摘 要:在圆形堆取料机设备制作后,整体发运条件限制较多发运困难,为保证各自制作的部件配合精度,使现场安装顺利,预先在工厂内部进行先行预组装,提前发现及避免遗漏的问题,让设备在现场减少装配单元,提高现场安装效率,而提出的一种在工厂内预装范围要求的方法。
关键词:圆形堆取料机;预组装;合拢精度
1 设备概述
圆形堆取料机是一台对原料进行均化处理、储存及输送等操作的散料设备,放置于圆形钢结构堆棚中[1]。主要由堆料机钢结构、悬臂胶带机、堆料回转部、下部中心料斗、门架钢结构、取料行走机构、取料俯仰机构、刮板取料机、附属结构等部分组成。
一般此类设备的部件都在设备使用场地内进行合拢安装,但经常会发生螺栓孔对不齐、合拢口面板错位、辅钢安装干涉、铰孔错位等现象,从而造成了现场返修困难,工时的浪费。为了缩短在使用现场的安装周期及提前识别合拢产生的问题点,提出了在制造厂内预先进行预合拢方法。
基于场内及发运条件限制,本文主要讨论为保证某圆形堆取料机(见图1)的制作精度,满足设备使用及现场安装的顺利安装,通过提前对圆形堆取料机钢结构部分结构进行场内预组装来解决现场合拢精度问题的方法。
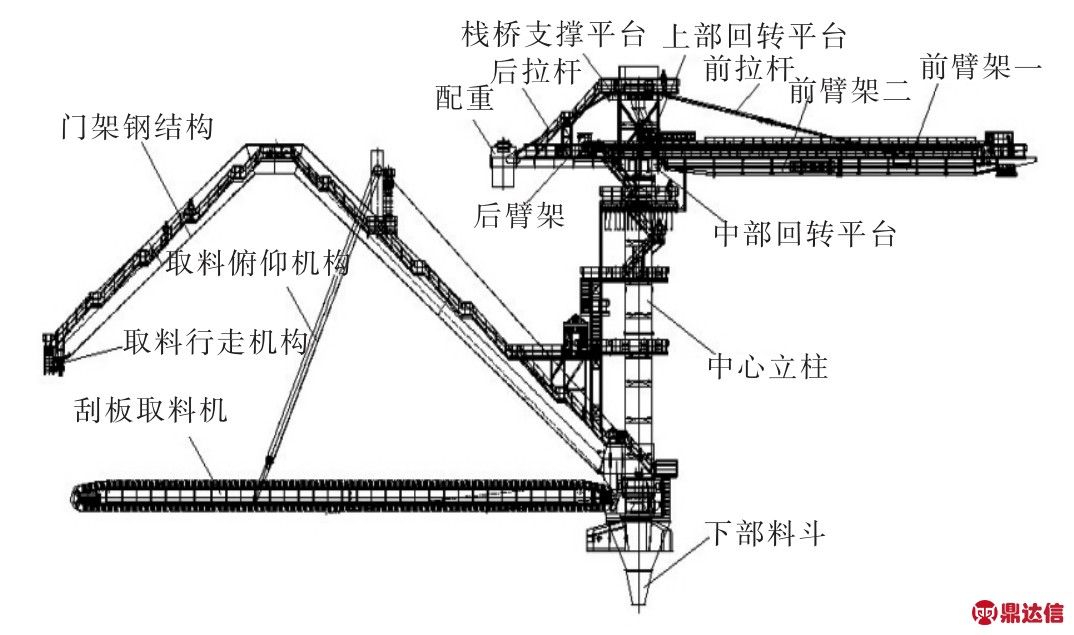
图1 某圆形堆取料机总体布置图
2 钢结构构件部分的预组装
如图1所示,设备的钢结构件主要指堆料机钢结构、悬臂胶带机、堆料回转部、下部中心料斗、门架钢结构、取料行走机构、取料俯仰机构、刮板取料机、附属结构等部分。
所有预组装部件的尺寸和精度要求必须符合GB50205-2017标准。由于整机合拢现场时的精度要求,对于中立柱轴线的偏差不应大于1.5 mm,现场圆形轨道半径偏差控制在6 mm以内,任意6 m范围内高低偏差控制±1 mm,极限偏差3 mm,机架(含门架、立柱、前后臂架、拉杆、回转部等)安装后相对中心线最大偏移值不大于8 mm,铰轴中心线与机架中心线的垂直度允差不大于2 mm。
结合上述要求,对于工厂内合拢时需控制堆料机钢结构、回转部个平面度都必须控制小于1 mm以内,门架合拢后必须检测中心轴线至连接行走处的尺寸控制在5 mm以内,前后臂架轴孔同轴度不得大于2 mm,与臂架中心线垂直度不大于±1.5 mm,臂架纵向中心环线应与整体纵向中心环线重合,且在同一垂直平面中,其偏差不得大于5 mm。其余部件精度按照下述部件合拢详细要求执行。
2.1 堆料机钢结构、堆料回转部、胶带机的预组装方案
1)堆料回转部的预组装:上部回转平台(重约8.423 t)、上部回转框架(重约5.028 t)、中部回转平台(重约12.382 t)进行预组装,预组装后需检查螺栓孔的对正情况,保证螺栓能顺利穿入,由于机械加工后的接合面是精基准,所以接合面的平行度是保证柱体直线度的必要条件,因此法兰平面间隙需小于1毫米[2]。见图2(需拆开单独发运)。
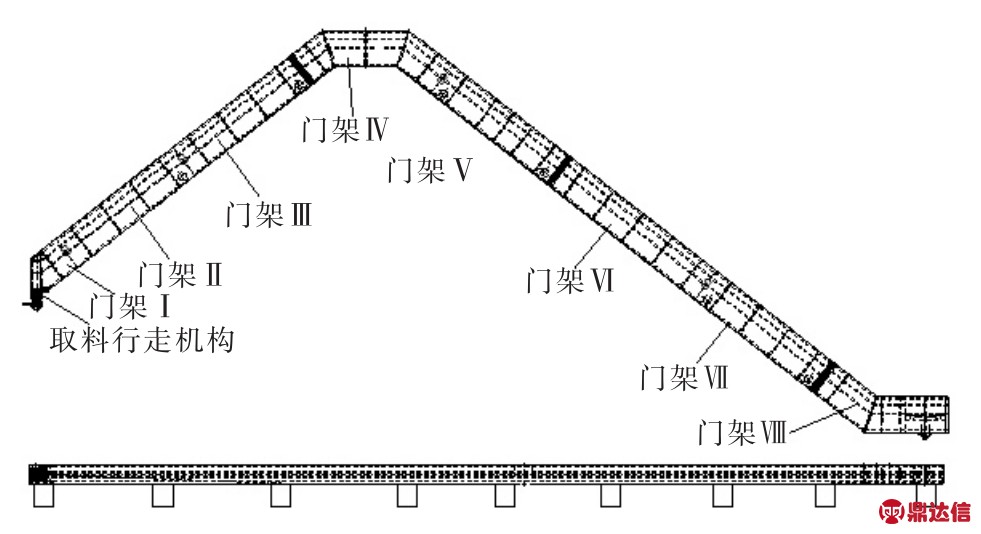
图2 堆料回转部图
2)回转框架上下工8个支撑面法兰先单独机加工,上面四个法兰板与上部回转平台的四角支撑面机加工后配钻打孔,并使用工艺螺栓将配钻的法兰拧在一起,下面四个法兰面与中部回转平台的四角支撑面机加工后配钻打孔[2],见图3。
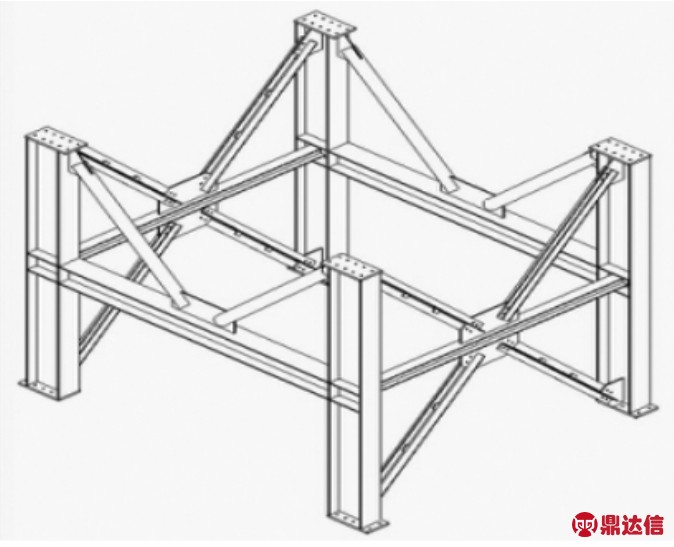
图3 回转框架
2.2 前臂架、后臂架与堆料回转部联接铰预组装
1)堆料回转部(重约 25.833 t)、前臂架(重约18.407 t)、后臂架(重约8.442 t)、前拉杆(重约5.3 t)、后拉杆(重约1.739 t)进行预组装见图4(需拆开单独发运)。
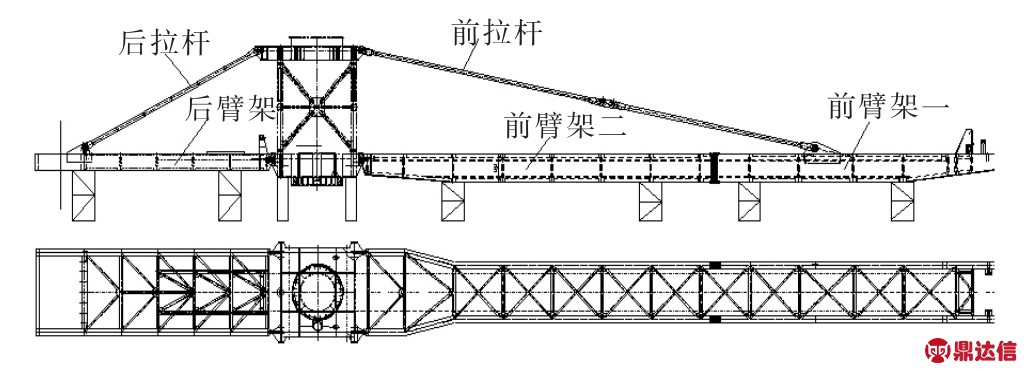
图4 前、后臂架与堆料回转部预装图
2)先将前臂架与后臂架吊放在已调好的水平高度的胎架上,使其中心与地样线相重合,检查铰轴应能顺利装配,且臂架中心与回转中心吻合,铰座间隙适当,无卡阻。
3)前拉杆、后拉杆的铰轴点与上部回转平台和中部回转平台铰轴点组装,前臂架和后臂架铰轴点预组装,铰轴应能顺利装配.见图5(需拆开单独发运)。
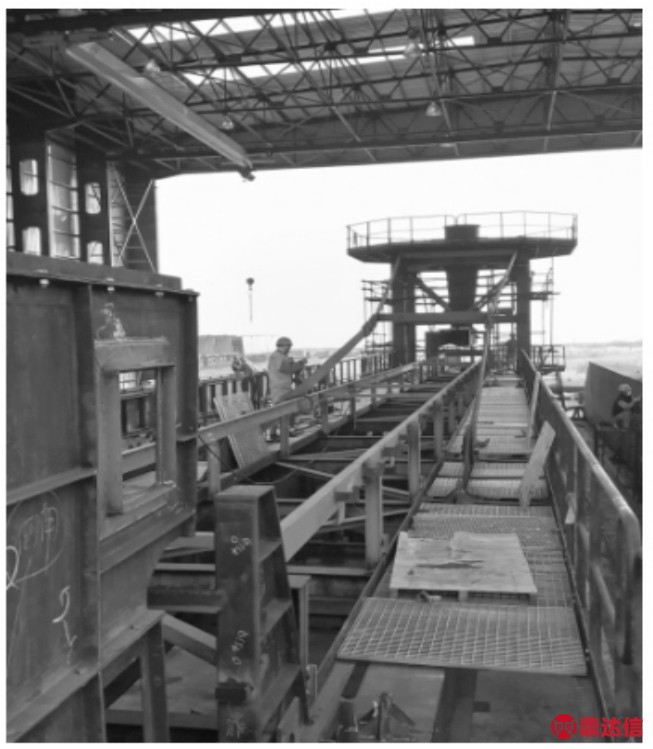
图5 预装实物图
4)前后臂架轴孔同轴度不得大于2 mm,与臂架中心线垂直度不大于±1.5 mm,全长范围内的最大旁弯量不大于5 mm。注意检查臂架纵向中心环线应与整体纵向中心环线重合,且在同一垂直平面中,其偏差不得大于5 mm。中部回转平台、前臂架、后臂架三者构件上的上平面应在同一水平面中,其前后臂架前后两端不得有下垂现象。左右两侧后铰座应在同一垂直平面内,偏差≤2 mm。
2.3 回转大轴承的预组装
1)上部回转轴承(重约1.55 t)、上部回转平台(重约8.423 t)、上部栈桥支撑平台(重约8.354 t)进行预组装。见图6(需拆开单独发运)。
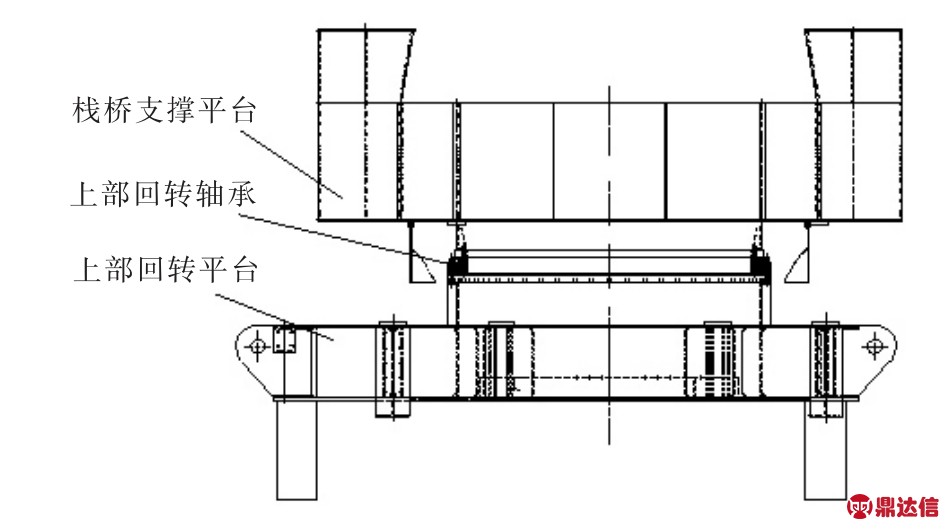
图6 上部回转大轴承的预装图
将上部回转平台吊放在已调好的水平高度的胎架上,并依次吊装上部回转轴承和栈桥支撑平台,检查大法兰螺栓孔与回转轴承的对正情况。
2)中部回转轴承(重约2.48 t)、中部回转平台(重约12.382 t)、中部回转驱动装置(重约1.262 t)进行预组装。见图7~图8(需拆开单独发运)。
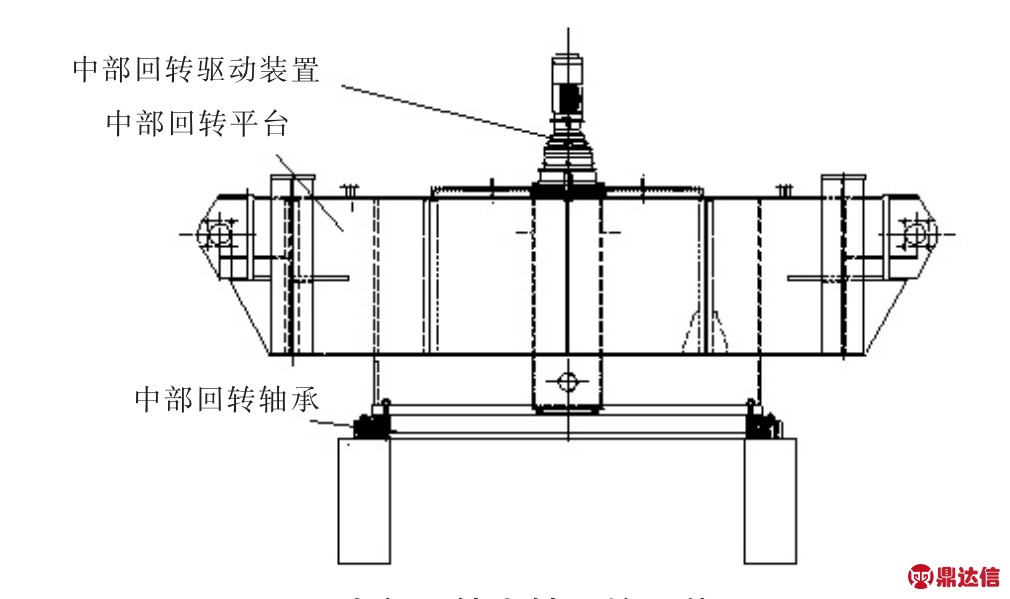
图7 中部回转大轴承的预装图

图8 预装实物图
3)将中部回转平台吊放在已调好的水平高度的胎架上,并吊装中部回转轴承在其上,检查大法兰螺栓孔与回转轴承的对正情况。将中部回转驱动装置预装,检查小齿轮和大齿圈的啮合是否符合传动要求,保证齿轮啮合间隙及啮合重合度(小齿轮齿顶圆与转盘轴承外齿轮齿根圆间隙1~1.5 mm,啮合重合度≥90%[3])见图9。
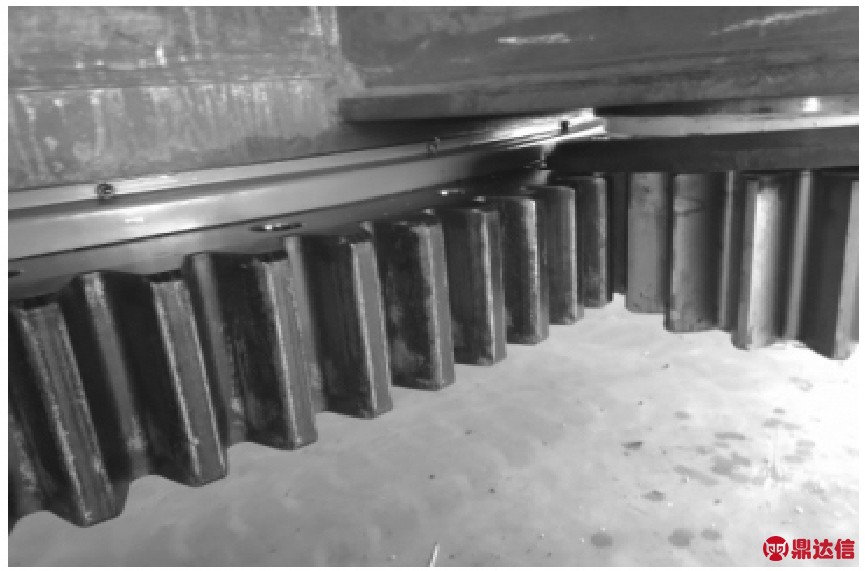
图9 现场实物图
2.4 门架钢结构的预组装方案:
1)门架ⅠⅡⅢ(重约20.849 t)、门架Ⅳ Ⅴ(重约16.221 t)、门架Ⅵ Ⅶ(重约 14.78 t)、门架Ⅷ(重约8.5 t)、取料行走机构(重约7.221 t)进行预组装。见图10(需拆开单独发运)。
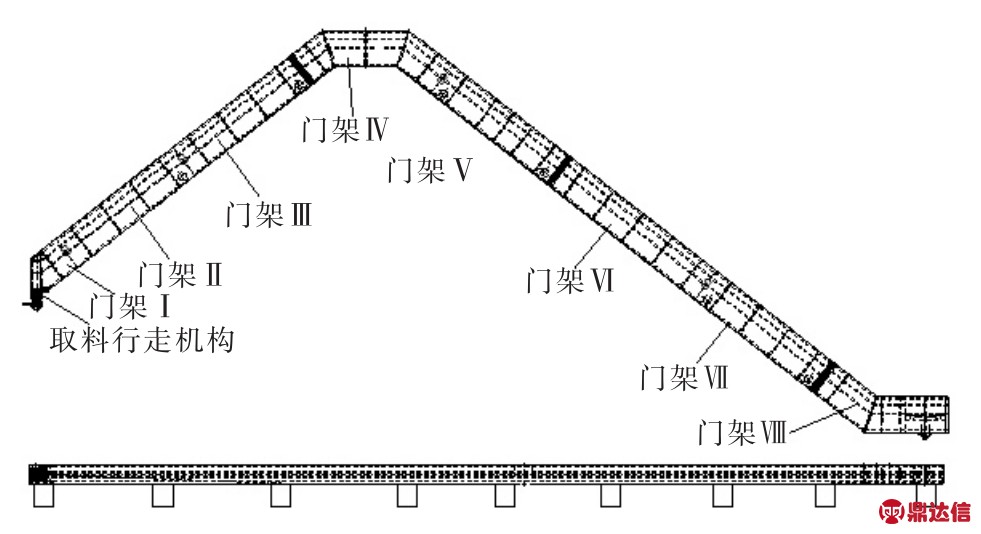
图10 门架预装图
2)整个门架为左右对称结构,预组装时分别将门架两侧箱体梁进行单独合拢,按工艺次序依次吊放在已调好的水平高度的胎架上侧躺进行预合拢,检查高强螺栓连接处对正情况,并检查门架角度是否和地样线重合,将行走机构的上部平衡轴承旋转90°进行预组装,查看与门架下部螺栓孔对正情况,以及车轮行走半径的尺寸,控制在±5 mm以内。
3)各平面分段制作说明如图11所示。
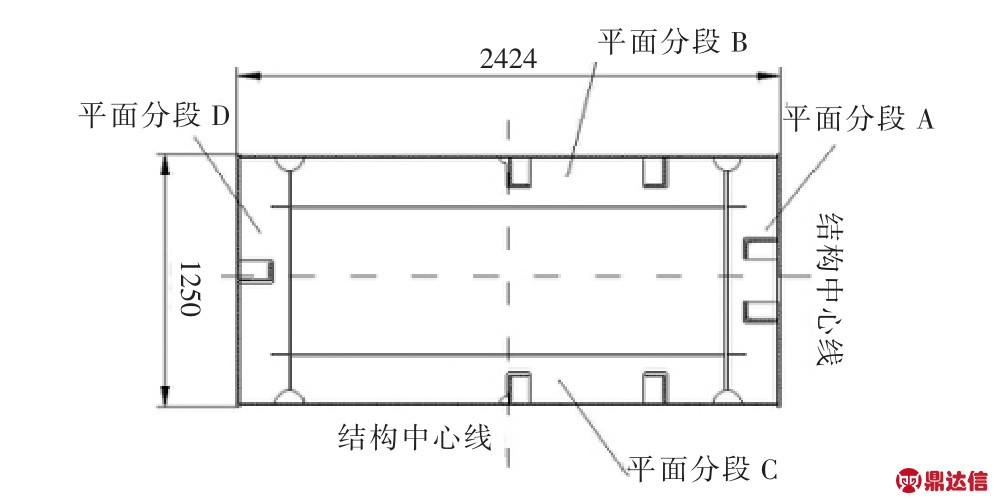
图11 各平面分段制作图
如图12平面分段制作时的定位基准线为结构中心线;
4)根据立体分段的结构形式,平面分段A,D制作时需要划出分段B,C在其上的装配定位线。并在分段端部进行洋冲标记,便于装配;
5)A立体分段的制作在专用胎架上进行,胎架为搁墩式,胎架水平±2mm;
6)B根据门架钢结构的结构形式,立体分段制作时采用侧躺制作,以平直的腹板面为基准(平面分段C),定位时以横梁的结构中心线为基准线。在平台上划出结构中心线、平面分段A,D的装配定位线以及横搁板的装配定位线(如图12)。
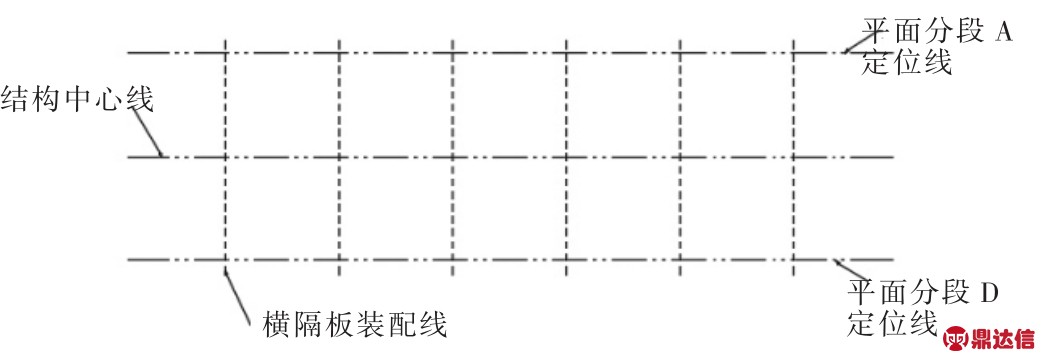
图12 定位基准线图
7)立体分段的装配顺序如下:
吊装平面分段C→用吊锤检测中心线是否与地线一致→点焊固定在胎架上→吊装横搁板→吊装平面分段D并定位点焊→吊装平面分段A并定位点焊→吊装平面分段B并定位点焊,装配结束后检验平面分段C和B及A和D的中心线是否在一个水平和垂直平面内,分段C和B可以用测量水平的方法检测,分段A和D可用悬挂吊锤的方法检测,允许误差±2 mm.测量整体尺寸,允许误差±4 mm,对角线差5 mm,平整度≤4 mm/m,整体10 mm以内。
2.5 刮板取料机机架的预组装方案
1)梁一(重约 9.148 t)、梁二(重约 16.103 t)、刮板轨道系统(约13.307 t)进行预组装。见图13(需拆开单独发运)
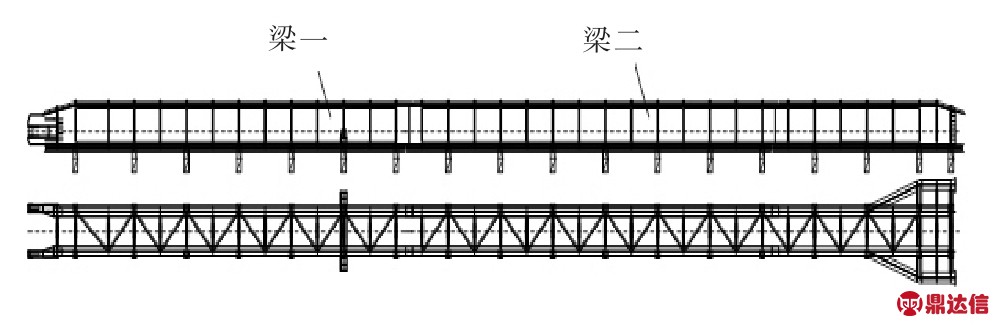
图13 刮板取料机机架预装图
2)整个刮板机架为桁架结构分三段组成[4],预组装时按工艺次序依次吊放在已调好的水平高度的胎架上进行预合拢,并检查机架和架体中心线是否和地样线重合,并检查各轨道是否满足运行要求。
3)梁一、梁二、轨道系统三者旁弯不得大于5 mm,左右两侧后铰座连接板应在同一垂直平面中偏差≤2 mm,两条轨道安装位置及对刮板机纵向中心对称度公差为3 mm,同一截面的两条导槽的高度差≤2 mm。
4)轨道系统的制作安装须在机架制作完成后进行,机架的上部与下部各3个轨道,共6根轨道,其中4根轨道均为角钢与耐磨板焊接,见图14。
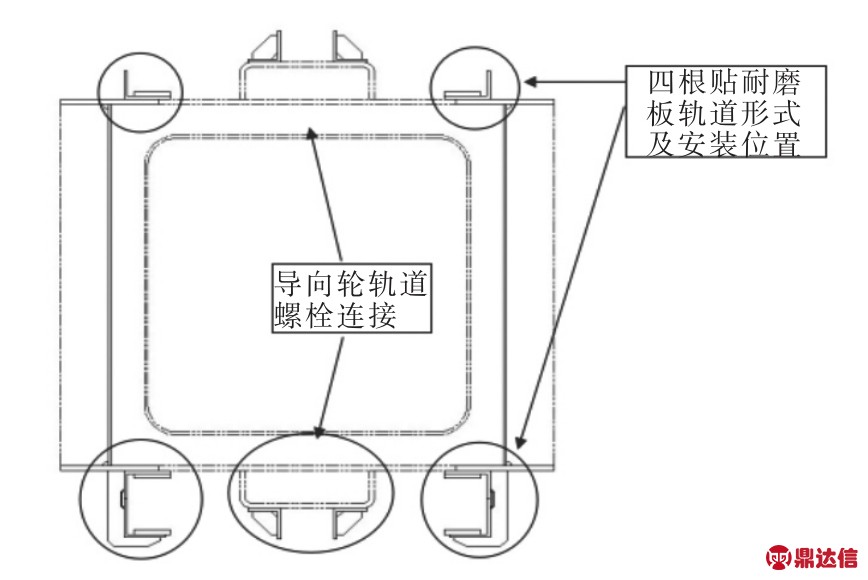
图14 轨道安装图
5)每条轨道在全长(约50 m)范围内垂直度,平行度误差不得大于5 mm,每条导轨直线度公差0.5/1000,最大不超过5 mm,两条导轨安装位置对刮板机纵向中心线对称度公差小于3 mm,同一截面的两条导轨的高差小于2 mm,实物图示15~图16。
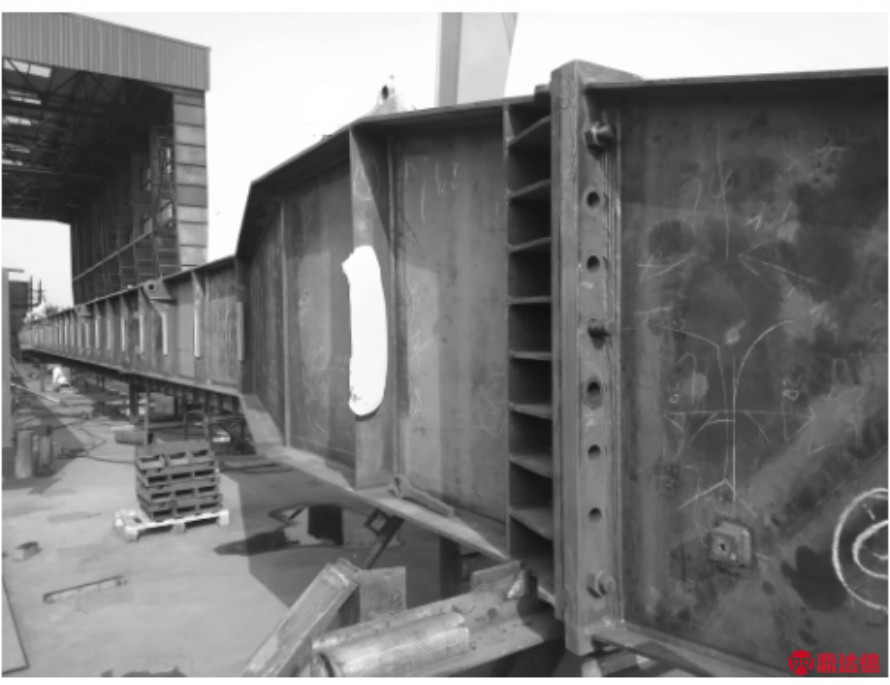
图15 刮板取料机机架现场实物
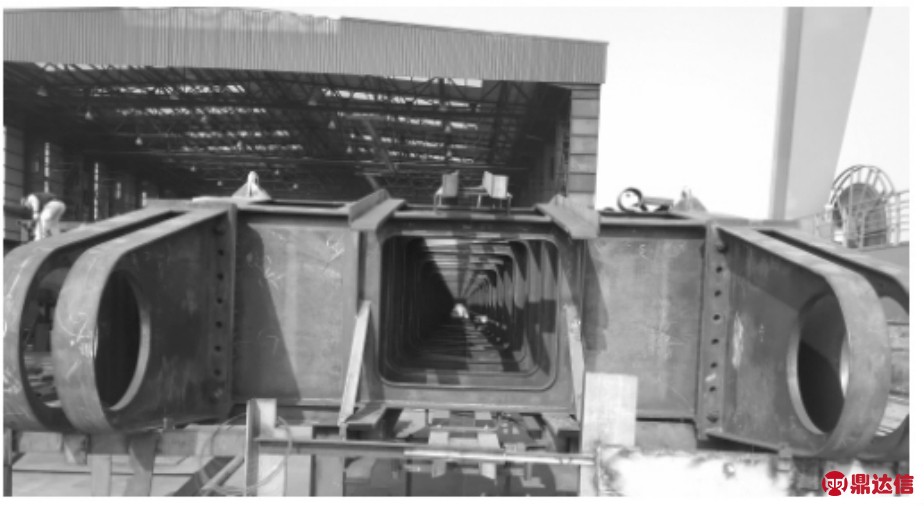
图16 刮板取料机机架现场实物
6)下部两侧轨道形式为两根角钢两根耐磨板组成,每个分段的轨道由两到三部分拼接(拼接处处理与上部类似),先整体装配好不进行焊接,待装到架体上时再进行焊接,为了控制变形焊接需严格焊接顺序如下图,并在内部每隔500 mm装配卡板,以保证开档尺寸,见图17。
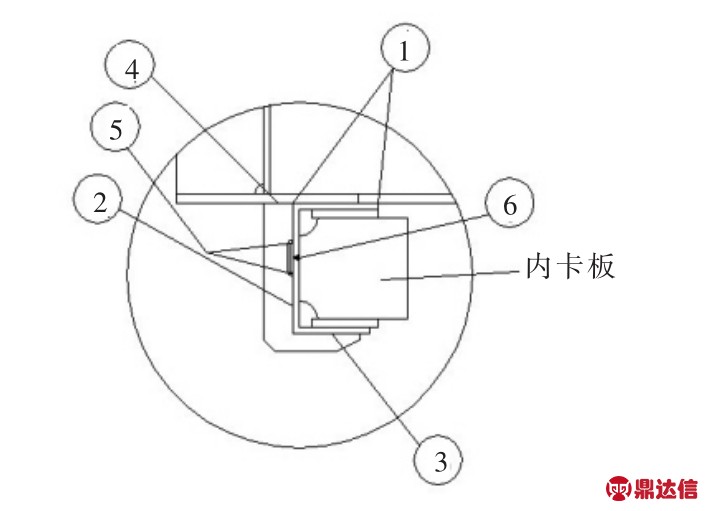
图17 隔板安装图
3 结束语
通过上文描述的预装方法提前在制造厂进行预组装,与以往的项目相比较,有效地减少了设备安装现场的合拢时间,完成整个项目缩短了7~10天的周期,并提前识别和规避了合拢现场所产生的问题,以往发生的异常现象如螺栓孔错位、对接合拢缝错位、辅钢干涉等均未发生。该方法实施后,有效地利用了厂内资源,提高了各部件的精度配合,减少了现场工作量以及有效地缩短了工期,提高了工作效率,证明该方法是有效的。