随着空间研究、开发与应用需求的不断提高,模块化航天器设计已经成为航天领域的热点 [1],航天器模块化设计是将航天器系统分散成一系列功能独立的模块单元。采用模块化设计的航天器,其通用平台和有效载荷均由不同功能的标准化在轨可更换模块组成。航天器出现故障后,只需对故障模块实施在轨更换。同时,多个模块在轨组装能够形成大型、应急型任务航天器,摆脱了当前运载工具对航天器规模的限制,大大缩短了航天器响应空间任务所需的时间。模块化的航天器设计理念具有广阔的应用空间,将会对航天器的应用方式、应用方法产生巨大的影响。模块制造加工完成后,如何能够快速、有效地将其送入太空进行应用及空间存储,是完成在轨模块更换任务的前提条件 [2-3]。在美国的快速响应体系中存在着这样的平台:美国空军的次级有效载荷适配器环;NASA的多样有效载荷释放器 [4]。它们安装在火箭适配器与发射主卫星之间,利用剩余空间装配多个功能不同的组件发射进入太空。这种平台提供了一种新的发射模块、小卫星进入太空并在轨释放分离的理念,能够有效利用火箭剩余空间进行发射,节约了成本,提高了发射效率。但是其结构复杂,通用性差。本文将主要针对如何利用火箭有效运载多模块进入太空进行研究。针对模块搭载所需的搭载适配器进行结构设计及有限元分析,设计一种结构简单、通用性好的搭载适配器方案,为实现模块的火箭搭载提供支撑。
1 搭载适配器应用方式
搭载适配器携带模块进入太空进行存储,是基于在轨服务概念的具体应用,可以理解为:通过搭载适配器将模块发射进入太空,并完成空间模块存储,航天员或者服务航天器能够利用存储模块通过模块更换、模块组装改善提高航天器的性能。模块的捕获存储过程主要有2种方式。
1) 服务星空间捕获。搭载适配器与火箭和主卫星分离后,机动变轨进入停泊轨道,空间服务航天器接收命令并进行机动变轨。当搭载适配器和服务航天器进入有效跟踪距离后,地面人员对搭载适配器发送信号。然后,搭载适配器启动自身的释放装置将各模块依次弹出,服务航天器利用其机械臂对模块进行捕获,并存储到自身的托盘存储装置中。搭载适配器自身也可以整体被服务航天器捕获。
2) 空间站存储。搭载适配器脱离主卫星与火箭后,机动变轨靠近空间站附近。当搭载适配器进入空间站机械臂的捕获包络内,地面遥操作人员或者机械臂自身根据运动规律,抓取搭载适配器。抓取完成后,可将搭载适配器通过机械臂运载进入空间站内部,搭载适配器将模块自主弹射分离,根据模块自带的射频信号进行识别,按模块类型对其进行分类存储,方便任务时的选取。
2 搭载适配器结构设计
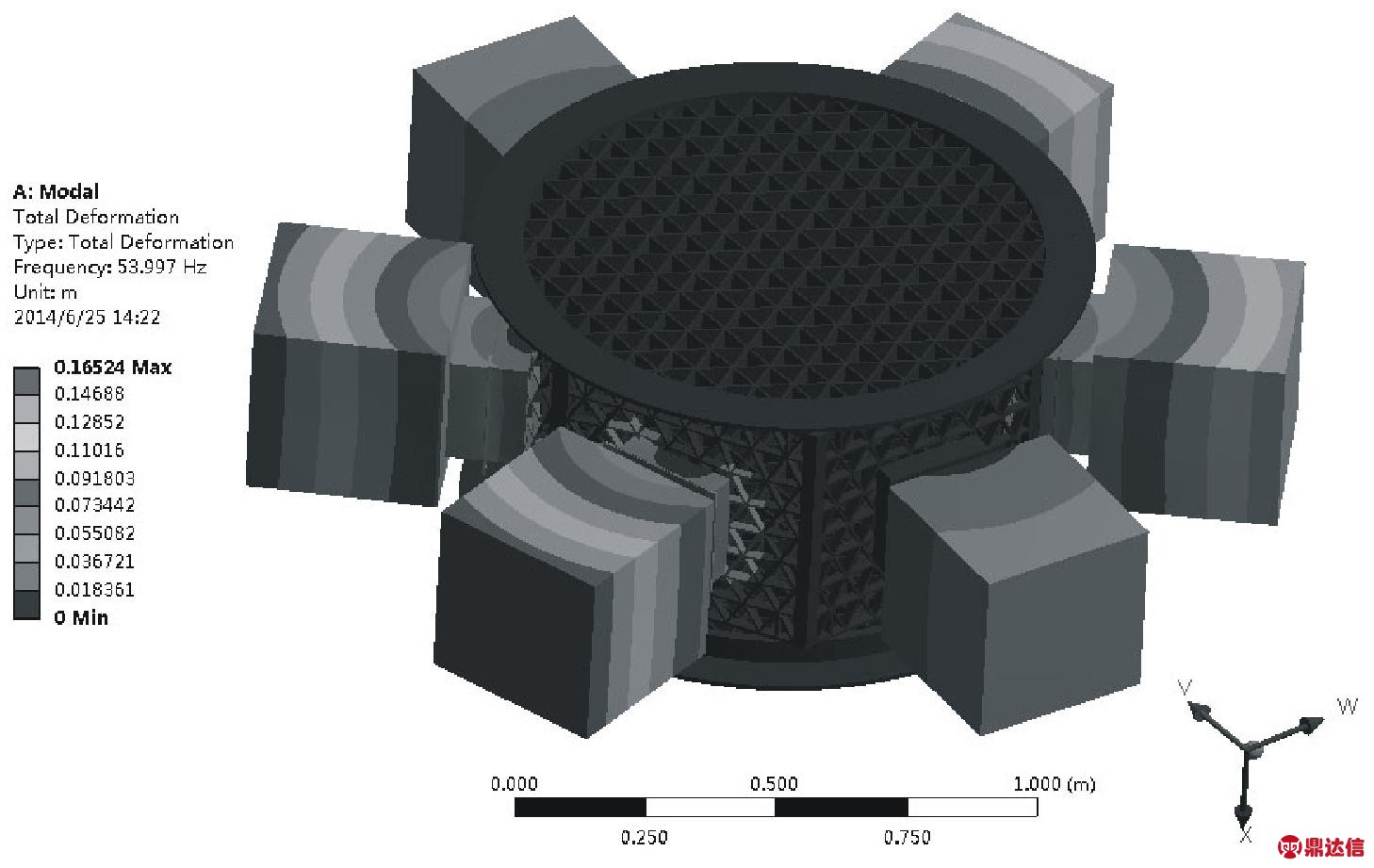
图1 搭载适配器详细结构
搭载适配器具体结构如图1所示。由搭载适配器箱体、搭载适配器接口装置、模块接口装置和模块组成。搭载适配器采用六边形网状栅格,便于设备安装。模块装配时,首先将搭载适配器接口装置、模块接口装置分别集成在搭载适配器和模块上,然后将2个接口装置进行连接即可装配完成。这种结构降低了整体重量,且易于模块安装,对航天器不会产生影响。
2.1 箱体设计方案
典型的航天器结构主要包括杆系结构、中心承力筒结构、蜂窝加层板结构等 [5]。杆系结构分为钢架结构和桁架结构。杆系结构在航天器的构型应用中起到十分重要的作用,它可以作为航天器的主承力结构、骨架结构、支撑结构、设备的连接固定结构,符合本文搭载适配器的结构设计理念。其中,杆系结构又分为钢架结构和桁架结构。本文只进行初步设计,所以将其当作桁架结构进行处理分析 [6]108-112。整个搭载适配器结构将每部分做成独立单元,同时达到能够快速集成、组装的目的。共包括侧板、顶板、底板和板间连接件4部分。
1) 侧板。侧板是搭载适配器的主承力结构,其他部件均安装固定在侧板结构上。因此侧板设计时必须满足一定的强度和刚度。同时为了方便安装搭载适配器的接口装置以及内部诸如成像载荷等外伸装置,在侧板中央预留一个六边形的框架。桁架结构的设计采用三角支撑型,进一步提高了侧板的整体稳定性。侧板上在肋结构的节点处冲制螺孔,便于安装内部、外部设备。同时侧板上还加工有销钉定位孔和螺栓定位孔,用于与板件连接件的固定连接。这些标准化的定位安装孔,极大地缩短了集成安装时间。
2) 顶板、底板。底板与火箭适配器相连接,顶板与卫星适配器相连接。顶板、底板的设计结构相同,选用铝合金锻件整体加工而成。顶板与底板的设计同样采用肋板式结构。既满足了机械结构的刚度和强度要求,同时能有效地减轻整体重量。顶板和底板与侧板之间通过螺钉进行固定连接。
3) 板间连接件。侧板与侧板之间采用专门设计的连接件进行固定连接。其大小由侧板的尺寸决定。连接件具有定位销孔、集成螺母安装孔等结构。本文设计的搭载适配器结构是由6个侧板组成的正六边形结构,因此连接件的夹角为120°,连接件与侧板之间通过螺栓螺母进行固定连接。集成时,通过正确匹配连接件与侧板的定位销孔,通过螺栓连接将2个组件固定安装在一起。
综上所述,对搭载适配器结构进行建模,模型的外尺寸由火箭整流罩尺寸及火箭适配器结构尺寸决定,但是外形一定要规则。搭载适配器能够在6个侧板上安装接口装置,并加装模块。
2.2 对接接口装置设计方案
反对称式异体同构中心式对接结构,是对接双方拥有相同的基本部件和接口,且双方在对接过程中都既能充当主动方也能充当被动方。对接时,接口装置的探杆和容纳孔分别与对方的容纳孔和探杆互相容纳,实现连接。此种对接方式设计简单,且容易满足对准精度要求。
搭载适配器与模块之间的接口设计,是为了达到统一标准,方便不同模块按需集成,且在搭载适配器装载模块与火箭分离后,搭载适配器本身可以在轨道将模块释放,同时模块上的接口装置可与存储机构对接固定。因此,一个简洁、统一的接口装置就成为搭载适配器设计的重要问题。反对称式异体同构中心式接口装置符合设计要求。
对接接口板应由圆柱凸轮/圆柱筒、电子接口、探针/锥型筒、射频卡、微动开关等组成 [6]202-205。
探针/锥型筒结构主要导引机械臂操作路径,校准2个对接接口板,克服机械臂操作误差。电子接口采用电源、数据接口一体化结构设计,实现电源与数据接口互连互通,对接和分离所需要的插拔力由圆柱筒/圆柱凸轮提供。圆柱筒/圆柱凸轮结构主要功能是提供电子接口所需插拔力,完成2个对接接口板机械固定。2个接口板处于机械固定还是分离,由滚子是否位于圆柱凸轮表面沟槽内决定。射频卡用于存储模块基本信息,方便模块存储时,存储装置能够读取功能模块的基本信息。微动开关主要是向控制计算机/航天员提供状态信号,确认接口装置成功对接,起到连接到位指示作用。
这样的设计方案,搭载适配器与模块之间的接口装置的设计与安装将会完全一样,可以实现搭载适配器与模块的组装对接。对接接口板的Pro/E仿真模型建立结果如图2所示。
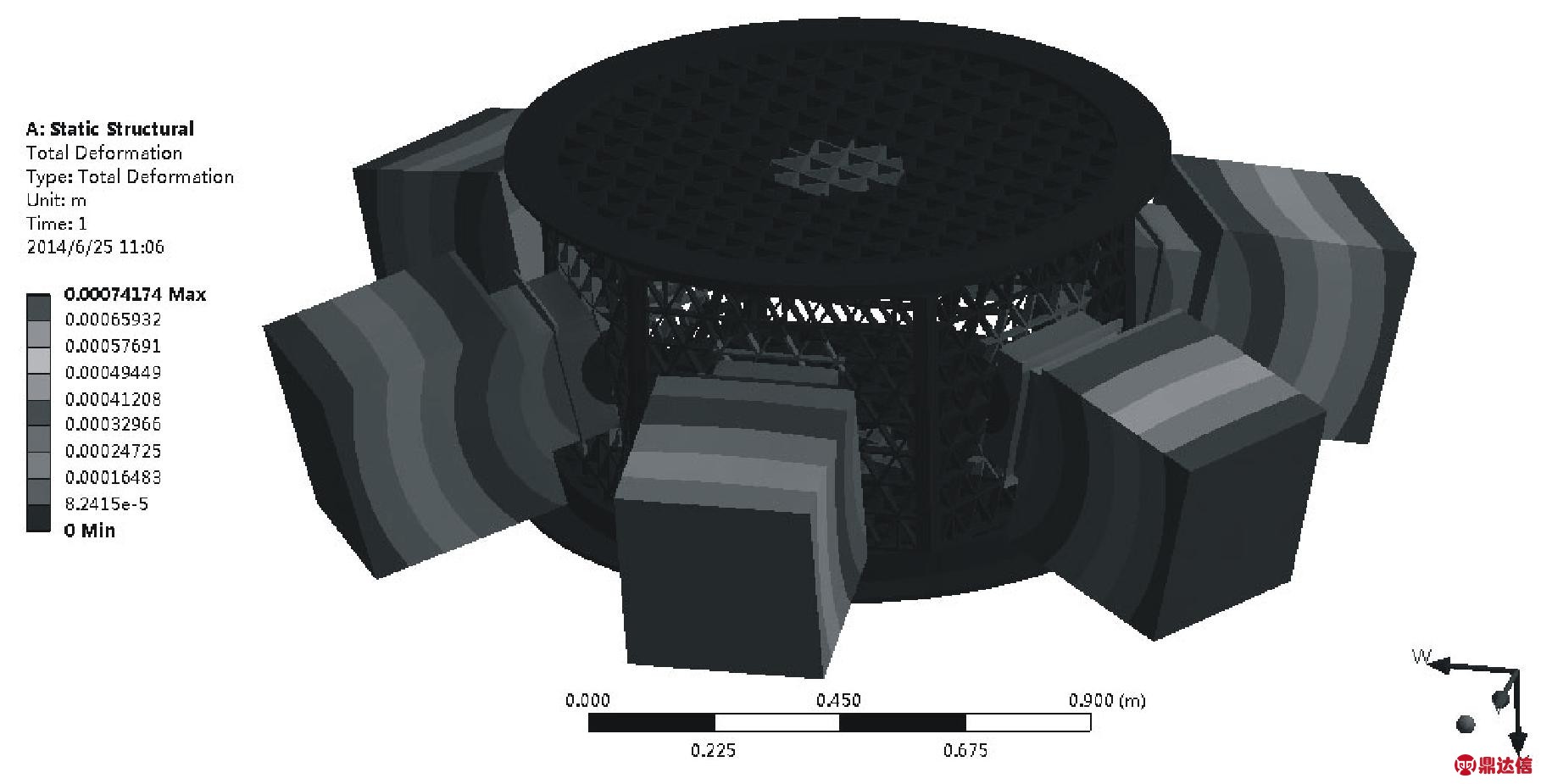
a) 搭载适配器接口装置 b) 模块接口装置
说明:1—圆柱凸轮/圆柱筒;2—探针/锥型筒;3—电子接口;
4—微动开关;5—射频卡;6—弹射装置
图2 接口装置示意图
因搭载适配器需要将模块弹射分离,故只需在与搭载适配器相连的接口装置内安装分离弹簧装置即可。
2.3 弹射机构设计方案
为了实现搭载适配器在空间可以自主释放发射模块,在对接口板进行设计时,需要考虑加装弹射分离装置。目前分离装置主要有弹簧、火工分离推杆、火工锁和分离火箭。搭载适配器分离模块时所需推力并不是很大,且不希望分离后会对两者产生较大的姿态影响,因此选择弹簧作为分离装置。弹簧结构简单,性能可靠,不会产生污染。将弹簧作为分离装置,是利用弹簧本身的弹性,在产生变形和复原的过程中,可以把机械功或动能转变为变形能,也可以把变形能转变成机械功或动能。通常为了提高弹簧分离时的精确与可靠,在弹簧上加装一套弹簧分离推杆,可减小弹簧侧向分力和轴线力矩对分离的影响。图3为设计的弹簧分离推杆,它由弹簧、内套筒、外套筒、调整螺母和顶杆组成。外套筒固定在与搭载适配器相连的接口装置内,内、外套筒接合面为滑动面,涂覆固体润滑液。分离时,内套筒在弹簧力的作用下向外滑动实现分离。调节螺母可以在一定程度上调节弹簧压紧高度,实现分离力的微调。顶杆采用球头设计,保证弹射分离时搭载适配器与模块之间不存在自由度约束。
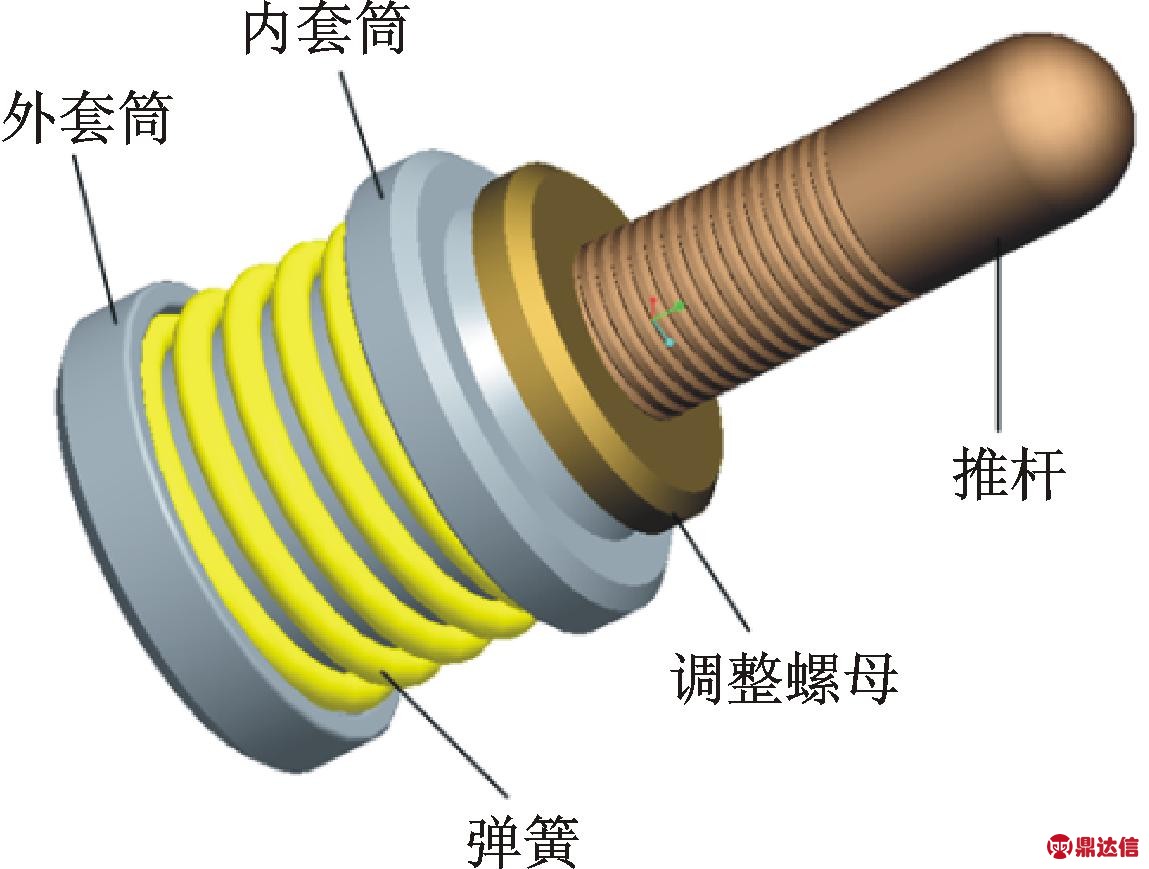
图3 弹射机构
当2个接口板对接时,弹簧分离机构位于与搭载适配器相连接口装置箱体内。当搭载适配器接受分离控制指令后,对接接口板刚性解锁,电动机带动圆柱凸轮/圆柱筒结构进行转动,2个接口板组件分离。在这个过程中电动机同时带动弹射机构上升,保证顶杆与对接接口板的相对位置和弹簧压缩量。当圆柱凸轮/圆柱筒机构分离完毕后,在弹簧的带动下,模块被弹射机构弹出,进入空间。分离过程如图4所示,分别演示了分离前、分离中和分离结束后的状态。
在设计的圆柱螺旋压缩弹簧中,选取弹簧中径 D 2=10.5 mm,弹簧直径 d=2 mm,弹簧最大压缩量 λ max=5 mm,选择碳素弹簧钢丝C级中应力弹簧。根据弹簧直径由GB/T 1239.6—1992查得抗拉强度 σ b=1 710 MPa。选取弹簧许用切应力[ τ]=680 MPa。最终计算得到弹簧分离力在0~157 N之间,满足空间分离力所需。
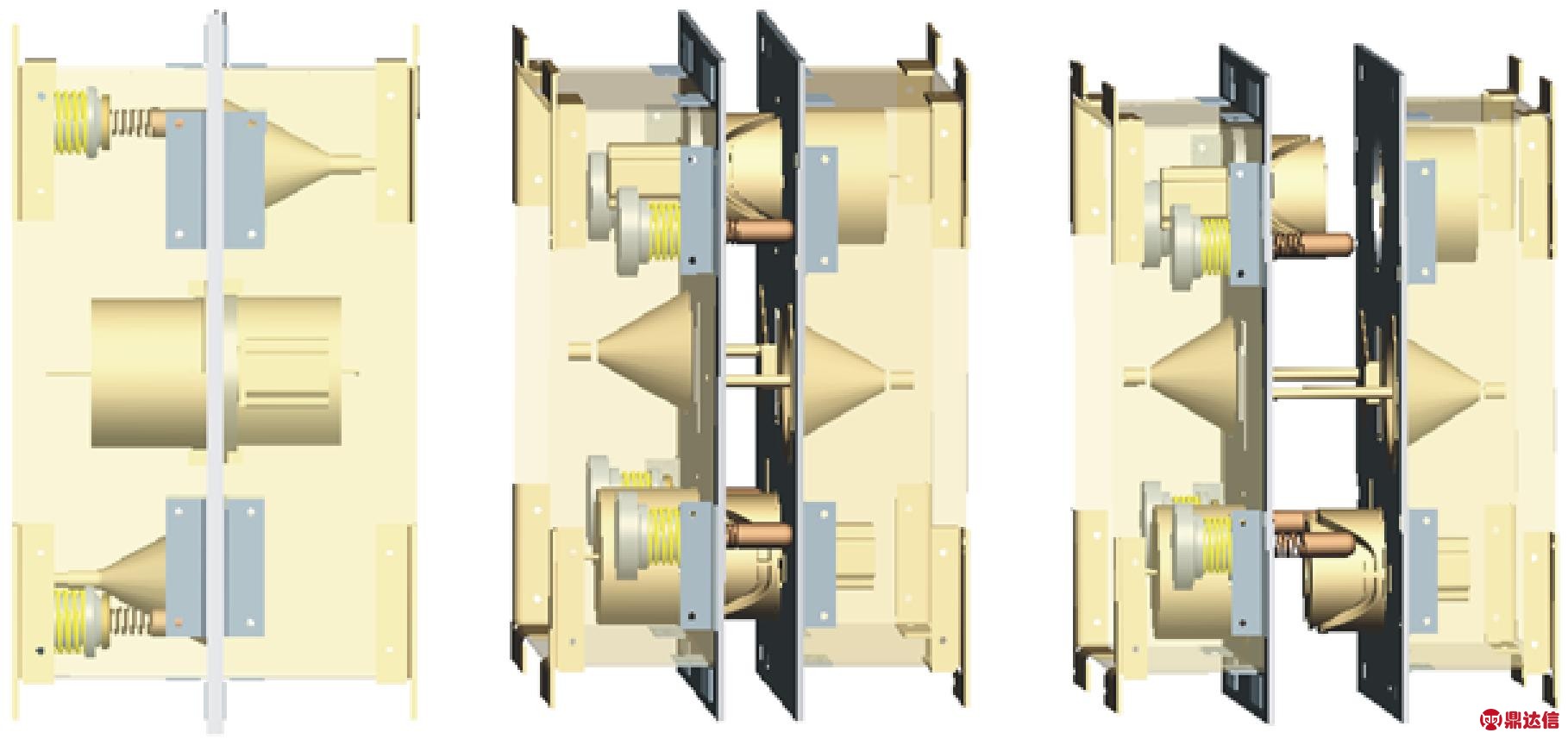
a) 分离前 b) 分离中c) 分离后
图4 弹簧分离推杆分离过程
3 有限元分析
考虑到搭载适配器发射过程中受力稳定性问题,将搭载适配器集成安装完毕后,对其整体进行结构分析。由于ANSYS软件和Pro/Engineer软件之间具有数据接口,同时ANSYS具有强大网格划分、加载求解、后处理等功能,因此使用ANSYS软件进行结构分析 [7]。结构材料采用铝合金,杨氏模量70 GPa,泊松比为0.33,密度2 770 kg/m 3,考虑火箭发射加速度问题,对其施加10 g n恒定加速度,要求在过载条件下搭载适配器满足要求。
静力学分析是计算结构在固定载荷作用下的响应,它不考虑阻尼和惯性的影响。通过静力学分析,可以得到结构内部的应力分布,检验结构的刚度和强度是否满足设计的要求 [8-9]。
搭载适配器在火箭整流罩内固定安装,因此,在ANSYS中需要在搭载适配器上板和下板边框位置添加固定约束,添加载荷进行分析后,得到过载条件下箱体和添加模块后的变形云图和应力云图分别如图5、图6所示。箱体结构的最大变形发生在上板与下板的中间部位,其最大变形量是6.720 3×10 -5 m,受到的最大应力是3.776 1×10 6 Pa;添加模块后的最大变形出现在模块外侧,最大变形量是7.417 4×10 -4 m,受到的最大应力是5.675 8×10 7 Pa。均小于铝合金的材料屈服强度75 MPa,且变形较小,不会对结构产生影响。可知,整体结构的设计符合要求。
模态分析是用来确定搭载适配器的振动特性,也就是确定其固有的频率和振型,确保结构设计避免共振或者让结构以特定的频率振动。通过模态分析,能够定性的预计搭载适配器上安装设备的工作环境,防止设备与搭载适配器之间因频率相近而产生过大的动态耦合载荷。同时也防止了整体作为载荷与火箭固连后的固有频率相吻合,造成破坏性的损伤。测量得到搭载适配器箱体和搭载适配器添加模块后整体的前两阶振型分别如图7、图8所示,其中箱体的一阶振频为288.12 Hz,添加模块后的一阶振频为53.997 Hz。满足设计要求。
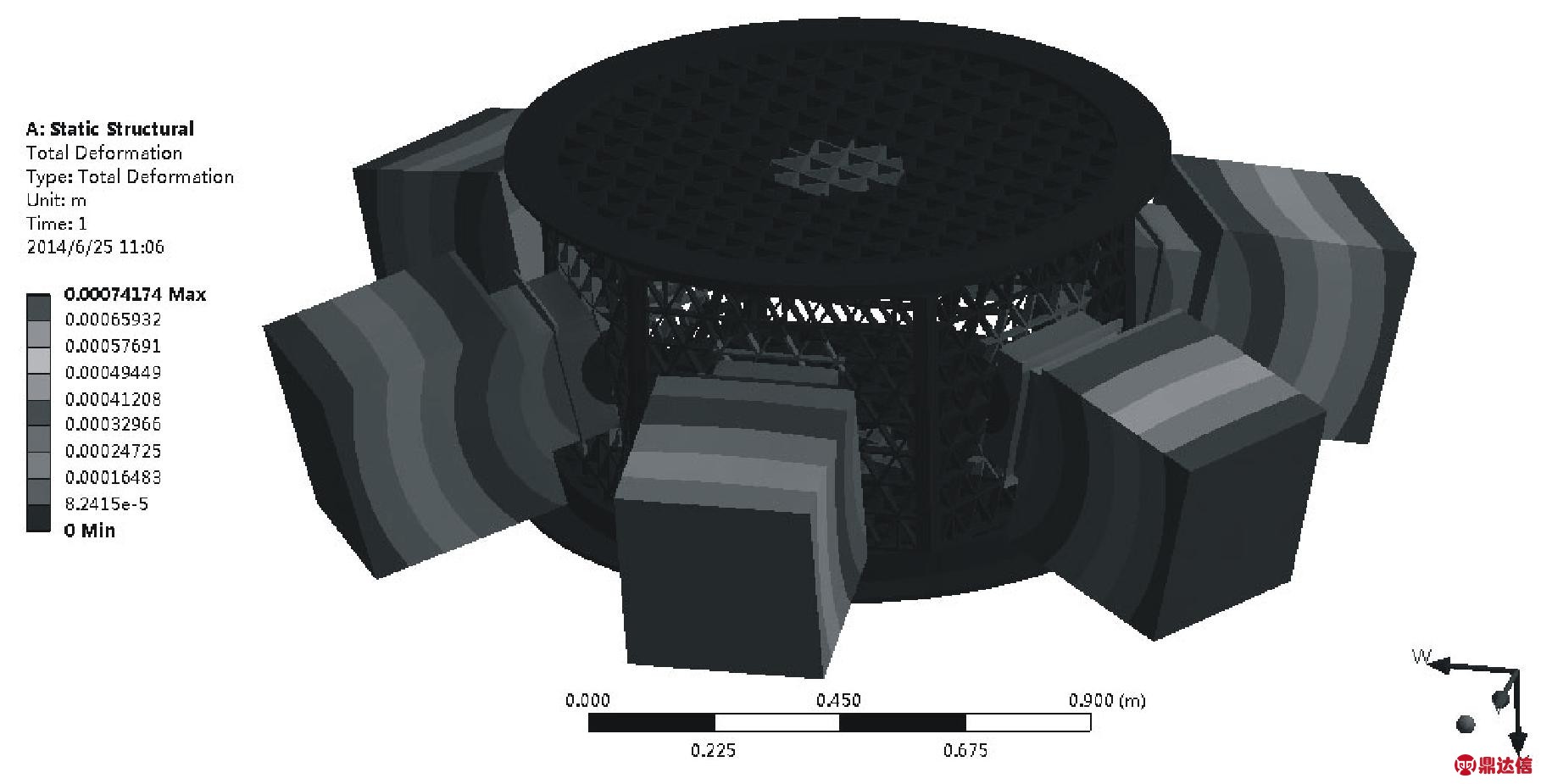
a) 变形云图
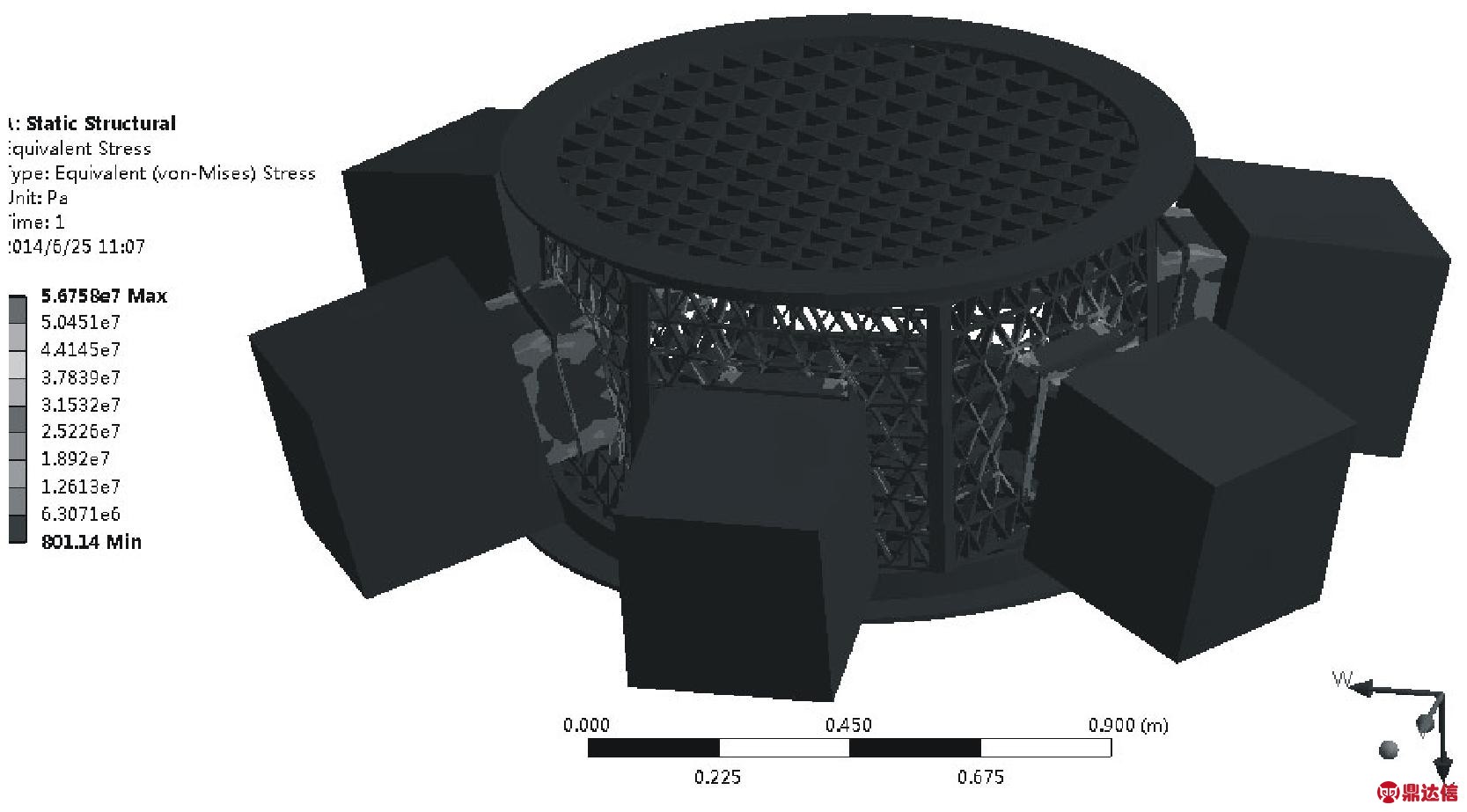
b) 应力云图
图5 搭载适配器箱体静力学分析
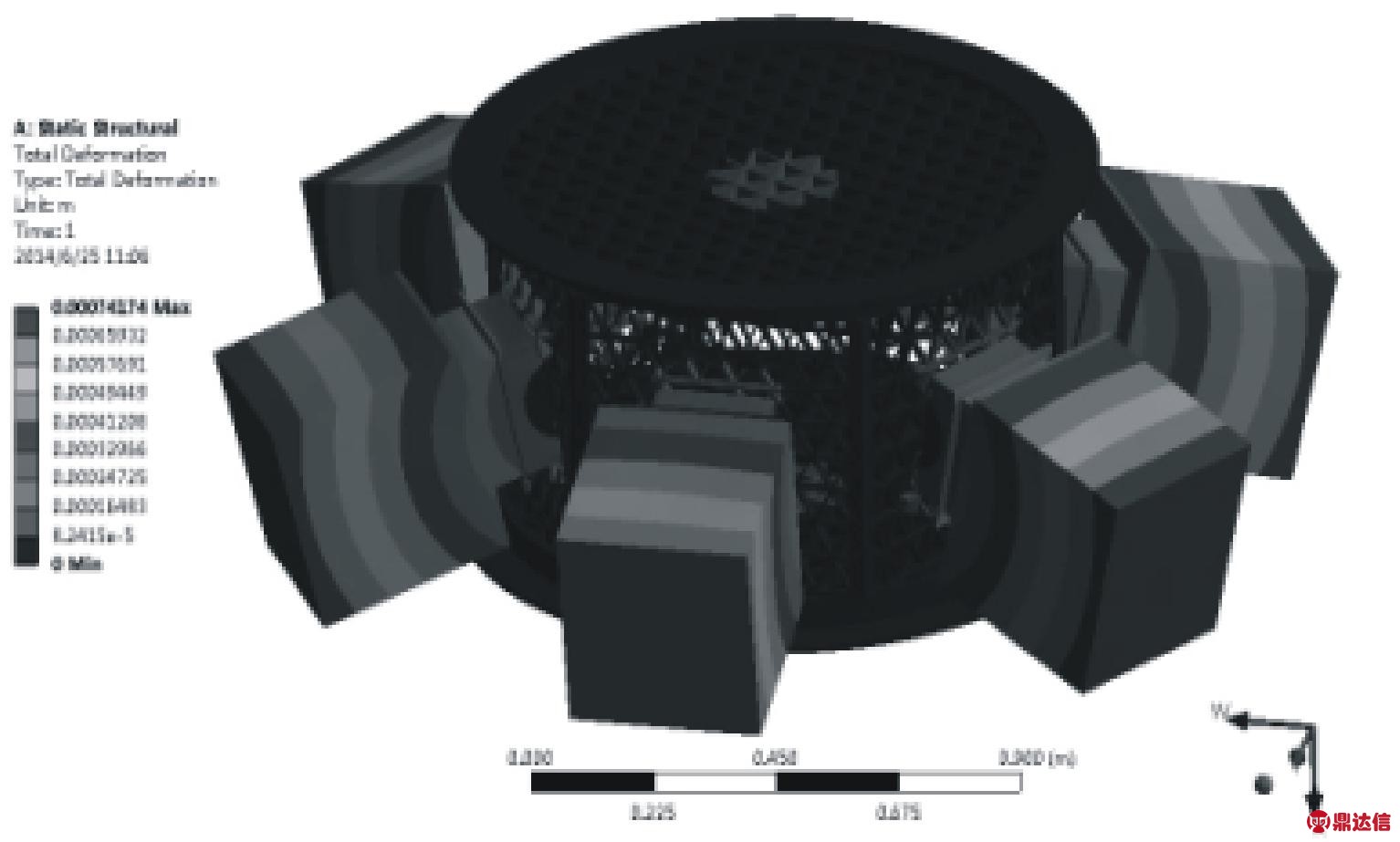
a) 变形云图
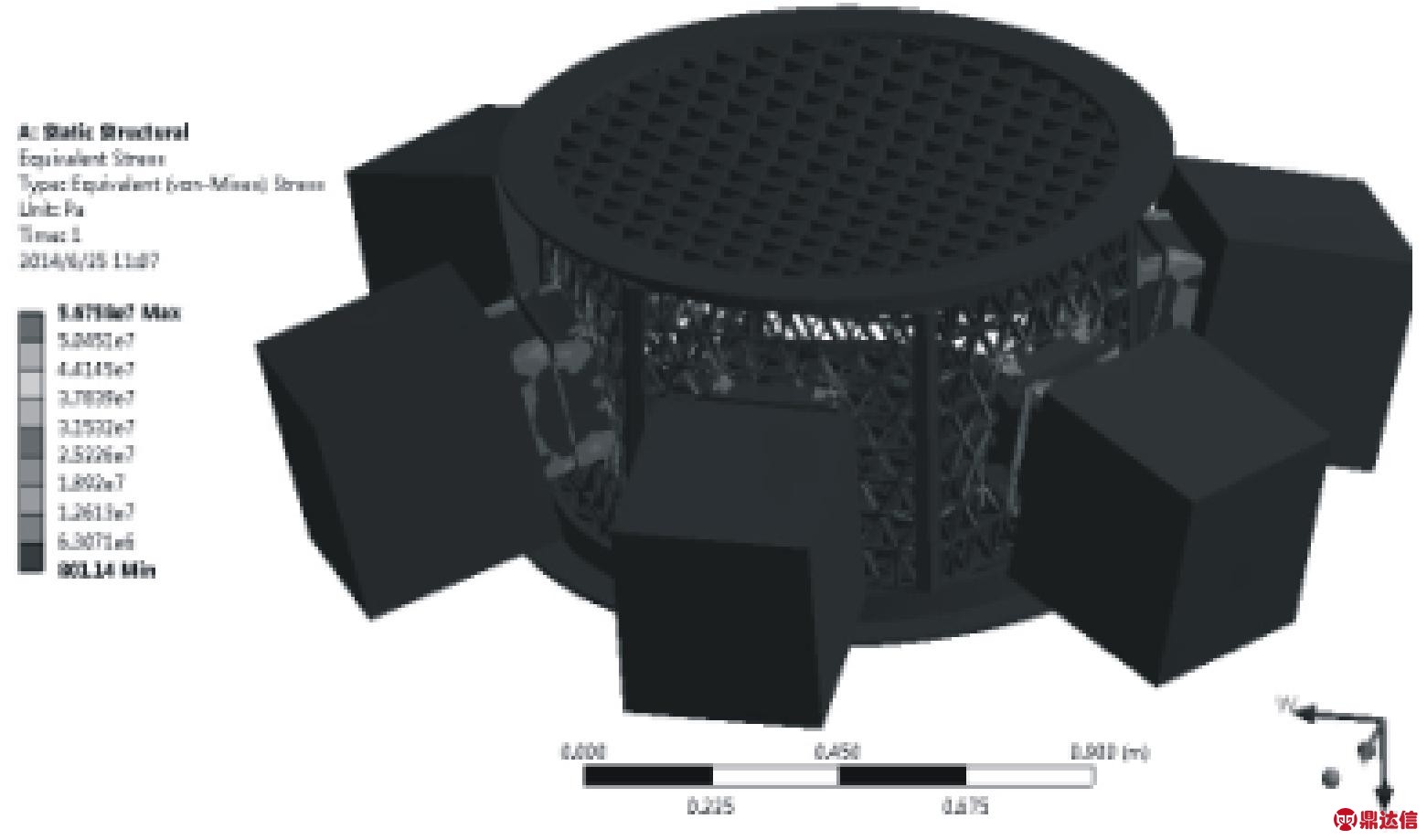
b) 应力云图
图6 搭载适配器添加模块后静力学分析
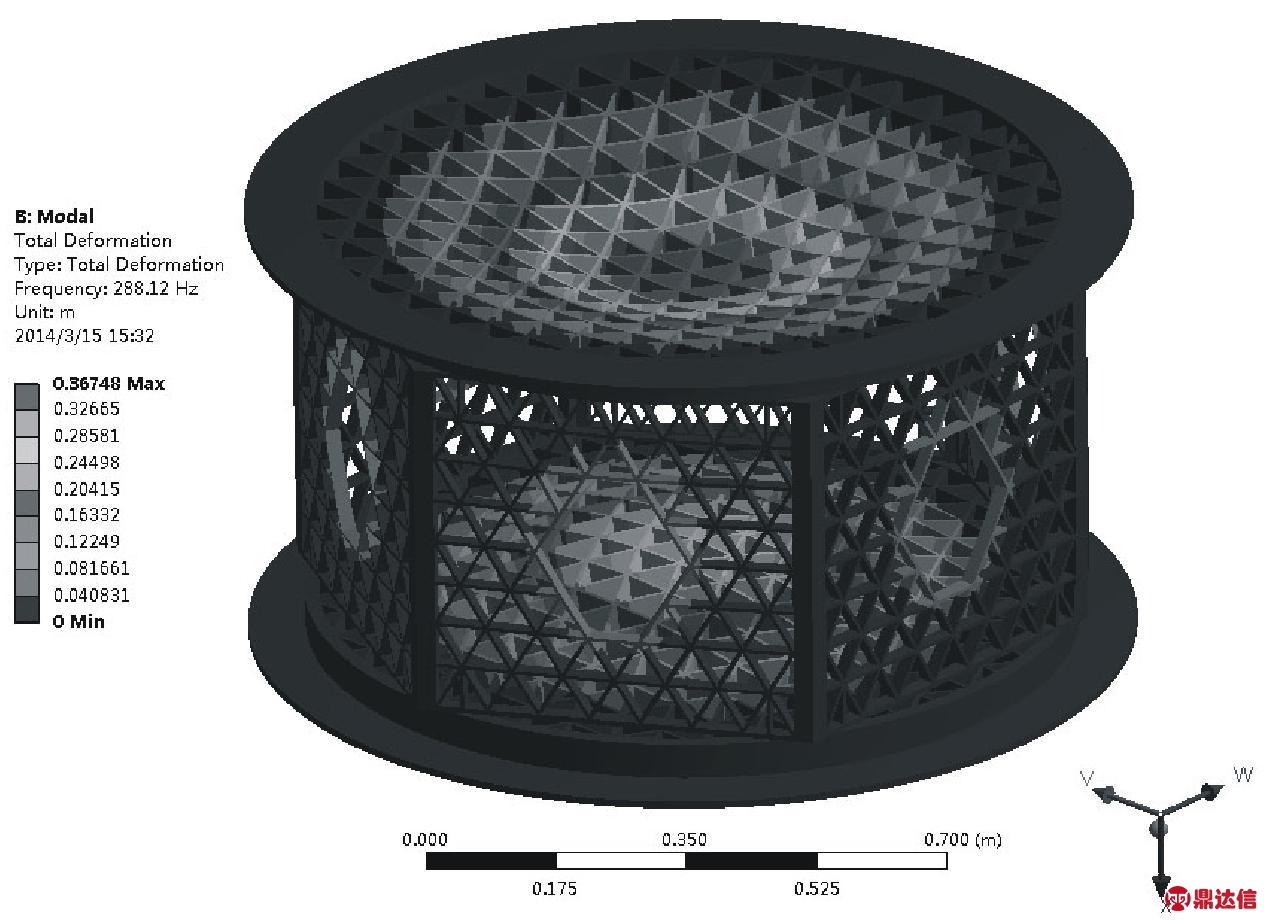
图7 搭载适配器箱体一阶振型
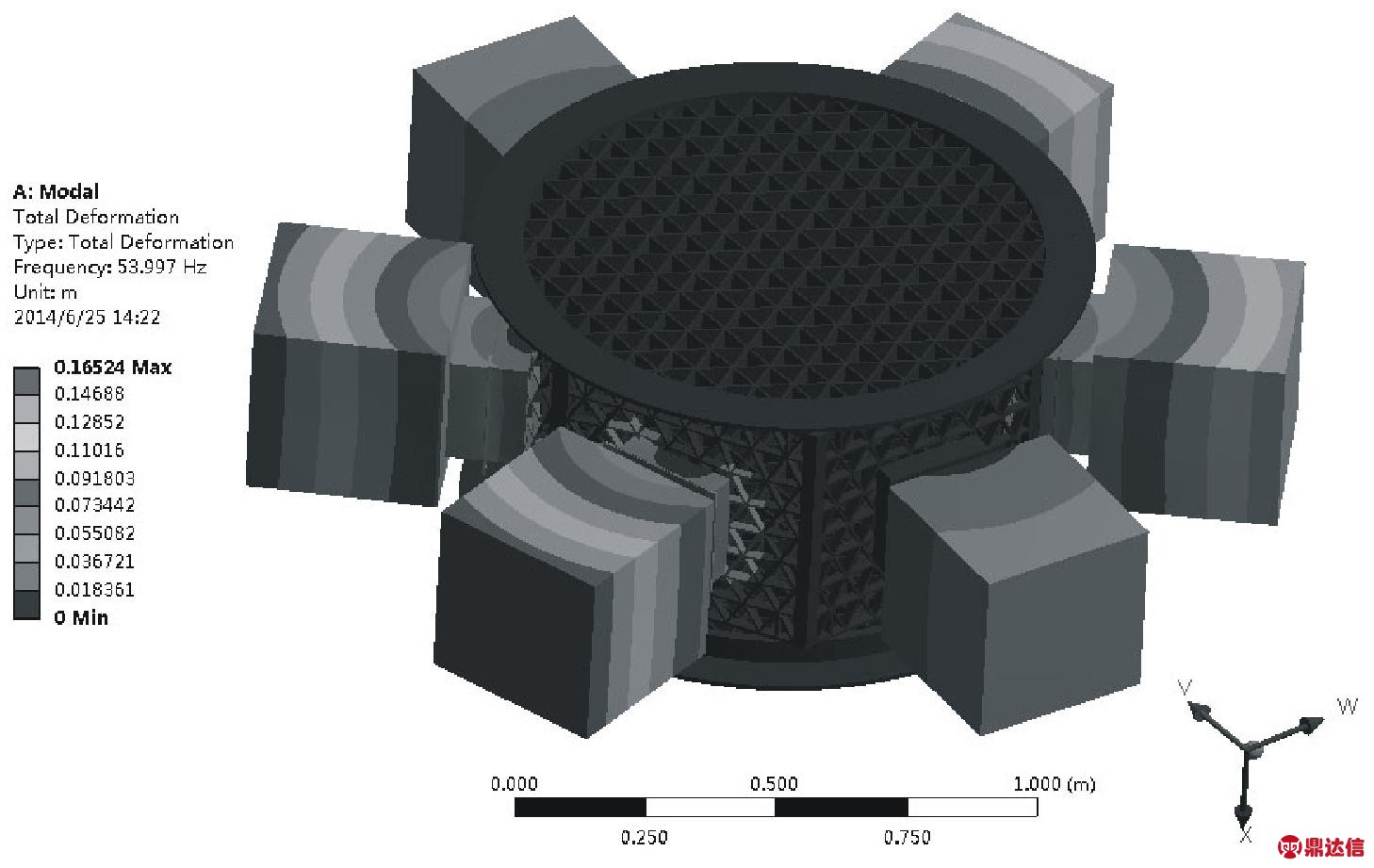
图8 搭载适配器添加模块一阶振型
4 结 束 语
在轨可更换模块技术是未来航天器和空间战术应用的重要发展方向,然而模块的设计应满足一系列的结构及空间设计要求。本文主要针对发射模块入轨的搭载适配器进行了结构设计和有限元分析,同时也介绍了搭载适配器的空间应用方式,并且搭载适配器的组成部件可按不同型号系列进行批量生产、库存,必要时可选择合适型号进行快速集成组装,标准化、通用化、系列化程度高。