摘 要:基于尿素选择性催化还原原理,利用计算流体动力学(CFD)方法,建立了柴油机尿素催化器CFD模型,模拟了在实际载荷工况条件下尿素-选择性催化还原技术(Urea-SCR)的尿素水溶液在排气管路中喷射雾化过程和喷射尿素颗粒的分布,得出柴油机的尿素喷射分布情况。研究结果表明:柴油机尿素SCR催化器的CFD模型能准确反映其尿素颗粒分布、浓度,可基本满足催化器对废气的催化条件,对带有尿素SCR催化器的柴油机的设计具有一定的指导意义,为缩短开发周期提供了方法参考和技术支持。
关 键 词:柴油机; 选择性催化还原; 喷射雾化; 计算流体动力学(CFD)
为了减少柴油机NOx的排放,国内外已经开发出了许多技术方案,以此满足更加严格的排放控制法规,其中尿素选择性催化还原(urea selective catalytic reduction,Urea-SCR)技术[1]是降低柴油机NOx排放的一种有效手段。在欧洲等发达国家和地区已经将Urea-SCR技术大量应用于车用柴油机的尾气处理中,从而降低柴油机的NOx排放。SCR技术具有良好的耐硫性,也被认为是我国实现废气排放标准的主要技术手段[2]。
由于我国地域辽阔,南北跨纬度近50°,温度、道路等环境差异较大,车用柴油机的分布区域较广,造成其运行工况复杂,且其排气的各项参数范围较大,因此车用SCR系统需要解决多种问题。较为关键的是系统中的管路布置和结构尺寸以及尿素喷射的合理控制[3-4]。
1 Urea-SCR系统
Urea-SCR系统主要由控制单元(ECU)、尿素泵(SM)、喷嘴(DM)、SCR催化器及相关液压管道和电线束组成。基本原理是将一定量的雾化后的尿素溶液注入排气管中,并在高温下热解和水解形成还原剂氨气(NH3),然后NH3在SCR中的催化剂作用下选择性地与废气中的NOx反应,产生氮和水,进而控制车用柴油机NOx的排放[5]。
2 SCR系统评价指标
2.1 均匀性系数
催化剂的速度与还原剂分布直接影响催化器的NOx转化效率[6]。催化剂的速度不均匀性体现在催化转化器中心区域的速度过大,导致其径向温度变化范围过大,进而产生变化较大的热应力,使催化转化器发生热疲劳损坏,并导致催化剂活性降低,降低催化效率。还原剂分布不均体现在催化转换器中的还原剂局部过量或不足,导致催化反应的转换率下降,降低NOx转化效率。
2.2 尿素颗粒直径分布
尿素液滴颗粒在排气管道中分布得越均匀,其与气体的接触面积就越大,越容易发生化学反应,提高SCR的转化效率,还可以防止液滴聚集。液滴聚集导致其贴附在管道壁上,进一步析出尿素晶体,降低催化器的效率,更严重时会堵塞催化器的小孔,使其发生破坏失效[7]。
3 SCR催化器CFD建模
3.1 几何模型
图1为催化转化器简化三维结构,采用的催化剂为钒基催化剂。催化剂共有4段,分布在不同部位,且催化剂孔密度为60孔/cm2,壁厚为0.13 mm,涂层厚度为0.015 mm。排气管与催化器的夹角为90°。如图1所示,整个催化器不具对称性,催化器内的还原剂分布不均,会导致催化反应程度不一致,从而导致NOx转化率降低[8]。因此,为了保证模拟能顺利进行,对整个催化转换器进行模拟。
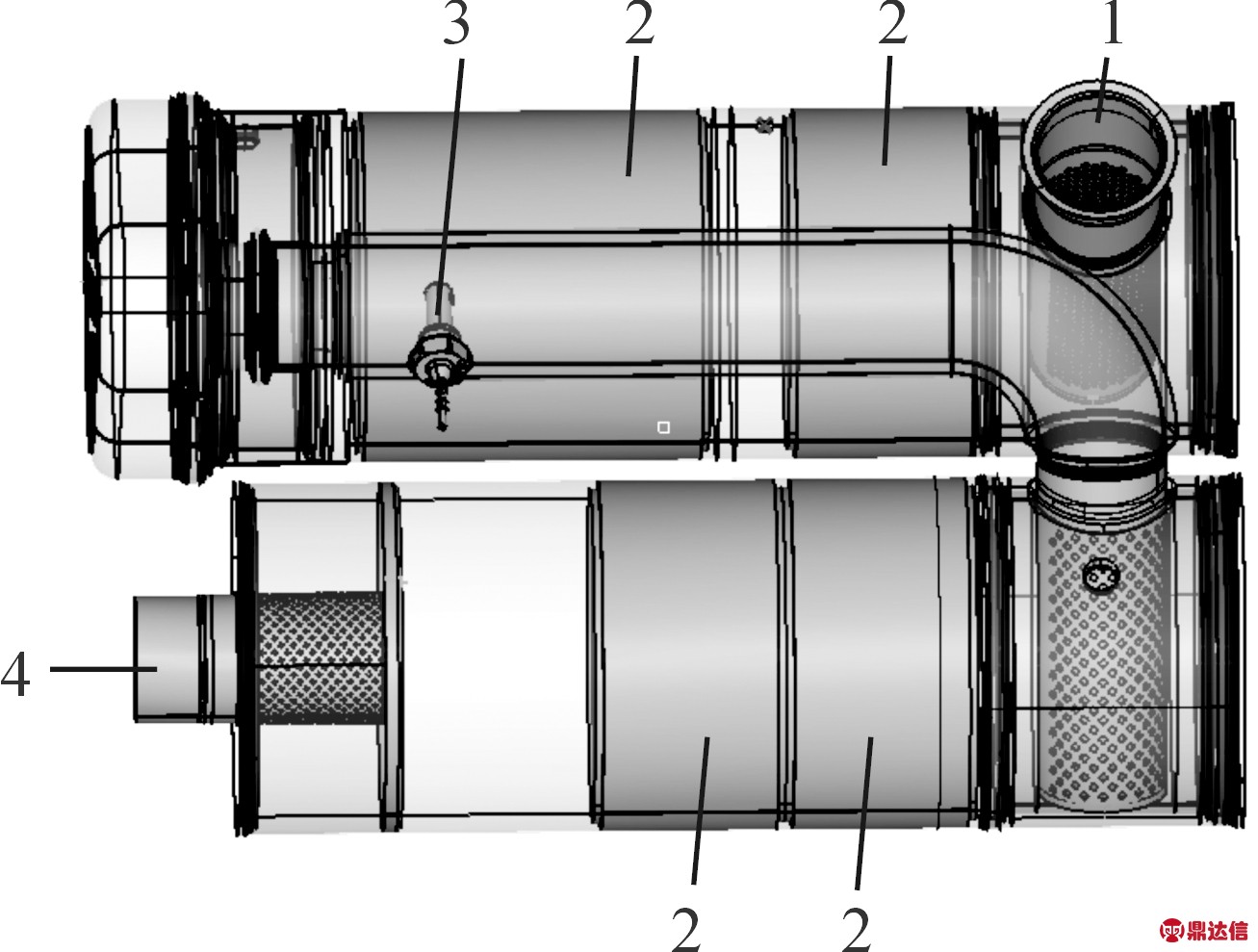
1.尾气入口;2.催化剂载体;3.雾化喷嘴;4.尾气出口
图1 催化转化器简化三维结构
催化转化器内部有催化剂载体、消音器管道和雾化喷嘴及固定安装装置。为了简化模型,把催化剂载体当成多孔介质处理,同时把消音器管道外表面布满的小孔半径扩大并保证其流通量不变,只保留氧化器、连接管、消音器和催化器。简化后共划分有 548 008个单元,节点数 136 536个。CFD网格模型图2所示,用CFD软件进行模拟计算。
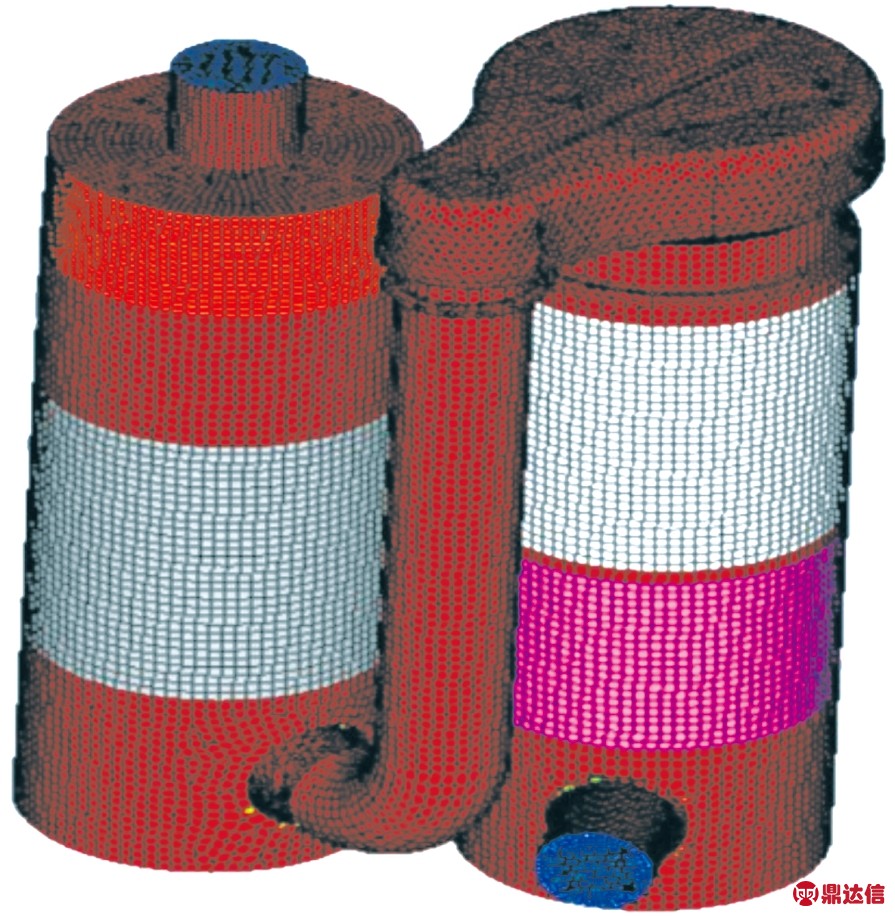
图2 CFD网格模型
3.2 计算模型
采用质量和动量守恒方程来描述SCR系统中的流体流动,利用雷诺方程和湍流模型分析溶液运动的过程,并利用湍流扩散模型分析尿素在排气管道中的扩散[9]。 从尿素溶液喷射点到SCR催化器的出口,涉及许多物理和化学反应,主要包括尿素溶液雾化、尿素溶液冲击催化器壁及液膜形成、尿素液滴的蒸发和热解以及催化剂的催化还原反应。此次分析只考虑尿素溶液在催化转化器中的雾化。
忽略尿素溶液的初始雾化过程,将尿素溶液看作是从喷嘴流出的离散液滴,再结合拉格朗日方法和欧拉方法来计算液滴轨迹。即尿素溶液雾化模拟采用离散液滴模型(DPM)模拟其在催化转化器中的雾化。
离散液滴模型(DPM)利用拉格朗日坐标系中的质点力微分方程求解尿素分散液滴的运动轨迹。在尿素溶液的流动过程中,喷雾颗粒受到惯性力、曳力、重力等作用力的综合影响,在旋转坐标系下,还会受到附加作用力的影响,从而导致喷雾颗粒的运动轨迹发生变化。为简化模型,将喷雾液滴假设为理想球形[10]。
离散液滴模型(DPM)对每个尿素液滴的求解运动控制方程为
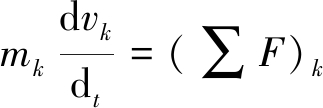
(1)
式中:vk为尿素液滴k的运动速度;mk为该液滴的质量;(∑F)k为该液滴所受的合力。
液滴运动轨道方程为
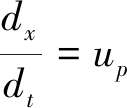
(2)
液滴的受力运动方程为
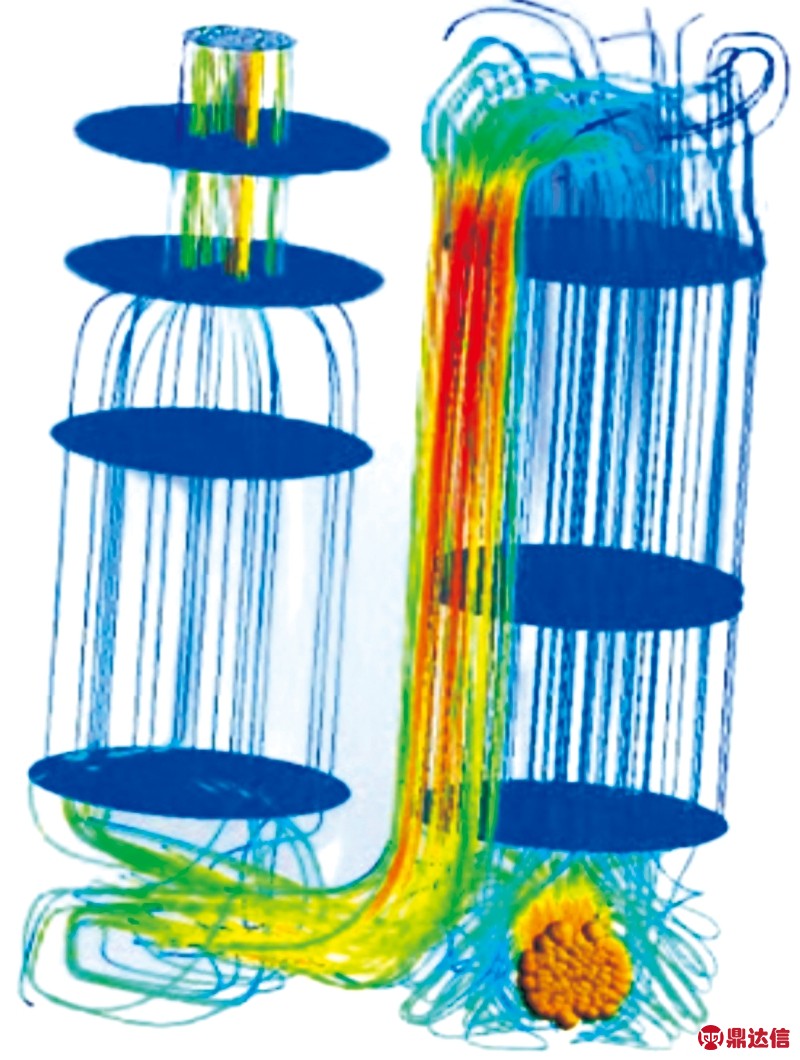
(3)
式中: fx为单位液滴质量的力;ρg为连续相密度;ρP为颗粒密度;g为重力加速度;u为连续相速度;uP为颗粒速度;fD(u-uP)为液滴单位质量曳力矢量,且:
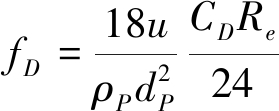
(4)
式中:CD为液滴的曳力系数;Re为液滴雷诺数,且:
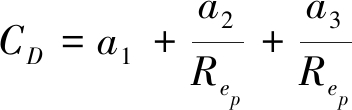
(5)
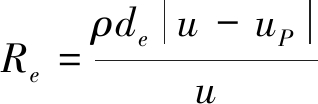
(6)
3.3 边界条件和参数
Fluent中的雾化模型一般实现的是对液滴的碰撞和蒸发等的模拟,而且不需要建立整个喷嘴的几何模型,极大地方便了模型的建立及计算仿真。
入口边界条件采用给定的排气流速和温度,排气速度为22.6 m/s,温度为780 K,水力直径为0.08 8m,湍动能设定为进口平均速度平方的5%;出口边界为大气压强,温度为450 K,水力直径为0.1 m,湍流强度为0.5%。
假设内流场壁面为光滑非渗透性的壁面,温度设为300 K,对流热交换系数为10 W/(m2·K)。将氧化催化器当成多孔介质处理,设定其黏性阻力系数为38.46 m-2,惯性阻力系数为20 000 m-2,并将黏性阻力系数与惯性阻力系数沿着气体流动的方向降低3个数量级。雾化喷嘴的设置参数如表1所示。
表1 雾化喷嘴的设置参数
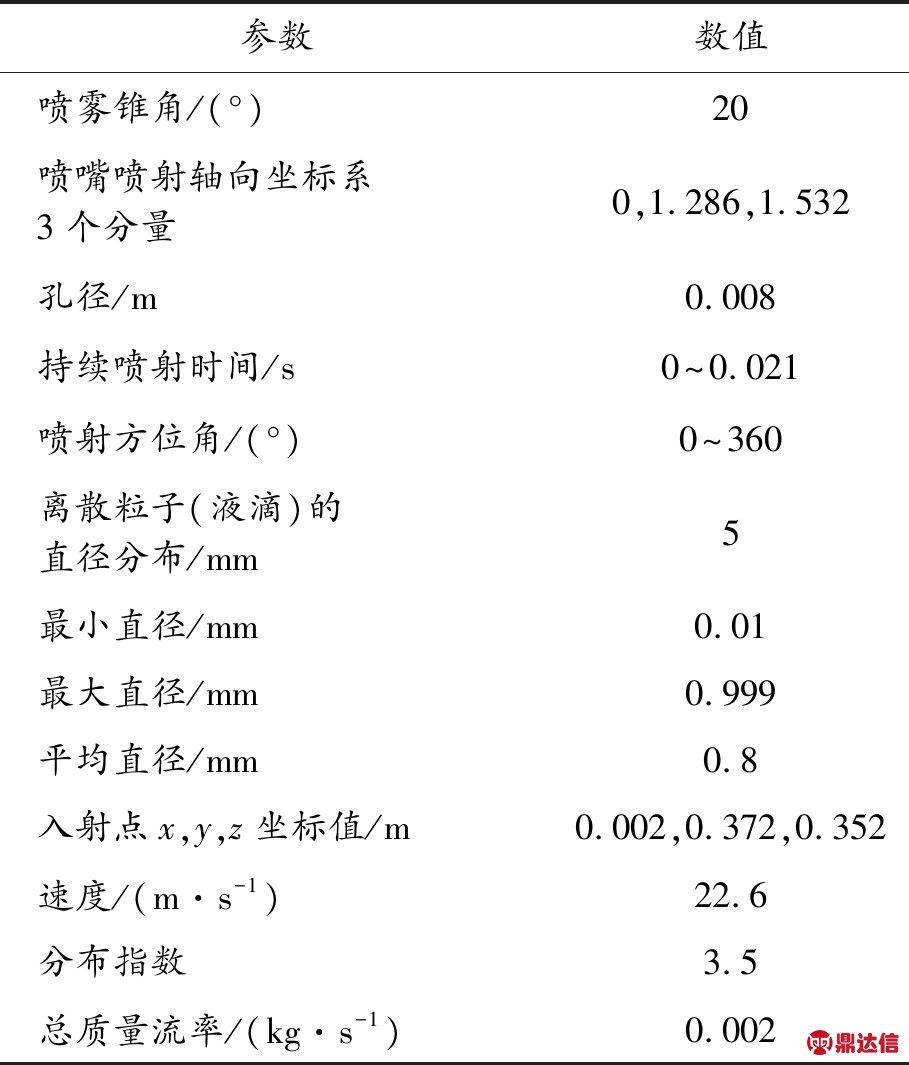
4 结果分析
由压力云图3可知:在多孔介质处有明显的压降,且基本呈线性变化,连接管处压力变化较小,这样对喷嘴喷出液滴的分布影响小,使液滴的流动更平稳,分布更均匀,不会导致液滴聚集或者大量附着在管壁上,避免造成尿素结晶,影响催化效率。
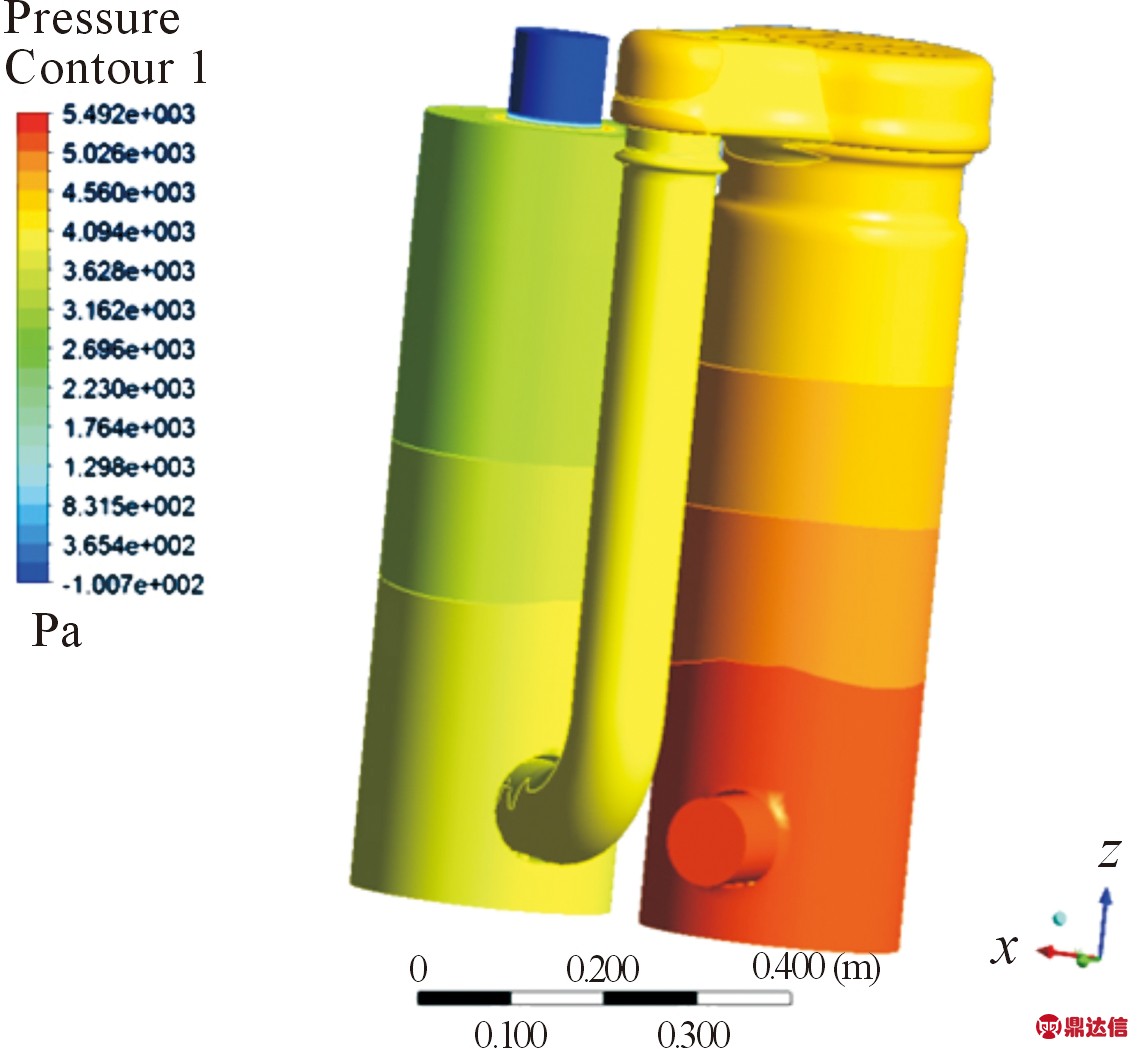
图3 压力云图
由速度云图4可知:在催化转化器的各个流域的轴线部位处流速比较大,最大值为26.8 m/s;在靠近壁面处流速比较小;在消音器小孔处的流通面小,流速快,很容易对内壁面产生持续不断的冲击,造成疲劳损伤破坏;在催化器载体流域内的流速比较缓慢,易于NH3与废气的混合与催化还原。
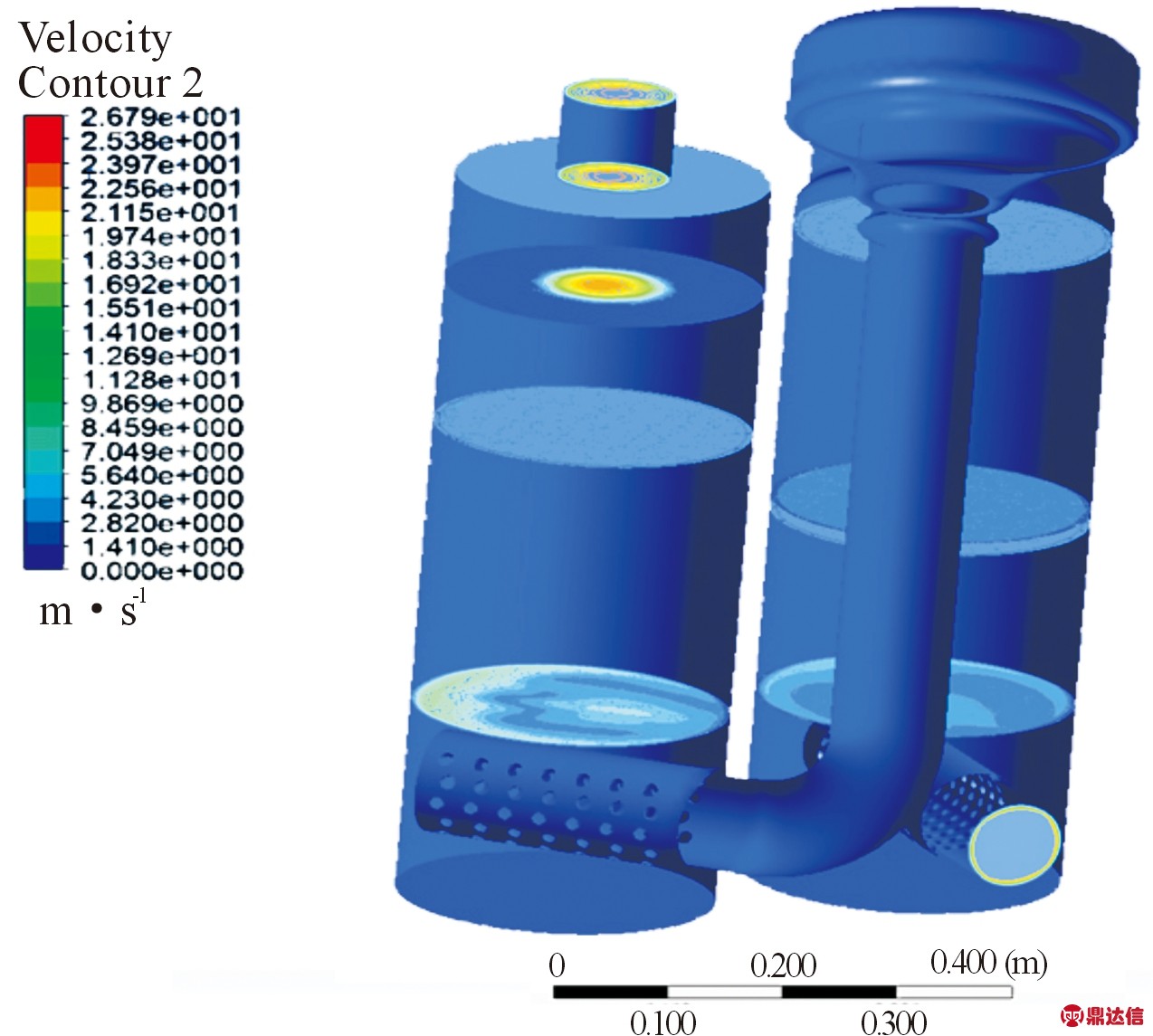
图4 速度云图
废气基本沿着管道流动,没有产生较大的涡流,在多孔介质区域速度方向基本一致,且在连接管即尿素喷射区域流速快。喷入的液滴大多数随废气向前流动,液滴受到高温排气的加热作用蒸发而产生水蒸气及熔融的尿素,在进入催化器之前全部汽化,且与废气均匀混合,有利于催化还原,极大地增加了载体的寿命。
流线图5表明:在消音器管道处流线分布较密集,流速快,但是因为流道截面积变化较大,流动较混乱,此处容易产生拖拽涡,从而产生诱导阻力,对废气的流动有极大干扰,不易于平稳过渡,会影响催化器入口处NH3的混合均匀性。
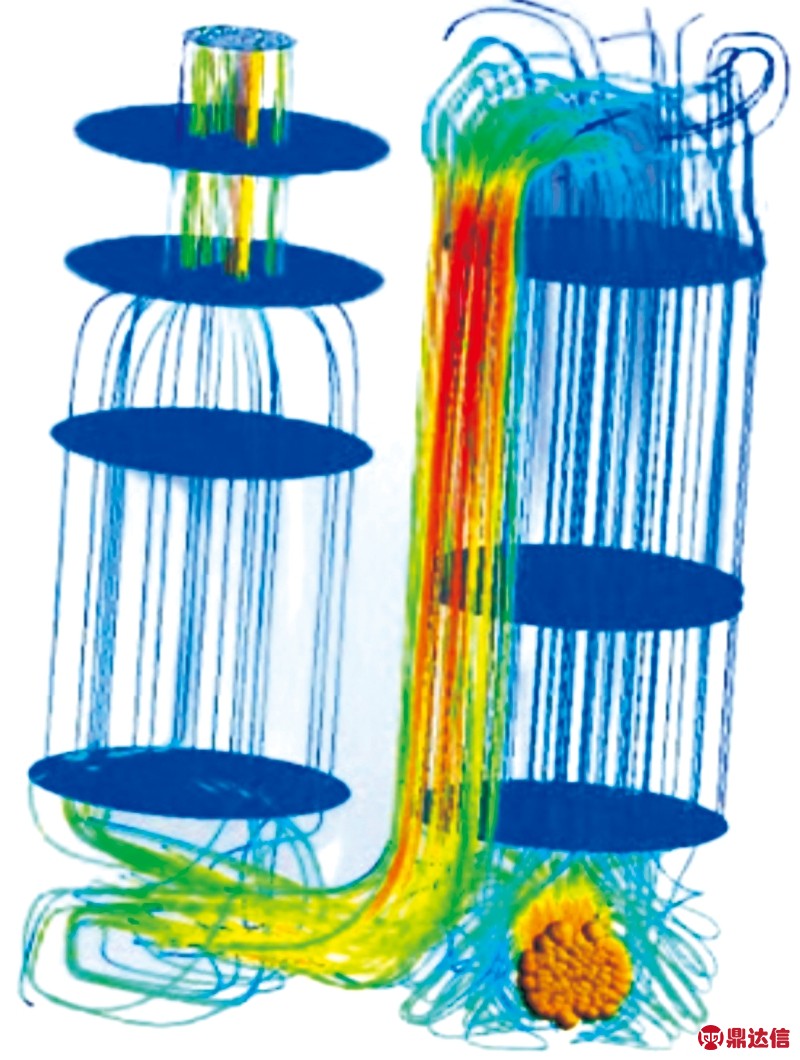
图5 流线图
由图6、7可知:在喷射轴线中心处的液滴质量最大,两边质量较小,这是因为外围液滴颗粒与废气接触的空间大,在受到作用力后容易分散破碎,而里面的液滴虽然流速快但受到喷射锥角的影响不易分散开,会造成液滴的二次包裹合聚,不利于尿素溶液的分解,进一步影响废气的催化还原。
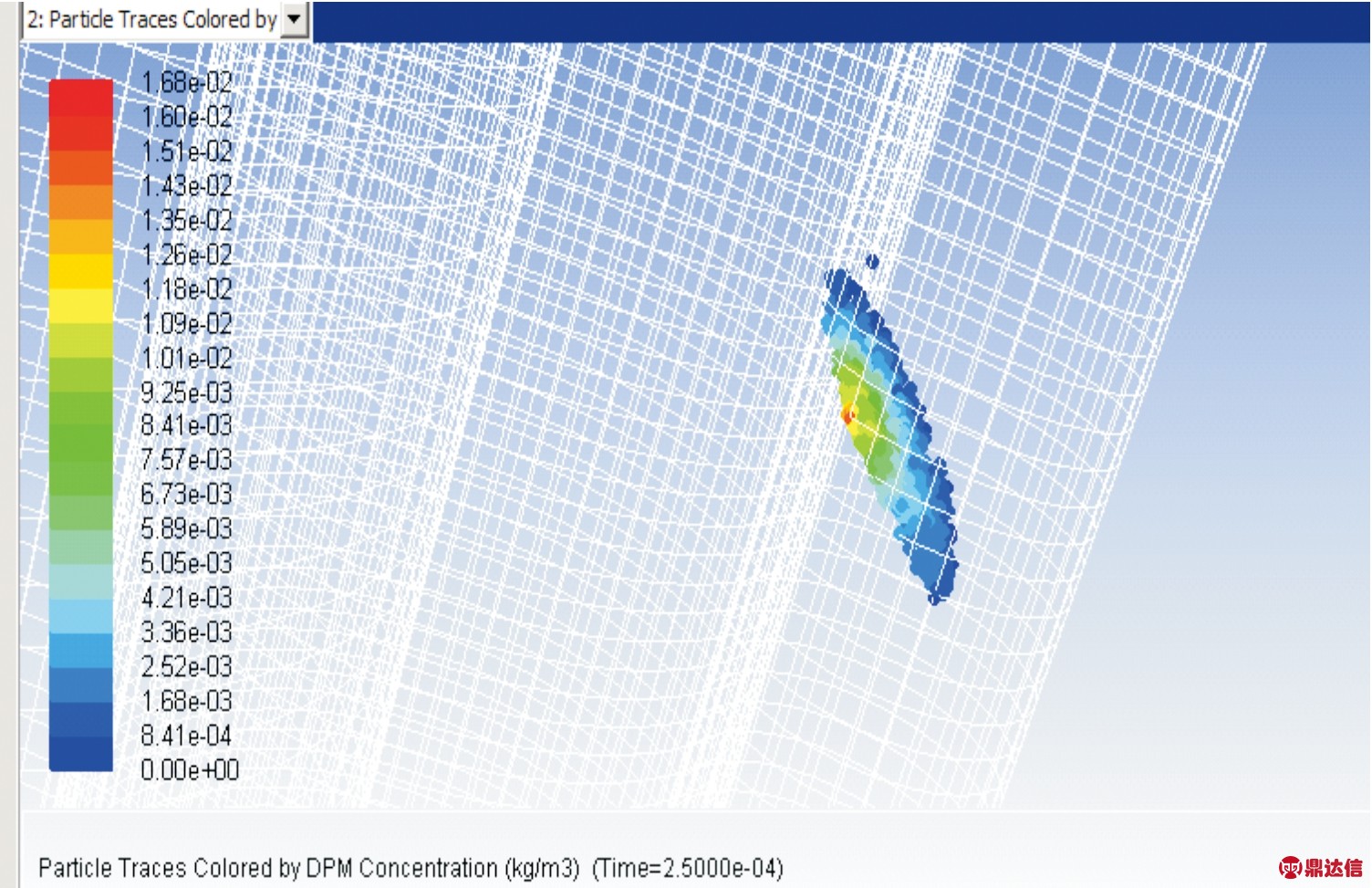
图6 离散相颗粒质量分数图1
由图8、9可知:液滴直径分布比较均匀,没有出现直径大或直径小的液滴颗粒聚拢的现象,液滴呈交错混合,即罗辛-拉姆勒Rosin-Rammler分布,这样易于液滴受热分解与废气混合,利于催化还原。
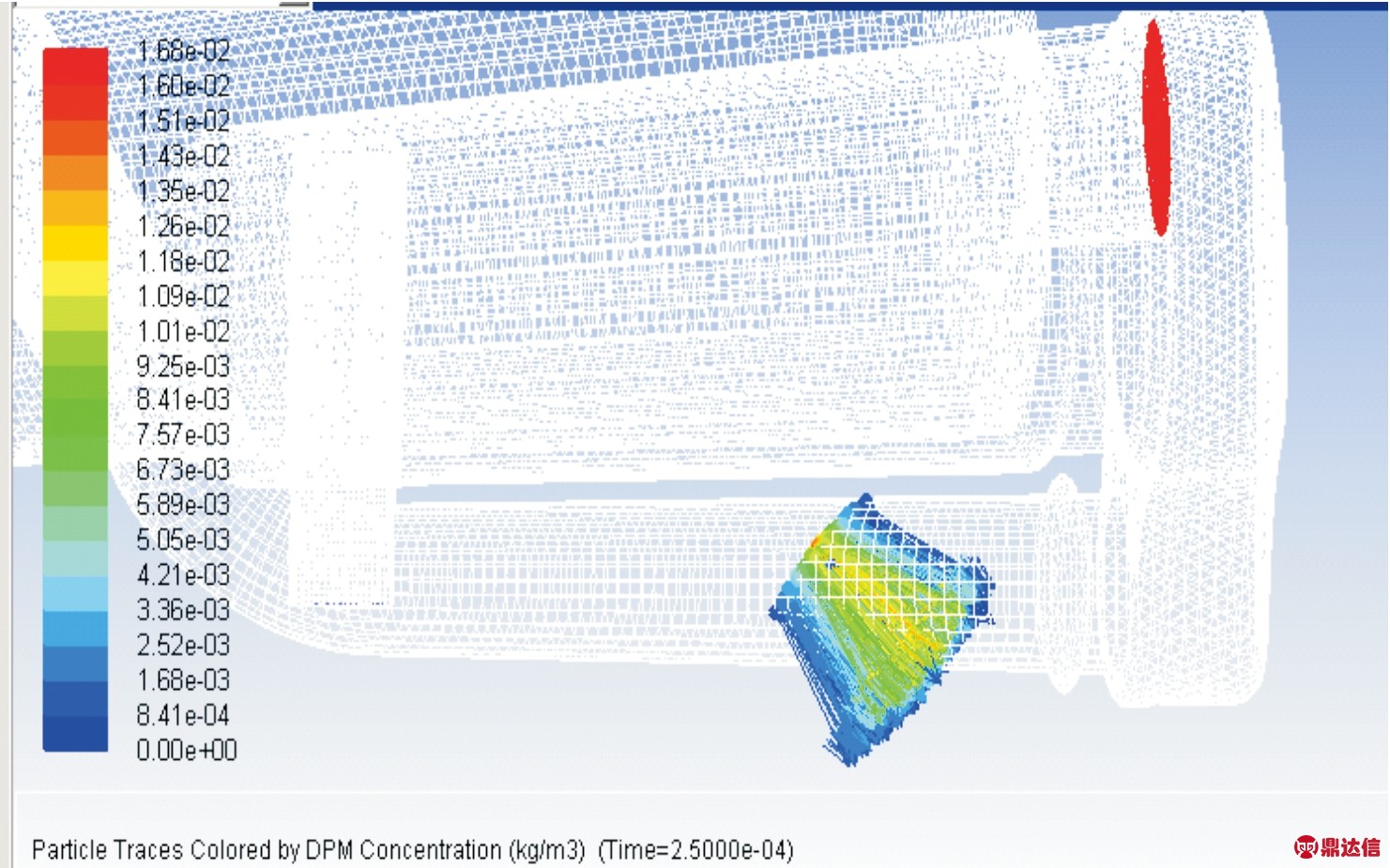
图7 离散相颗粒质量分数图2
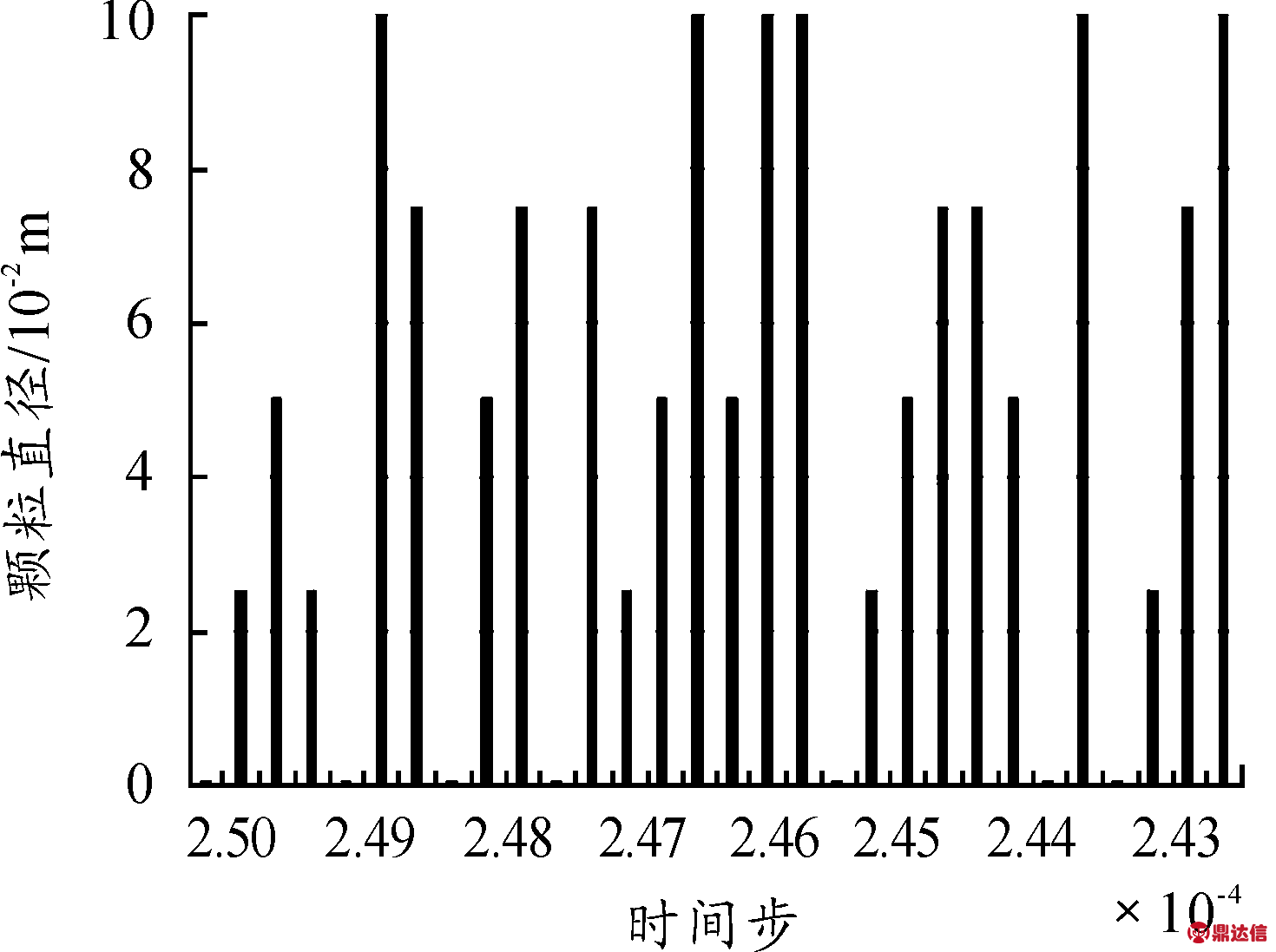
图8 颗粒直径分布
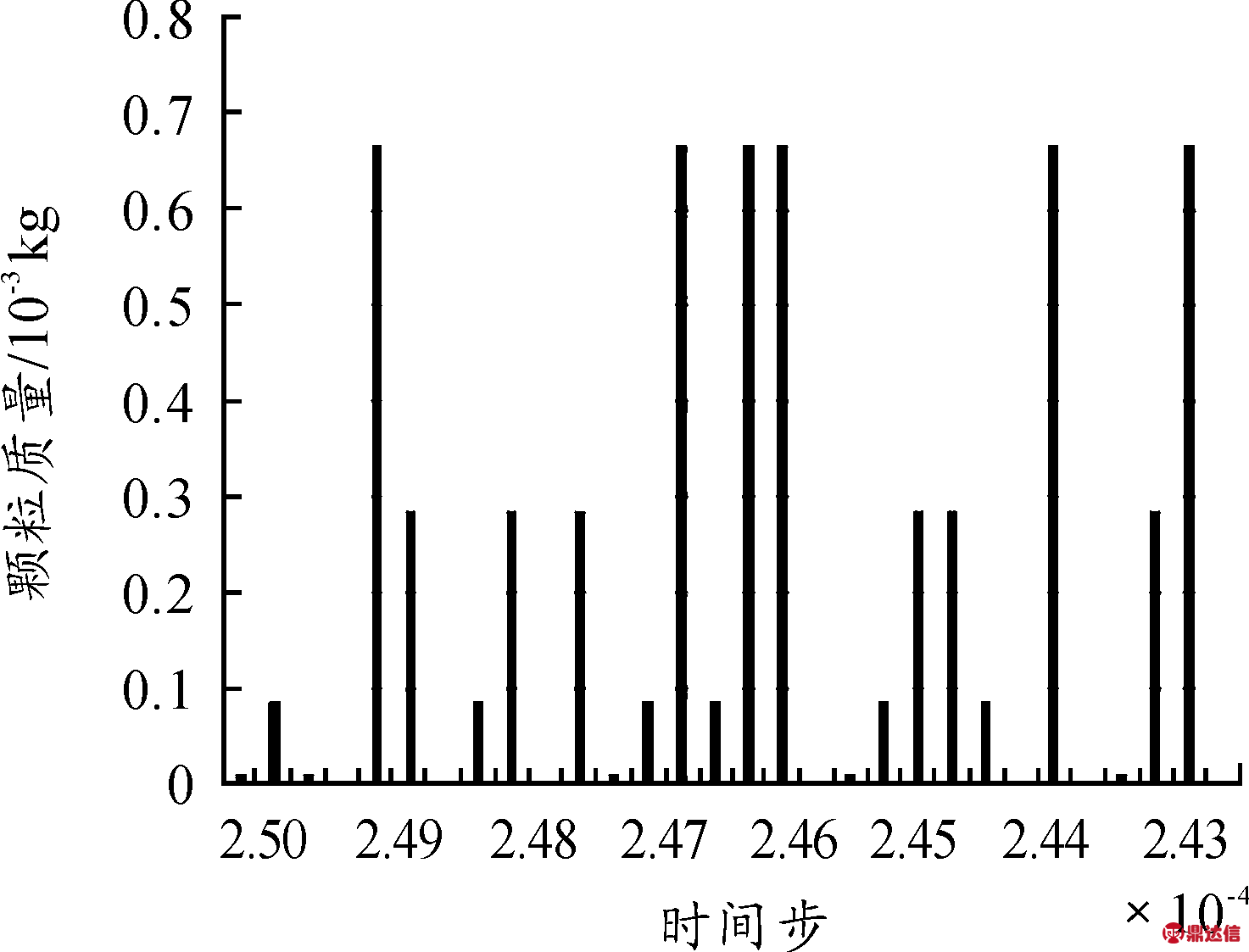
图9 颗粒质量分布
5 结论
1) 在SCR系统的排气管部位容易形成大小不一的结晶。尿素溶液喷嘴的布置位置、角度和距离对尿素液滴的运动轨迹影响较大,因此可以通过优化这些参数,提升SCR系统的工作性能,并降低NOx的排放。
2) 柴油机尿素SCR催化器的压力、速度、流线图以及尿素颗粒直径、质量分布能反映其尿素颗粒分布、浓度,基本满足催化器对废气的催化条件,对带有尿素SCR催化器的柴油机的设计具有一定的指导意义。