摘 要: 介绍了法兰盘金属件冲压模具的计算机辅助设计方法。对冲压模具进行工艺分析,确定倒装复合模方案。应用Pro/Engineer软件对冲压模具的结构进行三维造型设计,完成三维装配图。导出二维图纸后,应用AutoCAD软件修改为二维标准工程图。应用Mastercam软件完成计算机辅助制造编程,进而完成整套冲压模具的设计与加工。所介绍的方法充分利用了参数的关联性,体现了现代化设计的特色,具有设计周期短、准确率高等优点。
关键词: 法兰盘 冲压模具 计算机辅助设计
1 研究背景
模具是工业生产的基础工艺装备,被称为“工业之母”,75%的粗加工工业产品零件、 50%的精加工零件都由模具成型。模具涉及机械、汽车、轻工、电子、化工、冶金、建材等各个行业,应用范围十分广泛。冲压模具具有知识密集和技术密集的特点,设计制造时存在难度大、周期长、制造成本高等问题。随着我国智能产品的推进,产品日新月异,数字化、智能化成为新的趋势,模具种类也不断增多,大家都在为推动智能制造新时代的到来而努力探索。为了适应智能制造的发展,满足用户对模具制造高精度、低成本的迫切要求,模具设计与制造手段也应向智能化、标准化发展,模具工业正广泛应用现代先进制造技术来加速自身的技术进步[1]。笔者以法兰盘金属薄板件冲压模具为例,介绍模具的计算机辅助设计方法,包括卸料机构、推出机构、标准框架的选用,以及模具成型零件的设计与制造。
2 工艺方案
2.1 工艺分析
如图1所示,冲裁件为Q235A低碳钢板材料的圆形法兰盘金属件,厚度为2 mm,属于中小型零件,对称结构。Q235A低碳钢板材料塑性好,冲裁工艺性好。冲裁件生产纲领为年产量10万件,属大批量生产,适合应用模具生产[2]。
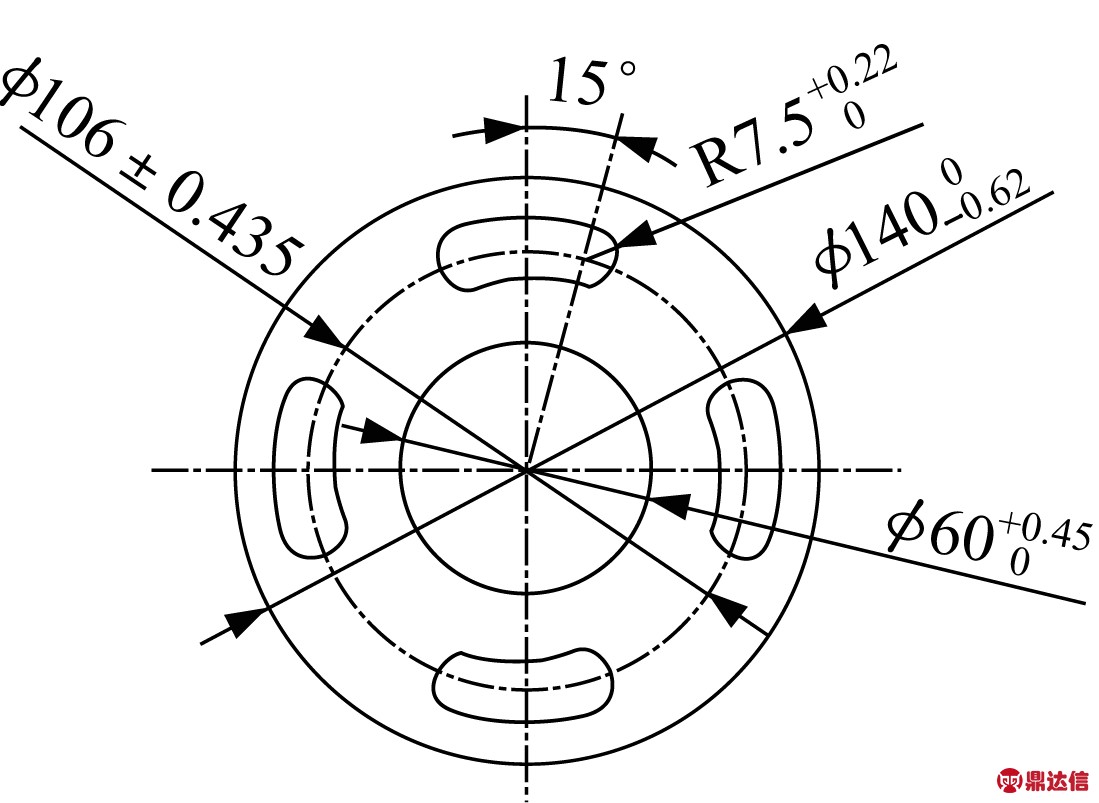
▲图1 法兰盘金属件
根据冲裁件结构特点及生产技术要求,为了保证模具的制造精度及降低生产成本,选择倒装式复合冲裁模设计方案。
2.2 排样设计
为保证冲裁精度,降低生产成本,保证模具使用寿命和操作方便,采用有较少搭边的单排排样形式,排样图如图2所示。查阅相关手册,冲裁件之间的搭边值设为1.5 mm,冲裁件与条料件侧边之间的搭边值设为1.8 mm。经计算,单个冲裁件面积A1为15 393 mm2,条料宽度B1为144.6 mm,条料步距S为147.1 mm,一个步距内冲压件数量n1为1,材料利用率η为[3]:
η=A1/(B1S)×100%=72.4%

▲图2 排样图
计算总冲压力时,首先确定冲裁力[4]。变形区的实际变形情况比较复杂,因此采用材料抗剪力因数K加以修正,一般K取1.3。冲裁件所有孔的周长总和La为599 mm,落料件周长Lb为439.8 mm,Q235A低碳钢板材料厚度t为2 mm,材料抗拉强度τ为350 MPa,冲孔力Fa为:
Fa=KLatτ=545 kN
落料力Fb为:
Fb=KLbtτ=400 kN
冲裁力F为:
F=Fa+Fb=945 kN
在冲裁时,零件或废料从凸模上卸下来的力称为卸料力FX,从凹模内将零件或废料顺着冲裁方向推出的力称为推件力FT,逆冲裁方向顶出的力称为顶件力FD凹模中的零件数量N取3。查阅相关国标,取卸料力因数KX为0.05,推件力因数KT为0.055,顶件力因数KD为0.06。卸料力FX为:
FX=KXFb=20 kN
推件力FT为:
FT=NKTFa=89.92 kN
顶件力FD为:
FD=KDF=56.7 kN
总冲压力F0为:
F0=F+FX+FT=1 054.92 kN
2.3 冲压设备选择
选用冲压设备,主要考虑的因素如下:① 设备类型和工作型式是否符合安全生产与环保要求;② 压力和功率是否满足完成工序任务的要求;③ 装模高度、工作台尺寸等是否适合完成工序所使用的模具。根据冲压件特点和工艺要求[5],选择公称压力为1 250 kN的JH21-125型开式固定台压力机,压力机主电机功率为11 kW,滑块行程为180 mm,最大闭合高度为350 mm,闭合高度调节量为90 mm,压力机工作台尺寸为680 mm×1 100 mm。
3 模具设计
模具总体构成如图3所示,采用标准模架,重点设计卸料机构、推件机构及成型零件。
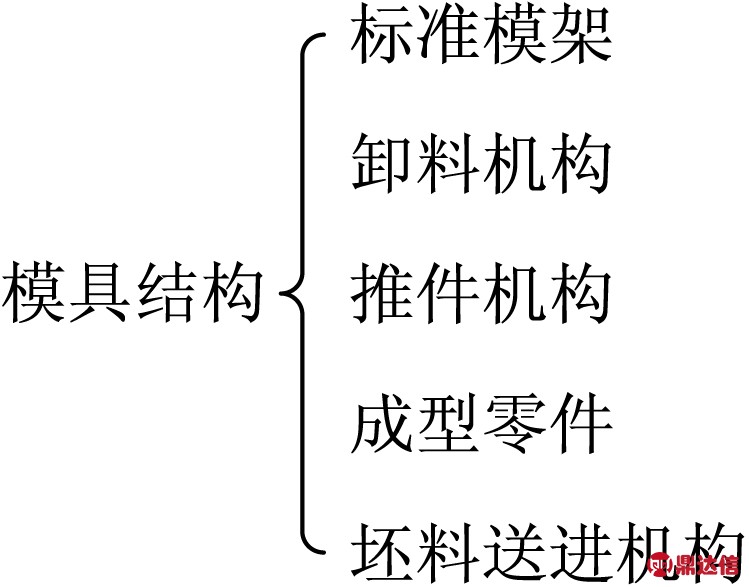
▲图3 模具总体构成
3.1 卸料机构
卸料机构的功能为将制件或废料从凹模中推出或顶出,不直接影响模具的加工精度。但是,卸料机构正常工作时,直接影响模具的工作效率及正常运行。模具在工作过程中需要卸下工件、条料废料、冲孔废料等,从模具的结构方面考虑,应尽量简单。冲孔废料设计为自动排出,针对条料废料,采用弹性卸料机构。弹性卸料机构如图4所示。
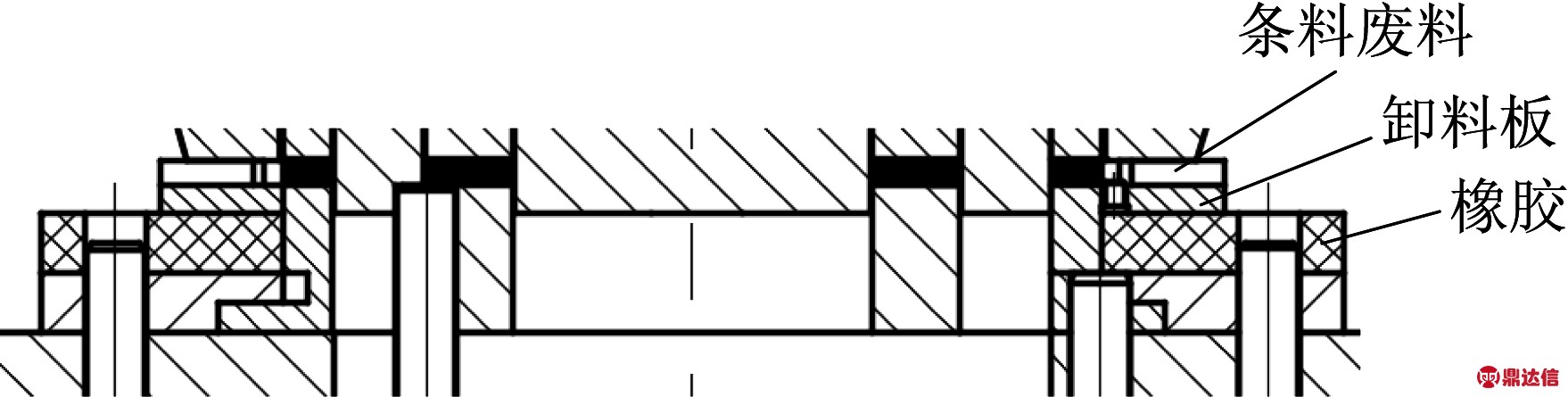
▲图4 弹性卸料机构
3.2 推件机构
法兰盘金属件的冲压力大小为中等,需要的推件力较大,从工作稳定性、可靠性方面考虑,选用刚性推件机构卸下法兰盘金属件[6],如图5所示。
3.3 成型零件
选用倒装式复合模,核心成型零件包括落料凹模、冲孔凸模、落料冲孔凸凹模。从保证模具的冲裁精度及安装维修方便考虑,落料凹模和冲孔凸模采用整体式结构,落料冲孔凸凹模采用凸缘式结构。模具刃口尺寸选用配合加工法计算,即落料以凹模为基准,冲孔以凸模为基准。刃口尺寸计算结果见表1[7]。
表1 刃口尺寸计算表
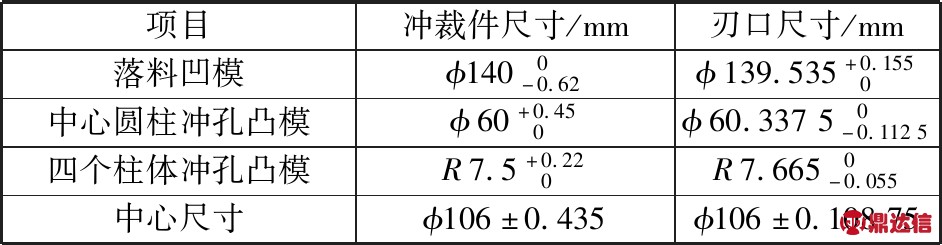
所设计的模具成型件三维图如图6所示。
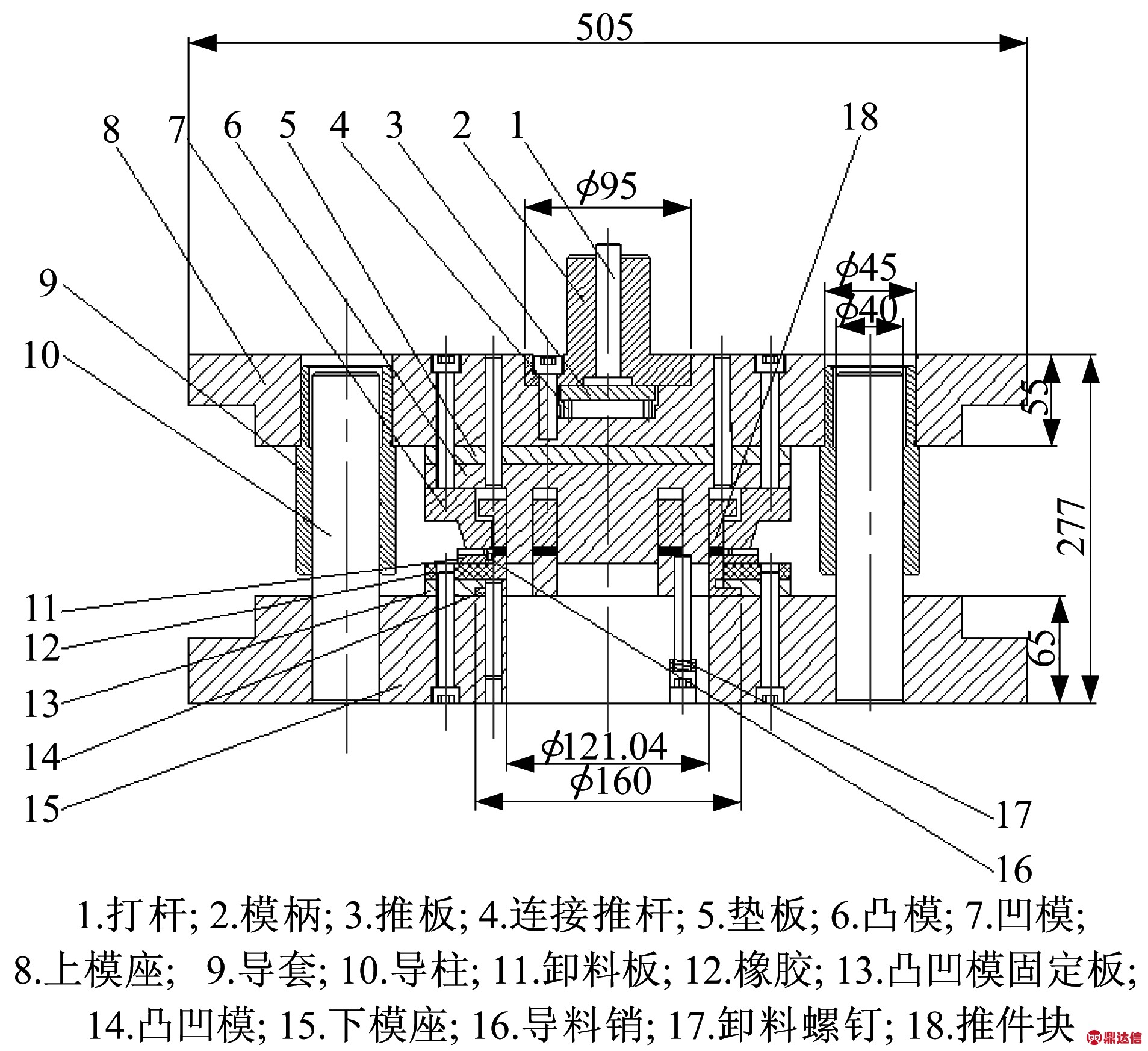
▲图5 刚性推件机构
3.4 标准模架与坯料送进机构
选用符合DB/T 2851.6—1990标准的滑动导向中间导柱圆形模架,结构简单,操作方便。坯料送进机构选用导料销导料、挡料销定位的常用结构[8]。标准模架如图7所示,坯料送进机构如图8所示。
4 设计方法
采用计算机辅助制造、计算机辅助工程技术进行计算机辅助设计[9]。总装图采用Pro/Engineer参数化软件进行三维建模和设计,并仿真分析各构件。设计合理后导出工程图,应用AutoCAD软件按标准格式绘制二维图,应用Mastercam软件进行编程加工,真正实现了一体化参数设计。
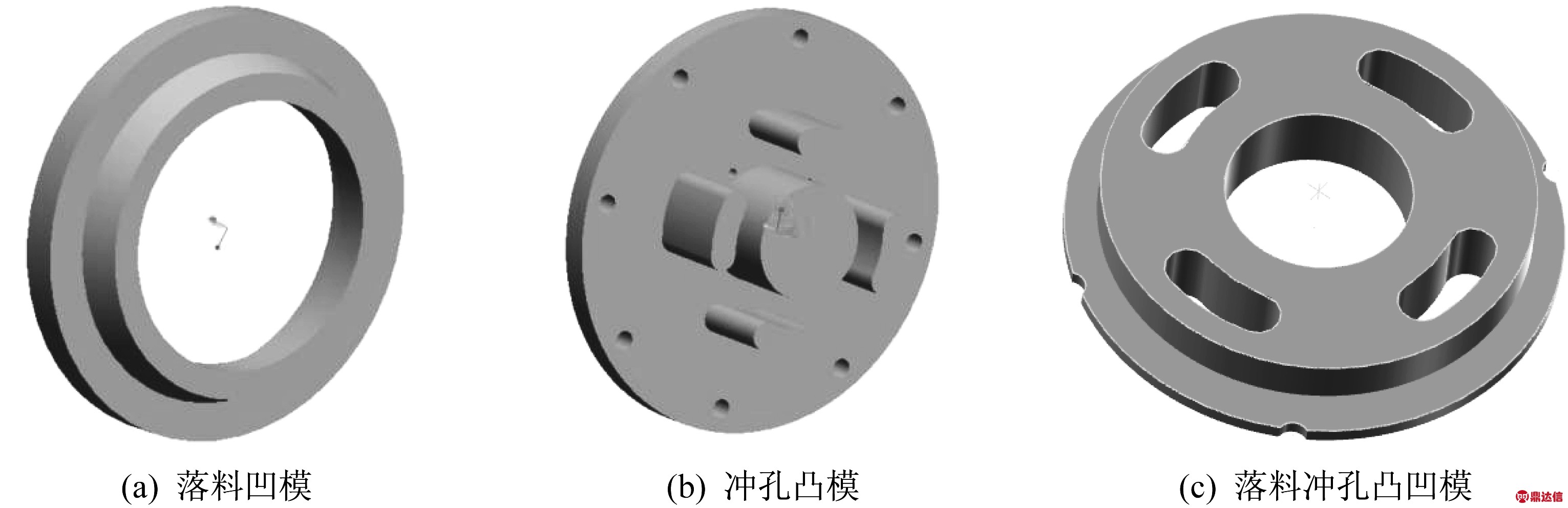
▲图6 模具成型件三维图
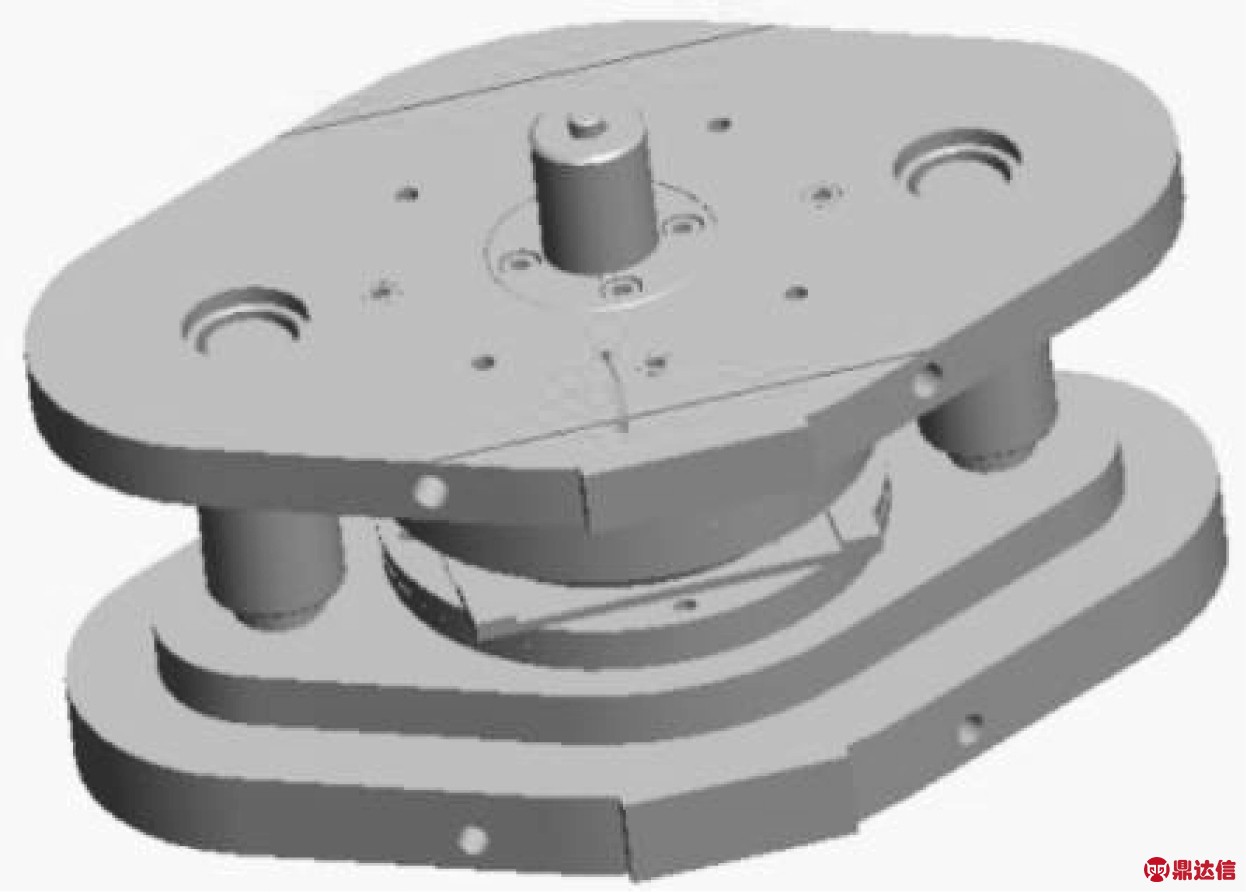
▲图7 标准模架
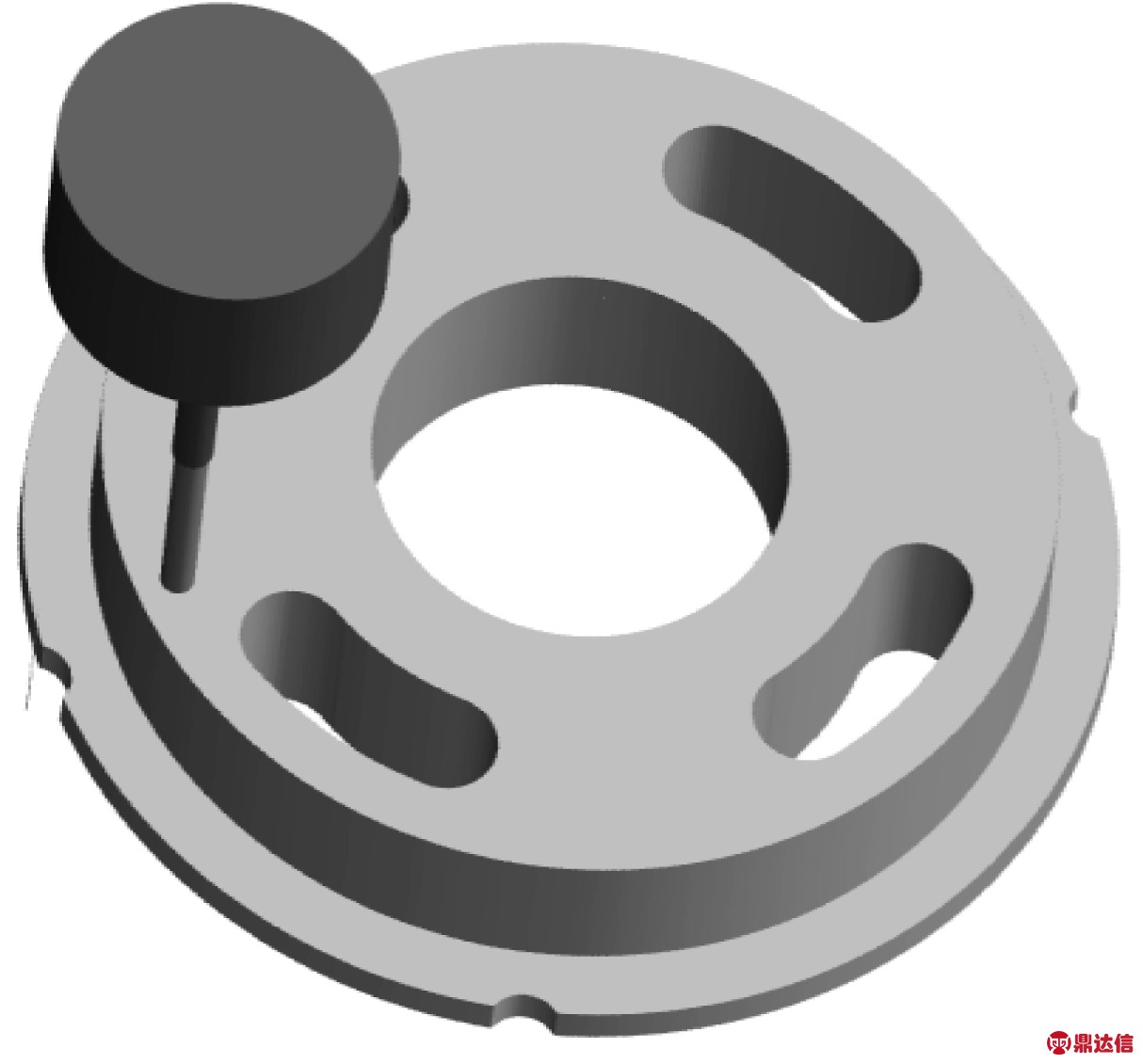
▲图8 坯料送进机构
4.1 计算机辅助设计绘图
应用Pro/Engineer软件设计模具三维总装图,Pro/Engineer是现今主流的计算机辅助设计、制造、工程软件之一,在国内产品设计领域占据重要位置。模具三维总装图如图9所示。
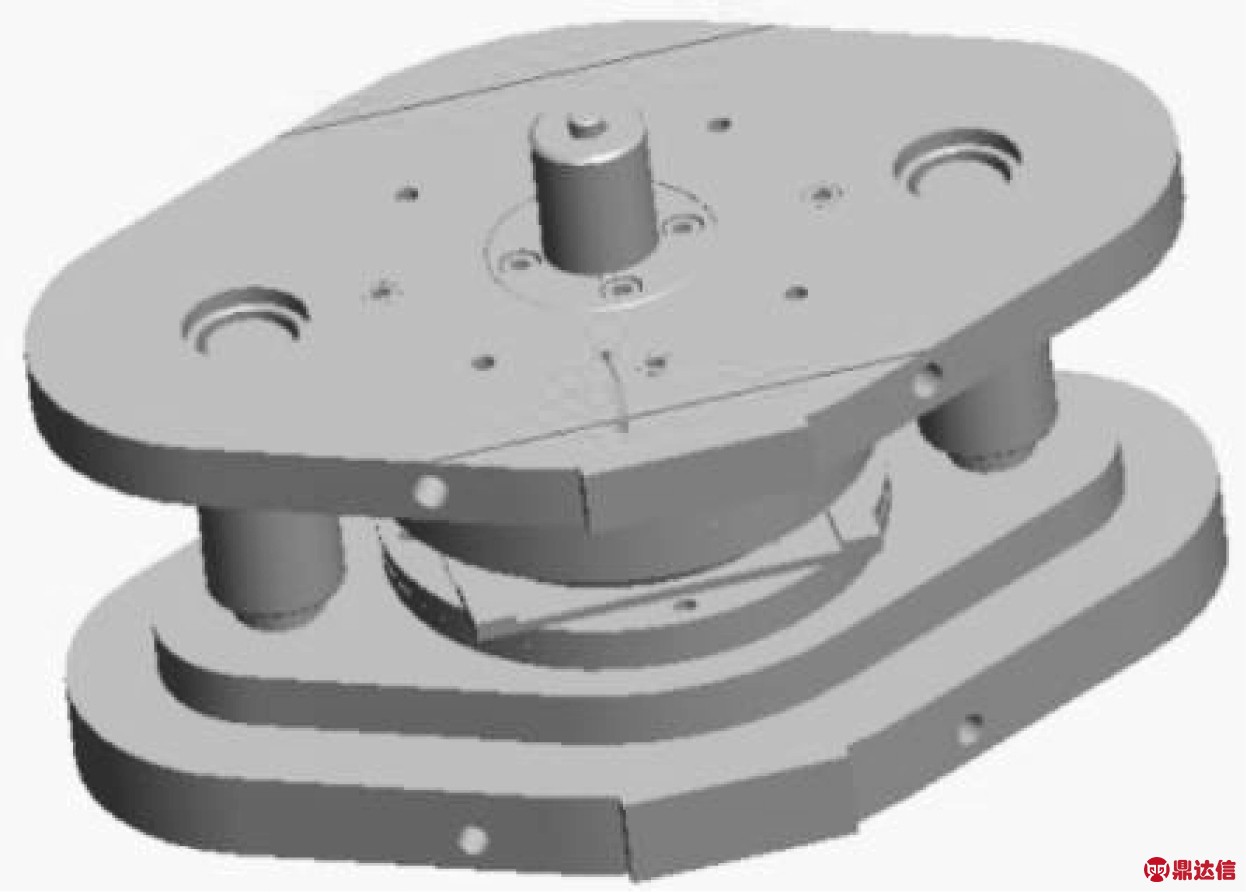
▲图9 模具三维总装图
在Pro/Engineer软件内导出产品的二维图和各零件图,再应用AutoCAD软件按标准格式及正常投影关系绘制标准二维图。凸凹模零件图如图10所示,模具装配图如图11所示。

▲图10 凸凹模零件图
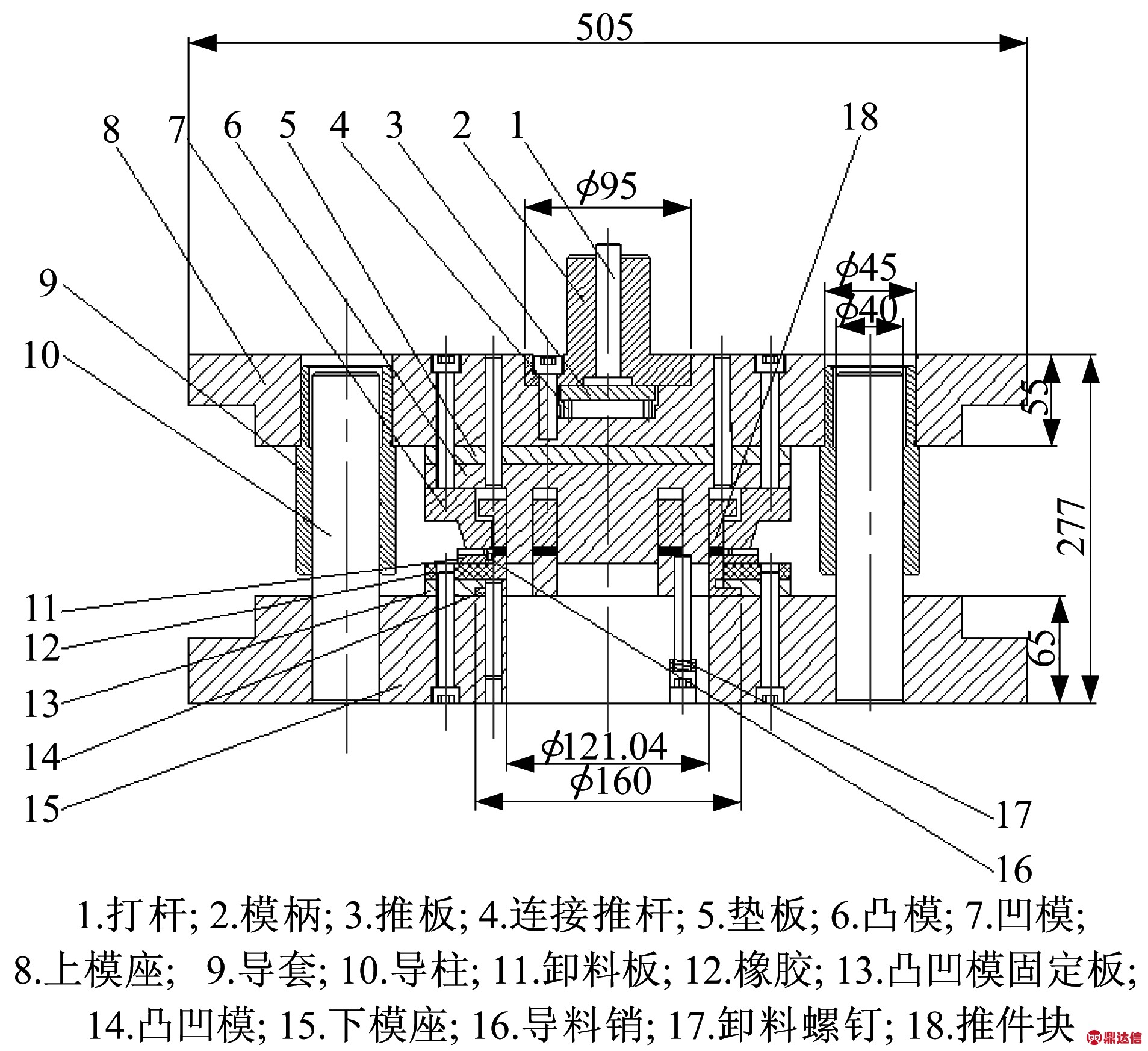
▲图11 模具装配图
一体化设计优点如下:① 利用装配校核好的三维图导出二维效果图,可减少绘图的尺寸错误,相当于自动校核一次;② 绘制效率高,修改方便,应用软件内的标准件图库,减少重复绘制,能有效缩短设计周期。
4.2 计算机辅助制造
应用Mastercam软件,对已设计好的核心成型零件进行计算机辅助制造编程加工。Mastercam软件可以将计算机辅助设计造型和计算机辅助制造数控编程集成于一个系统环境中,完成零件造型、刀具路径生成、加工模拟仿真、数控程序生成,与数控机床进行通信完成数据传输,最终完成零件的加工。在Mastercam软件中,完成所设计的模具核心成型零件冲孔凸模、落料凹模、落料冲孔凸凹模的加工仿真及数控程序编制,操作流程为,读取Pro/Engineer软件设计的三维图,分析零件加工工艺,设计刀具路径,选择合适的切削参数,仿真校验,后处理数控程序运行,与数控机床通信,将程序传送至各数控机床控制系统,各数控机床可以直接运行程序加工零件[10]。刀具路径设计如图12所示。落料冲孔凸凹模仿真加工效果如图13所示,冲孔凸模仿真加工效果如图14所示。
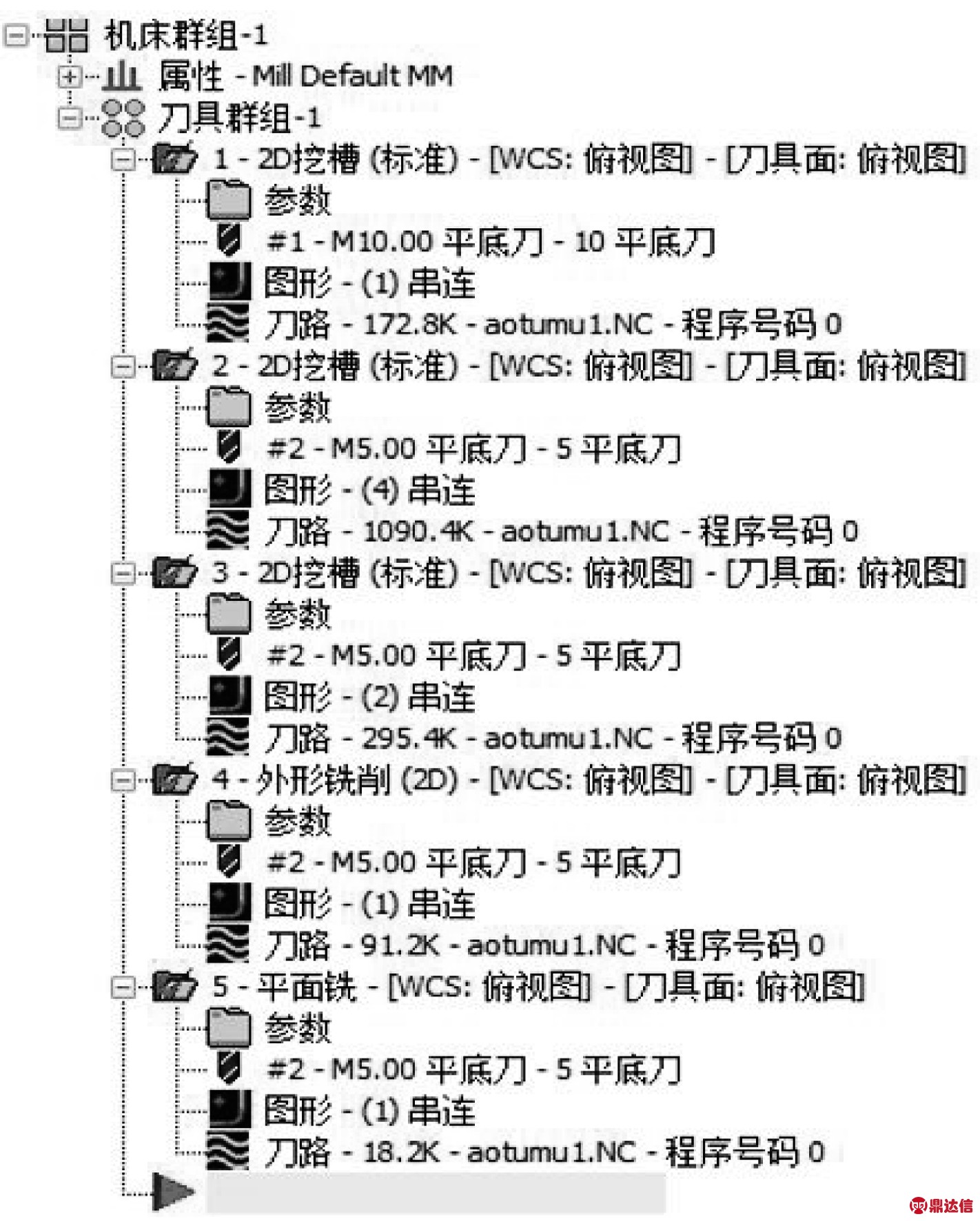
▲图12 刀具路径设计
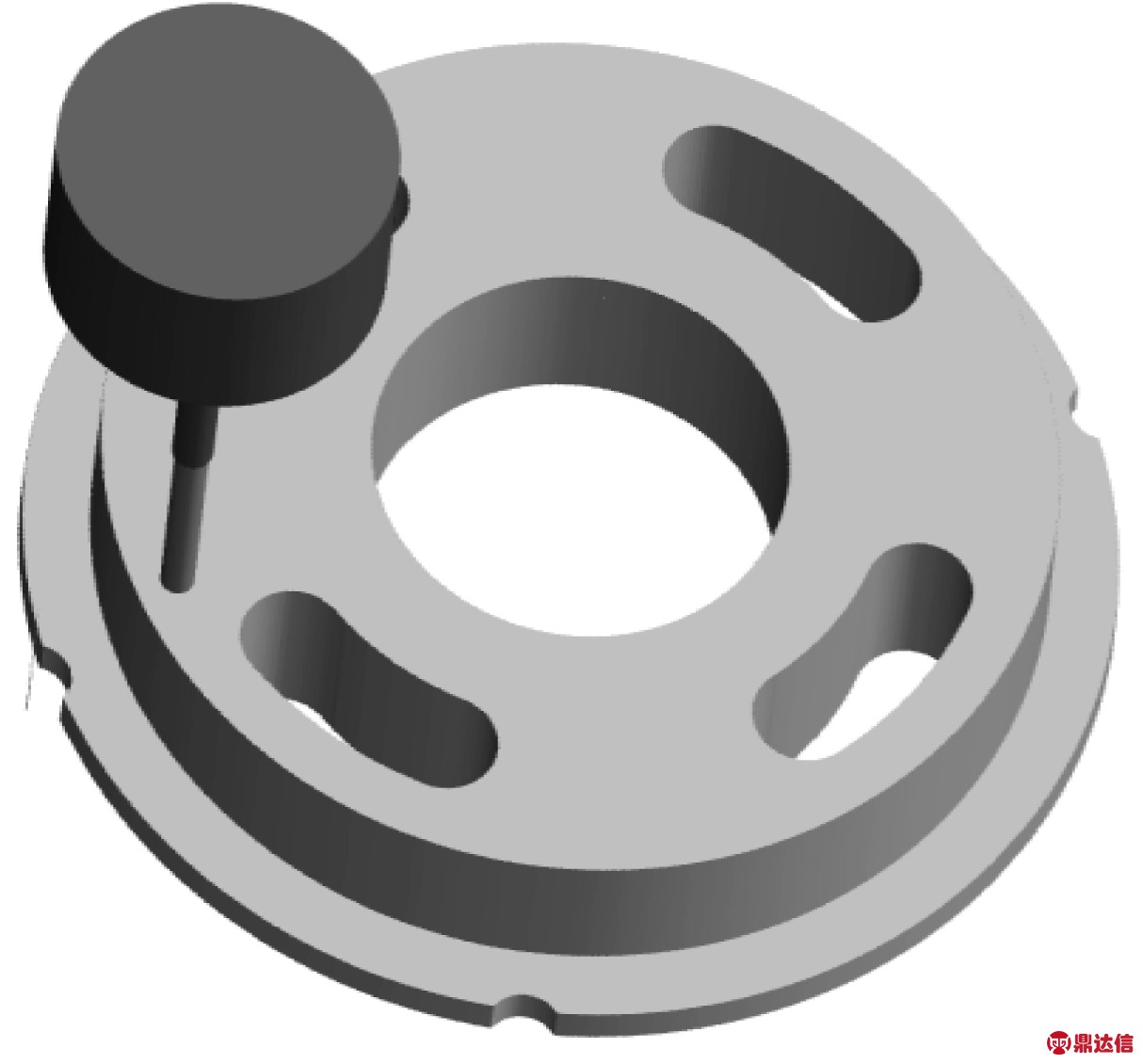
▲图13 落料冲孔凸凹模仿真加工效果
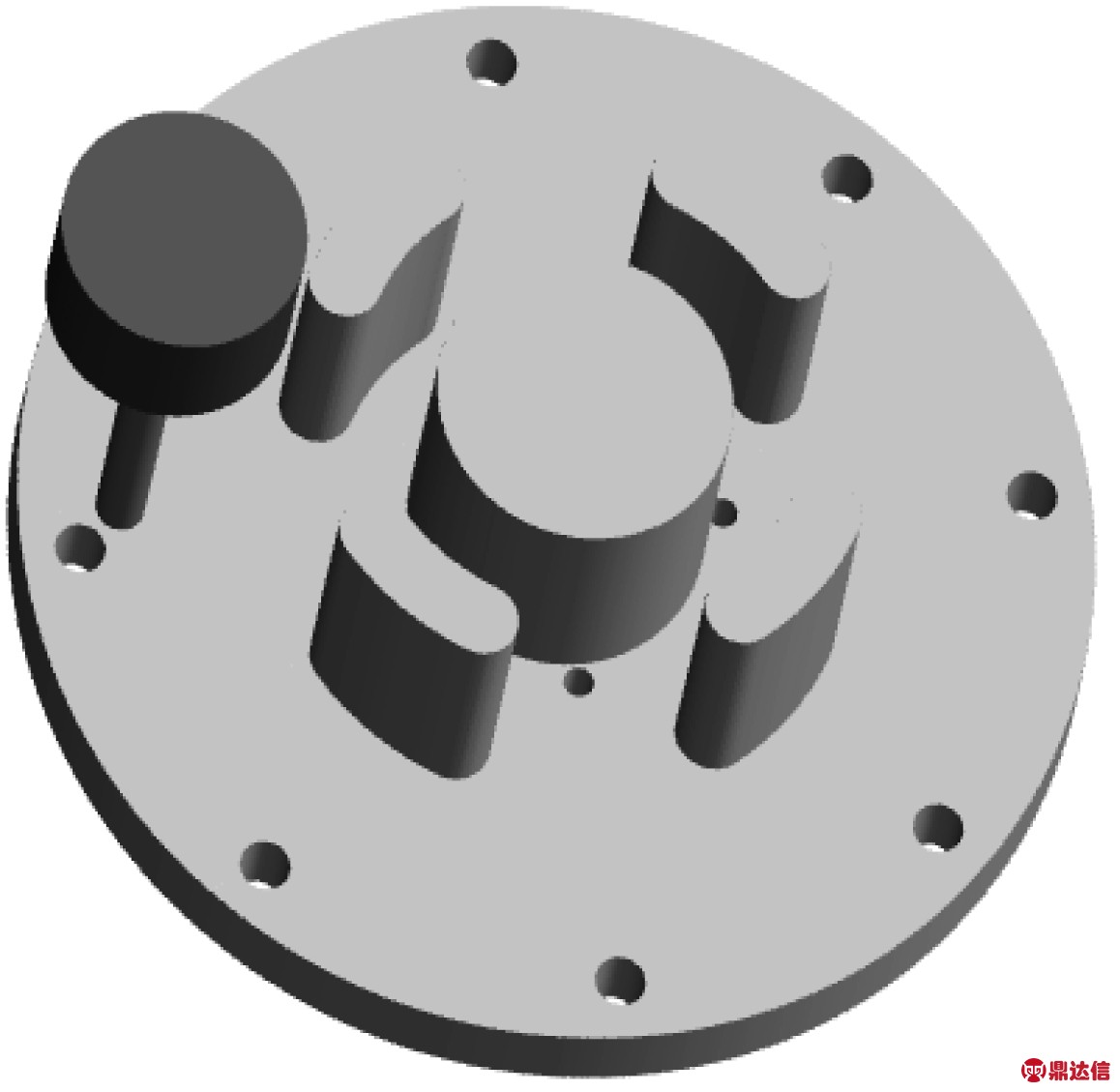
▲图14 冲孔凸模仿真加工效果图
后处理数控程序如下:
O0001
N110 G0 G17 G40 G49 G80 G90
N120 T2 M6
N130 G0 G90 G54 X-3.968 Y-87.128 A0.S1667 M3
N140 G43 H2 Z50.
N150 Z2.
N160 G1 Z-1.923 F600.
............
N6700 G1 X1.032 Y-87.212
N6710 G0 Z50.
N6720 M30
5 结束语
笔者介绍法兰盘金属件冲压模具的设计与制造,采用计算机辅助设计与计算机辅助制造一体化参数设计,在模具设计过程中应用 Pro/Engineer、AutoCAD、Mastercam等软件,创建模具三维模型,导出二维图,将设计好的零件图导入Mastercam软件进行计算机辅助制造加工。模具一体化参数设计有效保证了尺寸准确,出错率低,设计周期短,模具整体结构精简,工艺参数合理,充分展现了现代产品的设计方法,为同类模具和产品的设计与制造提供了借鉴。