某型飞机法兰盘表面缺陷的无损检测方法
张海兵, 王莉, 孙红光
【作者机构】 | 海军航空大学青岛校区 |
【来 源】 | 《无损检测》 2020年第2期 P74-76页 |
【分 类 号】 | V267.2 |
【分类导航】 | 航空、航天->航空->航空制造工艺->航空器的维护与修理 |
【关 键 词】 | 飞机 法兰盘 无损检测 |
【摘 要】 | 法兰盘是飞机着陆装置的关键部件,采用超声表面波检测技术对其进行检测,并分析了试验的影响因素,给出了法兰盘的超声表面波检测方法,同时采用磁轭法进行了复检验证。经应用表明,超声表面波法对于法兰盘的检测具有较大的优势。 |
【全文获取】 | ![]() |
某型飞机法兰盘表面缺陷的无损检测方法
摘 要: 法兰盘是飞机着陆装置的关键部件,采用超声表面波检测技术对其进行检测,并分析了试验的影响因素,给出了法兰盘的超声表面波检测方法,同时采用磁轭法进行了复检验证。经应用表明,超声表面波法对于法兰盘的检测具有较大的优势。
关键词: 飞机;法兰盘;无损检测
1 概述
主起落架法兰盘是飞机着陆装置的关键部件之一(见图1),主要作用是固定联接刹车盘。在飞机滑行过程中,当刹车盘对轮毂进行刹车时,刹车盘因受反作用力会对法兰盘施加一定的扭转剪切力,易使得法兰盘的过渡圆角边缘处产生疲劳裂纹,影响刹车工作效率,甚至导致刹车失效。因此,非常有必要定期对法兰盘进行无损检测。
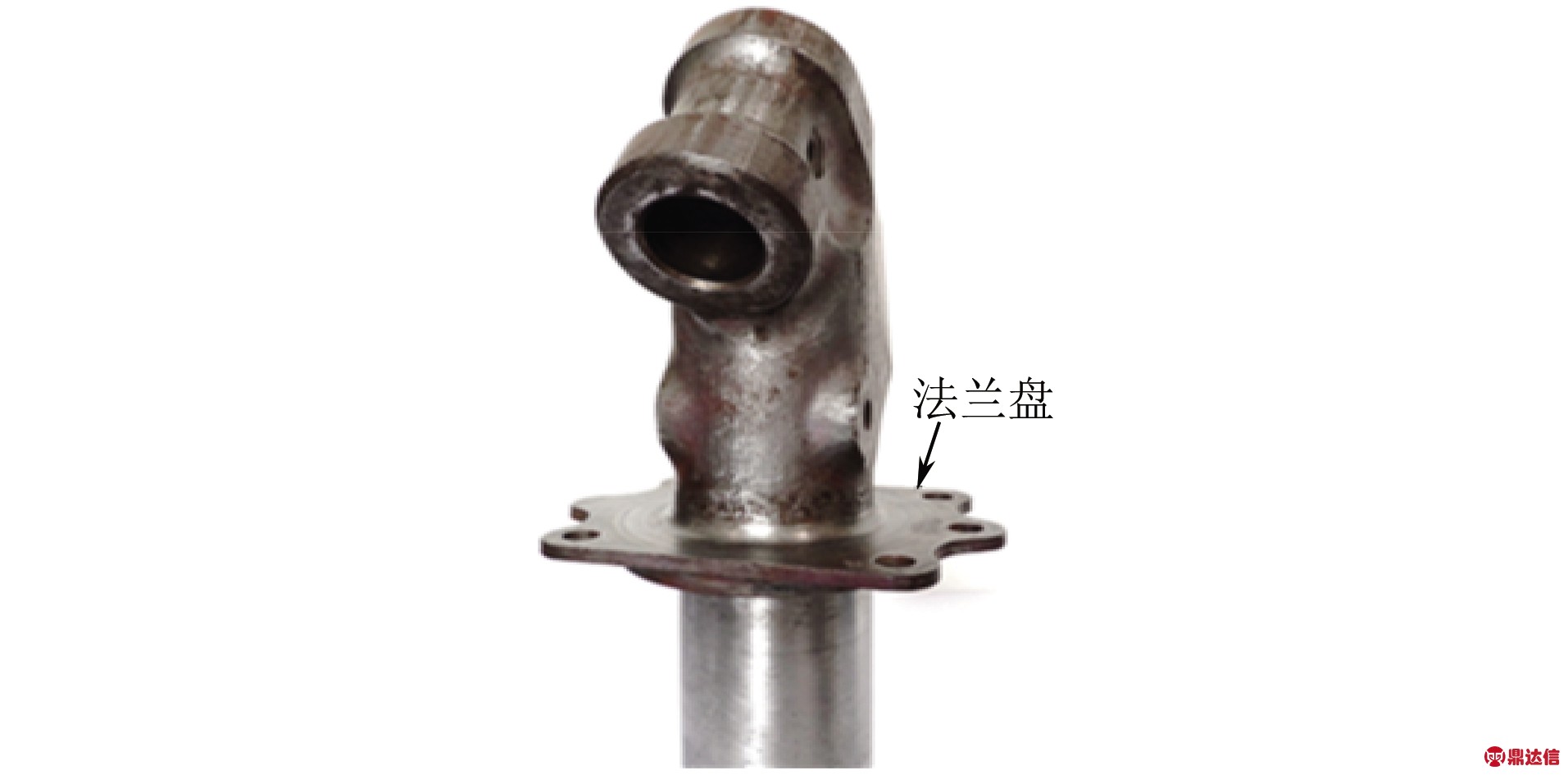
图1 主起落架轮轴法兰盘实物
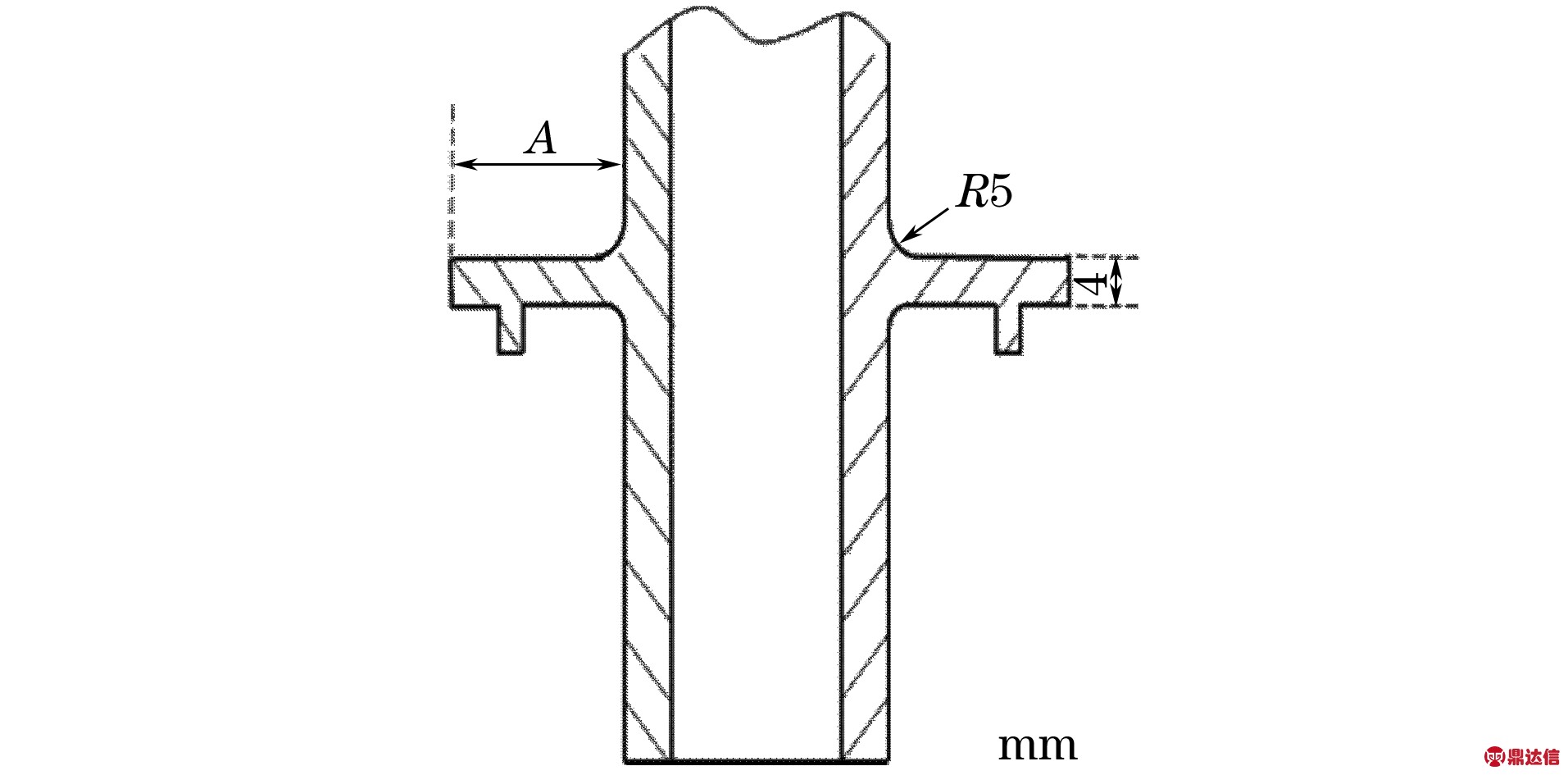
图2 法兰盘结构示意
2 检测方法
法兰盘结构示意如图2所示,应力集中部位如图中R5处所示。法兰盘表面有一层油漆,如对其实施磁粉检测和渗透检测,油漆层会对检测结果产生较大影响;如果采用涡流检测方法,原理上是可行的,但检测部位形状不规则,会引发大量干扰信号而影响检测的可靠性。故,综合考虑法兰盘表面状况和各类检测方法的适用性,认为超声表面波检测技术是一种较好的原位检测方法[1-3]。
另外法兰盘材料为30GrMnSiA,是一种铁磁性材料,选用磁粉检测方法作为复检的方法比较适用。
3 超声表面波检测
3.1 检测影响因素分析
超声表面波质点运动状态具有纵波和横波的综合特性[4],表面波检测法兰盘时主要受以下因素影响。
(1) 油污和表面光洁度的影响
表面波波长比横波波长短,衰减也大于横波的,当其沿工件表面传播时,对于表面的油污、不光洁等反应敏感,会发生大幅衰减。利用此特点,检测过程中可以用手指沾少量油在声束传播方向触压工件表面,并观察反射回波波高的变化,从而判断反射源及其所处位置。
(2) 裂纹的影响
当表面波遇到裂纹时,一部分信号在裂纹开口处仍以表面波的形式被反射,并沿工件表面的原路径返回;另一部分信号会沿裂纹表面传播,并在经过裂纹后仍以表面波的形式沿工件表面继续传播,同时部分表面波在裂纹尖端处发生波型转换,转换为变形纵波和变形横波在工件内部传播。
(3) 弧形转角的影响
表面波传播过程中,遇到凸面弧形转角边缘时,部分表面波信号会发生反射和透射;遇到凹面弧形转角边缘时,部分表面波会发生波型转换,出现转换横波在工件内部传播;而另一部分表面波信号将继续沿弧形表面传播。
3.2 超声表面波检测
3.2.1 探头的选择
超声表面波探头主要选择纵波折射法表面波换能器,压电晶片产生的纵波通过一定倾角的斜楔入射到工件表面,经波型转换后在工件中产生表面波。法兰盘的厚度为4 mm(见图2),待检测表面应较光洁。综合考虑航空机件判废要求和法兰盘尺寸结构,探头频率选择为2.5 MHz,晶片尺寸(长×宽)为6 mm×6 mm,入射角为62°。
3.2.2 扫描范围和灵敏度调整
超声表面波检测时,探头扫描速度调整方法[5]与斜探头的不同。将探头声波发射面涂以耦合剂,放在V-2型试块上,使探头前沿距离φ5 mm孔边沿30 mm,调整深度按键,使孔的反射波位于显示屏水平刻度“9”处,调整抑制读数为40%,使φ5 mm孔的反射波高度达到饱和。或者将探头放置在法兰盘标准试块上,表面波沿法兰盘表面向轮轴的根部传播(见图3),探头前沿距离过渡圆角R5内侧边(即轮轴外壁)15 mm,使底波(转换横波的回波)位于显示屏水平刻度“7”附近,调整抑制读数为40%,使底波高度达到饱和,此时显示屏水平扫描线与声程比为2∶1。
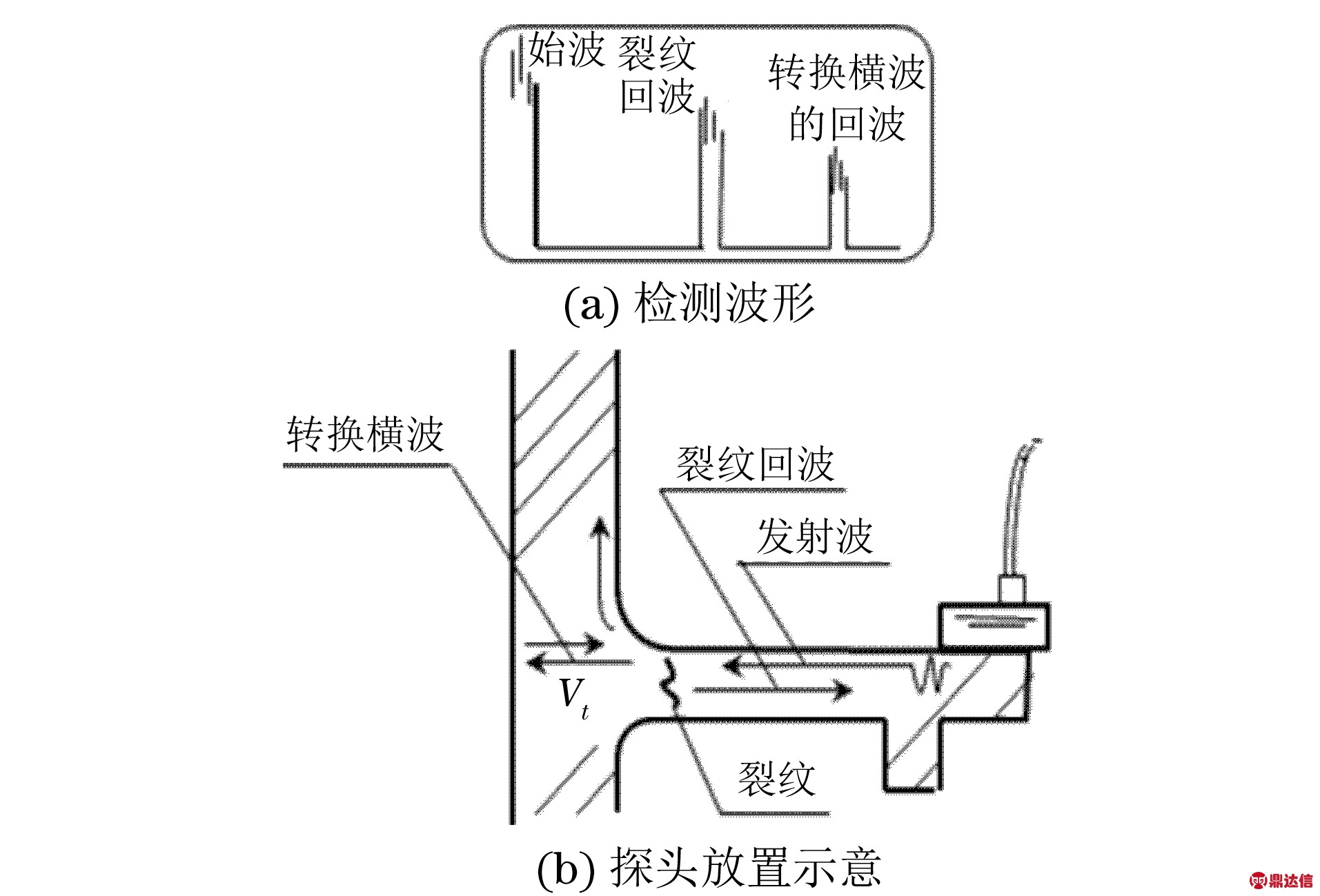
图3 主起落架法兰盘超声表面波检测波形与探头放置示意
3.2.3 检测步骤
(1) 分解机轮,取下刹车盘螺栓,将法兰盘清洗干净,如果发现探头扫查区存在漆层脱落、起泡,则进行局部除漆或打磨处理(用砂纸)。
(2) 将探头涂上耦合剂后放置在法兰盘上,指向轮轴的根部(见图3),当在图2 中A>27 mm的区域时,探头前沿距离过渡圆角R5内侧边15 mm,底波(转换横波的回波)位于显示屏水平刻度“7”附近,始波与底波之间的区域为缺陷监视区,尤其注意水平刻度“3.5”至“6”之间的区域。
(3) 当在图2中A<27 mm的区域时,为了使表面波能够完全入射至法兰盘内,探头前沿距离过渡圆角R5内侧边10 mm,底波(转换横波的回波)位于显示屏水平刻度“6”附近,水平刻度“2.5”至“5”之间的区域为缺陷重点监视区。
(4) 由于待检法兰盘表面有保护层,扫查时首先应该进行耦合补偿。调节仪器增益值,在探头和工件耦合良好的前提下,底波波高应达到饱和。
(5) 沿着法兰盘一周缓慢移动探头,探头始终指向轮轴根部圆角R5处,并作角度不大于10°的摆动,使底波基本处于最高波高状态,探头与法兰盘表面要保持耦合良好,注意观察显示屏上的缺陷监视区和底波波高的变化,以判定是否有缺陷,直至扫查一周结束。当缺陷监视区出现回波信号,同时底波波高降低时,应特别注意。
(6) 如果缺陷监视区出现回波信号,首先应将探头前的耦合剂擦拭干净,排除由此造成的干扰杂波。确认此回波是源自工件后,用手指触压法确定出反射源的位置,并观察该处是否有漆层脱落、刀痕、腐蚀坑或者其他凹坑等。若这些因素都排除后,回波仍然存在,应判定该处是否有裂纹,并通过磁粉检测方法验证复查,确定缺陷的性质和大小。当探头前沿距离过渡圆角R5内侧边10 mm时,应特别注意在水平刻度“3”附近有一波高约为40%(相对于满屏高度)的干扰波,此时可将探头适当前后移动少许,观察此回波幅度的变化,如果回波波高变化较大甚至消失,即为干扰波,若回波幅度较稳定,应进一步判定其是否为裂纹回波。
(7) 检测完毕后,将检测区域擦拭干净,对除漆部位及时进行局部补漆;发现缺陷回波信号时,还须及时做好记录。
4 磁轭法检测
4.1 检测影响因素
由于法兰盘检测部位形状不规则,使用磁轭法检测时两个磁极不容易放置,而且两磁极会与检测表面产生间隙。随着接触面间隙的增大,法兰盘表面磁场强度会产生损失,同时还会在接触部位产生相当强的漏磁场,漏磁场会吸附磁粉使得所在区域内的缺陷磁痕无法辨认而形成盲区。
另外,磁轭法为局部磁化方法,两极间的磁力线大体上平行于两极的连线,磁化区为一椭圆形,两极连线为短轴。磁化区内磁场强度的分布是不均匀的,在两极连线方向,两极附近磁场强,中心部位的弱;在垂直连线方向,连线附近的磁场强,远离连线处的弱。因此为了得到较理想的磁场,一是增大两磁极与法兰盘的接触面,二是检测区域尽量调整在两极连线的1/4和3/4处,远离两极端部并避开两级连线的中间部位,以避免盲区的影响以及磁痕堆积。
4.2 检测步骤
将两磁极放在被检法兰盘的表面,并施加一定压力使两磁极与被测件良好接触。按下按钮开关,开始磁化;松开开关,磁化结束。在打开磁轭开关的状态下,将磁粉施加于被测件表面,为保证检测灵敏度,采用黑色油基磁悬液。
因法兰盘检测部位为一圆形,磁轭法检测时应分段磁化,且区段间的有效部位须有一定重叠。
5 检测实例
在起落架周期性检测工作中,运用超声表面波对法兰盘进行检测,发现两例主起落架法兰盘R5圆角处裂纹,长度分别约为42,23 mm。其中一例波形显示如图4所示,可以看出,显示屏显示缺陷回波距离始波大约20 mm,由于显示屏水平扫描线与声程之比为2∶1,因此缺陷实际位置离探头前沿约10 mm,即位于R5过渡圆角起始处。采用磁轭法进行复检验证,证实了缺陷所处位置,磁痕形貌如图5所示,可见其磁痕浓密且两端尖锐,证明该缺陷为裂纹。综合分析裂纹的发展趋势,以及法兰盘受交变扭转剪切力的特点,判定该裂纹属疲劳裂纹。
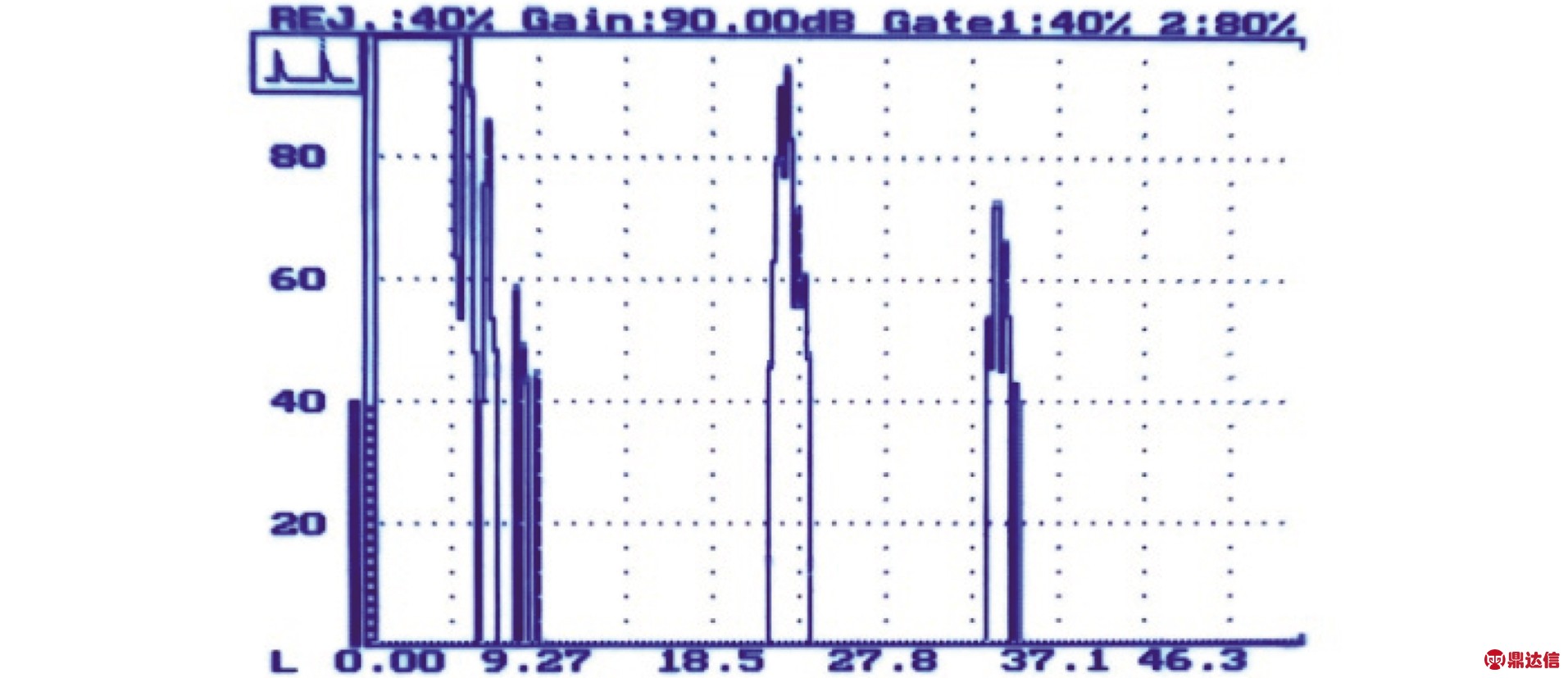
图4 带缺陷回波波形示例
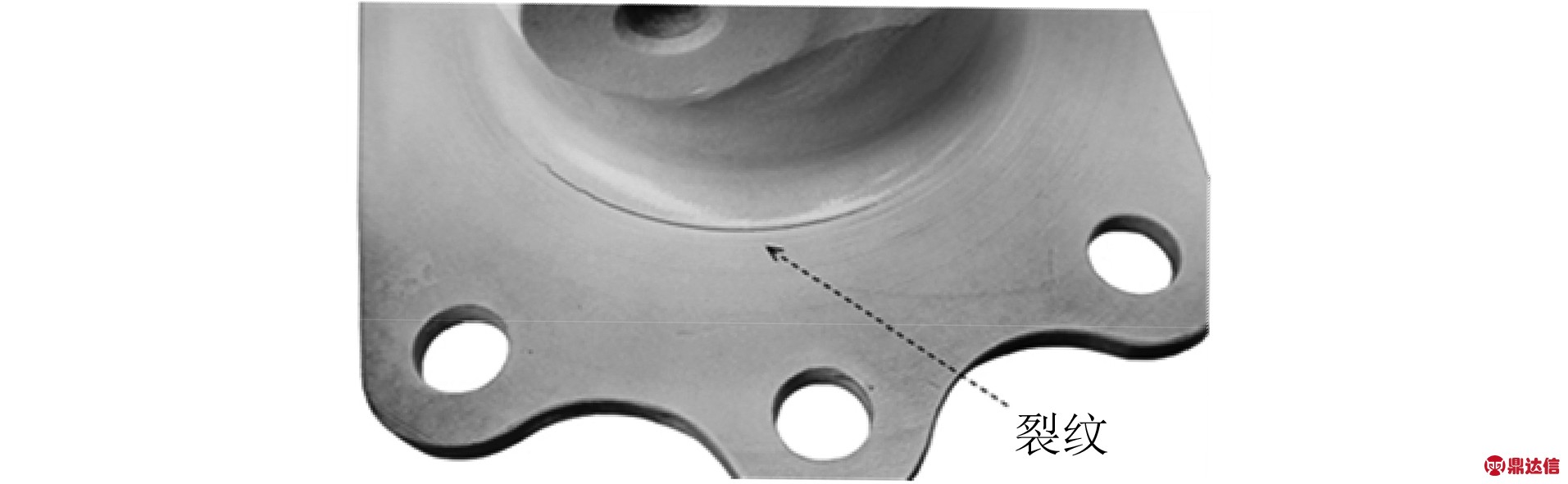
图5 法兰盘裂纹磁痕形貌
6 结语
法兰盘机件的检测试验表明表面波检测技术能有效应用于某型飞机主起落架法兰盘表面和近表面缺陷的检测中,该技术具有检测灵敏度高和工件预处理少等优点,既能保证检测的安全可靠性,又能避免因过多拆卸和打磨工件保护层可能导致的工件损伤,从而降低工件拆装成本,提高检测效率。