摘要:本文采用MCNP5软件建立了凸度仪模拟计算模型,并对其进行实验结果验证。分析了凸度仪固有散射的影响,随待测钢板厚度的增大,固有散射影响减小,对1~15mm厚度的钢板,系统固有散射占总散射影响的10%以下,而对大于15mm厚度的钢板,系统固有散射可近似为零。此外,对散射因子曲线在非对应源附近的鼓包现象进行了分析,分析结果表明,探测器支架具有防止另一排探测器散射干扰的作用。
关键词:散射校正;凸度仪;MCNP5
凸度仪是热轧钢板生产线上检测和控制板材凸度的关键设备,其精度越高,所产板材质量越高,过去此系统的生产技术主要被国外几家大公司垄断。目前清华大学核能与新能源技术研究院研制的凸度在线检测系统[1]实验样机已打破这一垄断,对0.9~25mm厚度范围内的被测钢板,达到±0.1%的测量精度,其中散射影响分析及校正是保证其高精度的关键因素。从散射来源分类,主要包括被测钢板自身造成的散射和凸度仪系统部件的散射两部分。凸度仪系统部件散射,又称固有散射,与系统结构、被测钢板、射线源和环境等均相关,影响因素复杂,很难通过理论模型分析研究。
蒙特卡罗(MC)方法是以概率统计、随机抽样为理论基础,真实地描述各粒子输运问题、物理实验过程等,进而解决理论分析、数值计算等难以解决的实际问题[2],所描述问题、系统越复杂,越能凸显MC方法的优越性,因此,基于凸度仪复杂的固有散射影响分析,必然首选MC方法。MC方法目前至少有5种计算粒子输运的程序软件[3-4]。本文采用通用性、几何能力和方差技巧等方面均较强,且具有可视化界面的MCNP5软件[5],建立与实验样机1∶1尺寸的仿真计算模型,并对其进行实验结果验证。基于此仿真模型,定量分析凸度仪固有散射影响及其随被测钢板厚度的变化情况,并给出可降低系统固有散射影响的建议方案。
1 凸度仪仿真模型
凸度仪结构示意图如图1 所示,主体支撑结构C形架由上臂、侧臂和下臂组成,材料为304不锈钢。上臂内安置两台相同的COMET MXR-225/02/FB型X光机,通过上臂下方的准直机构,将射线源准直为具有一定宽度的扇形束从上臂出射;下臂结构相对复杂,主要是两排电离室探测器,每排224路,各自对应S1、S2射线源,其排列方式在保证窗口中心正对射线源的同时,每路探测器以自身的一个角点为基准沿水平方向排列,图2 为下臂剖面图(x-z面),虚线框内为扇形射线束照射区域,此区域各主要部件参数列于表1。
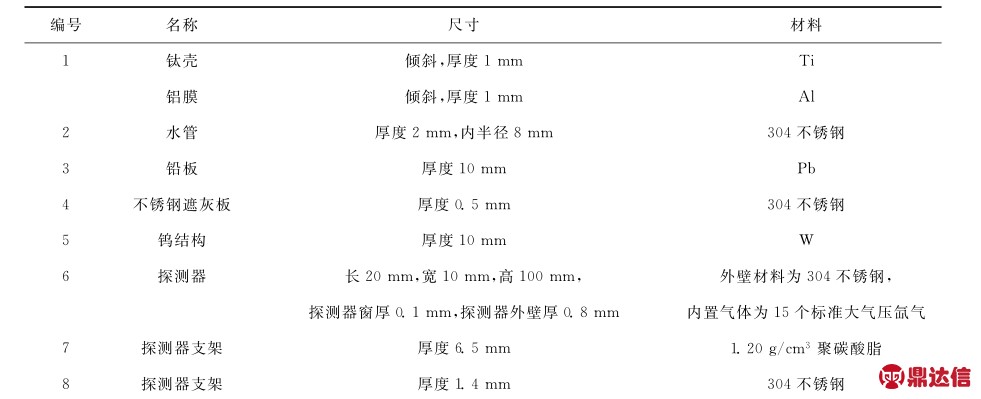
图1 凸度仪结构示意图
Fig.1 Structure diagram of profile gauge
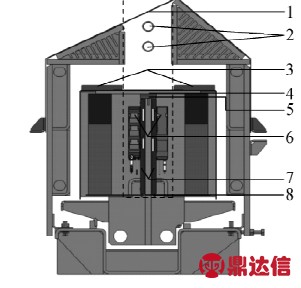
图2 下臂剖面图
Fig.2 Sectional view diagram of lower arm
表1 射线照射区域内各主要部件参数
Table 1 Parameters of main components within irradiated area
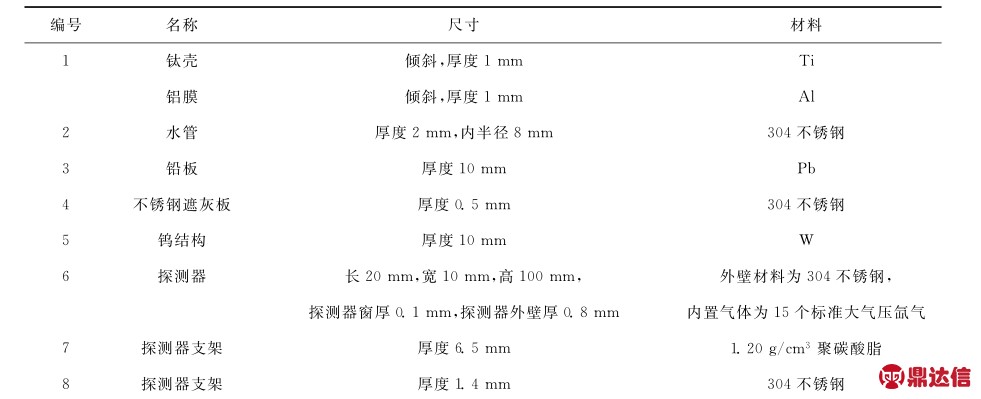
基于上述参数建立凸度仪仿真模型,射线源S1、S2分别设置为恰好覆盖各自224路探测器面的扇形束;下臂结构稍作简化,但保留射线束照射区域的所有部件;C行架的上臂、侧臂和下臂材料均为304不锈钢;被测钢板下表面至探测面的距离为60cm;凸度仪仿真模型在MCNP5软件可视界面下的显示如图3 ~7所示。
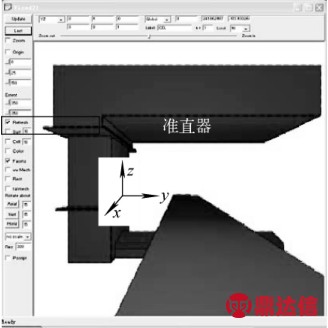
图3 凸度仪仿真模型3D显示
Fig.3 Simulation model 3Ddisplay
of profile gauge
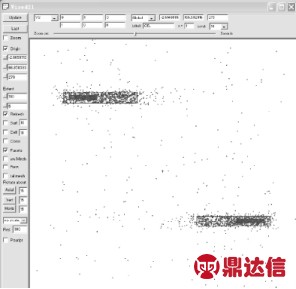
图4 上臂粒子出射口
Fig.4 Particle exit port of upper arm
2 仿真模型计算结果验证分析
基于仿真计算模型,设置被测钢板宽度为1 700mm,厚度为10mm;射线源采用管电压180kV下的X光机输出能谱(由MCNP5建模计算得到),将此模型下的散射因子计算结果与实验结果对比验证分析,分析结果如图8 所示。
定义散射因子(SPR)为:

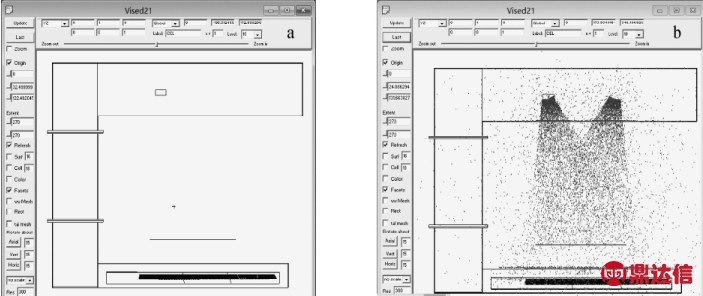
图5 仿真模型剖面(y-z面)图(a)及粒子径迹图(b)
Fig.5 Sectional view(y-z plane)diagram(a)and particle track diagram(b)of simulation model
其中,MCNP5模型计算过程中采用*F1计数卡,与电离室计数相对应。
由图8 可看出,仿真模型计算结果与实验结果基本吻合。在钢板边缘,散射因子较大,曲线较陡;在靠近正对射线源处,散射因子最小;探测器距正对射线源越远,射线斜穿钢板厚度越大,散射因子亦越大,这符合康普顿散射的基本物理规律。仿真模型计算结果与实验结果存在一定的偏差,主要原因为:1)由于实验用钢板宽度和钢板在辊轴上的位置是人工测量确定的,存在一定的误差;2)实验所得A、B排探测器散射因子曲线在远离对应源的钢板边缘位置,相比仿真模型结果出现明显鼓包现象,如图9 所示。
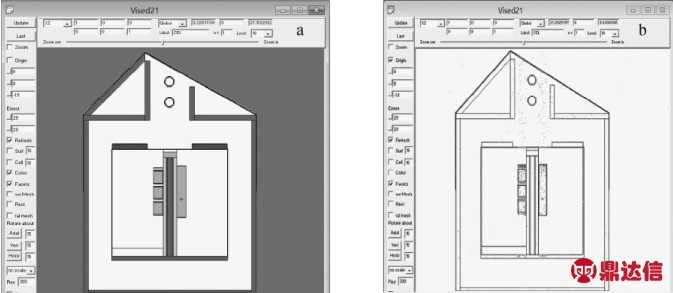
图6 仿真模型下臂剖面(x-z面)图(a)及粒子径迹图(b)
Fig.6 Sectional view(x-z plane)diagram(a)and particle track diagram(b)of lower arm in simulation model
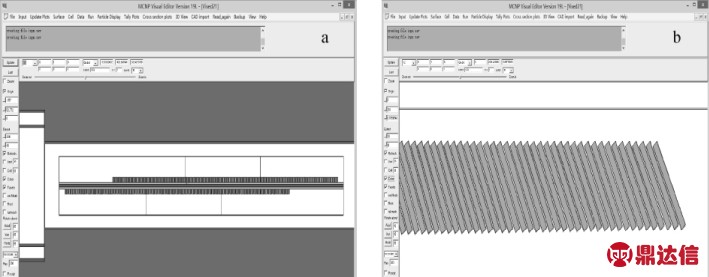
图7 仿真模型探测器排列(x-y面)图(a)及排列细节(y-z面)图(b)
Fig.7 Arrangement of detectors(x-yplane)diagram(a)and
arrangement detail(y-z plane)diagram(b)
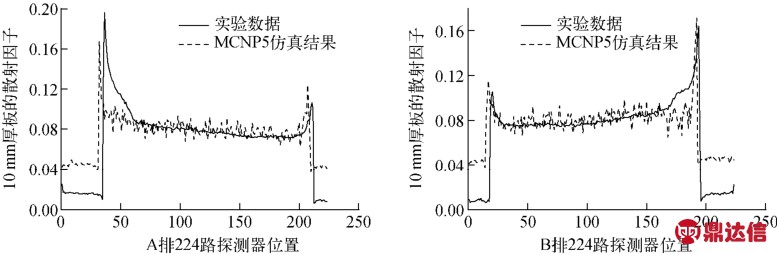
图8 散射因子计算结果与实验结果对比
Fig.8 Comparison of scatter-to-primary ratio between simulation result and experimental result
图9 中,阴影区域1是A源射线经钢板散射后进入到B排探测器,此散射量远小于B排探测器接收的透射量,因此可忽略;阴影区域2是A源直接照射到A排探测器上发生散射后进入B排探测器,而此位置的B排探测器远离B源,且射线束经钢板厚度的衰减,透射量减少,增加的散射量与减少的透射量的比值(即散射因子)增大,形成鼓包现象;钢板厚度越大,接收的透射量越少,鼓包现象也将越明显。
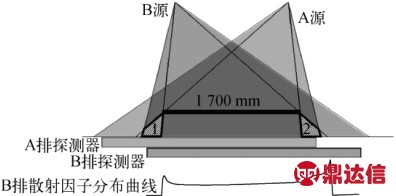
图9 散射因子曲线鼓包现象分析
Fig.9 Analysis of SPR curve bulge phenomenon
MCNP5计算结果并未明显鼓包的原因是,仿真模型的扇形束宽度恰好照射探测器窗面积,且中间有探测器支架吸收。而实验结果中扇形束的宽度无法测到,且探测器支架结构相对复杂,仿真模型的简化造成探测器支架的吸收率增大,因此会出现鼓包现象。
3 仿真模型下凸度仪固有散射影响分析
本部分内容用到两个模型:1)模型1,凸度仪仿真模型;2)模型2,只有射线源,钢板和A、B两排探测器3部分的计算模型。
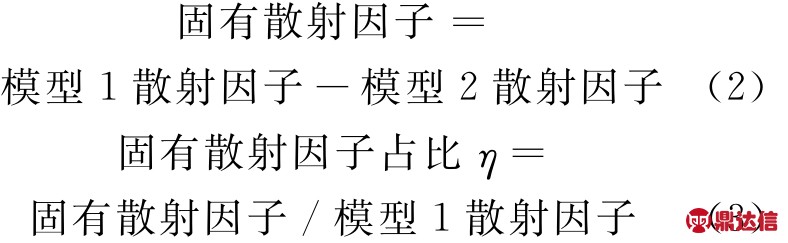
基于上述两个模型,分别计算厚度为1、5、10、15mm,宽度为1 700mm钢板的散射因子,由上述公式计算固有散射因子及其η。图10 、11为B排探测器散射因子、固有散射因子及其η的曲线分布,可看出:1)随钢板厚度的增大,除曲线鼓包范围探测器,凸度仪系统固有散射影响减小,到15mm厚度时,探测器的散射来源可近似全部为钢板,固有散射影响可忽略;2)随钢板厚度的增大,模型2的散射因子曲线鼓包现象变大,说明直接照射在A排的射线散射后造成B排的散射影响变大,与仿真模型对比,探测器支架起了很大的防A排散射干扰的作用;3)1~15mm厚度被测钢板,除鼓包范围探测器外,其余各路探测器的η小于10%,即固有散射影响占总散射影响的10%以下,鼓包范围探测器中,固有散射为负值。
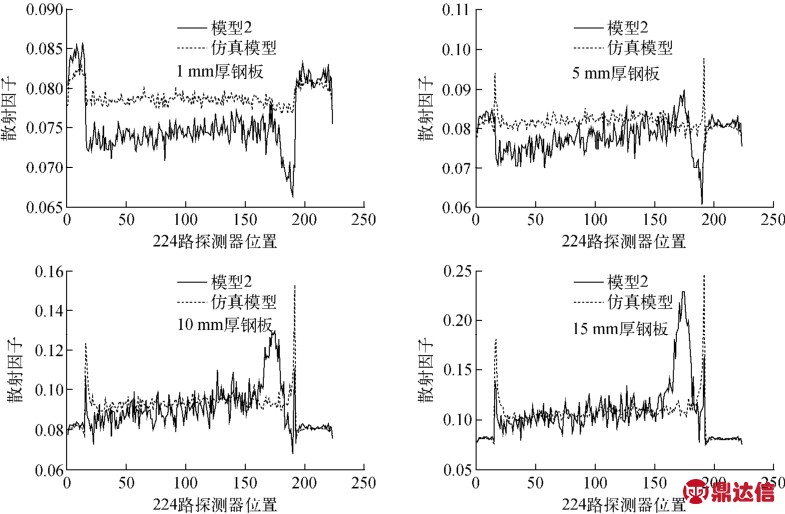
图10 不同钢板厚度下仿真模型和模型2的SPR分布
Fig.10 SPR distributions of simulation model and model 2 under different plate thicknesses

图11 固有散射因子及η分布
Fig.11 Distributions of inherent SPR andη
4 结论
为分析凸度仪固有散射影响,本文采用蒙特卡罗方法MCNP5软件,建立了凸度仪系统仿真模型,并给出了可视化界面下的3D显示和各方向的剖面图;采用实验数据对仿真模型计算结果进行验证,两者基本吻合,但实验数据存在鼓包现象,经分析为非对应源(如B源)直接照射到与它对应的探测器(B排探测器)上发生散射后对此探测器(A排探测器)的影响;最后分析了凸度仪固有散射的影响,随待测钢板厚度的增大,固有散射影响减小,对大于15mm厚度的钢板,系统固有散射可近似为零;对1~15mm厚度的钢板,系统固有散射占总散射影响的10%以下。