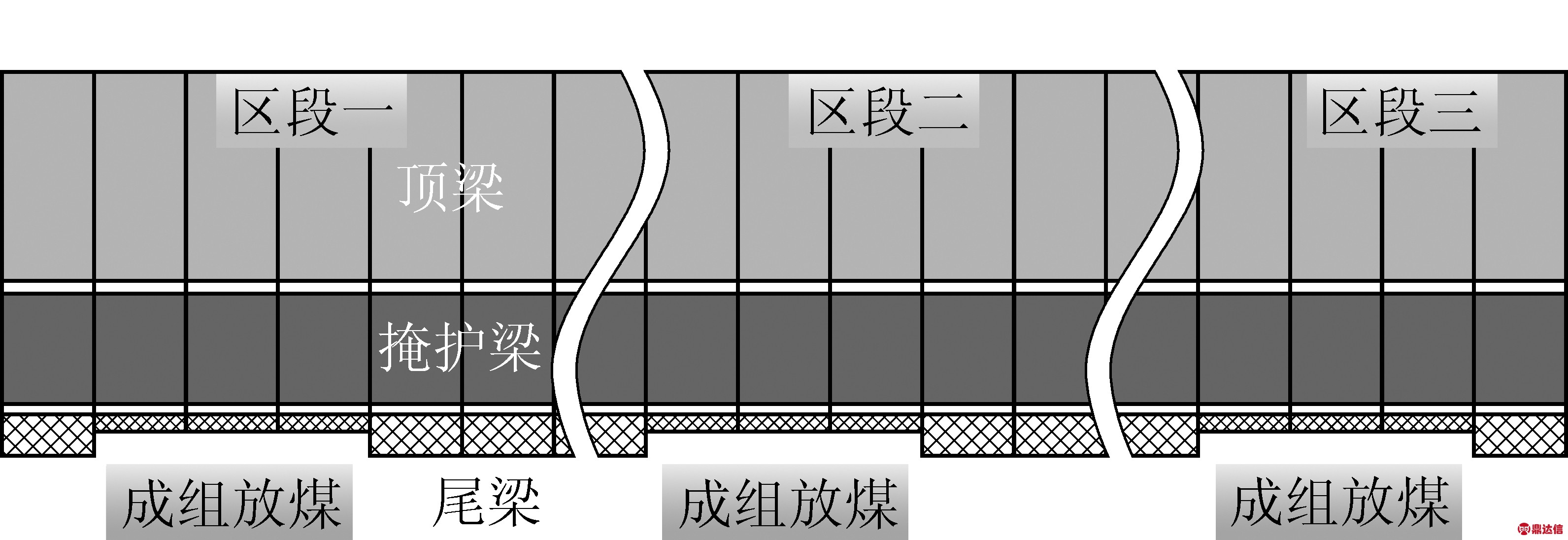
图12 分区段成组放煤
Fig.12 Group drawing of top coal with malti-area
5 结 论
1)超大采高智能化放顶煤工艺可实现“多割少放”、增强顶煤破碎程度和冒放效果,提高开采效率和顶煤采出率。
2)纯煤段采用智能化记忆放煤可提高自动化水平,煤矸混合模糊段采用人工反馈干预式放煤可保证采出率和煤质。
3)灰分在线检测自动评价和人工反馈干预式放煤实时评价系统相结合的放煤评价体系,可为实现基于大数据的完全智能化放煤积累基础数据。
4)采用多区段自动化成组放煤可提高放煤效率、缩短放煤时间,促进采放协调。